数控车工大赛试题设计.docx
《数控车工大赛试题设计.docx》由会员分享,可在线阅读,更多相关《数控车工大赛试题设计.docx(22页珍藏版)》请在冰豆网上搜索。
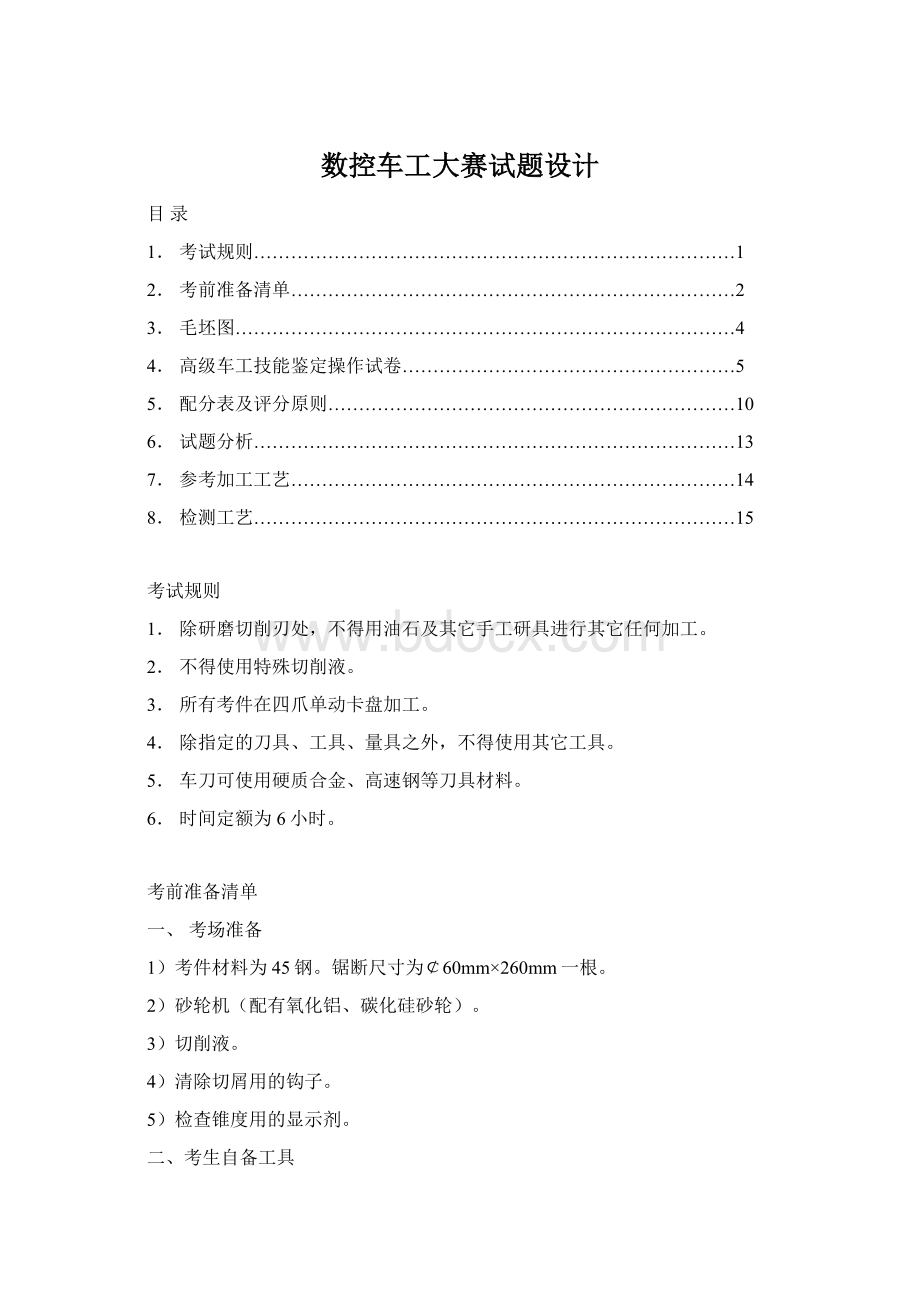
数控车工大赛试题设计
目录
1.考试规则……………………………………………………………………1
2.考前准备清单………………………………………………………………2
3.毛坯图………………………………………………………………………4
4.高级车工技能鉴定操作试卷………………………………………………5
5.配分表及评分原则…………………………………………………………10
6.试题分析……………………………………………………………………13
7.参考加工工艺………………………………………………………………14
8.检测工艺……………………………………………………………………15
考试规则
1.除研磨切削刃处,不得用油石及其它手工研具进行其它任何加工。
2.不得使用特殊切削液。
3.所有考件在四爪单动卡盘加工。
4.除指定的刀具、工具、量具之外,不得使用其它工具。
5.车刀可使用硬质合金、高速钢等刀具材料。
6.时间定额为6小时。
考前准备清单
一、考场准备
1)考件材料为45钢。
锯断尺寸为¢60mm×260mm一根。
2)砂轮机(配有氧化铝、碳化硅砂轮)。
3)切削液。
4)清除切屑用的钩子。
5)检查锥度用的显示剂。
二、考生自备工具
考生自备工具表
序号
名称
规格(mm)
分度值(读数值)(mm)
数量
备注
1
外径千分尺
0~25
0.01
1
2
外径千分尺
25~50
0.01
1
3
外径千分尺
50~75
0.01
1
4
游标卡尺
0~200
0.02
1
不准使用数显和带表的
6
游标深度尺
0~200
0.02
1
7
万能角度尺
0~320°
2′
1
8
钟面式百分表
10
0.01
1
9
杠杆百分表
0.8
0.01
1
10
磁性表座
1
11
螺纹对刀样板
30°、60°
各1
12
量针
d=0.866P
3根
13
内径百分表
18~35
0.01
1
14
内径百分表
35~50
0.01
1
15
外圆车刀
90°
自定
16
端面车刀
45°
自定
17
切断刀
宽3、4、5
自定
18
车槽刀
自定
19
外螺纹刀
60°
自定
20
外螺纹刀
30°
自定
21
内螺纹车刀
60°、M18×1.5长20
自定
不通孔
22
内孔车刀
¢20长50
自定
23
内孔台阶刀
¢20长40
自定
24
内沟槽车刀
¢16长21
1
25
网纹滚花刀
m=0.3(P≈1)
1
26
中心钻
B3.15
2
27
麻花钻
¢16、¢18
各1
28
螺纹通、止规
M18×1.5
各1
29
塞规
6+0.13-0.10
1
30
垫刀片
自定
31
铜皮
0.2~0.3
自定
32
铜垫块
4
33
钻夹头
¢1~¢13
1
34
回转顶尖
莫氏4号
1
35
变径套
莫氏1~4号
1套
36
油石
自定
37
楔铁
1
38
铜棒
1
39
剪刀
1
40
高速钢刀坯
12×12×100
41
活扳手
200、300
各1
42
一字旋具
200
1
43
毛刷
自定
44
内六角扳手
1套
45
计算器
1
46
尺寸公差表
GB1801-79
1
47
螺纹公差表
GB297-81
1
48
划线规
1
49
样冲
1
50
红丹粉
少量
51
划针
1
52
齐头扁锉
200
1
去毛刺用
53
锤子
1
54
机械工人手册
1
配分表及评分原则
一、考核项目评分表
配分系数表
序号
考核项目
配分
备注
1
件1—螺杆轴
20%
2
件2—本体
24%
3
件3—偏心锥体
18%
4
件4—偏心轴
20%
5
偏心螺杆总成
18%
件1—螺杆轴考核项目评分表
序号
考核项目
配分
评分标准
检测结果
得分
1
Tr40×6-7e大径¢400-0.375mm
5
超差全扣
2
Tr40×6-7e中径¢37-0.118-0.453mm
22
超差全扣
3
Tr40×6-7e小径¢330-0.537mm
5
超差全扣
4
大径¢420-0.03mm
5
超差全扣
6
槽6+0.13-0.10mm
5
超差全扣
7
¢36mm±0.015mm
3
超差全扣
8
台阶孔¢25mm×1mm
3
超差全扣
9
M18×1.5配合适中
8
超差全扣
10
M18×1.5表面粗糙度
5
超差全扣
11
内沟槽4mm×2mm
5
超差全扣
12
长度尺寸(1.5分×4处)
6
超差全扣
13
Tr40×6处Ra1.6m(10分×4处)
20
一处不合格扣10分
14
槽12mm×8mm
2
超差全扣
15
表面粗糙度Ra1.6m(1分×1处)
1
超差全扣
16
倒角(1分×5处)
5
一处不合格扣1分
件2—本体考核项目评分表
序号
考核项目
配分
评分标准
检测结果
得分
1
外径¢580-0.03mm
3
超差全扣
2
总长44±0.03mm
3
超差全扣
3
锥度2:
5,锥角允差±7′
6
超差全扣
4
孔¢28+0.0250mm
5
超差全扣
6
孔¢20+0.0210mm
5
超差全扣
7
孔¢20+0.0210mm(横向)
12
超差全扣
8
厚度尺寸44±0.03mm
12
超差全扣
9
15
超差全扣
10
10
超差全扣
11
6
超差全扣
12
孔20+0.0210mm轴线到端面距离23±0.025
8
超差全扣
13
长度尺寸(1.5分×2处)
3
一处不合格扣1。
5分
14
表面粗糙度Ra1.6m(1分×7处)
7
一处不合格扣1。
5分
15
倒角(1分×5处)
5
一处不合格扣1分
件3—偏心锥体考核项目评分表
序号
考核项目
配分
评分标准
检测结果
得分
1
外径¢400-0.025mm
5
超差全扣
2
外径¢280-0.025mm
5
超差全扣
3
孔20+0.0210mm
18
超差全扣
4
孔20+0.0210mm(横向)
23
超差全扣
5
偏心孔¢30+0.0250mm
4
超差全扣
6
偏心距2±0.02mm
4
超差全扣
7
锥度2:
5与件2配,接触面≥60%
10
接触面≥60%得满分,40%~50%得8分,少于40不得分
8
长度尺寸(2分×5处)
10
一处不合格扣2分
9
表面粗糙度Ra1.6m(3分×6处)
18
一处不合格扣4分
10
倒角(1分×3处)
3
一处不合格扣1分
件4—偏心轴考核项目评分表
序号
考核项目
配分
评分标准
检测结果
得分
1
外径¢52mm
5
超差全扣
2
偏心外圆¢30-0.009-0.034mm
20
超差全扣
3
偏心距2±0.02mm
23
超差全扣
4
¢20-0.02-0.04mm
10
超差全扣
6
M18×1.5中径
18
超差全扣
7
槽3mm×1mm
3
超差全扣
8
长度尺寸(2分×4处)
8
一处不合格扣2分
9
表面粗糙度Ra1.6m(2分×2处)
4
一处不合格扣2分
10
倒角(1.5分×6处)
9
一处不合格扣1。
5分
偏心螺杆总成考核项目评分表
序号
考核项目
配分
评分标准
检测结果
得分
1
装配A
10
超差全扣
2
装配B
5
超差全扣
3
50±0.05mm
25
超差全扣
4
A128±0.05mm
20
超差全扣
6
B128±0.05mm
20
超差全扣
7
51±0.05mm
20
超差全扣
监考人员
评分人员
成绩
二、评分原则
1)未注公差尺寸按IT14加工。
2)提前交检不加分。
在分数相同的情况下,优先考虑加工时间短的考生。
3)考虑到各量具之间存在差异和测量误差及机床精度等因素,超差≤0.005mm不扣分,超差0.005~0.015扣该项配分的50%,超差0.015以上不得分。
4)考件与同样严重不符的扣去该件全部配分。
5)严重超差者,如梯形螺纹Tr40×6大径小1mm以上者,配合公差比要求超差0.1mm以上者除扣去该项全部配分外,并扣去该件总分的20%~50%。
视具体情况而定,由评分组判定。
6)每一考件的实得分应等于评分表所得分乘以该件的配分系数。
试题分析
1.根据试件的的装配精度要求,确定考件的加工顺序为件4、件3、件2、件1。
2.要达到装配尺寸50±0.05mm(装配图A),车制考件2锥度为C=2:
5的圆锥孔时,与考件3的外圆锥配合后应达到50±0.05mm。
必要时,在允许的公差范围内可对考件2的左端面及考件3的¢400-0.025mm端面进行修正。
3.要达到装配尺寸128±0.05mm(装配图A),可将考件3的¢400-0.025mm端面放在最后再加工,把考件1、考件2、考件4按装配图A装配并测量出考件4右端面到考件1左端面的长度尺寸L,则在考件3¢400-0.025mm端面处在公差允许范围内进行车制,然后再达到128±0.05mm。
4.要达到装配尺寸51±0.05mm(装配图B),可将考件3和考件2组装后加工横孔¢20+0.0210mm,其加工方法是在考件2的¢28+0.0250mm孔底平面处加一调整垫块,调整垫块的厚度尺寸应根据组装尺寸51±0.05mm而确定。
采用该方法加工还便于装夹及找正¢20-0.02-0.04mm孔的轴线位置并容易达到尺寸23±0.025mm及51±0.05mm。
5.要达到装配尺寸128±0.05(装配图B),应在公差允许范围内进行车制考件4的偏心外圆厚度。
6.车制考件2尺寸44±0.03mm一侧平面时,应测量出外径¢58mm的实际值,并保证轴线到平面的值,而且在精车平面时,必须重新找正。
调头车另一侧平面时,可用一平行垫块,装夹时不已加工的平面与垫块靠平,用尾座顶尖顶住,夹紧、进行粗定位,然后去掉垫块,将杠杆百分表座放在中滑板上,使百分表测量头接触工件已加工表面,移动中滑板,校平已加工平面的跳动量在0.01mm之内,再粗精车另一侧平面,保证尺寸44±0.03mm对称误差不大于0.04mm及两平面的平行度误差不大于0.03mm。
参考加工工艺
一、车考件4—偏心轴
偏心轴的车削工序内容
工序号
工序内容
备注
1
用四爪单动卡盘夹住毛坯¢60外圆
(1)车端面,调整装夹长度,使工件伸出85mm左右
(2)钻中心孔¢3.15mm,用顶尖顶住
(3)粗车外圆¢52mm至¢52.5mm,长度尺寸至75mm
(4)粗车偏心外圆¢30-0.009-0.034mm至¢35mm,长度尺寸至65mm
(5)粗车外圆¢20-0.02-0.04mm,螺纹M18×1.5大径车至¢20.5,长度尺寸59mm
(6)精车外圆¢52mm至尺寸,精车螺纹M18×1.5大径至¢18-0.2-0.3mm,长度尺寸为15mm
(7)车槽3mm×1mm
(8)车螺纹M18×1.5
(9)倒角1×45°
(10)切断,长度尺寸至74mm
2
调头,夹住外圆¢20-0.02-0.04mm找正
(1)车端面,长度尺寸为73mm、8mm
(2)钻中心孔¢3.15mm
(3)滚花
(4)倒角
3
找正偏心轴线
(1)车偏心外圆¢30-0.009-0.034mm,厚度尺寸至6mm
(2)倒角1×45°
二、车考件3—偏心锥体
偏心锥体的车削工序内容
工序号
工序内容
备注
1
用单动四爪卡盘夹住毛坯¢60mm的外圆,使工件伸出55mm左右
(1)车端面,钻中心孔¢3.15mm
(2)钻孔¢18mm,深45mm
(3)车外圆¢400-0.025mm
(4)车外圆¢280-0.025mm保持长度17mm(即17=12+5)
(5)粗、精车孔20+0.0210mm
(6)车锥度为C=2:
5的外圆锥,长度尺寸12mm、5mm
(7)倒角
(8)切断,长度尺寸44mm
2
调头,用四爪单动卡盘垫铜块夹住外圆¢280-0.025mm处,找正偏心轴线
(1)车端面,保证总长尺寸为43mm
(2)车偏心孔¢30+0.0250mm,深度尺寸6mm
(3)孔口倒角
三、车考件2—本体
本体的车削工序内容
工序号
工序内容
备注
1
用四爪单动卡盘夹住毛坯¢60mm的外圆,夹持长度伸出60mm
(1)车端面,钻中心孔¢3.15mm
(2)粗车外圆¢580-0.03mm至¢59mm
(3)钻孔¢18mm
(4)精车外圆¢580-0.03mm
(5)车孔20+0.0210mm,深度尺寸6mm
(6)倒角
(7)切断,保持长度45mm
2
调头,夹住¢580-0.03mm外圆,找正外圆,使径向跳动≤0.01mm
(1)车端面,长度尺寸为44±0.03mm
(2)扩孔至¢26mm,深度尺寸37mm
(3)车孔¢28+0.0250mm,深度尺寸380-0.2mm
(4)车锥度为C=2:
5的圆锥孔小端直径至¢35.6+0.050mm,深度尺寸11mm
(5)车锥度为C=2:
5的圆锥孔,与件3配接触面大于60%,并保证组装尺寸50±0.05mm
(6)倒角
3
与件3组装,在¢28+0.0250mm孔内垫入工艺调整垫块,保证组装尺寸51±0.05mm(必要时可修正考件3的¢400-0.025mm的端面)
用四爪单动卡盘垫铜块夹住外形,,找正对称
(1)车平面,尺寸应根据外圆¢580-0.03mm实测尺寸,计算出轴线到平面值
(2)钻孔¢18mm
(3)车孔¢20+0.0210mm
(4)倒角
4
调头,找正对称尺寸及加工平面跳动值在0.01mm之内
(1)车平面,尺寸为44±0.03mm
(2)倒角
四、车考件1—螺杆轴
螺杆轴的车削工序内容
工序号
工序内容
备注
1
用四爪单动卡盘夹住毛坯¢60mm外圆
(1)车端面
(2)钻中心孔¢3.15mm,用顶尖顶住
(3)粗车外圆至¢41mm,长度尺寸至51mm
(4)粗车槽12mm×8mm
(5)粗车Tr40×6-7e大径至尺寸
(6)精车槽12mm×8mm
(7)倒角2×30°
(8)车梯形螺纹至尺寸
2
调头,夹住Tr40×6-7e处,使径向跳动≤0.03mm
(1)车端面
(2)钻中心孔¢3.15mm
(3)粗车外圆至¢420-0.03mm至¢43mm,粗切槽6+0.13-0.10mm
(4)车端面,保证总长70mm、16mm
(5)钻孔¢15mm,深14mm
(6)精车外圆¢420-0.03mm,槽6+0.13-0.10mm至尺寸
(7)倒角1×45°
(8)车螺纹M18×1.5底孔至¢16.5+0.2+0.1mm,深度尺寸至16mm
(9)车孔¢25mm×1mm
(10)车内沟槽4mm×2mm
(11)车内螺纹M18×1.5,与件4配合无松动
(12)孔口倒角1×45°
检测工艺
一、试件的检验
1.检查尺寸50±0.05mm、128±0.05mm依次将考件1~4按装配图A装配,并作必要的调整。
将件4端面置于测量平板上,用量块组合尺寸与件4长度等高,再用量块组合尺寸50mm,放置在与件4长度等高的量块面上,使杠杆百分表测量头接触量块面,调整百分表指针零位,移动百分表,使之测头与考件2左端面接触,按均匀分布三点进行测量,其百分表读数值应在公差范围内。
检查128±0.05mm时,可用量块组合尺寸128mm,检测方法与上面相同。
2.检查尺寸51±0.05mm、128±0.05mm根据装配图A检测后、拆卸考件,然后依次按装配图B装配,并作必要的调整,检查尺寸51±0.05mm时,可将考件4端面置于测量平板上,检查尺寸128±0.05mm时将件1端面置于测量平板上,检测方法与上面的
(1)相同。
二、考件1—螺杆轴的检验
1.检查梯形螺纹中径尺寸37-0.118-0.453mm根据考生自备工具表中的量针配备,采用三针测量法测量,在测量前先计算出量针测量距M,同时测量出螺纹大径尺寸¢40mm的实际尺寸d0,三针测量值M用下式计算
M=d1+3.924d0-4.316
测量值M的偏差应为中径偏差
2.检查螺纹M18×1.50-7g中径用三针测量法测量。
在测量前查普通螺纹基本尺寸表得中径尺寸为d2=17.026mm;查螺纹公差表得螺纹中径基本偏差为es=-0.032mm,中径公差为Td2=0.18mm。
三、考件3—偏心锥体的检验
1.检查偏心距2±0.02mm把偏心锥体装夹在测量棒上,测量棒与孔的配合间隙适当,并作转向定位,将测量棒装夹在精密V形架上,将杠杆百分表的球形测量头置于外圆上,并与外圆的上素线的一点接触,转动偏心锥体,在回转一周过程中,百分表所指示的最大值与在最小值之差的一半就是该测量截面的偏心距,接上述方法选三个截面进行测量,取其平均值作为偏心距,但当百分表球形测量头与外圆的上素线一点接触时,由于百分表测量杆移动方向和被测表面的垂直方向存在夹角,需将测得值按△测杆=△面/cosα。
△测杆是指测量干的位移量;
△面是指被测表面的变动量,又是指测量杆移动方向与被测表面垂直方向的夹角。
2.检查锥度2:
5(11°18′36″),用分度值为2′的万能角度尺测量值与公称角度值之差视为被测角度误差。
四、考件2—本体的检验
1.检查锥度为C=2:
5的圆锥角允差±7′测量前,查表锥度为C=2:
5的圆锥角α=11°18′36″,圆锥半角α/2=5°24′18″,可用万能角度尺测量。
2.检查锥孔与偏心锥体的接触情况用锥体涂色法检验,先用显示剂在偏心锥体的外圆锥面顺着圆锥素线均匀分布的三条线上涂色,,色层厚度约2~3m,然后将其放入本体的锥孔中(要紧密接触)来回转动,角度不大于60°。
取出偏心锥体观察显示剂擦去的情况是否符合接触面不小于60%的要求。
3.检查位置精度测量前,将平面置于测量平板上,用杠杆百分表找正基准A轴线水平位置(可在平面与平板之间用塞尺调整),并用杠杆百分表测量孔的下素线至平板的距离,然后将考件翻转180°,用上述方法重复测量孔的另一侧下素线至平板之间的距离,两侧测量值之差即为该零件的对称度误差。
四、考件4—偏心轴的检验
1.检查偏心距2±0.02mm测量时,偏心轴以¢20-0.02-0.04mm的轴线为测量基准,装夹在测量架的两顶尖间,用钟面式百分表接触偏心轴的偏心外圆。
在被测偏心套回转一周的过程中百分表指示出的最大值和最小值之差的一半就等于偏心距。