第二节 全合成工艺原理 全合成工艺是指由结构较简单的化工原料.docx
《第二节 全合成工艺原理 全合成工艺是指由结构较简单的化工原料.docx》由会员分享,可在线阅读,更多相关《第二节 全合成工艺原理 全合成工艺是指由结构较简单的化工原料.docx(13页珍藏版)》请在冰豆网上搜索。
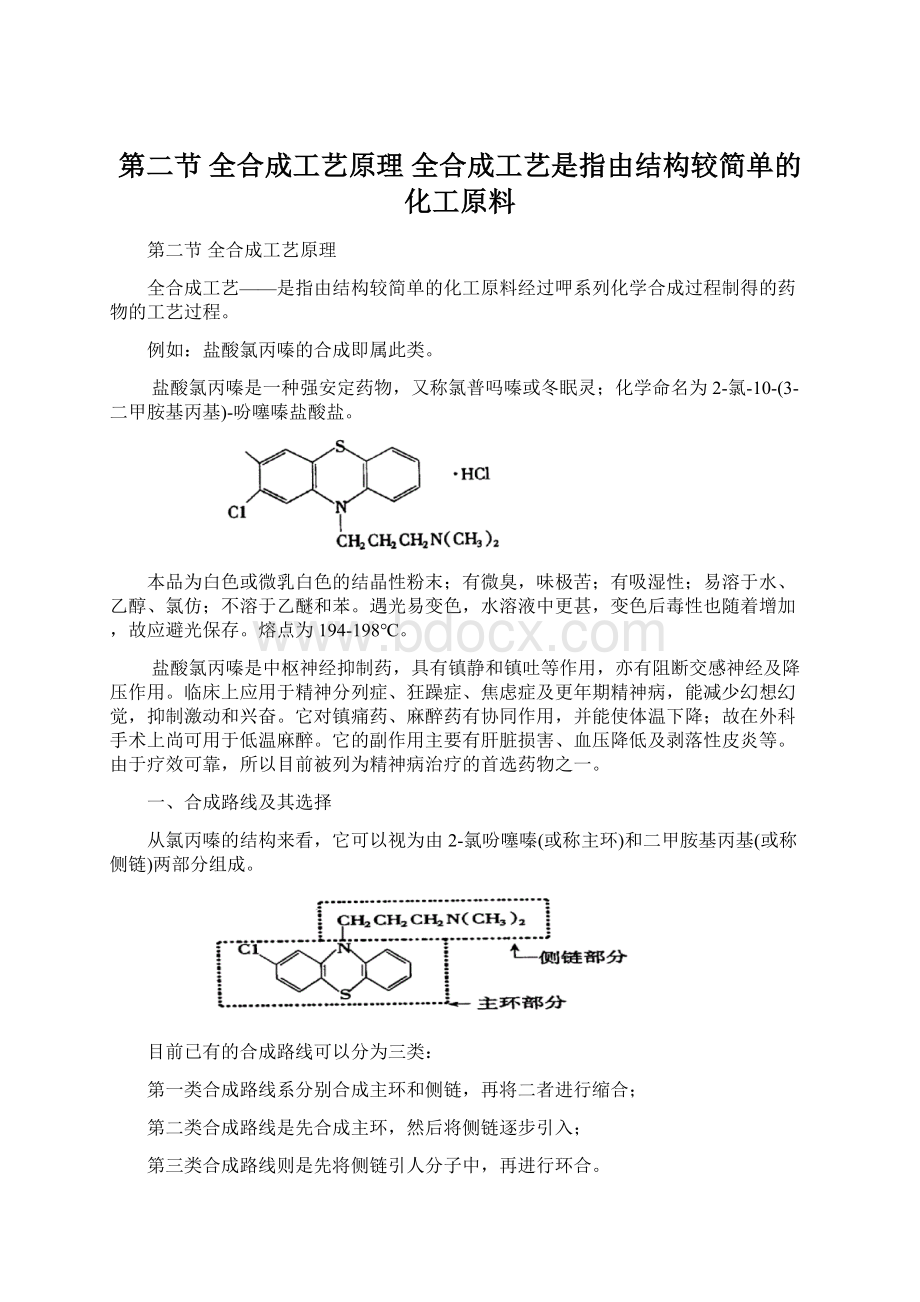
第二节全合成工艺原理全合成工艺是指由结构较简单的化工原料
第二节全合成工艺原理
全合成工艺——是指由结构较简单的化工原料经过呷系列化学合成过程制得的药物的工艺过程。
例如:
盐酸氯丙嗪的合成即属此类。
盐酸氯丙嗪是一种强安定药物,又称氯普吗嗪或冬眠灵;化学命名为2-氯-10-(3-二甲胺基丙基)-吩噻嗪盐酸盐。
本品为白色或微乳白色的结晶性粉末;有微臭,味极苦;有吸湿性;易溶于水、乙醇、氯仿;不溶于乙醚和苯。
遇光易变色,水溶液中更甚,变色后毒性也随着增加,故应避光保存。
熔点为194-198℃。
盐酸氯丙嗪是中枢神经抑制药,具有镇静和镇吐等作用,亦有阻断交感神经及降压作用。
临床上应用于精神分列症、狂躁症、焦虑症及更年期精神病,能减少幻想幻觉,抑制激动和兴奋。
它对镇痛药、麻醉药有协同作用,并能使体温下降;故在外科手术上尚可用于低温麻醉。
它的副作用主要有肝脏损害、血压降低及剥落性皮炎等。
由于疗效可靠,所以目前被列为精神病治疗的首选药物之一。
一、合成路线及其选择
从氯丙嗪的结构来看,它可以视为由2-氯吩噻嗪(或称主环)和二甲胺基丙基(或称侧链)两部分组成。
目前已有的合成路线可以分为三类:
第一类合成路线系分别合成主环和侧链,再将二者进行缩合;
第二类合成路线是先合成主环,然后将侧链逐步引入;
第三类合成路线则是先将侧链引人分子中,再进行环合。
(一)分别合成主环和侧链的路线
在第一类合成法中,主要的问题:
——是选用什么方法合成主环以及选用何种侧链试剂。
主环的合成方法很多,根据它的结构可以看出它可以由二苯硫醚类化合物制得;也可以由二苯胺类化合物制得。
由二苯硫醚类出发的合成路线有氮烯(nitrene)路线、Smiles重排法及Ullmann缩合法等三种;而由二苯胺类出发的合成路线主要是通过Ullmann反应及其类似的缩合反应进行的。
1.通过二苯硫醚类化合物的合成路线
(1)通过氮烯的主环合成法
这方面的合成路线有二个,一是先合成2-氨基4-氯二苯硫醚(26),后者进行重氮化、Sandmeyer反应制得叠氮化合物(27)。
叠氮化合物经分解产生氮烯化合物(28);而闭环而成主环(29)。
也可以由上法中的2-硝基4-氯二苯硫醚(25),经亚磷酸三乙酯还原诱发生成氮烯(28),经环合而成主环(29)。
通过氮烯的主环合成方法,它的特点是反应步骤较短,但原料供应不方便;硫酚还具有恶臭;此外收率也不及目前的生产方法,所以工业上没有采用。
(2)通过Smiles重排法的主环合成法
本法是由邻氨基硫酸(30)和2,4-二氯硝基苯(31)作用生成2-氨基-2'-硝基-5'-二苯硫醚(32),经乙酰化生成乙酰衍生物(33),经Smiles重排以获得主环。
通过Smiles重排所得的主环质量较好,但收率较低,原料供应不方便,需要自制,所以生产上未采用此法。
(3)通过Ullmann缩合反应的主环合成法
这条路线步骤较长,原料供应不易,收率也不高,因此也难以用在生产上。
以上三种主环合成法都是通过二苯硫醚类化合物来进行的,它们都有收率低,原料供应不便的缺点;并且大多数路线的反应步骤较长,因此限制了它们在工生产中的应用。
2.由二苯胺类出发的合成路线
这一类路线几乎都是经过Ullmann缩合反应来进行的,重要的有三种。
(1)先将邻氯苯甲酸(36)和间氯苯胺(35)在铜粉或铜盐的催化下经Ullmann反应制得3-氯-2,-羧基二苯胺(37),再在铁粉催化下经高温脱去羧基即得3-氯二苯胺(38),再在碘催化下,经升华硫作用,进行硫化环合,即可得到主环(39)。
实验发现,反应中尚有少量4-氯异构体生成(40),并留在反应母液中,母液可反复套用多次以提高收率。
脱羧反应和硫化环合反应的条件并不相互抵触,因此也尝试将此二步反应于一步完成,并取得成功。
(2)上法中的邻氯苯甲酸如用2,4-二氯苯甲酸代替(42),间氯苯胺以苯胺代替(41),也能按上法合成主环。
(3)上二法中所用的氯代苯甲酸分子中的羧酸基在反应中起活化氯原子的作用,反应后得设法除去,如用活性较强的溴,则可直接使用溴苯而不必用邻溴苯甲酸,但反应不易控制,容易产生各种各样的副产物。
为了使反应正常进行,间氯苯胺的氨基必须先行乙酰化保护。
使用溴苯的路线如下。
上述三种方法各有特点:
第
(1)种方法原料供应较为充足,邻氯苯甲酸为一综合利用产品,各步收率较为理想,特别是最后一步环合反应采用母液套用方法后,收率可达80%以上,所以本法已为国内生产所采用;但套用母液常会影响主环质量,从而影响产品
的收率和质量,所以操作、后处理要仔细,以保证主环质量。
在第
(2)种方法中,使用2,4-二氯苯甲酸和苯胺有其优点。
在Ullmann反应中,芳胺是作为亲核试剂参加反应的,芳环上的氯是吸电子基团,因此苯胺的亲核能力要比间氯苯胺强,而2,4-二氯苯甲酸的2-位氯也受4-位氯及羧酸基团的影响,它的亲核能力也稍大于邻氯苯甲酸,因此2,4-二氯苯甲酸和苯胺间的反应能力要比邻氯苯甲酸和间氯苯胺间的反应能力要强,收率也相应要高一些,并且苯胺的供应也较间氯苯胺充裕。
缺点是2,4-二氯苯甲酸一般需要自行制备,成本要比邻氯苯甲酸为高,在间氯苯胺供应紧张时,可以考虑作为一条备用路线。
第(3)种方法需用溴苯,间氯苯胺要经过乙酰化,因此生产成本和原料供应均不及前二法,并且收率也不高。
国外曾用本法生产过,国内也曾做过些工作,本法可以说是一条已被淘汰的路线。
至于能和主环缩合形成侧链的试剂很多,一般均是N,N-二甲胺基丙基的衍生物;形成侧链的反应可由下列通式表示之。
-OC00C2H5,-0CON(CH3)2。
也可以用[(CH3)2NCH2CH2CH20]2CO作为缩合试剂。
反应时常以芳烃类化合物如苯、甲苯、二甲苯或乙醚为溶剂,并在碱性缩合剂如氢氧化钠、氨基钠、丁基锂存在下进行。
当用二甲胺基丙[(CH3)2NCH2CH2CH20H)作试剂时,则需用对甲苯磺酰氯和氢氧化钠为缩合剂。
这很可能先生成二甲胺基丙醇的对甲苯磺酸酯,再在碱性条件下和主环缩合而成产品。
在生产上则选用N,N---甲胺基氯丙烷作为侧链试剂,这是因为它很容易从N,N-二甲胺基丙醇进行氯化制得,用氯化亚砜作为氯化剂试,它的合成路线如下:
(CH3)2NH+CH2=CHCH20HNaOH(CH3)2NCH2CH2CH20HSOCl2
(CH3)2NH+CH2=CHCH2Cl·HclOH-(CH3)2NH+CH2=CHCH2Cl
(二)先合成主环而后逐步引入侧链的路线
这类合成法国外曾应用过,但无显著优点。
(二)先引入侧链而后再进行环合的路线
在这类合成路线中,侧链在主环合成前就已引入分子中,可由下列二例作为代表来说明:
上述这类合成法在理论上虽是可行的,但如在例1中,把用升华硫进行环合放在最后一步,很难保证产品质量;而在例2中,原料及中间体供应并不容易,因此这类合成法很难应用到生产上去。
根据以上讨论,目前国内选用的合成路线系从邻氯苯甲酸出发,经与间氯苯胺缩合制成3-氯-'2'-羧基二苯胺,经高温铁粉催化脱羧得到3-氯二苯胺,再经碘催化环合即得2-氯吩噻嗪。
另外以丙烯醇为原料在氢氧化钠的催化下与二甲胺反应,得到N,N—二甲胺基丙醇,后者以氯化亚砜处理即可获得侧链(N,N-二甲胺基-3-氯丙烷)。
侧链在甲苯溶液中以氢氧化钠为缩合剂对主环(2-氯吩噻嗪)进行烃化反应即得氯丙嗪。
再在无水异丙醇中通干燥氯化氢制成氯丙嗪盐酸盐。
最后经过滤、洗涤、干燥,即可获得产品。
这条反应路线步骤较少,总收率较高,约在45%以上,原料供应也方便,所以为生产所采用。
二、2-氯吩噻嗪的生产工艺原理及其过程
(一)3-氯-2,-羧基-二苯胺的制备
1.工艺原理
邻氯苯甲酸(Ⅰ)和间氯苯胺(Ⅱ),在氢氧化钠存在下,以铜粉为催化剂进行缩合反应,可以得到3-氯-2’-羧基二苯胺(Ⅲ)。
邻氯苯甲酸(Ⅰ)和间氯苯胺(Ⅱ)的反应一般简称为芳胺化反应,又称Ullmann反应。
反应产物经脱羧后可得3-氯二苯胺(Ⅲ),供环合制备主环。
邻氯苯甲酸供应方便,并且由于羧基的影响,分子中氯原子比较活泼,收率也比较高。
如单从产品的结构要求来看,其分子中的羧基是多余的。
但是直接使用氯苯则反应活性不够;若使用活性较强的溴苯,其副反应较多,因此必须使用间氯苯胺的乙酰化衍生物;这样以后还要增加水解步骤;而且溴苯价又较贵。
所以使用邻—氯苯甲酸作为原料还是比较合适的。
这个反应是受铜粉催化的,当没有铜粉存在时,反应几乎不进行,只有加入铜粉反应才会进行;加人的亮黄色的铜粉,不久就转化成绿色的铜盐,所以反应中的催化剂可能是铜离子。
至于反应液为何会转绿,铜怎样会转化成铜离子,这可用铜粉和邻氯苯甲酸间的反应来解释。
这种解释可被反应母液中分出的苯甲酸及以下的实例所证明。
如果催化剂确实是铜离子而不是金属铜粉,那就可以解释生产过程中的一系列问题。
例如在反应开始配料用液碱中和邻氯苯甲酸时,中和液的pH必须在5—6间,如果反应液呈碱性,则铜离子一旦生成也因形成氢氧化铜沉淀而失去催化作用,使反应不能进行。
同时在反应回流过程中用滴加液碱方法中和反应时释出的氯化氢,这时也不可滴得过快,否则会使反应液呈碱性而使反应停止。
既然铜盐是真正的催化剂,那么可不可以不用铜粉而直接用铜盐作催化剂,实验证明是可以的,例如可用硫酸铜代替铜粉来进行Ullmann反应,并且反应中也不会产生副产物苯甲酸。
目前生产上已开始试用硫酸铜作为催化剂了。
从反应来看,间氯苯胺和邻氯苯甲酸作用,有氯化氢释出,所以在反应开始前加入液碱使邻氯苯甲酸成为钠盐,这样就可在反应中不断中和反应释出的氯化氢。
如果不加液碱,则随着反应的进行,反应液的酸度将不断上升,并导致反应产物的树脂化及脱羧等副反应,使收率降低,质量下降。
但是开始时液碱不可以一下子加得太多,因为当液碱用量超过理论量时,反应液初期就呈现强碱性,这样根据上述的理由,致使反应要有一个相当长的诱导期或甚至不反应。
正因为如此,所以生产上采用先投入略少于理论量的液碱,使反应液的pH值为5-6,呈微酸性,再在反应过程中不断补加液碱,使反应液始终保持在最佳的pH值4-5之间,不致使酸度过度上升。
最后反应液采取高温(80℃)酸析,这样可使晶体生长的相对速度大大超过晶核的形成速率,得到大而松的晶体颗粒,避免油状物析出,使便于过滤,洗涤效果也好,这对保证中间体质量有一定好处。
反应所得产品必须用热水反复洗涤,因为反应产物中夹杂有反应副产物苯甲酸以及未起反应的邻氯苯甲酸,作为杂质,这二个化合物在热水中溶解度颇大,可被热水洗掉;而产品3-氯-2,-羧基二苯胺,不论在冷水或热水中均几乎不溶,故用热水反复洗涤,正好可以除去上述这二种杂质。
2.工艺赶程
在反应罐中投入邻氯苯甲酸,再用液碱中和,控制反应液的pH值在5-6之间,务必使反应液不致呈碱性,先加入半量的间氯苯胺,加热到78-80℃,加人第一份催化剂铜粉,升温回流一小时后,反应液的pH即下降至4-5左右,随即加人另外半量的间氯苯胺和第二份催化剂铜粉,并在回流情况下在3h内滴加液碱呈碱性。
3h后再补加第三份铜粉。
加完后,再如上滴加液碱3h,滴完后,回流2h,再补加液碱使反应呈碱性,进行水汽蒸馏回收过量的未起反应的间氯苯胺,然后将料液用水稀释,并在80℃用稀酸(也可利用废酸)进行酸析,至pH2-3,将酸水放走,用热水洗涤,过滤,即得3-氯-2'-羧基二苯胺,可以不必精制,直接供下一步投料用。
(二)3-氯二苯胺的制备
1.工艺原理
上步反应所得的3-氯-2'-羧基二苯胺(Ⅰ)在高温和铁粉催化下脱羧生成3—氯二苯胺(Ⅱ)。
羧酸脱羧的难易,受分子结构的影响颇大,一般羧酸的α位有活性基团存在时,较易脱羧。
例如丙二酸经加热,就可以脱除二氧化碳而成醋酸,但醋酸加热很难进行脱羧而成甲烷。
芳香族羧酸的脱羧又较脂肪族容易些。
对于一些具有芳香性及芳香性杂环羧酸的脱羧,常可由加入铁粉、铜粉、或以铜粉加喹啉作为催化剂而加速。
3-氯-2'-羧基二苯胺(Ⅰ)由于受分子中二苯胺基结构的影响,它的脱羧能力要比苯甲酸强得多,当加热到高温时它就可以脱羧成3-氯二苯胺,但是脱羧温度过高,会产生一系列副反应,影响产品的收率和质量,所以在生产中采用铁粉作催化剂;以降低脱羧温度,提高收率和质量。
3-氯二苯胺(Ⅱ)的质量对于下一步硫化环合反应有一定影响,质量不好的3-氯二苯胺会使下一步合成主环的分批收率下降,产物色泽变深,影响产品质量。
同时主环制备要套用母液,3-氯二苯胺质量不好,还会影响母液套用的次数,这也会使主环总的收率下降。
为了保证质量,在减压蒸取3-氯二苯胺时,真空度要高,并要避免溢料。
好的3-氯二苯胺色淡,即使放置较久也不致引起变色,质量不好的3-氯二苯胺色深且不稳定,稍经放置,颜色即急剧变深,以致不适宜直接作为下步反应的原料。
对于质量不好的3-氯二苯胺(Ⅱ),可以经过水洗,稀碱液洗,水洗,干燥再行真空蒸馏,这样就可以获得质量较好的3-氯二苯胺(Ⅱ)。
2.工艺过程
反应罐中投入3-氯-2'-羧基二苯胺及催化剂铁粉,待内温升到180℃以后,保温1h,使其熔融。
开动搅拌,再加入第二份铁粉,在190-210℃保温4h,此时即有大量二氧化碳逸出。
反应结束后,自然冷却到180℃,分去下层铁粉后,用真空抽人蒸馏罐中进行蒸馏,收集沸点为195-240℃的馏份,直至馏出液颜色发红变深,馏出速度减慢,有烟气出现为止,此时蒸馏即可停止,残液应趁热从罐底放走,所得的间氯二苯胺(Ⅱ)应是澄明,浅黄色(浅黄绿色或微棕色)的油状液体,含量在97~101%为合格。
收率按邻氯苯甲酸计约在72%以上。
(三)2-氯吩噻嗪的制备
1.工艺原理
3-氯二苯胺(Ⅰ)在碘的催化下与升华硫作用生成主环2-氯吩噻嗪(Ⅱ)。
合成吩噻嗪的方法很多,其中由二苯胺衍生物在碘的催化下经硫化环合的制备方法是应用较久,较为实用的方法之一。
反应也可以在没有催化剂的存在下进行,但此时反应温度较高(250—300℃),收率也较低,所得产品的质量也较差,采用碘作催化剂,反应温度一般可降低到120-200℃,收率也明显提高。
除了用碘作催化剂以外,三氯化铝、活性白土、三氯化锑、三氯化铁、碘化铜、碘化硫、碘化氢等也可用来催化合成各种吩噻嗪。
可以说这种反应是受路易氏酸酸性催化的。
碘是一个温和的路易氏酸,目前合成吩噻嗪环大多是用碘作催化剂。
反应可以不用溶剂,但也可以在溶剂中进行。
用吡啶和二甲基甲酰胺往往对反应产生不利的作用,而氯苯、溴苯则效果较好。
有实验证明2—氯吩噻嗪在间二氯苯中进行合成,可以提高收率。
硫化剂除用升华硫以外,还可用氯化硫、五硫化锑、硫代硫酸钠、氯化亚砜等,但这些试剂常会发生各种副反应,如核上氯化等,故不宜使用。
至于有取代基的吩噻嗪,由于环合定位的不同,反应常有异构体产生,如3-氯二苯胺可以生成2-氯吩噻嗪或4-氯吩噻嗪。
据报道4-氯异构体的熔点较2-氯异构体低,溶解度也较2-氯异构体高。
有人曾分离出4-氯异构体的纯晶,但未作进一步的鉴定,有人认为4-氯异构体仅占反应物中的极少部分;有人认为4-氯和2-氯异构体之间有一种动态平衡存在,但是都缺乏足够的证据。
根据后一种看法,提出将反应母液反复套用,使其在反应中抑制4-氯异构体的进一步生成,这样就可提高总的收率。
过量的硫黄对反应是不利的,为使反应收率高、质量好,必须使用过量的3-氯二苯胺;但是3-氯二苯胺的用量过多必然会造成成本增加,但这点可借套用母液来解决。
即在第一批生产中使用新鲜原料时使用大大过量的3-氯二苯胺,反应后过量的3-氯二苯胺留在母液中,在以后套用时,只需加入相当于理论配比的原料,这样就可以使每批反应中的3-氯二苯胺始终保持足够的过量。
一般说在母液套用时,’随着套用次数的增加,所得2-氯吩噻嗪的质量也不断下降。
如果适当控制原料及中间体的质量,加强操作管理,就有可能套用20-40或更多的批号。
2-氯吩噻嗪应是淡黄色或浅银灰色的片状或鳞片状结晶,在空气中暴露过久,颜色就会转绿,并进而发蓝。
这种颜色的变化也是吩噻嗪化合物的一种通性。
而且这种色泽的稳定性也和产品的质量有关,优质的2-氯吩噻嗪即使长久放置,也不致变绿发蓝,而质量差的2-氯吩噻嗪变色较快,并且熔点也剧烈下降,以致不能用于下一步反应,这类绿色物质经研究是由吩噻嗪双分子氧化偶合而生成的,它的结构式经光谱分析、分离及合成等方面的证实确认为:
在碱性条件下这类正离子是不稳定的,很容易转化成红色的吩噻酮化合物。
2.工艺过程
在干燥的反应罐中,投入升华硫黄及对硫过量约60%的3-氯二苯胺,搅拌加热升温,在120℃以下投人摧化剂碘片,并升温至168-172℃,保温30min,冷却30min。
反应过程中反应罐内始终保持负压,不使反应释出的硫化氢气体散人大气中,并用液碱吸收之。
反应结束后,加入溶剂氯苯及活性炭,脱水升温至130℃,并回流1h进行过滤,滤液冷至15℃后,进行甩滤;再用氯苯及酒精洗涤,甩滤,即得产品2-氯吩噻嗪(主环)。
以上是用新鲜原料时的操作法,母液套用时的操作法如下:
将上一次反应母液进行溶剂回收,蒸尽后代替3-氯二苯胺投入反应罐中,然后再补加催化剂碘及接近分子比的升华硫和3-氯二苯胺,以下的操作和上述用新鲜原料时相同,反应所得母液仍按上法加以套用。
平均收率可达80%以上。
三、N,N---甲胺基.3。
氯丙烷的生产工艺及其原理
侧链的生产包括N,N--'甲胺基丙醇制备和侧链制备二个工序。
(一)N,N---甲胺基丙醇的制备
1.工艺原理
丙烯醇(Ⅰ)和二甲胺(Ⅱ)在固体氢氧化钠催化下经高压反应可以得到N,N-二甲胺基丙醇(Ⅲ)。
(CH3)2NH+CH2=CH·CH20H(CH3)2NCH2CH2CH20H
(Ⅱ)(Ⅰ)(Ⅲ)
这步反应是二甲胺对丙烯醇中的双键的亲核加成反应。
它是在高压下进行的,因此操作过程中要特别注意安全。
例如对温度控制要特别小心,当内温到140℃(或内压达140kPa)时就不可再继续加热,防止高温分解,内温超过155℃,压力有突然升高的危险,如果反应中温度上升,内压升到160kPa时,就应停止搅拌,并慢慢地打开安全阀放气,不使内温再行上升。
此外设备要定时检修,定期调换防爆膜,换膜后需经180kPa水压试验。
2.工艺过程
在带搅拌的高压罐内投入粒状烧碱或丙烯醇,冷冻到10℃以下,压人液化的二甲胺,即在120-123℃间保温6h,此时内压在110-120kPa间。
保温完毕后逐步加热使罐内压力上升到130KPa(或内温140℃),停止加热,让其自然升温升压至内压为150kPa(或内温150℃),即开冷却水进行冷却,以后如内温、内压再上升时,可作第二、第三次冷却,直到内温、内压不再上升为止。
反应结束,冷却加水,让粒状烧碱全部溶解后出料,分层,先常压蒸出丙烯醇,后减压蒸出粗氨基醇,再将其中低沸点物常压蒸馏除出,即得中间体二甲氨基丙醇,收率达80%以上。
(二)N-N-二甲胺基-3-氯丙烷的制备
1.工艺原理
N,N-二甲胺基丙醇(Ⅰ)经氯化亚砜处理可以获得侧链N,N-二甲胺基氯丙烷,它的反应方程式如下:
(CH3)2NCH2CH2CH20H+SOCl2(CH3)2NCH2CH2CH2C1·HCl+SO2
(CH3)2NCH2CH2CH2C1·HCl+NaOH(CH3)2NCH2CH2CH2C1+NaCl+H2O
此反应中用氯化亚砜作为氯化剂;此外,也可用氯化氢、氧氯化磷等,但效果不及氯化亚砜好。
反应所得的N,N--'甲胺基氯丙烷(Ⅱ)的甲苯溶液,可直接供下一步反应投料用,游离的侧链性质是不稳定的,久置,特别是温度高时易聚合变质,所以制得的侧链应及时投料,如果短期保存,则以冷冻保藏为好。
侧链的质量和最后产品的质量也有一定的关系,如要提高产品质量,应将侧链溶液精制,即将其甲苯溶液进行减压蒸馏,在蒸馏时,甲苯和侧链几乎同时馏出。
馏出温度要控制适宜,温度过低冷凝效果差,损耗大;温度过高,易分解变质,以50-60℃左右为好。
2.工艺过程
在反应罐中投人溶剂甲苯,搅拌下均匀地滴加N,N-二甲胺基丙醇和氯化亚砜,温度渐渐上升,控制在55-60℃。
于5-6小时内加完,加完后慢慢升温到65℃,开始保温,让其自然升温至95℃(约需4小时),反应结束。
反应时逸出大量二氧化硫和氯化氢气体应用氢氧化钠溶液吸收。
反应液冷却后析出结晶,慢慢加入水使溶解并静置,分取下层水溶液;甲苯层用水洗涤,合并水溶液。
水溶液另加人甲苯,在25℃以下用液碱碱化至PH12,分取甲苯,抽样化验甲苯中N,N-二甲胺基氯丙烷的含量,应在40-50%左右,即可供下一步反应投料,收率约在90%左右。
四、盐酸氯丙嗪的生产工艺及其原理
这部分包括氯丙嗪的制备及盐酸氯丙嗪的制备二步。
(一)氯丙嗪的制备
1.工艺原理
由上述制得的主环(Ⅰ)和侧链(Ⅱ)甲苯溶液可在甲苯中以氢氧化钠为缩合剂进行缩合反应而得氯丙嗪的游离碱(base)(Ⅲ)。
缩合反应的关键首先在于保证中间体的质量,如果主环和侧链的质量不好,得到的氯丙嗪游离碱(Ⅲ)质量就不好,用这种氯丙嗪游离碱(Ⅲ)成盐所得的产品质量极差,经过多次重结晶也很难达到药典规定,而且损耗也大。
如果将这种氯丙嗪游离碱(Ⅲ)进行真空蒸馏精制,则即使在真空度较高的情况下(如为133Pa),也常会发生分解,而产品质量并未得到改进,并且在工厂规模下,当数量较多,设备体积较大时,要达到这样的真空度也是有困难的。
正确的配料比和操作对保证产品的质量也有很大的关系,反应要求侧链过量,如果侧链投料不足,就会使2-氯吩噻嗪(Ⅰ)带人产品中去,使产品质量下降。
如果操作不仔细,反应中所产生的水未能及时蒸掉,也会造成反应产物收率和质量的下降。
2.工艺过程
在反应罐中加入甲苯,湿2-氯吩噻嗪,常压蒸出甲苯,1h后改用减压蒸馏,至蒸干,再加入新鲜甲苯、粒碱,回流脱水1h,直至分水器中基本不再出水为止,然后在6h内滴加侧链,滴完后再保温回流3h,每半小时分水一次,最后半小时分出水量应控制在一个小的范围内,否则要继续保温脱水,最多可延长3h,反应结束后冷却、加水,搅拌、静止分层,分去下层碱水,甲苯层用热水洗涤,再用盐酸提取,提取液再加入甲苯,用液碱进行碱析至pH为12-13,静止分层。
甲苯层通过活性炭过滤,滤后的甲苯溶液用热水洗,再进行减压回收甲苯,即可得到氯丙嗪游离碱,为浅黄色到橙黄色粘稠液体或蜡状固体,必要时可用石油醚精制,收率在90%以上。
(二)盐酸氯丙嗪的制备
1.工艺原理
这是氯丙嗪的游离碱(base)与氯化氢成盐的反应。
反应在无水异丙醇中进行,成盐反应所需的干燥氯化氢气体可由浓盐酸加到浓硫酸中产生并经浓硫酸干燥而得。
无水异丙醇的含水量必须控制在0.5%以下,水分过多,会大大增加氯丙嗪盐酸盐在异丙醇中的溶解度,从而增加损失。
氯化氢通入量颇为重要,如溴甲酚蓝颜色仍为黑蓝色表示氯化氢不足,这会影响产品收率;如转为黄色,则表示已过量,就会影响产品质量。
质量不好的盐酸氮丙嗪主要表现在熔点下降和色泽不合格,后者表现为外观色泽带灰带绿,并且水溶液带微绿色,不能用于针剂。
产品如最后用丙酮洗涤,或改用丙酮-异丙醇作为成盐反应的混合溶剂,对提高产品质量或外观色泽有一定的好处。
氯丙嗪盐酸盐的水溶液遇光较不稳定,易变色并导致毒性增加。
质量越差,稳定性也越差,亦更易变色,所以提高盐酸氯丙嗪的质量是非常重要的。
使氯丙嗪盐酸盐的水溶液变色主要是波长小于400nm的紫外线,可见光部分不会使其变色。
在氮气或空气中变色的情况差不多,因此氧对光分解的影响是不大的。
溶液的