钳工锉削技能实训教案.docx
《钳工锉削技能实训教案.docx》由会员分享,可在线阅读,更多相关《钳工锉削技能实训教案.docx(18页珍藏版)》请在冰豆网上搜索。
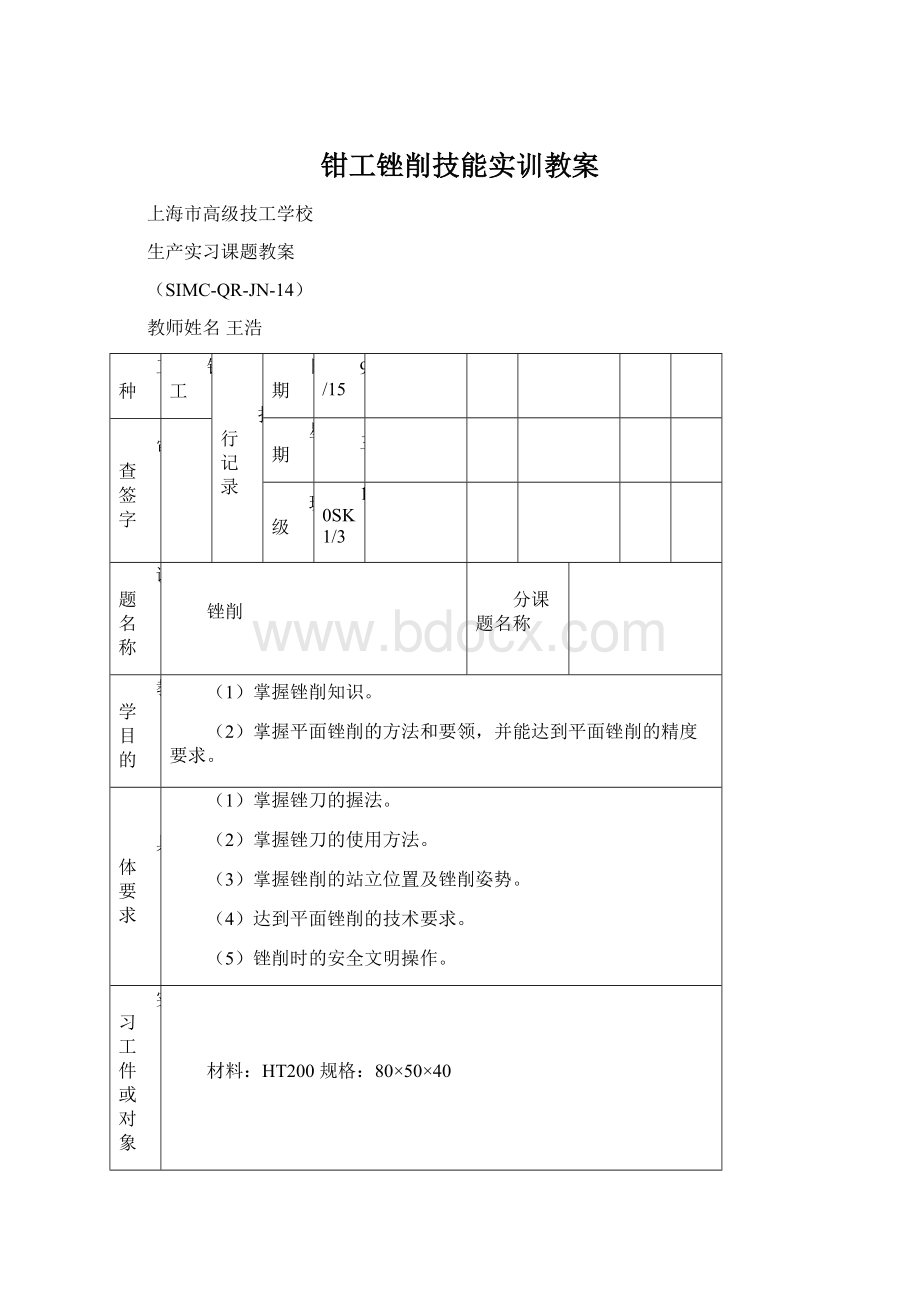
钳工锉削技能实训教案
上海市高级技工学校
生产实习课题教案
(SIMC-QR-JN-14)
教师姓名王浩
工种
钳工
执行记录
日期
9/15
星期
三
审查签字
班级
10SK1/3
课题名称
锉削
分课题名称
教学目的
(1)掌握锉削知识。
(2)掌握平面锉削的方法和要领,并能达到平面锉削的精度要求。
具体要求
(1)掌握锉刀的握法。
(2)掌握锉刀的使用方法。
(3)掌握锉削的站立位置及锉削姿势。
(4)达到平面锉削的技术要求。
(5)锉削时的安全文明操作。
实习工件或对象
材料:
HT200规格:
80×50×40
教学环节
时间分配
组织教学时间5分
巡回指导时间260分
简明工艺分析时间45分
结束指导时间5分
操作要领讲解和演示时间45分
教学后记
实习前准备
材料
工具
量具
刃具
设备
其他
实习课题图:
平面锉削
教学过程
教学内容
组织教学
简明工艺分析
操作要领
讲解与演示
巡回指导
结束指导
集队、点名
检查学生劳防用品穿戴情况
锉削练习
基本知识
一、锉削的概述
锉削是用锉刀对工件表面进行切削加工的操作。
二、锉刀的构造
锉刀由优质碳素工具钢T12、T13、或T12A、T13A制成,经热处理后切削部分硬度达到62~72HRC,如图所示。
图
锉刀面是锉削的主要工作面它的前端做成凸弧形上下两面都有锉齿,便于锉削。
锉刀边是指两个侧面,有的没有齿,有的其中一边有齿。
没有齿的一边叫光边,锉削内直角的一个面时不会碰伤另一相邻的面。
舌是用来装锉刀柄的。
1.钳工锉
钳工锉是适用于加工、锉削金属零件的各种形式的锉刀。
按锉纹来分,可分为分粗锉、细锉;按锉刀断面的形状来分,可分为扁锉、方锉、圆锉、半圆锉、三角锉五种,如图所示。
图
2.特种锉
特种锉是适用于锉削零件上的特殊表面的锉刀,如图所示。
图
3.整形锉
整形锉适用于修整零件上的细小部位,它由若干把各种断面形状的锉刀组成一套,如图所示。
图
三、锉刀的规格
圆锉刀尺寸规格以其断面直径表示;方锉刀尺寸规格以其边长为尺寸表示;其他以锉身长度表示,钳工常用有100㎜、150㎜、200㎜、250㎜、300㎜、350㎜等,锉刀的齿纹规格一般有粗、中、细之分。
四、锉刀的选择
1.锉刀断面形状的选择
锉刀断面形状的选择一般取决于工件加工表面的形状,如图所示。
图
2.锉刀锉纹的选择
选择锉刀齿纹粗细主要取决于加工余量、尺寸精度和表面粗糙度要求,(见表5-1)。
表5-1锉刀齿纹的粗细规格选用
适用场合
锉纹种类
锉削余量/㎜
尺寸精度/㎜
表面粗糙度Ra/μm
粗
0.5以上
0.2~0.5
50~12.5
中
0.2~0.5
0.05~0.2
0.05~0.20
0.02~0.05
6.3~3.2
3.2~1.6
细
0.05以下
0.01
0.8~0.4
3.锉刀规格的选择
选择锉刀长度取决于工件加工面的大小,工件加工面越大,所选锉刀规格也大,反之可选小规格的锉刀。
五、锉削方法
锉削姿势正确与否,对锉削质量、锉削力的运用和发挥以及对操作时的疲劳程度都起着决定影响。
锉削姿势的正确掌握,必须从握锉、站立步位和姿势动作以及操作用力这几方面进行协调一致的反复练习才能达到。
1.锉刀柄的装拆方法如图所示。
a)b)
a)装锉刀柄的方法b)拆锉刀柄的方法
图
2.锉刀的握法
因锉刀的种类较多,所以锉刀的握法必须随着锉刀的大小,使用的地方不同而改变。
大于250㎜扁锉的握法,如图所示。
右手紧握锉刀柄,柄端抵住在拇指根部的手掌上,大拇指放在锉刀柄上部,其余手指由下而上地握着锉刀柄;左手的握法是将拇指的根部肌肉压在锉刀头上,拇指自然伸直,其余四指弯向手心,用中指、无名指捏住锉刀前端。
还有两种左手的握法如图所示。
小锉刀的握法,如图5-8所示,左手的握法是将拇指的根部肌肉压在锉刀头上,拇指向前自然伸直,其余四指弯向手心,用中指、无名指捏住锉刀前端。
右手推动锉刀并决定推动方向,左手协同右手使锉刀保持平衡。
图
图
3.锉削姿势
锉削时人的站立位置与錾削时相似,如图所示。
图
锉削时站立步位和姿势及锉削动作:
锉削时身体的重心要落在左脚上,右膝伸直,左膝随着锉削时的往复运动而屈伸。
在锉刀向前锉削的动作过程中,身体和手臂的运动情况如图所示。
两手握住锉刀放在工件上面,左臂弯曲,小臂与工件锉削面的方向保持基本平行,右小臂要与工件锉削面的前后方向保持基本平行,但要自然;锉削行程,身体先于锉刀一起向前,右脚伸直并稍向前倾,重心在左脚,左膝部呈弯曲状态;当锉刀锉至约四分之三行程时,身体停止前进,两臂则继续将锉刀向前锉到头,同时,左腿自然伸直并随着锉削时的反作用力,将身体重心后移,使身体恢复原位,并顺势将锉刀收回;当锉刀收回将结束,身体又开始先于锉刀前倾,作第二次锉削的向前运动。
图
4.锉削时两手的用力和锉削速度
要锉出平直的平面,必须使锉刀保持直线的锉削运动。
为此,锉削时右手的压力要随锉刀推动而逐渐增加,左手的压力要随锉刀推动而逐渐减小,回程时不加压力,以减少锉齿的磨损如图所示。
锉削速度一般应在40次/分左右,推出时稍慢,回程时稍快,动作要自然协调。
5.平面锉削法
(1)顺向锉法,如图所示,它是一种最普及的锉削方法,锉刀运动方向与工件夹持方向始终一致,在锉削宽平面时,为使整个加工表面能均匀地锉削,没次退回锉刀时应在横向作适当的移动,还能保证锉纹整齐一致。
(2)交叉锉法:
它是从两个交叉方向对工件进行锉削,如图所示。
锉削时锉刀与工件的接触面增大,锉刀容易掌握平稳。
由于交叉锉为粗锉,因此在锉削完成之前,仍要改用顺向锉法,使锉痕为正直且保持一致的方向。
(3)推锉法:
一般用来锉削狭长的平面,或用顺向锉在锉刀推进受阻时采用的一种补偿方法,如图所示。
6.锉刀的保养
(1)新锉刀要先使用一面,用钝后再使用另一面。
(2)在粗锉时,应充分使用锉刀的有效全长,既提高了锉削效率,又可使锉齿避免局部磨损。
(3)锉刀上不可沾油与沾水。
(4)如锉屑嵌入齿缝内必须及时用钢丝刷沿着锉齿的纹路进行清除。
(5)不可锉毛坯件的硬皮及经过淬硬的工件。
(6)铸件表面如有硬皮,应先用砂轮磨去或用旧锉刀和锉刀的有齿侧边锉去,然后再进行正常锉削加工。
(7)锉刀使用完毕时必须清刷干净,以免生锈。
(8)无论在使用过程中或放入工具箱时,不可与其它工具或工件堆放在一起,也不可与其它锉刀互相重迭堆放,以免损坏锉齿。
注意:
1.锉削是钳工的一项重要基本操作。
正确的姿势是掌握锉削技能的基础,因此要求必须练好。
2.初次练习,会出现各种不正确的姿势,特别是身体和双手动作不协调,要随时注意及时纠正,若要让不正确的姿势成为习惯,纠正就困难了。
3.在练习姿势动作时,也要注意掌握两手用力如何变化才能使锉刀在工件上保持直线的平衡运动。
六、平面锉削
1.锉平平面的练习要领
用锉刀锉平平面的技能技巧必须通过反复的、多样性的刻苦练习才能形成。
而掌握要领的练习,可加快技能技巧的形成。
(1)掌握好正确的姿势和动作。
(2)做到锉削力的正确和熟练运用,使锉削时保持锉刀的直线平衡运动。
因此在操作时注意力要集中,练习过程要用心研究。
(3)练习前了解几种平面不平的具体形式和原因便于练习中分析改进(见表)。
表5-2平面不平的形式和原因
形式
产生的原因
平面中凸
1.锉削时双手的用力不能使锉刀保持平衡
2.锉刀在开始推出时,右手压力太大,锉刀推到前面,左手压力太大,锉刀被压下,造成前、后面多锉
3.锉削姿势不正确
4.锉刀自身中凹
对角扭曲或塌角
1.左手或右手施加压力时重心偏向锉刀一侧
2.工件未夹正确
3.锉刀自身扭曲
平面横向中凸中凹
锉刀在锉削时左右移动不均匀
2.检查平面度的方法
锉削工件时,由于锉削平面较小,其平面度通常都采用刀口直尺(或钢尺)通过透光法来检查。
检查时刀口直尺应垂直放在工件表面上,如图5-15a所示,并在加工面的纵向、横向、对角方向多次逐一进行,如图所示,以确定各方向的直线度误差。
如果刀口直尺与工件平面间透光微弱而均匀,说明该方向是直的;如果透光微弱而不一,说明该方向不直的;平面度误差值的确定,可用厚簿规(塞尺)作塞入检查。
对于中凹平面,其平面度误差可取各检查部位中的最大直线度误差值计;对于中凸平面,则应在两边以同样厚度的塞尺作塞入检查,其平面度误差可取各检查部位中的最大直线度误差值计,如图所示。
图
刀口直尺在被检查平面上改变位置时,不能在平面上拖动,应提起后再轻放到另一检查位置。
否则直尺的测量棱边容易磨损而降低其精度。
厚薄规是用来检查两个结合面之间间隙大小的片状量规,如图所示。
使用时根据被测间隙的大小,可用一片或数片重迭在一起作塞入检查,并须作两次极限尺寸的检验后才能得出其间隙的大小。
厚薄规的塞片很薄,容易弯曲和折断,所以测量时不能用力太大。
用毕后要擦拭干净,及时合到夹板中去。
图
3.锉削缺陷分析与纠正(见表5-3)
表5-3缺陷和产生原因
锉削缺陷及现象
产生原因
纠正措施
工件被夹坏
精加工过的表面被台虎钳口夹出伤痕
主要是因台虎钳口没有加护口或衬垫较软材料;有时虽有护口,如果工件较软而夹紧力过大,也会使工件表面夹坏
1.在夹紧工件时加护口衬垫
2.夹紧时夹紧力不要过大
空心工件被夹扁
夹紧力太大或直接用台虎钳口夹紧而变形
夹紧时夹紧力不要过大
尺寸和形状不准确
锉削时尺寸和形状尚未达到要求,但是已经没有加工余量了
除由于划线不正确或锉削时检查测量有误差外,主要是锉削加工量过大而又未及时检查,导致锉过了尺寸界限
1.提高划线精度
2.用量具经常测量加工尺寸
锉削平面出现中凸
由于操作技术不高或选用了虽然经过修整但是仍然存在中凹、不符合加工要求的锉刀,而使锉削的平面产生中凸。
有时也会造成废品
1.提高锉削技能
2.调整锉削方法
相邻面被锉坏
在锉削角度面时不细心,锉削动作过大,把已锉好的相邻面锉坏
修磨锉刀侧面
(小于90°)
表面粗糙
在精锉时仍采用较粗齿的锉刀
正确选用锉刀粗细规格
粗锉时锉痕太深,造成精锉时无法锉去齿痕
控制粗锉的尺寸
切屑嵌在锉刀纹中未及时清除,而把被锉削表面拉毛
及时清理锉刀上铁屑
在锉削直角面时,锉刀没有经过修磨过
修磨锉刀侧面
七、安全文明操作
(1)锉刀是右手工具,应放在台虎钳的右面,放在钳台上时锉刀柄不可露在钳桌外面,以免碰落地上砸伤脚或损坏锉刀。
(2)没有装柄的锉刀,锉刀柄已开裂或没有锉刀柄箍的锉刀不可使用。
(3)锉削时锉刀柄不能撞击到工件,以免锉刀柄脱落造成事故。
(4)不能用嘴吹锉屑,也不能用手擦摸锉削表面。
(5)锉刀不可作撬棒或手锤用。
(6)锉刀不得沾水和沾油。
锉屑嵌入齿缝必须用钢刷清除,不允许用手直接清除。
八、技能训练步骤
1.锉削姿势
(1)将实习件正确装夹在虎钳中间,锉削面高出钳口面约15㎜。
(2)用旧的300㎜粗扁锉,在实习件凸起的阶台上作锉削姿势练习。
开始采用慢动作练习,初步掌握后再作正常速度练习,要求全部采用一种握法,做顺向锉削。
(3)应自然地将锉刀握正、握稳,眼睛的视线要对着工件的锉削部位,锉削时主要应靠掌握和控制好手的运动轨迹及其位置来达到。
(4)要及时纠正自已的错误姿势,不能让不正确的姿势成为习惯,否则以后再纠正就困难了。
下面所列几种错误姿势,必须注意避免。
注意:
1.握锉刀柄握得过紧与锉削速度太快。
2.锉削时由于左手、右手、身体、两脚动作不协调,操作易疲劳。
3.锉削时两手用力变化没有配合好,手握锉刀运动不平稳。
4.站立位置和身体姿势不正确。
2.平面锉削
(1)用300㎜粗扁锉,加工基准面A面,达到平面度≤0.15㎜,表面粗糙度≤6.3μm。
(2)加工与基准面A面相垂直的第二基准面B面,达到平面度≤0.10㎜,与基准面A面的垂直度≤0.10㎜,表面粗糙度≤6.3μm。
(3)加工与基准面A面相平行的对平面,达到尺寸精度为30±0.20㎜,平面度≤0.15㎜,与基准面A面的平行度≤0.15㎜,表面粗糙度≤6.3μm。
(4)加工与基准面A面、基准面B面相垂直的第三基准面C面,达到对基准面A面、基准面B面垂直度≤0.10㎜、平面度≤0.10㎜、表面粗糙度≤6.3μm。
(5)用300㎜粗扁锉全面精度复检,并作必要的修整锉削,最后将各锐边均匀倒钝。
注意:
1.工件必须夹紧,伸出钳口高度一般在10—15㎜为宜。
2.锉屑要用刷子刷掉,不得用手擦或用嘴吹。
3.锉刀上不可沾油与沾水。
4.如锉屑嵌入齿缝内必须及时用钢丝刷沿着锉齿的纹路进行清除。
5.不可锉毛坯件的硬皮及经过淬硬的工件。
6.锉刀使用完毕时必须清刷干净,以免生锈。
(1)锉削姿势。
(2)锉平平面的练习要领。
(3检查平面度的方法。
(4)安全文明操作
1.注意学生在实习过程的每个细节,如有错误,及时加以纠正。
2.对学生不能理解的地方,再重复讲解一次,确保学生能真正掌握技能。
3.检查学生在生产实习中的安全文明生产,如有问题,及时加以纠正。
4.对学生的操作,加以评分,并备录在案。
1、总结一天实习情况,对好的学生加以表扬,对表现不好的学生加以批评。
2、对学生在实习过程中,出现过的问题进行讲评,使学生加深印象。
3、重申安全文明生产的重要性。