模具专业毕业设计说明书.docx
《模具专业毕业设计说明书.docx》由会员分享,可在线阅读,更多相关《模具专业毕业设计说明书.docx(15页珍藏版)》请在冰豆网上搜索。
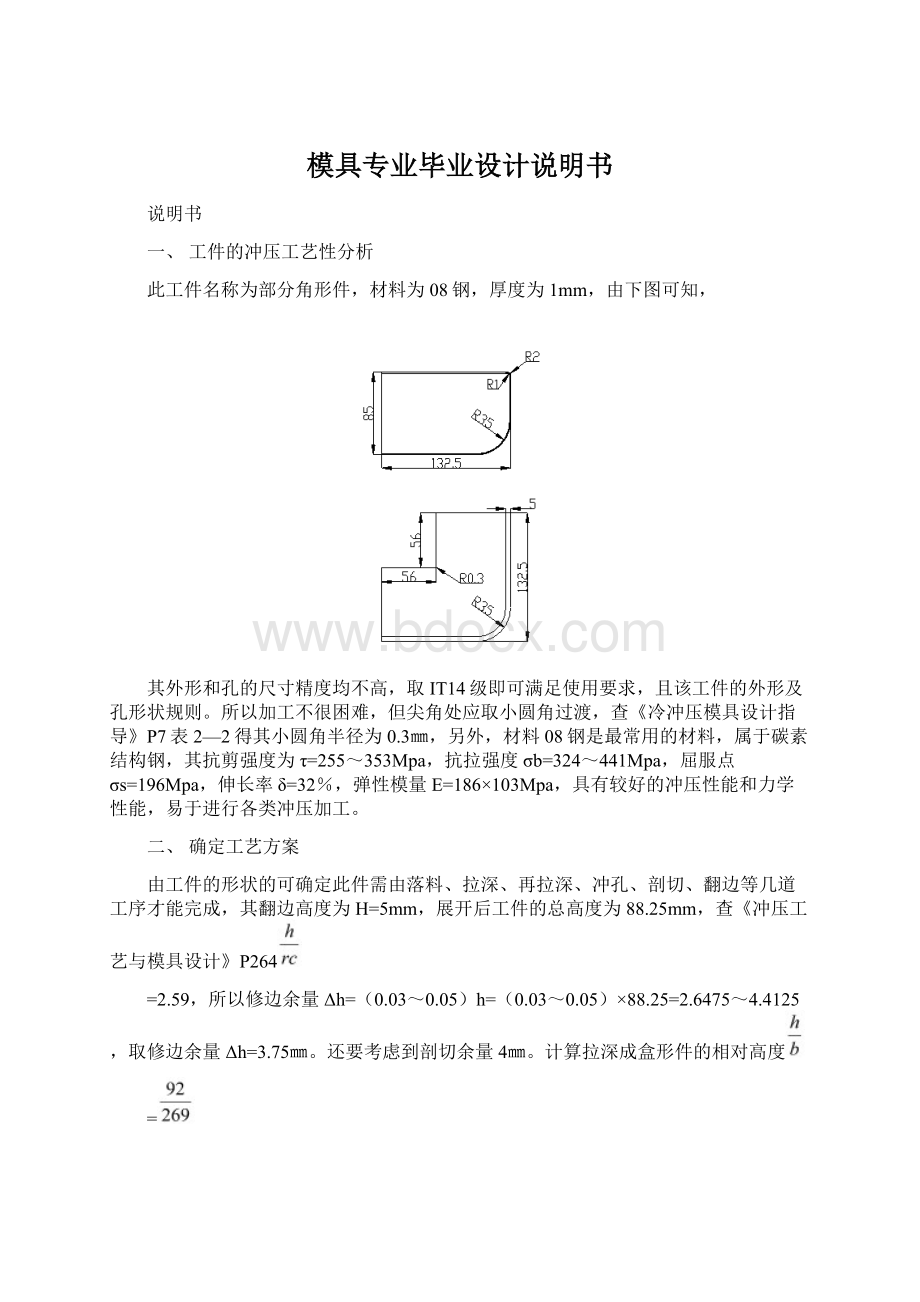
模具专业毕业设计说明书
说明书
一、工件的冲压工艺性分析
此工件名称为部分角形件,材料为08钢,厚度为1mm,由下图可知,
其外形和孔的尺寸精度均不高,取IT14级即可满足使用要求,且该工件的外形及孔形状规则。
所以加工不很困难,但尖角处应取小圆角过渡,查《冷冲压模具设计指导》P7表2—2得其小圆角半径为0.3㎜,另外,材料08钢是最常用的材料,属于碳素结构钢,其抗剪强度为τ=255~353Mpa,抗拉强度σb=324~441Mpa,屈服点σs=196Mpa,伸长率δ=32%,弹性模量Ε=186×103Mpa,具有较好的冲压性能和力学性能,易于进行各类冲压加工。
二、确定工艺方案
由工件的形状的可确定此件需由落料、拉深、再拉深、冲孔、剖切、翻边等几道工序才能完成,其翻边高度为H=5mm,展开后工件的总高度为88.25mm,查《冲压工艺与模具设计》P264
=2.59,所以修边余量Δh=(0.03~0.05)h=(0.03~0.05)×88.25=2.6475~4.4125,取修边余量Δh=3.75㎜。
还要考虑到剖切余量4㎜。
计算拉深成盒形件的相对高度
=
=0.34mm,查《冷冲压模具设计指导》P112表4—12得
=0.7~0.6,
=0.34<
=0.7~0.6高度不能一次拉深成形,所以需要进行两次拉深,校核角部的拉深系数m=
=
=0.43,查表4—13得M1=0.35,得M>M1,角部能一次拉成。
另外,此工件为部分角形件,生产批量为中、小批量,且零件的质量及精度没有特殊要求,所以按IT14级算。
为了降低模具费,所以采用单工序模具分散冲压成型,拉深后还得修边,应采用先落料、拉深、再拉深、修边、冲孔、剖切、翻边的工序组合。
三、毛坯尺寸的展开计算
1、工序分析
由上面分析知,此工件应先落料、拉深、再拉深、修边、冲孔、剖切、翻边等工序组成,所以应由工件先计算出拉深、翻边、落料等的毛坯尺寸。
2、翻边的毛坯尺寸计算
查《实用冲压工艺及模具设计手册》P598页
翻边的展开长度按式W=A+B-J计算,其中J为修正量,由本页图8—20查得J取1.75,所以W=A+B-J=85+5-1.75=88.25mm。
3、再拉深时的毛坯尺寸计算
查书《实用冲压工艺及模具设计手册》P516页
第一次拉深后为圆筒形件Dn-1=1.41B-0.82r+2δ
式中B=269㎜,r=34㎜,δ=(0.2~0.25)r=(0.2~0.25)×34=6.8~8.5㎜
所以Dn-1=1.41B-0.82r+2δ=1.41×269-0.82×34+2×(6.8~8.5)=366㎜
取首次拉深凹模圆角半径rn=(10~6)t=10㎜,首次拉深后制件的直径为d1=366㎜,并且第一次拉深后的半径应大于第二次拉深后的半径,所以取首次拉深凸模圆角半径r1=40㎜.
高度h=1/4(D2/dn-dn+1.72rn+0.57rn2/dn)=56.375mm=54㎜
4、第一次拉深时毛坯尺寸计算
查《冷冲压模具设计指导》P110页r=r底
D=1.13
=1.13
=437㎜
四、模具设计
(一)、第二次拉深模
1、模具及工件的工艺性分析
前一次拉深工件图
第二次拉深工件图
零件的生产工序为落料、拉深、再拉深、修边、冲孔、一次剖切、二次剖切、翻边。
模具采用单工序制作,由于第二次拉深模凸、凹模间隙较大,所以不需要精确的导向及标准模架进行导向,该件外形简单,形状规则,而且拉深过程中无较小圆角半径等问题,零件尺寸公差无特殊要求,按IT14级选取,选用普通的倒装式模具可达到拉深要求要求。
2、确定工艺方案
零件属于中、小批量生产,工艺性较好。
由于零件为规则的方盒形件,采用单工序模即可达到要求。
3、工艺与设计计算
(1)凸、凹模尺寸计算
凹模+成形凹模>凹模圆角半径+顶出装置高度+件的高度
所以凹模高度根据实际情况的需要取110㎜,成形凹模高度为20㎜,圆角取前一道工序的0.7-0.8倍的前一次拉深圆角直径,即r=8mm
根据情况凸模H定为220㎜L×B=267×267㎜
凸、凹模刃口尺寸
查《冷冲压模具设计指导》P210表8—14公差Δ=1.3㎜
查《冷冲压模具设计指导》P126表4—34得δp=0.06δd=0.08
查《冷冲压模具设计指导》P125表4—32得单边间隙
=(1~1.1)t,Z=2~2.2
查《冷冲压模具设计指导》P125表4—33
凹模尺寸:
Ld=(l+0.4Δ+Z)
=(269+0.4×1.4+2.1)
=271.66
凸模尺寸Lp=(l+0.4Δ)
=(269+0.4×1.4)
=269.56
通气孔直径d查《冷冲压模具设计指导》P311表5—16得d>9.5㎜取10㎜
高度h1>件高度H=92㎜
h1=(5~10)+H=100㎜
(2)、计算拉深力和压边力
查《冷冲压模具设计指导》P119表4—21得K5=0.9
据《冷冲压模具设计指导》P117表4—19得拉深力
Fl=(4b-1.72r)σbk5
=(4×269-1.72×34)×1×400×0.9
=366.307KN
压边力,查《冷冲压及塑料成型工艺与模具设计资料》P124表1-4-26得
F压=π/4〔D2-(d1-2rd)2〕p
查《冷冲压及塑料成型工艺与模具设计资料》P124表1-4-28得单位压边力P=2.5~3
带入数据F压=π/4〔3662-(269+2×34)2〕×(2.5~3)
=48.01KN
所以F总=Pl+F压=366.307KN+48.01KN=414.317KN
取JC23—63压力机F压=630KN
(0.7~0.8)F公=441~504KN
414.317KN<441~504KN
4、计算或估算模具各主要零件的外形尺寸
(1)工作零件
对于拉深模,由计算可知件一次拉深圆角部分能完成,但高度部分不能一次拉成,故采用两次拉深。
需要两套拉深模具来完成。
第二次拉深是将圆筒形件拉成所需要的方形盒件,在拉深过程中,由于空气压力的作用或润滑油的粘性等因素,使工件很易粘在凸模上,所以设计凸模时还应有通气孔,其通气孔的直径大小和高度由查表选取。
拉深模按普通的倒装式设计,选用单动压力机,上装弹性装置及通用弹顶器就能对工件进行压边,凹模内放推板,选有模柄孔的旋入式模柄,孔内放入顶杆即可将工件顶出。
有压边装置,便于采用通用的弹顶装置,以保证之间的定位精度。
由于拉深件无特殊要求,且拉深件高度较高,凹模作成分体式较经济性,所以成型凹模材料选Cr12MoV,热处理硬度为60-64HRC,周界尺寸为L×B×H=530×530×20mm,凹模为45号钢,周界尺寸为L×B×H=530×530×110mm,凸模材料选CrWMn,热处理硬度为58-62HRC,周界尺寸为L×B×H=267×267×220mm。
由于拉深件高度较高,而且凹模内还有推板的厚度,所以凸模固定板厚度H1≈0.4H=0.4×130≈50㎜,周界长度与凹模相同,530㎜×530㎜。
为保证模具固定,所以,模座长边比凸模固定板多40~70㎜的余量所以取模座外形尺寸为630㎜×530㎜×50㎜。
(2)、定位零件
由于前一次拉深得工件为圆筒件,不好定位和装卡,所以采用前一次拉深凸模内径配作压边圈的外径,跟凹模单边留有0.1-.05mm的间隙,并且留出台阶,另外在压边圈与凹模之间还设置了限位柱,为了控制压边圈与凹模之间的间隙,以克服在拉深后期由于压边力过大造成工件底角附近板料过分减薄,甚至拉破等现象。
拉深时直接把工件倒扣在压边圈上,因此压边圈的高度应大于前次工序件的高度
(3)、卸料和推件装置
拉深完的工件在回程由推件板从凹模内推出,进行卸料。
由于模具是倒装,推板由放在模柄内的顶杆顶出,成型凹模比凹模单边留有4㎜的台阶以致推板不能随件落下,而一直留在型腔内,所以顶杆采用普通的圆柱销即能工作,为了保证拉深完的件能在顺利卸料,把推板作成台阶式,而且工件尺寸较大,凹模、成型凹模和上模座板用螺钉和销钉连接在一起,
5、模具总体设计
有了上述各步计算所得的数据及确定的工艺方案,便可以对模具进行总体设计并画出草图。
根据凹模的外形尺寸,下模板的外形尺寸630㎜×530㎜×50㎜。
上模板的外形尺寸530㎜×530㎜×40㎜。
6、选定设备
查《冷冲压模具设计指导》P119表4—21得K5=0.9
据《冷冲压模具设计指导》P117表4—19得拉深力
Fl=(4b-1.72r)σbk5
=(4×269-1.72×34)×1×400×0.9
=366.307KN
压边力,查《冷冲压及塑料成型工艺与模具设计资料》P124表1-4-26得
F压=π/4〔D2-(d1-2rd)2〕p
查《冷冲压及塑料成型工艺与模具设计资料》P124表1-4-28得单位压边力
P=2.5~3
带入数据F压=π/4〔3662-(269+2×34)2〕×(2.5~3)=48.01KN
所以F总=Pl+F压=366.307KN+48.01KN=414.317KN,取JC23—63压力机,F压=630KN
公称压力630KN;
滑块行程100㎜;
最大封闭高度390㎜;
工作台尺寸:
前后570㎜,左右860㎜;
模柄直径50㎜,深度70㎜;
滑块底面尺寸:
前后360㎜,左右430㎜。
(二)、冲孔模
1、冲孔件
冲制件为方形如下图
2、分析冲孔件的工艺性
零件尺寸公差无特殊要求,按IT14级选取,原件冲孔116×116处是直角,由于冲裁件的内形转角处应避免尖角,应有适当的圆角,查《冲压工艺与模具设计》P6表2—1得圆角半径为0.3㎜,修改后的件图如上所示。
3、工艺与设计计算
(1)凸、凹模尺寸计算
凸模为正方形L=116㎜。
凸、凹模刃口尺寸计算
查《冷冲压模具设计指导》P16表2—12得δp=0.025δd=0.035
查《冷冲压模具设计指导》P16表2—13公差X=0.75㎜
查《冷冲压模具设计指导》P18表2—16公差Δ=0.87㎜
查《冷冲压模具设计指导》表2—14
凸模尺寸:
Bp=(B+XΔ)
=(116+0.75×0.87)
=116.6525
凹模工作部分尺寸均按凸模研配,保证两侧共有0.64~0.88㎜的均匀间隙即可
凹模厚度H=92+(2~5)㎜=95㎜
是否采用垫板,σ=
=
=
×(324~441)=11.17~15.20千帕<[σp]
所以得采用垫板
(2)、计算冲裁力,压力中心的确定,弹性元件的选用和核算等
a)压力中心的计算
由于工件在成型过程中为完全对称的形状,故其压力中心就是其件的中心位置,所以不用计算。
b)弹性元件的选用与核算
由于采用弹压卸料装置,用橡胶块作为弹性元件,具有承受负荷比弹簧大,具有安全及安装调整方便等优点,冲孔模的工作行程较小,选用橡胶块作为弹压卸料装置的弹性元件更为多见,所以此处选用的是硬度为邵氏70~80安的聚氨酯橡胶为弹性元件。
由于其性能比合成橡胶优异,不仅可获得较大的压力,而且可延长其使用寿命
橡胶高度H=
=
对于硬度为邵氏70~80A的合成橡胶,εj=35%εy=10%
Hg=t+1
H≥
=8㎜
根据实际需要H取20㎜
橡胶块截面尺寸计算A=
F≥F卸=7168N单位压力Fq查《冷冲压工艺与模具设计》P106表2—27得Fq=5.6mP,A=
=
=1280㎜2
橡胶高度校核
选取弹压卸料螺钉孔直径为d=10.5㎜
弹性体外径D=
=
=41.7㎜
=
=0.314<0.5
所以橡胶符合要求
4、选择设备及吨位的根据
冲孔力F=Ltσb=116×4×1×400=185.6KN
查《冷冲压模具设计指导》P22表2—20,K卸=0.04~0.05
F卸=K卸×F=0.04×185.6=7.424KN
F总=F+F卸=185.6+7.424=193.024KN
为了安全起见,选压力机J23—35,压力机规格:
最大闭合高度300㎜;
工作台尺寸:
前后380㎜,左右610㎜;
模柄直径50㎜,深度70㎜。
滑块行程80㎜;
滑块底面尺寸:
前后190㎜,左右210㎜。
5、模具结构的总体设计
(1)工作零件
由于在冲孔模之前是第二次拉深后得到的工件为盒形件,为了保证工件的精确定位,及冲孔位置精度的要求,采用再拉深时的凸模形状为凹模且与工件有一定的间隙,既要保证冲孔精度,又不能让工件在凹模上移动。
然后直接将盒形件倒扣在凹模上就能精确定位,不过比盒形件的高度高,留出点余量,以免发生件跟下模板碰撞,导致工件冲孔质量得不到保证,甚至报废,采用标准模架。
即可满足模具及件的要求。
凹模周界尺寸为L×B×H=267×267×95mm,材料选用9Mn2V,凸模周界尺寸为L×B×H=116×116×78mm,材料选T10A
(2)定位零件
由于前一次拉深得工件为方盒形件,不好定位和装卡,采用第二次拉深时的凸模的内径为标准进行配作冲孔件的凹模,所以采用前一次拉深凸模内径配作压边圈的外径,跟凹模单边留有0.1-.05mm的间隙,拉深时直接把工件倒扣在凹模上,因此凹模的高度应大于前次工序件的高度,取95mm。
(3)卸料与推件装置
由于工件是倒扣在凹模上,在凸模冲裁完,后回程时,工件很容易套在凸模上面,采用弹压卸料板和弹性元件橡胶进行卸料,这样可以减小元件在凸模工作完回程时工件套在凸模上起皱等现象的发生。
弹压卸料板、橡胶、凸模固定板、垫板和上模座板用螺钉和销钉连接在一起,弹压卸料板与凹模之间应用合适的间隙,在弹压卸料板无精确导向时,其型孔与凹模之间的双边间隙可取0.1~0.3mm,为确保卸料可靠,装配模具时,弹压卸料板的压料面应超出凸模端面0.2~0.5mm。
5、强度校核
凸模一般不用校核,但对于特别细长的凸模或凸模断面尺寸小而板料厚度大时,则应进行强度校核。
而此冲孔凸模截面尺寸相对板料厚度大,且凸模粗大,所以此凸模不必进行强度校核。
(五)、剖切模
1、确定工艺方案
冲制件为方形如下图
零件尺寸公差无特殊要求,按IT14级选取,
零件属于中、小批量生产,工艺性较好,由于模具的要求也不用太高,所以据综合要求模具采用单工序生产,选用标准模架比较经济性。
2、工艺与设计计算
(1)凸、凹模尺寸计算
凸模为长方形L=269
㎜,B=4
㎜。
由于剖切相当于斜刃冲裁,由于工件尺寸比较大,所以凸、凹模刃口尺寸按直边冲孔计算
查《冷冲压模具设计指导》P18表2—16公差Δ
=0.048㎜,Δ
=0.21㎜,XΔ
=0.048㎜,XΔ
=0.21㎜
查《冷冲压模具设计指导》表2—14
凸模尺寸:
Lp
=(L+XΔ)
=(4+0.048)
=4.048
Bp
=(B+XΔ)
=(289+0.21)
=289.21
凹模尺寸按凸模尺寸配制,其双面间隙为0.06-0.08㎜
为了留出足够的让凸模量,以致凸模能完全剖切凹模厚度H=110㎜
是否采用垫板,σ=
=
=
×(324~441)=164.4~220.5<σp]
所以得采用垫板
2)、计算冲裁力,压力中心的确定
a)压力中心的计算
由于工件在成型过程中为完全对称的形状,故其压力中心就是其件的中心位置,所以不用计算。
2)选择设备及吨位的根据
为了保证剖切制件的工艺性要求,模具的冲裁力按直边的冲孔力计算,F=Ltσb=(269+4)×2×300×1=163.8KN
由于压力机闭合高度不够,所以选大一号压力机J23—35,压力机规格:
最大闭合高度300㎜;
工作台尺寸:
前后380㎜,左右610㎜;
模柄直径50㎜,深度70㎜。
滑块行程80㎜;
滑块底面尺寸:
前后190㎜,左右210㎜。
3、模具的总体结构设计
(1)工作零件
将盒形件切成4均分,需要两次剖切才能完成。
第一次剖切与第二次剖切的模具结构基本相同,只是第二次剖切是凹模或凹模框尺寸大小不相同而已,剖切时的凸模工作截面作成4㎜宽的片,而且两边是斜刃的方式剖切便于使盒形件的直边部分先切到,不至于引起变形等,剖切后的废料顺漏料槽排除,件也随着一分为二自己脱落下来,不需要卸料装置。
要求模具的定位精度要高,否则制件很易不合格,凸模由于太薄,不好生产,也不好固定,而且如果把凸模固定板做得跟垫板一样尺寸大小的话,不好用销定位凸模,而且由于凸模大而薄,不好加工和生产。
所以只好采用护套的形式可以保证凸模的准确定位和工作,通过护套固定在凸模固定板上,凹模和模架及螺钉和孔的尺寸都跟冲孔模一样。
便于选材和进料,以及生产等。
凹模周界尺寸为L×B×H=267×267×110㎜,材料选用9Mn2V,凸模周界尺寸为L×B×H=289×4×150mm,材料选T10A
(2)定位零件
由于前一次拉深得工件为方盒形件,不好定位和装卡,采用冲孔时的凸模的内径为标准进行配作冲孔件的凹模,所以采用前一次拉深凸模内径配作凹模块外径,跟凹模单边留有0.1-.05mm的间隙,剖切时直接把工件倒扣在凹模块上,凹模块由螺钉和销钉固定在下模座上,因此凹模的高度应大于前次工序件的高度,取110mm。
(3)卸料与推件装置
由于工件是倒扣在凹模上,在凸模冲裁完,后回程时,由于工件相当与斜刃冲裁,所以不需要担心工件很容易套在凸模上,由于剖切模相当于把件一分为二,件和废料切完以后直接落下,省去了卸料装置,使模具更为简单,只需凸模通过销固定在凸模固定块上,再由凸模固定块跟板连接,上模由螺钉和销钉固定上模座、垫板和凸模固定板。
4、强度校核
凸模一般不用校核,但对于特别细长的凸模或凸模断面尺寸小而板料厚度大时,则应进行强度校核。
而此剖切模虽然薄而大。
但最小尺寸4㎜≥(2-3)t,还用护套固定,所以不用校核。
六.参考文献
1、钟毓斌.《冲压工艺与模具设计》.北京:
机械工业出版社,2000.5
2、王同海孙胜等编.《实用冲压设计技术》北京:
机械工业出版社.1995.4
3、王芳主编.《冷冲压模具设计指导》.北京:
机械工业出版社,1999.10
4、《冷冲压及塑料成型工艺与模具设计资料》.北京.机械工业出版社
5、郑家贤编.《实用冲压工艺及模具设计手册》.北京:
机械工业出版社,2005.1