机械毕业设计274T108吨自卸车拐轴的断裂原因分析及优化设计.docx
《机械毕业设计274T108吨自卸车拐轴的断裂原因分析及优化设计.docx》由会员分享,可在线阅读,更多相关《机械毕业设计274T108吨自卸车拐轴的断裂原因分析及优化设计.docx(23页珍藏版)》请在冰豆网上搜索。
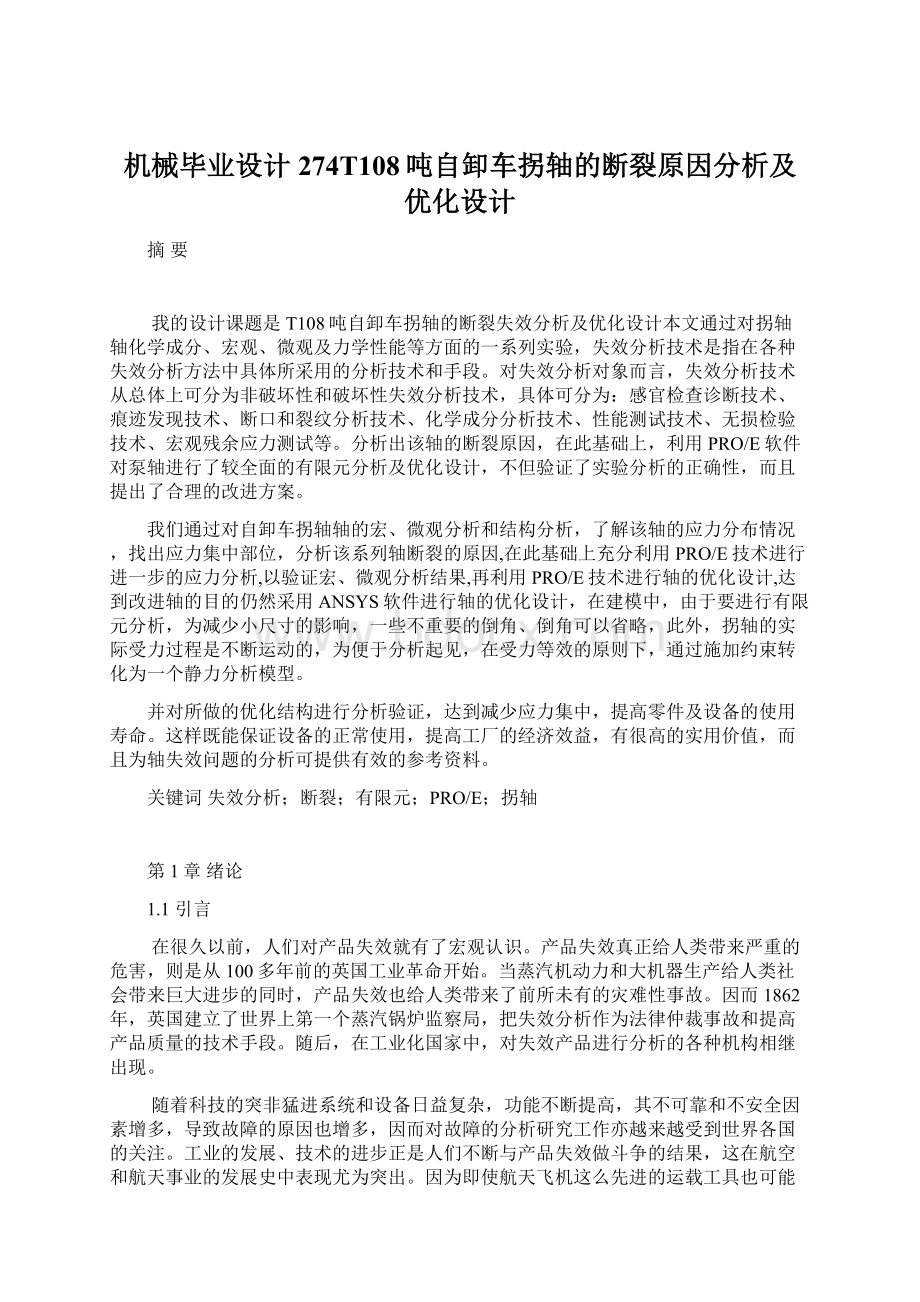
机械毕业设计274T108吨自卸车拐轴的断裂原因分析及优化设计
摘要
我的设计课题是T108吨自卸车拐轴的断裂失效分析及优化设计本文通过对拐轴轴化学成分、宏观、微观及力学性能等方面的一系列实验,失效分析技术是指在各种失效分析方法中具体所采用的分析技术和手段。
对失效分析对象而言,失效分析技术从总体上可分为非破坏性和破坏性失效分析技术,具体可分为:
感官检查诊断技术、痕迹发现技术、断口和裂纹分析技术、化学成分分析技术、性能测试技术、无损检验技术、宏观残余应力测试等。
分析出该轴的断裂原因,在此基础上,利用PRO/E软件对泵轴进行了较全面的有限元分析及优化设计,不但验证了实验分析的正确性,而且提出了合理的改进方案。
我们通过对自卸车拐轴轴的宏、微观分析和结构分析,了解该轴的应力分布情况,找出应力集中部位,分析该系列轴断裂的原因,在此基础上充分利用PRO/E技术进行进一步的应力分析,以验证宏、微观分析结果,再利用PRO/E技术进行轴的优化设计,达到改进轴的目的仍然采用ANSYS软件进行轴的优化设计,在建模中,由于要进行有限元分析,为减少小尺寸的影响,一些不重要的倒角、倒角可以省略,此外,拐轴的实际受力过程是不断运动的,为便于分析起见,在受力等效的原则下,通过施加约束转化为一个静力分析模型。
并对所做的优化结构进行分析验证,达到减少应力集中,提高零件及设备的使用寿命。
这样既能保证设备的正常使用,提高工厂的经济效益,有很高的实用价值,而且为轴失效问题的分析可提供有效的参考资料。
关键词失效分析;断裂;有限元;PRO/E;拐轴
第1章绪论
1.1引言
在很久以前,人们对产品失效就有了宏观认识。
产品失效真正给人类带来严重的危害,则是从100多年前的英国工业革命开始。
当蒸汽机动力和大机器生产给人类社会带来巨大进步的同时,产品失效也给人类带来了前所未有的灾难性事故。
因而1862年,英国建立了世界上第一个蒸汽锅炉监察局,把失效分析作为法律仲裁事故和提高产品质量的技术手段。
随后,在工业化国家中,对失效产品进行分析的各种机构相继出现。
随着科技的突非猛进系统和设备日益复杂,功能不断提高,其不可靠和不安全因素增多,导致故障的原因也增多,因而对故障的分析研究工作亦越来越受到世界各国的关注。
工业的发展、技术的进步正是人们不断与产品失效做斗争的结果,这在航空和航天事业的发展史中表现尤为突出。
因为即使航天飞机这么先进的运载工具也可能发生故障,如美国的价值12亿美元的“挑战者”号航天飞机,在1986年1月28号第11次升空时突然爆炸,使7名宇航员遇难,这一惨痛悲剧再次告戒人们忽视产品失效问题将带来灾难性的恶果。
任何一次失效都可以看成是产品在服役条案件下所做的一次最真实做可靠的学实验的结果;通过失效分析判断失效模式,找出失效的原因和影响因素,也就找到了薄弱环节所在,从而改进有关部门的工作。
提高产品质量。
失效分析是可靠性工程的技术基础之一;是安全工程的重要技术保障之一;是维修工程的理论基础和指导依据;可产生巨大的经济效益和社会效益。
因而开展失效分析工作是非常有意义的,其重要性一般包括以下几个方面:
1.可以保证产品的可靠性,减少由于设备失效造成的人身伤亡和直接的经济损失;
2.可以从中吸取大量的经验教训以利制定和完善产品质量管理的有关文件、标准和规定、是产品质量管理的一个重要环节;
3.有助于及时“吃透”国外先进技术、提高引进速度和效率;
4.通过对进口设备的失效分析可以向外商提供索赔依据或技术仲裁
5.可以使设备维修工作建立在失效分析的基础上,从而取得良好的事故预防;
6.失效分析的结果也是现行技术的规范、规程和标准的实用性的实地检验,可作为修订和制定文件的依据;
7.失效分析的头脑国际资料是指定科技开发规划和经济发展规划的重要依据,失效分析可以为各级人员正确处理现场技术问题提供科学的依据。
在我国,由于长期的历史原因,现有设备超期服役带病运行相当普遍,有相当一部分设备存在各种结构缺陷、工艺缺陷、加工缺陷、制造缺陷、材料缺陷和使用不当产生的裂纹或损伤腐蚀介质影响或长期超载运行等,或盲目使用这些设备而不及时采取措施进行监控和预防,必将发生事故,因而,,为了尽量减少事故的发生,需要进行失效分析的研究。
目前关于失效分析的研究比较多,他们大多采用传统的宏观、微观分析法对失效的原因进行分析,本文首先也将采用宏观、微观对T108吨自卸车拐轴进行失效分析。
1.2失效分析的发展简况
长期以来,人类在生产实践中不断与产品失效作斗争,但失效分析仅作为零星、分散、宏观的经验世代相传。
失效分析作为一种学科分支还是近半个世纪的事情。
材料科学的兴起、先进测试技术的应用以及近代物理、化学等的全面发展,使得人民能够从微观方面阐明产品失效的本质、规律和原因。
在此基础上,失效分析走上系统、综合、理论化的新阶段。
近半个世纪所积累的失效分析知识与技术千百倍于人类前期有关知识的总和。
但这种知识必然随着人类生产实践和科技进步而不断发展。
虽然由于科技的发展,产品在设计、生产、使用与维修上的技术改进,似的产品的可靠性日益提高,然而,失效事件并不会消失。
而且,产品的自动化程度愈高、技术愈密集,一旦出现失效,造成的损失就愈严重。
因此失效分析将随着科技的高速发展显得更为重要。
远在1862年英国建立世界第一个蒸气锅炉监察局时,失效分析就被作为法律仲裁产品质量事故的技术判断手段。
在1938-1945年间,美国质量管理学会发起“失效废品检验规划”,号召生产企业把失效分析作为重要环节纳入质量管理系统。
在四十年代末和五十年代初,为解决电子产品失效问题而发展起来的可靠性理论使失效分析进入到一个新的阶段。
到六十年代,人们更开始了机械设备系统可靠性理论的研究。
近年来,失效物理和失效分析在这种认识推动下,也得到了很大的重视和发展。
失效分析推动科学技术进步,促进国民经济健康发展,提高机械产品质量,在国民经济中有重要作用和意义。
1.3本课题的背景和意义。
此课题研究的拐轴是某厂108吨自卸车上一部件,在此称为主轴。
我们从设计图纸上了解到主轴的结构,按使用情况我们在主轴(拐轴)尾部接上管子,然后通过焊接用一个外径为450,内径为374,总长为1946的圆管约束,约束位置在离圆管端部418处,主轴端部离中心线472。
第2章对自卸车拐轴进行失效分析的方法
2.1失效分析的概况
2.1.1失效分析的基本概念
所谓失效,按照国家标准GB3187-82《可靠性基本词术语及定义》,就是:
“产品丧失规定的功能,对可恢复产品通常也称故障”(12)。
为了研究失效的原因,确定失效的模式或机理,并采取补救或预防措施以防止失效再度发生的技术活动与管理活动,叫做“失效分析”(12,13)。
因此失效分析是可靠性工程的重要组成部分,也是保证产品可靠性而需建立的反馈系统的重要环节。
失效分析是一门涉及系统分析、系统安全、产品设计、材料力学、断裂力学、断裂物理、断口学、材料学、测试技术、金属学、金属工艺、强度计算、产品质量全面管理等众多领域的综合学科,它包括三个方面:
1.事前故障的预测技术,如可靠度计算、故障率评价和可靠性分析法(故障树分析FTA,故障模式和影响分析FMEA,事件树分析ETA);
2.事中故障诊断技术(应力定量化技术、故障检测及故障征兆诊断技术、设备或系统强度、故障性能定量化技术及劣化定量化技术等);
3.事后失效分析(寿命预测技术、故障机理、失效模式的测定技术、失效评定的标准、维修技术等)。
上述事后分析也既是失效分析或故障分析,是指事故或鼓掌发生后的检测和分析,以便找到失效的部位、原因和机理;掌握产品的改进线索或修复方法,防止问题重复发生。
近年来,失效分析工作还注意了反馈与发展,在工况与质量上做了不少工作,从事前分析、事后预防发展到事中监控。
2.1.2失效的主要来源及模式
失效经常是由多方面原因造成的,其主要来源包括设计、选材、材料缺陷、制造工艺、再加工、组装、检查、试验、质量控制、贮运、工作条件、维修工作中预先未暴露的过载以及机械或化学的损伤等。
1.设计上的缺点:
机械缺口、改变设计、零件的是升级使用、设计判据不充分等。
2.材料选择上的缺点:
拉伸试验数据不准确。
3.材料中的缺陷:
铸件(冷隔、夹杂物、疏松、空隙和缩孔是铸件特有的)铸件(折叠、接逢、收缩、空洞和锻造流线花样为锻件特有的)。
4.加工中存在的问题:
各种冷热加工中的问题。
5.装配中的失误:
操作人员的疏忽行为、装配规程不完善、对中不良。
6.不合理的服役条件:
启动、停车、维修不当。
失效模式是失效的外在宏观表现形式和过程规律。
金属构件的失效模式可分为断裂、表面损伤和过量变形这三大方面。
具体的说,机械失效的主要模式如表2.2。
表2.2金属部件的各种失效模式
过量变形
1)力和温度或者力或温度引起弹性变形;2)屈服;3)压痕;4)蠕变;5)冲击变形
表面损伤
1)磨损
a。
粘着磨损;b。
磨粒磨损;c。
腐蚀磨损;d。
点腐蚀;e。
冲击磨损;f。
微振磨损;
g。
接触疲劳磨损;h。
剥落。
2)腐蚀
a。
均匀腐蚀;b。
缝隙腐蚀;c。
电池作用腐蚀;d。
点腐蚀;e。
晶间腐蚀;f。
选择侵出;g。
冲蚀;h。
气蚀;i。
氢损伤;j。
生物腐蚀;k。
应力腐蚀;l。
微振腐蚀
断裂
1)延性断裂
2)脆性断裂
3)冲击断裂
4)疲劳断裂
a。
高温疲劳;b。
高周疲劳;c。
低周疲劳;d。
热疲劳;
e。
接触疲劳;f。
冲击疲劳;g。
腐蚀疲劳;h。
微振疲劳
5)应力持久断裂
6)蠕变-疲劳复合断裂
2.2常用失效分析及技术
2.2.1常用失效方法(失效分析的一般程序与步骤)
1.失效分析的思路
失效分析思路是对于已经发生的事故考虑从什么地方开始,沿着什么样的程序去分析研究故障现象的因果关系,确定事故原因,完成分析任务.断裂分析思路一般是:
断裂失效事故-故障件裂纹或断口分析-力学性能分析-显微组织分析-结构受力分析-使用维护分析.必要时可进行工艺分析、材料成分分析、环境分析、相结构分析和残余应力分析。
2.断裂失效分析的一般程序
图2.1断裂失效分析的一般程序
3.失效分析的具体过程
(1)调查研究
①向机器操作者调查破坏过程,观察破坏现场,了解破坏构件在机器的部位和工作情况。
②向生产工人和技术人员调查构件的生产工艺历史和参数。
③向设计人员调查构件的设计过程和设计计算。
④外观检查,观察破坏构件的外形特征。
⑤服役条件、工作环境等的综合分析。
(2)断口分析、破面分析、变形量测定
①断裂试样的正确选择及切取。
②断口的宏观分析。
③断口的微观分析。
(3)内在质量的检验
①低倍检验:
主要检查夹杂、气孔等低倍检查项目。
②金相组织分析:
检查破断零件的裂纹分布及走向,金相组织是否正常。
③材料的化学成分分析:
主要复验材料的常规机械性能是否合格,据构件破坏部位的几何形状、应力分布情况、负载的变化等情况与该类情况下的静/动机械性能比较。
(4)判明失效的原因:
据上面的调查研究及实验检查结果,综合分析造成构件失效的原因。
(5)提高改进措施
(6)实际运行考验
2.2.2常用失效分析技术
失效分析技术是指在各种失效分析方法中具体所采用的分析技术和手段。
对失效分析对象而言,失效分析技术从总体上可分为非破坏性和破坏性失效分析技术,具体可分为:
感官检查诊断技术、痕迹发现技术、断口和裂纹分析技术、化学成分分析技术、性能测试技术、无损检验技术、宏观残余应力测试等。
1.感官检查诊断技术
失效分析与医生看病或诊察案件相似,对信息资料既要单独和分类推敲,又要综合分析,通盘考虑,然后提出疑问、假设,进一步有针对性地补充信息资料,多方考核,验证假设,从众多原因中,逐步确定取舍,从而得出可靠结论,并提出切实可行的预防措施,最后在实践中进一步验证。
感官检查是一种直观、简洁、使用方便、可靠性好的应用技术。
主要依靠人体感官功能智力、经验的结合获取、存储、加工处理信息,达到分析目的。
它主要包括视觉检查、触觉检查、嗅觉检查等。
2.痕迹发现技术
失效分析中进行宏观、微观分析时都离不开痕迹分析。
通过痕迹分析,不仅可对事故和失效发生、发展过程作出判断,并可为事故和失效分析结论提供可靠左证和依据。
所谓痕迹分析就是对表面形貌(花样)的变化、成分的变化(或材料的迁移)、颜色的变化、表层组织、性能的变化、残余应力的变化、以及表面污染状态的变化等变化特性进行诊断鉴别,找出变化的原因,为事故和机械失效分析提供线索和证据。
其主要研究内容是:
①研究机械表面上形成痕迹的物理、化学过程(即机制);
②研究痕迹对机械结构及其功能的影响;
③研究不同材料表面性能与痕迹的关系及其机械失效分析中的应用;
④痕迹的理化检验方法;
⑤痕迹的各种预防措施和表面强化或改进技术。
在一般情况下痕迹分析程序是:
①寻找、发现和显现痕迹;
②痕迹的提取、固定、显现、清洗、记录和保存;
③鉴定痕迹(这是痕迹分析的重点工作)一般原则是由表及里,由简而繁,先宏观后微观,先定性后定量。
遵循形貌-成分-组织结构-性能的分析顺序;
④痕迹的模拟再现试验;
⑤综合性分析;
⑥做分析结论并写出有建设性意见的报告。
3.断口的裂纹分析技术
断口和裂纹分析一般包括宏观分析与微观分析两个方面。
前者指用肉眼或40倍以下的放大镜、实体显微镜对断口或裂纹进行观察分析,可有效地确定对断裂起源和扩展方向;后者指用光学显微镜、透射电镜、扫描电镜等对断口或裂纹进行观察、鉴别与分析,可以有效地确定断裂类型与机理。
宏观分析和微观分析是不可分割的整体,二者不可互相取代,只能互相补充、互相促进。
过分依赖微观分析而不重视宏观分析,只根据几个微观视场的特征就作出判断,往往会导致全局性的判断失误;反之,忽视微观分析只进行宏观分析,则可能得出肤浅乃至错误的结论。
断口和裂纹分析技术一般包括:
分析对象的确定与显示技术、观察与照相记录技术、定性与定量分析技术及仪器与设备的使用技术等。
4.化学成分分析技术
在失效分析中,常常需要对失效零件的材料成分(包括定牌号、全成分或部分成分)、外来物(如擦痕或溅射附加物)、表面沉积物、腐蚀生成物及氧化物等定性或定量的分析,以便为最终的失效分析结论提供依据。
a.常用分析技术
该技术主要用于分析失效零件名义或宏观区域的材料成分,主要方法有:
1.湿法化学分析:
可准确分析含量较大的金属,阴离子的有无及其浓度;
2.半定量发射光谱和原子吸收光谱:
用于分析合金成分;
3.燃烧法:
用于测定金属中的碳硫氢氧氮的含量;
4.点滴法:
可以简单地定性分析金属中的合金元素、沉淀物、腐蚀物、土壤等;
5.红外、紫外光谱:
用于检测有机物质。
b.表面及微区分析技术
在失效分析中,相对于名义或宏观区域成分分析,失效零件的材料的表面成分及失效源区的微区分分析更为重要,尤其是对表面损伤或者由于诸如夹杂、成分偏析等造成的失效。
目前主要分析仪器有:
讹歇电子谱仪、离子探针、电子探针、x射线能谱仪、x射线波长谱仪等。
在扫描电镜上可装置饿歇电子谱仪、x射线能谱仪、x射线波长谱仪等,以满
足微区分分析需要。
C.铁谱分析技术
为了对齿轮等承受摩擦作用的机械零件进行动态监测,美国于1971年研制成功一种实验检测技术——铁谱技术。
该技术不仅在设备诊断等领域中具有重要的实用价值。
其分析对象是含有磨损粒子的润滑油,在铁谱仪中具有理论意义,而且在失效分析,故障诊断等领域中具有重要的实用价值。
其分析对象是含有磨损粒子的润滑油,在铁镨仪的剃度磁场中,磁性和几何尺寸各异的磨损粒子被分开来。
5.性能测试技术
对于一些重大的、复杂的断裂或变形失效,往往必须做力学方面的实验分析工作,优先考虑的试验有硬度试验、冲击试验、等。
若上诉试验不足以说明结论意见时,可进一步取样作其它性能试验,如拉伸实验,Kic,da/dn,耐磨性及腐蚀敏感性试验等。
6.无磨损检验技术
无损检验就是应用一些物理现象,在不改变I材料或零件形状和性能(包括机械性能和化学性质)条件下,迅速可靠的确定其表面或里边裂缝和其他的缺陷的大小、数量位置的方法。
在失效分析中应用无损检测技术的目的在于:
(1)检测失效件的同批服役件、库存件,防止同类事故的发生,若能查出第二件、第三件,则更有利于失效性质和失效原因的分析判断;
(2)某些容器、管道、壳体,甚至一些复杂形状的系统装置出现裂纹或泄露时,常需要借助于无损检验测量技术来确定其确切部位,以便取样分析或采取相应的补救措施;
(3)在脆性破坏中,利用无损检测技术来检测监视临界裂纹长度,防止发生脆断;
无损检验是一门系统的复杂的新兴科学,其检测方法以有十多种,有的正在不断完善,并向着自动化,提高性能及灵敏度,使用电视装置等方面发展(如X射线探伤、磁力探伤、超声波探伤等),有的还在发展中。
根据无损探伤的原理,其检验方法大致可分为五类;放射性探伤、电磁探伤、声试验探伤法、渗透探伤法和热试验法探伤。
7.宏观残余应力测试
金属零件经各种冷热加工(如切削、磨削加工、装配、冷拨、热处理等)之后,其部或多或少都存在残余应力。
残余应力的存在对材料的疲劳、耐磨蚀、尺寸稳定性都有影响,甚至在服役过程中一起的相变,据最近的调查分析,由于残余应力的影响或导致的机械零件失效达到50%以上。
因此在失效分析中,常需对机械零部件进行残余应力分析进行测定。
宏观残余应力测定方法很多,如电阻应变法、光弹复膜法、脆性涂料法、X射线法及声学法等。
2.3系统分析方法
随着科技的不断进步,设备的日益更新,其失效因数除物的因素外,还包括人的因素(如管理不善、判断失误、操作过失、责任心不强等)和软件方面的因素。
庞大复杂的设备可能的时效原因常常不止一个或几个,而是几十、甚至更多;若仅用物理失效方法难于解决复杂系统的失效分析任务。
而且目前一般的失效分析都是手工操作,分析耗时长。
因此,对复杂而急迫的设备的失效分析,必须应用系统工程的思想和方法。
失效分析的系统工程的方法有许多种,其中最常见的有:
PRO/E建模分析法、故障树分析方法、特征-因数分析法、失效模式与后果分析法、事件建模分析法是序树分析法等。
Pro/ENGINEE是1985年美国波士顿PTC公司开发出来的参数化建模软件,目前已经成为三维建模软件的领头羊。
目前已经发布了Pro/ENGINEERWILDFIRE3.O。
它包括了在工业设计和机械设计等方面的多项功能,还包括对大型装配体的管理、功能仿真、制造、产品数据管理等等。
而且Pro/ENGINEER还提供了目前所能达到的最全面、集成最紧密的产品开发环境,本文所进行轴的结构分析就是基于Pro/ENGINEER这一软件。
我们通过对自卸车拐轴轴的宏、微观分析和结构分析,了解该轴的应力分布情况,找出应力集中部位,分析该系列轴断裂的原因,在此基础上充分利用PRO/E技术进行进一步的应力分析,以验证宏、微观分析结果,再利用PRO/E技术进行轴的优化设计,达到改进轴的目的。
这样既能保证设备的正常使用,提高工厂的经济效益,有很高的实用价值,而且为轴失效问题的分析可提供有效的参考资料。
日本石川发明的特性因数图分析法是将已表现出来的失效或异常现象(即表现出来的结果称作特征)和引起这些现象的那些因数,用鱼骨结构联系起来,通过分析找出这些现象的直接原因。
2.4本章小结
本章主要介绍了失效分析的基本概念、失效的主要来源及模式、常用的失效分析方法及技术的失效的系统分析方法。
失效分析技术中主要介绍了感官检查诊断技术、痕迹发现技术、断口和裂纹分析技术、化学成分分析技术、性能测试技术、无损检验技术、宏观残余应力。
失效分析的系统分析方法则主要介绍了PRO/E和FMEA两类。
所谓“特征”,是指失效与异常现象,“要因”是指引起失效与故障的因素与原因。
“特征”用主杆箭头表示,“要因”用分箭头表示,就构成了特征要因分析图或失效鱼骨图。
在国外,尤其是日本,特征要因图广泛用于产品质量管理与失效分析中。
近几年来,在我国也得到了广泛的应用。
本课题研究中采用失效分析鱼骨图即特征要因图的方法。
对输出轴的断裂原因的原因主要从以下几个方面考虑:
原材料、设计、冷热加工工艺、装配及使用等。
具体的失效分析的鱼骨图如图1-4所示。
根据测试分析结果,消去不存在因素,留下来的因素即为自卸车拐轴断裂失效的原因。
图1-3失效分析基本程序图
失效现场查
收集背景资料
宏观分析
宏观断口分析
扫描电镜分析
金相组织分析
力学性能测试
设计工艺
第3章T108吨自卸车拐轴的断裂原因分析
此课题研究的拐轴是某厂108吨自卸车上一部件,在此称为主轴。
我们从设计图纸上了解到主轴的结构如图3-1所示,按使用情况我们在主轴(拐轴)尾部接上管子(结构如图3-2所示),然后通过焊接用一个外径为450,内径为374,总长为1946的圆管约束,约束位置在离圆管端部418处,主轴端部离中心线472(装配情况如图3-3所示)。
图3.1主轴的结构
图3.2管子结构
图3.3装配图
3.1实验结果与分析
下面将在结构、宏观、金相三个方面进行分析。
3.1.1结构分析
由图3.1可以看出该主轴的结构在过渡处有一个大约半径为6cm的圆角在该处,经分析很容易产生应力集中,而应力集中是一切机械零部件的死敌也可以说是机械失效的重要原因之一。
由于应力集中的原因对轴的强度、硬度、塑性、韧性、抗拉强度等都有很高的要求。
因此对制造零部件时,其工艺也要规范、精益求精,这才能保证轴的质量和机械的质量。
3.1.2断裂宏观检查
该轴靠近断口一端严重磨损,表面粗糙,呈焦油色,该区域内的断口表面也呈焦油色。
整个断口表面较粗糙,部分呈粗糙的贝纹花样,
贝纹间隔为3~5mm,属疲劳断裂区;部分为静段区,呈暗灰色,其中两处有石状断口特征。
疲劳区约占断口总面积62%。
宏观断口如图3.4所示。
裂纹源位于轴颈圆角表面严重磨损的一端,距曲柄平面5mm处。
裂纹由轴颈表面开始,一部分沿与轴线成45°角方向向轴颈内扩散,整个裂纹穿过轴颈上的油孔,最后在轴颈上形成斜断口。
图3.4拐轴的断裂实物图
轴圆角处未淬火区为从圆角根部向轴颈内约10mm范围,其硬度为24~30HRC;轴颈淬火区为从圆角根部向轴颈内约10mm范围,其硬度为24~30HRC;轴颈淬火区表面硬度为40~46HRC,心部为24~30HRC。
显然,该拐轴淬火后的表面硬度远未达到技术要求,其非淬火带尺寸也大于工艺中所要求的(5.7)mm。
裂纹源处开始于轴圆角处非淬火带上,裂纹源处断口平坦,光滑,呈灰色;在其一侧有台阶特征,呈放射状,另一侧有贝纹特征的弧线。
裂纹源处扫描断口形貌如图3.2所示,呈沿晶断裂特征,晶粒粗大。
表明裂纹在被削弱的晶界快速扩展的情况。
3.1.3金相检验
图3.1中箭头所指处为石状断口区,该区距轴颈表面约6mm,在此切取金相试样,在未经侵蚀的径向截面上,可观察到尺寸非常粗大晶界氧化物和晶界和晶界断裂,如图3.3所示。
在图3.3(a)中夹杂物上选不同形态的二点做能谱分析,结果列于表3.1,表明该夹杂物为氧化物。
氧化物夹杂伸长方向和品界开裂方向与曲轴流动方向一致,可以认为这些缺陷是存在于锻件中的。
图3.5裂纹源处断口扫描图
表3.1晶界氧化物成分(原子百分含量)
元素
O
Cr
Mn
Fe
Si
S
成分
Ⅰ
76.00