钢铁冶金学资料整理聂涛.docx
《钢铁冶金学资料整理聂涛.docx》由会员分享,可在线阅读,更多相关《钢铁冶金学资料整理聂涛.docx(8页珍藏版)》请在冰豆网上搜索。
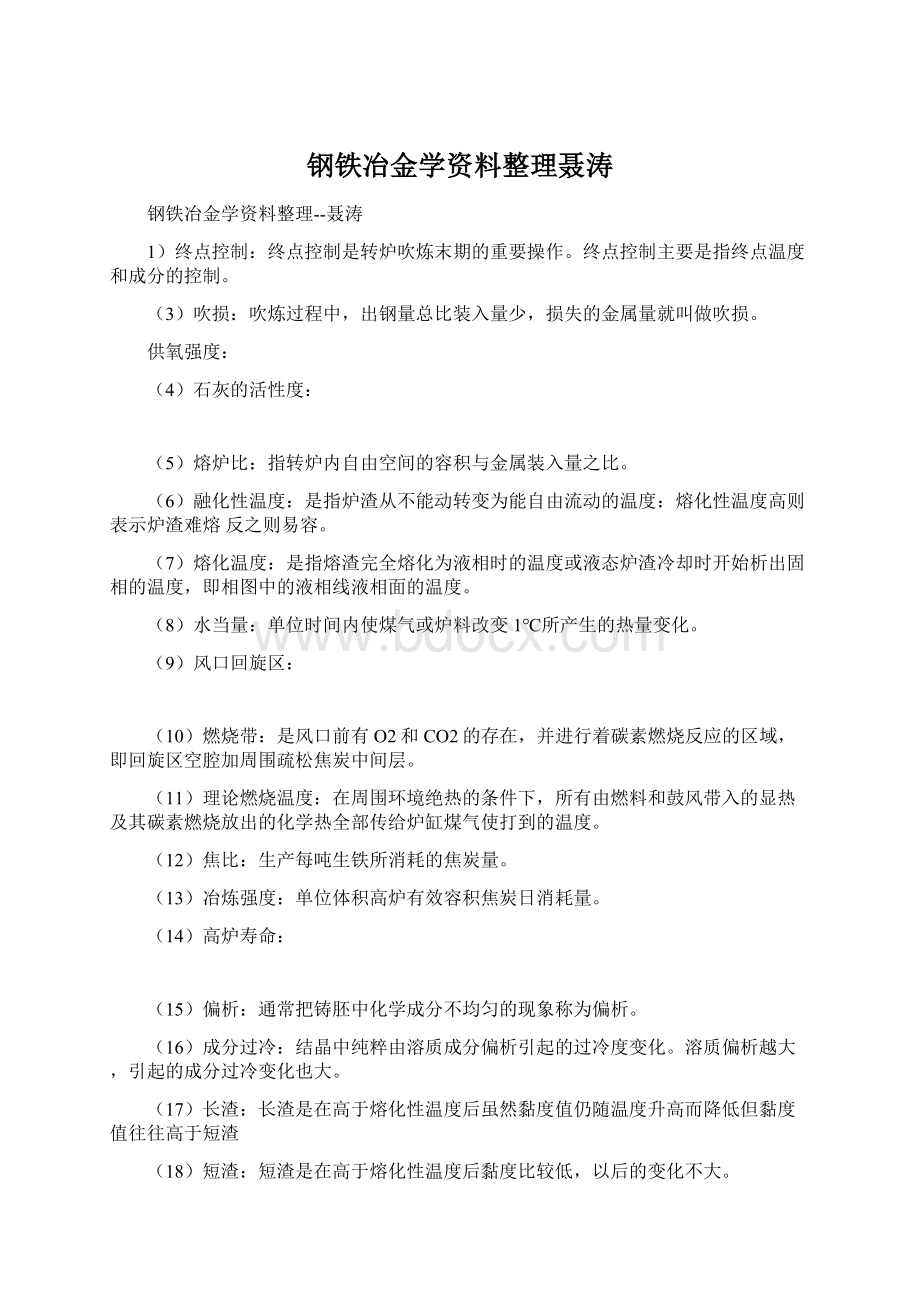
钢铁冶金学资料整理聂涛
钢铁冶金学资料整理--聂涛
1)终点控制:
终点控制是转炉吹炼末期的重要操作。
终点控制主要是指终点温度和成分的控制。
(3)吹损:
吹炼过程中,出钢量总比装入量少,损失的金属量就叫做吹损。
供氧强度:
(4)石灰的活性度:
(5)熔炉比:
指转炉内自由空间的容积与金属装入量之比。
(6)融化性温度:
是指炉渣从不能动转变为能自由流动的温度:
熔化性温度高则表示炉渣难熔反之则易容。
(7)熔化温度:
是指熔渣完全熔化为液相时的温度或液态炉渣冷却时开始析出固相的温度,即相图中的液相线液相面的温度。
(8)水当量:
单位时间内使煤气或炉料改变1℃所产生的热量变化。
(9)风口回旋区:
(10)燃烧带:
是风口前有O2和CO2的存在,并进行着碳素燃烧反应的区域,即回旋区空腔加周围疏松焦炭中间层。
(11)理论燃烧温度:
在周围环境绝热的条件下,所有由燃料和鼓风带入的显热及其碳素燃烧放出的化学热全部传给炉缸煤气使打到的温度。
(12)焦比:
生产每吨生铁所消耗的焦炭量。
(13)冶炼强度:
单位体积高炉有效容积焦炭日消耗量。
(14)高炉寿命:
(15)偏析:
通常把铸胚中化学成分不均匀的现象称为偏析。
(16)成分过冷:
结晶中纯粹由溶质成分偏析引起的过冷度变化。
溶质偏析越大,引起的成分过冷变化也大。
(17)长渣:
长渣是在高于熔化性温度后虽然黏度值仍随温度升高而降低但黏度值往往高于短渣
(18)短渣:
短渣是在高于熔化性温度后黏度比较低,以后的变化不大。
(19)碱度:
是指炉渣中碱性氧化物与酸性氧化物浓度的比值,用“R”来表示。
(20)炉渣的氧化性:
通常用渣中氧化亚铁总量Σ(FeO)表示。
(21)炉渣的氧化性:
炼钢生产中炉渣的氧化性是指炉渣向金属相的供氧的能力,也可以认为是炉渣氧化金属熔池中杂质的能力。
(22)炉渣的碱度:
熔渣中碱性氧化物浓度总和与酸性氧化物浓度总和之比称为熔渣的碱度,常用符号R表示
2-6烧结过程液相是如何形成的,不同碱度烧结矿的粘结相各有什么特点,对烧结矿质量有何影响?
答:
(1)烧结碱度烧结碱度烧结气氛烧结混合料的化学成分共同作用,化合物在烧结所能达到的温度范围内都能形成液相。
(2)烧结过程中液相的作用
Ø液相就是粘结相;液相具有流动性,能使烧结矿成分均匀;液相能使烧结矿冷凝后具有强度;液相中形成新的矿物,它能改善烧结矿的强度和还原性;烧结温度—烧结温度↑,液相生成量↑;烧结矿碱度—碱度↑,液相生成量;↑烧结气氛—还原气氛;烧结混合料的化学成分—SiO2量↑,液相生成量↑,反之;
(1)铁氧(Fe-O)体系:
铁氧化物固溶体。
高品位烧结矿的主要粘结相,脉石成分比较小。
(2)FeO--SiO2体系:
酸性烧结矿的主要粘结相。
特点:
强度比较高;但还原性比较差。
生成条件:
比较低的碱度,有SiO2,比较高的温度;还原性气氛。
工艺是燃料用量高。
(3)CaO--SiO2体系:
熔剂性烧结矿的主要粘结相。
特点:
固相反应生成能力强,反应速度快。
强度比较低;
原因是2CaO·SiO2有相变问题;不存在还原性问题。
生成条件:
比较高的碱度,有CaO;高温(生成的液相量是不多的)。
(4)CaO--Fe2O3体系:
熔剂性烧结矿的主要粘结相。
用,作用③是任何固体燃料所无法替代的。
要求:
①固定C高②灰分低③S、P含量低④挥发份和水分合适⑤强度高⑥粒度合适(为矿石平均粒度的3~5倍为宜,d小/d大≈0.7⑦反应性弱(C+CO2→CO)⑧燃烧性弱(C+O2→CO2)
3-5比较用co和H2氧化物的特点
答:
(1)与co还原一样均属间接还原,反应前后气相体积(co和H2)没有变化,即反应不受压力影响。
(2)除F2O3的还原外F3O4的还原均为可逆反应。
在一定温度下有固定的平衡气相成分,为了彻底还原铁的氧化物,都需要过量的还原剂。
(3)从热力学因素看810℃以上H2还原能力高于CO还原能力,810℃以下是则相反。
(4)从动力学学看,因为H2与其反应产物H2O的分子半径彼CO与其反应产物CO2的分子半径小,因而扩散能力强,以此说明不论在高温下还是在低温下H2还原反应速度都比CO还原反应速度快。
(5),在高炉冶炼条件下,H2还原氧化物时还可促进CO和C还原反应的加速进行。
因为H2还原时的产物H2O(气)会同CO和C作用放出氧,而H2又重新被还原出来,继续参加还原反应。
如此H2在CO和C的还原过程中,把走铁氧化物中夺取的氧又传给了CO或C气着中间媒介传递作用。
3-6直接还原和间接还原各有什么特点?
答:
直接还原:
还原剂碳量消耗cd=0.214rdW【Fe】用碳还原生成CO高温为吸热反应决定于碳的气化反应,高温在1100℃左右。
间接还原:
用CO或H2还原生成CO2,低温为放热反应,H2为吸热反应,决定于矿石的还原性能。
3-11高炉渣有哪些性质,对高炉冶炼有何影响?
答:
(1)、炉渣碱度:
以重量百分比浓度表示的简化表示法。
(2)、炉渣的熔化性
(3)、炉渣粘度
8-4脱碳反应在炼钢中的应用?
答:
碳能显著改变钢的液态和凝固性质,在16000C,[C]≤0.8%时,每增0.1%的碳:
Ø钢的熔点降低6.50C
Ø密度减少4kg/m3
Ø黏度降低0.7%
Ø[N]的溶解度降低0.001%
Ø[H]的溶解度降低0.4cm3/100g
Ø增大凝固区间17.790C。
Si、P、S降低碳的溶解度,Mn、V、Cr增加碳的溶解度,碳增加钢材的强度、硬度,碳降低钢材的焊接、耐腐蚀、冷加工性能
8-6从热力学和动力学角度分析炼钢过程脱硫、脱磷条件。
答:
有利于脱磷的工艺条件:
(1)、高碱度炉渣——R(3~4)
(2)、高氧化铁炉渣——w(FeO)(15%~20%)
(3)、低温
(4)、增加渣量
脱硫条件:
•结论:
高碱度、高FeO含量、高温、大渣量有利于脱硫。
•但是,以上操作生产带来困难和影响技术经济指标。
所以。
抑制钢中的含硫量——采用铁水预处理
8-8为什么要脱氧,脱氧的原理?
答:
因为1、氧的危害
•1)严重降低钢的力学性能,尤其是塑性和韧性。
•2)大量气泡的产生影响浇注的正常进行,将会破坏锭或坯的合理结构,严重影响钢锭质量,甚至造成废品。
• 3)钢中的氧能加剧硫的热脆危害。
2、脱氧的原理
炼钢过程中脱氧的原理是:
利用对氧的亲和力比Fe大的元素,如Mn、Si、Al等,把钢液中的氧夺走,形成不残留在钢液中的脱氧产物MnO、SiO2、Al2O3等并上浮到渣中。
能用来对钢液脱氧的元素或合金叫脱氧剂。
10-6什么是回磷,如何减少回磷?
回磷是指冶炼后期钢液中磷含量比中期有所回升,以及成品钢中的含磷量比冶炼终点钢水含磷量高的现象。
首先搞好前期化渣(尽可能采用软吹;使用活性石灰;使用合成渣料),尽快形成高氧化性炉渣,以利在吹炼前期低温去磷。
若铁水磷含量高,还可在化好渣的情况下倒掉部分高磷炉渣,以提高脱磷效率。
而在吹炼中、后期,则要控制好炉渣碱度和渣中(FeO),保证磷稳定在炉渣中,而不发生回磷现象。
在吹炼前期快速降低,进入吹炼中期略有回升,而到吹炼后期再度降低。
10-7什么是溅渣呼炉,其主要技术特点是什么?
溅渣护炉基本原理:
是利用高速氮气把MgO含量饱和或过饱和的炼钢终点渣喷溅在炉衬表面形成溅渣层。
溅渣层固化了镁碳砖表层的脱碳层,抑制了炉衬表层的氧化,并减轻了高温炉渣对砖表面的冲刷侵蚀。
技术特点
1、操作简便
2、成本低
3、时间短,3min左右
4、溅渣均匀覆盖整个炉膛内壁上
5、工人劳动强度低,无环境污染
6、由于炉龄提高,节省修砌炉时间
10-8什么叫转炉少渣冶炼,其技术特点?
11-1电炉氧化法冶炼过程包括那几个阶段?
其中熔化、氧化、还原各期的主要任务?
主要包括熔化期、氧化期、还原期
熔化期的主要任务
①将块状的固体炉料快速熔化,并加热到氧化温度;
②提前造渣,早期去磷
③减少钢液吸气与挥发
氧化期的目的
①继续脱磷到要求——脱磷;
②脱碳至规格下限——脱碳;
③去除气、去夹杂——二去;
④提高钢液温度——升温。
还原期的主要任务
①脱氧至要求——脱氧;
②脱硫至一定值——脱硫;
③调整成分——合金化;
④调整温度——调温。
11-3电炉炼钢采取无渣出钢的意义?
EBT电炉的优点?
无渣出钢的意义:
(1)传统“老三期”工艺操作:
装料熔化——氧化扒渣——造渣还原——带渣出钢。
带入钢包中的是还原性炉渣,它对进一步脱硫、脱氧、吸附夹杂等是有益无害的。
功能分化后,UHP电炉与炉外精炼相配合,电炉出钢时的炉渣是氧化性炉渣。
氧化渣要带入钢包精炼过程,将会给精炼带来极为不利的影响:
使钢液回磷,降低脱氧、脱硫能力,降低合金回收率,以及影响吹氩效果与真空度等。
EBT电炉的优点
(2)EBT电炉实现了无渣出钢和增加了水冷炉壁使用面积。
具体优点如下:
①出钢倾动角度的减少:
简化电炉倾动结构;降低短网的阻抗;增加水冷炉壁使用面积,提高炉体寿命。
②留钢留渣操作:
无渣出钢,改善钢质,有利于精炼操作;留钢留渣,有利电炉冶炼、节能。
③炉底部出钢:
降低出钢温度,节约电耗;减少二次氧化,提高钢的质量;提高钢包寿命。
转炉炼钢脱氧方法?
原理?
答:
1)转炉炼钢脱氧方法:
沉淀脱氧、扩散脱氧和真空脱氧
沉淀脱氧——铁合金直接加入到钢水中进行脱氧;
扩散脱氧——脱氧剂加到熔渣中,降低渣中(Fe)含量,使钢水中的氧向熔渣中转移;
真空脱氧——将钢水置于真空条件下,降低外界CO的分压破坏钢水中碳氧平衡,使碳氧反应继续;
(2)原理:
吹炼终点钢水[O]=0.02~0.08%,向钢中加入一种(或几种)与氧亲和力比Fe大的元素,常用脱氧剂Fe-Si、Fe-Mn、Al、Si-Al-Ca、Si-Al-Ba等;
电炉炼钢脱氧方法?
原理?
答:
电炉主要有(沉淀脱氧)(扩散脱氧);常用综合脱氧法,其还原操作以脱氧为核心.
①当钢液的T、P、C符合要求,扒渣>95%;
②加Fe-Mn、Fe-Si块等预脱氧(沉淀脱氧);
③加石灰、萤石、火砖块,造稀薄渣;
④还原,加C粉、Fe-Si粉等脱氧(扩散脱氧),分3~5批,7~10min/批;
⑤搅拌,取样、测温;
⑥调整成分——合金化;
⑦加Al或Ca-Si块等终脱氧(沉淀脱氧);
⑧出钢
原理:
在电炉炼钢中,主要应用沉淀脱氧对刚液进行预脱氧和终脱氧;加Fe-Mn、Fe-Si块等预脱氧(沉淀脱氧);加Al或Ca-Si块等终脱氧(沉淀脱氧);