高压气井带压过油管作业清除蜡堵.docx
《高压气井带压过油管作业清除蜡堵.docx》由会员分享,可在线阅读,更多相关《高压气井带压过油管作业清除蜡堵.docx(13页珍藏版)》请在冰豆网上搜索。
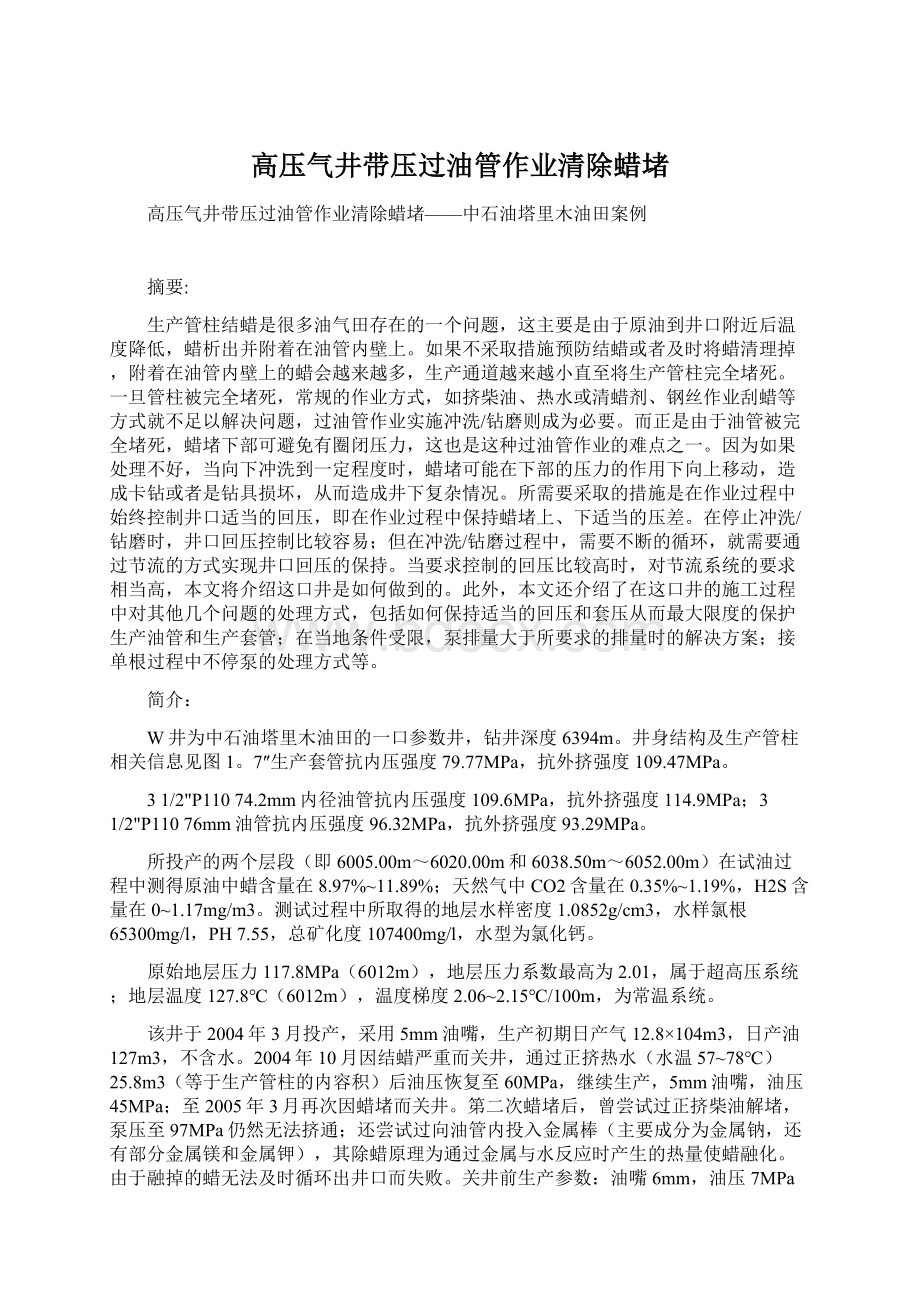
高压气井带压过油管作业清除蜡堵
高压气井带压过油管作业清除蜡堵——中石油塔里木油田案例
摘要:
生产管柱结蜡是很多油气田存在的一个问题,这主要是由于原油到井口附近后温度降低,蜡析出并附着在油管内壁上。
如果不采取措施预防结蜡或者及时将蜡清理掉,附着在油管内壁上的蜡会越来越多,生产通道越来越小直至将生产管柱完全堵死。
一旦管柱被完全堵死,常规的作业方式,如挤柴油、热水或清蜡剂、钢丝作业刮蜡等方式就不足以解决问题,过油管作业实施冲洗/钻磨则成为必要。
而正是由于油管被完全堵死,蜡堵下部可避免有圈闭压力,这也是这种过油管作业的难点之一。
因为如果处理不好,当向下冲洗到一定程度时,蜡堵可能在下部的压力的作用下向上移动,造成卡钻或者是钻具损坏,从而造成井下复杂情况。
所需要采取的措施是在作业过程中始终控制井口适当的回压,即在作业过程中保持蜡堵上、下适当的压差。
在停止冲洗/钻磨时,井口回压控制比较容易;但在冲洗/钻磨过程中,需要不断的循环,就需要通过节流的方式实现井口回压的保持。
当要求控制的回压比较高时,对节流系统的要求相当高,本文将介绍这口井是如何做到的。
此外,本文还介绍了在这口井的施工过程中对其他几个问题的处理方式,包括如何保持适当的回压和套压从而最大限度的保护生产油管和生产套管;在当地条件受限,泵排量大于所要求的排量时的解决方案;接单根过程中不停泵的处理方式等。
简介:
W井为中石油塔里木油田的一口参数井,钻井深度6394m。
井身结构及生产管柱相关信息见图1。
7″生产套管抗内压强度79.77MPa,抗外挤强度109.47MPa。
31/2"P11074.2mm内径油管抗内压强度109.6MPa,抗外挤强度114.9MPa;31/2"P11076mm油管抗内压强度96.32MPa,抗外挤强度93.29MPa。
所投产的两个层段(即6005.00m~6020.00m和6038.50m~6052.00m)在试油过程中测得原油中蜡含量在8.97%~11.89%;天然气中CO2含量在0.35%~1.19%,H2S含量在0~1.17mg/m3。
测试过程中所取得的地层水样密度1.0852g/cm3,水样氯根65300mg/l,PH7.55,总矿化度107400mg/l,水型为氯化钙。
原始地层压力117.8MPa(6012m),地层压力系数最高为2.01,属于超高压系统;地层温度127.8℃(6012m),温度梯度2.06~2.15℃/100m,为常温系统。
该井于2004年3月投产,采用5mm油嘴,生产初期日产气12.8×104m3,日产油127m3,不含水。
2004年10月因结蜡严重而关井,通过正挤热水(水温57~78℃)25.8m3(等于生产管柱的内容积)后油压恢复至60MPa,继续生产,5mm油嘴,油压45MPa;至2005年3月再次因蜡堵而关井。
第二次蜡堵后,曾尝试过正挤柴油解堵,泵压至97MPa仍然无法挤通;还尝试过向油管内投入金属棒(主要成分为金属钠,还有部分金属镁和金属钾),其除蜡原理为通过金属与水反应时产生的热量使蜡融化。
由于融掉的蜡无法及时循环出井口而失败。
关井前生产参数:
油嘴6mm,油压7MPa,日产油9.7m3、日产水19.3m3、日产气21120m3,含水66.5%。
W井采用4-6mm油嘴累计试采251天,累计产油8216.4m3,水5610.6m3,天然气1317.0×104m3。
作业前套压48MPa,油压46MPa。
曾通过3/8″管线尝试放套压,套压下降缓慢,油压保持不变。
但停止放压后,套压迅速恢复到48MPa。
油压可快速泄至零,泄压过程中套压保持不变,再次关井后油压缓慢上升。
施工方案的确定:
根据第二次蜡堵后试挤的情况以及油、套压放压的情况可以做出如下判断:
蜡堵上部油、套不连通,蜡堵中间存在微通道,蜡堵下部的气体可经由该通道窜到井口,但无法通过该通道将液体挤入井内使该通道增大从而解堵,因而无法压井也无法带压起出原井管柱;蜡堵下部、封隔器上部的油管存在泄漏或者封隔器存在泄漏。
据此,施工方案确定为:
利用带压作业设备下入11/4″油管及工具串,实施冲洗/钻磨,通过不断循环,将蜡循环出井口,从而达到清通蜡堵的目的;考虑到蜡堵下部有圈闭压力,在清通蜡堵前始终要保持一定的回压,确保蜡堵不会由于其长度在冲洗/钻磨过程中逐渐减短而在其下部圈闭压力作用下上行,造成钻具损坏或者被卡。
工具串首选喷嘴,以对蜡堵实施冲洗,之所以考虑下磨鞋实施钻磨的后备方案是考虑到这口井地层出砂,油管内可能存在砂桥。
而且以前蜡堵经受过高达97MPa的挤压,蜡堵压实的可能性比较大,可能冲洗效率低。
回压及循环流量的控制:
W井在2003年测试过程中记录的最高关井压力为90MPa;在第一次蜡堵清除后记录的关井压力为60MPa,但此时生产管柱内存在清水;第二次蜡堵后油压为46MPa。
根据以上情况,难以准确判断蜡堵下部圈闭压力的大小。
考虑到施工安全,回压应尽可能接近90MPa。
与磨鞋配套的井下马达所允许的最高排量为170L/min,但当地的高压低排量泵的最低排量为180L/min。
如果需要下磨鞋实施钻磨,则需要降低循环排量至170L/min以下。
有一种可能的方式是利用一套节流管汇进行分流,从而控制循环流量。
为确定计划使用的节流管汇是否能满足施工要求,特别在施工前进行了循环试验,以明确以下问题:
1、单个节流阀在如此高的节流压差下能够工作多长时间;
2、单个节流阀在如此高的节流压差下是否容易调节;
3、液体节流后温度的变化情况;
4、如果单个节流阀不能正常工作,那么是否可以通过多个串联的节流阀同时使用实现分级节流,降低每个节流阀的节流压差从而延长节流阀的寿命,确保施工的顺利进行;
5、通过使用一套节流管汇在泵出口进行分流从而降低循环流量是否可行。
考虑到单个节流阀可能被很快冲蚀而失效,而且采用分级节流的方式需要串联多个节流阀,因此拟采用的节流管汇采用特殊的组合方式,具体见图2。
该节流管汇有两个通道,每个通道均由两个闸阀和四个楔形节流阀串联组成。
循环试验流程见图3。
在第一阶段的试验中用于回压控制和分流的节流管汇后均连接了一套笼套式节流阀,目的是确定楔形节流阀和笼套式节流阀哪种更适用于W井的施工。
但对于笼套式节流阀,在340L/min的排量下,即使在全关状态也不能憋起压力,说明这种节流阀不适用于小排量的液体的节流。
在使用单个楔形节流阀试验的过程中,当压力憋至97MPa时,阀芯突然发生断裂,见图4。
在逐渐关楔形节流阀憋压的过程中,操作非常困难。
因此,不能使用单个楔形节流阀进行较高的回压的控制。
第二阶段的试验将笼套式节流阀均更换为动力油嘴,并尝试通过分级节流的方式实现分流和回压的控制。
分级节流控制回压的操作步骤为:
1、先将用于回压控制的节流管汇一个通道所有的闸阀和节流阀全开,动力油嘴全开;用于回压控制的节流管汇另一个通道的闸阀关闭;用于分流的通道关闭;
2、开泵循环;
3、缓慢关BPCC1,直至泵压憋至20MPa;
4、然后缓慢关BPCC2,至泵压憋至40MPa;
5、缓慢关BPCC3,至泵压憋至60MPa;
6、缓慢关BPCC4,至泵压憋至80MPa;
7、缓慢关PC1,至泵压憋至95MPa。
在此过程中始终保持泵排量340L/min不变。
继续保持泵排量不变循环,观察泵压变化情况。
测试分流的方式则是保持泵排量340L/min不变的情况下:
1、缓慢关BPCC1及BFCC1相同的圈数,直至泵压憋至20MPa;
2、缓慢关BPCC2及BFCC2相同的圈数,直至泵压憋至40MPa;
3、缓慢关BPCC3及BFCC3相同的圈数,直至泵压憋至60MPa;
4、缓慢关BPCC4及BFCC4相同的圈数,直至泵压憋至80MPa;
5、缓慢关PC1及PC2相同的圈数,至泵压憋至95MPa。
6、保持泵排量不变,通过调节PC1及PC2的开度调节分流的流量及进入循环系统循环的流量。
最后分流流量166L/min,循环流量164L/min,泵压93MPa,循环1小时。
液体温度由47℃上升至56℃(前面调节过程液体温度由27℃上升至47℃)。
期间泵压基本稳定。
试验结束后拆开所有的节流阀观察,所有的阀芯及阀座没有或者仅有轻微冲蚀。
通过以上试验得出以下结论:
利用这种特殊设计的节流管汇,通过分级节流的方式可以实现90MPa以上回压的控制;通过利用节流管汇分流的方式可以实现将泵排量降低至所要求的循环流量。
液体在经过泵增压和节流后温度会上升,但在可接受的范围内。
井口设备组合:
井口设备组合见图5。
采用的是高压带压作业的常规配置,所有设备均安装在原井采油树之上,依次为:
31/16″15K闸阀(用于提供额外的保障)+3套31/16″20K单闸板防喷器+31/16″20K四通+3套31/16″20K单闸板防喷器+变径四通+41/16″10K环形防喷器+变径法兰+150K带压作业设备。
施工流程设计:
现场施工流程图见图6。
该流程的特点为:
1、一套特殊设计的节流管汇用于回压的控制;一套相同的节流管汇用于在需要较低循环排量时进行分流;分流回路及循环回路均连接了流量计用于流量的监测;
2、考虑到该井生产过程中地层出砂,在用于回压控制的节流管汇前增加了出砂器,确保节流阀不会被固体颗粒冲蚀;
3、油管四通的侧出口连接了泵车、安全阀及节流管汇:
在套压过低时可以补压;在套压超过设定值时,安全阀自动打开泄压,防止套管被憋爆;套压持续过高时可通过节流管汇有控制的泄压,使套压保持在合理的范围内;
4、连接了两台乙二醇注入泵,分别用于在天然气出现时防止放喷管线及带压作业设备的放压管线内结冰;
5、设计了通过泵车-压井管汇-立管-水龙带-工作管柱-工具串-小环空-井口-出砂器-节流管汇-分离器-循环罐及泵车-压井管汇-31/16″20K四通-出砂器-节流管汇-分离器-循环罐两种循环通道,两种循环通道可自由切换,确保在接单根、卸单根等情况下不需要反复停泵和起泵,仅仅倒换流程即可。
既能很好的保持回压在一定范围内,也能提高施工效率;
6、接单根或者卸单根过程中卸油压通过节流阀进行,保护旋塞阀不受冲蚀;
7、接单根或者卸单根后恢复循环前先利用泵车平衡压力,然后才倒换流程恢复循环。
这样既能确保倒换流程时相关阀门前后压差最小,从而容易操作;同时避免了突然倒换流程时井下单流阀受到冲击。
井场设备摆放:
井场设备摆放图见图7。
所有高压管线、泵及管汇均集中摆放在井场东北角1/4的井场区域内,最大可能的减少了现场施工过程中的高压区域。
工作管柱和工具串组合:
工作管柱:
W井施工采用的是由11/4″3.02#S-135BTS-8油管组成的工作管柱。
工具串组合:
设计了用于冲洗和钻磨两种不同的工具串组合。
冲洗工具串组合:
1.93″15K双挡板回压阀+1.93″15K双挡板回压阀+1.93″15K双挡板回压阀+变扣+1.7″液压丢手工具+1.7″循环接头+1.75″喷嘴。
工具串总长2.50m。
喷嘴前部为半球形,后部为圆柱形,共有0.07″孔13个,其中6个均匀分布在后部的圆柱面上,用于冲洗附着在管壁上的蜡;6个均匀分布在球面的侧面,1个在球面顶部,均设计用于冲洗蜡堵。
施工过程中排量始终在180L/min,计算出口喷射速度为93.0m/s。
钻磨工具串组合:
1.93″15K双挡板回压阀+1.93″15K双挡板回压阀+1.93″15K双挡板回压阀+变扣+1.7″HZ震击器+1.7″液压丢手工具+1.7″循环接头+1.7″井下马达+2.25″平底磨鞋。
工具串总长7.87m。
由于实际施工过程中冲洗比较顺利,这种工具串没有用到。
循环液的选择:
考虑过的循环液有柴油、高闪点溶剂油、水基溶蜡液、普通水基溶液。
柴油是一种清蜡常用的介质,本身成本较低,容易获得,溶蜡效果也非常好。
但也有其缺点,主要在于其闪点低,仅55℃,容易发生闪燃,施工风险较高。
高闪点溶剂油兼具柴油的所有优点,但其闪点达到75℃。
但其对整个循环系统的橡胶件的影响不是很明确,因而没有采用。
施工前根据蜡样的性质配制了一种水基溶蜡液,溶蜡效果好,不存在闪燃的问题,但成本极高,因而最终没有采用。
最终选择的是一种能有效防止在井下形成水合物的普通水溶液。
其具体配方为:
15%乙二醇+85%NaCl溶液(密度1.17m/cm3)。
这种溶液不能溶解蜡,但不存在闪燃的问题,不会影响循环系统橡胶的性能,配制所需材料容易获得,且成本较低。
将这种溶液加热到一定温度,虽然不能溶解蜡,但能促使蜡的融化,同样可提高清蜡速度。
但过高的液体温度会导致整个循环系统温度过高,容易发生人员灼伤事故。
因此原计划采用常温的这种液体实施冲洗。
现场施工:
设备按设计安装、试压并调试合格后,下入冲洗工具串至采油树1#主阀上部,在1#主阀关闭的情况下,对正式施工过程中将要进行的操作程序进行了演练,以确保流程设计合理,同时使作业人员熟悉相关的操作。
演练包括:
通过井下工具串进行循环;切换到直接通过四通循环;通过节流管汇泄油压;平衡井下单流阀上下的压力后再次切换到通过井下工具串循环;同时缓慢起泵和打开节流阀以及同时缓慢停泵和关闭节流阀,确保起泵和停泵过程中回压始终保持在合理范围内。
演练结束后打开1#主阀,开泵循环,边冲洗边下入工具串。
在132m±探到蜡堵。
在冲洗到蜡堵底部前,中间有几次有大量气体返出,但继续快速向下冲洗时泵压很快上升,说明仍然有蜡堵。
说明油管内的蜡堵并不是连续的,中间存在气柱。
当冲洗到1751m±,泵压突然下降,随后有大量气体返出,继续快速向下冲洗没有憋泵的现象,说明蜡堵已完全解除。
在施工的前期,循环液的温度为常温,约20℃,冲洗出的蜡呈较大的块状(见图8),冲洗速度较慢,而且循环出井口后基本都留在除砂器内。
后来的施工均在施工前将循环液加热到45℃左右,冲洗出的蜡呈较细的粒状(见图9),而且大部分蜡均通过除砂器进入到循环罐内(见图10)。
施工前套压为48MPa,安全阀的打开压力设置在50MPa。
从以前放套压的情况看,套压虽然能通过放压降低,但很快又会恢复至原来的水平;持续放套压很可能会导致漏点处的泄漏越来越严重,最后甚至会导致原泄露点油套完全连通。
W井是一口老井,生产套管下入已有10年,其100%抗内压强度为79.77MPa,为确保套管不会被憋爆,取70%的抗内压强度,即55.8MPa为允许的套压上限。
而施工前的套压在允许的范围内,且较高的套压可以确保施工过程中生产油管内外压差较小,可以确保油管不会被憋爆。
因此该井采取的策略是保持原来的套压不变进行施工。
现场为确保绝对安全,与环空连通的安全阀的自动打开压力设置在50MPa。
套管在施工过程中套压呈缓慢上升的趋势,这主要是由油管内压力增加油管膨胀以及循环冲洗过程中循环液温度升高引起的。
套压最高曾达到49.5MPa,为避免因套压过高将安全阀打开压力设置为52MPa(65%的套管抗内压强度)。
整个施工过程中套压均未超过50MPa,安全阀也未因套压高出其设定值而开启。
在整个施工过程中,由于冲洗比较顺利,特别是循环液加热后,因此未更换工具串,泵排量一直保持在180L/min。
刚开始施工时,正常循环冲洗过程中泵压保持在88MPa,回压控制在75MPa左右。
随着向下冲洗的进行,泵压始终控制在90MPa以内,控制回压逐渐减小。
这是因为随着深度加深,循环摩阻越来越大,如果要保持75MPa的回压值,泵压会相应升高,但实际随着工具串深度的增加,逐渐获得越来越高的液柱,回压降低仍然可确保蜡堵上部的压力在75MPa以上。
而控制泵压在90MPa以内,离系统压力等级105MPa存在15MPa的差距,可以确保在由于下管柱速度过快等原因造成的泵压上升在安全的范围内。
结论:
1、对于结蜡问题比较严重的井,在完井前就应考虑防止结蜡,可采取在完井管柱上预置化学药剂注入阀,在生产过程中不断注入化学药剂;在生产过程中应监测蜡的形成程度及速度,并及时清除掉已形成的蜡,方法包括正挤柴油、热水及溶蜡剂,或者采取钢丝作业刮蜡等;如果蜡已完全将生产管柱堵死再处理,则施工难度、成本及风险都将极大的增加;
2、多个楔形节流阀串联起来组成的节流管汇在节流阀冲蚀比较严重的工况下使用非常实用。
有两种使用方法:
一种是每次使用一个节流阀(当节流压差较小时),当一个节流阀冲蚀严重失效时即可开始使用下一个节流阀,可在施工过程中极大地缩短作业时间,提高作业效率,在某些情况下可降低作业风险;另一种使用方式是在节流压差较大时采用分级节流的方式,即将节流压差平均分布在串联的各个节流阀上,能确保各个节流阀的寿命,从而确保施工的顺利进行;
3、在泵排量高于要求的循环排量时,可通过分流的方式降低循环排量,即使是在施工压力较高时也可实现。
其实施方式是在泵出口连接两套节流系统,一套用于分流,一套连接在循环通道上。
通过两套节流管汇内节流阀开度的调节实现泵出的液体一部分通过分流直接返回储液罐,而另一部分则进入循环系统。
分流系统在分流过程中会产生一定的热量使液体温度升高,但在可接受的范围内;
4、对于通过钻磨或者冲洗的方式清除蜡堵的作业,使用对蜡具有溶解作用的液体无疑会在一定程度上提高作业速度,但不具溶解作用的液体体系也能达到作业目的。
W井施工所使用的液体为15%乙二醇+85%NaCl溶液(密度1.17g/cm3),并不具溶蜡的作用。
对循环液适当加热有助于蜡堵的清理。
致谢:
作者在此向为本文的准备提供帮助的托普威尔石油技术股份公司表示感谢。
参考文献:
1、MarkEmbrey,SPE,andJamesLarke,SPE,BJServices:
“Paraffin-PlugRemediationinDeepWaterWellsviaCapillaryTubing:
ACostEffectiveAlternative”SPE135136,(2010)。