散热框的注塑模具设计开题报告.docx
《散热框的注塑模具设计开题报告.docx》由会员分享,可在线阅读,更多相关《散热框的注塑模具设计开题报告.docx(9页珍藏版)》请在冰豆网上搜索。
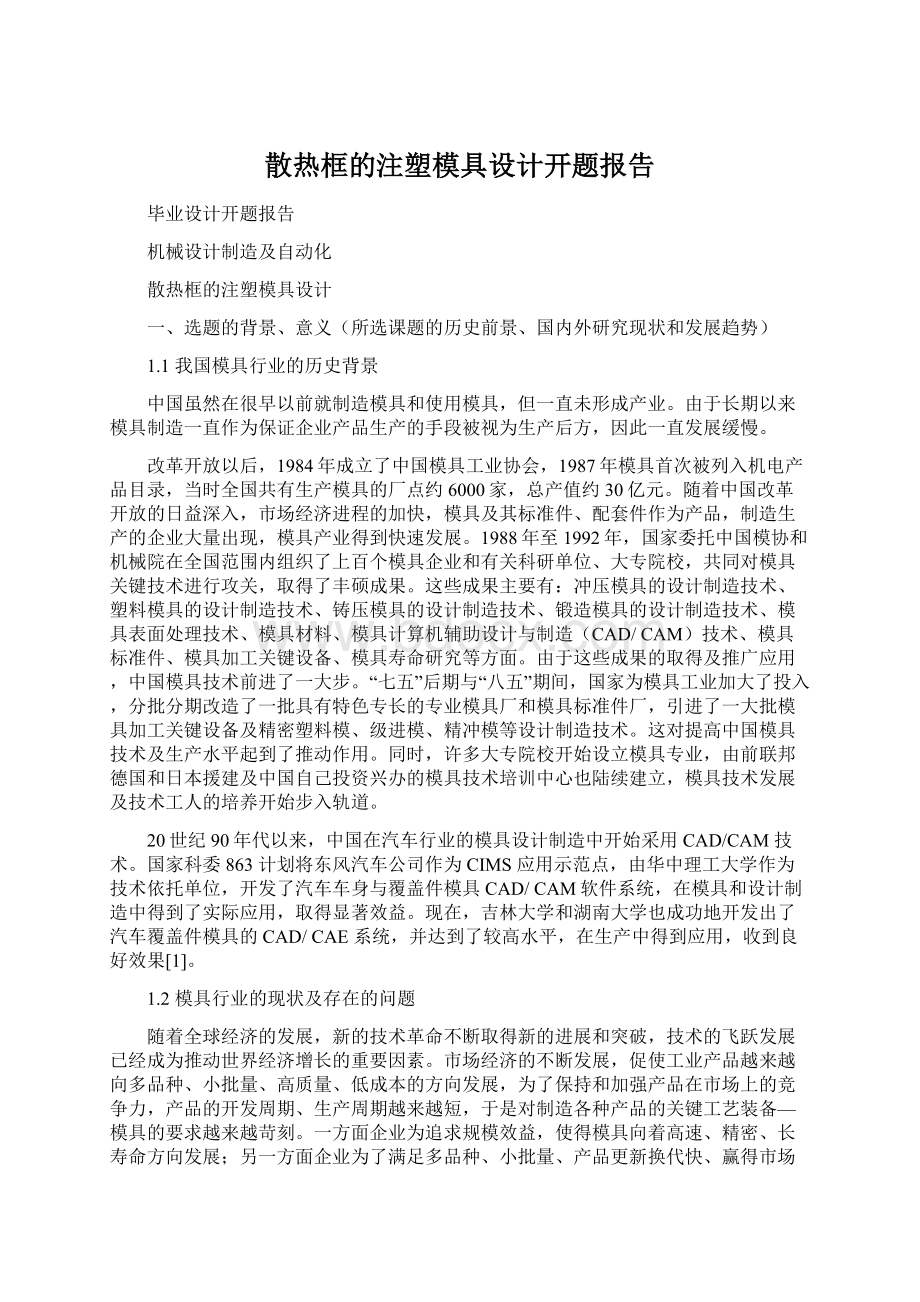
散热框的注塑模具设计开题报告
毕业设计开题报告
机械设计制造及自动化
散热框的注塑模具设计
一、选题的背景、意义(所选课题的历史前景、国内外研究现状和发展趋势)
1.1我国模具行业的历史背景
中国虽然在很早以前就制造模具和使用模具,但一直未形成产业。
由于长期以来模具制造一直作为保证企业产品生产的手段被视为生产后方,因此一直发展缓慢。
改革开放以后,1984年成立了中国模具工业协会,1987年模具首次被列入机电产品目录,当时全国共有生产模具的厂点约6000家,总产值约30亿元。
随着中国改革开放的日益深入,市场经济进程的加快,模具及其标准件、配套件作为产品,制造生产的企业大量出现,模具产业得到快速发展。
1988年至1992年,国家委托中国模协和机械院在全国范围内组织了上百个模具企业和有关科研单位、大专院校,共同对模具关键技术进行攻关,取得了丰硕成果。
这些成果主要有:
冲压模具的设计制造技术、塑料模具的设计制造技术、铸压模具的设计制造技术、锻造模具的设计制造技术、模具表面处理技术、模具材料、模具计算机辅助设计与制造(CAD/CAM)技术、模具标准件、模具加工关键设备、模具寿命研究等方面。
由于这些成果的取得及推广应用,中国模具技术前进了一大步。
“七五”后期与“八五”期间,国家为模具工业加大了投入,分批分期改造了一批具有特色专长的专业模具厂和模具标准件厂,引进了一大批模具加工关键设备及精密塑料模、级进模、精冲模等设计制造技术。
这对提高中国模具技术及生产水平起到了推动作用。
同时,许多大专院校开始设立模具专业,由前联邦德国和日本援建及中国自己投资兴办的模具技术培训中心也陆续建立,模具技术发展及技术工人的培养开始步入轨道。
20世纪90年代以来,中国在汽车行业的模具设计制造中开始采用CAD/CAM技术。
国家科委863计划将东风汽车公司作为CIMS应用示范点,由华中理工大学作为技术依托单位,开发了汽车车身与覆盖件模具CAD/CAM软件系统,在模具和设计制造中得到了实际应用,取得显著效益。
现在,吉林大学和湖南大学也成功地开发出了汽车覆盖件模具的CAD/CAE系统,并达到了较高水平,在生产中得到应用,收到良好效果[1]。
1.2模具行业的现状及存在的问题
随着全球经济的发展,新的技术革命不断取得新的进展和突破,技术的飞跃发展已经成为推动世界经济增长的重要因素。
市场经济的不断发展,促使工业产品越来越向多品种、小批量、高质量、低成本的方向发展,为了保持和加强产品在市场上的竞争力,产品的开发周期、生产周期越来越短,于是对制造各种产品的关键工艺装备—模具的要求越来越苛刻。
一方面企业为追求规模效益,使得模具向着高速、精密、长寿命方向发展;另一方面企业为了满足多品种、小批量、产品更新换代快、赢得市场的需要,要求模具向着制造周期短、成本低的快速经济的方向发展。
计算机技术、软件技术、新材料、新技术的发展,使得快速经济制模技术如虎添翼,应用范围不断扩大,类型不断增多,创造的经济效益和社会效益越来越显著[2]。
1.2.1我国塑料模具行业的现状及存在的问题
我国塑料模具的质量、技术和制造能力近年来确实发展很快,有些已达到或接近国际水平,尤其是改革开放政策的不断深入,“三资”企业蓬勃发展,对我国塑料模具设计制造水平的提高起到了非常大的作用。
然而,由于我国模具制造基础薄弱,各地发展极不平衡,因此总体来看,与国际先进水平相比和与国内外市场需求相比,差距还很大[3]。
表1是我国塑料模具产品水平与国外塑料模具产品水平的比较[4]。
表1国内外塑料模具产品水平比较
1.3塑料模具的发展趋势
近年来塑料成型模具的产量和水平发展十分迅速,高效率、自动化、大型、精密、长寿命模具在模具总产量中所占比例越来越大,从模具设计和制造两方面来看,模具发展趋势可
归纳为以下几点。
1.3.1理论研究不断发展,设计计算日趋成熟
由于对塑料成型加工原理的研究越来越深入,作为成型加工重要装备的模具其设计已经由经验设计逐步向理论计算发展,这些理论为塑料模具的计算机辅助设计和辅助工程奠定了基础。
其中重要的有对塑料熔体在模具内的流动、传热、取向、结晶的研究,模具的受力状态的研究等,其理论计算已达到了实用化阶段[5]。
1.3.2塑料模的高效率自动化
大力地发展和采用各种高效率自动化的模具结构,如多层多型腔注射模结构,各种能自动脱出产品和流道凝料的脱模机构,自动分型抽芯机构,热流道浇注系统以及产品的高效冷却结构,它能大大缩短成型周期。
高效自动化的模具与高速自动化的成型设备相配合对提高生产效率,提向产品质量,降低生产成本起着至关重要的作用。
1.3.3大型塑料模具
随着塑料应用领域日益扩大,在建筑、机械、汽车、仪器、家用电器上采用了许多大型注塑模具,如汽车壳体、保险杠、洗衣机桶、大周转箱等,这就相应地需要大型模具特别是大型注塑模具。
大型模具设计要求作详细准确地理论计算,由于模具自重大,物料流程长,型腔易变形,因此在结构设计上需作更为周密的考虑。
1.3.4高精度塑料模具
普通模塑塑料制件的精度比机械切削能达到的制件精度低得多。
但是在某些特殊的情况下需要高精度的塑件,例如作为机械零件使用的传动齿轮、轴承等,这种模具的配合精度和运动精度要求都很高、耐磨损、模温控制精确,在高压下成型,收缩变形小[6]。
1.3.5模具计算机辅助设计(CAD)辅助工程(CAE)
这是20世纪70年代迅速发展起来的,到80年代已进入实用化。
不同的软件可分别用于挤塑、注塑、压制、压铸、中空等模具的设计和对模具结构、产品质量进行分析,它由计算机硬件和专用软件组成。
CAD软件的主要功能是几何造型技术,它将制品图形立体地精确地显示在屏幕上,完成制件设计的绘图工作,对制品或模具进行力学分析。
而过程软件(CAE软件)中流动软件可模拟熔体在模内的流动过程。
冷却分析软件可模拟熔体的凝固过程和在模内温度的变化,预测可能出现的问题,如制品缺陷、翘曲、变形、内应力等,使设计结果优化。
计算机能大量储存和方便地查找各种设计数据(数据库)和标准件的图形(图形库),并能绘出模具的零件和装配图、使设计质量提高,设计速度加快许多倍[7]。
1.3.6模具制造新工艺的进展
塑料模具制造中最困难的部分莫过于型腔,特别是异形复杂型腔的切削加工,若按传统方式进行机械加工,十分费时费工,且难以保证质量。
为缩短制模周期,提高模具精度,减少钳工等手工操作工作量,采用了各种坐标机床、仿形机体、光控机床和数控机床等。
特别是近年来发展起来的计算机辅助制造(CAM)使模具制造技术取得了突破性进展,它采用计算机程序,控制数字机床的刀具和工件运动轨迹和加工程序,来完成模具型腔的加工过程。
采用注射模CAM后,模具的质量大大提高,而且成本降低10%一30%,加工周期缩短20%一50%。
电加工技术的进步给塑料模型腔加工带来了巨大方便,特别是用高硬度、高强度材料制造的型腔可在淬火后直接加工。
最常见的电加工技术有电火花、线切割、电强化、电抛光等。
用计算机程序控制电火花加工是一项正在发展的高效率、高精度型腔加工新技术.估计它将取代很大一部分型腔的机械切削加工工作量。
将模具的计算机辅助设计、辅助工程和辅助制造连成一体的设计与制造系统(即CAD/CAE/CAM一体化)是在模具型腔结构和尺寸经CAE软件优化后,将用CAD系统建造的型腔几何模型直接生成型腔加工的数控程序单,并指挥相关机床完成型腔的数控加工,模具计算机辅助设计的一些商品化的软件层出不穷,在不断开发过程中,采用CAD/CAE/CAM技术可以使塑模型腔达到±0.0001%的重复加工精度和±0.0002%的准确性[8]。
1.3.7简易制模工艺的研究
为了及时地更新产品的花色品种、降低成本和适应小批量产品生产的要求,开展了简易制模工艺的研究。
其所用的材料有木材、石膏、陶瓷、塑料等非金属,也有铸钢、铜合金、铝合金、锌合金、易熔合合。
制模方法有浇铸、喷涂、交联固化等;例如采用锌合金浇铸制模、以铝粉、细钢丝等填充增强的环氧树脂制模,聚氨酯弹性体制模,这些模具虽然精度较差,寿命不长,但制模周期特别短,成本低、有—定的适用范围。
1.3.8模具标准化
目前发达国家模具标准化程度达到30%以上,并齐完善的标准系列,包括零件标准和模架标准,国际标准化组织已制订了国际模具系列标准,标准件品种多,规格全,质量高,而且全部均已商品化。
近年来我国模具标准化工作有了很大的进展,基本上配齐了主要模具类别的零件标准。
在塑料模具方向有塑料注塑模零件标准、塑料注塑模零件技术条件、塑料注塑模模架标准、塑料注塑模技术条件等,其中零件标准包括模板、垫块、推杆、导柱、导套等十余种零件。
现已有不少专业厂成套生产标准模架,成批生产各种模具零件,作为商品出售。
模具标准化为塑料模具设计和制造都带来极大的方便,出于标准件可直接购买,因此模具设计制造者只需精心设计和加工型腔,这使得塑料模具的设计和制造周期大为缩短,成本降低,质量得到保证。
当前我国模具标准化程度还不高,尚需大力推广、充实完善、扩大模具标准件新系列[9]。
1.3.9特种塑料成型模具的研制
如随着成型新工艺而出现的气体辅助注塑成型模具、低发泡制品注塑模具、反应注塑成型模具、多层多腔注塑模具、多色注塑模具以及低发泡挤出机头、多层复合机头等。
此外在模具制造上采用特殊的模具钢材。
采用特殊的表面处理技术如离子注入、物理沉积、喷镀、刷镀等提高模具的使用寿命。
表面花纹加工新技术可提高塑件外观质量等[10]。
由于塑料工业的快速发展及各方面差距的存在,因此我国今后塑料模具的发展速度必将大于模具工业总体发展速度。
塑料模具生产企业在向着规模化和现代化发展的同时,“小而精”、“小而专”仍旧是一个必然的发展趋势[11]。
二、相关研究的最新成果及动态
最近几年来,注射成型技术发展的最新动向为:
低压注射成型、高速注射成型、复合注射成型和超级小超密注射成型。
2.1低压注射成型
低压注射成型发展背景是:
首先,传统注射成型技术存在着庞大机器与生产小制品的矛盾;其次在成型方面容易产生种类繁多的缺点,诸如制品残余应力过大、飞边、注料不足、折皱、焦烧、脱模不良、熔接缝、裂痕、翘曲变形、缩孔;另外在塑化方面存在色调不均匀、分散不良、混炼不充分、熔体温度不均等缺点,而制品的各方面质量指标要求却在不断提高,因而导致了低压注射成型迅速发展。
低压注射成型的主要优点有:
(1)注射压力、锁模力低、模腔压力也低
低压注射成型的锁模力一般仅为传统注射成型的一半左右,模腔压力仅为传统注射成型的一半,为传统精密注射成型的40%。
因此,可实现小锁模力、小型注射机生产大制品。
(2)节能
由于注射压力、锁模力都比传统的注射成型低,一般在能量消耗方面会节省10%左右。
(3)成型周期缩短
一般比传统的注射成型缩短8%~10%,若是成型大面积薄壁制品,则成型周期更短。
(4)模具费用降低
因为注射压力显著降低,则模具的强度、刚度均可降低,当模具材料相同时,模具重量也会降低,同时模具制造及维护费用也降低。
(5)制品内应力、取向分布不均匀性减少
这防止和减少了制品的变形,不仅制品的尺寸、形状精密、模具的形态“转写”复制功能得以充分发挥,而且传统注射成型制品的常见缺陷基本上都可消除。
因此,现在许多精密度要求很高的制品都采用低压注射成型技术。
例如DAD、DVA、CD等光碟、光学透镜、笔记本电脑光导器等都改用低压注射成型,取得了非常好的效果。
低压注射成型之所以具有这么多优点,并且愈来愈广泛地被采用,主要是由于它不是在模具紧紧锁合的情况下用高注射压力将塑料熔体强行注满模腔。
低压注射成型具体实施技术可分为:
注射压缩成型、高注射速率低压注射成型、气体辅助注射成型等。
低压注射成型的实施,并不需要完全更改传统注射机,而只需对模具进行一些特殊设计或采用某些辅助系统,但关键是需对注射机的控制系统作些新的更改[12]。
2.2高速注射成型
该技术是适应制品的精密成型的需要,减少模腔内压力、温度和取向的不均匀而开发的。
其特点主要是充模时间短、物料熔体流动阻力和压力损失小,因此特别适用于大型薄壁制品的生产。
通常高速注射成型的实施需要具备如下条件:
(1)注射机的注射力足够高
(2)注射机的刚度高
(3)成型条件参数节换响应状态优良
(4)成型条件的稳定性、重复性良好
(5)物料塑化均匀
目前高速注射成型的注射速率已达1000mm/s,注射速率达1017cm3/s[13]。
2.3复合(共)注射成型
由于对塑料制品功能多样化的要求日益增多,因此在注射成型领域内展开了各式各样的复合注射成型技术开发。
复合注射成型技术包括三种:
(1)二色、多色注射成型
以往的多色注射成型多数采用注射模具的位置交换的方式来实现,而目前则采用专用注射机来完成,最突出的应用例子是汽车照明灯罩的生产。
(2)多材质注射成型
这种注射成型方法主要是为了使制品同时满足多种不同性能的要求而开发的。
例如制品要求耐候性、化学稳定性、气体阻隔性、导电性、屏蔽电磁波性等性能的某种组合,则必须采用多材质(不同树脂)的多层复合注射成型技术。
(3)内加装饰件注射成型
此种注射成型技术多用于改善制品的耐候性、装饰性和功能性的要求,很多功能薄膜连同粘接层预先制备好,注射充模前置于模腔,然后借助注人模腔的熔体使其间达成一体,从而提高制品的功能性[14]。
2.4超极小、超精密注射成型
这种注射成型技术自80年代末期至今发展速度非常快。
像日本的Sumitomo公司、Nissei公司、Juken公司、东芝机械、日精树脂工业,英国的ButlerDesigen公司、MCP公司,瑞士的IutronEngineering公司、Rolla公司,德国的IKV、Battenfeld公司,西班牙的Cosmold公司等都竞相开发微型精密注射成型机,这些公司都有相当数量的机台投人工业生产。
超极小、超精密注射成型技术所采用的注射机有螺杆式的,也有柱塞式的。
最大合模力为250KN,最小的合模力仅为12KN有卧式的,也有立式的;制品重量可在0.1~0.00013g范围;制品尺寸精度达0.005mm。
实施超级小、超精密注射成型加工,牵涉到材质、制品设计、注射机、模具、控制、检测、投料方式、制品收集、环境洁净级别等广泛领域的技术。
对于超级小、超精密注射成型技术而言,目前的普遍水平处于可实现0.0001g级制品的生产,其所用的注射机、模具加工和制造、控制系统等技术已较成熟,预定下一步的目标是生产0.00001g级的制品[15]。
三、课题的研究内容及拟采取的研究方法(技术路线)、研究难点及预期达到的目标
3.1研究内容
本设计项目的内容是对散热框进行注塑模具设计。
3.2技术路线及方法
注塑模具的设计须按照以下几个步骤进行
3.2.1塑件分析
(1)明确塑件设计要求仔细阅读塑件制品零件图,从制品的塑料品种,塑件形状,尺寸精度,表面粗糙度等各方面考虑注塑成型工艺的可行性和经济性,必要时,要与产品设计者探讨塑件的材料种类与结构修改的可能性。
(2)明确塑件的生产批量小批量生产时,为降低成本,模具尽可能简单;在大批量生产时,应保证塑件质量前提条件下,尽量采用一模多腔或高速自动化生产,以缩短生产周期,提高生产率,因此对模具的推出机构,塑件和流道凝料的自动脱模机构提出严格要求。
(3)计算塑件的体积和质量计算塑件的体积和质量是为了选用注塑机,提高设备利用率,确定模具型腔数。
3.2.2注塑机选用
根据塑件的体积或重量大致确定模具的结构,初步确定注塑机型号,了解所使用的注塑机与设计模具有关的技术参数,如注塑机定位圈的直径,喷嘴前端孔径及球面半径,注塑机最大注塑量,锁模力,注塑压力,固定模板和移动模板面积大小及安装螺孔位置,注塑机拉杆的间距,闭合厚度,开模行程,顶出行程等。
3.2.3模具设计的有关计算
(1)凹,凸模零件工作尺寸的计算;
(2)型腔壁厚,底板厚度的确定;
(3)模具加热,冷却系统的确定。
3.2.4模具结构设计
(1)塑件成型位置及分型面选择;
(2)模具型腔数的确定,型腔的排列和流道布局以及浇口位置设置;
(3)模具工作零件的结构设计;
(4)侧分型与抽芯机构的设计;
(5)顶出机构设计;
(6)排气方式设计。
3.2.5模具总体尺寸的确定,选购模架
模架已逐渐标准化,根据生产厂家提供的模架图册,选定模架,在以上模具零部件设计基础上初步绘出模具的完整结构图。
3.2.6注塑机参数的校核
(1)最大注塑量的校核;
(2)注塑压力的校核;
(3)锁模力的校核;
(4)模具与注塑机安装部分相关尺寸校核,包括闭合高度,开模行程,模座安装尺寸等几方面的相关尺寸校核。
3.2.7模具结构总装图和零件工作图的绘制
模具总图绘制必须符合机械制图国家标准,其画法与一般机械图画法原则上没有区别,只是为了更清楚地表达模具中成型制品的形状,浇口位置的设置,在模具总图的俯视图上,可将定模拿掉,而只画动模部分的俯视图。
模具总装图应该包括必要尺寸,如模具闭合尺寸,外形尺寸,特征尺寸(与注塑机配合的定位环尺寸),装配尺寸,极限尺寸(活动零件移动起止点)及技术条件,编写零件明细表等。
通常主要工作零件加工周期较长,加工精度较高,因此应首先认真绘制,而其余零部件应尽量采用标准件[16][17]。
3.3研究难点
(1)注塑零件的设计与工艺路线
(2)模具结构设计
3.4预期达到的目标
通过本次毕业设计能更好的掌握注塑模具的设计方法,对PRO/E软件的运用更加熟练深入并能将所设计的模具应用于生产实践。
四、论文详细工作进度和安排
2010.11.15-2010.11.20下达任务书;
2010.11.21-2011.01.10查阅资料,完成文献综述和2篇外文翻译;
2011.01.11-2011.02.25完成开题报告;
2011.02.26-2011.03.29完成毕业实习及报告,第6周返校,保证设计时间;
2011.03.30-2011.05.09完成注塑模具的设计,绘制出工程图;
2011.05.09-2011.05.20完成毕业论文初稿;
2011.05.21-2011.05.26完成毕业论文终稿,答辩前准备;
2011.05.27-2011.05.29毕业答辩。
五、主要参考文献
[1]郑东晖.我国模具工业发展情况分析[J].成功(教育),2009(02):
296.
[2]罗继相.浅谈我国模具行业现状及发展趋势和对策[J].模具技术,2001(03):
72.
[3]XiaYuhai.PresentStateandDevelopmentoftheDie&MouldIndustrial[J].MODERNMANUFACTURINGTECHNOLOGYANDEQUIPMENT,2007(6):
5.
[4]周永泰.我国塑料模具现状与发展趋势[J].塑料,2000(6):
23,24.
[5]李和平,吴霞.现代模具行业现状与发展趋势综述[J].商场现大化,2007(3):
257.
[6]许俊远.注射成型技术的发展概况[J].广西经贸,1999(08):
35.
[7]RenHonglie.NewDevelopmentTrendofInternationalInuectionMoldingTechnology[J].LIGHTINDUSTRYMACHINERY,1999(01):
12.
[8]盛晓敏,邓朝晖.先进制造技术[M],北京:
机械工业出版社,2000:
47.
[9]申开智.塑料成型模具[M].北京:
中国轻工业出版,2002.9:
78.
[10]曹将栋.现代注塑模具设计的一些先进技术概述[J].机电信息,2009(30):
162.
[11]杨守滨.浅谈注塑模具先进制造关键技术发展[J].科技创新导报,2008
(2):
78.
[12]吴智华.注射成型技术的发展动态[J].塑料包装,2001(04):
17,18.
[13]HongLihua.StatusandToolingDie&MoldIndustryDevelopmentTrendofChina[J].MECHANICAL&ELECTRICALTECHNOLOGY,2007(30):
21.
[14]周永泰.中国模具正在加速融入世界并实现国际共赢[J].模具工业,2006,32(4):
6.
[15]李发致.模具先进制造技术[M].北京:
机械工业出版社,2003:
32.
[16]夏江梅.塑料成型模具与设备[M].北京:
机械工业出版社,2005.4:
31-34.
[17]徐佩弦.塑料制品与模具设计[M].北京:
中国轻工业出版社,2001.7:
25-27.