客车内饰板常见装配方式分析.docx
《客车内饰板常见装配方式分析.docx》由会员分享,可在线阅读,更多相关《客车内饰板常见装配方式分析.docx(13页珍藏版)》请在冰豆网上搜索。
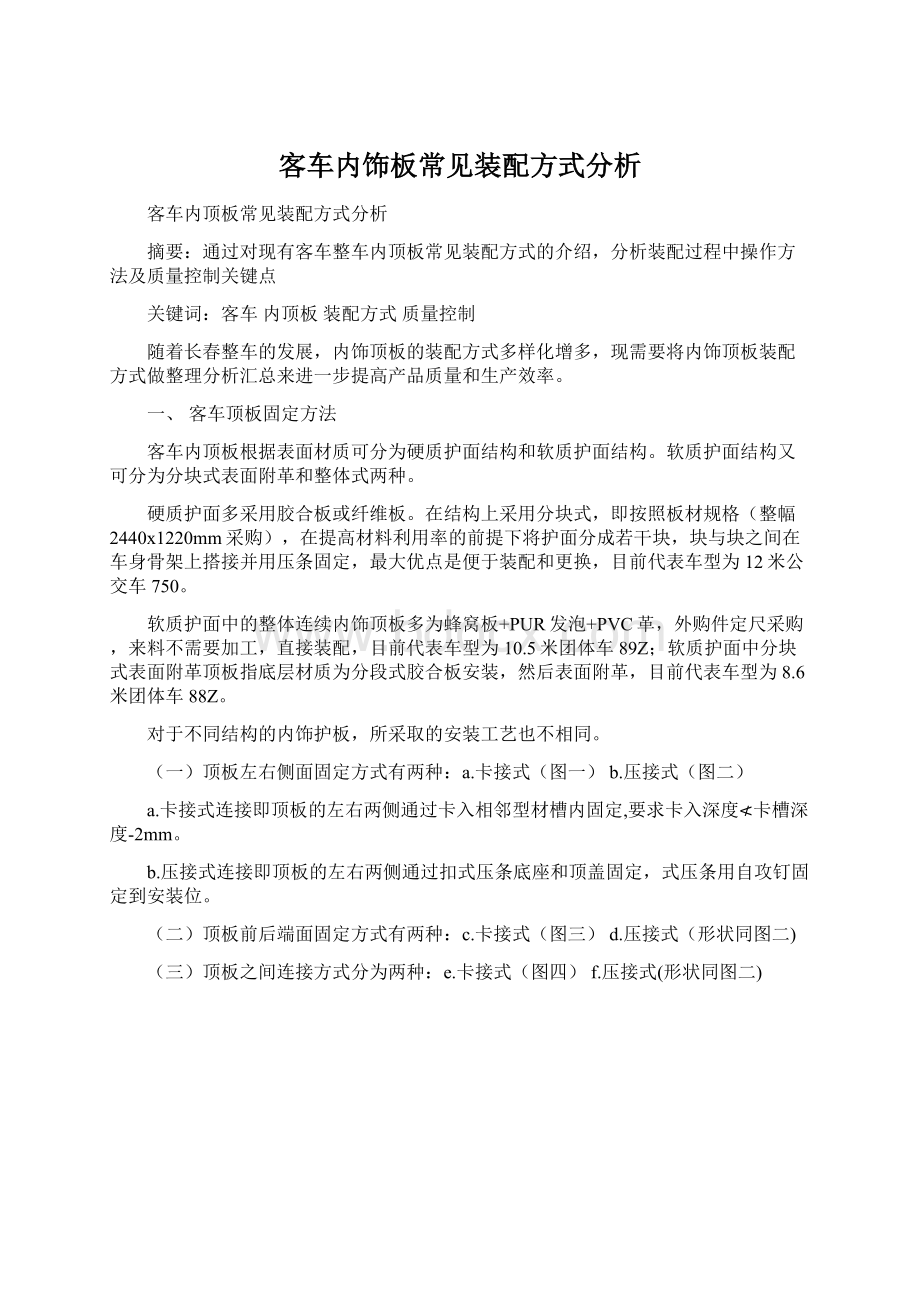
客车内饰板常见装配方式分析
客车内顶板常见装配方式分析
摘要:
通过对现有客车整车内顶板常见装配方式的介绍,分析装配过程中操作方法及质量控制关键点
关键词:
客车内顶板装配方式质量控制
随着长春整车的发展,内饰顶板的装配方式多样化增多,现需要将内饰顶板装配方式做整理分析汇总来进一步提高产品质量和生产效率。
一、客车顶板固定方法
客车内顶板根据表面材质可分为硬质护面结构和软质护面结构。
软质护面结构又可分为分块式表面附革和整体式两种。
硬质护面多采用胶合板或纤维板。
在结构上采用分块式,即按照板材规格(整幅2440x1220mm采购),在提高材料利用率的前提下将护面分成若干块,块与块之间在车身骨架上搭接并用压条固定,最大优点是便于装配和更换,目前代表车型为12米公交车750。
软质护面中的整体连续内饰顶板多为蜂窝板+PUR发泡+PVC革,外购件定尺采购,来料不需要加工,直接装配,目前代表车型为10.5米团体车89Z;软质护面中分块式表面附革顶板指底层材质为分段式胶合板安装,然后表面附革,目前代表车型为8.6米团体车88Z。
对于不同结构的内饰护板,所采取的安装工艺也不相同。
(一)顶板左右侧面固定方式有两种:
a.卡接式(图一)b.压接式(图二)
a.卡接式连接即顶板的左右两侧通过卡入相邻型材槽内固定,要求卡入深度≮卡槽深度-2mm。
b.压接式连接即顶板的左右两侧通过扣式压条底座和顶盖固定,式压条用自攻钉固定到安装位。
(二)顶板前后端面固定方式有两种:
c.卡接式(图三)d.压接式(形状同图二)
(三)顶板之间连接方式分为两种:
e.卡接式(图四)f.压接式(形状同图二)
图一图二
图三图四
二、硬质护面顶板装配方法具体介绍
(一)顶板固定方式全为卡接式(ace组合)安装方法
1.1在木工房将顶板按照产品要求下料修形并开出安全天窗、空调回风口等尺寸位置,要求切口平直,周边无毛刺,对于圆形孔位要用正确的开孔器开孔,开孔后不得划伤表面(铝扣板开孔后表面平整,不得有凹坑等)卡接式顶板下料时长度和宽度尺寸不能过小,要求装配后卡入滑槽深度符合要求。
1.2在顶板两侧固定型材装配完毕后(一般为长条顶灯),按照从前向后的装配顺序安装内顶板。
根据型材滑槽内侧间距L1配裁出最前端半工字压条的长度,切口平直,无毛刺。
将半工字压条用产品要求的标准件以图纸间距固定到顶棚上,工字压条和滑槽外露面间隙≯0.5mm。
1.3将下好料的侧板从滑槽后侧塞入滑槽内,然后从后向前推动,推动时两边同时推,推力均匀,推到前端卡入压条内,卡入深度符合上述要求。
卡接不到位时,可用木槌在敲击后端。
1.4将工字压条下料长度为L1,将下料完毕的工字压条小端卡入已装配完毕的顶板后端,用产品要求的标准件和间距将压条后端固定到顶棚上。
1.5用上述同样的方法安装其余的顶板和压条。
最后一块顶板安装时,因为周边已存在三个滑槽限位,此时安装先将顶板前端部左右两侧卡入滑槽后侧,向前推动顶板前端如槽后,将后侧半工字压条卡入顶板上要求顶板安装完毕不空鼓,卡接深度符合要求,对于有鼓动处,若无其他件(如扶手杆)安装在其上,需增加纽扣泡钉固定,泡钉固定时纵向位置一致,间距均匀,颜色符合要求。
1.6安全天窗和空调回风口、顶灯线束等顶板开孔处先在周边用十字槽沉头自攻钉将顶板固定到顶棚上。
(二)顶板固定当时全为压接式(bdf组合)安装方法
2.1在木工房将顶板按照产品要求下料修形并开出安全天窗、空调回风口等尺寸位置,要求切口平直,周边无毛刺,对于圆形孔位要用正确的开孔器开孔,开孔后不得划伤表面(铝扣板开孔后表面平整,不得有凹坑等)压接顶板下料时长度和宽度尺寸不能过小,要求装配后顶板之间、顶板与相邻被压接件间隙≯3mm。
2.2在两侧顶板固定型材装配完毕后(一般为长条顶灯),按照从前向后的装配顺序安装内顶板。
将最前侧顶板前端置于安装位,顶板中心与车身重心对正后,在顶板周边以间距500mm用产品要求的标准件固定到顶板上。
用同样的方法固定其余的顶板
2.3在顶板安装后,将扣式压条按照产品要求长度下料后将最前端将扣式压条底座置于安装位置后,配钻孔,用产品要求的标准件固定,要求压条底座安装无褶皱,无波浪形
2.4用同样的方法安装其余横向扣式压条,相邻压条平行度≯3mm。
2.5安装纵向扣式压条,要求纵向压条平行度不≯4/2000,若纵向压条最前(后)端与横向压条切口为45°即成90°拼接时,要求接头错位≯1mm,接头间隙≯0.5mm。
2.6将压条扣盖或嵌芯安装到位,要求安装后表面平整,无波浪,嵌芯嵌接到位,对于有封头压条,将封头固定到位
2.7安全天窗和空调回风口、顶灯线束等顶板开孔处先在周边用十字槽沉头自攻钉将顶板固定到顶棚上
2.8对于顶板为压接和卡接固定时,按照先卡接在压接,先横向后纵向原则固定
(三)顶板固定当时为卡接和压接组合式
目前卡接和压接组合式安装方式较少,在进行此类装配时,按照从前到后原则装配,依据先卡接后压接方法固定。
三、分段式表面附革式顶板安装方法介绍
3.1附革式顶板基板安装时在木工房先下料完毕,与上述硬质护面安装顺寻不相同是:
顶板安装在周边型材安装之前。
3.2将顶板用产品要求的标准件型号和间隙按照从一端开始固定到车上,要求固定后不空鼓,不歪斜,接缝间隙尽可能的小,无高差,对于有高差的需要找平。
3.3底板固定好后,在接缝处用腻子补缝以确保整个板面平整。
腻子干燥后,用打磨机对接缝处及整个板面打磨找平。
3.4对找平后的底板表面清洁,先用抹布擦去上面腻子污垢等杂质,然后用气嘴进一步清洁。
在清洁后的底板表面和附革面料背面喷地板革粘接胶,要求喷洒均匀,边缘喷洒到位,不得漏喷,一面喷250-300g/m2等胶挥发到稍微粘手时,从一个方向将附革层粘贴到底板上,同时用橡木刮刮平表面,消除气泡和褶皱边缘粘贴牢固到位
3.5将附革层修剪同时开出天窗孔、空调孔等孔位,修剪时要求和基板边线平齐,切口边缘无撕裂,边缘无翘起。
四、检查标准总结
顶板安装完毕后要进行安装质量检验,常见的检查项目及要求如下:
检查项目
检查标准
检查方法及手段
顶板
安装牢固、整齐、服帖、无鼓动声、清洁贴面无明显缺陷
目测、手感
顶板压条
1.装配牢固整齐、平顺与内挡板贴合间隙≯1.5mm2.接头错位≯1mm3.接头间隙≯0.5mm
4.相邻压条平行度≯3mm
目测
手感
卷尺、塞尺
紧固件装配质量
规格正确,紧固牢固,外露紧固件排列整齐,间隔均匀,其间距极限偏差为±2mm,边距的极限偏差为边距的±10%
卷尺
内装饰件
外观无损伤,安装服帖,接口处无缝隙等现象
目测
清洁
装配件清洁,施工现场无杂物,内饰件安装表面无灰尘、污渍
目测
永磁交流伺服电机位置反馈传感器检测相位与电机磁极相位的对齐方式
2008-11-07 来源:
internet 浏览:
504
主流的伺服电机位置反馈元件包括增量式编码器,绝对式编码器,正余弦编码器,旋转变压器等。
为支持永磁交流伺服驱动的矢量控制,这些位置反馈元件就必须能够为伺服驱动器提供永磁交流伺服电机的永磁体磁极相位,或曰电机电角度信息,为此当位置反馈元件与电机完成定位安装时,就有必要调整好位置反馈元件的角度检测相位与电机电角度相位之间的相互关系,这种调整可以称作电角度相位初始化,也可以称作编码器零位调整或对齐。
下面列出了采用增量式编码器,绝对式编码器,正余弦编码器,旋转变压器等位置反馈元件的永磁交流伺服电机的传感器检测相位与电机电角度相位的对齐方式。
增量式编码器的相位对齐方式
在此讨论中,增量式编码器的输出信号为方波信号,又可以分为带换相信号的增量式编码器和普通的增量式编码器,普通的增量式编码器具备两相正交方波脉冲输出信号A和B,以及零位信号Z;带换相信号的增量式编码器除具备ABZ输出信号外,还具备互差120度的电子换相信号UVW,UVW各自的每转周期数与电机转子的磁极对数一致。
带换相信号的增量式编码器的UVW电子换相信号的相位与转子磁极相位,或曰电角度相位之间的对齐方法如下:
1.用一个直流电源给电机的UV绕组通以小于额定电流的直流电,U入,V出,将电机轴定向至一个平衡位置;
2.用示波器观察编码器的U相信号和Z信号;
3.调整编码器转轴与电机轴的相对位置;
4.一边调整,一边观察编码器U相信号跳变沿,和Z信号,直到Z信号稳定在高电平上(在此默认Z信号的常态为低电平),锁定编码器与电机的相对位置关系;
5.来回扭转电机轴,撒手后,若电机轴每次自由回复到平衡位置时,Z信号都能稳定在高电平上,则对齐有效。
撤掉直流电源后,验证如下:
1.用示波器观察编码器的U相信号和电机的UV线反电势波形;
2.转动电机轴,编码器的U相信号上升沿与电机的UV线反电势波形由低到高的过零点重合,编码器的Z信号也出现在这个过零点上。
上述验证方法,也可以用作对齐方法。
需要注意的是,此时增量式编码器的U相信号的相位零点即与电机UV线反电势的相位零点对齐,由于电机的U相反电势,与UV线反电势之间相差30度,因而这样对齐后,增量式编码器的U相信号的相位零点与电机U相反电势的-30度相位点对齐,而电机电角度相位与U相反电势波形的相位一致,所以此时增量式编码器的U相信号的相位零点与电机电角度相位的-30度点对齐。
有些伺服企业习惯于将编码器的U相信号零点与电机电角度的零点直接对齐,为达到此目的,可以:
1.用3个阻值相等的电阻接成星型,然后将星型连接的3个电阻分别接入电机的UVW三相绕组引线;
2.以示波器观察电机U相输入与星型电阻的中点,就可以近似得到电机的U相反电势波形;
3.依据操作的方便程度,调整编码器转轴与电机轴的相对位置,或者编码器外壳与电机外壳的相对位置;
4.一边调整,一边观察编码器的U相信号上升沿和电机U相反电势波形由低到高的过零点,最终使上升沿和过零点重合,锁定编码器与电机的相对位置关系,完成对齐。
由于普通增量式编码器不具备UVW相位信息,而Z信号也只能反映一圈内的一个点位,不具备直接的相位对齐潜力,因而不作为本讨论的话题。
绝对式编码器的相位对齐方式
绝对式编码器的相位对齐对于单圈和多圈而言,差别不大,其实都是在一圈内对齐编码器的检测相位与电机电角度的相位。
早期的绝对式编码器会以单独的引脚给出单圈相位的最高位的电平,利用此电平的0和1的翻转,也可以实现编码器和电机的相位对齐,方法如下:
1.用一个直流电源给电机的UV绕组通以小于额定电流的直流电,U入,V出,将电机轴定向至一个平衡位置;
2.用示波器观察绝对编码器的最高计数位电平信号;
3.调整编码器转轴与电机轴的相对位置;
4.一边调整,一边观察最高计数位信号的跳变沿,直到跳变沿准确出现在电机轴的定向平衡位置处,锁定编码器与电机的相对位置关系;
5.来回扭转电机轴,撒手后,若电机轴每次自由回复到平衡位置时,跳变沿都能准确复现,则对齐有效。
这类绝对式编码器目前已经被采用EnDAT,BiSS,Hyperface等串行协议,以及日系专用串行协议的新型绝对式编码器广泛取代,因而最高位信号就不符存在了,此时对齐编码器和电机相位的方法也有所变化,其中一种非常实用的方法是利用编码器内部的EEPROM,存储编码器随机安装在电机轴上后实测的相位,具体方法如下:
1.将编码器随机安装在电机上,即固结编码器转轴与电机轴,以及编码器外壳与电机外壳;
2.用一个直流电源给电机的UV绕组通以小于额定电流的直流电,U入,V出,将电机轴定向至一个平衡位置;
3.用伺服驱动器读取绝对编码器的单圈位置值,并存入编码器内部记录电机电角度初始相位的EEPROM中;
4.对齐过程结束。
由于此时电机轴已定向于电角度相位的-30度方向,因此存入的编码器内部EEPROM中的位置检测值就对应电机电角度的-30度相位。
此后,驱动器将任意时刻的单圈位置检测数据与这个存储值做差,并根据电机极对数进行必要的换算,再加上-30度,就可以得到该时刻的电机电角度相位。
这种对齐方式需要编码器和伺服驱动器的支持和配合方能实现,日系伺服的编码器相位之所以不便于最终用户直接调整的根本原因就在于不肯向用户提供这种对齐方式的功能界面和操作方法。
这种对齐方法的一大好处是,只需向电机绕组提供确定相序和方向的转子定向电流,无需调整编码器和电机轴之间的角度关系,因而编码器可以以任意初始角度直接安装在电机上,且无需精细,甚至简单的调整过程,操作简单,工艺性好。
如果绝对式编码器既没有可供使用的EEPROM,又没有可供检测的最高计数位引脚,则对齐方法会相对复杂。
如果驱动器支持单圈绝对位置信息的读出和显示,则可以考虑:
1.用一个直流电源给电机的UV绕组通以小于额定电流的直流电,U入,V出,将电机轴定向至一个平衡位置;
2.利用伺服驱动器读取并显示绝对编码器的单圈位置值;
3.调整编码器转轴与电机轴的相对位置;
4.经过上述调整,使显示的单圈绝对位置值充分接近根据电机的极对数折算出来的电机-30度电角度所应对应的单圈绝对位置点,锁定编码器与电机的相对位置关系;
5.来回扭转电机轴,撒手后,若电机轴每次自由回复到平衡位置时,上述折算位置点都能准确复现,则对齐有效。
如果用户连绝对值信息都无法获得,那么就只能借助原厂的专用工装,一边检测绝对位置检测值,一边检测电机电角度相位,利用工装,调整编码器和电机的相对角位置关系,将编码器相位与电机电角度相位相互对齐,然后再锁定。
这样一来,用户就更加无从自行解决编码器的相位对齐问题了。
个人推荐采用在EEPROM中存储初始安装位置的方法,简单,实用,适应性好,便于向用户开放,以便用户自行安装编码器,并完成电机电角度的相位整定。
正余弦编码器的相位对齐方式
普通的正余弦编码器具备一对正交的sin,cos1Vp-p信号,相当于方波信号的增量式编码器的AB正交信号,每圈会重复许许多多个信号周期,比如2048等;以及一个窄幅的对称三角波Index信号,相当于增量式编码器的Z信号,一圈一般出现一个;这种正余弦编码器实质上也是一种增量式编码器。
另一种正余弦编码器除了具备上述正交的sin、cos信号外,还具备一对一圈只出现一个信号周期的相互正交的1Vp-p的正弦型C、D信号,如果以C信号为sin,则D信号为cos,通过sin、cos信号的高倍率细分技术,不仅可以使正余弦编码器获得比原始信号周期更为细密的名义检测分辨率,比如2048线的正余弦编码器经2048细分后,就可以达到每转400多万线的名义检测分辨率,当前很多欧美伺服厂家都提供这类高分辨率的伺服系统,而国内厂家尚不多见;此外带C、D信号的正余弦编码器的C、D信号经过细分后,还可以提供较高的每转绝对位置信息,比如每转2048个绝对位置,因此带C、D信号的正余弦编码器可以视作一种模拟式的单圈绝对编码器。
采用这种编码器的伺服电机的初始电角度相位对齐方式如下:
1.用一个直流电源给电机的UV绕组通以小于额定电流的直流电,U入,V出,将电机轴定向至一个平衡位置;
2.用示波器观察正余弦编码器的C信号波形;
3.调整编码器转轴与电机轴的相对位置;
4.一边调整,一边观察C信号波形,直到由低到高的过零点准确出现在电机轴的定向平衡位置处,锁定编码器与电机的相对位置关系;
5.来回扭转电机轴,撒手后,若电机轴每次自由回复到平衡位置时,过零点都能准确复现,则对齐有效。
撤掉直流电源后,验证如下:
1.用示波器观察编码器的C相信号和电机的UV线反电势波形;
2.转动电机轴,编码器的C相信号由低到高的过零点与电机的UV线反电势波形由低到高的过零点重合。
这种验证方法,也可以用作对齐方法。
此时C信号的过零点与电机电角度相位的-30度点对齐。
如果想直接和电机电角度的0度点对齐,可以考虑:
1.用3个阻值相等的电阻接成星型,然后将星型连接的3个电阻分别接入电机的UVW三相绕组引线;
2.以示波器观察电机U相输入与星型电阻的中点,就可以近似得到电机的U相反电势波形;
3.调整编码器转轴与电机轴的相对位置;
4.一边调整,一边观察编码器的C相信号由低到高的过零点和电机U相反电势波形由低到高的过零点,最终使2个过零点重合,锁定编码器与电机的相对位置关系,完成对齐。
由于普通正余弦编码器不具备一圈之内的相位信息,而Index信号也只能反映一圈内的一个点位,不具备直接的相位对齐潜力,因而在此也不作为讨论的话题。
如果可接入正余弦编码器的伺服驱动器能够为用户提供从C、D中获取的单圈绝对位置信息,则可以考虑:
1.用一个直流电源给电机的UV绕组通以小于额定电流的直流电,U入,V出,将电机轴定向至一个平衡位置;
2.利用伺服驱动器读取并显示从C、D信号中获取的单圈绝对位置信息;
3.调整旋变轴与电机轴的相对位置;
4.经过上述调整,使显示的绝对位置值充分接近根据电机的极对数折算出来的电机-30度电角度所应对应的绝对位置点,锁定编码器与电机的相对位置关系;
5.来回扭转电机轴,撒手后,若电机轴每次自由回复到平衡位置时,上述折算绝对位置点都能准确复现,则对齐有效。
此后可以在撤掉直流电源后,得到与前面基本相同的对齐验证效果:
1.用示波器观察正余弦编码器的C相信号和电机的UV线反电势波形;
2.转动电机轴,验证编码器的C相信号由低到高的过零点与电机的UV线反电势波形由低到高的过零点重合。
如果利用驱动器内部的EEPROM等非易失性存储器,也可以存储正余弦编码器随机安装在电机轴上后实测的相位,具体方法如下:
1.将正余弦随机安装在电机上,即固结编码器转轴与电机轴,以及编码器外壳与电机外壳;
2.用一个直流电源给电机的UV绕组通以小于额定电流的直流电,U入,V出,将电机轴定向至一个平衡位置;
3.用伺服驱动器读取由C、D信号解析出来的单圈绝对位置值,并存入驱动器内部记录电机电角度初始安装相位的EEPROM等非易失性存储器中;
4.对齐过程结束。
由于此时电机轴已定向于电角度相位的-30度方向,因此存入的驱动器内部EEPROM等非易失性存储器中的位置检测值就对应电机电角度的-30度相位。
此后,驱动器将任意时刻由编码器解析出来的与电角度相关的单圈绝对位置值与这个存储值做差,并根据电机极对数进行必要的换算,再加上-30度,就可以得到该时刻的电机电角度相位。
这种对齐方式需要伺服驱动器的在国内和操作上予以支持和配合方能实现,而且由于记录电机电角度初始相位的EEPROM等非易失性存储器位于伺服驱动器中,因此一旦对齐后,电机就和驱动器事实上绑定了,如果需要更换电机、正余弦编码器、或者驱动器,都需要重新进行初始安装相位的对齐操作,并重新绑定电机和驱动器的配套关系。
旋转变压器的相位对齐方式
旋转变压器简称旋变,是由经过特殊电磁设计的高性能硅钢叠片和漆包线构成的,相比于采用光电技术的编码器而言,具有耐热,耐振。
耐冲击,耐油污,甚至耐腐蚀等恶劣工作环境的适应能力,因而为武器系统等工况恶劣的应用广泛采用,一对极(单速)的旋变可以视作一种单圈绝对式反馈系统,应用也最为广泛,因而在此仅以单速旋变为讨论对象,多速旋变与伺服电机配套,个人认为其极对数最好采用电机极对数的约数,一便于电机度的对应和极对数分解。
旋变的信号引线一般为6根,分为3组,分别对应一个激励线圈,和2个正交的感应线圈,激励线圈接受输入的正弦型激励信号,感应线圈依据旋变转定子的相互角位置关系,感应出来具有SIN和COS包络的检测信号。
旋变SIN和COS输出信号是根据转定子之间的角度对激励正弦信号的调制结果,如果激励信号是sinωt,转定子之间的角度为θ,则SIN信号为sinωt×sinθ,则COS信号为sinωt×cosθ,根据SIN,COS信号和原始的激励信号,通过必要的检测电路,就可以获得较高分辨率的位置检测结果,目前商用旋变系统的检测分辨率可以达到每圈2的12次方,即4096,而科学研究和航空航天系统甚至可以达到2的20次方以上,不过体积和成本也都非常可观。
商用旋变与伺服电机电角度相位的对齐方法如下:
1.用一个直流电源给电机的UV绕组通以小于额定电流的直流电,U入,V出;
2.然后用示波器观察旋变的SIN线圈的信号引线输出;
3.依据操作的方便程度,调整电机轴上的旋变转子与电机轴的相对位置,或者旋变定子与电机外壳的相对位置;
4.一边调整,一边观察旋变SIN信号的包络,一直调整到信号包络的幅值完全归零,锁定旋变;
5.来回扭转电机轴,撒手后,若电机轴每次自由回复到平衡位置时,信号包络的幅值过零点都能准确复现,则对齐有效。
撤掉直流电源,进行对齐验证:
1.用示波器观察旋变的SIN信号和电机的UV线反电势波形;
2.转动电机轴,验证旋变的SIN信号包络过零点与电机的UV线反电势波形由低到高的过零点重合。
这个验证方法,也可以用作对齐方法。
此时SIN信号包络的过零点与电机电角度相位的-30度点对齐。
如果想直接和电机电角度的0度点对齐,可以考虑:
1.用3个阻值相等的电阻接成星型,然后将星型连接的3个电阻分别接入电机的UVW三相绕组引线;
2.以示波器观察电机U相输入与星型电阻的中点,就可以近似得到电机的U相反电势波形;
3.依据操作的方便程度,调整编码器转轴与电机轴的相对位置,或者编码器外壳与电机外壳的相对位置;
4.一边调整,一边观察旋变的SIN信号包络的过零点和电机U相反电势波形由低到高的过零点,最终使这2个过零点重合,锁定编码器与电机的相对位置关系,完成对齐。
需要指出的是,在上述操作中需有效区分旋变的SIN包络信号中的正半周和负半周。
由于SIN信号是以转定子之间的角度为θ的sinθ值对激励信号的调制结果,因而与sinθ的正半周对应的SIN信号包络中,被调制的激励信号与原始激励信号同相,而与sinθ的负半周对应的SIN信号包络中,被调制的激励信号与原始激励信号反相,据此可以区别和判断旋变输出的SIN包络信号波形中的正半周和负半周。
对齐时,需要取sinθ由负半周向正半周过渡点对应的SIN包络信号的过零点,如果取反了,或者未加准确判断的话,对齐后的电角度有可能错位180度,从而造成速度外环进入正反馈。
如果可接入旋变的伺服驱动器能够为用户提供从旋变信号中获取的与电机电角度相关的绝对位置信息,则可以考虑:
1.用一个直流电源给电机的UV绕组通以小于额定电流的直流电,U入,V出,将电机轴定向至一个平衡位置;
2.利用伺服驱动器读取并显示从旋变信号中获取的与电机电角度相关的绝对位置信息;
3.依据操作的方便程度,调整旋变轴与电机轴的相对位置,或者旋变外壳与电机外壳的相对位置;
4.经过上述调整,使显示的绝对位置值充分接近根据电机的极对数折算出来的电机-30度电角度所应对应的绝对位置点,锁定编码器与电机的相对位置关系;
5.来回扭转电机轴,撒手后,若电机轴每次自由回复到平衡位置时,上述折算绝对位置点都能准确复现,则对齐有效。
此后可以在撤掉直流电源后,得到与前面基本相同的对齐验证效果:
1.用示波器观察旋变的SIN信号和电机的UV线反电势波形;
2.转动电机轴,验证旋变的SIN信号包络过零点与电机的UV线反电势波形由低到高的过零点重合。
如果利用驱动器内部的EEPROM等非易失性存储器,也可以存储旋变随机安