注塑生产新技术.docx
《注塑生产新技术.docx》由会员分享,可在线阅读,更多相关《注塑生产新技术.docx(9页珍藏版)》请在冰豆网上搜索。
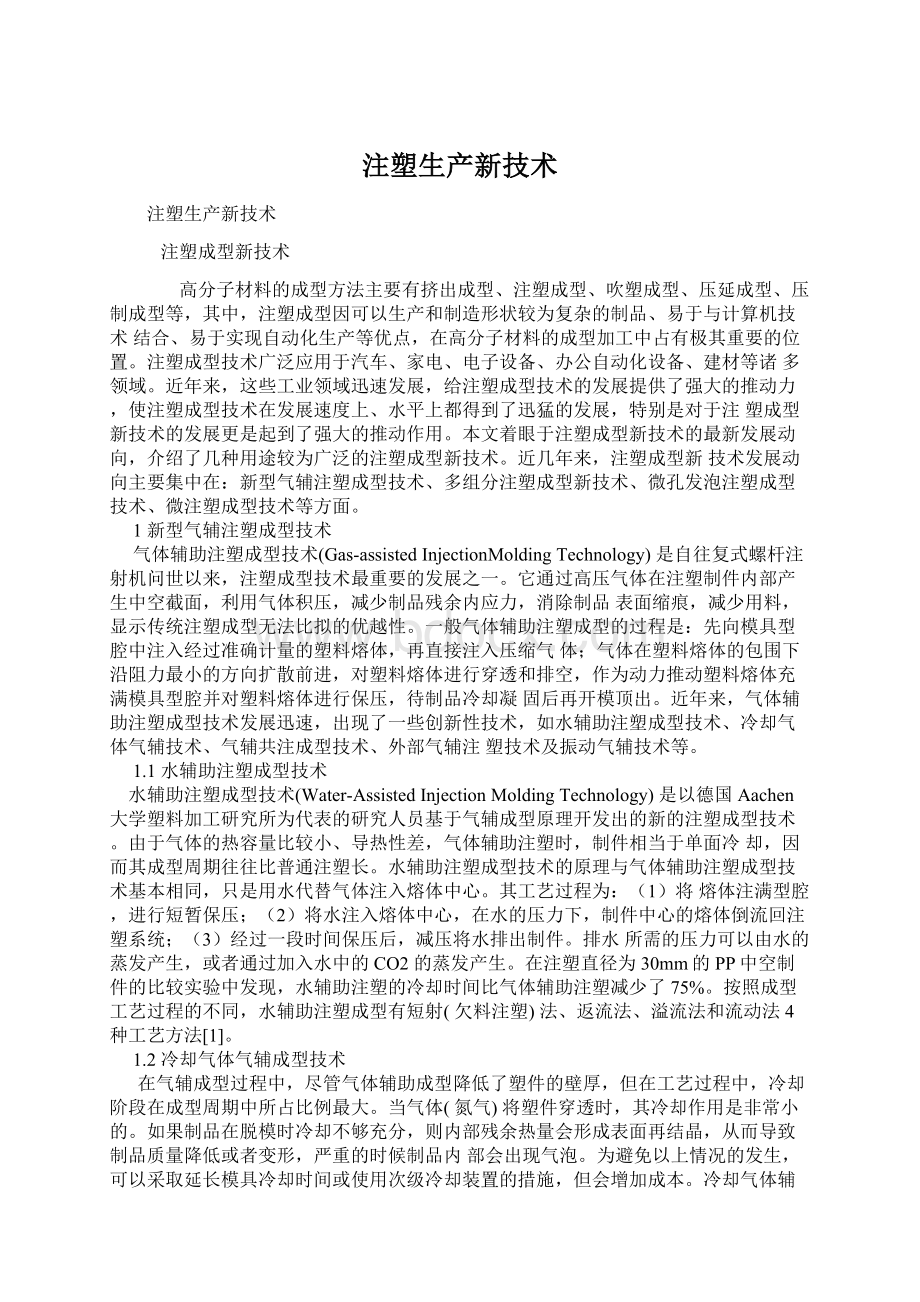
注塑生产新技术
注塑生产新技术
注塑成型新技术
高分子材料的成型方法主要有挤出成型、注塑成型、吹塑成型、压延成型、压制成型等,其中,注塑成型因可以生产和制造形状较为复杂的制品、易于与计算机技术结合、易于实现自动化生产等优点,在高分子材料的成型加工中占有极其重要的位置。
注塑成型技术广泛应用于汽车、家电、电子设备、办公自动化设备、建材等诸多领域。
近年来,这些工业领域迅速发展,给注塑成型技术的发展提供了强大的推动力,使注塑成型技术在发展速度上、水平上都得到了迅猛的发展,特别是对于注塑成型新技术的发展更是起到了强大的推动作用。
本文着眼于注塑成型新技术的最新发展动向,介绍了几种用途较为广泛的注塑成型新技术。
近几年来,注塑成型新技术发展动向主要集中在:
新型气辅注塑成型技术、多组分注塑成型新技术、微孔发泡注塑成型技术、微注塑成型技术等方面。
1新型气辅注塑成型技术
气体辅助注塑成型技术(Gas-assistedInjectionMoldingTechnology)是自往复式螺杆注射机问世以来,注塑成型技术最重要的发展之一。
它通过高压气体在注塑制件内部产生中空截面,利用气体积压,减少制品残余内应力,消除制品表面缩痕,减少用料,显示传统注塑成型无法比拟的优越性。
一般气体辅助注塑成型的过程是:
先向模具型腔中注入经过准确计量的塑料熔体,再直接注入压缩气体;气体在塑料熔体的包围下沿阻力最小的方向扩散前进,对塑料熔体进行穿透和排空,作为动力推动塑料熔体充满模具型腔并对塑料熔体进行保压,待制品冷却凝固后再开模顶出。
近年来,气体辅助注塑成型技术发展迅速,出现了一些创新性技术,如水辅助注塑成型技术、冷却气体气辅技术、气辅共注成型技术、外部气辅注塑技术及振动气辅技术等。
1.1水辅助注塑成型技术
水辅助注塑成型技术(Water-AssistedInjectionMoldingTechnology)是以德国Aachen大学塑料加工研究所为代表的研究人员基于气辅成型原理开发出的新的注塑成型技术。
由于气体的热容量比较小、导热性差,气体辅助注塑时,制件相当于单面冷却,因而其成型周期往往比普通注塑长。
水辅助注塑成型技术的原理与气体辅助注塑成型技术基本相同,只是用水代替气体注入熔体中心。
其工艺过程为:
(1)将熔体注满型腔,进行短暂保压;
(2)将水注入熔体中心,在水的压力下,制件中心的熔体倒流回注塑系统;(3)经过一段时间保压后,减压将水排出制件。
排水所需的压力可以由水的蒸发产生,或者通过加入水中的CO2的蒸发产生。
在注塑直径为30mm的PP中空制件的比较实验中发现,水辅助注塑的冷却时间比气体辅助注塑减少了75%。
按照成型工艺过程的不同,水辅助注塑成型有短射(欠料注塑)法、返流法、溢流法和流动法4种工艺方法[1]。
1.2冷却气体气辅成型技术
在气辅成型过程中,尽管气体辅助成型降低了塑件的壁厚,但在工艺过程中,冷却阶段在成型周期中所占比例最大。
当气体(氮气)将塑件穿透时,其冷却作用是非常小的。
如果制品在脱模时冷却不够充分,则内部残余热量会形成表面再结晶,从而导致制品质量降低或者变形,严重的时候制品内部会出现气泡。
为避免以上情况的发生,可以采取延长模具冷却时间或使用次级冷却装置的措施,但会增加成本。
冷却气体辅助成型技术便是针对以上的问题而出现的一种新的气辅成型方法。
在冷却气体辅助成型工艺中,气体通常被冷却至–20℃~180℃。
冷却气体形成的过程是:
常温气体通过一个腔室,在其中被液氮冷却。
这种冷却气体辅助成型技术的主要优势在于:
当冷却气体穿透熔体时,在模腔内会产生塞流效应,塞流产生的残余壁厚比传统气体辅助成型要小;冷却气体也防止了制件内部起泡,并能产生较光滑的内表面[2]。
1.3气辅共注成型技术
气辅共注成型技术(Co-InjectionandGas-AssistedInjectionMolding)是将聚合物共注成型技术与气辅技术相结合而得到的一种新工艺。
聚合物共注成型技术是同时或者先后向模腔内注入不同的聚合物熔体,形成多层结构的一种成型技术,而与共注成型工艺相比多了一个注气过程;相对气辅成型而言,则多了一个多层结构的形成过程[3-5]。
气辅共注成型的过程包括三个阶段:
(1)共注塑阶段。
此阶段与一般共注成型工艺类似,只是在形成表/内层结构后,当表层和内层所注入的材料总量占型腔总体积一定比例时,停止注塑熔体,此过程可谓气辅过程的“欠料注塑”,只是注入两种以上的熔体;
(2)气辅注塑阶段。
气体对内层熔体进行穿透,随着气体的推进,被气体“排挤”的内层熔体又带动表层熔体向前流动;(3)保压冷却,释压脱模,获得制品。
为了实现聚合物的气辅共注成型,必须对原有共注成型设备进行改造,即在共注成型设备的基础上增加一套气辅系统。
1.4外部气体辅助成型技术
外部气体辅助注塑成型技术(ExternalGasMoldingTechnology)是与传统的内部气体注塑成型不同的一种气体辅助注塑方法。
传统的气体辅助成型技术是将气体注入塑料熔体内以形成中空的部位或管道,而新型气辅成型技术是将气体注入模腔表面的局部密封位置中(相当于在塑料熔体外部),故称之为“外气注塑”[6]。
1.5振动气辅成型技术
一般的气体辅助注塑成型属于非动态成型工艺,而振动气体辅助注塑成型(VibratedGas-AssistMolding)工艺最大的不同便是引入振动波,使常规气体辅助注塑成型时注入的“稳态气体”,变为具有一定振动强度的“动态气体”,从而利用气体作为媒介将振动力场引入到气辅注塑成型的充模、保压和冷却过程中,使其成为动态的成型工艺[7]。
2多组分注塑成型技术
多组分注塑(Multi-ComponentInjectionMolding)是由至少两种不同的材料通过注塑成型得到所需部件的加工过程,其整合各组分的优越性能,可以生产普通单组分注塑过程无法实现的特殊性能制品。
这种由两种或更多种材料组成的产品,与传统的由一种材料成型的注塑产品相比具有不同的物理特性。
多组分注塑成型的独特之处在于[8]:
(1)可将不同加工特性的材料复合成型;
(2)提高制品手感和外观,集多种性能于一体;(3)缩短了产品的设计、生产及成型周期,降低了成本;(4)省略了传统注塑成型后二次加工、装配的过程。
2.1多组分注塑成型工艺
当前,多组分注塑成型主要有共注塑成型、三明治成型、双色注塑成型、包覆成型、多色注塑成型等技术[9],而根据各组分在其成型过程中结合形式的不同,大致可分为顺序注塑成型和叠加注塑成型两大类。
2.1.1顺序注塑成型
顺序注塑成型是指依次注入物料的工艺过程,这一过程是通过特殊的多组分喷嘴来实现的。
其过程是先向模腔中注入第一种熔融组分形成制品表层,然后通过切换多组分喷嘴的切换阀,注射第二种组分,形成制品的内核部分,其过程如图1所示。
就常见的双组分夹芯注塑来说,可以将两组分某方面的性能互补,扬长避短,以达到单组分制品无法获得的性能。
顺序注塑成型应用最多的有以下三大类:
(1)对于大体积制品,内核利用回收的物料,而外层为起装饰作用的新材料;
(2)对于要求承受弯曲应力等载荷的制品,其外层使用玻纤增强材料,而内核可以采用非增强材料;(3)对于厚壁制品,常使用发泡物料制成其内核[10-11]。
图1顺序注塑成型示意图
Fig.1Theschematicdiagramofsequenceinjectionmolding
2.1.2叠加注塑成型
叠加注塑成型过程是通过不同的浇口或流道将多种组分(通常是两种)注塑到一起,或者将一种组分叠加在另一种组分之上。
与顺序注塑成型相比,其关键在于模具部分的改进和变化。
叠加注塑成型又可分为“熔融/熔融”注塑成型和“固体/熔融”注塑成型两种[10]。
“熔融/熔融”注塑成型也就是一般说的共注塑成型,其特点是同时把两种熔融组分经由不同的浇口注入模腔。
“固体/熔融”注塑成型的特点是在第一种熔融组分部分固化后,再注塑第二种,甚至第三种、第四种组分。
如模内自组装注塑成型,是在第一种组分完全固化后,通过内部或外部的传递机构转移至下一成型位置,注入下一组分,实现多组分注塑,如图2所示[10,12]。
图2模内自组装注塑成型示意图
Fig.2Theschematicdiagramofnorminnerself-assembledinjectionmolding
2.2多组分注塑成型设备
不同的成型工艺需要由对应的成型设备来实现。
对应于上述多组分注塑成型工艺的分类,相应成型设备的注射单元的主要形式有:
(1)数个注射单元水平方向相互平行或互成一定角度的布局(L型或V型)设计或在竖直面内垂直分布;
(2)两个注射单元共用一个喷嘴,注塑部分允许两种组分交替顺序注塑或间歇顺序注塑。
多组分成型设备的代表有德国(KraussMaffei)克劳斯•玛菲公司的Revolution旋转压板双组分注塑系统等[13]。
2.3多组分注塑成型技术的发展趋势
随着塑料注塑制品的广泛应用,多组分技术在当代注塑技术中具有巨大的机遇和希望。
与单一组分的普通注塑技术相比,多组分技术在设计和功能上具有明显的优势。
不同热塑性塑料共成型、弹性体塑料和热固性塑料共成型、超壁双组分成型、装饰性衬里成型等是多组分技术的趋势[14]。
另外,用多组分技术制出的具有磁性、导热或导电性等填充型功能热塑性塑料制件也成为当前研究热点。
3粉末注塑成型技术
粉末注塑成型(PowderInjectionMolding)是将现代塑料注塑成型技术引入粉末冶金领域而形成的一门新型粉末冶金成型新技术。
它是塑料成型工艺学、高分子化学、粉末冶金工艺学和金属材料学等多学科渗透与交叉的产物,利用模具注塑成型坯件,并通过烧结快速制造高密度、高精度、三维复杂形状的结构零件,能够快速准确地将设计思想物化为具有一定结构、一定功能的制品,并可直接批量生产出零件,是制造技术行业一次新的变革。
3.1粉末注塑成型的工艺过程及技术特点
粉末注塑成型的工艺流程,如图3所示。
(1)选取符合粉末注塑成型技术要求的金属粉末和有机黏结剂;
(2)在一定温度下,采用适当的方法将粉末和黏结剂混合成均匀的喂料;(3)用注塑成型机将制成粒状后的喂料注入模腔内后冷凝成型,得到成型坯件;(4)对成型坯件进行脱脂处理;(5)烧结成型坯件,得到最终产品。
图3粉末注塑成型的工艺流程
Fig.3Theflowchartofpowderinjectionmolding
粉末注塑成型技术在制造具有复杂形状、均匀组织结构和高性能、高强度、高精度的产品方面显示了独特的优势。
不仅具有常规粉末冶金工艺工序少、无切削或少切削、经济效益高等优点,而且克服了传统粉末冶金工艺制品、材质不均匀、机械性能低,不易成型薄壁、复杂结构的缺点,特别适合于大批量生产小型、复杂形状以及具有特殊要求的金属零件,采用粉末注塑成型进行大批量生产有较大的成本优势,生产成本只有传统工艺的20%~60%。
粉末注塑成型技术的出现,给各行各业设计和制造人员提供了崭新的设计思路和制造技术,采用粉末注塑成型技术可以大胆采用原来由于可加工性和加工经济性差而不得不放弃的一些结构复杂的设计方案。
还可使原来由于加工困难、而不得不采用的组合件、拼装件进行一次复合完成加工[15-16]。
3.2粉末注塑成型工艺的新发展
近几年,粉末注塑成型技术得到快速发展。
其最大特点是粉末注塑成型技术与其他成型技术相结合,得到了许多优异的产品。
微型注塑成型和双组分注塑成型与粉末注塑成型结合:
以微型拉伸试样作为研究对象,证明双组分注塑成型粉末产品切实可行,开发的产品实例为一种微型加热针。
Arburg公司注塑了质量为0.0679g的陶瓷产品,用作绝缘材料[17-18]。
振动辅助注塑成型:
殷小春等[19]对振动辅助注塑成型应用于金属粉末注塑成型过程进行了研究。
结果表明:
振动力场可以使不同径向位置处的模腔最大压力随振动振幅、频率的增加而减小,从而可以在不影响制品性能的条件下降低注塑成型压力,以拓宽金属粉末注塑成型的适用范围。
今后,粉末注塑成型技术研究和开发的主要方向是:
开发高效、低成本的预混合粉生产技术;研究和开发工艺性能更佳的新型黏结剂,建立起黏结剂设计原理和数据库[20];开发粉末注塑成型过程模拟与仿真技术,为模具设计和注塑工艺制定奠定理论基础;发展低温、快速脱脂和低温烧结技术,减小缺陷和变形。
4微孔发泡注塑成型
微孔泡沫塑料(MCF)是指微孔直径为0.1~10.0μm,微孔密度达109~1015个/cm3,材料密度比发泡前减少5%~98%的泡沫塑料。
与不发泡塑料相比,微孔泡沫塑料具有优良的冲击性能、高疲劳寿命、低介电常数和热导率。
由于微孔发泡塑料达到了既降低材料的成本又提高其性能的双重效果,性价比更高,因此具有极大的应用前景。
利用气体超临界液体状态在整个聚合体中产生分布均一和尺寸统一的微小的气孔(根据聚合体不同的材质及应用,其尺寸通常为
度,缩短了成型周期。
一般采用用微注塑成型的零件,其成型循环时间较从前缩短40%左右[30-31]。
图4微型注塑的工艺过程
Fig.4Theprocessofmicro-injectionmolding
5.2微注塑成型设备
微注射机是微注塑成型的关键。
与传统注塑成型技术相比,微注塑成型技术对生产设备有许多特殊要求,主要表现为以下几个方面:
(1)高注射速率;
(2)精密注射量计量;(3)快速反应能力。
按驱动方式分类,可分为液压/气压式驱动、全电式驱动和电液复合式驱动。
按塑化和注射单元的机构设计分类,可分为螺杆式、柱塞式、螺杆柱塞混合式及其他特殊形式。
螺杆式微注射机的代表型号有德国Dr.BOY公司的BOY12A,日精树脂工业株式会社的HM7-DENKEY,树研工业的JMW-015S-5T及东芝的EC5。
柱塞式微注射机代表机型有西班牙Cronoplast公司的Babyplast6/10,英国MCP公司的Rabbit2/3和美国MedicalMurray公司的Sesame。
螺杆柱塞混合式微注射机的代表型号有英国MCP公司的12/90HSP,日本Sodick公司的TR18S3A及Battenfeld公司的Microsystem50[32]。
6结语
目前,注塑成型技术是塑料加工中最常用的方法之一,可用来生产空间几何形状非常复杂的塑料制件。
近年来,各种注塑成型技术取得了显著的进步,其发展总趋势是不断满足高分子制向高度集成化、高度精密化、高产量等方面发展的要求,实现对制品材料的聚集态、相形态、组织态等方面的控制,或实现对制品进行异质材料的复合,最大程度地发挥聚合物的特性,达到制品高性能的目的。
深入研究塑料注塑成型技术与注塑成型设备,克服制品中的缺陷,对科技进步与人们高标准的生活要求有重要意义。
参考文献(略)