钢板焊接工艺设计说明书.docx
《钢板焊接工艺设计说明书.docx》由会员分享,可在线阅读,更多相关《钢板焊接工艺设计说明书.docx(12页珍藏版)》请在冰豆网上搜索。
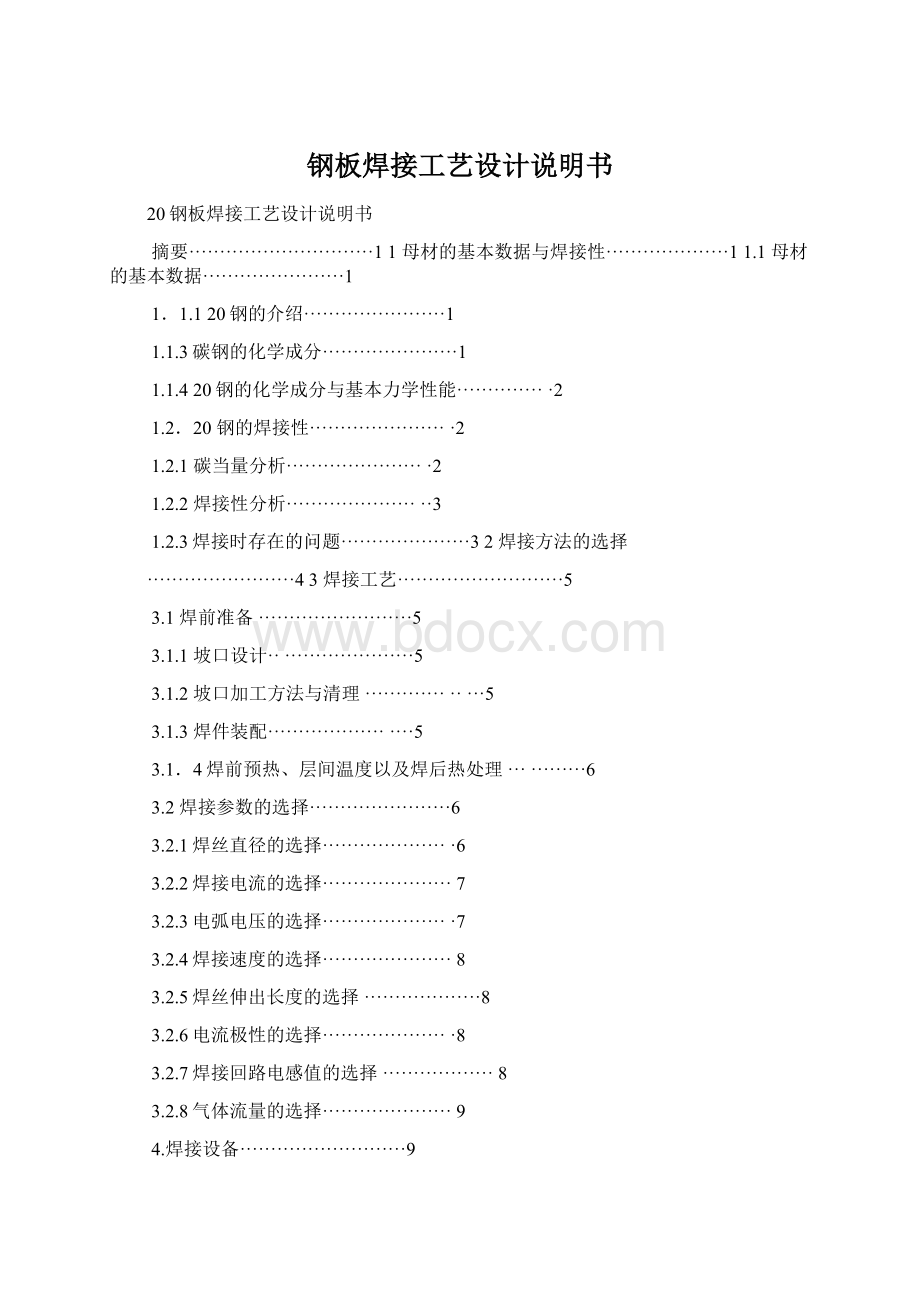
钢板焊接工艺设计说明书
20钢板焊接工艺设计说明书
摘要······························11母材的基本数据与焊接性····················11.1母材的基本数据·······················1
1.1.120钢的介绍·······················1
1.1.3碳钢的化学成分······················1
1.1.420钢的化学成分与基本力学性能···············2
1.2.20钢的焊接性·······················2
1.2.1碳当量分析·······················2
1.2.2焊接性分析·······················3
1.2.3焊接时存在的问题·····················32焊接方法的选择
························43焊接工艺···························5
3.1焊前准备·························5
3.1.1坡口设计·······················5
3.1.2坡口加工方法与清理··················5
3.1.3焊件装配·······················5
3.1.4焊前预热、层间温度以及焊后热处理············6
3.2焊接参数的选择·······················6
3.2.1焊丝直径的选择·····················6
3.2.2焊接电流的选择·····················7
3.2.3电弧电压的选择·····················7
3.2.4焊接速度的选择·····················8
3.2.5焊丝伸出长度的选择···················8
3.2.6电流极性的选择·····················8
3.2.7焊接回路电感值的选择··················8
3.2.8气体流量的选择·····················9
4.焊接设备···························9
5.焊接材料··························101
5.1CO2气体·························10
5.2焊丝··························11
5.2.1焊丝的选择······················11
5.2.2焊丝的质量······················116焊接实施方法及步骤·····················11
6.1引弧
···························11
6.2焊接··························12
6.3收弧··························127施焊时注意事项·······················128.CO2焊常见缺陷、产生原因及特征与预防措施··········129焊后检测··························1410结语····························1411参考文献··························15
2
学生:
若忆江南
指导教师:
燕子
(CMME.CTGU)
摘要:
分析普通低碳钢的焊接性,以常见的低碳钢板(20钢,2-8×100×300)的焊接为例,研究了焊接方法的确定,焊接参数、焊接材料、焊接设备的合理选择;指出了焊接施焊方法、步骤以及注意事项;讨论了焊接缺陷及其预防措施以及焊后检验。
关键词:
低碳钢;薄板;CO2气体保护焊;焊接工艺
1母材基本数据与焊接性
1.1母材的基本数据
1.1.120钢的介绍
碳钢是铁和碳的合金,碳钢中除了以碳作为合金元素外,还有少量的Mn和Si有益元素,还有S、P等杂质。
优质碳素钢的牌号用两位数表示,20钢是优质碳素钢,其w(C)=0.2%。
碳钢是钢材中产量最多,应用最广的材料,被用来制造大部分焊接结构。
1.1.2碳钢按含碳量的分类,如表1。
表1碳钢按含碳量的分类
1.1.3碳钢的化学成分,如表2所示。
表2碳素结构钢的化学成分表
3
1.1.420钢的化学成分与基本力学性能
其化学成分和基本力学性能分别如表3、表4。
表320钢的化学成分表
表420钢的基本力学性能
强度比15号钢稍高,很少淬火,无回火脆性。
冷变形塑性高、一般供弯曲、压延、弯边和锤拱等加工,电弧焊和接触焊的焊接性能好,气焊时厚度小,外形要求严格或形状复杂的制件上易发生裂纹。
切削加工性冷拔或正火状态较退火状态好、一般用于制造受力不大而韧性要求高的。
1.2.20钢的焊接性
1.2.1碳当量分析
由前述20钢的化学成分表计算其碳当量:
Ceq?
C?
?
?
6155?
0.24?
?
?
0615?
0.38
根据一般生产经验,碳当量Ceq<0.40时,淬硬性较小,焊接性良好,焊接时一般不需要预热、控制层间温度或后热(板厚太大时预热);Ceq=0.40-0.60时,淬硬倾向较大,焊性较差,一般需要预热(如钢号:
30、35、45等);Ceq>0.6时,淬硬倾向更严
4
重,焊接性很差,焊前必须采用较高的预热温度,控制层间温度和后热,并采用低氢焊接工艺(如碳素钢铸件、碳素工具钢)。
1.2.2焊接性分析
这里讨论的-8×100×300规格20钢板,由于含碳量低,锰、硅含量也少,所以,通常情况下不会因焊接而产生严重硬化组织或淬火组织。
其焊后的接头塑性和冲击韧度良好,无回火脆性,但淬硬性淬透性较差。
焊接时,一般不需要预热、控制层间温度和后热,焊后也不必采用热处理改善组织,整个焊接过程不必采取特殊的工艺措施,但如果结构件的刚度增大,则焊缝裂纹倾向也增大,焊接刚度大的构件时宜选用低氢焊接工艺,焊前预热,焊后消除应力热处理。
常用低碳钢焊前预热及焊后回火温度见表5。
表5常用低碳钢焊前预热及焊后回火温度
这里讨论的-8×100×300规格20钢板,由于含碳量低,锰、硅含量也少,所以,通常情况下不会因焊接热周期的快速冷却而产生严重硬化组织或淬火组织。
其焊后的接头塑性和冲击韧度良好,无回火脆性,但淬硬性淬透性较差。
因此,在焊接板厚小于70mm的焊件时,焊前不需预热,不必严格保持层间温度除了锅炉压力容器等重要的焊接结构外,一般不需要预热、控制层间温度和后热,焊后也不必采用热处理改善组织,整个焊接过程不必采取特殊的工艺措施,焊接性能优良。
1.2.3焊接时存在的问题
尽管如此,低碳钢当采用高热输入焊接法焊接,或结构件的刚度增大使焊缝裂纹倾向也增大时,以及在其他一些情况下,也会出现各种问题,如:
1)焊缝金属的热裂纹问题。
在直边对接接头的单面或双面埋弧焊中,当母材的w(C)
超过0.20,w(S)大于0.03,且板厚大于16mm时,往往会在焊缝的中心线形成热裂纹。
5
2)液化裂纹问题。
若钢材冶炼质量低劣,存在明显的偏析带,使硫磷等有害杂质含
量局部偏高;当以高热输入焊接时,焊缝熔合区在高温停留的时间较长,如焊接应变速率高于晶体变形能力的增长速度,就会产生液化裂纹。
3)层状撕裂问题在焊接厚度大于60mm的碳钢厚板接头时,如钢材的冶炼质量较差,
存在较多的非金属夹杂物,则在焊接应力较高的接头中,在焊接热影响区或靠近热影响区部位,有时会形成层状撕裂。
此外,某些焊接方法会减低低碳钢焊接接头的质量。
如电渣焊,由于线能量大,回事焊接热影响区的粗晶区的晶粒长得十分粗大,引起冲击韧度的严重下降,焊后必须经行细化晶粒的火处理,以提高冲击韧度。
总之,低碳钢是属于焊接性最好、最容易焊接的钢种,所有焊接方法都能适用于低碳钢的焊接。
2焊接方法的选择
焊接方法必须根据被焊材料的焊接性、接头形式、焊接厚度、焊缝空间位置、焊接结构特点及工作等多方面因素考虑后予以选择确定。
焊接方法的选择原则是在保证产品质量条件下,优先选择常用的焊接方法。
20钢是焊接性良好的钢种,所以各种方法都能应用,如手工电弧焊、埋弧焊、CO2气体保护焊、电渣焊、气焊、电阻焊、氩弧焊、钎焊等。
其中常用的是手工电弧焊、二氧化碳气体保护焊、氩弧焊、埋弧焊等。
CO2气体保护焊具有焊接生产率高、成本低、变形量小、质量高等优点,适用范围广等特点,初不适于焊接焊接容易氧化的有色金属及其合金外,可以焊接碳钢和合金结构钢构件,甚至用于焊接不锈钢也去的了较好的效果,在许多金属结构的生产中已经逐渐取代了焊条电弧焊和埋弧焊,在汽车制造、机车和车辆制造、化工机械、矿山机械部门得到广泛的应用。
这里优先选用常规的实心焊丝半自动CO2气体保护焊。
CO2气体密度较大,隔离空气、保护焊接区的效果十分良好,CO2气体保护焊的工艺特点:
1)CO2电弧穿透能力强,焊丝熔化率高,生产率可比手工焊高1-3倍;
2)CO2气体保护焊的成本只有埋弧焊和手工电弧焊的40%-50%;
3)抗锈蚀能力较强,焊缝含氢量低。
4)合金元素烧损严重;
5)金属飞溅增加;
6)引起CO气孔。
解决上述问题的途径是用含有Si、Mn、Al等脱氧元素的焊丝。
6
3焊接工艺
3.1焊前准备
焊前准备包括坡口设计、坡口加工、清理焊件、装配等。
3.1.1坡口设计
CO2焊采用细滴过渡时,电弧穿透力较大,熔深较大,容易烧穿焊件,所以坡口开得要小些,钝边适当大些,对接间隙不能超过2mm.如果用直径1.6mm的焊丝,钝边可留4~6mm,坡口角度可减小到45°左右。
板厚小于12mm的板材开I形坡口。
图1坡口形式
3.1.2破口加工方法与清理图2接头形式
破口加工的方法主要有机械加工、气割和碳弧气刨等。
CO2焊时对坡口精度的要求比焊条电弧焊高。
焊定位焊缝之前应将坡口周围10~20mm范围内的油污、铁锈、氧化皮及其他赃物去除,否则影响焊件质量。
6mm一下板上的氧化膜对质量几乎无影响;焊厚板时,氧化皮能影响电弧稳定性,恶化焊缝成形及生成气孔。
为了去除氧化皮中的水分和油类,焊前最好用气体火焰烤一下,但要充分加热,否则,在焊件冷却时会生成水珠。
它进入坡口间隙反而会造成相反效果。
为了防锈,许多钢板表面都涂有油漆,焊接时不一定都要除去,要看对焊缝有无影响,有影响的涂料一定要出去,没有影响的(如底料)可以不除去。
3.1.3焊件装配
主要有定位焊和使用夹具两种方法。
定位焊缝是为了装配和固定焊件上的接缝位置而进行的焊接。
定位焊缝本身易产生气孔和夹渣,也是导致随后焊接时产生气孔和夹渣的主要原因,所以必须认真的进行定位焊缝的焊接。
定位焊缝尽可能使焊缝分布在焊缝的背面,当背面难以施焊时,可以在正面焊一条短焊缝,再焊时该处就不必再焊接。
装配是为了防止焊接变形和维持预定的坡口,装配质量对焊接质量有很大的影响,,一般小尺寸的规则零件采用夹具装配。
使用夹具定位时,应考虑磁偏吹的问题。
根据采用的坡口形式与接头形式,对-8×100×300的装配,采取简单的方法,直接在焊接平台上装配好后用重块压住即可,焊完一侧之后彻底清根,再翻身焊接另一侧。
7
图3焊件装配示意图(搁置于焊接平台上)
3.1.4焊前预热、层间温度以及焊后热处理
由对焊接性的分析及表5可知,不需要焊前预热、焊后热处理,由于采用I形坡口双面焊,不需要控制层间温度。
3.2焊接参数的选择
CO2焊的焊接参数较多,主要包括焊接电流、电弧电压、焊接速度、焊丝直径、焊
丝伸出长度、电流极性、焊接回路电感值和气体流量等。
由于碳钢和低合金钢的二氧化碳保护焊接在实际工程中的应用较多,已有比较成熟的焊接参数经验组合,现截取文献中推荐的焊接参数如表6[1]?
[2]:
表6水平对接
3.2.1焊丝直径的选择
下面将依据此表并具体结合本文讨论的规格钢板选取焊接工艺参数。
厚度为1-4mm时,应采用直径0.5—1.2mm的焊丝。
厚度大于4mm时,应采用直径大于或等于1.6mm的焊丝。
直径为1.6mm和2.0mm的焊丝可用于短路过渡和细颗粒过渡焊接,而直径大于2.0mm的焊丝只能用于细滴过渡焊接,焊丝直径的选择见表7。
8
这里,板厚为8mm,则应选直径大于或等于1.6mm的焊丝,又因为焊丝直径的为1.6mm时,短路过渡不适用于平焊,故,根据表7的最后一行,应采用直径1.6mm焊丝,细滴过度。
3.2.2焊接电流的选择
焊接电流的作用是熔化焊丝和工件,同时也是决定熔深的最主要因素。
焊接电流的使用范围随焊丝直径和熔滴过渡形式的不同而不同。
焊丝直径为1.6mm且短路过渡时,
应选用焊接电流小于200A,能得到飞溅小成形美观的焊道。
细颗粒过渡的焊接电流选用在350A以上,能得到熔深较大的焊道,常用于厚板焊接。
焊接电流的选择可参照表8。
可见,按表8选取焊接电流并参照表6,讨论的钢板厚度不大,为防止烧透,将表6中的电流值在保证熔滴过渡形式的条件下适当减小选取焊接电流依次为340A和350A。
3.2.3电弧电压的选择
电弧电压是焊接参数中很重要的一个参数。
电弧电压的大小决定了电弧的长短和熔滴的过渡形式,它对焊缝成形、飞溅、焊接缺陷以及焊缝的力学性能有很大的影响、电弧电压对焊接过程和对金属与气体间的冶金反应的影响均比焊接电流大,且随着焊丝直径的减小,这种影响程度增大。
实现短路过渡的条件之一是保持较短的电弧长度,即低电压。
但电弧电压过低,电弧引燃困难,焊丝会插入熔池,使得电弧不能稳定燃烧;若过高,则短路过渡转变为粗滴的长弧过渡,焊接过程不稳定。
为获得良好的工艺性能,应选择最佳的电弧电压值,该值是一个很窄的区间,一般只有1-2V的范围。
其选择见表9。
表9常用焊接电流及电弧电压的适用范围
9
和34V。
按表选取焊接电弧电压,由于其对熔深的影响较小,可按照表6选取,即分别为33.5V
3.2.4焊接速度的选择
主要依据生产效率和焊接质量来选择。
速度过快,保护效果差,同时使冷却速度加快,使焊缝塑性降低,且不利于焊缝成形,易咬边;速度过慢,熔敷金属在电弧下堆积,电弧热和电弧力受阻,焊道不均匀,焊缝组织粗大。
实际生产中,焊速不超过0.5m/min,即30m/h,再考虑到钢板较薄,不易选择过大的焊速,取27m/h。
另外,根据接头和坡口尺寸、焊接速度、焊丝直径、及焊接层数,可以在此估计送丝速度——认为装配前坡口的体积约等于焊接熔敷金属即焊丝的体积,则可得所需焊丝的长度约等于
3.2.5焊丝伸出长度的选择
由于短路过渡时采用细丝,因而在在焊丝伸出长度上产生的电阻热很大,成为焊接参数中不可忽视的因素。
在其他焊接参数一定的情况下,焊丝伸出长度增大,焊接电流下降,熔深也减小;焊丝上的电阻热也增大,有利于熔化焊丝,从提高生产效率来看是
10
焊接所需时间
L1?
8?
100?
1.5
?
10?
3m
3.14
?
1.624
100?
10?
3
T1?
2?
h
27
v1?
L1
?
80m/hT1
因此,焊机的送丝速度约为
有利的。
但过大,焊丝容易发生过热而成段熔断,飞溅严重,影响焊接质量。
另外气体保护效果也变差。
过小,会妨碍观察电弧,影响焊工操作。
且易使飞溅堵塞喷嘴,还会使导电嘴过热而夹住焊丝,甚至烧毁导电嘴。
根据生产经验,焊丝伸出长度应为焊丝直径的10—12倍。
这里选取16mm。
3.2.6电流极性的选择
CO2焊主要采用直流反接法。
表10极性的应用范围及特点
选用直流反接。
焊接回路电感主要用于调节电源的动特性,来获得合适的短路电流增长速度di/dt,
3.2.7焊接回路电感值的选择
从而减小飞溅,并调节短路频率和燃烧时间,以控制电弧热量和熔透深度。
焊接回路的电感值应根据焊丝直径和焊接位置来选择。
在短路过渡中,熔滴过度周期短,需要较大的di/dt,应选择较小的电感值;粗焊丝焊时熔化慢,熔滴过渡周期长,则需要较小的di/dt,需要较大的电感值。
另外,在平焊位置焊接时要求短路电流增长速度di/dt比立焊和仰焊时低些。
焊接回路的电感值的选择见表11。
表11焊接回路电感值的选择
3.2.8气体流量的选择
CO2气体流量的大小主要是根据对焊接区域的保护效果来决定。
在焊接电流较大、焊接速度较快、焊丝伸出长度较长以及在室外作业等情况下,气体流量要适当加大,以
因此这里选择细滴过渡的第四行,0.4~0.8mH。
11
使气体有足够的挺度,提高其看干扰能力。
保护气流量越大。
焊接速度,焊丝干伸长越大,保护气流量越大。
内角焊比外角焊保护效果好,保护气流量应取下限。
气体流量过大或者过小,都将影响保护效果,容易造成焊接缺陷。
气体流量的选择见表12。
表12
选用粗丝CO2焊的CO2流量,取20L·min-1。
至此,焊接参数已全部选毕,整理于后页表14。
4.焊接设备
CO2半自动焊设备由以下几部分组成:
焊接电源、控制系统、送丝系统、焊枪和气路系统等。
半自动焊机的主要特点是自动送进焊丝,而焊枪的移动则是靠手工操作。
在实际生产中,CO2焊设备以半自动焊为主。
查有关资料[2]可知,NBC—400A半自动CO2焊机用来焊接厚度2mm以上的低碳钢、低合金钢。
其基本参数如下表13。
[2]
12
5.焊接材料
CO2焊用的焊接材料主要指CO2气体、焊丝。
5.1CO2气体
纯CO2气体是无色,略带有酸味的气体。
密度为1.97kg/m3,比空气重。
在常温下把CO2气体加压至5~7Mpa时变为液体。
常温下液态CO2比较轻。
在0℃,0.1Mpa时,1kg的液态CO2可产生509L的CO2气体。
焊接用CO2气体应该有较高纯度,一般技术标准
规定(体积分数)是:
O2<0.1%,H2O<(1―2)g/m,CO2>99.5%。
焊接时焊接前应放
出一部分气体,检查其是否潮湿。
瓶装CO2气体,采用40L标准钢瓶,可灌入25kg液态的CO2,约占钢瓶的80%,基余20%的空间充满了CO2气体。
在0℃时保饱各气压为
3.63Mpa;20℃时保饱各气压为5.72Mpa;30℃时保饱各气压为7.48Mpa,因此,CO2气瓶要防止烈日暴晒或靠近热源,以免发生爆炸。
气瓶中的压力降到1Mpa时,应停止用气。
CO2气体纯度对焊缝金属的致密性和塑性有很大影响。
CO2气体中的主要杂质是H2O和N2,其中H2O的危害较大,易产生H气孔,甚至产生冷裂缝。
3
5.2焊丝
5.2.1焊丝的选择
CO2气保护焊必须含有足够含量的Mn、Si等脱氧元素,以减少焊缝金属中的含氧量和防止产生气孔。
而且焊丝的含碳量要低,通常要求w(C)<0.11%,这样可以减少气孔和飞溅,而且焊丝应保证焊缝金属有满意的力学性能和抗裂性能,此外,当要求焊缝金属具有更高的抗气孔能力时,则希望焊丝中还含有固氮元素。
常用焊丝的牌号、化学成分及用途见[1]表8-6.其中H08Mn2SiA焊丝在CO2焊中应用最广。
它有较好的工艺性、能力学性能及抗热裂纹性能,适于焊接低碳钢、屈服点σs<500MPa的低合金钢。
这里选用此焊丝。
表2焊丝牌号H08Mn2SiA的化学成分及用途
5.2.2焊丝的质量
焊丝表面必须光滑平整,不应有毛刺、划痕、锈蚀和氧化皮等,也不应有对焊接性能或焊接设备操作性能具有不良影响的杂质。
焊接合金钢和大厚度低合金钢时,应采用13
机械、化学或加热办法除掉焊丝上的水分和污染物。
焊丝的镀铜层要均匀牢固,用缠绕法检查镀铜层的结合力时,应不出现鳞与剥落现象。
焊丝的挺度应使焊丝均匀连续送进。
6焊接实施方法及步骤
按照焊接工艺进行焊前准备,检查全部连接是否正确,水、电、气连接完毕合上电源,调整焊接规范参数。
6.1引弧
CO2气体保护焊采用碰撞引弧,引弧时不必抬起焊枪,只要保证焊枪与工作距离。
1)引弧前先按遥控盒上的点动开关或焊枪上的控制开关将焊丝送出枪嘴,保持伸出长度10~15mm。
2)将焊枪按要求放在引弧处,此时焊丝端部与工件未接触,枪嘴高度由焊接电流决定。
3)按下焊枪上控制开关,焊机自动提前送气,延时接通电源,保持高电压、慢送丝,当焊丝碰撞工件短路后自然引燃电弧。
短路时,焊枪有自动顶起的倾向,故引弧时要稍用力下压焊枪,防止因焊枪抬起太高,电弧太长而熄灭。
6.2焊接
引燃电弧后,通常采用左焊法,焊接过程中要保持焊枪适当的倾斜和枪嘴高度,使焊接尽可能地匀速移动。
当坡口较宽时为保证二侧熔合好,焊枪作横向摆动。
焊接时,必须根据焊接实际效果判断焊接工艺参数是否合适。
看清熔池情况、电弧稳定性、飞溅大小及焊缝成形的好坏来修正焊接工艺参数,直至满意为止。
6.3收弧
焊接结束前必须收弧。
若收弧不当容易产生弧坑并出现裂纹、气孔等缺陷。
焊接结束前必须采取措施。
焊机有收弧坑控制电路。
焊枪在收弧处停止前进,同时接通此电路,焊接电流电弧电压自动减小,待熔池填满。
若焊机没有弧坑控制电路或因电流小没有使用弧坑控制电路。
在收弧处焊枪停止前进,并在熔池未凝固时反复断弧、引弧几次,直至填满弧坑为止。
操作要快,若熔池已凝固才引弧,则可能产生未熔合和气孔等缺陷。
7施焊时注意事项
电源、气瓶、送丝机、焊枪等连接方式参阅书。
选择正确的持枪姿势:
1)身体与焊枪处于自然状态,手腕能灵活带动焊枪平移或转动。
2)焊接过程中软管电缆最小曲率半径应大于300m/m焊接时可任意拖动焊枪。
3)焊接过程中能维持焊枪倾角不变还能清楚方便观察熔池。
14
3)保持焊枪匀速向前移动,可根据电流大小、熔池的形状、工件熔化情况调整焊枪前移速度,力争匀速前进。
必要时可以根据实际情况调整运条方式,不采用直线运条方式而进行小幅的横向被动以免烧透焊件。
8.CO2焊常见缺陷、产生原因及特征与预防措施
气孔:
1焊接时候卷入空气;2.预热器不起作用;3.焊接区域风大,气体保护不好;
4.喷嘴被飞溅物堵塞,不通畅,喷嘴与工件距离过大;5.焊件表面油污、锈蚀处理不彻底;
6.电弧过长,电弧电压过高;7.焊丝中Si-Mn含量不足。
咬边:
1.电弧过长,电弧电压过高;2.焊接速度过快、焊接电流过大;3.焊工摆动不当。
焊缝成型不良:
1.工艺参数不合适;2.焊丝矫正机构调节不当;3.送丝轮中心偏移;4.导电嘴松动。
电弧不稳:
1.外界网络电压影响;2.焊接参数调节不当;3.导电嘴松动;4.送丝机构、导电嘴堵塞等。
飞溅:
1..焊接电参数调节不匹配;2.气流量过大3.工件表面过于粗糙4.焊丝伸出长度过长。
未焊透:
1.焊接电流太小,送丝不当;2.焊接速度过快或过慢;3.坡口角度太小,间隙过小;4.焊丝位置不当,对中性差;5.焊工技能水平。
15
9焊后检测
(1)焊缝外观检查。
焊缝进行外观检验前,应将妨碍检验的渣皮、飞溅等清理干净。
外观检验可用目测、5~10倍的放大镜及专用检具(如焊口检测器)进行检查。
(2)焊后无损探伤检验。
可采用渗透探伤等方法对焊缝外表面缺陷进行检查。
可采用射线探伤、超声探伤和磁粉探伤等无损伤方法对焊缝内部缺陷进行检验。
射线探伤的方法应符合相应国家标准GB332