建筑钢结构检测取样方法及数量.docx
《建筑钢结构检测取样方法及数量.docx》由会员分享,可在线阅读,更多相关《建筑钢结构检测取样方法及数量.docx(13页珍藏版)》请在冰豆网上搜索。
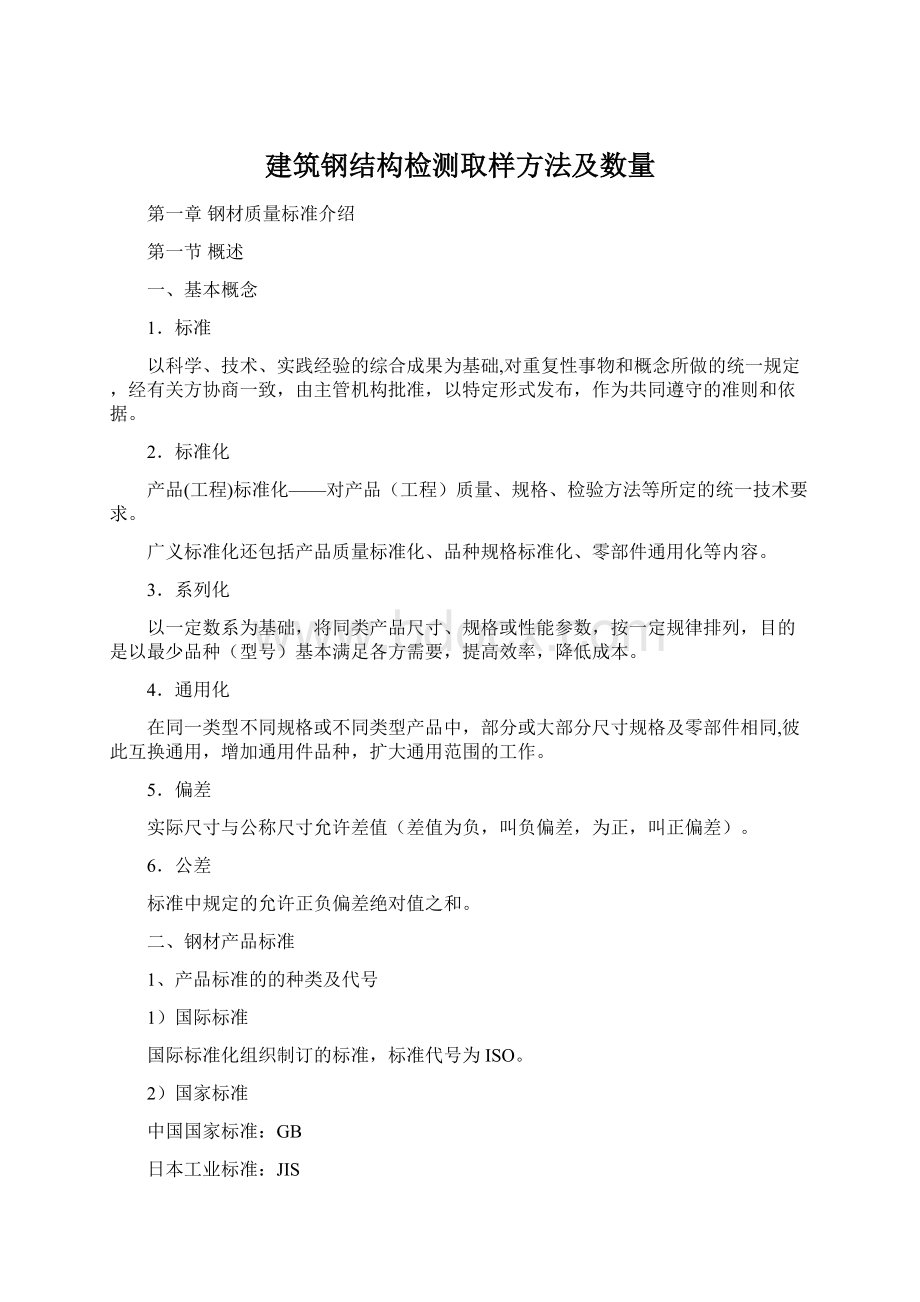
建筑钢结构检测取样方法及数量
第一章钢材质量标准介绍
第一节概述
一、基本概念
1.标准
以科学、技术、实践经验的综合成果为基础,对重复性事物和概念所做的统一规定,经有关方协商一致,由主管机构批准,以特定形式发布,作为共同遵守的准则和依据。
2.标准化
产品(工程)标准化——对产品(工程)质量、规格、检验方法等所定的统一技术要求。
广义标准化还包括产品质量标准化、品种规格标准化、零部件通用化等内容。
3.系列化
以一定数系为基础,将同类产品尺寸、规格或性能参数,按一定规律排列,目的是以最少品种(型号)基本满足各方需要,提高效率,降低成本。
4.通用化
在同一类型不同规格或不同类型产品中,部分或大部分尺寸规格及零部件相同,彼此互换通用,增加通用件品种,扩大通用范围的工作。
5.偏差
实际尺寸与公称尺寸允许差值(差值为负,叫负偏差,为正,叫正偏差)。
6.公差
标准中规定的允许正负偏差绝对值之和。
二、钢材产品标准
1、产品标准的的种类及代号
1)国际标准
国际标准化组织制订的标准,标准代号为ISO。
2)国家标准
中国国家标准:
GB
日本工业标准:
JIS
美国钢铁协会标准:
AISI
美国材料试验协会标准:
ASTM
英国国家标准:
BS
德国国家标准:
DIN
2、产品标准的内容
1)品种(规格)标准
2)性能标准(技术条件)
3)试验标准
4)交货标准
5)特殊条件
第二章钢材质量检验
第一节概述
一、质量检验的目的
验证钢板能否达到某种标准要求,挑出不合格品,并将合格品分出等级。
二、质量检验的种类
按生产流程,检验有进货检验、工序检验、成品检验。
第二节钢材质量检验方法
一、组织观察法
组织观察——观察金属的某一断面,研究其中出现的相的种类、数量、分布、形状、大小及其相互关系,据此了解该金属材料的组织状况。
组织——用肉眼或借助于各种不同放大倍数的显微镜所观察到的金属材料内部的情景。
用肉眼或放大几十倍的放大镜所观察到的组织,称为低倍组织或宏观组织;
用放大100~2000倍的显微镜所观察到的组织,称为高倍组织或显微组织;
用放大几千倍到几十万倍的电子显微镜所观察到的组织,称为电镜组织或精细组织。
二、材料试验法
1.金属材料室温拉伸试验GB/T228-2002
拉伸试样的横截面有圆形、矩形、多边形、环形,特殊情况下也可以是其它形状。
试样原始横截面积用S0表示,试样原始标距(受力前测量伸长用的试样圆柱或棱柱部分的长度)用L0表示。
根据试样的原始标距L0与原始横截面积S0的关系,试样可分为比例试样和非比例试样。
国际上使用的比例系数为5.65和11.3两种,即比例试样有两种习惯上称第一种为短比例试样,称第二种为长比例试样,一般采用短比例试样。
GB/T228-2002还规定原始标距应不小于15mm。
当试样横截面积太小,以致于采用比例系数为5.65的值不能符合这一最小标距要求时,可以采用11.3的值或采用非比例试样。
非比例试样的原始标距与其横截面积无关。
根据拉伸曲线上各特殊点的载荷与试样原横截面积的关系,可以测得材料的强度指标和塑性指标。
金属材料的强度指标包括上屈服强度(ReH)、下屈服强度(ReL)、规定非比例延伸强度(RP)、规定总延伸强度(Rt)、规定残余延伸强度(Rr)、抗拉强度(Rm)。
塑性指标包括断后伸长率(A)、断面收缩率(Z)。
由于对同一材料用不同长度的标准试样所测得的断后伸长率数值不同,因此应注明试样尺寸比例。
对于比例试样,若原始标距为5.65可不标,若原始标距不是5.65则应附下脚注说明所使用的比例系数,如A11.3表示原始标距为11.3的断后伸长率;对于非比例试样,符号A应附以下脚注说明所使用的原始标距,以毫米(mm)表示,如A80mm表示原始标距为为80mm的断后伸长率。
拉伸试样的原始标距为50mm,原始直径为10mm,拉断后对接试样的标距长度为79mm,缩颈区的最小直径为4.9mm,求其断后伸长率和断面收缩率。
某厂购进一批钢,假如按国家标准规定,它的机械性能指标应不低于下列数值:
ReH=340N/mm2、Rm=540N/mm2、A=19%、Z=45%。
验收时将购进的这批钢制成d=10mm的圆形短比例试样作室温拉伸试验,得到如下数据:
试验力首次下降前的最大力是28260N、断裂前的最大试验力是45530N,断后标距为60.5mm,缩颈区的最小直径为7.3mm。
试问这批钢的力学性能是否合格。
2.金属材料布氏硬度试验GB/T231.1-2009
布氏硬度的表示方法由五部分组成,如“600HBW1/30/20”,第一部分为布氏硬度值,第二部分为硬度符号,第三部分为硬质合金球直径(单位:
mm),第四部分为施加的试验力对应的kgf值,第五部分为试验力保持时间,若试验力保持时间为标准规定的保持时间(10~15s)则不标出,如“400HBW1/30”。
3.金属材料洛氏硬度试验GB/T230.1-2009
洛氏硬度的表示方法由四部分组成,如“70HR30TW”。
第一部分“70”为洛氏硬度值,第二部分“HR”为洛氏硬度符号,第三部分“30T”为洛氏硬度标尺符号,第四部分“W”为压头类型(W——硬质合金球,S——钢球,压头为金刚石圆锥时不标示)。
GB/T230.1-2009还规定,洛氏硬度试验一般在10~35℃室温下进行,初试验力保持时间不应超过3s,从初试验力施加到总试验力的时间应在1~8s之间,总试验力保持时间为4s±2s。
当产品标准中另有规定时,施加全部试验力的时间可以超过6s,但在试验结果中应注明,如“65HRFW,10s”。
4.金属材料纸氏硬度试验GB/T4340.1-2009
维氏硬度试验结果的表示由四部分组成,如“640HV30/20”。
第一部分“640”为维氏硬度值,第二部分“HV”为维氏硬度符号,第三部分“30”为维氏硬度试验力的kgf值,第四部分“20”为试验力保持时间,若试验力保持时间为标准规定的保持时间(10~15s)则不标出,如“450HV0.1”。
5.冲击试验
冲击性能指标的表示方法
GB/T229-2007GB/T229-1994
符号名称符号名称
KU2U型缺口试样在2mm摆锤刀刃下的冲击吸收能量AKU2缺口深度2mm的U型缺口试样的冲击吸收功
KU8U型缺口试样在8mm摆锤刀刃下的冲击吸收能量AKU5缺口深度5mm的U型缺口试样的冲击吸收功
KV2V型缺口试样在2mm摆锤刀刃下的冲击吸收能量AKVV型缺口试样的冲击吸收功
KV8V型缺口试样在8mm摆锤刀刃下的冲击吸收能量
注:
GB/T229-2007中规定摆锤刀刃半径为2mm和8mm两种,GB/T229-1994中摆锤刀刃半径为2~2.5mm,缺口深度一致
第三章钢材表面缺陷
1.掌握下列缺陷的特征、产生原因及预防的控制措施。
折迭、耳子、结疤、浪形、塔形、欠酸洗
2.掌握下列缺陷的特征
夹杂、过烧、辊印、轧疤、扭转、弯曲、错牙、脱方、分层、氢致裂纹、疲劳断裂、松卷、扁卷、镰刀弯、折边、楔形、麻点、过酸洗、塔形、瓢曲
第四章质量管理
第一节概述
一、车间管理的内容
车间管理就其业务范围来说,大致可以归纳为以下:
计划管理、生产管理、质量管理、技术管理、设备管理、物质管理、劳动管理(即劳动工资管理)、财务管理。
二、质量管理的发展阶段
一般按照质量管理所依据的手段和方式,将质量管理大致划分为如下四个阶段:
1.传统管理阶段
产品质量主要是靠工人的实际操作经验,靠手摸、眼看等感官估计和简单的度量衡测量而定,工人既是操作者又是质量检验者、质量管理者。
经验就是“标准”。
质量标准的实施是靠“师傅带徒弟”的方式口授手教进行的,故有人称之为“操作者的质量管理”。
2.质量检验管理阶段
通过严格检验来控制和保证出厂或转入下道工序的产品质量。
检验工作是这一阶段执行质量职能的主要内容。
这种检验属于“事后检验”,无法在生产过程中起到预防、控制产品质量的作用,一经发现废品,就很难补救。
3.统计质量管理阶段
这一阶段利用数理统计原理,预防产品废品并检验产品质量。
在方式上是由专职检验人员转移给专业的质量控制工程师和技术员承担。
4.现代质量管理阶段
这一阶段强调进行全面质量管理,强调执行质量职能是公司全体员工的责任,应该使全体员工都具有质量的意识和承担质量的责任,而不能仅仅依赖质量检验和运用统计方法,也不能把质量职能完全交给专职的质量控制工程师和技术人员。
三、全面质量管理
1.全面质量管理(TQM)的概念
由企业全体人员参加、以数理统计方法为主要手段,专业管理和其它管理相结合,建立一整套质量管理体系,保证用最经济的方法研制、生产、销售用户满意的优质产品的一套科学管理方法。
原来也称TQC。
2.全面质量管理的特点
全面质量管理的基本核心是强调提高人的工作质量,保证工序质量,以工序质量保证产品质量,达到全面提高企业和社会经济效益的目的。
在推行质量管理时应注意做到“三全、一多样”,即全过程的、全员的、全企业的质量管理;所运用的方法必须多种多样,因地制宜。
3.全面质量管理的基本观点
全面质量管理有五个基本观点:
1)广义质量观点;
全面质量管理中的“质量”是广义的,它包括产品本身的质量和工程质量和工作质量。
产品质量:
产品的性能、寿命、可靠性、安全性、经济性、使用价值等。
工程质量:
工程的好坏(工程——产品生产过程中,操作者、原材料、设备、方法、环境等因素共同决定产品质量的过程)。
工作质量:
全体人员在各自的有关工作中的质量。
2)用户第一;
3)预防为主;
4)一切用数据说话;
5)全面质量管理是每个职工的本质工作。
4.全面质量管理的工作方式
全面质量管理的工作方式是“计划(P)、实施(D)、检查(C)、处理(A)”四个阶段的循环方式,简称PDCA循环。
第一阶段即计划阶段(P),就是要适应用户要求,以社会经济效益为目标,通过市场研究,制定技术经济指标,研制、设计质量目标,确定达到这些目标的具体措施和方法。
第二阶段即执行阶段(D),就是执行计划、完成任务。
第三阶段即检查阶段(C),检查实施产品质量计划是否达到预期的效果,总结成败所在和经验教训。
第四阶段即处理阶段(A),根据检查结果,采用相应的处理措施巩固成绩、克服缺点、吸取教训,进入新的PDCA循环。
第二节现代质量管理的基本概念
1.质量
产品、过程或服务满足规定或潜在要求(或需要)的特征和特性总和,称为质量。
“规定”就是产品质量标准、工程建设质量标准和服务质量标准等质量标准。
“潜在要求”或“潜在需要”往往随时间而变化,它包括适用性、安全性、可用性、可靠性、可维修性、经济性等几个方面。
产品质量是产品的使用价值。
即产品满足人们(社会的、个人的)的需要所具有的那些自然属性。
服务质量是指服务的适用性,即服务能满足他人的需要所具备的那些特性。
如安全、迅速、方便、经济等等。
2.质量管理(QM)指对确定和达到质量要求所必需的职能和活动的管理。
3.质量控制(QC)指为保持某一产品、过程或服务质量满足规定的要求所采取的作业技术和活动。
4.质量保证(QA)指为使人们相信某一产品、过程或服务质量能满足规定的质量要求所必须的有计划、有系统的全部活动。
5.质量体系
为保证产品、过程或服务质量满足规定或潜在的要求,由组织机构、职责、程序、活动、能力和资源等构成的有机整体,称为质量体系。
6.质量成本
将产品质量保持在规定的水平上所需的费用,称为质量成本。
质量成本包括预防成本、鉴定成本、内部损失成本、外部损失成本。
7.质量管理小组(QC小组)
QC小组是企业职工参加现场质量管理活动的群众性基层组织。
8.产品可靠性
产品在规定条件下和规定时间内,完成规定任务的能力,称为可靠性。
9.产品可用性
产品在规定的条件下,完成规定的功能的能力。
产品的可用性是产品能力的一种定量表现,所谓可用性是产品能连续不断运转,随时可用的能力。
10.产品安全性
产品在制造、储存和使用过程中保证人身与环境免遭危害的程度。
或说在设计时为使产品失效不致引起人身物质等重大损失而采取的预防措施。
11.产品维修性
指在规定条件下,使用的产品在规定时间内按规定的程序和方法进行维修时,保持或恢复到能完成规定功能的能力。
12.使用寿命
产品在规定的使用条件下完成规定功能的工作总时间。
第三节质量管理的基础工作
一、标准化工作
企业推行标准化,一般应符合以下具体要求:
1)权威性(要硬性规定以“标”为“法”,在企业内应该有专门的部门监督检查。
2)群众性。
要在总结经验的基础上,有领导地依靠大家来制定和执行标准。
3)科学性。
要充分运用现代化管理技术(如价值工程、运筹学、工业工程等),使制定的标准有科学依据。
4)连贯性。
各部门、各方面的标准要连贯一致,互相配合和协调。
同时,标准既不能“朝令夕改”,也不能长期不修改(国标和行标一般应3~5年修订一次,企业标准修改期可更短一些)。
修订时也要考虑前后标准的协调一致。
5)明确性。
标准要成文,内容要明确,要求要具体,不宜抽象和模棱两可。
二、计量工作
三、质量信息和质量教育工作
第四节质量管理方法与工具
现代的质量管理工作是以数理统计方法及现代科学管理方法作为基本手段来控制和预防质量问题的。
“以数据说话”是质量管理的基本特点之一。
在实际工作中,经常用数据来说明问题的程度和实质,如反映某项质量问题的严重程度,评价工作有效性等等。
为了形象地描述分析问题,经常采用排列图、因果分析图、调查表、直方图、散布图、控制图和数据分层法等,被称为“质量管理常用的七种工具”。
一、排列图
排列图——在产品质量管理中,把影响产品质量的各种缺陷、问题(或原因),按其不同类别整理出数据,然后将数据按不合格品数目多少(或金额多少)顺序排列而作的图。
又称主次因素分析图,或称为帕累托(Pareto)(巴雷特)图。
排列图有两个纵坐标,一个横坐标。
左纵坐标表示频数(件数、金额、工时等),右纵坐标表示频率(以百分比表示)。
横坐标表示影响质量的各种因素,按其影响程度大小从左到右顺序排列。
直方条的高度表示某个因素影响大小,折线表示各影响因素大小的累计百分数(帕累托曲线、巴雷特曲线)。
某厂某月镀锡原板废品数统计如下表所示。
试计算各种废品的频数,画出排列图,并分析引起废品的主要因素、次要因素和一般因素。
建 筑 钢 结 构 检 测 取 样 方 法 及 数 量
第一部分:
见证取样检测
一、钢材质量
对属于下列情况之一的钢材,应对钢材进行化学成分分析和力学性能的抽样复验:
(1) 国外进口钢材;
(2) 钢材混批;
(3) 板厚等于或大于40mm,且设计有Z向性能要求的厚板;
(4) 建筑结构安全等级为一级,大跨度钢结构中主要受力构件所采用的钢材;
(5) 设计有复验要求的钢材;
(6) 对质量有疑义的钢材。
1、化学成分分析(主控项目)
(1)检验指标:
碳、硅、锰、硫、磷及其他合金元素
(2) 依据标准:
《钢和铁化学成分测定用试样的取样和制样方法》GB/T20066-2006
《建筑结构检测技术标准》GB/T50344-2004
(3) 取样方法及数量:
钢材化学成分分析,可根据需要进行全成分分析或主要成分分析。
所采用的取样方法应保证分析试样能代表抽样产品的化学成分平均值。
分析试样应去除表面涂层、除湿、除尘、以及除去其他形式的污染。
分析试样应尽可能避开孔隙、裂纹、疏松、毛刺、折叠或其他表面缺陷。
制备的分析试样的质量应足够大,以便可能进行必要的复检验。
对屑状或粉末状样品,其质量一般为100g。
可采取钻、切、车、冲等方法制取屑状样品。
不能用钻取方法制备屑状样品时,样品应该切小或破碎,然后用破碎机或振动磨粉碎。
振动磨有盘磨和环磨。
制取的粉末分析试样应全部通过规定孔径的筛。
钢材化学成分的分析每批钢材取1个试样。
2、力学性能检验(主控项目)
(1) 检验指标:
屈服点、抗拉强度、伸长率、冷弯、冲击功
(2) 依据标准:
《钢及钢产品力学性能试验取样位置及试验制备》GB /T2975-1998
《建筑结构检测技术标准》GB/T50344-2004
(3) 取样方法及数量:
应在外观及尺寸合格的钢材上取样,产品应具有足够大的尺寸。
取样时应防止出现过热、加工硬化而影响力学性能。
取样的位置及方向应符合GB /T2975-1998附录A的规定。
当工程没有与结构同批的钢材时,可在构件上截取试样,但应确保结构构件的安全。
按每批钢材,拉伸试验取1个试样,冷弯试验取1个试样,冲击试验取3个试样。
当被检钢材的屈服点或抗拉强度不满足要求时,应补充取样进行拉神试验。
补充试验应将同类构件同一规格的钢材划为1批,每批抽样3个。
二、紧固件及网架节点连接质量
1、高强度大六角头螺栓连接副(主控项目)
高强度大六角头螺栓连接副出厂时要进行扭拒系数及机械性能试验,并且螺栓进场后要进行扭拒系数复验。
(1) 检验指标:
扭矩系数(强制检验项目)、楔负载、螺栓实物最小拉力载荷、螺母保证载荷、螺母及垫圈硬度
(2) 依据标准:
《钢结构工程施工质量验收规范》GB50205-2001
《钢结构用高强度大六角头螺栓、大六角头螺母、垫圈技术条件》GB/T1231-2006
(3) 取样方法及数量:
同一性能等级、材料、炉号、螺纹规格、长度(当螺栓长度≤100mm时,长度相差≤15mm;螺栓长度>100mm时,长度相差≤20mm,可视为同一长度)、机械加工、热处理工艺、表面处理工艺的螺栓为同批;同一性能等级、材料、炉号、螺纹规格、机械加工、热处理工艺、表面处理工艺的螺母为同批;同一性能等级、材料、炉号、规格、机械加工、热处理工艺、表面处理工艺的垫圈为同批。
分别由同批螺栓、螺母、垫圈组成的连接副为同批连接副。
每3000套为一批,不足3000套视为一批,每种规格及批次取8套。
送检的高强螺栓要保证出厂状态(出厂后3个月内),并且表面清洁、螺纹无损伤。
2、扭剪型高强度螺栓连接副(主控项目)
扭剪型高强度螺栓连接副出厂时要进行紧固预拉力及机械性能试验,螺栓进场后必须进行紧固预拉力复验。
(1) 检验指标:
紧固预拉力(强制检验项目)、楔负载、螺栓实物最小拉力载荷、螺母保证载荷、螺母及垫圈硬度
(2) 依据标准:
《钢结构工程施工质量验收规范》GB50205-2001
《钢结构用扭剪型高强度螺栓连接副》GB/T3632-2008
(3) 取样方法及数量:
同高强度大六角头螺栓
3、钢网架用高强度螺栓(一般项目)
钢网架用高强度螺栓出厂时要进行螺栓实物拉力载荷试验。
对建筑结构安全等级为一级,跨度40m及以上的螺栓球节点钢网架结构,其连接高强度螺栓应进行表面硬度试验。
(1) 检验指标:
螺栓实物拉力载荷、表面硬度
(2) 依据标准:
《钢结构工程施工质量验收规范》GB50205-2001
《钢网架螺栓球节点用高强度螺栓》GB/T16939-1997
(3) 取样方法及数量:
同一性能等级、材料、炉号、规格、机械加工、热处理及表面处理工艺的螺栓为同一批。
对于≤M36的螺栓最大批量为5000只,对于>M36的螺栓最大批量为2000只。
每批次及规格抽取8只。
4、高强度螺栓连接摩擦面(强制检验项目)
钢结构制作和安装单位应进行高强度螺栓连接摩擦面的抗滑移系数试验和复验,现场处理的构件摩擦面应单独进行摩擦面抗滑移系数试验。
(1) 检验指标:
抗滑移系数
(2) 依据标准:
《钢结构工程施工质量验收规范》GB50205-2001
《钢结构高强度螺栓连接的设计、施工及验收标准》JGJ82-1991
(3) 取样方法及数量:
每2000吨为一批,不足2000吨视为一批,每种规格、批次及摩擦面处理方法取3组(6个芯板+6个侧板+12个高强螺栓)。
钢板厚度要根据螺栓长度及工程中有代表性的部位确定,试件板面应平整,无油污,孔和板的边缘无飞边、毛刺,并且芯板厚度要保证摩擦面滑移前钢板始终处于弹性变形状态。
抗滑移试件的加工尺寸及要求见附录B。
5、网架节点承载力(主控项目)
对建筑结构安全等级为一级,跨度40m及以上的公共建筑钢网架结构,且设计有要求时,应按下列项目进行节点承载力试验。
(1) 检验指标:
焊接球节点承载力、螺栓球节点承载力、杆件及焊缝承载力
(2) 依据标准:
《钢结构工程施工质量验收规范》GB50205-2001
《网架结构工程质量检验评定标准》JGJ78-1991
(3) 取样方法及数量:
焊接球节点必须按设计采用的钢管与焊接球焊接成试件,检查数量为每个工程可取受力最不利的球节点以600只为一批,不足600只仍按一批,每批取3只为一组随机抽检。
螺栓球与高强度螺栓配合,检查数量为每个工程可取受力最不利的球节点以600只为一批,不足600只仍按一批,每批取3只为一组随机抽检。
钢管与封板或锥头焊接成试件,检查数量为每个工程可取受力最不利的杆件以300根为一批,不足300根仍按一批,每批取3根为一组随机抽检。
第二部分:
现场检测
一、焊接质量
1、焊缝外观质量检查(一般项目)
(1) 依据标准:
《钢结构工程施工质量验收规范》GB50205-2001
(2) 取样方法及数量:
每批同类构件抽查10%,且不应少于3件;被抽查构件中,每种焊缝按条数抽查5%,且不应少于1条;每条检查1除,总抽查数不应少于10处。
2、焊脚尺寸检查(主控项目)
T型接头、十字接头、角接接头等要求熔透的对接和角对接组合焊缝及设计有疲劳验算要求的吊车梁或类似构件的腹板与上翼缘连接焊缝要进行焊脚尺寸检查。
(1) 依据标准:
《钢结构工程施工质量验收规范》GB50205-2001
(2) 取样方法及数量:
同类焊缝抽查10%,且不应少于3条。
3、焊缝表面探伤(磁粉、渗透)(一般项目)
当外观检查焊缝表面质量有疑义时,采用磁粉或渗透探伤。
(1) 依据标准:
《钢结构工程施工质量验收规范》GB50205-2001
(2) 取样方法及数量:
每批同类构件抽查10%,且不应少于3件;被抽查构件中,每种焊缝按条数抽查5%,且不应少于1条;每条检查1除,总抽查数不应少于10处。
4、焊缝内部探伤(射线、超声)(强制检验项目)
设计要求全焊透的一级或二级焊缝需要进行超声波探伤进行内部缺陷的检验,超声波探伤不能对缺陷作出判断时,应采用射线探伤。
(1) 依据标准:
《钢结构工程施工质量验收规范》GB50205-2001
(2) 取样方法及数量:
每种类型焊缝按条数抽检3%,并不少于3条焊缝。
探伤长度不应小于200mm。
焊 缝 质 量 等 级一 级二 级
内部缺陷
超声波探伤评定等级ⅡⅢ
检验等级B级B级
探伤比例100%20%
内部缺陷
射线探伤评定等级ⅡⅢ
检验等级AB级AB级
探伤比例100%20%
注:
探伤比例的计数方法应按以下原则确定:
(1)对工厂制作焊缝,应按每条焊缝计算百分比,且探伤长度应不小于200mm,当焊缝长度不足200 mm时,应对整条焊缝进行探伤;
(2)对现场安装焊缝,应按同一类型、同一施焊条件的焊缝条数计算百分比,探伤长度应不小于200 mm,并应不少于1条焊缝。
二、紧固件连接质量
1、高强度螺栓终拧扭矩检测(强制检验项目)
高强度大六角头螺栓连接副终拧完成1h后、48h内应进行终拧扭拒检查。
当扭剪型高强度螺栓的梅花头未拧掉时,也要进行终拧扭拒检查。
(1) 依据标准:
《钢结构工程施工质量验收规范》GB50205-2001
(2) 取样方法及数量:
按节点数抽检3%,