转炉炼钢车间设计.docx
《转炉炼钢车间设计.docx》由会员分享,可在线阅读,更多相关《转炉炼钢车间设计.docx(26页珍藏版)》请在冰豆网上搜索。
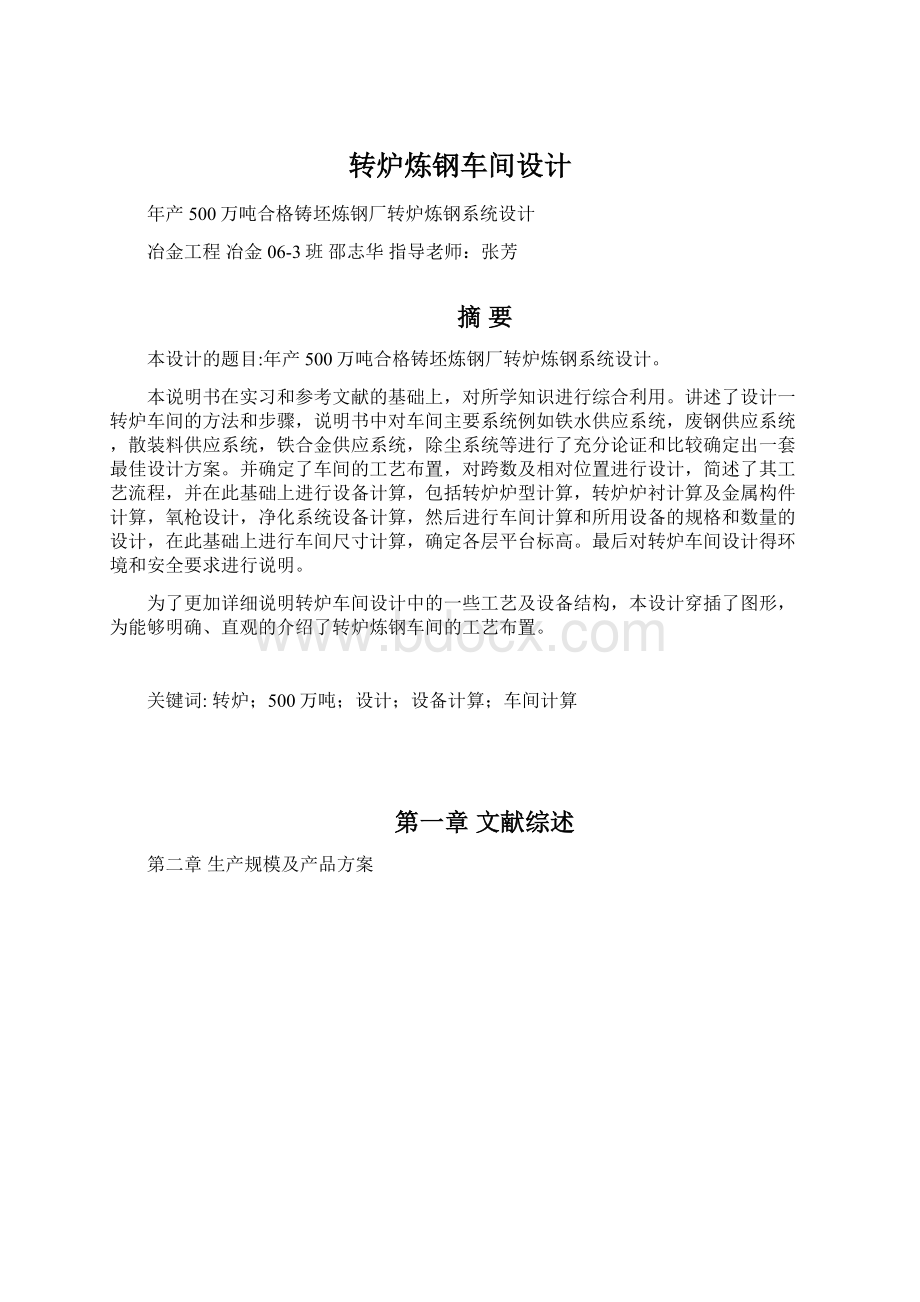
转炉炼钢车间设计
年产500万吨合格铸坯炼钢厂转炉炼钢系统设计
冶金工程冶金06-3班邵志华指导老师:
张芳
摘要
本设计的题目:
年产500万吨合格铸坯炼钢厂转炉炼钢系统设计。
本说明书在实习和参考文献的基础上,对所学知识进行综合利用。
讲述了设计一转炉车间的方法和步骤,说明书中对车间主要系统例如铁水供应系统,废钢供应系统,散装料供应系统,铁合金供应系统,除尘系统等进行了充分论证和比较确定出一套最佳设计方案。
并确定了车间的工艺布置,对跨数及相对位置进行设计,简述了其工艺流程,并在此基础上进行设备计算,包括转炉炉型计算,转炉炉衬计算及金属构件计算,氧枪设计,净化系统设备计算,然后进行车间计算和所用设备的规格和数量的设计,在此基础上进行车间尺寸计算,确定各层平台标高。
最后对转炉车间设计得环境和安全要求进行说明。
为了更加详细说明转炉车间设计中的一些工艺及设备结构,本设计穿插了图形,为能够明确、直观的介绍了转炉炼钢车间的工艺布置。
关键词:
转炉;500万吨;设计;设备计算;车间计算
第一章文献综述
第二章生产规模及产品方案
2.1金属平衡计算
图2.1金属平衡表
2.2生产规模的确定
该转炉车间的生产规模是年产合格铸坯500万吨。
2.2.1转炉座数和大小的确定
设计年产500万吨合格铸坯的转炉炼钢系统。
由金属平衡表计算可知,所需的转炉钢水年产量为546万吨。
每一座吹炼转炉的年出钢炉数N为:
(2-1)
式中:
T1—每炉钢的平均冶炼时间,min;
T2—一年的有效作业天数,d;
1440—一天的日历时间,min;
365—一年的日历天数,d;
η—转炉的作业率,取84%;
转炉车间年产钢水量:
W=n×N×q(2-2)
式中:
W—转炉车间年产钢水量,t;
n—转炉车间经常吹炼炉子座数;
N—每一座吹炼炉的年出钢炉数;
q—转炉公称容量,t。
n×q=5460000÷11037.6=494.7吨所以,取n=2,则q=250t
所以:
本设计选两座250吨的转炉进行炼钢。
3.1转炉炉型选择及计算
转炉炉型选筒球形,其中球缺体半径取R=1.1D。
3.1.1转炉主要尺寸参数的确定和计算
(1)炉容比
炉容比取0.90m3/t
(2)熔池尺寸计算
①熔池直径D
㎜(3-1)
式中:
G—新炉金属装入量,取公称容量250t;
t—平均每炉钢纯吹氧时间,min,(取16min);
K—系数(取1.50)
D—熔池直径,mm;
②熔池深度h
(3-2)
(3-3)
式中:
V池—转炉熔池有效容积,m3;
T—转炉内钢水密度,取6.8t/m3;
(3)炉帽尺寸计算
①炉帽倾角θ:
取θ=60◦
②炉口直径d口:
d口=(0.43~0.53)D(3-4)
本设计取d口=0.43D=0.43×5929.3=2549.6mm
③炉帽高度H帽:
㎜(3-5)
式中H口—炉口直线段高度,取H口=300㎜:
④炉帽总容积V帽:
m3(3-6)
(4)炉身尺寸计算
①炉身体积V身:
取炉容比为0.90m3/t
VT=0.90×T=0.90×250=225m3(3-7)
V身=VT-V帽-V池=143.23m3(3-8)
式中:
VT—转炉有效容积,m3;
②炉身高度H身:
㎜(3-9)
(5)出钢口尺寸的确定
①出钢口中心线水平倾角θ1:
取θ1=0°;
②出钢口直径d出:
㎜(3-10)
(6)转炉有效高度H内:
H内=h+H身+H帽=1668.92+5190.4+3226.91=10086.23㎜(3-11)
(7)转炉总高H总:
H总=H内+H衬+δ底+δ帽=10086.23+1060+130=11276.23㎜(3-12)
(8)炉壳直径D壳:
D壳=D+D衬+2δ身=5929.3+2020+160=8109.3㎜(3-13)
式中:
δ身—炉身钢板厚度,取80㎜;
D衬—炉身处两侧炉衬的厚度;
(9)高宽比核定:
H总/D壳=11276.23/8109.3=1.39(在1.2~1.4范围内)
所以设计合格。
3.2转炉炉衬设计
炉衬设计得主要任务是选择合适的炉衬材质,确定合理的炉衬组成和厚度,并确定相应各层厚度,以确保获得经济上的最佳炉龄。
3.2.1炉衬材质选择
表3.1转炉炉衬厚度选取值
名称
工作层/㎜
填充层/㎜
永久层/㎜
绝热层/㎜
炉帽
600
90
140
20
炉身(加料侧)
800
90
150
20
炉身(出钢侧)
700
90
150
20
炉底
600
90
350
20
3.3复吹转炉底部供气构件设计
3.3.1底气种类
本设计确定采用加强搅拌型,所以顶枪吹氧,底部吹惰性气体和中性气体N2等。
3.3.2底气用量
采用底吹N2、Ar、CO2等气体时,供气强度小于0.03m3/(t·min)时,其冶金特征已接近顶吹法;达到0.2~0.3m3/(t·min),则可以降低炉渣和金属的氧化性,并达到足够的搅拌强度。
最大供气强度一般不超过0.3m3/(t·min)。
全程吹Ar,成本太高;全程吹N2,又会增加钢中的氮。
考虑到经济效益和产品需求,底部全程供气,只是前期吹N2,末期再改吹Ar。
3.3.3供气构件
本设计采用类环缝式喷嘴,在环缝中设有许多细金属管,它兼有透气砖和喷嘴的优点,适用于喷吹各种气体和粉剂,还简化了细金属管砖的制作工艺,是很有发展前途的一种供气构件。
在本设计当中,由于是250t转炉,喷嘴数量选6个。
3.3.4底吹元件布置
底吹喷嘴布置应使底吹和顶吹产生的熔池环流运动同向,且是熔池搅拌均匀时间最短,以此获得最佳的搅拌效果。
喷嘴布置在按炉底部φ=0.45D同心圆上,且相互成60°分布即偏轴心布置。
3.4转炉炉体金属构件设计
转炉金属构件是指炉壳、支承装置(托圈与耳轴)和倾动机构。
3.4.1炉壳设计
炉壳通常由炉帽、炉身和炉底三部分组成。
主要承受钢水、炉渣及耐材的静载荷,以及金属料冲击;热应力作用,其材质应具有高的强度,本设计采用锅炉钢板和合金钢板。
3.4.3倾动机构的设计
本设计采用全悬挂式倾动机构,采用无级调速,转速为0.15~1.5r/min。
第四章氧气转炉供氧系统设计
4.1氧气的供应
4.1.2转炉炼钢车间需氧量计算
(1)一座转炉吹炼时的小时耗氧量计算
①平均小时耗氧量Q1(Nm3/h):
Nm3/h(4-1)
式中:
G—平均炉产钢水量,t;
W—吨钢耗氧量,m3/t,可取45~55m3/t;
T1—平均每炉钢水冶炼时间,min。
②高峰小时耗氧量Q2(m3/h):
Nm3/h(4-2)
式中:
T2—平均每炉纯吹氧时间,min。
(2)车间小时耗氧量
①车间平均小时耗氧量Q3(m3/h):
Q3=NQ1=2×20625=41250m3/h(4-3)
式中:
N—车间经常吹炼的炉座数。
②车间高峰小时耗氧量Q4(m3/h):
Q4=n/N×Q2=41250m3/h(4-4)
4.1.3制氧机能力的选择
根据转炉车间的小时平均需氧量确定选取制氧机座数及能力。
本设计选取2座26000m3/h的制氧机。
4.2氧枪设计
氧枪由喷头、枪身和尾部结构三部分组成。
喷头常用紫铜制成;枪身由三层无缝钢管套装而成;尾部结构连接输氧管和冷却水进出软管。
4.2.1喷头设计
(1)喷头类型与选择
本设计选用拉瓦尔型喷头,孔数定为5孔,喷孔夹角为15°,喷孔布置选择周边布置,出口马赫数M=2.0。
(2)喷头尺寸计算
①氧流量计算
m3/min(4-5)
式中:
每吨钢耗氧量为55~65m3/t,本设计选55m3/t;
②理论计算氧压
由等熵流函数表可查得:
当马赫数M=2.0时,P/P0=0.1278,将选取的P=1.01×105Pa带入,则可求得P0=7.90×105Pa
其中:
P—转炉炉膛内气体压力,即喷孔出口处气流的压力,Pa,选取范围(1.01~1.04)×105Pa;
P0—使用氧压,在设计喷头时按理论计算氧压选取,Pa;
③选用喷孔出口马赫数与喷孔数。
综合考虑,选取马赫数Ma=2.0。
参照武钢炼钢三分厂250t转炉氧气使用情况,选取转炉喷孔数为5孔,能保证氧气流股有一定的冲击面积与冲突深度,熔池内尽快形成乳化区,减少喷溅,提高成渣速度和改善热效率。
④计算吼口直径。
喷头每个喷孔氧气流量q:
m3/min(标态)(4-6)
喷管实际氧气流量QV:
(4-7)
式中:
一般单孔CD=0.95~0.96;三孔喷头CD=0.90~0.96。
由式(4-7),并且取CD=0.96,T0=290K,又P0=7.90×105Pa,代入上式,则
由上式可求得:
d喉=47㎜
⑤求喷孔出口直径
根据等熵流表,在Ma=2.0时,A出/A喉=1.6875,即
,故喷孔出口直径
㎜(4-8)
⑥计算扩张段长度。
取扩张段的半锥角α为4°,则扩张段长度
㎜(4-9)
⑦确定喷孔倾角β:
多孔喷头的各个流股是否发生交汇以效应角θ为界,大于θ则各流股很少交汇,小于θ则必定交汇。
按照经验,喷头倾角β=12.8°~15.4°为宜。
综合考虑选取β=15°。
⑧喷孔喉口段长度确定
喉口段长度的作用:
一是稳定气流;二是使收缩段和扩张段加工方便,为此过长的喉口段反而会使阻损增大,因此喉口段长度推荐为5~10㎜。
本设计选取8㎜。
4.2.2氧枪枪身设计
氧枪枪身由三层无缝钢管套装而成,内层管是氧气通道,内层管与中层管之间是冷却水进水通道,中层管与外层管之间是冷却水通道。
(1)枪身各层尺寸的确定
①中心氧管管径的确定
管内氧气工况流量Q0:
(4-10)
式中:
P标—标准大气压,Pa;
P0—管内氧气工况压力,Pa;
T标—标准温度,273K;
T0—管内氧气实际温度,一般取290K。
取中心管内氧气流速V0=50m/s,则中心氧管内径
㎜(4-11)
式中:
F1—中心氧管内截面积,㎡;
V0—管内氧气流速,m/s,一般取40~50m/s,这里取V0=45m/s;
根据标准热轧无缝钢管产品规格,选取中心钢管为φ219㎜×8㎜。
②中外层钢管管径
根据生产实践经验,选取氧枪冷却水耗量Q水=250t/h;冷却水进水速度V进=6m/s,出水速度V出=7m/s。
又中心氧管外径d1外=219㎜,则:
进水环缝面积
(4-12)
出水环缝面积
(4-13)
所以,中层钢管的内径d2:
(4-14)
选取中层钢管d2外=φ253㎜×8㎜。
同理,外层钢管内径
(4-15)
选取外层钢管d3外=φ280㎜×8㎜。
(2)氧枪长度的确定
氧枪全长包括下部枪身长度l1和尾部长度l2。
氧枪尾部装有氧枪把持器,冷却水进出管接头,氧气管接头和吊环等。
故l2的长度取决于炉子容量和烟罩尺寸。
本设计参照宝钢三百吨转炉参数,取氧枪总长为24m,氧枪工作行程为18m。
第五章转炉车间原材料供应
5.1铁水供应
由于所建的是两座250吨的转炉,所以采用容量为600吨的混铁车。
车间所需混铁车台数N(台)为:
(5-1)
式中:
Pmax—高炉铁水最高日产量,t/d;
Q—混铁车容量,t,取600t;
n—混铁车装满系数,可取0.9;
c—混铁车日周转次数,一般取2~3次/d;
η—混铁车作业率,约取0.75;
经计算得知,选取14个鱼雷罐车。
5.1.2铁水包选择
由金属料平衡可计算出每炉钢水需要铁水231t,考虑过余装量10%后可装254t,由此选择铁水包容量为260t。
参照盛钢桶尺寸计算,选取铁水包全高为4759㎜,空铁水包重72.05t,其它数据兼同钢包。
铁水包耳轴位置选取为铁水包全高一半偏上500㎜。
本设计铁水包数选用6个,其中两个为备用。
5.2废钢的供应
废钢是作为冷却剂加入转炉的。
根据氧气顶吹转炉热平衡计算,废钢的加入量一般为10~30%。
加入转炉的废钢块度,最大长度不得大于炉口直径的1/3,最大截面积要小于炉口的面积的1/7。
根据炉子吨位的不同,废钢块单重波动范围为150~2000kg。
(1)废钢的加入方式
目前在氧气顶吹转炉车间,向转炉加入废钢的方式有两种,一种是直接用桥式吊车吊运废钢槽倒入转炉;另一种是用废钢加料车装入废钢;
本设计选用直接用桥式吊车吊运废钢槽倒入转炉。
(2)废钢堆场面积
废钢间面积的大小决定于废钢需要的堆存用的面积、铁路条数、料槽位置及称量设备占用的面积,高度取决于工艺操作所需要的吊车轨面标高。
废钢堆积的面积可按下式估算:
㎡(5-2)
式中:
Q—每日所需废钢量,t/d;
x—废钢储存定额(天数),d,取3天;
H—废钢储存允许高度,有坑时包含的深度,取1.2m;
ρ—废钢堆积密度,t/m3,取2.2t/m3;
(3)废钢料斗容积V(m3):
废钢入炉一般通过废钢料斗,由普通吊车像兑铁水那样装入转炉。
废钢料斗容积的大小决定于每炉废钢的装入量。
废钢料斗容积V计算如下:
(5-3)
式中:
q—每炉加入废钢量,t;
n—料斗装满系数,取0.8;
f—每炉加入废钢的斗数,取1;
ρ—废钢堆积密度,t/m3;
5.3散状材料的供应
转炉散状材料包括石灰、白云石、萤石、铁矿石、氧化铁皮、焦炭等。
品种多,批量少,批次多,要求迅速、准确、可靠的供料。
供应系统包括散状料堆场、地下(地面)料仓、由地下料仓送往主厂房的运料设施、转炉上方高位料仓、称量和向转炉加料的设施。
散状料供应流程如
5.3.1散状料的供应流程
5.3.2散状料供应和主要设备选型
(1)地面料仓容积和数量的确定
地面料仓的容积V(m3):
(5-4)
式中:
Q—一天需要的原料量,t;
t—贮存天数;
0.8—料仓装满系数;
Y—散料堆积密度,t/m3;
根据公式5-4可得:
铁矿石:
石灰:
萤石:
白云石:
焦炭粉:
选用标准料仓,总容量为:
V总=126m3
故料仓需要个数:
铁矿石料仓个数:
n=936.2/126=7.43取8个
石灰料仓个数:
n=1212.1/126=9.6取10个
萤石料仓个数:
n=455.4/126=3.6取4个
白云石料仓个数:
n=2661.3/126=21.1取22个
焦炭粉料仓个数:
n=201.6/126=1.6取2个
(2)上料方式的选择
本设计采用全胶带运输上料系统,其作业流程如下:
地下(或地面)料仓→固定胶带运输机→转运漏斗→可逆式胶带运输机→高位料仓→分散称量漏斗→电磁振动给料器→汇集胶带运输机→汇集料斗→转炉
这种上料系统的特点是运输能力大,上料速度快而且可靠,能够进行连续作业,有利于自动化;但它的占地面积大,投资多,上料和配料时有粉尘外逸现象。
5.3.3高位料仓容积和数量的确定
高位料仓的作用在于临时储料,并利用重力向转炉及时和可靠地供料保证转炉正常生产。
高位料仓的横截面一般为矩形,上部为长方体,下部为四角锥形。
椎体部分的倾角不小于45°~50°,放料口尺寸为标准散状料尺寸的3~6倍以上,一般大致为150~300㎜,以保证料仓内的散状料能自由下落,避免堆积成拱和卡料。
高位料仓沿炉子跨纵向布置有三种方案,分布为共用高位料仓、部分共用高位料仓、单独高位料仓。
本设计选用共用高位料仓。
高位料仓容积计算:
(5-4)
式中:
V—料仓容积;
q—一天内转炉原料消耗量,t;
0.8—料仓装满系数;
t—原料贮存时间,h;
Y—散料堆积密度,t/m3;
石灰按6~8小时备料,其它24h,白班上料,Y堆比重t/m3。
铁矿石:
石灰:
萤石:
白云石:
焦炭粉:
各散料标准仓计算和数量的确定:
铁矿石、石灰、萤石、白云石、焦粉用料仓容量选25m3,则:
铁矿石料仓的个数为:
93.62/25=3.7取4个
石灰料仓个数:
404.03/25=16.2取17个
萤石料仓个数:
45.54/25=1.8取2个
白云石料仓个数:
266.13/25=10.64取11个
焦炭粉料仓个数:
20.10/25=0.8取1个
采用共用料仓,其优点是料仓数目少,停炉后料仓中剩余石灰处理方便。
缺点是称量及下部给料器的作业频率太高,出现临时故障时会影响生产。
5.4铁合金的供应
铁合金料仓容积计算:
(5-5)
式中:
V—料仓容积;
Q—一天内转炉原料消耗量,t;
0.8—料仓装满系数;
t—原料贮存时间,h;
Y—铁合金堆积密度,t/m3;
铁合金储存天数为3天
FeSi(Si45):
FeMn(Mn76):
各种铁合金标准仓计算和数量的确定:
铁合金用料仓容量选25m3,则:
FeSi(Si45)所用料仓个数:
104.5/25=4.18取5个
FeMn(Mn76)所用料仓个数:
109.9/25=4.3取5个
大型转炉炼钢车间的铁合盒供应采用类似于散状料系统的全胶带供料系统。
这种系统工作可靠,运输量大,机械化程度高,对于需要铁合金品种多,用量大的炼钢车间特别适用。
第六章转炉车间烟气净化与回收
6.1转炉烟气与烟尘
6.1.1烟气特征
(1)烟气来源及化学组成
在转炉吹炼过程中,熔池碳氧反应生成的CO和CO2,是转炉烟气的基本来源;其次是炉气从炉口排出时吸入部分空气,可燃成分有少量燃烧生成废气,也有少量来自炉料和炉衬中的水分,以及生烧石灰中分解出来的CO2气体等。
在未燃的烟气中,烟气主要成分是CO,含有少量CO2和N2以及极少量的O2和H2。
(2)烟气温度
转炉未燃烟气温度为1400~1600℃,燃烧烟气温度为1800~2000℃,因此烟气净化系统中必须设置冷却设备。
(3)烟气量
转炉未燃法平均烟气量为60~80m3/t。
(4)烟气的发热量
转炉未燃法中,当烟气含60%~80%CO时,其发热量波动在7745.95~10048.8kJ/m3。
6.1.2烟尘的特征
(1)烟尘的来源
在氧气转炉熔池反应区内,局部温度可达2500~2800℃,使一定数量的铁和铁氧化物蒸发,并夹带部分散料粉尘和渣粒,组成烟尘,随炉气排出。
烟尘量约为入炉金属料量的0.8%~1.3%,烟气中的含尘量为15~120g/m3。
在大型炉每熔炼1t钢约产生20kg粉尘,吹氧时烟气含尘浓度可达20~30g/m3。
(2)烟尘成分
未燃法转炉烟尘中60%以上为FeO,其颜色呈黑色。
(3)烟尘粒度
转炉未燃法尘粒大于10μm的达70%。
6.2烟气净化方案选择
(1)炉口附近烟气处理方法
转炉烟气从炉口逸出,在进入烟罩过程中或燃烧,或不燃烧,或部分燃烧,然后经过汽化冷却烟道或水冷烟道,温度有所下降;进入净化系统后,烟气还需进一步冷却,有利于提高净化效率,简化净化设备系统
本设计炉口烟气处理方法选用未燃法,并选用炉口微压差控制法来控制烟罩不吸入空气。
(2)转炉烟气净化方法
本设计转炉烟气净化采用未燃法干法静电除尘,未燃法电除尘通常是将空气过剩系数控制在0.3以下,故烟气量小得多,且可回收煤气和获得干尘,被认为是最经济的方法,越来越受到各国的重视。
6.3烟气净化系统
参照邯钢集团邯宝公司炼钢厂2座250t顶底复吹转炉,年设计生产能力是520万t转炉除尘系统[26]。
本设计采用LT法干法除尘系统。
该LT法烟气净化系统的主要参数如下:
炉气量:
17000m3/h
炉口烟气温度:
1450℃
从汽化冷却烟道出来烟气温度:
800~1000℃
从蒸发冷却器出来烟气温度:
150~200℃
放散管处烟尘浓度:
≤68mg/m3
煤气进入煤气柜温度:
≤70℃
煤气回收量:
≥100m3/t
6.4烟气净化回收系统主要设备
6.4.1烟罩
烟罩位于炉口之上,主要作用是收集烟气使之不外溢,且可控制吸入的空气量。
烟罩一般有固定段与活动段两部分组成,二者用水封连接。
活动烟罩下沿直径D2:
D2≈(2.5~3)d口=6373~7648.8㎜取7200㎜
式中:
d口—转炉炉口直径,㎜;
活动烟罩的高度Ht:
Ht≈0.5d口=0.5×2549.6=1274.8㎜
可使烟罩下沿能降到炉口以下200~300㎜处。
活动烟罩的升降行程S为300~500㎜。
固定烟罩内的直径要大于炉口烟气射流进入烟罩时的直径。
取烟气从炉口喷出自由射流的扩张角25°,由此可求得烟气射流直径为:
d口+2Httan25°=3738.5㎜
所以本设计固定烟罩直径D1取4000㎜。
烟气在烟道内的流速取30~40m/s。
烟道垂直段高度一般为3~4m,斜烟道的倾斜角为55°~60°。
6.4.3静电除尘器
静电除尘的原理是利用放电作用,使烟气中气体分子电离,由此导致尘粒带电,遂被静电吸引沉积于集尘电极上。
根据收尘电极的形式可分为管式电除尘器和板式电除尘器。
管式电除尘器的管径通常为150~300㎜,长2~5m。
烟气在静电除尘器内的流速一般为2~3m/s,烟气温度控制在不低于150~200℃。
静电除尘器效率高,可达到99.9%,而且除尘效率稳定,不受气量波动的影响,最适合于捕集小于1μm的烟尘,处理气体量大,阻力损失小(一般在300Pa以下)。
6.4.4煤气柜
煤气柜是贮存煤气之用,以便于连续供给用户成分、压力、质量稳定的煤气,是复吹转炉回收系统中重要设备之一。
由于转炉煤气容易爆炸,从安全与回收煤气质量出发,要求整个系统严密,并规定当煤气中含O2量大于2%时停止回收,利用燃烧器所产生的CO2废气,清洗烟道中残存的O2以保证安全。
经过静电除尘器精除尘的烟气经煤气冷却器降温至70℃后进入煤气柜。
参照参照邯钢集团邯宝公司炼钢厂250t转炉烟气回收系统,选用10万m3的煤气柜。
第七章冶金辅助设备的计算
7.1盛钢桶的计算
7.1.1盛钢桶容积计算
(1)盛钢桶容纳钢水量
本设计盛钢桶的额定容量为P=250t,一般考虑应有10%的过余装量,则钢包内钢水实际容量为:
P+0.1P=1.1P=1.1×250=275t(7-1)
(2)盛钢桶内渣量
出钢时一般将炉内熔渣全部或绝大部分随钢水倒入钢包内。
渣量一般为金属量的3%~5%,设计时取较大比例为15%,即渣量为:
1.1P×0.15=275×0.15=41.25t(7-2)
(3)盛钢桶的容积及尺寸计算
盛钢桶的实际容积即为钢与渣的总容积,取钢液比容为0.15m3/t,熔渣比容取0.28m3/t。
因此,钢包容积为:
0.15×1.1P+0.28×(1.1P×0.15)=0.2112P=52.8m3(7-3)
设钢包内型上部宽为D,下部宽度DH,高为H,若采用D/H=1,锥度为15%,则钢包下部内径宽:
DH=D-0.15H=0.85D(7-4)
盛钢桶的容积按圆锥台计算:
(7-5)
将H=D,DH=0.85D带入上式得:
V=0.673D3(7-6)
所以可求得:
D=0.680P1/3=4.28m
H=0.680P1/3=4.28m
DH=0.578P1/3=3.6m
(4)盛钢桶砖衬的厚度
钢桶桶壁砖衬厚度约等于:
Jb=0.07D=0.07×4280