20万吨高塔造粒颗粒硝酸铵工艺安全操作规程.docx
《20万吨高塔造粒颗粒硝酸铵工艺安全操作规程.docx》由会员分享,可在线阅读,更多相关《20万吨高塔造粒颗粒硝酸铵工艺安全操作规程.docx(31页珍藏版)》请在冰豆网上搜索。
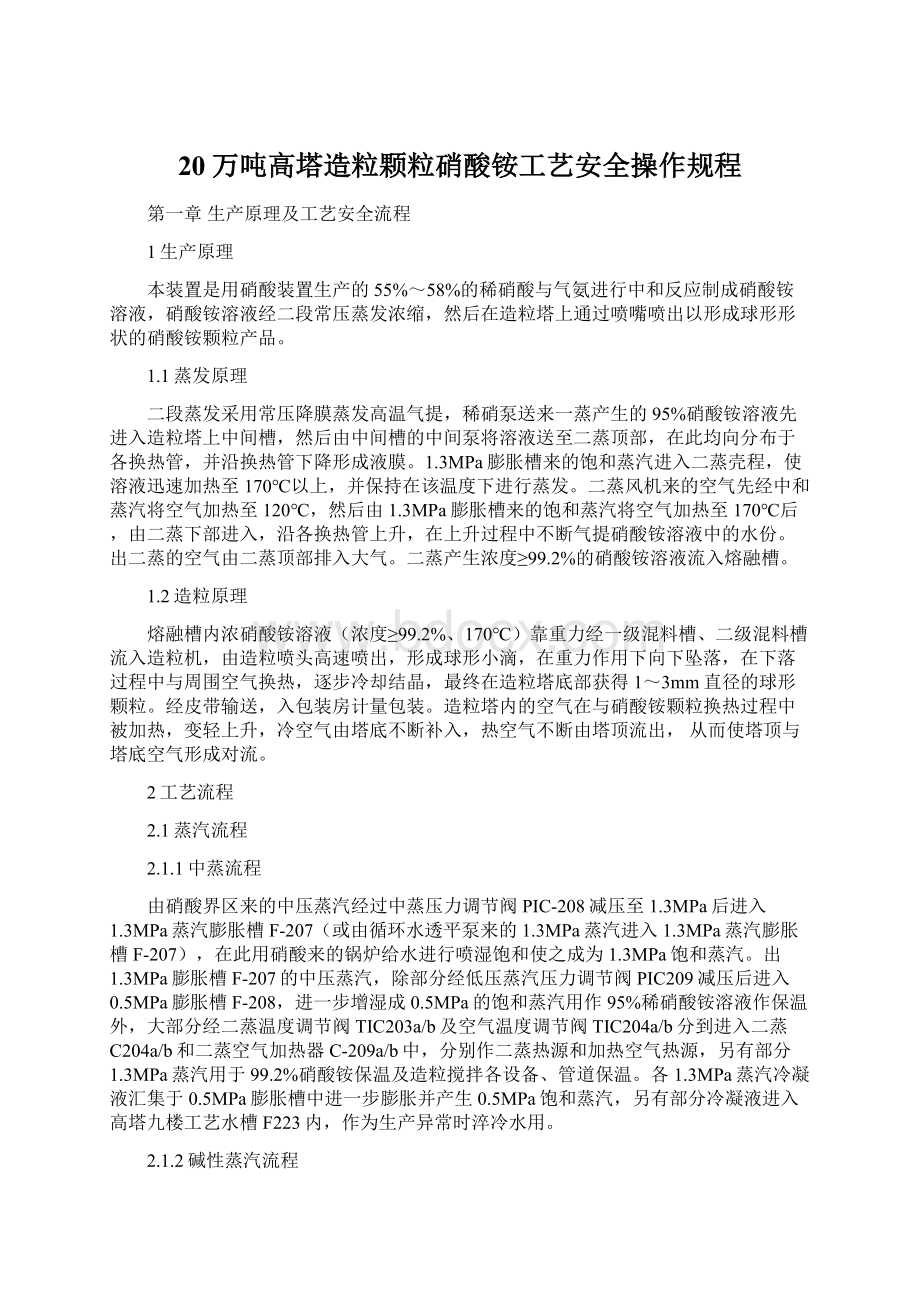
20万吨高塔造粒颗粒硝酸铵工艺安全操作规程
第一章生产原理及工艺安全流程
1生产原理
本装置是用硝酸装置生产的55%~58%的稀硝酸与气氨进行中和反应制成硝酸铵溶液,硝酸铵溶液经二段常压蒸发浓缩,然后在造粒塔上通过喷嘴喷出以形成球形形状的硝酸铵颗粒产品。
1.1蒸发原理
二段蒸发采用常压降膜蒸发高温气提,稀硝泵送来一蒸产生的95%硝酸铵溶液先进入造粒塔上中间槽,然后由中间槽的中间泵将溶液送至二蒸顶部,在此均向分布于各换热管,并沿换热管下降形成液膜。
1.3MPa膨胀槽来的饱和蒸汽进入二蒸壳程,使溶液迅速加热至170℃以上,并保持在该温度下进行蒸发。
二蒸风机来的空气先经中和蒸汽将空气加热至120℃,然后由1.3MPa膨胀槽来的饱和蒸汽将空气加热至170℃后,由二蒸下部进入,沿各换热管上升,在上升过程中不断气提硝酸铵溶液中的水份。
出二蒸的空气由二蒸顶部排入大气。
二蒸产生浓度≥99.2%的硝酸铵溶液流入熔融槽。
1.2造粒原理
熔融槽内浓硝酸铵溶液(浓度≥99.2%、170℃)靠重力经一级混料槽、二级混料槽流入造粒机,由造粒喷头高速喷出,形成球形小滴,在重力作用下向下坠落,在下落过程中与周围空气换热,逐步冷却结晶,最终在造粒塔底部获得1~3mm直径的球形颗粒。
经皮带输送,入包装房计量包装。
造粒塔内的空气在与硝酸铵颗粒换热过程中被加热,变轻上升,冷空气由塔底不断补入,热空气不断由塔顶流出,从而使塔顶与塔底空气形成对流。
2工艺流程
2.1蒸汽流程
2.1.1中蒸流程
由硝酸界区来的中压蒸汽经过中蒸压力调节阀PIC-208减压至1.3MPa后进入1.3MPa蒸汽膨胀槽F-207(或由循环水透平泵来的1.3MPa蒸汽进入1.3MPa蒸汽膨胀槽F-207),在此用硝酸来的锅炉给水进行喷湿饱和使之成为1.3MPa饱和蒸汽。
出1.3MPa膨胀槽F-207的中压蒸汽,除部分经低压蒸汽压力调节阀PIC209减压后进入0.5MPa膨胀槽F-208,进一步增湿成0.5MPa的饱和蒸汽用作95%稀硝酸铵溶液作保温外,大部分经二蒸温度调节阀TIC203a/b及空气温度调节阀TIC204a/b分到进入二蒸C204a/b和二蒸空气加热器C-209a/b中,分别作二蒸热源和加热空气热源,另有部分1.3MPa蒸汽用于99.2%硝酸铵保温及造粒搅拌各设备、管道保温。
各1.3MPa蒸汽冷凝液汇集于0.5MPa膨胀槽中进一步膨胀并产生0.5MPa饱和蒸汽,另有部分冷凝液进入高塔九楼工艺水槽F223内,作为生产异常时淬冷水用。
2.1.2碱性蒸汽流程
出中和器的废热蒸汽(0.36MPa,140℃),用于二蒸空气加热器C-209a/b一段,作空气预加热热源,用于将空气从常温加热至120℃,换热后中和冷凝液汇集于中和冷凝液闪蒸槽F-211中。
2.2硝酸铵溶液流程
稀硝槽F-204中95%的硝酸铵溶液由稀硝泵P202a/b升压后,经稀硝槽液位调节阀LIC205调节后送入造粒塔上六楼中间槽,然后由中间泵a/b将溶液送至二段蒸发器C204a/b顶部。
进二段蒸发器的硝酸铵溶液在二段蒸发器顶部均匀分布,沿各换热管溢流,沿管壁向下形成液膜,在二段蒸发器壳程由1.3MPa蒸汽加热至170℃以上,并保持在170℃。
空气先经过风机进口过滤网除去其中的固体杂质,再由二蒸风机P-214a/b升压后进入空气加热器C-209a/b,经两段加热(一段采用中和废热蒸汽、二段采用1.3MPa中压蒸汽)后,温度上升至170℃,进入二蒸底部后沿各换热管上升,与从上而下的硝酸铵溶液逆流接触,硝酸铵中的大部分水份被蒸发进入气相,蒸发所需热量由壳程的1.3MPa中蒸提供,出二段蒸发器废汽从二段蒸发器顶部排入大气中,出二蒸的硝酸铵溶液浓度达99.2%以上,温度170℃,在重力作用下流入熔融槽F-206。
靠重力经一级混料槽、二级混料槽流入造粒机,由造粒喷头高速喷出,形成球形小滴,在重力作用下向下坠落,在下落过程中与周围空气换热,逐步冷却结晶,最终在造粒塔底部获得1~3mm直径的球形颗粒。
2.3氨流程
气氨经气氨过滤器G-201除去其中的油雾后进入气氨过热器C-202,在此利用中和器出口废热蒸汽预热至70℃,然后由DN25管线送至高塔界区内,分别进入中间槽、喷头处和熔融槽加氨口,作生产过程硝酸铵溶液及成品pH调整用。
2.4空气流程
空气先经过风机进口过滤网除去其中的固体杂质,再由二蒸风机P-214a/b升压后进入空气加热器C-209a/b,经两段加热(一段采用中和废热蒸汽、二段采用1.3MPa中压蒸汽)后,温度上升至170℃,进入二蒸底部后沿各换热管上升,与从上而下的硝酸铵溶液逆流接触,蒸发提浓硝酸铵溶液浓度,出二段蒸发器的废汽从二段蒸发器顶部排入大气中。
2.5二蒸流程
二段蒸发采用常压降膜蒸发高温气提,稀硝泵送来一蒸产生的95%硝酸铵溶液先进入造粒塔上中间槽,然后由中间槽的中间泵将溶液送至二蒸顶部,在此均向分布于各换热管,并沿换热管下降形成液膜。
1.3MPa膨胀槽来的饱和蒸汽进入二蒸壳程,使溶液迅速加热至180℃并保持在该温度下进行蒸发。
二蒸风机来的空气先经中和蒸汽将空气加热至120℃,然后由1.3MPa膨胀槽来的饱和蒸汽将空气加热至180℃后,由二蒸下部进入,沿各换热管上升,在上升过程中不断气提硝酸铵溶液中的水份。
出二蒸的空气由二蒸顶部排入大气。
二蒸产生99.8%的硝酸铵溶液流入熔融槽。
由于浓硝酸铵溶液浓度很高,为防止其固化溶液温度必须保持在180℃左右。
而高浓度与高温度的结合意味着硝酸铵距分解的安全区域相对较小,因而必须严格操作以防可能出现分解爆炸。
因此,在任何时候都不能使硝酸铵溶液过热,这就是为什么要使用1.3MPa饱和蒸汽的原因,因该蒸汽具有稳定的温度195℃。
实际操作时该压力略低于1.3MPa,但应保证蒸汽温度在190℃~195℃之间,若蒸汽温度升至200℃,则系统会联锁并停止二蒸系统。
2.6包装流程
由造粒喷头高速喷出1~3mm直径的球形颗粒在塔内经换热冷却后落入塔底料斗收集皮带a、b、c内,后汇总于输送皮带d,再经斜皮带i进入输送皮带h后流入2#包装机或经包装三楼分料皮带流入1#包装机,经称重缝包过金检机检测合格后入库。
2.7水流程
2.7.1脱盐水流程
由硝酸工艺水泵加压后送至高塔六楼和九楼工艺水槽F223内,分别用于中间泵泵冷却水和异常情况淬冷水用。
2.7.2消防水流程
由循环水站高塔专用消防泵加压后送至塔顶消防水箱内,然后由消防水箱底部分别进入各楼层消防栓内,供消防设施用,另高塔七楼消防栓前引管至一级混料槽和二级混料槽,风别用阀门进行单独控制,以备出现温度异常情况时作淬冷水用。
2.8仪表空气流程
仪表空气由硝酸界区仪表空气缓冲罐出口送至高塔界区内,在高塔六楼管道井处设有DN80总阀,后分别送入各调节阀和仪表空气用户。
第二章二段蒸发岗位职责及操作
1岗位任务
将稀硝泵送来一蒸产生的95%硝酸铵溶液采用二段蒸发(即常压降膜蒸发高温气提)形成99.2%硝酸铵溶液经造粒喷头造粒喷出。
本岗位管辖的设备主要包括中间槽、中间泵、空气加热器、二段蒸发器、二蒸风机、熔融槽、二蒸冷凝液槽、造粒机及其相关管线。
2开停车程序
2.1开车准备
2.1.1检查各脱盐水用户阀门是否已关闭后,联系主控送脱盐水上塔。
2.1.2检查主控室二蒸操作电脑、配料系统操作电脑、二蒸系统仪表控制柜、配料系统仪表控制柜、斗提机及二蒸风机变频控制柜、一级混料槽及二级混料槽控制柜和造粒机控制柜正常且已通电。
2.1.3检查以下各阀必须开启:
2.1.3.1中间槽和熔融槽保温盘管蒸汽阀。
2.1.3.2中间泵出口AN管夹套蒸汽及冷凝液阀(冷凝液阀只开1~2圈即可)。
2.1.3.3TV-203a/b前后截止阀及疏水阀主线。
2.1.3.4TV-204a/b前后截止阀及疏水阀主线。
2.1.3.5二蒸冷凝液槽LV218a/b前后截止阀。
2.1.3.6XV204淬冷水阀前截止阀及熔融槽顶部球阀。
2.1.3.7碱性蒸汽总阀及碱性冷凝液阀,其冷凝液阀需全开。
2.1.3.8空气加热器C209a/b中压蒸汽排水阀及疏水阀主线,碱性蒸汽排水阀。
2.1.3.9中间槽硝酸铵溶液入口管和硝酸铵溶液溢流管,夹套蒸汽阀、冷凝液阀(冷凝液阀只开1-2圈即可)及中间槽入口管和溢流管吹扫阀。
2.1.3.10中间泵出口至二段蒸发器a/b管道、二段蒸发器a/b出口至熔融槽管道、熔融槽溢流管、熔融槽至一级混料槽、一级混料槽至二级混料槽、二级混料槽至造粒机夹套蒸汽阀、冷凝液阀(冷凝液阀只开1-2圈即可)及其吹扫阀。
2.1.4检查各加氨管线是否通畅,各加氨阀是否已关死。
2.1.5检查熔融槽顶部手动补水阀以关死。
2.1.6检查中间槽硝酸铵溶液入口管、中间槽硝酸铵溶液溢流管、中间泵出口至二段蒸发器a/b管道、二段蒸发器a/b出口至熔融槽管道、熔融槽溢流管、熔融槽至一级混料槽、一级混料槽至二级混料槽、二级混料槽至造粒机、中间泵出口至七楼阀门组管道是否通畅。
2.1.7检查风机润混油是否足够,同时盘车致少一圈确认无卡塞后启动风机。
2.1.8检查中间泵是否完好,同时盘车致少一圈确认无卡塞现象。
2.1.9检查造粒机是否安装完好,喷头是否清洗干净,喷头孔径安装是否正确,并通电运行查看喷头运转情况是否正常(特别是方向及电机完好性)。
2.1.10主控人员检查控制系统是否完好,并进行二蒸连锁试验,检查确认各连锁阀动作是否正确、到位。
2.1.11检查六楼、七楼、八楼排气扇是否完好,并启动排风扇。
2.1.12检查消防水箱液位是否足够(大于等于1.2m),工艺水槽液位是否足够(大于等于40%以上)。
2.1.13联系包装岗位确认准备工作完成后,适当开启塔底两导淋阀(导淋阀只开1~2圈即可),到塔底管廊平台分别引中压蒸汽和碱性蒸汽及气氨上塔;
注:
在送汽时注意要缓慢开启中压蒸汽总阀和碱性蒸汽总阀,缓慢进行预热,切记过快过猛。
2.2正常开车
2.2.1中压蒸汽和碱性蒸汽上塔后,主控人员投用二蒸连锁,并手动微开TIC-204a/b、TIC-203a/b以预热管道,预热充分后分别设定170℃投自动。
2.2.2待空气加热器出口温度TIC-204a/b和二段蒸发器底部TIC-203a/b温度达到140℃以上后,联系硝酸铵岗位送硝酸铵溶液到中间槽,同时关闭中间槽硝酸铵溶液入口管和溢流管吹扫阀。
2.2.3待中间槽液位至少50%时,关闭中间泵出口阀和中间泵出口至二段蒸发器a/b管道、二段蒸发器a/b出口至熔融槽管道、熔融槽溢流管、、中间泵出口至七楼阀门组管道吹扫阀,稍开回路阀(回路阀不可开的过大,否则回流泵转速过快易造成叶轮松动,回路阀开度以泵1~2转/秒为宜),同时打开中间泵冷却水,经盘车后启动中间泵。
主控人员打开HV205a/b向二段蒸发器送硝酸铵溶液(阀门开度由小逐渐增大,一般不得超过50%阀位)。
并打开中间槽加氨阀(开度大小以六楼无明显氨味为准)。
2.2.4当熔融槽内建立液位后主控人员应全开LV-206,使硝酸铵溶液在稀硝槽→中间槽→中间泵→二蒸→熔融槽→中间槽之间循环提浓(俗称小循环),当中间槽开始溢流时,使硝酸铵溶液在稀硝槽→中间槽→中间泵→二蒸→熔融槽→中间槽→稀硝槽之间循环提浓(俗称大循环)。
同时打开熔融槽加氨阀。
注:
(1)主控人员密切关注熔融槽内液位,当液位达到95%时,要立即通知现场人员到回流视镜处查看硝酸铵溶液是否回流;
(2)当中间槽液位达到90%时,现场人员要到六楼查看中间槽溢流管是否正常,以防止管道堵塞冒槽。
2.2.5当二段蒸发器底部TV-203a/b和熔融槽温度达到170℃至少5分钟时准备造粒,同时通知包装班组人员做好准备工作。
2.2.6关闭熔融槽至一级混料槽、一级混料槽至二级混料槽、二级混料槽至造粒机管道吹扫阀,手动全开HV-202前截止阀。
2.2.7按程序启动造粒喷头,同时手动打开HV20230%开度,并逐渐增大至规定负荷。
2.2.8开始造粒后,到高塔六楼下一层观察孔内观察喷头喷料情况是否正常,同时取成品样检测pH值,并根据检测结果及时调整加氨阀开度,确保pH值在4.5~6.5之间。
2.2.9包装开始包装下料后,及时进行重量抽检,确保重量合格。
2.2.10根据塔下物料颗粒情况适时调整喷头频率(喷头频率与转速对应关系为1赫兹9转)。
2.2.11根据负荷大小,开大或关小中间泵出口至二段蒸发器HV205阀位的大小来调节二蒸加、减负荷,在加减负荷过程中熔融槽液位必须控制在50-60%,同时确保熔融槽及二段蒸发器底部温度TIC-203a/b在170℃以上。
2.3正常停车
2.3.1根据指令和负荷大小,逐渐减小中间泵至而段蒸发器HV205阀门的开度,将进二段蒸发器负荷减到最小。
2.3.2通知硝酸铵主控停止向中间槽送硝酸铵溶液,同时并监控好熔融槽及二段蒸发器底部温度TIC-203a/b在170~180℃,以防发生二蒸联锁。
并关闭中间槽保温盘管,打开中间槽硝酸铵溶液入口管和硝酸铵溶液溢流管吹扫阀。
2.3.3待中间槽、熔融槽内溶液造粒完毕后,停中间泵,(中间槽液位泵至30%、熔融槽液位降至15%时),关闭负荷阀HV202及其前总阀,手动全开进二段蒸发器负荷调节阀HV205,同时手动打开熔融槽顶部加水发,待熔融槽内温度降低80℃时关闭加水阀。
2.3.4关闭熔融槽、中间槽加氨阀;
2.3.4打开中间泵出口至二段蒸发器a/b管道、二段蒸发器a/b出口至熔融槽管道、熔融槽溢流管、熔融槽至一级混料槽、一级混料槽至二级混料槽、二级混料槽至造粒机、中间泵出口至七楼阀门组管道蒸汽吹扫阀,将管道内溶液吹扫干净。
2.3.5包装班组人员接停车通知后,造粒塔停止造粒后,将料仓内物料称重包装完入库,随后依次停止高塔底部塔底料斗收集皮带a、b、c、汇总、皮带d、斜皮带i、输送皮带h、包装三楼分料皮带及包装机、缝包机、折边机、喷码机、金检机,并打扫现场卫生。
2.3.6管道吹扫完毕后关闭中间泵出口至二段蒸发器a/b管道、二段蒸发器a/b出口至熔融槽管道、熔融槽溢流管、熔融槽至一级混料槽、一级混料槽至二级混料槽、二级混料槽至造粒机、中间泵出口至七楼阀门组管道蒸汽吹扫阀,停二蒸风机,主控人员将各调节阀阀位全关,到塔底管廊平台关闭中压蒸汽、碱性蒸汽及气氨管线总阀。
2.3.7停至六楼、七楼、八楼排气扇,关闭中间泵冷却水。
2.4事故停车处理
2.4.1二蒸系统联锁停车
2.4.1.1当二蒸系统发生联锁时,应立即到现场快速手动开熔融槽脱盐水阀以降温,通知停止造粒。
同时手动关闭HV-202并立即到现场查看TV-203a/b、TV-204a/b、LV206是否已关闭,若没有关闭应快速手动关闭其前后截止阀;HV205是否全开,XV-204是否已全开;二蒸风机和中间泵是否已停止运行,若没有停则立即手动停止运行。
2.4.1.2立即打开喷头吹扫蒸汽,待联锁解除后重新提浓后重新造粒,其开车程序同2.1~2.11。
2.4.1.3通知包装班组人员做好再次开车相关准备工作。
2.4.2断仪表空气或断电
4.2.1当二蒸系统出现断空气、断电时应立即通知主控人员立即按二蒸联锁时的处理程序立即处理,待空气或电恢复后重新开车。
2.4.2.2若故障暂时无法处理,暂不能再次开车情况,则按正常停车程序进行处理,待空气或电恢复后重新开车。
2.4.3熔融槽、二段蒸发器底部TV-203a/b超温
2.4.3.1当熔融槽、二段蒸发器底部TV-203a/b超温时,立即通知主控人员立即按二蒸联锁时的处理程序立即处理,同时立即向熔融槽加脱盐水直到熔融槽内温度降到170℃以下时停止加水。
同时关闭负荷阀HV202,立即打开喷头吹扫蒸汽,待联锁解除后重新提浓后重新造粒,其开车程序同2.1~2.11。
2.4.4造粒机喷头故障。
2.4.4.1立即停止在造粒喷头,关闭负荷阀HV-202前总阀,开HV-202阀前吹除蒸汽吹除3~5分钟后关闭该蒸汽。
2.4.4.3待喷头无料时开喷头蒸汽吹除3~5分钟后关闭该蒸汽。
2.4.4.4通知主控人员使硝酸铵溶液在中间槽→中间泵→二蒸→熔融槽→中间槽之间打循环,并控制温度在170℃以内,并配合机修更换喷头修复后准备重新开车。
2.4.4.5若故障暂时无法处理,暂不能再次开车情况,则按正常停车程序进行处理,待故障修复后重新开车。
2.5二蒸连锁
本装装置采用二段蒸发,高温气提以达到很高的硝酸铵浓度。
而硝酸铵溶液高浓度与高温度的结合,意味着只有很窄的安全范围,因此特设有二蒸联锁。
2.5.1出现以下情况时二蒸联锁会自动启动。
(1)中压蒸汽温度TI5218≥200℃
(2)二蒸蒸发温度TIC5203a/b≥185℃
(3)熔融槽温度TI-5211≥185℃
(4)二蒸空气温度TIC5204a/b≥185℃
(5)一级混料槽温度≥185℃
(6)二级混料槽温度≥185℃
2.5.2二蒸联锁时除联锁动作,各联锁阀动作如下:
自动关闭:
二蒸空气温度调节阀TIC203a/b、二蒸温度调节阀TIC204a/b。
自动打开:
熔融槽槽淬冷水阀XV204、熔融槽槽液位调节阀LIC206、进二蒸负荷阀HV205a/b。
手动打开:
熔融槽顶部手动淬冷水阀,关闭负荷阀HV202。
3.常见故障处理
故障
原因
处理
中间泵异响
泵出口及副线阀开得过大
关小出口及副线阀
机械故障(比如轴承坏)
倒泵后联系机修工维修
断冷却水或冷却水开得太小
加大冷却水阀开度
中间泵不起压
中间槽液位过低(低于30%)
联系主控提高中间槽液位
中间泵入口短节垫子坏(漏气)
联系机修更换垫子
中间泵到出口阀间短节堵管
联系机修折下短节用蒸汽吹通
中间泵跳车
泵体内有异物卡死中间泵
联系机修处理
出口阀开得过大导致泵超电流
启备泵关小出口阀后,联系电工处理
轴承坏把轴卡死
联系机修处理
中间槽液位波动大
LI-217出现假液位
联系仪表调校液位计
LV-205或LV-206故障
联系仪表调校该调节阀
中间泵跳车或堵管
重启中间泵或吹堵
熔融槽液位波动大
LV-206出现假液位
联系仪表调校液位计
LV-206或HV-202故障
联系仪表调校该调节阀
中间泵出口或副线阀开得过大或过小
调整中间泵出口或副线阀
二蒸温度提不够
1.3MPa膨胀槽压力、温度不够
联系调度提中蒸压力、减小膨胀槽喷水
二蒸负荷过大
关小中间泵出口或副阀
TV-203a/b调节阀故障
联系仪表校该调节阀或开该调节阀副线阀和疏水阀副线
TV-204a/b调节阀故障
中蒸冷凝液疏水阀故障(有渣子堵死)
联系钳工更换或维修疏水阀
二蒸风机出、入口压差过大
调节风机入口导叶使压差在指标范围内
中间槽内硝酸铵溶液浓度不够
调整一蒸真空
造料机异响
内圈或外圈电机各轴承坏或缺油
更换喷头后联系电工检修
内圈或外圈的减速器齿轮缺油
联系机修对减速器齿轮箱加油
电机风叶有擦、刮现象
联系电工检修
造料喷头堵
喷头内渣子过多堵住喷头各小孔
更换喷头并清洗
喷头使用时间过长堵塞
更换喷头并清洗
喷头跳车
有物料喷头运动部件卡死
停造粒后用蒸汽吹除喷头3-5分钟后,重新投造粒
有其它异物把喷头内圈卡死
更换喷头并清洗
4安全注意事项
4.1每次开车前必须对二蒸联锁进行模拟试验(空投试验)确保正常生产时灵敏、准确、好用。
42在发生联锁时,应立即检查各阀位是否动作,同时确认淬冷水正加入硝酸铵熔融槽。
若联锁后硝酸铵熔融槽温度仍继续上升,应立即打开脱盐水槽到硝酸铵熔融槽的淬冷水手动阀。
4.3二蒸系统的中压蒸汽温度、二蒸蒸发温度、硝酸铵熔融槽温度、二蒸空气温度高联锁,在达到联锁值时联锁未动作时,应立即手动启动二蒸联锁以确保装置安全。
4.4接受蒸汽时,应先开导淋阀排尽冷凝液,严防水击损坏设备、管道和阀门。
4.5硝酸铵对于震动、冲击或磨擦不敏感,也没有自燃的性质,但硝酸铵在有机物、无机物和金属粉末的存在下易引起火灾。
若各储槽内硝酸铵复合肥料浆出现着火现象时时,要及时采用加水控制火情并立即用水扑火。
4.6每小时对生产现场巡查一次,检查各设备、容器的压力、温度,严禁超温超压。
4.7巡检时上下楼梯应注意安全,防止踏空、摔跤等。
4.8在检查转动设备时,应规范佩戴安全帽,正确处理好头发、工作服、手套等,避免卷入转动设备中。
现场的蒸汽管道较多,巡检或操作时应注意防止被烫伤。
4.9要监控中间槽、熔融槽硝酸铵溶液的pH值在4.5-6.0,确保产品质量,同时防止因溶液酸化导致硝酸铵分解发生安全事故。
4.10当溶液管道出现堵塞时,在吹扫管道时,应在管道堵塞处的下部进行蒸气吹扫,吹扫出的溶液要能自动排走,以防局部过热,出现爆管和人身伤亡事故。
4.11严格执行开停车操作规程,确保人身与设备安全。
第三章成品包装岗位
1岗位任务与职责
由造粒喷头高速喷出1~3mm直径的球形颗粒在塔内经换热冷却后落入塔底料斗收集皮带a、b、c内,后汇总于输送皮带d,再经斜皮带i进入输送皮带h后流入2#包装机或经包装三楼分料皮带流入1#包装机,经称重缝包过金检机检测合格后入库。
2本岗位主要设备
塔底收集皮带a、b、c,汇总皮带d,斜皮带i,输送皮带h,1#、2#包装机,1#、2#金检机,叉车
3开停车程序
3.1开车前的检查准备工作
进行下列项目操作之前,务必对本岗位设备的减速机、轴承进行检查注油,并注油至设备要求的正常油位。
3.1.1领取颗粒硝铵的合格包装袋,并定置摆放到相应位置。
3.1.2检查自动称重包装系统是否正常,并对其进行校准,称重传感器的盖板必须盖好,不允许随意取下盖板。
3.1.3检查仪表空气压力是否满足生产要求,,气压不足时,及时通知空压站调整压力。
3.1.4检查、调节喷码机是否工作正常,喷码设置是否符合规定要求。
3.1.5检查折边机、缝包机是否能够正常工作,缝纫针是否穿线,缝包线的张紧度是否合乎要求。
3.1.6检查各皮带是否皮运转正常。
3.1.7检查高塔底部塔底料斗收集皮带a、b、c、汇总、皮带d、斜皮带i、输送皮带h、包装三楼分料皮带及包装机、缝包机、折边机、喷码机、金检机是否正常,各润滑部位润滑油是否充足,并依次启动上述设备。
注:
在此过程中,包装班组人员要和仪表人员共同对包装称重系统进行校验并合格。
3.1.8检查确认转运叉车是否能够正常运行。
3.2放料
3.2.1料仓内物料达到一定量后即可开始放料,但物料不得超过料仓的1/2。
3.2.2放料时如发现成品粒度异常或水份高,禁止包装成成品。
3.2.3放料时如有金检机报警时,必须立即停止放料,并对报警产品重新过金检机,如果再次报警,做废料处理。
3.2.4经常检查料仓料位情况,禁止出现溢仓现象,交班时必须清仓。
3.2.5当料仓无料时,放料结束;及时对所属设备进行维护保养并清理现场卫生。
3.2.6当班期间定时对产品重量进行沉重自检,确保重量符合要求,否则停止包装成品,联系仪表人员对包装称进行校称。
3.3折边、缝包
3.4.1将内膜袋扎好口的包装袋口部抻直,平稳的输送到折边机。
3.4.2经过折边的包装袋由缝包机自动缝包,自动切线。
缝线要直,不允许出现斜线和折皱。
3.4.3对缝线弯曲、斜角或未缝上线的包装袋应及时取下,重新缝包。
3.4.4对线辫过长的应及时重新切线,成品袋两头线辫不能超过5±1cm。
3.4.5缝包结束后,及时清理现场及设备卫生,对缝包机进行维护保养,及时润滑,缝包机油使用要适量,不允许对成品袋造成油污染。
4安全注意事项
4.1工作期间穿戴好必须的劳保用品;
4.2放料时动作敏捷