中国计量学院质量管理软件实习报告1分析.docx
《中国计量学院质量管理软件实习报告1分析.docx》由会员分享,可在线阅读,更多相关《中国计量学院质量管理软件实习报告1分析.docx(19页珍藏版)》请在冰豆网上搜索。
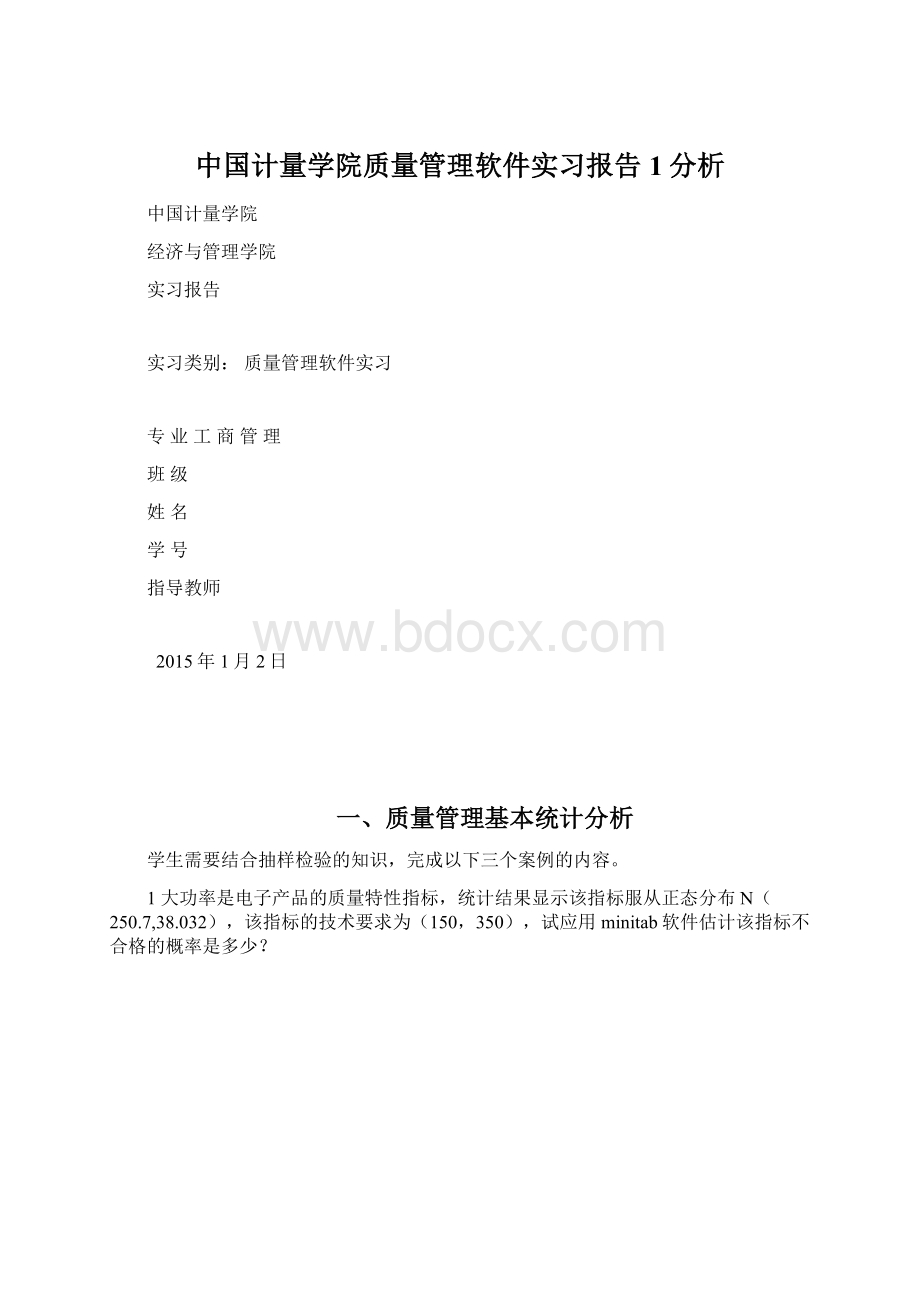
中国计量学院质量管理软件实习报告1分析
中国计量学院
经济与管理学院
实习报告
实习类别:
质量管理软件实习
专业工商管理
班级
姓名
学号
指导教师
2015年1月2日
一、质量管理基本统计分析
学生需要结合抽样检验的知识,完成以下三个案例的内容。
1大功率是电子产品的质量特性指标,统计结果显示该指标服从正态分布N(250.7,38.032),该指标的技术要求为(150,350),试应用minitab软件估计该指标不合格的概率是多少?
2现有批量为N=1000的一批产品,采用抽样方案(10,1)进行抽检,再假设此产品不合格品率为5%。
试应用minitab软件估计这批产品被判为接收的概率是多少?
③某产品有26个指标,如Beta1、Vbe1等,历史数据表明平均每百单位产品出现不合格0.5个。
现用抽样方案(100,2)检验,试应用minitab软件估计该批产品被判为接收的概率是多少?
或随机抽取100个产品,出现2个以下不合格的概率是多少?
由软件可以判断以样方案(100,2)检验,该批产品被判为接收的概率是0.985897。
二、质量管理常用工具应用与分析
1.排列图(案例2)
某精密铸造机匣小组一周的质量不良项目有:
表面疵点、气孔、未充满、形状不佳、尺寸超差及其他等项,其缺陷记录如下表所示,试进行计算并做排列图。
表2-1缺陷记录表
缺陷项目
频数/个
疵点
41
气孔
18
未充满
13
形状不佳
10
尺寸超差
6
其他
7
合计
95
试制作频数统计表,并进行排列图分析。
表2-2频数统计表
缺陷项目
频数/个
频率/%
累计频率/%
疵点
41
0.43
0.43
气孔
18
0.19
0.62
未充满
13
0.14
0.76
形状不佳
10
0.11
0.86
尺寸超差
6
0.06
0.93
其他
7
0.07
1.00
合计
95
1.00
表2-3缺陷记录的排列图
疵点、气孔、未充满在0~80%间,是关键因素,形状不佳在80%~90%间是重要因素。
一般因素是尺寸超差和其他。
要提高产品质量,必须从疵点、气孔、未充满这三个方面下手。
2.直方图(案例1)
某公司收集到的某产品质量特性数据见下表所示,其样本大小为n=100。
表2-4质量特性实测数据表
6
50
55
55
50
44
38
5
50
52
48
52
52
52
48
55
45
49
50
54
45
5
55
60
55
56
43
47
5
43
54
53
45
43
48
43
45
43
53
53
49
47
48
4
50
47
48
54
5
43
45
54
55
55
47
63
50
49
55
60
45
52
47
55
55
56
50
46
45
47
依据收集的数据制作直方图,并对图形进行分析,指出所做图形属于哪种典型形状,并说明可能的原因是什么?
并通过相应的直方图指出平均值是多少,第一四分位数、第三四分位数分别是多少?
表2-4质量特性实测
该图形是折齿形。
这多数是因为测量方法或读数有问题。
也可能是作图时数据分组不当引起的。
均值是50.05.第一四分位数、第三四分位数分别是47,54
3.散点图(案例2)
某化工产品的反应温度和收率之间有一定的关系,收集的数据如下表。
序号
x(℃)
y(收率%)
49.2
16.7
50.0
17.0
49.3
16.8
49.0
16.6
49.0
16.7
49.5
16.8
49.8
16.9
49.9
17.0
50.2
17.1
50.2
17.1
请制作散点图,并说明属于典型形状中的哪种典型类型?
并进一步进行回归分析,建立一元回归模型,并预测当反应温度为50℃时,化工产品的收率在显著性水平α=5%时置信区间。
图2-5反应温度和收率之间的散点图
X,Y是强正相关。
当鼠标接近回归线,得到它的回归方程是:
Y=-1.413+0.3685X(℃)当反应温度为50℃时,化工产品的收率在显著性水平α=5%时置信区间为(16.9780,17.0494)
三、正交试验设计应用与分析
(1)熟悉minitab软件的常用菜单,尤其是DOE菜单;复习质量管理知识中试验设计技术,尤其是正交试验设计。
(2)学生可以从试验设计备选案例中任选1个案例,也可以自主设计一个案例,如榨苹果汁案例,或者通过其他途径另外寻找一个案例,并进行试验设计。
对于自主设计或另外寻找的案例,评分时根据选择案例的质量给予适当加分。
(3)对试验结果分别采用极差分析、方差分析、信噪比分析,并确定最佳的因素水平组合。
1.试验设计(案例1)
设计某电感电路,此电路由电阻R(欧姆)和电感L(亨利),Cd为输入电压V(伏特),输出电流的强度y,规格要求电流强度m=10±4A。
影响电感电路输出电流强度y的因素水平确定。
据经验和技术,R的优选范围为0-10Ω,取三个水平:
0.5Ω,5.0Ω,9.5Ω;电感L的优选范围为0-0.03H,取三个水平:
0.01H,0.02H,0.03H;电源电压的优选范围为50-150V,取三个水平50V,100V,150V。
试验设计及试验结果见下表所示。
试验序号
A(电阻R)
B(电感L)
C(电压V)
D
y1
y2
y3
1
1
1
1
1
13.6
12.8
13.7
2
1
2
2
2
11.2
10.9
10.6
3
1
3
3
3
7.2
8.4
8.9
4
2
1
2
3
10.8
9.2
10.1
5
2
2
3
1
9.0
9.8
10.3
6
2
3
1
2
8.0
8.6
8.9
7
3
1
3
2
6.7
7.2
7.6
8
3
2
1
3
6.9
7.5
7.8
9
3
3
2
1
6.6
7.1
7.4
先以y1为单试验结果进行极差分析;再以y1、y2、y3为三个试验结果进行信噪比分析。
(1)以y1为单试验结果进行极差分析
图3-1均值主效应图
极差分析:
RA=3.933*3=11.799RB=3.10*3=9.30RC=1.900*3=5.700
所以A因素对结果的影响最大,B因素其次,C因素最后。
输出电流的强度y,规格要求电流强度m=10±4A,属望目特性,所以最好的试验条件是A1B1C3
(2)以y1、y2、y3为三个试验结果进行信噪比分析
表3-2信噪比
分析:
A、B、C中C的信噪比为3.78最大,表示C因素对结果的影响比较小。
所以主要影响因素是A,其次是B,最后是C.信噪比越大越好,所以最佳的试验条件是A1B2C1
四、统计过程控制应用与分析
1.统计过程控制(案例4)
某手表厂为了提高手表的质量,应用排列图分析造成手表不合格品的各种原因,发现“停摆”占第一位。
为了解决停摆问题,再次应用排列图分析造成停摆的原因,结果发现主要是由于螺栓松动引发的螺栓脱落造成的。
厂方决定应用控制图对装配作业中的螺栓扭矩进行过程控制。
测量25个样本的数据如下表。
序号
Xi1
Xi2
Xi3
Xi4
Xi5
1
154
174
164
166
162
2
166
170
162
166
164
3
168
166
160
162
160
4
168
164
170
164
166
5
5
167
6
164
8
7
167
169
159
175
165
8
4
166
9
2
164
1
56
174
11
168
174
166
160
166
12
148
160
162
164
170
153
151
14
164
166
164
170
164
168
172
16
4
152
17
1
168
18
166
166
172
164
162
19
17
60
2
54
160
21
162
164
165
169
153
22
166
160
170
172
158
23
172
164
159
165
160
24
174
164
166
157
162
25
8
170
试通过平均值-极差控制图应用minitab软件进行统计过程控制分析,其中规格界限为160±20。
(1)表4-1控制图
R图检验得出样本点17是不合格点,应剔除。
(2)剔除后,再画R图。
剔除第17个样本点后得到下图:
表4-2控制图
(3)从R图看出个样本点正常,所以绘制下图X图。
表4-3控制图
从Xbar控制图得出结果:
第13个样本点是不合格的,应予以剔除。
(4)剔除后,重新得到新的R控制图和Xbar控制图:
表4-4控制图
(5)过程能力分析
表4-4控制图
由上图可得标准差为5.5,CP=1.20CPK=0.95<1.0处于过程能力判断标准的第四等级,过程能力不足,表示技术管理能力已很差,应采取措施立即改正。
可以采用以下措施:
(1)调整过程加工的分布中心,减小偏移量
(2)从人机料法环这五个方面改进,提高过程能力,减少分散程度。
五、测量系统分析
1.测量系统分析(案例1)
一家公司的质检部门新购买一台测厚仪,在正式使用之前,需要对此测量系统进行评估。
根据实际需要的量程范围,挑选了3个有代表性的标准部件。
然后随机选择3个检验员以随机的方式对每个部件测量3次,测量结果见下表所示。
试对该测量系统进行评估。
部件
操作员
数据
部件
操作员
数据
部件
操作员
数据
3
3
413.75
2
3
386.25
1
3
383.75
3
3
268.75
2
3
478.75
1
3
373.75
3
3
420
2
3
436.25
1
3
446.25
3
2
426.25
2
2
406.25
1
2
388.75
3
2
471.25
2
2
531.25
1
2
157.5
3
2
432.5
2
2
435
1
2
456.25
3
1
368.75
2
1
408.75
1
1
405
3
1
270
2
1
608.75
1
1
273.75
3
1
398.75
2
1
443.75
1
1
476.25
分析:
在方差分析表中,F值越大表明对结果的影响越显著。
部件的F值为2.66887,操作员的F值为0.03618.所以部件对结果影响显著。
合计量具(重复性与再现性之和)的研究变异为91.85%,远远大于30%,所以该测量系统是不靠谱的。
六、综合案例分析
1.综合案例一
某单位拟采购厚度要求为20±4mm的塑料板,这种塑料板的厚度超出规格界限时,造成的损失为100元。
现选择了4家供应商单位进行评价。
分别测量了4家供应商同型号各30个塑料板,这些塑料板都是在生产过程稳定的条件下抽样测量的,测量结果见下表所示。
供应商A
18.65
17.44
18.59
18.15
20.73
16.83
21.36
19.95
18.65
20.94
20.90
21.52
17.82
20.14
17.61
19.02
19.67
20.20
19.54
20.43
20.87
20.09
21.41
21.66
20.78
19.33
19.42
21.24
18.09
20.73
供应商B
18.65
17.38
18.19
19.21
18.63
17.85
17.15
17.62
17.25
17.18
17.67
17.54
17.06
17.51
18.01
17.42
17.74
17.08
17.14
18.79
17.65
18.71
17.75
18.09
17.18
17.28
18.32
18.71
18.18
17.47
供应商C
16.94
16.32
17.67
17.55
17.95
17.27
17.32
17.23
16.94
16.79
16.98
17.40
17.37
16.48
17.05
16.98
17.51
18.17
17.40
16.81
17.21
16.88
17.36
17.01
17.27
17.30
17.44
17.02
17.06
17.36
供应商D
18.79
19.48
19.47
20.10
20.18
20.09
17.62
22.34
24.30
19.03
21.91
21.35
18.08
17.64
19.46
21.99
23.46
20.94
21.60
19.93
18.59
19.71
16.60
21.29
14.77
17.54
17.87
23.52
19.35
20.44
试对上述四家供货商的供货能力进行综合评价。
(1)过程能力分析:
通过下列图可以得出四个供应商
供应商A
供应商B
供应商C
供应商D
均值
19.73
17.8
17.2
19.9
标准差
1.38
0.61
0.38
2.16
CP
0.97
2.18
3.45
0.62
CPK
0.90
0.99
1.04
0.60
PPK
0.91
1.00
1.05
0.61
1、从均值来看,四个供应商都符合了20±4mm的厚度要求。
供应商A供应商D的均值离目标值比较接近。
2、从标准差来看,供应商D的标准差较大,产品比较分散,不稳定。
所以从2、标准差看供应商B、C更优。
3、从CP和CPK看,供应商B、C的偏移量比较大,均超过了1.67。
过程能力过高。
这设备精度的浪费。
如果要考虑选择B、C供应商,可以重新制定标准,以提高产品的质量水平。
4、从CPK、PPK指数看,四个企业的短期过程能力指数和长期过程能力指数没有太大差异,可见能力还是比较稳定的。
5、从以上几个点考虑选择供应商A比较好。
图6-1各个供应商的过程能力分析图
(2)质量损失分析
采用望目特性的质量损失函数计算各供应商的质量损失:
容差Δ=4cm,不合格损失A=100元,
确定系数K:
=100/16=6.25
平均质量损失:
(m为目标值20,n为数值个数30)
通过下表计算可得4个供应商的平均质量损失:
A:
11.81
B:
32.13
C:
49.81
D:
27.75
A供应商的平均质量损失最小,所以选A供应商。
表6-2供应商平均质量损失计算表
总结:
结合以上两种方法的判断,选择供应商A最合理。
2.综合案例二
下表是从某化工企业两个废水排水口各测量20次PH值所得的数据,废水排放PH值要求的范围为6-9。
x
8.25
8.74
8.58
8.64
8.98
8.23
8.19
8.22
8.16
8.44
8.19
8.82
8.04
8.94
8.51
8.36
8.53
8.32
8.08
8.15
y
8.63
7.62
7.65
7.93
8.05
8.34
8.24
8.84
8.84
7.79
8.33
8.64
8.73
8.44
8.09
8.00
8.09
8.16
8.7
8.84
请同学们应用所学质量管理专业知识对上述数据进行分析。
(1)描述性分析:
观察PH值得大致分布情况,判断是否有异常情况不满足PH排放要求
表6-3直方图
两组数据均满足废水排放PH值6-9要求
由X的直方图得出,整个图形的形态是单峰型,过程处于稳定状态,该组数据的均值8.419是标准差是0.2871,数据集中在8.0-9.0之间;虽然。
但是X排放口比较接近临界值9.0,需采取一定的措施,降低污水PH值。
由Y的直方图得出,整个图形的形态是折齿型。
该组数据的均值是8.298,标准差是0.3982,数据集中在7.5-8.75之间。
(2)过程能力分析
图6-4X的过程能力
a)CP=1.72
CPK=0.67
X的CP=1.72是很充足的,但是由于存在偏移量,过程能力指数下降到0.67,造成过程能力不足。
所以企业可以调整过程加工的分布中心,使得分布中心左移消除偏移量,是提高过程能力指数的有效措施。
图6-5X的过程能力
b)CP=1.24
CPK=0.55
X的CP=1.24是很充足的,但是由于存在偏移量,过程能力指数下降到0.55,造成过程能力不足。
所以企业应该调整过程加工的分布中心,消除偏移量。
综上,X,Y均存在较大的偏移量,企业可以通过加酸等方式来调整分布中心,减少偏移量。
尤其是X排放口,需要立即采取措施,否则有可能超出污水排放要求的上限。