浙江工业大学生物工程设备电子书稿1.docx
《浙江工业大学生物工程设备电子书稿1.docx》由会员分享,可在线阅读,更多相关《浙江工业大学生物工程设备电子书稿1.docx(34页珍藏版)》请在冰豆网上搜索。
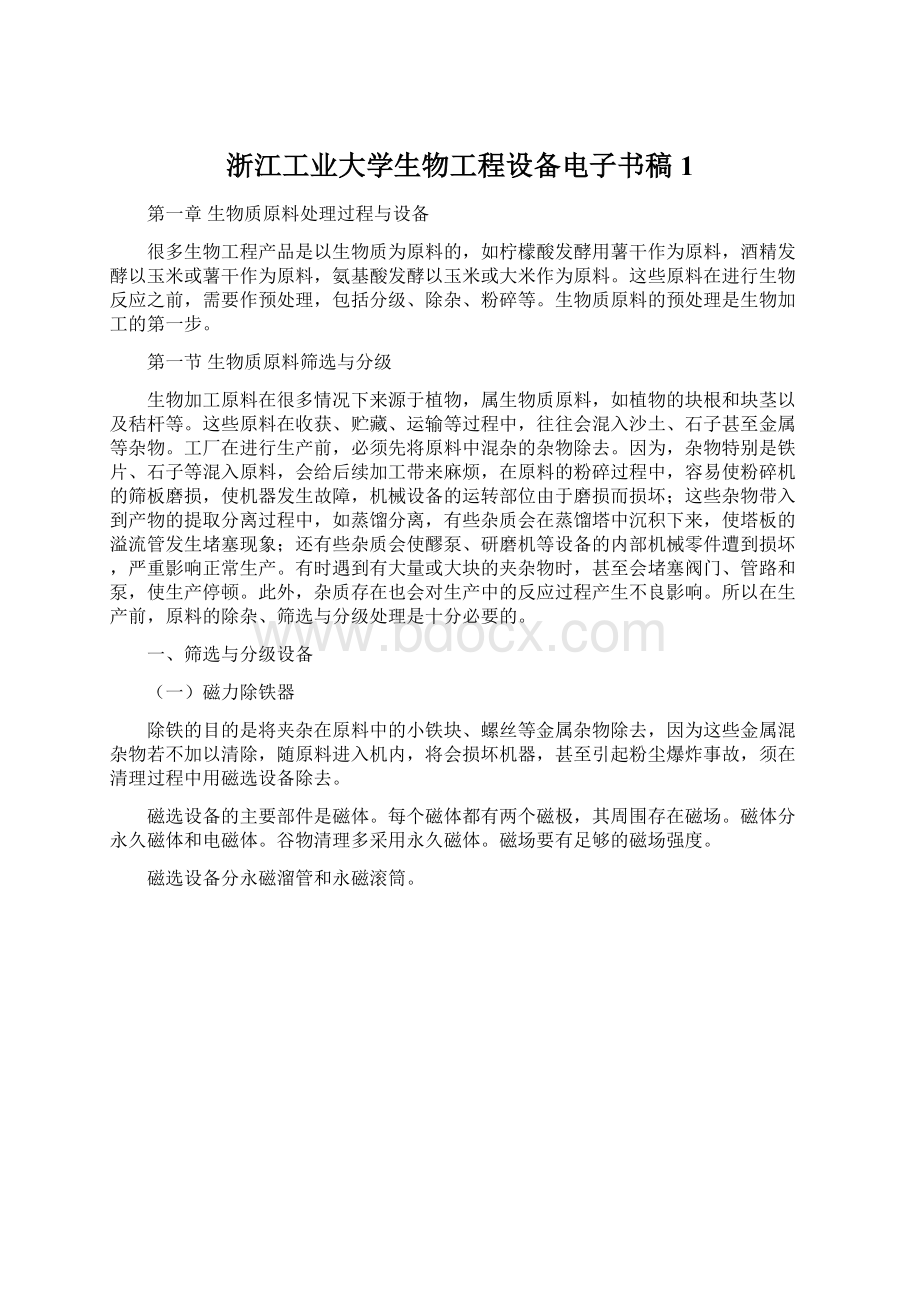
浙江工业大学生物工程设备电子书稿1
第一章生物质原料处理过程与设备
很多生物工程产品是以生物质为原料的,如柠檬酸发酵用薯干作为原料,酒精发酵以玉米或薯干作为原料,氨基酸发酵以玉米或大米作为原料。
这些原料在进行生物反应之前,需要作预处理,包括分级、除杂、粉碎等。
生物质原料的预处理是生物加工的第一步。
第一节生物质原料筛选与分级
生物加工原料在很多情况下来源于植物,属生物质原料,如植物的块根和块茎以及秸杆等。
这些原料在收获、贮藏、运输等过程中,往往会混入沙土、石子甚至金属等杂物。
工厂在进行生产前,必须先将原料中混杂的杂物除去。
因为,杂物特别是铁片、石子等混入原料,会给后续加工带来麻烦,在原料的粉碎过程中,容易使粉碎机的筛板磨损,使机器发生故障,机械设备的运转部位由于磨损而损坏;这些杂物带入到产物的提取分离过程中,如蒸馏分离,有些杂质会在蒸馏塔中沉积下来,使塔板的溢流管发生堵塞现象;还有些杂质会使醪泵、研磨机等设备的内部机械零件遭到损坏,严重影响正常生产。
有时遇到有大量或大块的夹杂物时,甚至会堵塞阀门、管路和泵,使生产停顿。
此外,杂质存在也会对生产中的反应过程产生不良影响。
所以在生产前,原料的除杂、筛选与分级处理是十分必要的。
一、筛选与分级设备
(一)磁力除铁器
除铁的目的是将夹杂在原料中的小铁块、螺丝等金属杂物除去,因为这些金属混杂物若不加以清除,随原料进入机内,将会损坏机器,甚至引起粉尘爆炸事故,须在清理过程中用磁选设备除去。
磁选设备的主要部件是磁体。
每个磁体都有两个磁极,其周围存在磁场。
磁体分永久磁体和电磁体。
谷物清理多采用永久磁体。
磁场要有足够的磁场强度。
磁选设备分永磁溜管和永磁滚筒。
1.永磁溜管
永磁溜管(图1-1)的永久磁铁装在溜管上边的盖板上。
一般在溜管上设置2~3个盖板,每个盖板上装有两组前后错开的磁铁。
工作时,原料从溜管上端流下,磁性物体被磁铁吸住。
工作一段时间后进行清理,可依次交替地取下盖板,除去磁性杂质。
溜管可连续地进行磁选。
永磁溜管结构简单,不占地方。
为了提高分离效率,应使流过溜管的物料层薄而均匀。
2.永磁滚筒
永磁滚筒(图1-2)主要由进料装置、滚筒、磁芯、机壳和传动装置等部分组成。
磁芯由锶钙铁氧体永久磁铁和铁隔板按一定顺序排列成170°的圆弧形,安装在固定的轴上,形成多极头开放磁路。
磁芯圆弧表面与滚筒内表面间隙小而均匀(一般小于2mm),滚筒由非磁性材料制成,外表面敷有无毒而耐磨的聚氨酯涂料作保护层,以延长使用寿命。
滚筒通过蜗轮蜗杆机构由电动机带动旋转。
磁芯固定不动。
滚筒重量轻,转动惯量小。
永磁滚筒能自动地排除磁性杂质,除杂效率高(98%以上),特别适合于除去粒状物料中的磁性杂质。
为了有效地保障安全生产和产品质量,在原料加工的全过程中,凡是高速运转的机器的全部应装有磁选设备。
为了保证磁选效果,物料通过磁极面的速度不宜过快,永磁溜管的物料速度一般为0.15~0.25m/s,永磁滚筒的圆周速度一般为0.6m/s左右。
(二)精选机
颗粒状的生物质原料(如大麦、小麦)等必须进行精选和分级,其主要原理是按颗粒长度进行分级,以除去不必要的杂粒。
常用的精选机有滚筒精选机和碟片精选机两种,其都是利用带有袋孔(窝眼)的工作面来分离杂粒,袋孔中嵌入长度不同的颗粒,带升高度不同而分离。
结构示意图如图1-3。
1.碟片式精选机
在金属碟片的平面上制成许多袋形的凹孔,孔的大小和形式视除杂条件而定。
碟片在粮堆中运动时,短小的颗粒嵌入袋孔被带到较高的位置才会落下,因此只要把收集短粒斜槽放在适当位置上,就能将短粒分出来,如图1-4和图1-5所示。
碟片精选机的特点是工作面积大,转速高,产量比滚筒精选机大;而且为除去不同品种杂质所需要的不同袋孔可用于同一机器中,即在同一台机器上安装不同袋孔的碟片;碟片损坏可以部分更换,还可分别检查每次碟片的除杂效果,因此碟片精选机是比较优越的精选机,缺点是碟片上的袋孔容易磨损,功率消耗较大。
表1-1所示为碟片精选机的技术特性。
表1-1碟片精选机的技术特性
型号
项目
FTTф25〞×27
FTTф25〞×23
生产能力,t/24h
140
120
碟片直径,mm
630
630
碟片数目
27
23
碟片转速:
除芥麦
除燕麦
55—60
70—75
55—60
70—75
传动轮转速,r/min
175
17.5
所需功率,kW
1.9
1.5
外形尺寸,mm
2200×872×853
1900×872×853
2.滚筒精选机
图1-6所为滚筒精选机工作示意图。
袋孔2是开在筛转圆管1的内表面,长粒子大麦依靠进料位差和利用滚筒本身的倾斜度,沿滚筒长度方向流动由另一端流出,而短粒子大麦嵌入袋孔的位置较深,被带到较高位置而落入中央槽4之中由螺旋输送机3送出。
根据滚筒转速差别又分为快速滚筒精选机和慢速滚筒精选机,两者结构基本相似,但由于高速时使颗粒的离心力增大,中央、斜槽和螺旋输送机位置应较低速的高。
高速滚筒精选机和低速滚筒精选机技术特性举例列于表1-2中,作为参考。
表1-2滚筒精选机技术特性
技术特性
低速滚筒精选机
高速滚筒精选机
从大麦中除芥麦时生产能力,kg/h
1000
3000
功率,kW
0.3
0.55
圆筒直径,mm
600
600
圆筒长度,mm
2200
2000
筒转速,r/min
13
45
轴转速,r/min
50
120
尺寸:
长,mm
830
2853
宽,mm
640
640
重量,kg
300
350
此外低速滚筒精选机的安装应与水平线成5°~10°角,颗粒原料向出口运动速度约为0.03~0.05m/s,平均生产率为100~140[kg/h·m2(袋孔面积)]。
而高速滚筒精选机可接近水平安装,其生产率可达500kg/h·m2。
二、筛选设备
筛选是谷物等生物质原料清理除杂最常用的方法。
筛面上配备适当的筛孔,使物料在筛面上作相对运动。
生产用的生物质原料大多数都是粉粒状的,例如各种谷物、大米、麸皮等等。
其中常含有各种杂质,如泥土、砂石、草籽、杂谷、金属等,这必须先用筛子清除。
为保证生产质量,生产过程又往往将粒度不同的物料加以分级,这也要用筛子来完成。
这两方面的操作都可称为筛选。
筛选操作常常是将物料从筛的一端加入,并使其向筛的另一端移动,从而使尺寸小于筛孔的物料穿过筛孔落下,成为筛下物,而尺寸大于筛孔的物料经过筛面从筛的另一端引出。
筛选可以用人工的方法进行,但这时生产效率将会受到极大的限制。
生物加工过程中的筛选操作都由筛选机械来完成。
筛选机械有很多种不同的构造,发酵工厂中常用的是振动筛和转筒筛。
振动筛是原料加工中应用最广的一种筛选与风选结合的清理设备,多用于清除小及轻的杂质。
振动筛主要由进料装置、筛体、吸风除尘装置和支架等部分组成,如图1-7所示。
进料装置的作用是保证进入筛面的物料流量稳定并沿筛面均匀分布,以提高清理效率。
进料量可以调节。
进料装置由进料斗和流量控制活门构成。
按其构造有喂料辊和压力进料装置两种。
喂料辊进料装置需要传动,只有筛面较宽时才采用。
压力门进料装置结构简单,操作方便,喂料均匀,特别是重锤压力门进料装置,动作灵敏,能随进料变化自动调节流量,故为筛选设备普遍采用。
筛体是振动筛的主要工作部件,它由筛框、筛子、筛面清理装置、吊杆、限振机构等组成。
筛体内有三层筛面:
第一层是接料筛面,筛孔最大,筛上物为大型杂质,筛下物为粮粒及大型杂物,筛面反向倾斜,以使筛下物集中落到第二层的过程中,筛条的棱对料产生切割作用,厚度约有筛孔的1/4,一层料及其中的细粒被棱切割而被筛下。
曲筛的分级粒度大致是筛孔尺寸的一半。
但随着筛条棱的磨损,通过筛孔的粒度将减少。
振动筛是一种平面筛,常用筛子有两种:
一种是由金属丝(或其他丝线)编织而成的;另一种是冲孔的金属板。
筛孔的形状有圆形、正方形、长方形等。
大麦粗选机用的是长方形的冲孔筛板。
筛板开孔率一般为50~60%,开孔率越大,筛选效率越高,但开孔率过大会影响筛子的强度。
目前使用的筛选机,筛宽在500~1600mm之间,振幅通常取4~6mm,频率可在200~650次/分范围内选取,其生产能力由下面公式决定:
,kg/h(1-1)
式中
——筛面的宽度,m;
——单位筛宽流量,kg/(m•h);
如不知道
值,也可用下面近似公式计算生产能力:
,kg/h(1-2)
式中
——筛面有效宽度,m,取B0=0.95
;
——筛面物料层厚度,m,取
=1~2
(
为物料最大直径);
——物料沿筛面运动的平均速度,m/s,取0.5(m/s)以下;
——物料松散系数,取0.36~0.64;
——物料的密度,kg/m3。
生物加工厂如啤酒厂,常用的另一种筛是圆筒分级筛,用于大麦精选后的分级。
根据大麦分级的要求,在圆筒筛上布置不同孔径的筛面,一般安排矩形孔筛子用1mm厚的钢板制作,筛孔长25mm,宽2.2~2.5mm,可以将大麦分成三极,即大麦腹径(颗粒厚度)为2.5mm以上,2.2mm~2.5mm和2.2mm以下3种。
前两种为制麦芽用,后者作饲料。
有时根据具体情况可以多增加一种筛板如原大麦较大时,可增设矩形孔25×2.8mm,如原大麦较瘦小,可增设矩形孔25×2.0mm,将大麦分成四级。
圆筒分级筛如图1-8所示。
筛筒的倾斜角度为3-5°;筛筒直径与长度之比为1:
4~6;圆周速度约为0.7~1.0m/s,速度太快,粒子反而难以穿过筛孔,使生产率下降。
圆筒用厚1.5~2.0mm的钢板冲孔后卷成筒状筛,整个圆筒往往分成几节筒筛,布置不同孔径的筛面,筒筛之间用角钢连接作加强圈,如用摩擦传动则可作为传动的滚筒。
圆筒用托轮支承在用角钢或槽钢焊接的机架上,圆筒一般以齿轮传动。
筛分的原料由分设在下部的两个螺旋输送机分别送出,未筛出的一级大麦从最末端卸出。
圆筒分级的优点是:
设备简单,电动机传动方便。
缺点是:
筛面利用率小,仅为整个筛面的五分之一。
圆筒分级筛的生产能力可用下面的经验公式计算:
,kg/h(1-3)
式中
——单位筛面负荷量,kg/(m2•h),大麦取
=450~550kg/(m2•h);
——筛面直径,m2;
——筛筒长度,m;
——筛面有效系数,取
=1/4~1/6。
第二节生物质原料的粉碎
在生物生产中,为了加速后续的生物反应和化学反应等过程的反应速度,对于使用的固体生物质原料,常须将其粉碎。
使大块固体物料破碎成小块物料的操作,通常称为粉碎,而使小块物料进一步粉碎为粉末状物料,有时则称为磨碎或研磨,很多情况下,统称为粉碎。
在以固体生物质为原料的生物反应生产过程中,对原料粉碎的效果好坏,不仅直接反映出粉碎操作的合理性和经济性,而且会间接影响到下一工序如蒸煮、浸出、水解(酸解和酶解)和发酵等的效果和效率。
生物工厂均采用某种型式的机械方法,达到固体生物质原料粉碎的目的。
粉碎机械有多种类型,但机械粉碎的工作原理主要有以下几种方式:
(1)挤压粉碎固体原料放在两挤压面之间,当挤压面施加的挤压力达到一定值后,物料即被粉碎。
大块物料往往先以这种方式破碎。
(2)冲击粉碎物料受瞬时冲击力而被粉碎。
这种方式特别适用于脆性物料的破碎。
(3)磨碎物料在两相对运动的硬质材料平面或各种形状的研磨体之间,受到摩擦作用而被研磨成细粒。
这种方式多用于小块物料的细磨。
(4)劈碎物体放在一带有齿的面和一平面间受挤压即劈裂而粉碎。
(5)剪碎物料在两个破碎工作面间,如同承受载荷的两支点(或多支点)梁,除了在外力作用点受劈力外,还发生弯曲折断。
多用于较大块的长或薄的硬、脆性物料粉碎。
固体物料的粉碎,可按粉碎物料和成品的粒度大小,可作如下的分类:
(1)粗碎原料粒度范围为40~1500mm,成品粒度约为5~50mm;
(2)中、细碎原料粒度范围为5~50mm,成品粒度为0.1~5mm;
(3)微粉碎原料粒度范围为5~10mm,成品粒度<100μm左右;
(4)超微粉碎原料粒度范围为0.5~5mm,而成品<10~25μm。
物料粉碎前后的粒度比称为粉碎比或粉碎度。
如以X表示之,则:
(1-4)
式中
——粉碎前物料的平均粒径,mm;
——粉碎后物料的平均粒径,mm。
可见粉碎比表示粉碎操作中物料粒度变小的比例。
磨碎时粉碎比较粗碎和中、细碎时为大。
对于一次粉碎后的粉碎比,粗碎约为2~6,中、细碎为5~50,磨碎为50以上。
总粉碎比是表示经过几道粉碎步骤后的总结果。
粉碎物料时,须根据固体物料的物理性质、块粒大小、需要破碎或粉磨的程度,选择适当的破碎方法。
一般来说,任何一种粉碎机往往利用几种破碎方式进行物料的粉碎。
选择粉碎物料的方法,必须根据物料的物理性质,物料的大小,粉碎的程度等,应特别注意物料的硬度和破裂性。
对坚硬的和脆性的物料,挤压和冲击很有效。
对韧性物料剪切力作用较好。
对方向性物料则以劈碎为宜。
但不论哪一种粉碎机,很少单独使用其中的一种方法,而是几种方法的组合,使粉碎更加有效。
无论粉碎机械属哪种作用力形式,原料的性质如何及所需粉碎度怎样,都应符合下述一些基本要求:
(1)粉碎后的物料颗粒大小要均匀;
(2)已被粉碎的物块,须立即从轧压部位排除;
(3)操作能自动化,如能不断地自动卸料等;
(4)容易更换磨损的部分,在操作发生障碍时,有保险装置使能自动停车;
(5)产生极少的粉尘,以减少环境污染及保障工人健康;
(6)单位产品消耗的能量要小。
一、粉碎设备
(一)锤式粉碎机
锤式粉碎机是利用快速的锤刀对物料进行冲击粉碎,广泛用于各种中等硬度的物料,如地瓜、玉米等生物质原料的中碎与细碎作业,尤其使用于脆性物料。
由于脆性物料抗冲击性较弱,因此,从工作原理来说,采用这种破碎方式非常合理。
锤式粉碎机最大特点是具有很高的破碎比(达10~50)这是其他粉碎机不能比拟的。
此外单位产量能耗低、构造简单、结构紧凑、生产能力高等都是锤式粉碎机的优点。
因此,这种粉碎机在工业上获得广泛应用。
但锤式粉碎机也存在一些缺点,如工作部件易于磨损,物料含水量过高(超过10~15%)时,易于堵塞,因而维修工作量大。
锤片粉碎机的结构如图1-9所示,它比较简单,更换锤片和筛面操作方便,但运转时震动声音较大,如果转子安装的平稳,则锤片运转也较均衡。
这种粉碎机适用与甘薯干块状原料和野生植物原料的粉碎,操作要求低,较易把小块原料锤碎成细粉末,对原料品种变化的适应性也较强。
锤碎机内有一根水平轴,轴上装有一些圆盘,圆盘的周边安装着板状锤片(杆锤),周围有圆筒形外壳。
外壳分为两部分,上部为有沟形的表面,下部则为有孔的筛板,以被粉碎的物料通过筛孔落下。
这种设备的一般形式可以自制,轴的圆周线速达60--70米/秒。
锤碎机的主要构件如下:
1.锤刀
其主要部件是一个转动的圆筒,它装在轴上,主要是利用许多锤刀作圆周运动来锤碎原料。
锤刀的形式一般有矩形、带角矩形和斧形,有高碳钢片制成。
矩形的锤刀具有可多次再用的优点,当一般的角被磨钝后,可以倒转换再用,直至四边角全部用遍为止。
但装换时,应注意避免由于重量的不等而引起转子的不平衡。
由于矩形锤刀有多次再用的优点,所以,粉碎一般原料时,多采用这种锤刀。
但是对韧性较大的原料进行粉碎时,则采用斧形锤刀较适宜,由于斧形锤刀的重心偏于尖端,与同样重量的矩形锤刀相比较,斧形锤刀的打击粉碎力要大的多。
如图1-10所示。
原料的粉碎是由于锤刀的撞击作用,因此锤刀磨损甚速,经常要更换,否则会降低粉碎效果,而经常调换新的锤刀,则钢板耗用量大。
为了充分有效使用锤刀,某厂对锤刀的装置进行改进,如图1-11所示,于圆形的转子距离中心轴不同的位置上,对称地开有许多孔,而磨损的锤刀,可把磨损后的刀角切平,装在离中心轴较远的孔上。
这样既保证了锤刀顶端到筛面的距离,也可节省制造新锤刀的刚材。
2.筛面
用来控制粉碎程度,筛面采用铁板冲制。
粉料通风的筛孔,孔径在1.5~2.5毫米之间,许多酒精厂所采用的筛孔大小都在此范围内。
提高粉碎机效率的方法,一般有下列常用的几种:
(1)采用密闭循环法,为了减少磨损,能较快地把大少不同的物料颗粒分开,将没有达到规定的颗粒,与已达到要求的细粉,一起通过筛面,再在粉碎机外部用单独的筛子,把不合要求的物料分离开来,重新回到粉碎机中进行粉碎。
如此密闭循环,可提高生产能力达45~70%。
(2)增加吸风装置,增加吸风机后,可以加速粉料离开筛孔,把粉碎机内已经粉碎好的细粉抽出来,提高了粉碎机的工作效率。
据某厂采用后的经验,安装了旋风分离器,可以提高粉碎机的生产能力大约30%左右,而电耗也大为降低。
(3)采用鳞状筛代替平筛。
含水分较高的原料,会使粉碎带来困难,使锤碎机的筛孔被堵塞,粉碎效果显著降低,电耗也会增大,这时可采用湿式粉碎来解决此问题。
在年产不同的工厂里,采用锤碎机的数量也各有不同,产量大的工厂一般数量多些,这与动力大小也有关系。
但是,必须同时设有两套,一套备用,轮流使用。
锤碎机通常发生的不正常情况及其处理措施如下:
(1)出现锤碎机堵塞现象
其产生的原因可能有下面三个:
即进料量太多;筛孔堵塞;有异物落入机内。
通常可采用下列三个措施来处理:
首先是打开锤碎机,进行疏通;还可以取出筛子,疏通筛眼;或者可以停止磨粉,取出异物。
(2)锤碎机运转时有杂声
这是由于硬质杂物落入锤碎机内。
一般采取的措施是:
停止锤碎机运转,取出杂物,并检查筛子是否损坏。
(3)粉粒直径过大,超过规定范围
这是应为筛子磨损或破裂而引起的,处理的办法是调换新筛子。
(4)锤碎机落料过大的原因是筛子未装,或者是筛子脱头裂口大
采取的措施是停车检查,装筛或是换筛。
筛板用以控制物料的粒度,筛板上有许多筛孔、筛孔直径根据产品粒度来确定。
筛板上的孔有圆形或长条形,细粉碎机的筛孔多为圆形,粗粉碎机的筛孔多为长条形。
筛板表面与锤刀顶端间隙对产品粒度有影响,产品粒度越小,间隙也越小,一般为5~10mm。
锤式粉碎机的生产能力,可按半经验公式计算。
设从一个圆孔中排出的产品体积为:
,m3(1-5)
式中
——筛孔直径,m;
——产品粒度,m;
——排料系数,一般取0.7。
锤刀扫过筛孔时,才有产品排出,如果转子上有K排锤刀,则转子转动一周,锤刀就扫过K次,排料也为K次,如果转子转数为n(r/min),筛孔总数为Z个,则每小时排出产品的体积为:
,m3/h(1-6)
如果是长方形筛孔,则:
,m3(1-7)
式中
——筛孔长度,m;
——筛孔宽度,m。
动力消耗可按下面经验公式估算:
,KW(1-8)
式中
——锤刀末端的直径,m;
——转子轴向长度,m;
——转子转速,r/min;
——系数,由实验确定。
(二)辊式粉碎机
辊式粉碎机广泛用于破碎粘性和湿物料块。
啤酒厂粉碎麦芽和大米都是用辊式粉碎机,常用的有两辊式、四辊式、无辊式和六辊式等。
1.两辊式粉碎机
两辊式粉碎机主要工作机构为两个相对旋转的平行装置的圆柱形辊筒。
工作时,装在两辊之间的物料由于辊筒对物料的摩擦作用而被拖入两辊的间隙中被粉碎。
两辊式粉碎机制造简便,结构紧凑,运行平稳。
通常适于中碎和细碎。
两辊式粉碎机依照装配结构可分为:
(1)一个辊筒的轴承座可沿导轨滑移,另一辊筒轴承座固定(图1-12a);
(2)两个辊筒轴承座均可沿导轨滑移(图1-12b)。
按照辊筒表面形状可分为:
(1)辊筒表面光滑的;
(2)辊筒表面有齿的;(3)辊筒表面有凸棱或凹槽的。
按照粉碎工作原理可分为:
(1)由挤压作用进行粉碎作业的;
(2)由挤压、剪切与研磨作用联合作用进行粉碎作业的。
图1-13为一台两辊式粉碎机,其中一个辊筒轴承座为可移动的。
作为粉碎作业工作部件的两个辊筒相对转动。
固定辊筒的轴承座装在机架上,可移动的辊筒的轴承座为弹簧压紧,在承受载荷过大时,弹簧被压缩,轴承座可沿导轨滑移。
两轴承之间装有支撑架及可拆装的钢垫片,增减垫片厚度可调节两辊间的间隙。
当辊筒间隙内落入不能粉碎的硬物时,可移动辊筒使弹簧压缩而向后滑移。
硬物通过后,借弹簧力恢复到原来位置。
辊间的挤压力可由调节螺母及弹簧压板来调整。
辊筒外表面装配有耐磨护套,护套材料大多用锰钢。
为延长护套使用寿命,也有在护套表面焊一层耐磨硬质合金。
两辊筒下侧设有刮刀,用于刮除粘附在辊面上的物料。
传动机构直接驱动固定辊筒,而在辊筒另一端装配一对相啮合的齿轮,以驱动可滑移的辊筒使之与固定辊筒相对旋转。
由于在粉碎过程中两辊筒的中心距经常变动,因此齿轮对的齿形应是特别加高的。
两辊式粉碎机也有用其他型式传动机构的。
有的用一台电动机和一台有两个轴头的减速箱,通过万向联轴节分别拖动两个辊箱,以适应在粉碎过程中辊筒的移动。
高速两辊式粉碎机往往采用两台电动机分别传动。
要求成品粒度较细的两辊粉碎机,除了要求辊筒有较高线速度(最高可达8~10m/s),还应使两辊筒具有一定转速差(一般为15~20%)。
这样物料在两辊筒之间不仅经受挤压粉碎,同时经受研磨作用。
可是这种粉碎机辊筒表面磨损常常出现不均匀,从而使辊面上磨出一些环形条纹或沟槽。
为消除这一缺陷,往往采用一种能使辊筒旋转时作往复轴向移动的机构,如在轴头上安装一个槽形凸轮,依靠固定于机架上的小滚子而促使辊筒工作时往复轴向移动。
两个辊筒的轴承均能移动的两辊粉碎机,工作时运行较平稳,但传动机构本身较复杂,造价较高,故未能得到广泛应用。
2.四辊式粉碎机
四辊式粉碎机由两对辊筒和一组筛子所组成,如图1-14所示。
原料经第一对辊筒粉碎后,由筛选装置分离出皮壳排出,粉粒再进入第二对辊筒粉碎。
3.五辊式粉碎机
该机前三个辊筒是光辊,组成两个磨碎单元;后两个辊筒是丝辊,单独成一磨碎单元。
通过筛选装置的配合,可以分离出细粉、细粒和皮壳,如图1-15所示。
该机性能很好,如在啤酒加工过程中应用,通过调节可以应用于各种麦芽。
4.六辊式粉碎机
该机性能与五辊式相同。
它由三对辊筒组成,前两对用光辊,主要以挤压作用粉碎原料,可以使得生物质原料的皮壳不致粉碎得太细而影响后一工序的操作,如啤酒厂的麦芽汁过滤。
第三对辊筒用丝辊,将筛出的粗粒粉碎成细粉和细粒,以利于糖化时充分浸出有用物质。
该机的构造原理如图1-16所示。
6.辊式粉碎机生产能力及功率计算
辊式粉碎机的生产能力可用下式计算:
,kg/h(1-12)
式中
——辊筒直径,m;
——辊筒转速,r/min;
——辊筒长度,m;
——两辊间隙,b≈0.00015~0.0001m;
——物料的容量,对于干麦芽γ=500kg/m3;
——填充系数,对麦芽
=0.5~0.7,
值与物料性质及操作均匀度有关,准确数据在生产实践中查得。
根据经验,100mm长度的双辊粉碎机每小时生产能力为150~200kg。
四辊式粉碎机每小时生产能力为200~300kg。
粉碎机用于粉碎麦芽时,其功率可按下经验公式估算:
,kw(1-13)
式中
——系数,取
=100~110;
——粉碎机生产能力,t/h;
——麦芽粒子腹径,cm;
——辊筒转速,r/min。
根据经验,每小时500kg生产量的功率消耗为1kw左右。
(三)湿式粉碎机
生物加工工厂中,粉碎原料时,往往会逸出较多的粉尘,影响环境。
这是干法粉碎的一个不足之处。
为了避免这一缺点,在某些产品的生产过程中,采用湿式粉碎操作,其所用到的粉碎机称为湿式粉碎机。
湿式粉碎设备主要包括:
输料装置、加料器、粉碎机和加热器等几部分。
粉碎可采用一级或二级粉碎(两台粉碎机