炼焦工艺.docx
《炼焦工艺.docx》由会员分享,可在线阅读,更多相关《炼焦工艺.docx(23页珍藏版)》请在冰豆网上搜索。
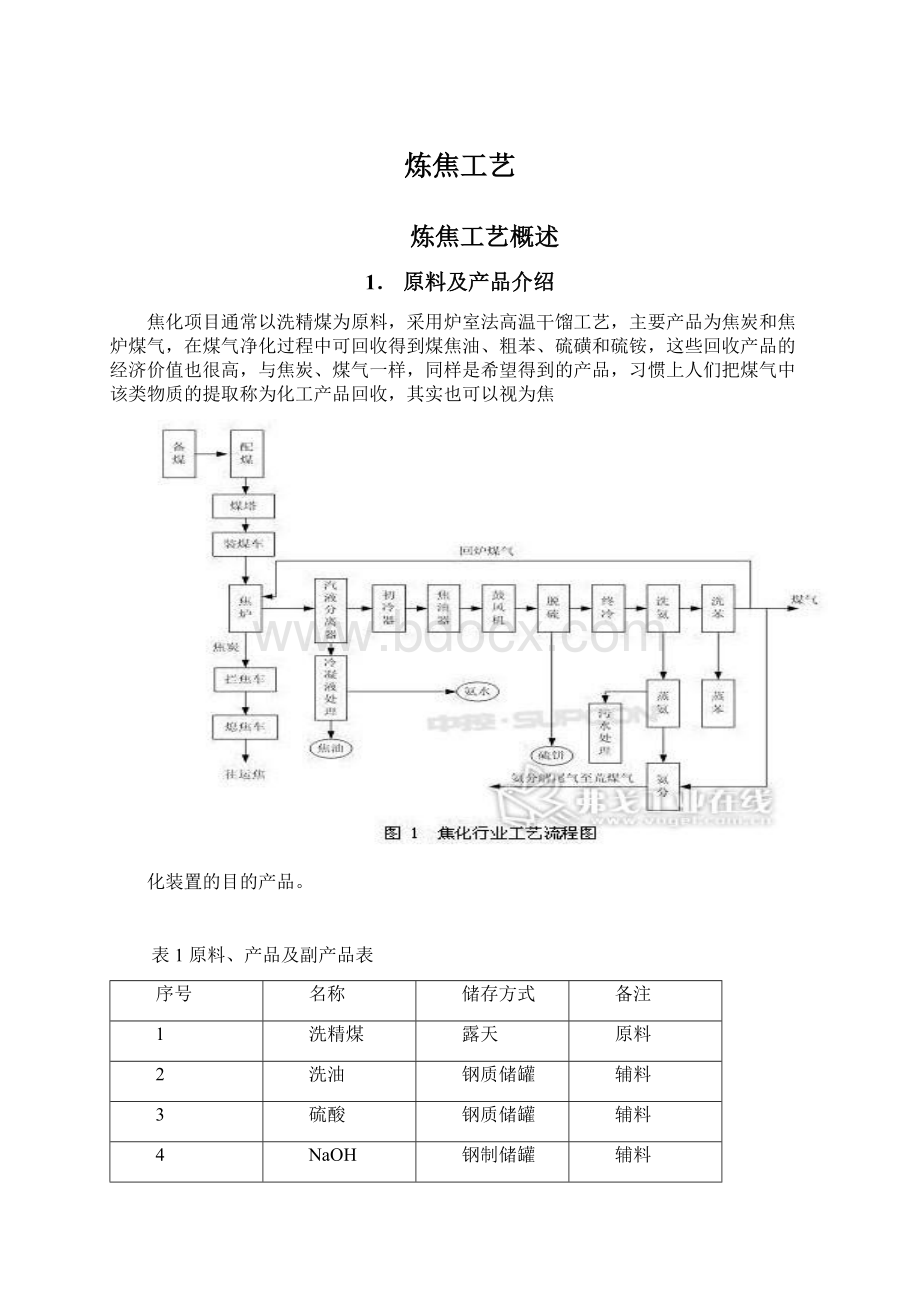
炼焦工艺
炼焦工艺概述
1.原料及产品介绍
焦化项目通常以洗精煤为原料,采用炉室法高温干馏工艺,主要产品为焦炭和焦炉煤气,在煤气净化过程中可回收得到煤焦油、粗苯、硫磺和硫铵,这些回收产品的经济价值也很高,与焦炭、煤气一样,同样是希望得到的产品,习惯上人们把煤气中该类物质的提取称为化工产品回收,其实也可以视为焦
化装置的目的产品。
表1原料、产品及副产品表
序号
名称
储存方式
备注
1
洗精煤
露天
原料
2
洗油
钢质储罐
辅料
3
硫酸
钢质储罐
辅料
4
NaOH
钢制储罐
辅料
5
脱硫剂
袋装
辅料
6
焦炭(干基)
露天堆存
产品
7
焦炉煤气
管道输送
自用或外售
8
煤焦油
钢制储罐
副产品
9
粗苯
钢制储罐
副产品
10
硫铵
袋装码垛
副产品
11
硫磺
袋装码垛
副产品
12
氨水(3~5%)
储槽
中间产品
1、洗精煤
现行我国煤炭分类方法系按煤的煤化程度分为褐煤、烟煤和无烟煤,烟煤包括的品类较多,进一步可按挥发份和粘结指数将烟煤细分为气煤、肥煤、焦煤和瘦煤。
炼焦用煤是一类变质程度中等的烟煤,在行业内规定采用干燥基灰份A/d,硫含量St,挥发份Vdaf,粘结指数G和胶质层厚度Y等指标来评价表征烟煤的工艺性能。
由矿山开采的原煤灰份和硫分往往较大,因此用于炼焦的煤预先进行洗选,以除去原煤中灰份较大的煤矸石、黄铁矿和粘土,原煤经洗选加工后称为洗精煤。
使用单一煤种炼焦,往往难以达到质量、各项性能指标俱佳的冶金焦,在实际生产中,一般将3~6个品种的原料煤按实验选定的比例混配后用于炼焦。
炼焦配煤比根据煤源情况大致比例为:
焦煤75%,瘦煤12.5%,肥煤12.5%,各煤源、煤质指标为下:
表2煤种煤质状况表
煤种
干燥基灰分A/d%
硫含量St%
挥发份Vdaf%
粘结指数G值
瘦煤
13~14
0.6
15~16
45~55
焦煤
12~13
0.6
16~18
80~85
肥煤
11~13
0.6
26~30
85~90
配合煤入炉技术标准为,水分Wt≤10%,挥发份Vdaf20~24%,灰份A/d9~10%,硫份St/d0.6~0.8%,粘结指数G58~72,粒度(<3mm)>80%。
储存:
外采洗精煤由汽车运至储煤场,汽车自卸人工清扫车底,铲车分煤种整理堆存,煤场储煤能力为40天的用量。
2、洗油
煤焦油加工产品,系焦油蒸馏230~300℃之间的馏出物,成分复杂,主要的组份为甲基萘、二甲基萘、联苯、四氢化萘及少量的萘、苊、芴、氧芴等,由于洗油组份皆属芳香烃类,因而对苯族烃具有良好的互溶性,适用于吸收煤气中的苯族烃。
在吸收塔内洗油与煤气逆流接触,煤气中的粗苯转移到洗油中,吸收了粗苯的富洗油被加热后粗苯又从富洗油中脱出,实现了煤气中苯族烃的回收。
储存:
洗油自煤焦油加工企业购得,汽车槽车运抵厂内,经泵将外进新鲜洗油导入洗油槽,洗油无腐蚀性,常温下蒸汽压很低,使用一般钢制设备装储即可满足要求。
运行中,洗油会有一定量的消耗,新洗油及时补充。
3、硫酸
用以吸收煤气中的氨,在硫铵工段,于硫铵饱和器内使含氨的煤气与喷洒的硫酸相接触,硫酸与氨反应生成硫酸铵,并从饱和液中结晶析出,再经过滤干燥制成硫铵产品。
工业硫酸包括浓硫酸和发烟硫酸两大类,焦化项目一般使用98%的浓硫酸。
储存:
浓硫酸可与黑色金属反应在金属表面形成致密的钝化膜,钝化膜可阻止硫酸继续反应深入腐蚀金属本体,实验证明,浓度在70%以上的浓硫酸可以稳定的储存于碳钢容器内,浓硫酸应避免与有机物、金属粉末等接触,禁止在储存硫酸的容器附近抽烟或动用明火。
4、氢氧化钠(液碱)
在废水蒸氨过程中加入一定量的氢氧化钠,以分解其中的固定铵(不挥发性铵),市售液体烧碱依其所采用的生产工艺、设备类型不同有30%、42%、45%等数种浓度不同的商品。
焦化项目一般采用30%氢氧化钠溶液。
储存:
氢氧化钠属强碱性物质,对玻璃、陶瓷类材料有腐蚀作用,适宜储存在普通钢制容器内。
5、脱硫剂
选用FAS法脱硫,所用的脱硫催化剂是NCA-2型镍催化剂,在催化剂下部放置了100mm厚、直径50mm的Al2O3惰性球,作为催化剂的支撑,以防止催化剂从格栅上跌落,镍催化剂层的高度为2200mm。
Al2O3惰性球以袋装形式购进,一般购进后立刻装入克劳斯炉内。
6、焦炭
焦炭主要用于高炉冶炼,其次用于铸造、合成造气、有色金属生产、炼制电石等。
冶金焦在焦炭品种中质量要求最高,依据可供煤源的现实情况,产品规格及质量指标执行有关国家标准。
冶金焦执行GB/T1996-2003的二级标准。
储存:
成品焦炭需保持干燥,含水量稳定,避免雨淋,水浸和粘污,在钢铁联合企业内,焦炭随产随用,无需待销存储,通常把焦炭暂存于焦仓内,再由仓底的漏咀装车,或投放到运输带上输走,实现“不落地”输送。
对于多数非钢铁企业的焦化厂,一般设有地面硬化的储焦场,焦炭堆存在露天的或设有顶棚的堆场内。
7、焦炉煤气
煤干馏过程中的挥发性产物,未净化的煤气称为荒煤气,净化回收后的煤气称为净煤气。
焦炉煤气的主要组分如下
表2焦炉煤气组成主要成分表
组分
H2
CO
CO2
N2
CH4
CnNm
O2
体积分数%
55~59
6~8.5
1.5~2.5
3~3.5
24~26
2.0~2.5
0.3~0.8
初出焦炉的荒煤气,除主要组分外,尚含多种少量组分。
表3荒煤气少量组分(杂质)表
组分名称
水蒸气
焦油气
苯族烃
氨
硫化氢
氰化物
萘
其他
含量/g·m~3
205~450
80~120
30~45
8~12
6~20
1~2.5
10
2.5~3.1
焦炉煤气的产生量与炼焦煤种、焦炉炉型有关,一般而言,每吨干煤产生量在300~450Nm3之间,大部分工程设计吨干煤产煤气304Nm3,在焦化厂,焦炉所产煤气一般要有40~50%用做焦炉自身加热的燃料,称为回炉煤气。
储存:
焦炉煤气不便也不可能大量储存,多数情况下,根据煤气用户的耗气量和用气规律,为了峰谷调节,建有适当能力的储气柜。
8、煤焦油
煤焦油于成焦阶段从炉内煤饼中产出,在集气管内遇喷洒氨水急冷,由气态凝为液滴,在煤气-氨水分离器、初冷器、电捕焦油器等设备处收集后,送入焦油氨水澄清分离槽,与氨水、焦油渣分离后得到。
焦油的产率、组成与所用煤种、炉型、操作条件有关,焦油产率以入炉干煤计在2.5~4.5%之间,煤焦油应符合YB/T5075-93标准。
储存:
煤焦油常温下为稠厚液体状态,对金属材料腐蚀性小。
可采用普通碳钢储罐或防渗混凝土储罐贮存,储槽上需装备用于加热焦油的换热部件,排出滗析水的切水部件和清渣门,它们的作用分别是:
换热部件使热媒对焦油加热,使其保持好的流动性便于取出输送;切水部件的作用是排出浮于焦油油面上的游离水,焦油存放过程中原悬浮包存在焦油中的水滴会部分析出,水比焦油轻,浮于油面上,不便从油罐底阀排出,需在油罐上部筒壁上设置切水部件;至于清渣门,因为焦油中不可避免的会夹带少量的煤粉和焦粉,同时也有部分不饱合组分在贮存期间发生聚合生成树脂状聚合物,这些物质沉积在罐底,需定期机械方式清理,因此需在油罐底部设有方便进出,清渣、排渣用的人孔或大法兰盲板(清渣门)。
9、粗苯
粗苯系煤气中的苯族烃,在洗脱苯工段,经溶剂洗油从煤气中吸收,再将吸收了苯族烃后的富洗油加热蒸馏使苯族烃从溶剂中脱出,冷凝收集而得到粗苯,粗苯各组分大致组成见下表:
表4粗苯各组分平均含量表
序号
组份名称
含量%
序号
组份名称
含量%
1
苯
55~70
10
氧茚
0.6-2.5
2
甲苯
12~22
11
茚
1.5~2.5
3
二甲苯
2.6~6.0
12
二硫化碳
0.3~1.5
4
三甲苯
2.0~5.0
13
噻吩
0.2~1.0
5
乙苯
0.5~1.0
14
甲基噻吩
0.1~1.0
6
C9芳烃
0.08~0.2
15
吡啶类
0.1~0.5
7
C5~C8烯烃
0.5~1.2
16
酚类
0.1~0.6
8
环戊二烯
0.5~1.0
17
萘
0.5~2.0
9
苯乙烯
0.5~1.0
18
饱和脂肪烃
0.5~0.8
粗苯应执行行业标准《焦化粗苯》(YB/T5022-1993)。
储存:
粗苯可储存在钢制的容器内,粗苯为易燃液体,挥发性较强,罐上装有呼吸阀、阻火器、固定式泡沫灭火设施以及淋水降温设施;粗苯容易产生静电和静电积聚,在储罐结构设计、安装施工和工艺操作均采取相应的防雷、防静电措施。
10、硫铵
通常采用硫酸吸收法(化学吸收)脱除煤气中的氨,反应生成的硫酸铵经饱和结晶、过滤分离、流化床干燥后制成硫铵产品,产品执行国家标准《硫酸铵》(GB535-1995)一级品标准。
储存:
硫铵为细小颗粒状结晶,溶于水后显酸性,对碳钢有腐蚀作用,产品使用防潮衬膜编织袋包装,码垛存放。
该工程在硫铵工段建有产品仓库,库房为封闭式建筑,阴凉通风,防晒,防雨淋,防水浸。
11、硫磺
脱酸塔顶逸出的带有硫化氢的酸性气体进入克劳斯炉,1/3的酸性气体燃烧生成SO2与2/3酸性气体中的H2S反应,在一定量的焦炉煤气和空气助燃的情况下,经克劳斯炉的燃烧器燃烧后产生过程气。
过程气中的硫化氢及二氧化硫在炉内催化剂的作用下经克劳斯反应生成元素硫,经过配置在克劳斯炉后面的废热锅炉部分硫磺被冷凝下来,然后过程气依次进入装有催化剂的Ⅰ段反应器和Ⅱ段反应器,并在其中生成硫磺,硫磺经硫冷凝器冷却分离后经液封槽流入硫池,硫池内的液态硫用浸没式泵抽送至硫磺结片机制成固体状硫磺,其纯度可达99.7%。
固体片状硫磺以商品出售。
储存:
袋装码垛存放。
2.工艺概述
焦炭是煤干馏的产物,在高炉冶炼过程中起着还原剂、热源和支撑作用。
炼焦过程从配煤工序开始,选用多种不同工艺性质的煤种按一定比例进行调配,并经调湿、粉碎,制备成为符合炼焦工艺要求的配合煤。
配合煤在隔绝空气条件下,在焦炉中加热至950~1050℃,经高温干馏生产焦炭。
焦炉是一座由列阵式炉室及火道组成的耐火材料砌筑体,受热后的配合煤在不同温度下发生一系列的分解、裂解、缩合、缩聚、塑化、黏结、浸润、挥发、析出等复杂的化学、物理变化,生成焦炭和气体挥发物,该气体挥发物称荒煤气。
荒煤气经过冷却、除尘、化学吸收、溶剂洗涤等操作以回收其中的煤焦油、硫、粗苯,并脱除粉尘、油雾、硫化氢和氨。
净化后的煤气部分供做焦炉加热的燃料或外售。
焦化工程主要由配煤、炼焦、煤气净化等生产车间组成,各主要生产车间的基本工艺过程简述如下:
2.1配煤车间
配煤车间主要工艺过程是将外来炼焦用煤进行接收、储存,并加工成符合焦炉生产要求的装炉煤。
该车间由受煤工序、贮煤工序、配煤工序、粉碎工序、贮煤塔及相应的带式输送机和转运站等组成,并设有推土机库、煤焦制样室等辅助生产设施。
1)受煤工序
炼焦用煤采用汽车运抵厂内。
汽车运入的炼焦煤采用自卸车至汽车受煤坑或煤场,受煤坑下部出口采用往复式给料机将煤卸到带式输送机上,直接送入配煤槽内;卸入煤场内的原料煤按煤种经铲车分别整理堆存。
2)贮煤工序
炼焦煤在贮煤场贮存使其煤质均匀并达到脱水目的。
贮煤场堆取料采用装载机作业,贮量一般为20万吨,约为焦炉40天的用煤量。
煤场内设喷洒装置,定期对煤场进行喷水抑尘,在煤场两端还设有煤泥沉淀池,防止煤泥外排。
3)配煤工序
配煤工序通常设有直径为8m的双曲线斗嘴圆筒仓,圆筒仓下部设置了铁质锥形漏斗,以方便控制圆筒仓内煤粉下落速度,每个漏斗外部设置4个空气炮,作用是将粘连在漏斗内壁上的煤粉震落,漏斗底部设电子自动配料称,根据配煤试验确定的配比将各种炼焦用原料煤自动投放到输送带上,配合后的炼焦煤由带式输送机送至粉碎工序。
4、粉碎工序
由配煤工序运来的配合煤,先经除铁装置将煤料中的铁杂质吸净后,进入可逆反击锤式粉碎机进行粉碎,粉碎机单台能力为400~450t/h,配合煤粉碎细度要求小于3mm的颗粒达到80%以上,通过通廊及转运站由带式输送机输送至贮煤塔顶,经可逆回转布料机布入贮煤塔,准备入焦炉。
配煤车间工艺流程见下图。
高炉用冶金焦要求具有足够的强度、耐磨性、反应后强度,以及尽可能低的灰分、硫分和高的含碳量。
单品种煤源很难满足高质量的综合要求;另一方面,适合炼焦的烟煤在全世界范围内都比较短缺,所以现代炼焦企业无一例外的均采取多种不同煤化程度的煤,科学配比,并在入炉前进行工艺技术处理。
表5配煤先进技术列比选择表
项目
主要内容及特点
卸煤
采用机械方式,消除或尽量减少人工的卸煤。
可选卸煤机械有翻车机、堆取料机、螺旋卸车机、龙门吊车、铲车等。
贮煤
(1)封闭式仓筒,分煤种储存。
可消除储煤中风吹扬尘及雨淋塌堆,造价高。
(2)露天不同煤种分别堆放,煤场四周设防风网或水幕,防止煤尘扬起及飘散
(3)露天不同煤种分别堆存。
四周设喷洒抑尘水管及防细煤外流的挡水沟,防尘墙,经济实用,抑尘效果较好。
配煤
电子称配煤,保证最佳技术经济效果。
粉碎流程
(1)混合粉碎,
特点:
工艺过程简单,设备少,无碎后混合设备,但不同硬度的煤破碎程度不一致。
(2)分级粉碎。
将各单煤种先粉碎后,再按配比混合。
特点:
可按煤种硬度分别控制粉碎细度,有利焦炭质量,但过程复杂,设备台数增加。
煤料输送
(1)带式输送机封闭通廊,连续作业
(2)人工或机械搬运特点:
劳动强度大,作业环境差
2.2炼焦车间
炼焦采用捣固煤饼入炉炼焦工艺。
包括装煤、干馏(焦化)、出焦、熄焦、筛焦工序。
1)装煤工序
由配煤车间送来的配合煤装入煤塔,通过摇动给料器将煤装入捣固装煤车的煤箱内,用捣固锤将煤捣固成煤饼,由捣固装煤车按作业计划从机侧炉门送入炭化室内。
煤饼在炭化室内经过一个结焦周期的高温干馏炼制成焦炭并产出荒煤气。
2)干馏
炭化室中混合精煤由两侧燃烧室进行干馏加热,在350~500℃时,煤中脱质形成气、液、固三相共存胶质体,温度继续升高后液态产物继续分解,一部分呈气态析出,一部分则与固态颗粒融为一体。
当超过胶质体固化温度时,发生粘结并形成半焦,温度继续升高后,半焦内的有机质进一步分解,当超过650℃时半焦阶段结束,超过750℃后有机质全部成为固态物,炭网增大,并向石墨化结构发展,多孔体变紧,变硬形成焦炭。
煤在干馏过程中产生的荒煤气汇集到炭化室顶部空间,进入上升管,经桥管汇入集气管,800℃左右的荒煤气被桥管集气管内喷洒的氨水冷却到84℃左右。
荒煤气中焦油被冷凝下来。
煤气和冷凝下来的焦油同氨水一起,经吸煤气管道进入化产回收车间进行煤气净化及化产品的回收处理。
焦炉加热采用自产焦炉煤气,由焦炉地下室煤气管道分配后直接送入燃烧室,与从废气开闭器进入的空气汇合燃烧。
燃烧后的废气通过立火道顶部跨越孔进入下降气流的立火道,再经过蓄热室,由格子砖把废气的部分余热回收后,经过小烟道、废气交换开闭器、分烟道、总烟道、烟囱,最后排向空中。
焦炉烟囱通常高110m。
3)出焦、熄焦
炭化室的焦炭成熟后,由机侧推焦机摘掉炉门,然后由推焦机推焦杆将炭化室中焦炭向焦侧推出,成熟的焦炭用推焦机推出,经拦焦车导入熄焦车,熄焦车由电机车牵引至熄焦塔内进行喷水熄焦。
熄焦后的焦炭卸至晾焦台,在焦台补充熄焦并晾干后利用自动刮板机放焦,进入焦炭胶带输送机送筛、贮焦工序。
4)筛焦工序
筛焦即将熄焦后的焦炭,按要求筛分成不同粒级,贮存待运。
筛焦工序由筛焦楼、贮焦槽、贮焦场以及相应的带式输送机和各转运站等设施组成。
湿熄焦后的焦炭经焦台送往筛焦楼,在筛焦楼内通过多层振动筛分成<10mm、10~25mm、25~40mm、>40mm四级后,分别运至贮焦场,并通过汽车外运销售。
炼焦车间工艺流程见下图。
炼焦技术的发展趋势主要体现在以下几个方面:
1、在保证和提高焦炭质量的同时,节省优质焦炭的用量,扩大炼焦煤炭源及合理利用,开发了入炉煤预热、捣固、配型煤、配添加剂等炼焦煤料的预处理技术;
2、节约能源和提高能源利用效率的技术,焦炉是焦化厂的核心设备,炼焦的能量消耗85%以上是用在焦炉的加热上,大容积焦炉不仅可以提高劳动效率,在能量消耗定额上也有明确的降低,另一方面是加强废热的回收,成型的焦炭红热状态下出炉时带走的热能要相当于加热耗能的40%以上,干熄焦可回收红焦热量的80%。
3、环境保护和污染物的控制,由于固体物料的处理过程很难做到完全密闭,尤其在装煤和生产过程中伴随产生大量的烟尘,是造成炼焦生产高污染的主要原因,采用大功率风机,设置适当的收尘、集尘和除尘设施,实现装煤和推焦过程扬尘的有效控制。
表6炼焦先进技术列比选择表
技术项目
主要内容及特点
炼焦煤预处理
1)捣固炼焦技术,配合煤在捣固机内经过锤头分层压实捣固后,推入炭化室炼焦。
特点:
煤料经捣固密度增加,提高了粘结性,可在保证焦炭质量的前提下,多用品级较低的气煤,扩大了可用炼焦煤的资源。
同时具有焦炉生产能力增加,工艺简单,投资少,见效快的优点。
2)煤预热炼焦技术:
入炉煤在惰性气体中快速加热到150~250℃后快速装煤,入炉煤堆密度比湿煤提高10~15%。
特点:
改善焦炭质量增加气煤用量;生产能力提高固密度增加,结焦期间缩短能力提高30~50%,降低炼焦能耗,减轻环境污染。
但装炉技术要求高,难度大,投资和操作费用较高。
3)配型煤技术:
将一部分入炉煤加入粘结剂加压成块,然后按比例与散装煤混入装炉。
特点:
可改善煤的结焦性,配煤在结焦阶段膨胀压力显著提高,使煤粒紧凑,焦炭结构坚实,散煤比例减少,使焦炭裂纹减少;因型煤粘结剂的加入改善了粘结性,提高了焦炭强度。
但使用设备较多,投资明显增加。
焦炉结构
1)炭化室高度:
是衡量焦炉技术水平的主要指标,高炭化室代表炉容大,产量高,节约能源。
顶装焦炉炭化室高度国外已有7.85m炉型投用,国内也出现7m以上的焦炉,捣固装煤存在煤饼散塌的问题,已成熟定型的捣固装煤焦炉炭化室高度4.35m,高5.5m的焦炉已设计定型,建成投产。
2)配有蓄热室:
完成焦炉加热后的废烟气在排空前,对其显热进行蓄热式回收,提高能源利用率。
3)硅砖耐火材料:
炭化室内墙使用硅砖,具有更高的耐火温度,可缩短结焦时间,焦炭密度增加,挥发份降低,质量提高
4)燃烧室双联火道,废气循环,煤气下喷,煤气、空气比例流量计算机控制
装煤及出焦除尘
在装煤及出焦操作时段,炉门需开启,并仍有煤焦落料发生,出炉煤的分解以及落料的诱导气流作用,使烟尘产生并逸散,是炼焦过程最主要的污染物发生源。
1)地面除尘站:
在炉顶产尘部位设置移动式集尘罩,经过用自动接口装置与集尘干管连接,地面设大功率风机抽吸,将含尘烟气引入过滤式除尘器,滤除尘粒后废气排空。
特点:
装煤及出焦时的挥发性烟尘得到有效控制,无组织排放量基本消除,除尘效率高,烟尘去除率98%以上,是目前焦炉烟尘控制治理最有效的技术。
但投资较大,运行费用高。
2)消烟除尘车技术:
炉顶消烟除尘车,将装煤时所产生的烟尘自排烟孔吸入除尘车,经煤气焚烧烟气中的有机物,文丘里除尘器中射水捕尘后放空。
特点:
简单易行,投资少。
但该技术仅有装煤除尘,出焦产尘无控制,且烟气发生高峰时消烟除尘效果不理想。
熄焦
出炉的红焦进行冷却至常温称为熄焦,冷却过程避免氧化烧损。
1)干熄焦技术:
利用惰性气体熄灭赤热焦炭的方法。
以惰性气体冷却红焦,吸收了红焦热量的惰性气体作为二次能量在换热设备中放出热量,转变成电能,惰性气体循环使用。
特点:
提高焦炭质量:
焦炭的机械强度、耐磨性、筛分组成、反应后强度均有明显提高;节能及经济效益明显,每吨焦炭回收热量可产生0.5吨,温度450℃,压力3.9MPa中压蒸汽,可发电116kWh,但投资巨大,技术复杂,操作管理水平要求很高。
2)湿法熄焦技术:
出炉红焦上喷水熄灭和冷却。
特点:
操作简单,投资省,熄焦效果可靠,易掌握。
与干熄焦相比,红焦热量不能回收,耗水量较大。
2.3化产回收车间
化产回收车间包括冷鼓电捕工序、脱硫工序、硫铵工序、洗脱苯工序。
冷鼓电捕工序采用两段冷却的横管初冷器冷却和电捕焦油器捕集焦油雾;脱硫工序采用FAS脱硫工艺;硫铵工序采用喷淋式饱和器法;洗脱苯工序煤气脱苯采用洗油洗苯工艺,富油脱苯采用管式炉加热及带萘油侧线的单塔生产粗苯工艺。
各工序工艺流程简述如下:
1)冷鼓电捕工序
该工序包括焦炉荒煤气的两段间壁式初步冷却、煤气电捕除焦油、煤气输送及焦油、氨水分离等工艺过程。
来自焦炉800℃的荒煤气与焦油、氨水沿吸煤气管道至气液分离器,气液分离后荒煤气由上部导出来,进入横管初冷器,初冷器依冷媒温度不同分为上、下两段冷却,上段用32℃循环水间接冷却至43~45℃,下段用16℃低温水将煤气冷却到21~22℃。
由横管初冷器下部引出的煤气,进入电捕焦油器,除掉煤气中携带的焦油,再由煤气鼓风机压送到硫铵工序。
由气液分离器分离下来的焦油和氨水混合液首先进入机械化焦油氨水澄清槽,在此进行氨水、焦油和焦油渣的分离。
上部的氨水流入循环氨水中间槽,再由循环氨水泵送至焦炉系统,分别用于冷却出炉的高温荒煤气,剩余氨水送入剩余氨水贮槽,用剩余氨水泵送至进蒸氨工序。
澄清槽下部的焦油经液位调节器控制流入焦油槽。
机械化焦油底部沉降的焦油渣经槽底缓缓移动的刮板刮至焦油渣车,定期送往配煤系统,掺入炼焦煤中。
2)脱硫工序
该工序包括煤气的硫化氢洗涤、脱氰脱酸、硫磺回收、尾气洗涤、蒸氨等工艺过程。
(1)硫化氢洗涤
来自电捕焦油器温度约25~30℃的煤气进入脱硫塔。
脱硫塔由下部的预冷段、中部的脱硫段和顶部的碱洗段组成。
进入脱硫塔煤气在预冷段冷却至22℃后进入中部的脱硫段。
从脱硫塔出来的140℃贫液先经贫富液换热器与富油换热,贫液温度从140℃冷却至60℃~70℃后进入贫液槽。
再经贫液泵抽出,经一段贫液冷却器用循环水冷却至40℃.部分贫液作为冷料送至脱酸塔顶;另一部分贫液经二段贫液冷却器用制冷水冷却至22℃后送往脱硫塔的脱硫段喷洒。
为了吸收脱硫段产生的反应热,设置了中段循环冷却器。
脱硫液用泵抽出,经冷却器冷却后送回脱硫段喷洒。
吸收了硫化氢的富液,从脱硫塔满流至富液槽。
脱硫塔的顶部设有碱洗段,用碱液循环泵循环喷洒,碱液循环量约为100m3/h。
用浓度为30%~40%碱与软水在配碱槽中配成浓度为10%~20%的碱液。
脱硫塔顶部碱洗段的液位调节由送往蒸氨工段的碱量来控制。
送往蒸氨工段的碱量是有分解剩余氨水中的固定铵所需减量决定。
通过计量泵将碱液补充到循环系统。
配碱槽设有高液位报警。
从蒸氨工段来的氨气送往脱硫塔的入口煤气管。
从贫液泵出口的支管到焦油氨水分离槽作为系统的排污。
贫油槽的液位靠补充的软水量用调节阀控制,以确保整个系统的水平衡。
补充的软水量由中控室显示记录。
脱硫塔后的富液从脱硫段自流入富液槽,富液用富液泵抽出分两系送往脱氰脱酸工序。
(2)脱氰脱酸
从硫化氢洗涤装置控制的富液,通过与脱酸塔低热贫液换热至125℃,再经富液加热器用蒸汽加热至140℃后进入脱氰反应塔。
在脱氰反应塔内,富液中的氰化氢按下式反应水解为甲酸和氨。
HNC+2H2O→HCOOH+NH3(放热反应)
脱氰效率可达85%~90%,使塔后富液中的HCN浓度下降到0.2g/L以下进入脱酸塔。
140℃的富液从脱氰反应塔顶送至脱酸塔中部。
脱酸塔在0.25~0.30MPa(表)压力下操作。
脱酸塔进料口以下为汽提段,塔底设有再沸器,用大于0.8MPa的蒸汽加热,脱酸