4000t分解炉第五次数据校正.docx
《4000t分解炉第五次数据校正.docx》由会员分享,可在线阅读,更多相关《4000t分解炉第五次数据校正.docx(15页珍藏版)》请在冰豆网上搜索。
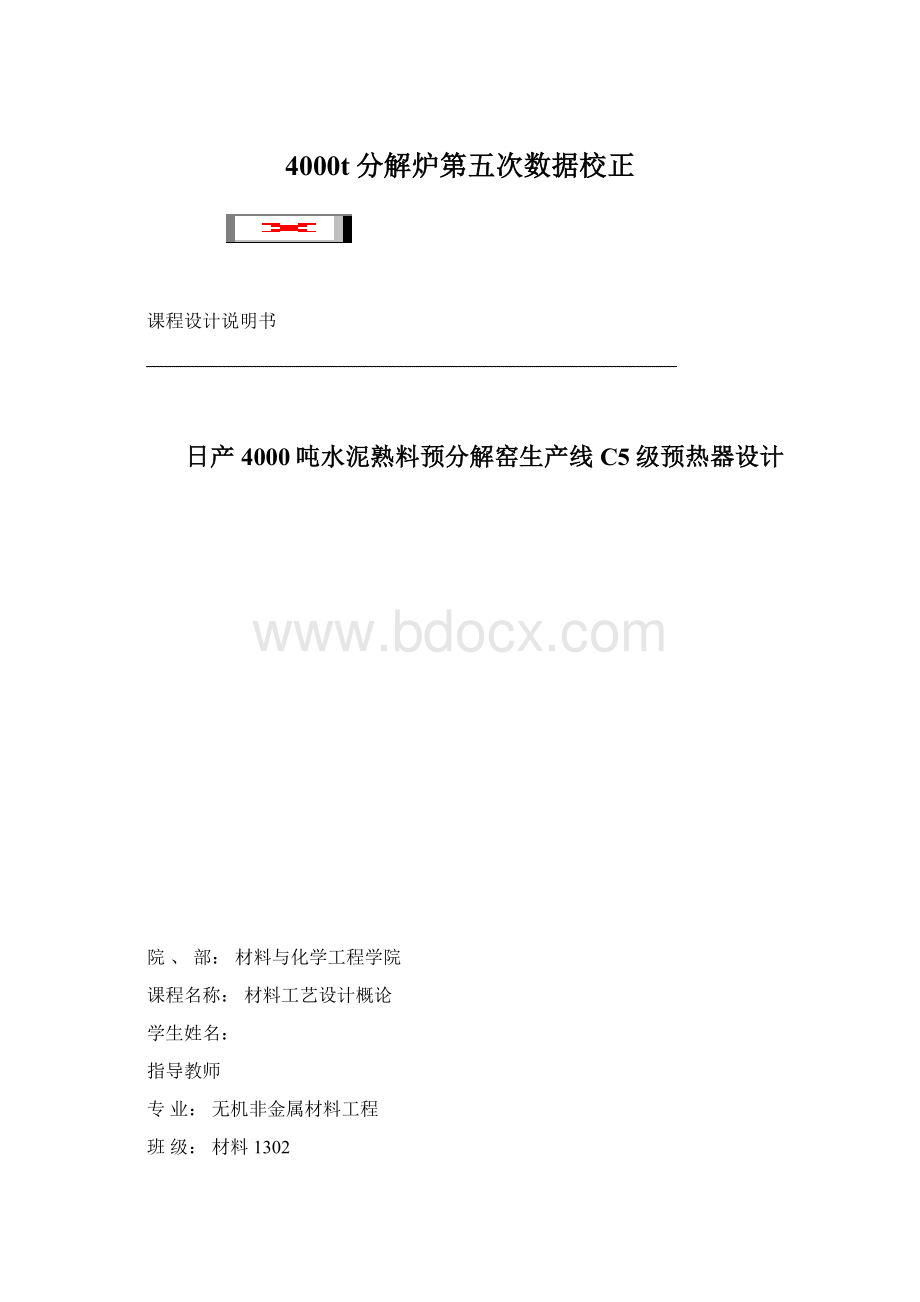
4000t分解炉第五次数据校正
课程设计说明书
日产4000吨水泥熟料预分解窑生产线C5级预热器设计
院、部:
材料与化学工程学院
课程名称:
材料工艺设计概论
学生姓名:
指导教师
专业:
无机非金属材料工程
班级:
材料1302
完成时间:
2016年12月
目录
1、设计任务书...................................................1
2、摘要.........................................................4
3、引言.........................................................4
4、设计方案与指导思想...........................................5
5、设计原始资料.................................................5
6、设计计算.....................................................6
7、窑尾系统简介................................................12
8、参考文献....................................................13
《水泥生产技术与设备》课程设计
任务书(5)
一、设计题目
日产4000吨水泥熟料预分解窑生产线C5级预热器设计。
二、原始资料
1、原材料化学成份
(1)石灰质、粘土质、铁质原料(%)
名称
Loss
SiO2
Al2O3
Fe2O3
CaO
MgO
SO3
Σ
石灰石
39.58
3.39
1.48
0.69
51.25
1.21
97.60
粘土
5.48
66.09
14.41
7.11
2.34
2.30
97.73
铁粉
2.38
36.32
2.68
54.33
0.80
96.51
(2)煤的工业分析(%)及发热量
Mt
Mad
Aad
Vad
Fcad
Qnetad
Qnetar
7.0
1.08
27.94
14.57
57.66
5063
4990
(3)煤灰的化学成份(%)
SiO2
Al2O3
Fe2O3
CaO
MgO
SO3
其它
Σ
43.00
28.99
8.39
6.50
1.06
7.10
4.96
100
2、料耗及热耗
实际料耗:
生产损失为3-5%(具体自行拟定);
烧成热耗:
3100-3170KJ/kg熟料(具体自行拟定);
3、原、燃料水份(%)
煤
石灰石
粘土
铁粉
8.7
1.8
12
9.5
4、当地自然条件
历年平均气温:
18.5℃;相对湿度:
73%;
绝对最高气温:
40.3℃;平均湿度:
79%;
绝对最低气温:
-5℃;常年主导风向:
东南风。
平均气压:
96300Pa。
三、设计内容及设计原则
1、设计内容
日产4000吨水泥熟料预分解窑生产线C5级预热器设计。
2、设计基本原则
(1)在满足工艺要求,确保工艺畅通;
(2)充分考虑安全因素,确保安全生产。
四、设计成果
1、完成设计说明书一份
(1)设计方案与设计指导思想
(2)设计计算部分
1)配料计算(率值自行拟定);
2)生料消耗定额(理论料耗与实际料耗)计算;
3)年产熟料计算(窑年运转率自行拟定);
4)要求窑尾预热器系统废气量计算
依据窑年产量、燃煤等计算系统及各级预热器需处理气体量。
5)各级预热器主要结构参数计算
依据要求各级预热器要求处理废气量及相关参数,计算各级预热器直径、排气管直径等主要结构参数。
6)计算本组设计预热器级数的其他参数:
如预热器直筒高度、锥体结构参数、进口型式与高宽参数、内筒深度等。
2、绘制图纸
(1)C5级旋风预热器结构图,1号图1-2张;
(2)要求:
以全面、准确反映自己所设计部分的内容为准。
五、时间与进度安排
1、设计时间:
2周。
2、进度安排
(1)资料与文献查阅,2-3天;
(2)设计计算与选型,3-4天(两项合计时间1周);
(3)绘图与设计文件整理,1周。
六、分组安排与要求
1、设计班级与分组安排
(1)设计班级:
材料1302班,
(2)分6组,每6人一组。
2、要求
(1)本任务书设计人员为6人,但每人须独立完成第四项设计成果要求的工作;
(2)计算时,各人“自行拟定”参数在本组中不得完全相同,即要求独立完成计算;
(3)各人图纸不得完全相同。
湖南工学院材料教研室
指导教师:
袁龙华
2016年12月
摘 要
预分解窑是新型干法水泥生产线的而一个重要标志,是当代高新技术在水泥工业的集成。
设计的目的之一,就是在保证水泥产量和质量的前提下,提高物料的分解率,缩短物料的分解时间,降低熟料单位热耗等。
本次设计的内容是日产2500吨水泥熟料预分解窑生产线C2级预热器设计。
在设备选用上,尽量选用国内设备以便维修保养方便。
设计的内容具体为:
1.配料计算
2.物料平衡
3.预热器的参数
4.旋风筒的类型
预分解窑系统具有高效率、低能耗、自动化等优点,它是在悬浮预热器和回转窑之间,增设一个分解炉或利用窑尾烟室管道,使燃料的燃烧放热过程与生料的吸热分解过程同时在悬浮态或流化态下极其迅速地进行,因而窑系统的煅烧效率大幅度提高。
该系统目前运用技术已日趋成熟,为大多数大型水泥厂家所接受。
关键词:
配料; 平衡; 分解; 设计; 预热器
引 言
新型干法水泥生产技术是20世纪50年代发展起来,到目前为止,日本、德国等发达国家,以悬浮预热和预分解为核心的新型干法水泥熟料生产设备率占95%,我国第一套悬浮预热和预分解窑1976年投产。
该技术优点:
传热迅速,热效率高,单位容积较湿法水泥产量大,热耗低。
新型干法水泥生产技术的重要标志就是预分解技术诞生和发展。
预分解窑是20世纪70年代发展起来的一种煅烧工艺设备。
它是在悬浮预热器和回转窑之间,增设一个分解炉或利用窑尾烟室管道,在其中加入30~60%的燃料,使燃料的燃烧放热过程与生料的吸热分解过程同时在悬浮态或流化态下极其迅速地进行,使生料在入回转窑之前基本上完成碳酸盐的分解反应,因而窑系统的煅烧效率大幅度提高。
预分解窑法生产具有均化、节能、环保、自动控制、长期安全运转和科学管理六大保证体系,是当代高新技术在水泥工业的集成,其特征如下:
1、生料制备全过程广泛采用现代化均化技术。
使矿山采运-原料预均化-生料粉末-生料均化过程,成为生料均化过程中完整的"均化链"。
2、用悬浮预热及预分解技术改变了传统回转窑内物料堆积态的预热忽和分解方法。
3、采用高效多功能挤压粉磨技术和新型机械粉体运输装置。
根据日本上潼具贞研究空气输送的动力系数μ(指单位时间内输送单位重量物料至单位长度所需动力)是提升机的2-4倍,是皮带输送机的15-40倍。
因此,采用新型机械输送代替空气输送粉体物料,节能是相当可观的。
4、工艺设备大型化,使水泥工业向集约化方向发展。
5、为"清洁生产和广泛利用废渣、废料、再生燃料和降解有毒有害危险废弃物创造了有利条件。
6、生产控制自动化。
7、广泛采用新型耐热、耐磨、隔热和配套耐火材料。
8、应用IT技术,实现现代化管理等。
4、设计方案与设计指导思想
4、1设计指导思想
水泥厂需要用大量的矿物原料如石灰石等,因此水泥厂大都自行开采矿山,并靠近矿源建厂。
水泥工业能耗和电耗较大,因此在水泥厂设计中要注意确保能源供应,并充分重视节约能源的问题。
水泥厂存在粉尘和噪声两大污染。
因此,设计时必须加强收尘措施,尽量搞好厂区绿化。
从发展来看,水泥工业的发展逐渐趋向大型化和自动化。
因此在设计时,应尽量采用新技术、新方案并重点考虑节约能源。
从水泥厂的整体设计来说,工艺设计是主体,它的主要任务是确定工艺流程,进行工艺设计的选型和布置。
但工厂设计是各专业共同完成的一个整体。
因此,工业设计与其他专业的设计有着密切的联系,特别是工艺布置和土建的关系更为密切,生产设备的布置直接影响到建筑物的结构形式和尺寸。
因此,工艺人员只有与其他人员相互配合,共同研究,才能产生较好的方案。
5设计原始资料
(1)石灰质、粘土质、铁质原料(%)
名称
Loss
SiO2
Al2O3
Fe2O3
CaO
MgO
SO3
Σ
石灰石
39.58
3.39
1.48
0.69
51.25
1.21
97.60
粘土
5.48
66.09
14.41
7.11
2.34
2.30
97.73
铁粉
2.38
36.32
2.68
54.33
0.80
96.51
(2)煤的工业分析(%)及发热量
Mt
Mad
Aad
Vad
Fcad
Qnetad
Qnetar
7.0
1.08
27.94
14.57
57.66
5063
4990
(3)煤灰的化学成份(%)
SiO2
Al2O3
Fe2O3
CaO
MgO
SO3
其它
Σ
43.00
28.99
8.39
6.50
1.06
7.10
4.96
100
6设计计算
6.1原料配合比计算
(1)计算煤灰掺入量
GA=QAadS/Qnet.ad×100
GA-熟料中煤灰掺入量;
Q—单位熟料热耗。
Kj/kg;
Aad-煤空气干燥基灰分含量,%;
S-煤灰沉落率,%
Qnet.ad-煤空气干燥基低热值。
Kj/kg煤。
选取单位熟料热耗为3100kJ/kg,S=100.
由此可得煤灰掺入量为GA=QAadS/Qnet.ad×100=3100×27.94/21184=4.09%
6.2率值选择
对于预分解窑都是选择高硅率,高铝率,中配合比的配料方案,取熟料率值为KH=0.87~0.92,SM=2.2~2.6,IM=1.4~1.8
6.3计算干燥原料配合比
假定干燥原料配合比为石灰石82%,粘土质原料14%,铁质原料4%,以此计算生料的化学成分。
表一生料的化学成分(%)
名称
LOSS
SiO2
Al2O3
Fe2O3
CaO
MgO
SO3
石灰石
31.68
2.71
1.18
0.55
41.00
0.97
粘土
0.87
10.62
2.31
1.14
0.37
0.44
铁粉
0.095
1.48
0.11
2.18
0.032
生料
32.65
14.81
3.60
3.87
41.40
1.41
灼烧生料
/
21.99
5.35
5.75
61.47
2.09
煤灰掺入量GA=4.090%,则灼烧生料配合比为100%-4.09%=95.91%。
按此计算熟料的化学成分,见表二。
表二熟料的化学成分(%)
名称
配合比
SiO2
Al2O3
Fe2O3
CaO
MgO
SO3
灼烧生料
95.91
21.21
5.15
5.54
59.29
2.01
煤灰
4.09
1.52
1.03
0.29
0.23
0.038
0.25
熟料
100
22.37
6.18
5.83
59.52
2.05
0.25
则熟料的率值计算如下:
KH=(CaO-1.65Al2O3-0.35Fe2O3-0.7SO3)/2.8SiO2=0.75
SM=SiO2/(Al2O3+Fe2O3)=1.90
IM=Al2O3/Fe2O3=1.05
由上述计算结果可知,KH较低。
SM值较低,IM值较低,增加石灰石的量,调整原料配合比为石灰石83.3%,粘土12.7%,铁矿石4%,重新计算结果如下表
表三重新计算的生料化学成分
名称
LOSS
SiO2
Al2O3
Fe2O3
CaO
MgO
SO3
石灰石
32.90
2.83
1.24
0.38
42.65
1.02
粘土
0.69
8.59
1.79
0.40
0.29
0.34
铁粉
0.10
1.45
0.11
2.18
0.032
0.00
生料
33.69
12.87
3.14
2.86
42.97
1.36
灼烧生料
19.95
4.96
3.44
66.43
2.08
表四重新计算的熟料化学成分
名称
配合比
SiO2
Al2O3
Fe2O3
CaO
MgO
SO3
灼烧生料
95.91
19.89
4.78
3.36
65.10
2.01
煤灰
4.09
1.92
1.03
0.14
0.23
0.037
0.26
熟料
100
21.81
5.81
3.50
65.33
2.047
0.26
则熟料的率值计算如下:
KH=(CaO-1.65Al2O3-0.35Fe2O3-0.7SO3)/2.8SiO2=0.89
SM=SiO2/(Al2O3+Fe2O3)=2.34
IM=Al2O3/Fe2O3=1.66
由上述结果可知三个率值基本达到要求,可按此配料生产,干燥原料配合比为石灰石83.3%,铁矿石4%,粘土12.7%
6.4计算湿润原料质量配合比
原料水分为石灰石1.8%。
粘土12%,铁粉9.5%
湿石灰石=83.3%/98.2%=84.82%
湿粘土质原料=12.7%/88%=14.43%
湿铁质原料=4%/90.5%=4.41%
换算成质量百分比
湿石灰石=81.55%湿粘土质原料=14.12%湿铁质原料=4.33%
6.5生料消耗定额(理论料耗与实际料耗)计算
考虑煤灰掺入量时,1t熟料的干生料理论消耗量:
KT=(100-s)/(100-I)
式中KT——干生料理论消耗量(t/t熟料);
I——干生料的烧失量(%);
s——煤灰掺入量,以熟料百分数表示(%)。
则有:
KT=(100-4.09)/(100-33.69)=1.455(t/t熟料);
考虑煤灰掺入量时,1t熟料的干生料消耗定额:
K生=100K干/(100-P生)
式中K生——干生料消耗定额(t/t熟料);
P生——生料的生产损失(%),一般3%~5%,计算时取4%。
则有:
K生=(100×1.455)/(100-4)=1.516(t/t熟料);
各种干原料消耗定额:
K原=K生×X
式中K原——某种干原料的消耗定额(t/t熟料);
X——干生料中该原料的配合比(%)。
则有K石灰石=1.516×83.3%=1.263;
K粘土=1.516×12.7%=0.192;
K铁粉=1.516×4.00%=0.061
各物料的湿消耗定额:
K湿=100K干/(100-W0)
式中K湿、K干——分别表示湿、干物料消耗定额(t/t熟料);
W0——该湿物料的天然水分(%)。
K湿石灰石=100×1.263/(100-1.8)=1.286(t/t熟料)
K湿粘土=100×0.192/(100-12)=0.218(t/t熟料)
K湿铁粉=100×0.061/(100-9.5)=0.0674(t/t熟料)
K湿生料=100×1.516(100-3.465)=1.57(t/t熟料)
湿原料质量百分比:
石灰石:
1.286/1.57×100%=81.91%
粘土:
0.218/1.57×100%=13.89%
铁粉:
0.0674/1.57×100%=4.29%
6.6年产熟料计算
设计任务要求设计日产4000吨水泥熟料,根据水泥熟料日产量确定水泥熟料年产量:
Qy=365ηQd,对预分解窑年利用率为:
85%≤η≤95%,
取η=90%;
Qy=365×0.90×4000=1314000(t),
即该窑的年产水泥熟料1314000吨
6.7气体量计算
拟定q=3100kj/kg
熟料耗煤量q/Qnet.ad=3100/21184=0.1463(kg/kg熟料)
理论空气量Va0=(0.241Qnet.ad/1000+0.5)q/Qnet.ad=0.821(Nm3/kg熟料)
理论废气量Vg=(0.231net.ad/1000+1.65)q/Qnet.ad=0.961(Nm3/kg熟料)
理论料耗=L0=(100-s)/(100-I)=96.45/66.16=1.455(Nm3/kg熟料)
I-生料烧失量,s-煤灰掺入量
生料气体生成废气量全部生成CO2,(标准状况下密度为1.9777Kg/m3)
Ur=L0×I/P=0.2475
生料水分蒸发废气量(水蒸气密度为0.8036kg/m3)
Uh=0.5L0/(100-0.5)P=0.00906
6.8窑尾烟室排出废气量
生料入窑分解后生成的CO2量
L0×I%×(1/p)×e==1.455×33.69%×(1/1.9777)×7%=0.0173(Nm3/kg熟料)
窑内煤粉燃烧生成废气量Vg×40%=0.961×40%=0.3844(Nm3/kg熟料)
过剩空气量(a-1)Va0×40%=(1.2-1)×0.821×40%=0.0657(Nm3/kg熟料)
窑尾排出的总的废气量为=0.0173+0.3844+0.0657=0.4674(Nm3/kg熟料)
V工=V标×(T工/T标)×(P标/P工)
=0.4674×(273.15+1000)/273.15×(101325/101025)
=2.169m3/kg
6.9分解炉内废气量
燃煤烧废气量=0.961(Nm3/kg熟料)
生料分解放出CO2量UR=0.2475×97%=0.2304(Nm3/kg熟料)
过剩空气量(a-1)×Va0=(1.2-1)×0.821=0.1642(Nm3/kg熟料)
分解炉内废气量=0.961+0.2304+0.1642=1.3556(Nm3/kg熟料)
V工=V标×(T工/T标)×(P标/P工)
=1.1244×(273.15+876)/273.15×(101325/100375)
=5.5332m3/kg
6.10五级预热器废气量
出分解炉废气量为1.3556(Nm3/kg熟料)
五级预热器漏风量,取燃煤需用空气量的1%
Vao×1%=0.0082(Nm3/kg熟料)
五级预热器分解的CO2量0.2475×3%=0.0074(Nm3/kg熟料)
五级预热器废气量=1.3556+0.0082+0.0074=1.3712(Nm3/kg熟料)
V工=V标×(T工/T标)×(P标/P工)
=1.3712×(273.15+880)/273.15×(101325/99025)
=5.9227m3/kg
6.11预热器主要结构参数计算
(1)C5旋风筒处理气体量
单位时间出口风量=5.9227×208.33/3.6=206.8229m3/s
C5旋风筒的直径和高度(假想截面风速为5m/s)
D=
=7.260m
(2)圆柱体的高度
第五级旋风筒C5高度,h=0.75D=5.445m
(3)锥体高度
五级旋风筒锥体高度H/D一般在0.9到1.2之间选用,此次选1
锥体高度h2=1×旋风筒高度=5.445m
(4)锥角
圆锥体结构尺寸,由旋风筒直径和排灰口直径及锥边仰角决定(de--排料口直径(m),统一取1m)
tana=2H/D-de
a=60.1°
6.12C5旋风筒进风口尺寸
旋风筒进风口形式一般为矩形,长宽比在2左右,C1圆筒部分较长,一般在(2-2.5)D,其他级在(1.5-1.8)D之间。
(1)进风口的横截面积
F=V/W
F-进旋风口的风量
W-旋风筒进口风速,取20m/s
五级旋风筒的横截面积F5=19.19m2
(2)旋风筒进风口高度,取高宽比为2
高b5=4,宽a=2
6.13排气管尺寸
(1)内筒外径
内筒外径一般取0.5-0.6D,本次取0.5.
d5=0.5D=3.63m
(2)内筒插入深度
最下一级旋风筒C5=0.25b5=1.00m
6.14旋风筒其他相关尺寸
(1)旋风筒之间连接管道的内径
d=(4v/лw)½
V-管道内气体的流量
w-管道内气体的流速。
取19m/s
d5=3.2m
(2)旋风筒的钢板厚度
&=D/1000+0.002m=0.00926m
旋风筒结构尺寸表(直入式)
旋风筒
C5
旋风筒直径D(m)
7.26
内筒外径d5(m)
3.63
内筒深度c5(m)
1.00
圆柱体高度(m)
5.445
锥角a(°)
60.1
进风口高度(m)
4.00
进风口宽度(m)
2.00
连接管道内径(m)
3.2
钢板厚度(mm)
9.26
排料口直径(m)
1.00
7窑尾工艺流程简介
图一
窑尾系统由预分解窑、分解炉、回转窑、篦冷机组成。
生料经预热器提高温度,完成预热和部分分解后,进入分解炉内进行碳酸钙分解,然后在窑内完成烧结成熟料的任务,出窑高温熟料则在冷却中被冷却。
预热器充分利用逆流和悬浮两种热交换方式提高热交换效果,如图一所示,气流方向为:
窑尾烟室→分解炉→C5→C4→C3→C2→C1;料流方向:
C1→C2→C3→C4→C5→分解炉→回转窑。
逆流热交换主要在各级旋风筒连接风管内进行,旋风筒主要起物料的收集作用,并通过下料管将收集的物料喂入下一级旋风筒。
参考文献
[1]李海涛主编,《新型干法水泥生产技术与设备》,化学工业出版社,2012
[2]陈景华、张长森、蔡树元主编,《无机非金属材料热工过程及设备》,华东理工大学出版社,2014
[3]肖争鸣,李坚利,《水泥工艺技术》,化学工业出版社,2006
[4]胡道和,《水泥工业热工设备》,武汉理工大学出版社,2009
[5]熊会思,熊然,《新型干法水泥厂设备选型使用手册》,中国建材工业出版社,2007
[6]林宗寿,《水泥工艺学》,武汉理工大学出版社,2012