主轴箱结构设计资料.docx
《主轴箱结构设计资料.docx》由会员分享,可在线阅读,更多相关《主轴箱结构设计资料.docx(25页珍藏版)》请在冰豆网上搜索。
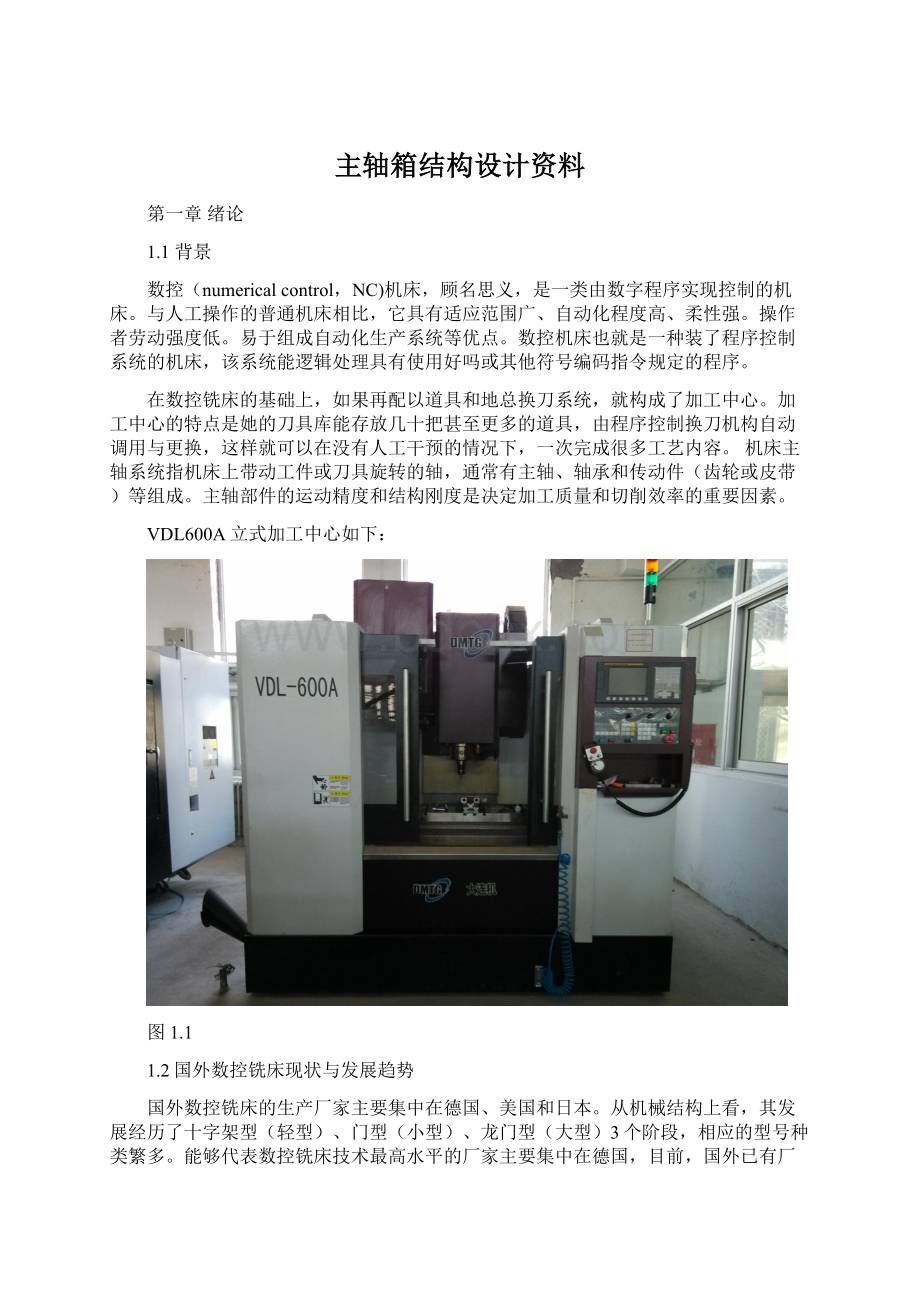
主轴箱结构设计资料
第一章绪论
1.1背景
数控(numericalcontrol,NC)机床,顾名思义,是一类由数字程序实现控制的机床。
与人工操作的普通机床相比,它具有适应范围广、自动化程度高、柔性强。
操作者劳动强度低。
易于组成自动化生产系统等优点。
数控机床也就是一种装了程序控制系统的机床,该系统能逻辑处理具有使用好吗或其他符号编码指令规定的程序。
在数控铣床的基础上,如果再配以道具和地总换刀系统,就构成了加工中心。
加工中心的特点是她的刀具库能存放几十把甚至更多的道具,由程序控制换刀机构自动调用与更换,这样就可以在没有人工干预的情况下,一次完成很多工艺内容。
机床主轴系统指机床上带动工件或刀具旋转的轴,通常有主轴、轴承和传动件(齿轮或皮带)等组成。
主轴部件的运动精度和结构刚度是决定加工质量和切削效率的重要因素。
VDL600A立式加工中心如下:
图1.1
1.2国外数控铣床现状与发展趋势
国外数控铣床的生产厂家主要集中在德国、美国和日本。
从机械结构上看,其发展经历了十字架型(轻型)、门型(小型)、龙门型(大型)3个阶段,相应的型号种类繁多。
能够代表数控铣床技术最高水平的厂家主要集中在德国,目前,国外已有厂家在龙门式切割机上安装一个专用切割机械手,开发出五轴控制系统的龙门式专用切割工具,该系统可以在空间切割出各种轨迹,利用特殊的跟踪探头,在切割过程中控制切割运行轨迹。
我国工厂的板材下料中应用最为普遍的是数控铣床和等离子切割,所用的设备包括手工下料、仿形机下料、半自动切割机下料及数控切割机下料等。
与其他切割方式比较而言,手工下料随意性大、灵活方便,并且不需要专用配套下料设备。
但手工切割下料的缺点也是显而易见的,其割缝质量差、尺寸误差大、材料浪费大、后道加工工序的工作量大,同时劳动条件恶劣。
用仿形机下料,虽可大大提高下料工件的质量,但必须预先加工与工件相适应的靠模,不适于单件、小批量和大工件下料。
半自动切割机虽然降低了工人劳动强度,但其功能简单,只适合一种形状的切割。
上述3种切割方式,相对于数控切割来说由于设备成本较低、操作简单,所以在我国的中小企业甚至在一些大型企业中仍在广泛使用。
随着国内经济形势的蓬勃发展以及以焊代铸趋势的加速,数控铣床的优势正在逐渐为人们所认识。
数控铣床不仅使板材利用率大幅度提高,产品质量得到改进,而且改善了工人的劳动环境,劳动效率进一步提高。
目前,我国金属加工行业使用的数控铣床是以火焰和普通等离子切割机为主,但纯火焰切割,已不能适应现代生产的需要,该类切割机可满足不同材料、不同厚度的金属板材的下料以及金属零件的加工的需要,因此需求量将会越来越大,但与国外的差距仍极为明显,主要表现为:
发达国家金属加工行业90%为数控切割机下料,仅10%为手工下料;而我国数控切割机下料仅占下料总量的10%,其中数控铣床下料所占比例更小。
1.3数控机床的组成与分类
一数控机床的组成
数控机床的种类很多,但是任何一种数控机床都主要由数控系统、伺服系统和机械系统组成。
1数控系统:
数控系统是数控机床的核心,是数控机床的“指挥系统”。
数控系统通常是一台带有专门系统软件的专用微型计算机。
2伺服系统:
伺服系统(或称驱动系统)是数控机床的执行机构,是由驱动和执行两大部分组成。
用于实现数控机床的进给伺服控制和株洲伺服控制。
它接受数控装置的指令信息,并按指令信息的要求控制执行部件的进给熟读、方向和位移。
3机械系统:
数控机床的机械系统,除机床基础件意外,有下列各部分组成:
(1)主轴部件:
包括主轴电动机和主轴传动系统。
(2)进给系统:
包括进给执行电动机和进给传动系统。
(3)实现共建回转、定位的装置和附件。
(4)实现某些部件动作和辅助功能的系统和装置。
(5)刀库和自动换刀装置(AutormaticToolsChanger,简称ATC)
(6)自动托盘交换装置(AutormaticPalletChanger,简称APC)
机床基础件或称机床大件,通常是指床身(或底座)、立柱、滑座和工作台等,它是整台机床的基础和框架。
[9]
二数控机床的分类
1按工艺用途分
按照工艺的不同,数控机床可分为数控车床、数控铣床、数控钻床、数控镗床、数控齿轮加工机床、数控电火花加工机床、数控线切割机床、数控冲床、数控剪床、数控液压机等各种工艺用途的数控机床。
2按运动方式划分
按运动方式即刀具与工件相对运动方式,数控机床可分为:
点位控制、直线控制和轮廓控制。
3按伺服系统类型划分
按伺服系统类型的不同,数控机床可分为:
开环伺服系统数控机床、闭环伺服系统数控机床和半闭环伺服系统时空机床。
(1)开环伺服系统数控机床
开环伺服系统数控机床是一种不叫原始的数控机床。
这类机床的数控系统将零件的程序处理后,输出数据指令给伺服系统,驱动机床运动,没有来自位置传感器的反馈信号。
最典型的系统就是采用步进电动机的伺服系统。
这类系统的信息流是单向的,即进给脉冲发出去以后,实际移动值不再反馈回来,所以称为开环控制。
这类机床较为经济,但加工速度和加工精度较低。
(2)闭环伺服系统数控机床
闭环伺服系统数控机床带有检测装置,直接对工作台的位移量进行检测。
这类控制系统,因为把机床工作台纳入位置控制环,故称为闭环控制系统。
该系统可以消除包括工作台传动链在内的运动误差,因而定位精度高、调节速度快。
但由于该系统受进给丝杠的拉压刚度、扭转刚度、摩擦阻尼特性和间隙等非线性因素的影响,给调试工作造成较大的困难。
(3)半闭环伺服系统数控机床
大多数数控机床是半闭环伺服系统,这类系统介于开环和闭环之间,精度没有闭环高,调试却比闭环方便,因而得到了广泛的应用。
1.4本文研究内容
主要研究主轴箱部分,如图1.2,该主轴箱具有以下要求:
1合理设计加工主轴箱结构;2经过对该设备刀具切削力计算,合理主运动电动机、传动部件、轴承组件、主轴。
气压传动等零部件参数计算以及选型等;3设计主轴箱的整体结构;4设计主轴箱、主轴等主要零件;5切削力计算;
图1.2
第2章VDL主轴传动系统
与普通机床的主轴传动系统相比数控机床在结构上比较简单,这是因为变速功能全部或大部分由主轴电动机的无级调速来承担。
省去了繁杂的齿轮变速机构,还有一些数控机床设计中还存在二级或三级齿轮变速机构用以扩大主轴电动机无级变速的范围。
2.1主轴变速系统
变速方式有有极变速和无极变速。
无极变速:
速度连续变化,有无数个设置点。
如,电子式旋钮风扇的风力档的变化,旋钮从最小到最大位置之间,有无数个位置。
有极变速:
速度不是连续变化,仅有限的几个变化位置。
如,机械式按钮风扇的风力档的变化,只有1,2,3,4等几个档位。
由于无极变速简化了主轴箱的结构,也保证了加工时能选用合理的切削用量,获得好的加工质量,一般都采用无极变速。
目前主轴类型有以下几种:
1
、齿轮传动主轴
大中型数控机床常采用这种变速方式。
如图a所示,通过少数几对齿轮变速,扩大调速范围,扩大输出转矩,满足主轴低速是对主轴扭矩特性要求。
滑移齿轮的移位大都采用液压拨叉或直接由液压缸带动齿轮来实现。
2、直接驱动主轴
从电动机到加工刀具的传动效率而言,直接驱动方式几乎可以实现100%的传动效率。
直接驱动主轴可以在低转矩下实现高转速工作。
由于不存在皮带或齿轮等中间传动链,直接驱动主轴的转矩不会随着电机转速的下降而增加。
就振动而言,这种传动系统表现良好,也就是说能够达到高速转动,并保持良好地加工表面加工质量。
3、通过带传动的主传动
这种传动主要用在转速较高、变速范围不大的机床。
如图b。
结构简单,安装调试方便,且在一定条件下能满足转速与转矩的输出要求。
带传动可以避免齿轮传动的噪声与振动。
常用的带有三角带和同步齿形带。
4内置电机驱动主轴
这种主轴也被称为电主轴。
集成在主轴上前后轴承之间的电机可以是同步电机也可以是异步电机。
这种驱动方式可以有效的减少震动和噪声,实现15000r/min乃至更高的转速,而且其结构更为紧凑,这就是电主轴能在告诉加工机床中普遍应用的原因。
通过调研,我做的VDL600A立式加工中心所用的是高扭力齿形皮带传动的无极变速方式。
加工中心的主轴组件
加工中心主轴组件是机床的一个重要组成部分,除了具有一般数控机床主轴组件所具有的主轴、主轴支承及装在主轴上的传动件和密封件外,还具有刀具自动加紧、主轴自动准停和主轴装刀孔吹净等装置。
1.范围:
各种不同的机床对调速范围的要求不同,多用途,通用性比较大的机床,要求主轴的调速范围大,不但有低速大转距的功能,而且还要有比较高的速度。
2.热变形:
电动机、主轴及传动件都有热源。
降低温升,减少热变形是对主传动系统要求的重要指标。
3.旋转精度和运动精度
(1)主轴的旋转精度:
是指装配后,在无载荷,低速转动条件下,测量主轴前端和300mm处的径向和轴向跳动值。
(2)主轴在以工作速度旋转时,测量上述两项精度称为运动精度。
4.主轴的静刚度和抗振性
由于数控机床的加工精度比较高,主轴的转速又很高。
因此,主轴组件的质量分布是否均匀以及主轴组件的阻尼等,对主轴组件的静刚度和抗振性都会产生影响。
5.主轴组件的耐磨性
主轴组件必须有足够的耐磨性,使之能够长期保持要求的准确精度。
凡是有机械摩擦的部位,轴承,锥孔等都要有足够的硬度,轴承还应具有良好的润滑。
2.2主轴电机的选择
2.2.1主轴切削力
铣削用量的选择
为使组合铣床更好的提高生产效率,便于人工操作,最少的停车损失和使刀具的寿命更长、加工质量更好,合理的选择铣削用量是非常必要的。
表3-3为硬质合金端铣刀的铣削用量。
铣削用量的选择应该使选择的刀具充分发挥其性能。
所以就不能选择太低。
考虑到批量生产时也没必要把切削用量选太高,以免增加刀具损耗。
总之要根据加工精度和加工材料,工作条件和技术要求进行分析。
所以以上的选择是可行的。
2.2 确定切削力、切削功率
根据选定的切削用量(组要指切削速度v及进给量f),确定切削力,作为选择动力部件(滑台)及夹具设计的依据;确定切削扭矩,用以确定主轴及其他传动件(齿轮、传动轴等)的尺寸;确定切削功率,用以选择主传动电机功率。
一銑削力和主切削功率计算
1.转速
根据设计要求转速的范围为:
60~8000,主轴在工作时其转速通常为:
10r/s
则转速:
v=nd/2=0.625m/s
2.主切削力Fc
因选取硬质合金端面銑削45,钢工件,由<机床设计手册>得:
式中:
ap-铣削深度(mm);
ae-铣削接触弧深度(mm);
af-每齿进给量(mm/Z);
-每秒(分)进给量(mm/s,mm/min);
f-每转进给量(mm/r);
d0-铣刀外径mm;
n0-铣刀转速(r/s),
Z-铣刀齿数。
根据表2.1,选取:
ap=2.0mm;ae=5;af=1.0mm;
=5mm;d=125mm;n=20;Cf=78.5;Xf=1.0;Yf=0.75;Zf=1.1;Wf=0.2;qF=1.3带入式中得:
Fz=5600N
P=FV=3500W,圆整取P=4.0KW;
则驱动电机功率:
则电机的功率为6.0kw。
铣刀类型
刀具材料
公式中的系数及指数
CF
XF
YF
ZF
WF
qF
加工碳素结构钢σb=0.637GPa
端铣刀
硬质合金
790
1.0
0.75
1.1
0.2
1.3
高速钢
78.5
0.95
0.8
1.1
0
1.1
圆柱铣刀
硬质合金
96.7
1.0
0.75
0.88
0
0.87
高速钢
65
1.0
0.72
0.86
0
0.86
立铣刀
硬质合金
11.9
1.0
0.75
0.85
-0.13
0.73
高速钢
65
1.0
0.72
0.86
0
0.86
圆盘铣刀、切槽及切断铣刀
硬质合金
250
1.1
0.8
0.9
0.1
1.1
高速钢
65
1.0
0.72
0.86
0
0.86
凹凸半圆及角铣刀
高速钢
45
1.0
0.72
0.86
0
0.86
加工不锈钢1Cr18Ni9TiHB=141
端铣刀
硬质合金
218
0.92
0.78
1.0
0
1.15
立铣刀
高速钢
82
1.0
0.6
0.75
0
0.68
加工灰铸铁HB=190
端铣刀
硬质合金
54.5
0.9
0.74
1.0
0
1.0
圆柱铣刀
58
1.0
0.8
0.75
0
0.9
圆柱铣刀、立铣刀、圆盘铣刀、切槽及切断铣刀
高速钢
30
1.0
0.65
0.83
0
0.83
加工可锻铸铁HB=150
端铣刀
硬质合金
491
1.0
0.75
1.1
0.2
1.3
圆柱铣刀、立铣刀、圆盘铣刀、切槽及切断铣刀
高速钢
30
1.0
0.72
0.86
0
0.86
加工中等硬度非均质铜合金HB=100-140
圆柱铣刀、立铣刀、圆盘铣刀、切槽及切断铣刀
22.6
1.0
0.72
0.86
0
0.86
表2.1
2.3传动设计
VDL主轴的驱动路线采用电机驱动,带传动,带传动驱动主轴,这种结构简单,效率高,由电机控制来实现无极变速。
带采用同步带传动,同步带传动具有:
同步带传动综合了带传动和链传动的特点,同步带传动的优点是:
(1)无相对滑动,带长不变,传动比稳定;
(2)带薄而轻,强力层强度高,适用于高速传动,速度可达40m/s;
(3)带的柔性好,课用直径较小的带轮,传动结构紧凑,能获得较大的传动比;
(4)传动效率高,可达0.98-0.99,因而应用日益广泛;
(5)初拉力较小,故轴和轴承上所受的载荷小。
主要缺点是制造、安装精度要求较高、成本高。
同步带主要用于要求传动比准确的中、小功率传动中,如计算机、录音机、磨床和纺织机等。
[13]
第三章同步带传动
3.1材料选择
根据设计要求,选用聚氨酯同步带,由带背、带齿、抗拉层三部分组成。
带背和带齿材料为聚氨酯,抗拉层采用钢丝绳,适用于中小功率的高速运转部分。
[13]
3.2参数计算
设计计算的内容主要是:
齿形带的模数、齿数、和宽度的结构和尺寸,传动中心距,作用在轴上载荷以及结构设计。
1.模数的选取
模数主要根据齿形带所传递的计算功率Pd和小带轮转速n1确定的,通过查《现代数控机床》表4-33查得Pd=KA*P,式中P———传动功率
表4-1工作情况系数KA
载荷性质
一天运转时间/h
≤10
10~16
16以上
载荷平稳
1.0
1.1
1.2
载荷变化小
1.2
1.4
1.6
载荷变化大
1.4
1.7
2.0
选取KA=1.7,所以PC=5.7×1.7=9.69KW
由齿形带模数选用图可选m=4
2.小带轮齿数Z1:
由《机械传动装置设计手册》表8-38得Zmin=22,所以取Z1=30
3.同步带节距Pb:
由PD=9.35KWn1=1500r/min,查表选取节距Pb=12.566mm,齿形角2β=40。
齿根厚S=5.75mm。
齿顶厚St=4mm,齿高hg=ht+e=2.4+2.7=5.1mm,齿根圆半径Rr=齿顶圆半径Ra=0.40mm,带高hs=4.4mm,节顶距δ=1.000mm,带bs=35~40mm。
4.节圆直径d1:
d1=
=121.2㎜
5.大带轮齿数z2与直径:
z2=iz1=60
6.大带轮直径d2=id1=1.5×96=242.2㎜
7.带的速度V:
V=
=7.536,(式4-1)
由表查得[13]
Vmax=35~40V8.定中心距a0:
5(d1+d2)≤a0≤2(d1+d2)
所以:
0.7(96+144)≤a0≤2(96+144)
则有168≤a0≤480初选a0=278
9.带的节线长度Lp以及齿数Zb:
Lp0=2a0+
(d1+d2)+
=2300+
×240+
=978.72(式4-2)
查表选取Lp=1005㎜Zb=80
10.计算中心距a(采用中心距可调)
a≈a0+
=300+
㎜(式4-3)
选取a=314㎜
11.带轮与带的啮合齿数Zm:
Zm≈
=11.82取Zm=12(式4-4)
因为当m≥2时,Zm应不小于6,所以计算的Zm满足条件。
12.带宽bs:
bs≥
查表取Kz=1.20,Fa=20N/mm(式4-5)
Fc=mbV2=4.8×10-3×7.5362=0.273
所以bs≥
㎜选取bs=40㎜
13.作用与轴上的力Fr:
Fr=
(式4-6)
14.小带轮最小包角ɑ:
α≈180º-60º(d2-d1)/a=180。
-60。
(144-96)/314=170.8。
15.带轮宽度bf,bf1,bf2
bf=bs+(1.5~3)=41.5~43
bf1=bs+(6~7)=46~47
bf2=bs+(3~5)=43~4[14]
第4章主轴组件的设计
主加工中心主轴组件是机床的一个重要组成部分,除了具有一般数控机床主轴组件所具有的主轴、主轴支承及装在主轴上的传动件和密封件外,还具有刀具自动加紧、主轴自动准停和主轴装刀孔吹净等装置。
轴组件主要包括:
主轴、主轴支撑和安装在主轴上的传动件、密封件等,因为主轴带动工件或刀具直接参加工件表面形成运动,所以它的工作性能对加工质量和生产率产生直接影响,是机床最重要的部件之一。
4.1主轴组件的设计要求
回转精度:
主轴组件的回转精度,是指主轴的回转精度。
当主轴做回转运动时,线速度为零的点的连线称为主轴的得回转中心线。
回转中心线的空间位置,每一瞬间都是变化的,这些瞬间回转中心线的平均空单位转移不为理想回转中心线。
瞬时回转中心线相对于理想回转中心线在空间位置的距离,就是主轴的回转误差,而回转误差的范围,就是主轴的回转精度。
纯径转误差、角度误差和轴向误差,它们很少单独存在。
当径向误差和角度误差同时存在构成径向跳动,而轴向误差和角度误差同时存在构成端面跳动。
由于主轴的回转误差一般都是一个空间旋转矢量,它并不是在所有的情况下都表示为被加工工件所得的加工形状。
主轴回转精度的测量,一般分为三种静态测量、动态测量和间接测量。
目前我国在生产中沿着传统的静态测量法,用一个精密的检测棒插入主轴锥孔中千分表触头触及检测棒圆柱表面,以低速转动主轴进行测量。
千分表最大和最小的读数差既认为是主轴的径向回转误差。
端面误差一般以包括主轴所在平面内的直角坐标系的垂直度,数据综合表示。
动态测量是用一标准球装在主轴中心线上,与主轴中心线上,与主轴同时旋转;在主轴同时旋转;在工作台上安装两个互成90度角的非接触传感器,通过仪器记录回转情况。
间接测量是用小的切削量用小的切削量回工有色金属试件,然后在圆度仪上测量试件的圆度来评价。
出厂时,普通级加工中心的回转精度用静态测量法测量,当L=300mm时允许误差应小于0.02㎜。
造成主轴回转误差的原因主要是由于主轴的结构及其加工精度、主轴轴承的选用及刚度等,而主轴及其回转零件的不平衡,在回转时引起的激振力,也会造成主轴的回转误差。
因此加工中心的主轴不平衡量要控制在0.4㎜/s以下。
主轴刚度:
主轴组件的刚度是指受外力作用时,主轴组件抵抗变形的能力。
通常抵以主轴前端产生单位位移时,在位移方向上所施加的作用力大小来表示。
主轴组件的刚度越大,主轴受力的变形就越小。
主轴组件的刚度不足,在切削力及其他力的作用下,主轴将产生较大的弹性变形,不仅影响工件的加工质量,还会破坏齿轮、轴承的正常工作条件,使其加快磨损,降低精度。
主轴部件的刚度与主轴结构尺寸、支撑跨距、所选轴承类型及配置形势、砂间隙的调整、主轴上传动元件的位置等有关。
主轴抗振性:
主轴组件的抗振性是指切削加工时,主轴保持平稳的运转而不发生振动的能力。
主轴组件抗振性及在必要时安装阻尼(消振)器。
另外,使主轴固有频率远远大于激振力的频率。
主轴温升:
主轴组件在运转中,温升过高会起两方面的不良结果:
一是主轴组件和箱体因热膨胀而变形,主轴的回转中心线和机床其他件的相对位置会有变化,直接影响加工精度;其次是轴承等元件会因温度过高而改变已调好的间隙和破坏正常润滑条件,影响轴承的正常工作。
严重时甚至会发生:
“抱轴”。
数控机床在解决温升问题时,一般采用恒温主轴箱。
主轴的耐磨性:
主轴组件必须有足够的耐磨性,以便长期保持精度。
主轴上易磨损的地方是刀具或工件的安装部位以及移动式主轴的工作部位。
为了提高耐磨性,主轴的上述部位应该淬硬,或者经过氮化处理,以提高硬度增加耐磨性。
主轴轴承也需要有良好的润滑,提高其耐磨性。
以上这些要求,有的还是矛盾的,例如高刚度和高速,高速和高精度等,这就要具体问题具体分析,例如设计高效数控机床的主轴组件的主轴应满足高速和高刚度的要求;设计高精度数控机床时,主轴应满足高刚度、低温升的要求。
同时,主轴结构要保证个部件定位可靠,工艺性能好等要求。
提高主轴组件抗振性的措施
(1)尽量缩短主轴前轴承结构的长度,适当增大跨矩;
(2)尽量提高前轴承的刚度和阻尼;
(3)提高前轴承的精度,把推力轴承放在前支撑初可提高抗振性;
(4)对高速旋转的零件作静、动平衡,提高齿轮、主轴的制造精度都可适当减少强迫振动源;
(5)对于非连续切削过程的铣削,滚削等加装飞轮可减少振动;
(6)应用阻尼器消耗振动能量是有效的措施;考虑系统的固有频率,避免共振。
减少主轴组件热变形的措施
(1)把热源移至机床以外。
(2)改善主传动的润滑条件。
如进行箱外循环润滑,用低粘度的润滑油、油雾润滑等,特别注意前轴承的润滑情况。
(3)采用冷却散热装置。
例如用热管冷却减少机床各部位的温差,进行热补偿。
如可以在结构设计采用一些自动补偿的装置设法使热变形朝不影响加工精度的方向发展。
还可以在工艺上减少热变形的影响。
如先空运转一段时间再加工。
把粗、精加工分开等。
4.2主轴材料的选择及尺寸、参数的计算
主轴是主轴组件的重要组成部分,它的结构尺寸和形状、制造精度、材料、及其热处理,对主轴组件的工作性能都有很大的影响。
主轴结构随系统设计要求的不同而有各种形式。
主轴的主要尺寸参数包括:
主轴直径、内孔直径、悬伸长度和支撑跨距。
评价和考虑主轴的主要尺寸参数的依据使主轴的刚度、结构工艺性和主轴组件的工艺适应范围。
1.主轴直径
主轴直径越大,其刚度越高,但使得轴承和轴上其他零件的尺寸相应增大。
轴承的直径越大,同等级精度轴承的公差值也越大,要保证主轴的旋转精度就越困难。
同时极限转数下降。
主轴后端支撑轴颈的直径可视为0.7~0.8的前支承轴颈值,实际尺寸要在主轴组件结构设计时确定。
前、后轴颈的差值越小则主轴的刚度越高,工艺性能也越好。
2.主轴内孔直径
主轴的内孔用来安放棒料、刀具夹紧装置固定刀具、传动气动或液动卡盘等。
主轴孔径越大,可通过的棒料直径也越大,机床的适用范围就越广,同时主轴部件的相对重量也越轻。
主轴孔径的大小主要受主轴刚度的制约。
主轴的孔径与主轴的直径之比,小于0.3时空心主轴的刚度几乎与实心主轴的刚度相当;等于0.35时,空心主轴的刚度为实心主轴刚度的90%;大于0.7时空心主轴的刚度急剧下降。
一般可取其比值为0.5左右。
根据设计要求,此设计选用的主轴材料