机械制造技术基础课程设计减速器传动轴设计1.docx
《机械制造技术基础课程设计减速器传动轴设计1.docx》由会员分享,可在线阅读,更多相关《机械制造技术基础课程设计减速器传动轴设计1.docx(19页珍藏版)》请在冰豆网上搜索。
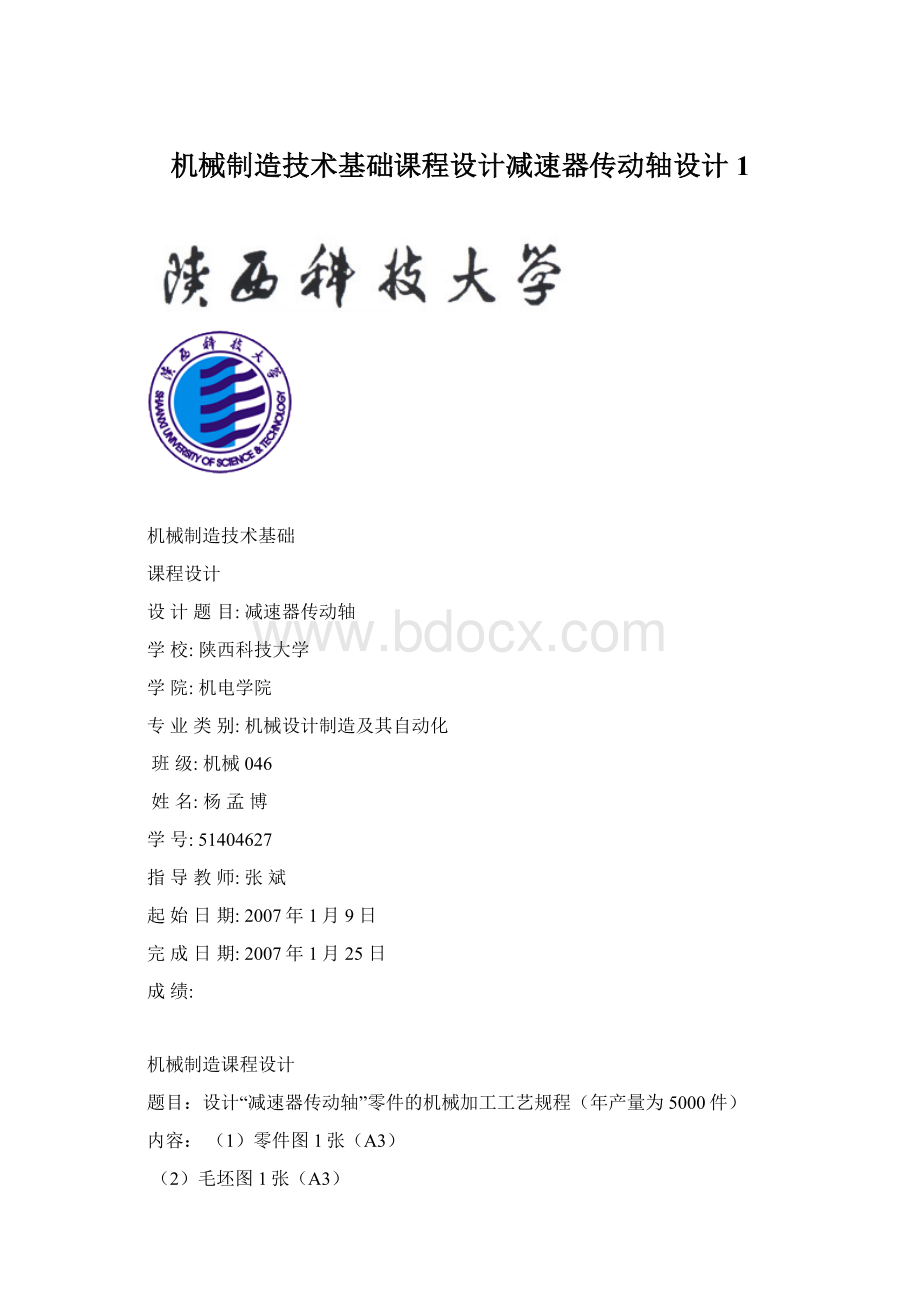
机械制造技术基础课程设计减速器传动轴设计1
机械制造技术基础
课程设计
设计题目:
减速器传动轴
学校:
陕西科技大学
学院:
机电学院
专业类别:
机械设计制造及其自动化
班级:
机械046
姓名:
杨孟博
学号:
51404627
指导教师:
张斌
起始日期:
2007年1月9日
完成日期:
2007年1月25日
成绩:
机械制造课程设计
题目:
设计“减速器传动轴”零件的机械加工工艺规程(年产量为5000件)
内容:
(1)零件图1张(A3)
(2)毛坯图1张(A3)
(3)工序简图1张(A2)
(4)工序卡片2张
(5)课程设计说明书1份
班级:
机械046
学生:
杨孟博
指导教师:
张斌
学号:
51404627
2007年1月25日
目录
1设计说明…………………………………………………………………41.1题目所给的零件是传动轴………………………………………4
1.2零件的工艺分析……………………………………………………41.3其主要加工表面位置要求…………………………………………41.4零件的材料………………………………………………………4
2工艺规程的设计………………………………………………………52.1零件表面加工方法的选择………………………………………5
2.2制定工艺路线……………………………………………………6
3机械加工余量﹑工序尺寸及毛坯尺寸的确定…………………………6
3.1确定加工余量……………………………………………………6
3.2确定毛坯尺寸……………………………………………………7
4确定切削用量及基本工时……………………………………………8
4.1车两端面……………………………………………………………9
4.2计算切削用量……………………………………………………9
5:
选择量具………………………………………………………………15
5.1选择刀具………………………………………………………15
5.2选择量具………………………………………………………15
6:
总结……………………………………………………………………16
7:
参考文献………………………………………………………………17
机械制造基础课程设计说明书
本次设计是在基本学完大学基础课,技术基础课以及大部分专业课后进行的。
是在毕业设计之前做的较全面较深入地对所学各课程进行的综合性复习及应用。
为我提供了一次理论联合实际训练的机会,在我的大学生涯中占有非常重要的地位。
我希望通过本次课程设计对自己的综合性训练,从中锻炼自己的独立思考问题,解决问题的能力,为今后的自己未来生活及工作打下一个良好的基础。
但由于能力有限,此设计难免有不宜之处。
恳请各位老师及同学给予指教。
一零件的分析
1.1题目所给的零件是传动轴(5000件年产)
此课程设计研究的是一传动轴。
该轴在机械制造领域中有着广泛的应用。
其主要作用是传递扭矩,使机构获得动力.
1.2零件的工艺分析
:
该传动轴需要加工的部分主要为回转面。
另外,轴两端为螺纹加工部分。
轴的各个轴肩相邻处需要加工退槽或者是砂轮越程槽。
轴肩两端要进行倒角加工。
在轴径为Φ40±0.005mm,Φ50±0.005mm和右端螺纹部分要加工键槽。
该传动轴的加工表面除了轴径为Φ64和Φ54的两部分表面的精度要求较小外,其他表面的粗糙度要求都为0.8。
为此可以以Φ64为分界分别对两边轴表面进行加工。
1.3其主要加工表面位置要求:
Φ40±0.005外圆相对A-B的圆跳动为0.02
Φ45±0.005相对于A-B的圆跳动为0.02
Φ54端面相对于A-B的圆跳动为0.02
Φ64外圆相对A-B的圆跳动为0.02
Φ50±0.008外圆相对A-B的圆跳动为0.02
Φ40±0.005外圆内花键槽关于A-B对称度为0.03。
Φ50±0.008花键槽关于A-B的对称度为0.03。
1.4零件的材料
材料为45钢考虑到轴在工作过程中经常承受变化的不稳定冲击性载荷,且轴的阶梯直径相差很大。
所以选用锻件,以使金属纤维尽量不被切断以保证工作可以正常可靠的进行。
由与其年产量达5000件,是大规模生产水平,且零件尺寸不大。
故可以模锻成型。
这对提高生产率,保证加工质量也是有利的。
二工艺规程设计
2.1零件表面加工方法的选择:
本零件的加工面有外圆,端面,槽等。
材料为45钢。
其加工方法如下:
2.1.2基准的选择:
粗基准的选择:
对于一般轴类零件而言,一般以外圆做为粗基准。
对于本零件来说,根据粗准的选择原则,零件上有较多的加工面时,为使各加工表面都得到足够的加工余量,应该选择毛坯上加工余量最少的表面做为粗基准。
对于本传动轴来说,轴径为Φ64mm慢慢的外圆表面精度较小,故其加工余量也会小,从而可做为粗基准分别加工其两边的表面。
而当加工传动轴的两端面时,为保证两端面的相互位置精度时,采用互为基准原则进行切削加工。
精基准的选择:
由精基准统一原则,对加工轴类零件时,采用两个顶尖孔做为统一精基准来加工轴上所有的外圆表面及端面。
这样可以保证各外圆表面间的同轴度和端面对轴心线的垂直度。
其次,还可以减少夹具的种类,降低夹具的设计和制造费用。
2.1.3Φ64㎜,Φ54㎜两个外圆面为未注明公差尺寸。
根据GB1800-79规定其公差等级按IT12,表面粗糙度为Ra6.3需进行粗车。
2.1.4Φ40±0.005㎜,Φ45±0.005㎜,Φ50±0.005㎜,Φ45±0.005㎜,有公差要求。
公差等级为IT7。
表面粗糙度为Ra0.8,可采用粗车→半精车→精车→磨削。
2.1.5槽的槽深公差等级分别为IT13,IT13和IT14。
其表面粗糙度分别为Ra3.2,Ra3.2和Ra6.3。
采用粗铣,半精铣。
由以上分析可得到如下方案:
工艺路线方案一:
工序1:
车两端面,钻中心孔车床
工序2:
车外圆,切槽,倒角车床
工序3:
车螺纹车床
工序4:
铣键槽磨床
工序5:
去毛刺钳工
工序6:
磨外圆磨床
工序7:
终检×
工艺路线方案二:
工序1:
两边同时车铣端面,钻中心孔。
工序2:
粗车轴上各外圆表面,半精车Φ64×54mm,×6mm
工序3:
以Φ64×54m和左端面孔定位,半精车轴左部的所有外表面。
工序4:
以Φ64×54mm和右端面孔定位,半精车轴右训的所有外表面。
工序5:
以两端面孔定位切退刀槽和砂轮越程槽,倒角。
工序6:
工两端面轴外表面上的螺纹。
工序7:
铣键槽。
工序8:
磨削各外圆。
工序9:
终检。
2.2制定工艺路线:
由工艺方案一,二分析。
方案一:
工序比较集中,这样能减少工件安装次数,有利于保证位置公差要求。
还能减少辅助时间,提高劳动生产效率。
对于小批量生产来说这样加工能使生产成本降低。
但对于大批加量加工来说,这样的加工方案并不能降低生产成本,反而会让生产成本增加。
方案二:
工序比较相对来说比较分散,同时考虑到该轴比较细长,采用端面孔定位加工轴上的各表面时,由于刀具的切深抗力会使得轴产生一定程度上的挠度,从而使得各表面产生不同程度的加工误差。
为此,在车外表面时,可采用一个端面孔和Φ64x54mm部分进行定位分别进行加工。
这样能减少加工时切削力引起太大的挠度误差。
综合以上两个方案的优点和不足从而制定一个最优的方案如下:
1:
车两端面,钻中心孔组合车床
2:
粗车外圆Φ64mm,Φ40±0.005㎜,Φ45±0.005㎜,Φ50±0.005㎜,Φ45±0.005㎜(两端中心孔定位)
车床
3:
精车外圆Φ40±0.005㎜,Φ35±0.005㎜,Φ50±0.008㎜,Φ45±0.005㎜,切退刀槽,倒角(两端中心孔定位)车床
4:
车螺纹2×M32×1.5-6g,(两端中心孔定位)车床
5:
铣键槽(两端中心孔定位)铣床
6:
去毛刺钳工
7:
磨外圆面H,M,G,P,N磨床
8:
终检
三:
确定机械加工余量及毛坯尺寸。
设计毛坯图。
3.1确定加工余量,按JB3835-85确定,确定时根据估算的锻件质量,加工精度和锻件形状复杂系数。
由表2.2-25可查得外表面的加工余量。
3.1.1锻件质量计算得2.96kg,估算为4.8㎏
3.1.2加工精度除Φ64㎜,Φ54㎜外一般表面的加工精度为IT7。
3.1.3锻件形状复杂系数、
S=
S=0.834,长度偏差为
3.1.4根据光轴类和多台阶轴类的机械加工余量及公差(JZ4-59,JZ8-50)表5-28查得加工余量为6±2㎜。
3.2确定毛坯尺寸
由上面查得的加工余量。
分析此零件,除Φ64㎜,Φ54㎜外一般的表面皆为Ra0.8。
因此只需将零件的尺寸加上余量值即可(由于有的只需粗加工,这时可取所差数据中的较小值。
当表面需要粗车→半精车→精车时,可取较大值)。
其毛坯尺寸如下表:
(毛坯图附图2)
零件尺寸
单面加工尺寸
毛坯尺寸
Φ45±0.005㎜
3㎜
Φ51±0.005㎜
Φ64㎜
2㎜
Φ68㎜
Φ45±0.005㎜
3㎜
Φ51±0.005㎜
3.2.1外圆Φ52加工表面
考虑其毛坯加工表面长度为125㎜,表面粗糙度为Ra6.3。
其毛坯尺寸为Φ64㎜,所以只需粗车单边余量1.5㎜就能满足要求。
3.2.2外圆表面2×Φ45±0.005㎜,Φ40±0.005㎜,
2×M32×1.5-6g,毛坯为实心,其精度为IT7.参照《工艺手册》表可确定其工序尺寸及余量。
3.2.3
传动轴毛坯(锻件)尺寸允许偏差
Φ40±0.005㎜
+1.5
-0.6
表2.2-13
Φ45±0.005㎜
+1.5
-0.6
Φ54㎜
+1.5
-0.6
Φ64㎜
+1.5
-0.6
Φ50±0.005㎜
+1.5
-0.6
Φ45±0.005㎜
+1.5
-0.6
340㎜
直线度公差1.5
表2.2-19
3.2.4确定毛坯热处理方式
传动轴经锻造后应安排退火,正火,以消除残留的锻造应力,并使不均匀的金相组织通过重新结晶而得到细化,均匀的组织,从而改善加工性能。
3.2.5加工表面加工余量偏差的确定
加工表面
工序双边余量
工序尺寸及公差
表面粗糙度
粗
半精
精
粗
半精
精
粗
半精
精
Φ64㎜
3
Φ64±0.01
Ra6.3
Φ54㎜
13
Φ54±0.01
Ra6.3
Φ40±0.005㎜
2.4
2.2
0.2
Φ42.4±0.01
Φ42.2±0.01
Φ40.2±0.01
Ra6.3
Ra3.2
Ra0.08
Φ45±0.005㎜
3.4
2.2
0.2
Φ48.4±0.01
Φ47.2±0.01
Φ45.2±0.01
Ra6.3
Ra3.2
Ra0.08
Φ50±0.008㎜
3.4
2.2
0.2
Φ53.4±0.01
Φ52.2±0.01
Φ50.2±0.01
Ra6.3
Ra3.2
Ra0.08
四确定切削用量及基本工时
4.1车两端面,打中心孔,粗车Φ64㎜,Φ50±0.008㎜,Φ54㎜,表面粗糙度值为Ra6.3,
4.1.1加工条件:
材料45钢模锻正火
4.1.2机床选择:
CA6140卧式车床
4.1.3刀具选择:
刀片材料为YT15,刀杆尺寸16㎜×25㎜,
=90°,
°,
=12°,
=0.5㎜。
4.2计算切削用量
4.2.1粗车Φ64㎜
确定端面最大加工余量:
已知毛坯长度方向的余量为2(-0.7~1.5)。
考虑7°的锻模拔模斜度。
则毛坯的最大加工余量为8㎜。
分两次加工,切削深度为2㎜,公差为IT13。
计算切削速度
按〈〈切削手册〉表1.27,切削速度的计算公式为(刀具寿命选T=60min)
V=
m/min
式中
=242,
=0.15,
=0.35,m=0.2,修正系数k(查〈〈切削手册〉〉表1.28即
=1.44,Ks=0.8,Kk=1.04,
=0.81,Kbv=0.97
所以v=108.6m/min
确定机床的主轴转速
n=
=1000×108.6/(3.14×68)=500r/min
按照机床说明书(见〈〈工艺手册〉〉表6.2-8),与500相近的机床转速为500r/min。
计算切削工时
按照〈〈工艺手册〉〉表6.2-1,取l=130,
=130/(0.52×500)=0.50min
4.2.2粗车Φ50±0.005㎜
切削深度:
单边余量为1.7㎜,可一次切削。
进给量:
根据〈〈工艺手册〉〉表1.4,选择f=0.50
计算切削速度:
见〈〈工艺手册〉〉表1.27
V=
m/min
=116m/min
确定主轴转速:
n=
=1000×116/(3.14×64)=577r/min
按照机床说明书(见〈〈工艺手册〉〉表6.2-8),与710相近的机床转速为560r/min。
切削工时:
按照〈〈工艺手册〉〉表6.2-1,取l=80,
=80/(0.50×560)=0.286min
4.2.3粗车Φ54㎜
切削深度:
单边余量为4㎜,可一次切削。
进给量:
根据〈〈工艺手册〉〉表1.4,选择f=0.50
计算切削速度:
见〈〈工艺手册〉〉表1.27
V=
m/min
=129m/min
确定主轴转速:
n=
=1000×129/(3.14×64)=641r/min
按照机床说明书(见〈〈工艺手册〉〉表6.2-8),与790相近的机床转速为710r/min。
此时实际切削速度为124m/min
切削工时:
按照〈〈工艺手册〉〉表6.2-1,取l=6
=6/(0.50×710)=0.016min
4.2.4粗车Φ45±0.005㎜
切削深度:
单边余量为1.7㎜,可一次切削。
进给量:
根据〈〈工艺手册〉〉表1.4,选择
f=0.50
计算切削速度:
见〈〈工艺手册〉〉表1.27
V=
m/min
=122m/min
确定主轴转速:
n=
=1000×122/(3.14×51)=761r/min
按照机床说明书(见〈〈工艺手册〉〉表6.2-8),与761相近的机床转速为710r/min。
此时实际切削速度为114m/min
切削工时:
按照〈〈工艺手册〉〉表6.2-1,取l=52,
=(125+105)/(0.50×710)=0.481min
4.2.5粗车Φ40±0.0065㎜
切削深度:
单边余量为2.5㎜,可一次切削。
进给量:
根据〈〈工艺手册〉〉表1.4,f=0.50
计算切削速度:
见〈〈工艺手册〉〉表1.27
V=
m/min
=138m/min
确定主轴转速:
n=
=1000×138/(3.14×47.6)=923r/min
按照机床说明书(见〈〈工艺手册〉〉表6.2-8),与923相近的机床转速为900r/min。
此时实际切削速度为134m/min
切削工时:
按照〈〈工艺手册〉〉表6.2-1,取l=55,
=55/(0.50×900)=0.122min
验证机床功率:
主切削力F按〈〈工艺手册〉〉表1.29所示公式计算
F=
式中
=2880,
=1.0,
=0.75,
=0.94,
=0.89
所以F=2780N
=6.43KW
由〈〈切削手册〉〉表1.30中机床说明书可知CA6140卧式车床主电动机的功率为7.5KW。
所以机床的功率足够,能够保证正常加工。
验证机床进位系统强度
以知主切削力为F=2780N,径向切削力
按〈〈切削手册〉〉表1.2所示公式计算。
=279N
径向切削力Ff按〈〈切削手册〉〉表1.29所示公式计算。
=1292N
取机床导轨与床鞍之间的摩擦系数μ=0.1。
则切削力在纵向进给方向上对进给机构的作用力:
F=
+μ(
+F)=1292+27.9+278=1597.9N
小于机床纵给方向可以承受的最大纵向力。
(〈〈切削手册〉〉表1.30)所以机床系统可正常工作。
工序2的切削用量及基本时间
工步
切削深度
进给量
切削速度
车床转速
基本时间
粗车外圆Φ64㎜
4
0.5
v=108.6m/min
500r/min。
0.50min
粗车Φ50±0.005㎜
1.7
0.5
116m/min
760r/min。
0.286min
粗车Φ54㎜
4
0.5
129m/min
760r/min。
0.016min
粗车Φ45±0.005㎜
1.7㎜
0.5
122m/min
710r/min。
0.481min
粗车Φ40±0.005㎜
2.4
0.5
138m/min
900r/min。
0.122min
Φ32
3
0.5
207m/min
1200r/min
0.025min
粗车Φ45±0.005㎜
1.7
0.5
122m/min
710r/min。
0.481min
Φ32mm
3
0.5
207m/min
1200r/min
0.02min
4.2.6精加工
机床选择:
C620-1卧式车床。
刀具选择:
刀片材料为YT15,刀杆尺寸16㎜×25㎜,
=90°,
=15°,
=12°,
=0.5㎜。
工序3的切削用量及基本时间
工步
切削深度
进给量
切削速度
车床转速
基本时间
Φ40±0.005㎜
1.2
0.3
150m/min
1200r/min
0.056min
Φ45±0.005㎜
1.2
0.3
150m/min
1200r/min
0.161min
Φ50.005㎜
1.2
0.3
150m/min
1200r/min
0.15min
Φ45±0.005㎜
1.2
0.3
150m/min
1200r/min
0.15min
切退刀槽
倒角
4.2.7车螺纹2×M24×1.5-6g㎜
计算切削速度由参考文献(7)表中21查得。
车床选择:
CM6125卧式车床
刀具寿命T=60㎜选择高速螺纹车刀。
切削深度为1.5,走刀次数为1。
由表6.2-14中公式计算得粗车时切削速度为21.57m/min。
确定主轴转速:
n=1000v/(D×π)
=1000×21.57/(3.14×32)
=134r/min
按机床说明书取n=320r/min
实际切削速度:
V=(320×3.14×32)/1000
=32.2m/min
切削工时:
取长度l=20㎜
=20/(320×0.2)
=0.3125min
4.2.8铣键槽
由表4.2-37得
1)选择铣床X51立式铣床
2)刀具选择高速钢错齿三面刃铣刀d=125mmL=13mmz=20.
3)刀具角度选择前角γ=15°,后角α=12°(周齿),α=6°(端齿)
4)纵向进给量f=50mm/min
5)横向进给量f=25mm/min
6)加工时间T1=25/25+12/50=1.24min
T2=63/25+14/50=2.8min
T3=20/25+8/50=0.96min
T=T1+T2+T3=1.24+2.8+0.96=4.0min
4.2.9磨削
选择砂轮见〈〈工艺手册〉〉第三章磨料选择各表。
结果为:
WA46Kv6P350×40
1)切削用量:
砂轮转速为n=1500r/min(见机床说明书)
2)砂轮的切削速度V=27.5m/s
3)f=0.5轴向方向的进给量B=20㎜
4)工件速度V=10m/min
5)径向方向的进给量f=0.015/20行程
6)切削工时T=(2×L×b×Z×b×k)/(1000×v×Fa×Fv)
L加工长度120,70,60,20,80,
b加工宽度40,45,50,45
Z单边加工余量0.1
k系数1.10
v工作台移动速度
Fa工作台往返一次砂轮轴向进给量
Fv工作台往返一次砂轮轴向进给量
T=2×(20+80+60+70+120)×(40+45+50+45)×0.1×1.1/(1000×10×20×0.015)
=2.31min
五选择夹具
本零件除粗铣及半精铣槽等工序需用专用夹具外,其他各工序使用通用夹具(三爪自定心卡盘)即可。
5.1选择刀具
(1)在车床上加工的工序,一般都选用硬质合金车刀和镗刀。
加工钢质零件采用YT类硬质合金,粗加工用YT5,半精加工用YT15,精加工用YT30,切槽刀宜选用高速钢。
(2)铣刀按表3.1-40选错齿三面刃铣刀。
零件要求铣切深度为4mm,5mm,3mm,按表3.1-28,铣刀直径应为60-75mm,因此所选铣刀:
半精铣工序铣刀直径d=70mm,齿数z=20
5.2选择量具
本零件属成批生产,一般均采用通用量具。
选择量具的方法有二种:
一是按计量器具的不确定度选择;二是按计量器具的测量方法极限误差选择。
选择时,采用其中的一种方法即可。
5.2.1选择各外圆加工面的量具
工序2中粗车外圆Φ52㎜达到图纸要求,现按计量器具的不确定度选择该加工表面加工时所用量具:
该尺寸公差T=0.016。
按表5.1-1,计量器具不确定度允许值U1=0.009mm。
根据表5.1-2分度值0.02游标卡尺,其不确定度数值U=0.02mm,U>U1,所以不能选用,必须U外圆加工面所用量具
工序
加工面尺寸
尺寸公差量具
2
Φ64㎜,Φ54㎜,Φ40±0.005㎜,Φ45±0.005㎜,Φ50±0.005㎜,Φ45±0.005㎜,Φ32㎜
分度值0.02测量范围0-150游标卡尺
3
Φ40±0.005㎜Φ45±0.005㎜,Φ50±0.005㎜,Φ45±0.005㎜
分度值0.01mm测量范围25-150mm外径百分尺
4
2×M32×1.5-6g
0.095分度值0.01mm测量范围0-50mm外径百分尺
5.2.2选择加工轴向尺寸所用量具,加工轴向尺寸所选量具如下表
:
加工轴向尺寸所选量具
340
分度值0.01测量范围250~500mm外径百分尺
20,50,120,1.5,
6,80,160,0.5
分度值0.01测量范围0~150mm外径百分尺
5.2.3选择加工槽所用量具