数控线切割编程与加工操作.docx
《数控线切割编程与加工操作.docx》由会员分享,可在线阅读,更多相关《数控线切割编程与加工操作.docx(34页珍藏版)》请在冰豆网上搜索。
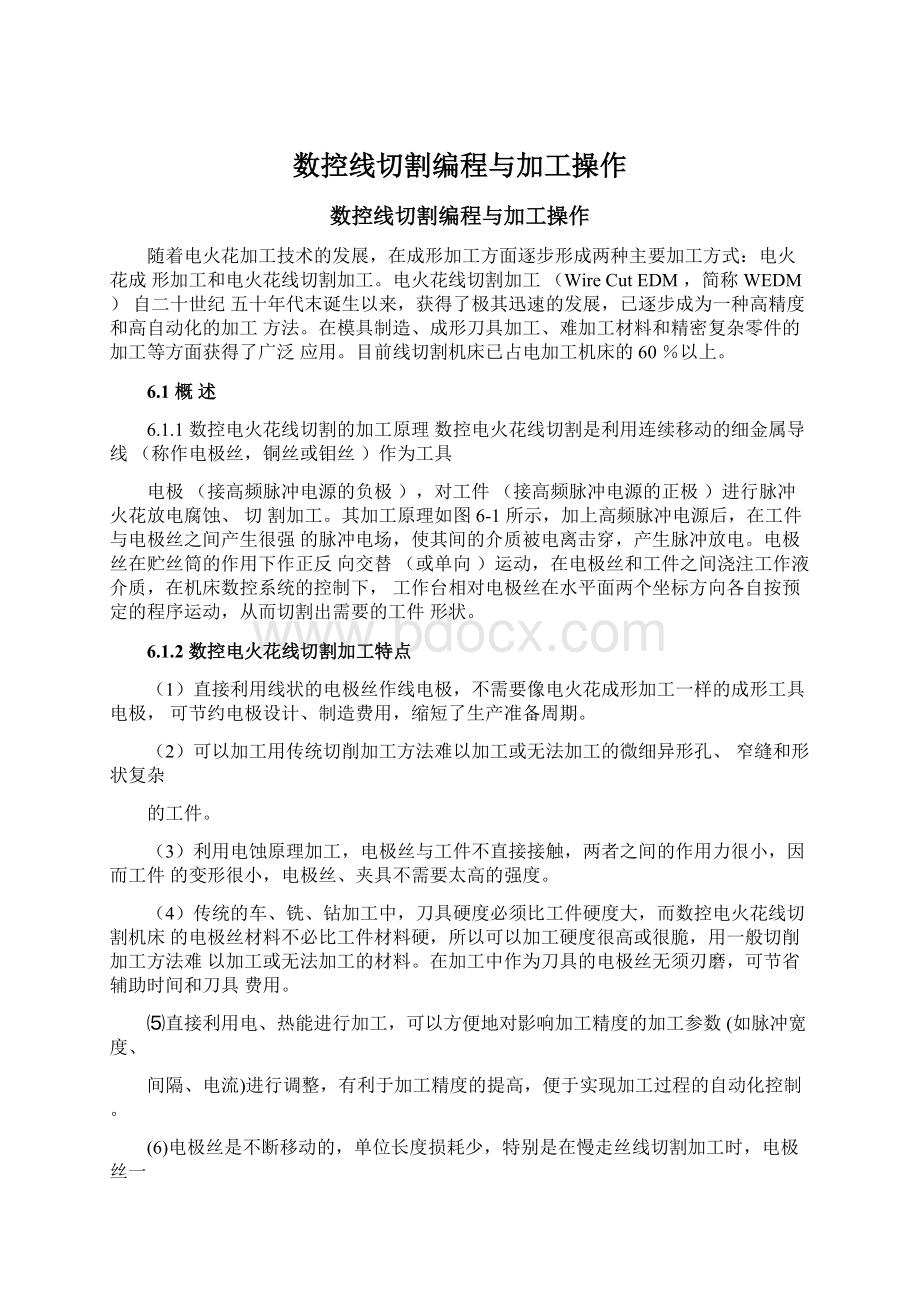
数控线切割编程与加工操作
数控线切割编程与加工操作
随着电火花加工技术的发展,在成形加工方面逐步形成两种主要加工方式:
电火花成形加工和电火花线切割加工。
电火花线切割加工(WireCutEDM,简称WEDM)自二十世纪五十年代末诞生以来,获得了极其迅速的发展,已逐步成为一种高精度和高自动化的加工方法。
在模具制造、成形刀具加工、难加工材料和精密复杂零件的加工等方面获得了广泛应用。
目前线切割机床已占电加工机床的60%以上。
6.1概述
6.1.1数控电火花线切割的加工原理数控电火花线切割是利用连续移动的细金属导线(称作电极丝,铜丝或钼丝)作为工具
电极(接高频脉冲电源的负极),对工件(接高频脉冲电源的正极)进行脉冲火花放电腐蚀、切割加工。
其加工原理如图6-1所示,加上高频脉冲电源后,在工件与电极丝之间产生很强的脉冲电场,使其间的介质被电离击穿,产生脉冲放电。
电极丝在贮丝筒的作用下作正反向交替(或单向)运动,在电极丝和工件之间浇注工作液介质,在机床数控系统的控制下,工作台相对电极丝在水平面两个坐标方向各自按预定的程序运动,从而切割出需要的工件形状。
6.1.2数控电火花线切割加工特点
(1)直接利用线状的电极丝作线电极,不需要像电火花成形加工一样的成形工具电极,可节约电极设计、制造费用,缩短了生产准备周期。
(2)可以加工用传统切削加工方法难以加工或无法加工的微细异形孔、窄缝和形状复杂
的工件。
(3)利用电蚀原理加工,电极丝与工件不直接接触,两者之间的作用力很小,因而工件的变形很小,电极丝、夹具不需要太高的强度。
(4)传统的车、铣、钻加工中,刀具硬度必须比工件硬度大,而数控电火花线切割机床的电极丝材料不必比工件材料硬,所以可以加工硬度很高或很脆,用一般切削加工方法难以加工或无法加工的材料。
在加工中作为刀具的电极丝无须刃磨,可节省辅助时间和刀具费用。
⑸直接利用电、热能进行加工,可以方便地对影响加工精度的加工参数(如脉冲宽度、
间隔、电流)进行调整,有利于加工精度的提高,便于实现加工过程的自动化控制。
(6)电极丝是不断移动的,单位长度损耗少,特别是在慢走丝线切割加工时,电极丝一
次性使用,故加工精度高(可达土2口m)。
(7)采用线切割加工冲模时,可实现凸、凹模一次加工成形。
(a)工件及其运动方向(b)电火花线切割加工装置原理图
图6-1电火花线切割原理
1—绝缘底板;2—工件;3—脉冲电源;4—电极丝(钼丝);5—导向轮;6—支架;7—贮丝筒
6.1.3数控电火花线切割的应用
线切割加工的生产应用,为新产品的试制、精密零件及模具的制造开辟了一条新的工艺途径,具体应用有以下三个方面:
(1)模具制造适合于加工各种形状的冲裁模,一次编程后通过调整不同的间隙补偿量,就可以切割出凸模、凹模、凸模固定板、凹模固定板、卸料板等,模具的配合间隙、加工精度通常都能达到要求。
此外电火花线切割还可以加工粉末冶金模、电机转子模、弯曲模、塑压模等各种类型的模具。
(2)电火花成形加工用的电极一般穿孔加工的电极以及带锥度型腔加工的电极,若采
用银钨、铜钨合金之类的材料,用线切割加工特别经济,同时也可加工微细、形状复杂的
电极。
(3)新产品试制及难加工零件在试制新产品时,用线切割在坯料上直接切割出零件,
由于不需另行制造模具,可大大缩短制造周期,降低成本。
加工薄件时可多片叠加在一起加工。
在零件制造方面,可用于加工品种多、数量少的零件,还可加工特殊难加工材料的零件,如凸轮、样板、成形刀具、异形槽、窄缝等。
6.2数控电火花线切割工艺与工装基础
电火花线切割加工,一般作为工件加工中的最后工序,要达到加工零件的加工要求,应合理控制线切割加工的各种工艺因素,同时选择合适工装。
6.2.1线切割加工的主要工艺指标
1•切割速度Vwi在保持一定的表面粗糙度的前提下,单位时间内电极丝中心在工件
上切过的面积总和即为切割速度,单位为mm2•min-1。
2•表面粗糙度我国和欧洲常用轮廓算术平均偏差Ra(口m)来表示,日本常用Rmax
来表示。
3.电极丝损耗量对高速走丝机床,用电极丝在切割10000mm2面积后电极丝直径的减小量来表示,一般减小量不应大于0.01mm。
4•加工精度加工精度指所加工工件的尺寸精度、形状精度和位置精度的总称。
6.2.2影响线切割工艺指标的若干因素
影响线切割工艺指标的因素很多,也很复杂,主要包括以下几个方面:
1.电参数对工艺指标的影响
主要包括以下几方面:
(1)脉冲宽度twtw增大时,单个脉冲能量增多,切割速度提高,表面粗糙度数值变大,放电间隙增大,加工精度有所下降。
粗加工时取较大的脉宽,精加工时取较小的脉宽,切
割厚大工件时取较大的脉宽。
(2)脉冲间隔tt增大,单个脉冲能量降低,切割速度降低,表面粗糙度数值有所增大,粗加工及切割厚大工件时脉冲间隔取宽些,而精加工时取窄些。
⑶开路电压U。
开路电压增大时,放电间隙增大,排屑容易,提高了切割速度和加工稳定性,但易造成电极丝振动,工件表面粗糙度变差,加工精度有所降低。
通常精加工时取的开路电压比粗加工低,切割大厚度工件时取较高的开路电压。
一般U0=60〜150V。
(4)放电峰值电流ip放电峰值电流是决定单脉冲能量的主要因素之一。
ip增大,单个脉冲能量增多,切割速度迅速提高,表面粗糙度数值增大,电极丝损耗比加大甚至容易断丝,加工精度有所下降。
粗加工及切割厚件时应取较大的放电峰值电流,精加工时取较小的放电峰值电流。
⑸放电波形电火花线切割加工的脉冲电源主要有晶体管矩形波脉冲电源和高频分
组脉冲电源。
在相同的工艺条件下高频分组脉冲能获得较好的加工效果,其脉冲波形如图6-2所示,它是矩形波改造后得到的一种波形,即把较高频率的脉冲分组输出。
矩形波脉冲电源在提高切割速度和降低表面粗糙度之间存在矛盾,二者不能兼顾,只适用于一般精度和表面粗糙度的加工。
高频分组脉冲波形是解决这个矛盾的比较有效的电源形式,得到了越来越广泛的应用。
(6)极性线切割加工因脉冲较窄,所以都用正极性加工,即工件接电源的正极,否则切割速度会变低而电极丝损耗增大。
⑺变频、进给速度即预置进给速度的调节,对切割速度、加工速度和表面质量的影
响很大。
因此,调节预置进给速度应紧密跟踪工件蚀除速度,以保持加工间隙恒定在最佳值上。
这样可使有效放电状态的比例大,而开路和短路的比例少,使切割速度达到给定加工条件下的最大值,相应的加工精度和表面质量也好。
如果预置进给速度调得太快,超过工件可能的蚀除速度,会出现频繁的短路现象,切割速度反而低,表面粗糙度也差,上下端面切缝呈焦黄色,甚至可能断丝;反之,进给速度调得太慢,大大落后于工件的蚀除速度,极间将偏于开路,有时会时而开路时而短路,上下端面切缝发焦黄色。
这两种情况都大大影响工艺指标。
因此,应按电压表、电流表调节进给旋钮,使表针稳定不动,此时进给速度均匀、平稳,是线切割加工速度和表面粗糙度均好的最佳状态。
2.非电参数对工艺指标的影响
(1)走丝速度对工艺指标的影响
对于高速走丝线切割机床,在一定的范围内,随着走丝速度的提高,有利于电极丝把工作液带入较大厚度的工件放电间隙中,有利于放电通道的消电离和电蚀产物的排除,保持放电加工的稳定,从而提高切割速度;但走丝速度过高,将加大机械振动,降低加工精度和切割速度,表面粗糙度也将恶化,并且易断丝。
低速走丝时由于电极丝张力均匀,振动较小,电极丝直径较小,因而加工稳定性、表面粗糙度及加工精度等均很好。
表6-1是在瑞士阿奇公司低速走丝电火花线切割机床上切
割加工的工艺效果,可供参考。
表6-1低速走丝线切割加工的工艺效果
工件材料
电极丝直径
d(mm)
切割厚度
H(mm)
切缝厚度
s(mm)
表面粗糙度
Rz(卩m)
切割速度
21
vwi(mmmin)
电极丝
材料
碳钢铬钢
0.1
2~20
0.13
0.2~0.3
7
黄铜丝
0.15
2~50
0.19
0.35~0.5
12
0.2
2~75
0.259
0.35~0.71
25
0.25
10~125
0.34
0.35~0.71
25
0.3
75〜150
0.378
0.35~0.5
25
铜
0.25
2~40
0.32
0.35~0.7
19.4
硬质合金
0.1
2~20
0.19
0.15~0.24
3.5
0.15
2~30
0.229
0.24~0.25
7.1
0.25
2~50
0.361
0.2~0.5
12.2
石墨
0.25
2~40
0.351
0.35~0.6
12
铝
0.25
2~40
0.34
0.5~0.83
60
碳钢铬钢
0.08
2~10
0.105
0.35~0.55
5
钼丝
0.1
2~10
0.125
0.47~0.59
7
硬质合金
0.08
2~12.7
0.105
0.078~0.2
3
4
0.1
2~12.7
0.125
0.118~0.2
3
6
(2)工件厚度及材料对工艺指标的影响
工件薄时,工作液容易进入并充满放电间隙,有利于排屑和消电离,加工稳定性好;但工件太薄时,电极丝容易产生抖动,对加工精度和表面粗糙度不利,且脉冲利用率低,切削速度因而下降。
工件厚时,工作液难于进入和充满放电间隙,加工稳定性差,但电极丝不易抖动,因而加工精度和表面粗糙度较好,但过厚时排屑困难,导致切割速度下降。
(3)电极丝材料及直径对加工指标的影响
高速走丝用的电极丝材料应具有良好的导电性、较大的抗拉强度和良好的耐电腐蚀性能,且电极丝的质量应该均匀,不能有弯折和打结现象。
钼丝韧性好,放电后不易变脆,不易断丝,因而应用广泛。
黄铜丝加工稳定,切割速度高,但电极丝损耗大。
低速走丝线切割机床上常采用0.2mm的黄铜丝,也可采用钨丝、钼丝。
电极丝直径大时,能承受较大的电流,从而使切割速度提高,同时切缝宽,放电产生
的腐蚀物排除条件得到改善而使加工稳定,但加工精度和表面粗糙度下降。
当直径过大时,
切缝过宽,需要蚀除的材料增多,导致切割速度下降,而且难于加工出内尖角的工件。
高速走丝时电极丝的直径可在0.1〜0.25mm之间选用,常用的电极丝为0.12〜0.18mm,低
速走丝直径可在0.076〜0.3mm之间,最常采用的为0.2mm。
电极丝直径及与之相适应的切割厚度见表6-2所示。
表6-2电极丝直径与合适的切割厚度
电机丝材料
电机丝直径/mm
合适的切割厚度/mm
钨丝
$0.05
0〜5
$0.07
0〜8
$0.10
0〜30
铜丝
$0.10
0〜15
$0.15
0〜30
$0.20
0〜80
$0.25
0〜100
(4)工作液对加工指标的影响
在电火花线切割加工中,工作液为脉冲放电的介质,对加工工艺指标的影响很大。
同时,工作液通过循环过滤装置连续地向加工区供给,对电极丝和工件进行冷却,并及时从加工区排除电蚀产物,以保持脉冲放电过程能稳定而顺利地进行。
低速走丝线切割机床大都采用去离子水作工作液,只有在特殊精加工时才采用绝缘性能较高的煤油。
高速走丝线切割机床大都使用专用乳化液。
乳化液的品种很多,各有特点,有的适合精加工,有的适合于大厚度切割,有的适合于高速切割等。
因此,必须按照线切割加工的需要正确选用。
(5)工件材料内部残余应力的影响
对热处理后的坯料进行线切割时,由于大面积去除金属和切断加工,材料内部残余应力的相对平衡状态受到破坏,从而产生很大的变形,零件的加工精度下降,有的零件甚至在切割中出现裂纹、断裂。
减少变形和裂纹的措施如下:
1改善热处理工艺,减少内部残余应力。
图6-3减少切割体积
2减少切割体积,在淬火前先用切削加工方法把中心部分材料切除或预钻孔,使热处
理均匀发生,如图6-3所示。
3精度要求高的,采用二次切割法。
第一次加工单边留下余量0.1〜0.5mm,余量大
小根据淬硬程度、工件厚度、壁厚等确定。
第二次加工时将第一次加工的变形切除,如图
6-4所示。
4为了避免材料组织及内应力对加工精度的影响,必须合理地选择切割的走向和进刀
点。
通常切割路径应使夹持部分位于程序的最后一条加工语句处,如图6-5所示,这样可
以减小工件变形引起的误差。
进入点的选择要尽量避免留下接刀痕,如图6-6所示。
当接
刀痕不可避免时,应尽量把进刀点放在尺寸精度要求不高或容易钳修处,如图6-7所示。
图6-7进刀点易于钳修
5若精度要求高,应先在坯料内加工出穿丝孔,以免当从坯料外切入时引起坯料切开
处变形,如图6-8所示。
6工件上的剩磁会使内应力不均匀,且加工时对排屑不利,因此平磨过的工件应先充分去磁。
6.2.3电火花线切割典型夹具、附件及工件装夹
工件装夹的形式对加工精度有直接影响。
电火花线切割加工机床的夹具一般是在通用夹具上采用压板螺钉固定工件。
为了适应各种形状工件加工的需要,还可使用磁性夹具、旋转夹具或专用附件。
图6-9磁性夹具的基本原理
1常用工夹具、附件
(1)
压板夹具由于线切割机床主要用
于切割冲模的型腔,因此机床出厂时通常只提供一对夹持板形工件的压板夹具(压板、紧固螺钉等)。
(2)磁性夹具采用磁性工作台或磁性
表座夹持工件,不需要压板和螺钉,操作快
速方便,定位后不会因压紧而变动,见图6-9。
要注意保护上述两类夹具的基准面,避免工件将其划伤或拉毛。
压板夹具应定期修磨基准面,保持两件夹具的等高性。
夹具的绝缘性也应经常检查和测试,因有时绝缘体受损造成绝缘电阻减小,影响正常的切割。
(3)分度夹具分度夹具(见图6-10)是根据加工电机转子、定子等多型孔的旋转形工件设计的,可保证高的分度精度。
近年来,因微机控制器及自动编程机对加工图形具有对称、旋转等功能,所以分度夹具用得较少。
(4)3R夹具瑞典System3R公司生产的3R夹具具有以下基本特点:
•安装简单:
仅需内六角螺栓与机床台面固定;
-高精度:
重复定位精度土0.002mm;
-预调工件:
可在机床外调节好工件,再装到机床上直接进入加工;•五面加工:
可在机床上实现精确的五面加工;
-适应范围广:
可装夹方形,圆形等大小不同的工件;
-易于装夹:
使用十分方便。
3R基准导轨是3R线切割新概念中的基本元件,它能给线切割机床的工作台提供x、y、
z方向的固定基准。
并且可以有不同的长度和不同位置的安装孔,以应用于不同的线切割机床,如图6-11所示。
(5)数控回转工作台(简称转台)在数控线切割机床上,用来加工圆形或阿基米德螺旋线型凸轮,可大大简化编程工作,结构如图6-12所示。
步进电动机经过二级蜗轮蜗杆传动
标准心轴,其传动比为1:
1800,步进电动机每转一步(1.5),心轴旋转3〃(0.001),相当于
工件半径为70mm的圆周上移动1卩m。
如果旋转与坐标运动结合起来,可加工正弦、余弦、双曲线、螺旋线等特殊曲线轮廓的工件。
2.工件的正确装夹方法
(1)正确装夹的一般要求
1工件的基准面应清洁无毛刺,经热处理的工件,在穿丝孔内及扩孔的台阶处,要清除热处理残留物及氧化皮。
2夹具应具有必要的精度,将其稳固地固定在工作台上,拧紧螺丝时用力要均匀。
3
工件装夹的位置应有利于工件找正,并应与机床行程相适应,工作台移动时工件不得与丝架相碰。
4对工件的夹紧力要均匀,不得使工件变形或翘曲。
5大批零件加工时,最好采用专用夹具,以提高生产效率。
6细小、精密、薄壁的工件应固定在不易变形的辅助夹具上。
(2)工件在工作台上的装夹位置对编程的影响
1适当的定位可以简化编程工作工件在工作台上的位置不同,会影响工件轮廓线的
方位,也就影响各点坐标的计算结果,从而影响各段程序。
在图6-13a中,若使工件的a
角为0°、90°以外的任意角,则矩形轮廓各线段都成了切割程序中的斜线,这样,计算各点的坐标、填写程序单及穿制纸带等都比较麻烦,还可能发生错误。
如条件允许,使工
2
图6-11回转工作台
1-定位心轴;2-基座;3-步进电动机;4-蜗杆蜗轮
件的a角成0°和90°,则各条程序皆为直线程序,这就简化了编程,从而减少差错。
同理,图6-13b中的图形,当a角为0°、90°或45°时,也会简化编程,提高质量,而为其他角度时,会使编程复杂些。
2合理的定位可充分发挥机床的效能有时则与上述情况相反,如图6-14所示,工件
的最大长度尺寸为139mm,最大宽度为20mm,工作台行程为100mmx120mm。
很明显,若用图6-14a的定位方法,在一次装夹中就不能完成全部轮廓的加工,如选图6-14b的定
位方法,可使全部轮廓落入工作台行程范围内,虽然编程比较复杂,但可在一次装夹中完成全部加工。
3
正确定位可提高加工的稳定性在加工时,执行各条程序切割的稳定性并不相同,
如较长直线的切割过程,就容易出现加工电流不稳定、进给不均匀等,严重时还会引起断丝。
因此编程时应使零件的定位尽量避开较长的直线程序。
6.3线切割编程
数控线切割编程与数控车、铳床、加工中心的编程过程一样,也是根据零件图样提供的数据,经过分析和计算,编写出线切割机床数控装置能接受的程序。
编程方法分手工编程和自动编程两种。
一般形状简单的零件数控线切割采用手工编程,目前我国数控线切割机床常用的手工编程格式有3B、4B、ISO格式。
6.3.13B格式程序编制
我国早期数控线切割机床使用的是5指令3B格式编程,一般用于高速走丝,不能实
现电极丝半径和放电间隙的自动补偿。
1程序格式
指令格式为:
BXBYBJGZ
其中:
B叫分隔符号,用它来区分、隔离X、Y和J数值,B后的数值如为0,则此0可不写,但分隔符号B不能省略。
G为计数方向,有Gx和Gy两种。
Z为加工码,有12种,即Li、L2、L3、L4、NRi、NR2、NR3、NR4、SR、SR2、SR3、SR4。
加工圆弧时,程序中的X、Y必须是圆弧起点对其圆心的坐标值。
加工斜线时,程序中的X、Y必须是该斜线段终点对其起点的坐标值,斜线段程序中的X、Y值允许把它们
同时缩小相同的倍数,只要其比值保持不变即可,因为X、Y值只用来确定斜线的斜率,
但J值不能缩小。
对于与坐标轴重合的线段,在其程序中的X或Y值,均可不必写出或全
写为0,但分隔符号B必须保留。
X,Y坐标值为绝对值,单位为卩m,1卩m以下的按四舍五入计。
2.计数方向G和计数长度J
(1)计数方向G及其选择按x轴方向、y轴方向计数,分为Gx、Gy两种。
它确定在加工直线或圆弧时按哪个坐标轴方向取计数长度值。
在加工直线时规定终点接近x轴时应取Gx,终点接近y轴时应取Gy。
加工圆弧时终
点接近x轴时应取Gy,接近y轴时应取Gx。
这样设定的原因在于,加工直线时终点接近x轴,即进给的X分量多,x轴走几步,y轴才走一步。
用x轴计数不致于漏步,可保持较高的精度。
而圆弧的终点接近x轴时线段趋于垂直方向,即y轴走几步,x轴才走一步,
因此用Y计数能保持较高的精度,如图6-15所示。
⑵计数长度J的确定当计数方向确定后,计数长度J应取计数方向从起点到终点移
动的总距离,即圆弧或直线段在计数方向坐标轴上投影长度的总和。
对于斜线,如图6-16a取J=xe,如图6-16b取J=ye即可。
图6-15计数方向的决定图6-16直线J的确定
对于圆弧,它可能跨越几个象限,如图6-17的圆弧都是从A加工到B,图a为Gx,
J=Jxl+Jx2;图b为GY,J=Jyl+Jy2+Jy3。
(3)加工指令Z加工指令是用来确定轨迹的形状、起点、终点所在坐标象限和加工方向的,它包括直线插补指令(L)和圆弧插补指令(R)两类。
圆弧插补指令(R)根据加工方向又可分为顺圆插补(SR|、SR2、SR3、SR4)和逆圆插补(NRi、
NR2、NR3、NR4),字母后面的数字表示该圆弧的起点所在象限,如SRl表示顺圆弧插补,
其起点在第一象限。
如图6-18a、b所示。
注意:
坐标系的原点是圆弧的圆心。
直线插补指令(Ll、L2、L3、L4),表示加工的直线终点分别在坐标系的第一、二、三、四象限;如果加工的直线与坐标轴重合,根据进给方向来确定指令(Li、L2、L3、L4)。
如图
6-18c、d所示。
注意:
坐标系的原点是直线的起点。
例如:
起点为(2,3),终点为(7,10)的直线的3B指令是:
B5000B7000B7000GyL1;半径为9.22,圆心坐标为(0,0),起点坐标为(-2,9),终点坐标为(9,-2)的圆弧3B指令是:
B2000B9000B25440GyNR2。
图6-18直线和圆弧加工指令
【例6-1】试用3B格式编写如图6-19所示轨迹的程序,切割路线为:
AtCtD
tE,不考虑切入路线的程序。
编制程序如下:
BBB40000GxLi
(AtB)
B1B9B90000GyLi
(BC)
B30000B40000B60000GxNRi
(CD)
B1B9B90000GyL4
(DE)
D
(停机)
3.标注公差尺寸的编程计算
根据大量的统计表明,线切割加工后的实际尺寸大部分是在公差带的中值附近。
因此对标注有公差的尺寸,应采用中差尺寸编程。
其计算公式为:
中差尺寸=基本尺寸+(上偏差+下偏差)/2
例如:
半径R2O00.o2的中差尺寸为:
20+(0-0.02)/2=19.99。
实际加工和编程时,要考虑钼丝半径r丝和单边放电间隙
3电的影响。
对于切割凹体,应将编程轨迹减小(r丝+3电),切割
凸体,则应偏移增大(r丝+3电)。
切割模具时,还应考虑凸凹模之间的配合间隙3
4.间隙补偿量的确定
在数控线切割加工时,控制装置所控制的是电极丝中心轨迹,如图6-20所示(图中
双点画线为电极丝中心轨迹),加工凸模时电极丝中心轨迹应在所加工图形的外面;加工凹模时,电极丝中心轨迹应在要求加工图形的里面。
工件图形与电极丝中心轨迹间的距离,在圆弧的半径方向和线段的垂直方向都
等于间隙补偿量f。
图6-20电极丝中心轨迹
(1)间隙补偿量的符号可根据在电极
丝中心轨迹图形中圆弧半径及直线段法线长度的变化情况来确定。
对于圆弧,当考虑电极丝中心轨迹后,其圆弧半径比原图形半径增大时取+f,减小时取一f;对于直线段,当考
虑电极丝中心轨迹后,使该直线段的法线长度P增加时取+f,减小时则取一f,如图6-21
所示。
(2)间隙补偿量的算法加工冲模的凸、凹模时,应考虑电极丝半径,丝、电极丝和工件
之间的单边放电间隙3电及凸模和凹模间的单边配合间隙3配。
当加工冲孔模具时(即冲后要
求保证工件孔的尺寸),凸模尺寸由孔的尺寸确定。
因3配在凹模上扣除,故凸模的间隙补偿量f凸=「丝+3电,凹模的间隙补偿量f凹=r丝+3电一3配。
当加工落料模时(即冲后要求保
证冲下的工件尺寸),凹模尺寸由工件尺寸确定。
因3配在凸模上扣除,固凸模