阀体毕业设计.docx
《阀体毕业设计.docx》由会员分享,可在线阅读,更多相关《阀体毕业设计.docx(14页珍藏版)》请在冰豆网上搜索。
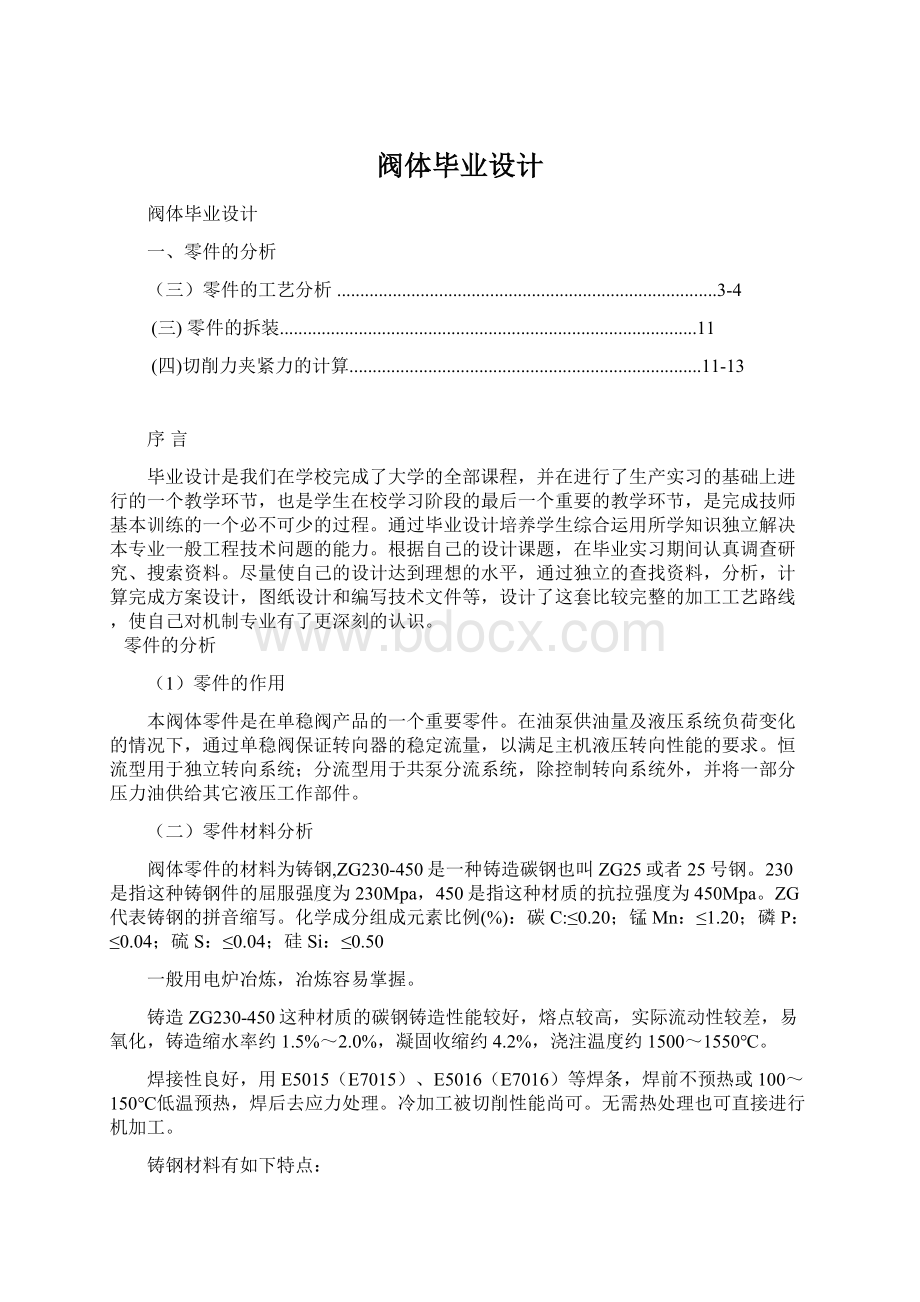
阀体毕业设计
阀体毕业设计
一、零件的分析
(三)零件的工艺分析..................................................................................3-4
(三)零件的拆装..........................................................................................11
(四)切削力夹紧力的计算............................................................................11-13
序言
毕业设计是我们在学校完成了大学的全部课程,并在进行了生产实习的基础上进行的一个教学环节,也是学生在校学习阶段的最后一个重要的教学环节,是完成技师基本训练的一个必不可少的过程。
通过毕业设计培养学生综合运用所学知识独立解决本专业一般工程技术问题的能力。
根据自己的设计课题,在毕业实习期间认真调查研究、搜索资料。
尽量使自己的设计达到理想的水平,通过独立的查找资料,分析,计算完成方案设计,图纸设计和编写技术文件等,设计了这套比较完整的加工工艺路线,使自己对机制专业有了更深刻的认识。
零件的分析
(1)零件的作用
本阀体零件是在单稳阀产品的一个重要零件。
在油泵供油量及液压系统负荷变化的情况下,通过单稳阀保证转向器的稳定流量,以满足主机液压转向性能的要求。
恒流型用于独立转向系统;分流型用于共泵分流系统,除控制转向系统外,并将一部分压力油供给其它液压工作部件。
(二)零件材料分析
阀体零件的材料为铸钢,ZG230-450是一种铸造碳钢也叫ZG25或者25号钢。
230是指这种铸钢件的屈服强度为230Mpa,450是指这种材质的抗拉强度为450Mpa。
ZG代表铸钢的拼音缩写。
化学成分组成元素比例(%):
碳C:
≤0.20;锰Mn:
≤1.20;磷P:
≤0.04;硫S:
≤0.04;硅Si:
≤0.50
一般用电炉冶炼,冶炼容易掌握。
铸造ZG230-450这种材质的碳钢铸造性能较好,熔点较高,实际流动性较差,易氧化,铸造缩水率约1.5%~2.0%,凝固收缩约4.2%,浇注温度约1500~1550℃。
焊接性良好,用E5015(E7015)、E5016(E7016)等焊条,焊前不预热或100~150℃低温预热,焊后去应力处理。
冷加工被切削性能尚可。
无需热处理也可直接进行机加工。
铸钢材料有如下特点:
1.综合机械性能高,抗压强度和本身的抗拉强度相等,消振性能差;
2.壁厚变化对机械性能影响较小,壁厚增大,机械性能不是成正比例增大;
3.铸造性能差,流动性能不好,收缩大,对缺口的敏感性大,因此易产生内应力,变形,开裂,缩孔,缩松等缺陷。
针对以上特点,在加工过程中,要求车削、铣削应尽量减小机械震动,在钻孔加工过程中,也可用钻模钻孔来减小找正和加工震动。
(三)零件的工艺分析
1、零件图样分析
零件图样分析是便于正常掌握零件的外表面轮廓,各部分形状,位置精度及公差,表面粗糙度,定位基准,以及加工前毛坯尺寸的检查等。
正确的零件图形分析能使工人正确的掌握各个部分加工余量,切削用量,进给量,背吃刀量的选择,以及公差尺寸的控制和形状,位置公差的正确把握。
图形分析包括确定零件所需要加工的表面,表面形状,粗糙度值大小等,准确的零件图形分析能使后面的加工工艺过程卡的确定,工序的排列,基准的选择,刀具的选用,切削用量的选择等有很大的帮助。
因此零件图形分析此步骤在整个加工过程中非常重要.。
下面是阀体零件图形的分析结果:
左端表面
这一组加工表面包括:
左端面,Φ50+0.1600孔,Φ43孔,Φ35+0.1600孔及左端平面上的4个M12的螺纹孔。
右端表面
这一组加工表面包括:
右端面,Φ20孔,Φ28.5孔和M36×2mm的外螺纹表面及其倒角
上端表面
这一组加工表面包括:
上端面及其2×45°止口,Φ18+0.1100孔,Φ22+0.130
⊥
0.08
B
表示Φ35孔的低面与横向中心线的垂直度公差是0.08mm
⊥
0.04
B
表示Φ18孔与轴向中心线的垂直度公差是0.04mm0孔,
Φ26孔,Φ24.3内槽孔及M24的内螺纹表面。
现将以上一些主要加工表面的尺寸精度及表面粗糙度分析如表2-1所示:
表2-1加工表面的尺寸精度及表面粗糙度
加工表面
公差等级
表面粗糙度Ra
Φ50
孔
IT11
12.5
Φ35
孔
IT7
1.6
Φ43
IT12
12.5
Φ20
孔
IT12
12.5
Φ28.5
孔
IT12
12.5
Φ18+0.1100孔
IT11
6.3
Φ22+0.1300孔
IT11
6.3
Φ26
孔
IT12
12.5
左、右端面
IT12
12.5
上端面
IT12
12.5
45°±30’’止口
角度公差等级10级
12.5
2、结构工艺性分析
零件结构工艺性的分析,可从零件尺寸和公差的标注,零件的组成要素和零件的整体结构等三方面来阐述。
阀体加工面的标注尺寸是按照加工顺序标注,避免多尺寸同时保证,由形状简单和易接近的轮廓要素为基准标注尺寸,例如,尺寸Φ50-0.180以左端面为标注基准,尺寸7以孔Φ35右端为基准,尺寸15以右端面为标注基准,像这样标注则可以避免不必要的尺寸换算。
对零件组成要素的工艺性分析是对组成零件各加工面的的分析,阀体加工面为端面,台阶面孔,整体形状比较简单,这些能采用普通和标准刀具进行加工,且刀具易进入退出和顺利通过加工表面.加工面和非加工面明显分开,加工面之间也应明显分开。
阀体零件整体结构工艺性这方面主要是:
阀体整体形状无特别处,是通用件,装夹基准可选用Φ40毛坯外圆为装夹基准,还有Φ35孔内壁均可作为装夹基准,通过零件材料的分析,再加上铸造后经过时效热处理,其综合学性能较好,便于切削加工。
1、工艺规程设计
(一)确定毛坯的制造形式
阀体零件最常用的毛坯是铸铁和铸钢,由于毛坯经过铸造后,能使金属内部纤维组织沿表面均匀分布,可获得较高的抗拉、抗弯及抗扭强度,所以一般比较重要的孔大都采用铸件。
阀类零件应根据不同工作条件和使用要求选用不同的材料和不同的热处理,以获得一定的强度、韧性和耐磨性。
此阀体采用ZG230-450,经过调质可得到较好的切削性能,而且能获得较高的强度和韧性等综合力学性能,重要表面经局部淬火后再回火,表面硬度可达45~52HRC。
(二)基面的选择
定位基准是加工中用来使工件在机床或夹具上定位的所依据的工件上的点、线、面。
基准的选择是工艺规程设计中的重要部分,基准选择的合理与否直接影响零件的加工质量,甚至还有可能造成零件的报废,使生产无法正常进行。
按工件用作定位的表面状况把定位基准为粗基准、精基准,以及辅助基准。
在起始工序中,只能选用未经加上过的毛坯表面作为定位基准,这种基准称为粗基准。
用加工过的表面所作的定位基准称为精基准。
1、粗基准的选择
粗基准的选择对工件主要有两个方面的影响,一是影响工件上加工上表面与不加工表面的相互位置,二是影响加工余量的分配。
粗基准的选择原则:
1对于同时具有加工表面和不加工表面的零件,当必须保证不加工表面与加工表面的互为位置时,应选择不加工表面为粗基准。
如果零件上有多个不加工表面,应选择其中与加工表面互为位置要求高的表面为粗基准。
2如果必须首先保证工件某重要表面的加工余量均匀,应选择该表面作粗基准。
3如需保证各加工表面都有足够的加工余量,应选加工余量较小的表面作组基准。
4作粗基准的表面应平整,没有浇口、冒口、飞边等缺陷,以便定位可靠。
5粗基准在同一尺寸方向只允许使用一次。
根据以上原则,又因为阀体的主要加工表面是内孔,而M36外圆是不加工表面,所以选择M36的外圆为粗基准,这样可以保证各加工表面均有加工余量,又使重要孔的加工余量尽量均匀,同时又可以保证经加工后工件壁厚均匀。
2、精基准的选择
选择精基准主要从保证工件的位置精度和装夹方便这两方面来考虑。
精基准的选择原则:
1基准重合原则
.以设计基准为定位基准,避免基准不重合误差,
.调整法加工零件时,如果基准不重合将出现基准不重合误差。
2基准统一原则
.选用统一的定位基准来加工工件上的各个加工表面。
以避免基准的转换带来的误差,利于保证各表面的位置精度,简化工艺规程,夹具设计和制造缩短生产准备周期。
.典型的基准统一原则是轴类零件、盘类零件和箱体类零件。
轴的精基准为轴两端的中心孔,齿轮是典型的盘类零件,常以中心孔及—个端面为精加工基准,而箱体类常以一个平面及平面上的两个定位用工艺孔为精基准。
3自为基准原则
.当某些精加工表面要求加工余量小而均匀时,可选择该加工表面本身作为定位基准,以搞高加工面本身的精度和表面质量。
4互为基准原则
.能够提高重要表面间的相互位置精度,或使加工余量小而均匀。
⑤所选择精基准应能保证工件定位准确,装夹方便,夹具结构简单适用。
根据以上原则,选择阀体的左端面作为精基准,因为他们是阀体的设计基准,这样能够使加工遵循基准重合的原则,同时以加工中心线定位可以加工多处表面,便于在不同的工序中都使用中心线定位,着也符合基准统一原则。
(三)制定工艺路线
方案一:
工序01:
铸造
工序02:
热处理
工序10:
粗车左端外圆
工序20:
粗精左端内孔
工序30:
粗车右端端面
工序40:
粗精外螺纹
工序50:
粗车右端内孔
工序60:
粗车上端面
工序70:
粗车内孔
工序80:
粗车内孔槽
工序90:
精车内孔
工序100:
粗精车内螺纹
工序110:
粗铣上端面
工序120:
钻标记孔
工序130:
扩孔
工序140:
铰孔
工序150:
攻螺纹
工序160:
检验
工序170.上油
工序180.入库
(四)机械加工余量、工序尺寸的确定
阀体零件的材料为铸钢,ZG230-450是一种铸造碳钢也叫ZG25或者25号钢。
230是指这种铸钢件的屈服强度为230Mpa,450是指这种材质的抗拉强度为450Mpa。
根据上述原始资料及加工工艺,分别确定各加工表面的机械加工余量、工序尺寸。
尺寸如下:
1.左端面(φ50
,φ43,35
)
此工序的加工过程为在三爪内装一个固定挡铁,用三爪夹右端外圆粗车左端面保证尺寸12mm至图纸尺寸要求,留工件总长78mm。
粗车内孔φ50mm深5mm和φ43mm深34mm至图纸尺寸要求,粗车内孔φ35mm至尺寸φ34mm40.8mm。
精车内孔φ35mm深41mm至图纸尺寸要求,保证Φ35孔的低面与横向中心线的垂直度公差是0.08mm
表示此道工序内加工精度均较低,最终加工要求IT12,故查表确定粗加工的经济加工精度等级为IT13。
查尺寸公差表确定粗加工各相关尺寸的工序尺寸表示为:
φ43
。
左端面:
余量2mm
Φ50mm孔2Z=8mm
φ43mm孔2Z=4.5mm
Φ35mm孔2Z=0,.5mm
2.右端面
此工序的加工过程为以φ35mm孔和底板定位,底板两边用压板压紧,粗车右端面保证总长75mm至图纸尺寸要求。
粗车螺纹M36X2-6g大径至尺寸φ35.8mm,倒C1.5mm角,粗车内孔φ28.5mm深5mm和φ20mm通孔至图纸尺寸要求
右端面:
余量3mm
Φ20mm孔2Z=1mm
Φ28.5mm孔2Z=4.75mm
M36X2-6g螺纹2Z=1mm
上端面
用底面和φ35mm孔定位,用V形块限制转动,粗车上端面保证尺寸56mm至图纸尺寸要求。
2、钻φ17mm底孔
3、粗车内孔φ26mm深4mm至图纸尺寸要求。
粗车螺纹M24X1.5-7H小径至尺寸φ22.5mm深16mm和φ22mm孔至尺寸φ21mm深29mm,通孔φ18至尺寸φ17.5mm。
精车内孔φ22mm深29mm和通孔φ18mm至图纸尺寸要求,保证轴线与左端面尺寸21±0.04mm。
切内孔槽φ24.3mm深16mm宽3mm至图纸尺寸要求。
车M24X1.5-7H内螺纹深16mm至图纸尺寸要求。
钻孔:
Φ17mm
Φ26mm孔2Z=4.5mm
螺纹M24X1.5-7H小径2Z=2.75mm
φ22mm孔2Z=2.5mm
φ24.3mm内孔槽2Z=3.65mm
Φ18mm孔2Z=0.5mm
(五)确定切削用量
转速n(r/min)的计算公式如下:
n=1000v/πd(5-1)
式中d——刀具(或工件)直径(mm)
V——切削速度(m/min)
工序1
1.车削左端面
(1)查表D取100mm
(2)进给量的确定查表,按工件材料选取,该工步的每转进给量f选为0.7mm/r。
(3)切削速度的计算查表,按工件材料条件选取,切削速度v可取为100m/min。
由公式n=1000v/πd可求得该工序主轴转速n=318.47r/min,参照卧式车床CD6140A主轴转范围,取转速n=350r/min。
再将此转速代入公式可求出该工序的实际切削速度
2.粗车内孔查表D取60mm
(1)查表D取60mm
(2)进给量的确定取f=0.6mm/r
(3)切削速度的计算查表,按工件材料条件选取,切削速度v可取为100m/min。
由公式n=1000v/πd可求得该工序主轴转速n=530r/min,参照卧式车床CAD6140A主轴转范围,取转速n=560/min。
再将此转速代入公式可求出该工序的实际切削速度
3.精车内孔
(1)查表D取40mm
(2)进给量的确定取f=0.4mm/r
(3)切削速度的计算查表,按工件材料条件选取,切削速度v可取为120m/min。
由公式n=1000v/πd可求得该工序主轴转速n=955.41r/min,参照卧式车床CAD6140A主轴转范围,取转速n=1120/min。
再将此转速代入公式可求出该工序的实际切削速度
工序2
1.车右端削面
(1)查表D取40mm
(2)进给量的确定查表,按工件材料选取,该工步的每转进给量f选为0.5mm/r。
(3)切削速度的计算查表,按工件材料条件选取,切削速度v可取为100m/min。
由公式n=1000v/πd可求得该工序主轴转速n=796.1r/min,参照卧式车床CD6140A主轴转范围,取转速n=870r/min。
再将此转速代入公式可求出该工序的实际切削速度
2.粗车外圆
(1)查表D取40mm
(2)进给量的确定取f=0.6mm/r
(3)切削速度的计算查表,按工件材料条件选取,切削速度v可取为100m/min。
由公式n=1000v/πd可求得该工序主轴转速n=796.1r/min,参照卧式车床CAD6140A主轴转范围,取转速n=870/min。
再将此转速代入公式可求出该工序的实际切削速度
3.粗车内孔
(1)查表D取40mm
(2)进给量的确定取f=0.3mm/r
(3)切削速度的计算查表,按工件材料条件选取,切削速度v可取为100m/min。
由公式n=1000v/πd可求得该工序主轴转速n=796.1r/min,参照卧式车床CD6140A主轴转范围,取转速n=870/min。
再将此转速代入公式可求出该工序的实际切削速度
4.车外螺纹
(1)查表D取40mm
(2)进给量的确定取f=2mm/r
(3)切削速度的计算查表,按工件材料条件选取,切削速度v可取为60m/min。
由公式n=1000v/πd可求得该工序主轴转速n=530r/min,参照卧式车床CD6140A主轴转范围,取转速n=560/min。
再将此转速代入公式可求出该工序的实际切削速度
工序3
1.车削上端面
(1)查表D取40mm
(2)进给量的确定取f=0.4mm/r
(3)切削速度的计算查表,按工件材料条件选取,切削速度v可取为100m/min。
由公式n=1000v/πd可求得该工序主轴转速n=796.1r/min,参照卧式车床CD6140A主轴转范围,取转速n=870/min。
再将此转速代入公式可求出该工序的实际切削速度
2.钻孔
钻速350r/min深度35mm
3.粗车内孔
(1)查表D取40mm
(2)进给量的确定取f=0.4mm/r
(3)切削速度的计算查表,按工件材料条件选取切削速度v可取为100m/min。
由公式n=1000v/πd可求得该工序主轴转速n=796.1r/min,参照卧式车床CD6140A主轴转范围,取转速n=870/min。
再将此转速代入公式可求出该工序的实际切削速度
4.精车内孔
(1)查表D取20mm
(2)进给量的确定取f=0.4mm/r
(3)切削速度的计算查表,按工件材料条件选取,切削速度v可取为120m/min。
由公式n=1000v/πd可求得该工序主轴转速n=955.41r/min,参照卧式车床CAD6140A主轴转范围,取转速n=1120/min。
再将此转速代入公式可求出该工序的实际切削速度
5.粗加工内孔槽
(1)查表D取20mm
(2)进给量的确定取f=0.2mm/r
(3)切削速度的计算查表,按工件材料条件选取,切削速度v可取为30m/min。
由公式n=1000v/πd可求得该工序主轴转速n=425r/min,参照卧式车床CAD6140A主轴转范围,取转速n=450/min。
再将此转速代入公式可求出该工序的实际切削速度
6.车内螺纹
(1)查表D取20mm
(2)进给量的确定取f=1.5mm/r
(3)切削速度的计算查表,按工件材料条件选取,切削速度v可取为70m/min。
由公式n=1000v/πd可求得该工序主轴转速n=955.41r/min,参照卧式车床CAD6140A主轴转范围,取转速n=1120/min。
再将此转速代入公式可求出该工序的实际切削速度
2、专用夹具设计
1.定位方案
此工件是以一端面、Φ35孔和零件一侧面为定位基准,采用平面和定位销组合定位方案,在定位平面及定位销的圆柱面上夹紧,其中平面限制3个自由度、短圆柱销限制2个自由度,共限制了五个自由度,然后在侧平面上加一个V形块来限制旋转的自由度,所有六个自由度都被限制了,使零件有了正确的位置。
2.定位误差的分析与计算
定位误差是由基准不重合误差△jb和定位副制造不准确误差△db两部分组成,定位误差的大小事两项误差在工序尺寸方向上的代数和,△dw=△jb±△db
该工件定位方案是采用平面与定位销定位,其定位销与孔的配合采用Ø20H7/f7基孔制配合,其基本尺寸为20mm,公差IT7=0.021mm,因此定位孔与心轴外圆间最小间隙△S=0,在销垂直放置时,定位误差△dw=T1+T2+△S=0.021+0.021+0=0.042mm。
该定位误差小于工件加工要求的1/5—1/3,因此该定位方案是合理的。
3.零件的拆装
用底面和短销的定位,装夹零件用V形块限制转动,装上快换垫圈用螺母夹紧。
拆卸时只要将螺母旋松拿掉快换垫圈就可拿掉零件。
4.切削力与夹紧力计算
铸钢密度为:
7.8g/cm³
平衡力的计算
零件可看作长75mm,宽80mm,高96mm,。
所以
工件重:
d²=3.14X4²=50.24cm²50.24X12.6=633.024cm³
d²=3.14X1.65²=8.55cm²8.55X12.6=107.7cm³
d²=3.14X2.25²=15.89cm²15.89X3.9=61.971cm³
633.024-107.7-61.971=463.353cm³
463.353X7=3243.5g所以工件总重估计为3.25KG
(3)Fc圆周切削分力计算
Ap为切削层的深度Ff为轴向切削力f为每转进给量Kp修正系数
通过《机床夹具设计手册》表1-2-3得公式
902apf
=902X2X1
X0.87=1569.48N
防止工件移动:
Wk=
=
=2774.47N
(4)Fp径向切削分力计算
530ap
f
=530X2
1
=860.44N
防止工件移动;Wk=
=
=1528.1N
(5)Ff轴向切削分力计算
451apf
=451X2X1
X0.87=784.74N
防止工件移动;Wk=
=
=1387.23N
3力的合力为784.74²+1569.48²+860.44²=3819441.332N
=1954.33N
经计算,夹紧力大于切削力,加紧合理。
根据已知工件的扭力,计算平衡块的大小。
本夹具以V形块作平衡块,已知平衡块长42mm,宽15mm,高30mm。
V形块V形口重170x30x85x0.78=338130
V形块缺口重70x200x50x0.78=218400
V形块重210x200x80x0.78—338130—218400=1081420
V形块扭力1081420x92.55x40=4221840000
V形块扭力接近工件扭力,所以,平衡可以。
课程设计心得体会
随着写总结的开始,2013年的的毕业设计将到此结束。
同时也意味着我在宁波技师学院三年学习生涯即将结束。
即将告别校园,步入社会谋求更好的发展。
我不再是学生,而是社会工作者。
未来个人发展要靠自己的双手去缔造。
本次我的毕业设计是对阀体零件夹具的设计,以前我对阀体知之甚少,可经过一个多月的毕业设计,使我对阀体的生产及加工过程进一步的了解。
让我懂得阀体带给我们的不仅是方便,而且对机器起到不可低估的作用。
毕业设计贯穿设计、制造、使用,维护的整个过程,设计时的疏忽总会在这些方面反映出来,成功与否是很容易判断的。
设计的过程中,受制造的影响很大,亦就是说好的设计是不能脱离制造的,对制造越了解,越有助于提高设计水平,通过此次课程使理论和实际结合起来,知识得到进一步巩固、加深和拓展;学习和掌握了机械设计的一般步骤和方法,培养了设计能力和解决实际实际问题的能力。
毕业设计往往离不开自己的阅历,经验的积累固然可以从书本上学到不少,但是事非躬亲很难在脑海中留下深刻的印象,对别人的经验,自己没有一定的基础,要理解吸收真的是一件很不容易的事。
毕业设计过程中,我们了解到一直贯穿这两个特点——质量和速度。
一个企业在生产中没有这两个特点是不能生存下去的。
质量是消费者对产品的要求,速度是企业对谋求利益的要求。
虽然这两点表面上看是相背的,但是一家好的企业要有能力处理好这两点的平衡。
对于加工方面,对于新技术和新想法,也要遵循这个规律。
相信只有简单的模仿,才有最终的创造;只有日积月累,才有最终的从容不迫!
在本次设计中,我非常感谢我的指导老师,由于时间紧促,不妥之处在所难免,恳请老师指教。
相关参考资料
1、《机械加工工艺设计员手册》陈宏钧主编机械工业出版社
2、《机械加工工艺师手册》杨叔子主编机械工业出版社
3、《金属切削手册》第二版上海市金属切削技术协会编
上海科技技术出版社
4、《五金手册》第二版李维荣主编机械工业出版社
5、《机床夹具设计手册》徐鸿本主编辽宁科学技术出版社
6、《金属热处理标准应用手册》全国热处理标准化技术委员会编
机械工业出版社
7、《公差与配合实用手册》方昆凡主编,机械工业出版社