精冲基本知识.docx
《精冲基本知识.docx》由会员分享,可在线阅读,更多相关《精冲基本知识.docx(24页珍藏版)》请在冰豆网上搜索。
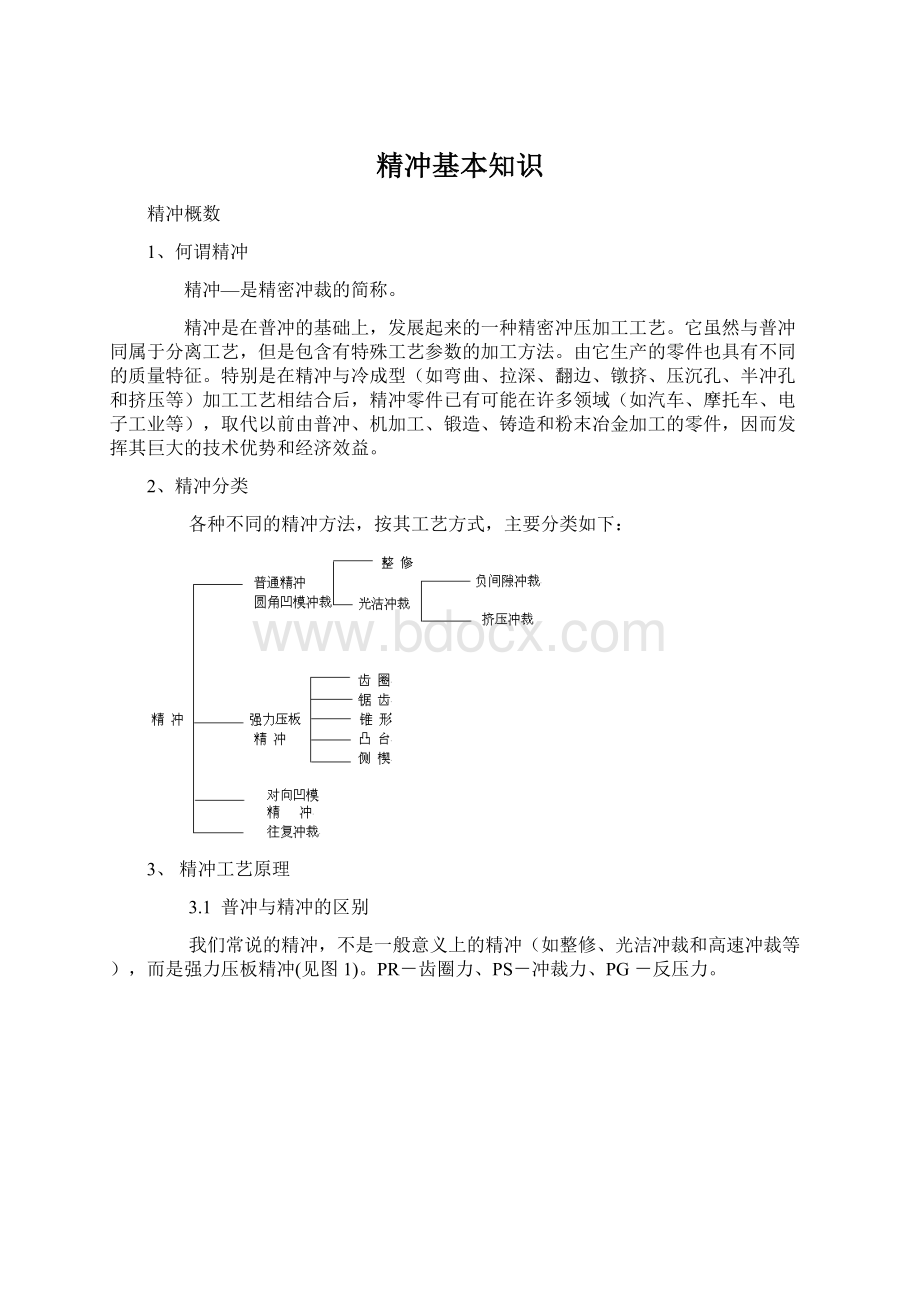
精冲基本知识
精冲概数
1、何谓精冲
精冲—是精密冲裁的简称。
精冲是在普冲的基础上,发展起来的一种精密冲压加工工艺。
它虽然与普冲同属于分离工艺,但是包含有特殊工艺参数的加工方法。
由它生产的零件也具有不同的质量特征。
特别是在精冲与冷成型(如弯曲、拉深、翻边、镦挤、压沉孔、半冲孔和挤压等)加工工艺相结合后,精冲零件已有可能在许多领域(如汽车、摩托车、电子工业等),取代以前由普冲、机加工、锻造、铸造和粉末冶金加工的零件,因而发挥其巨大的技术优势和经济效益。
2、精冲分类
各种不同的精冲方法,按其工艺方式,主要分类如下:
3、精冲工艺原理
3.1 普冲与精冲的区别
我们常说的精冲,不是一般意义上的精冲(如整修、光洁冲裁和高速冲裁等),而是强力压板精冲(见图1)。
PR-齿圈力、PS-冲裁力、PG-反压力。
强力压板精冲的基本原理是在专用(三向力)压力机上,借助特殊结构模具,在强力作用下,使材料产生塑性—剪切变形,从而得到优质精冲件。
3.2 精冲工艺特点
表1为普冲和精冲二种不同工艺方法的特点。
技术特征
普冲
精冲
1.材料分离形式
剪切变形(控制撕裂)
塑—剪变形(抑制撕裂)
2.工件品质
●尺寸精度
ISO11-13
ISO7-11
●冲裁面粗糙度Ra(μm)
Ra>6.3
Ra1.6~0.4
●形位误差:
平面度
大
小(0.02mm/10mm)
不垂直度
大
小(单面0.0026mm/1mm)
塌角
(20~35)%S
(10~25)%S
毛刺
双向,大
单向,小
3.模具
●间隙
双边(5~10)%S
单边0.5%S
●刃口
锋利
倒角
4.冲压材料
无要求
塑性好(球化处理)
5.润滑
一般
特殊
6.压力机
●力态
普通(单向力)
特殊(三向力)
●工艺负载
变形功小
变形功为普冲的2~2.5倍
●环保
有噪音,振动大
噪音低,振动小
7.成本
低
高(回报周期短)
表1
3.3 模具工作原理
精冲机是实现精冲工艺的专用设备。
如图2所示,精冲时精冲机上有三种力(PS、PR、PG)作用于模具上。
冲裁开始前通过齿圈力PR,经剪切线外的导板(6),使V形齿圈(8)压入材料并压紧在凹模上,从而在V形齿圈的内面产生横向侧压力,以阻止材料在剪切区内撕裂和在剪切区外金属的横向流动。
同时反压力PG又在剪切线内由顶件器(4)将材料压紧在凸模上,并在压紧状态中,在冲裁力PS作用下进行冲裁。
剪切区内的金属处三向压应力状态,从而提高了材料的塑性。
此时,材料就沿着凹模刃口形状,呈纯剪切的形式冲裁零件。
冲裁结束后,PR和PG压力释放,模具开启,由退料力PRA和顶件力PGA分别将零件和废料顶出。
并用压缩空气将其吹除。
1.凸模;2.凹模;3.内形凸模;4.顶件器;5.顶杆;6.导板;7.压板;8.齿圈;9.精冲材料;10.精冲零件;11.内形废料;
PS—冲裁力;PR—齿圈力;PG—反压力;PRA—卸料力;PGA—顶件力;SP—冲裁间隙
3.4、精冲工作过程(见图3)
a)模具开启,送入材料;
b)模具闭合,在刃口(冲裁线)内外的材料利用齿圈力和反压力压紧;
c)用冲裁力PS冲裁材料,压紧力PR和PG全过程有效压紧;
d)滑块行程结束,冲件在凹模内,内孔废料冲入落料凸模中;
e)齿圈力PR和反压力PG卸除,模具开启;
f)在施加齿圈力的位置,此时作用为:
顶出内孔废料和卸除冲压搭边的卸料力PRA;
g)在施加反压力的位置,此时作用为:
从凹模中顶冲件的顶件力PGA。
材料开始送进;
h)吹卸或清除精冲件和内孔废料。
材料送进完成。
PR—齿圈力PG—反压力PS—冲裁力PRA—卸料力PGA—顶件力
1—压板2—凹模3—冲裁(落料)凸模4—顶件器5—精冲材料6—精冲零件7—冲内孔废料
精冲模设计简介
有关精冲模设计,已经在出版的“简明精冲手册”以及国内外有关的技术文献中都有详细介绍。
这里仅仅是一个设计提纲供大家参考。
让我们互相学习,共同交流,为精冲技术的发展而努力。
下面仅以固定凸模式模具为例,说明在设计各主要元件,应注意的问题。
1、精冲机吨位选择
精冲件所需总压力:
FT=FS+FG+FR
FS—冲裁力,FG—反顶力FR—齿圈力
但当前随着新产品不断日新月异,生产技术要求精冲件有很多压印或挤压工艺,如何考虑压印或挤压力。
一般,挤压压力与挤压面积、挤压深度和材料变形程度等因素有关。
挤压力经验公式
FP=A×f×Rm×(1+hp/s)
A—压印的投形面积
f—抗拉强度系数
Rm—抗拉强度
hp—压印深度
S—材料厚度
在使用上述公式计算挤压力FP时发现,当材料的变形程度>20%时,所得挤压力与实际所需相差很大。
如图所示,直径26mm,料厚7mm,挤压深度3.5mm材料AiSiC1008时。
其计算值为:
FP≈40T
而实际挤压力FP≈110T
因此,当有挤压工序的工件,在考虑所需挤压力时,根据材料的相对变形程度,(当∑>20%时),对该公式作必要的修正。
FP=A×F×E×RM×(1+HPS)
E—相对变形程度E的系数。
2、精冲模架选择
在工作中固定凸模式模架有双导柱和四导柱两种模架。
2.1双导柱模架选择
2.1.1工件几何形状为全对称,或变曲对称。
2.1.2工件有效工作直径在50~60的范围内。
2.1.3材料厚度至8MM以下。
2.1.4各限之间偏裁不大于25%的非对称件。
2.1.5工件为板小件,工步以2—3步的连续模
2.2四导柱模架选择
除采用双导柱模架条件以外的情况均采用四导柱模架。
至于凹模板,固定板,齿圈板,垫板等零件都已标准化。
凸模也有固定的形式。
3、传力杆
传力杆至精冲模中的作用是传递各项压力,必要时需进行许可页截计算。
P=FD
P—传力杆许可页荷
D—传力杆直径
—单位面积上的许可截
3.1下传力杆
3.1.1下传力分布
下传力捍的分布,应以最大可能达到对称,均衡要求。
3.1.2下传力杆直径,在顶件的空间允许的情况下直径越来越好,不宜采用,直径3MM的顶杆。
如果此处必须设置顶杆,应作技术处理(如异形杆)。
3.1.3由于FELNTOOL、SCHMID,精冲模架结构的特点,采用该模架,设计挤压工件时,必须设计支承杆(见图2),支承杆的放置,应在挤压位置的中心。
以保证挤压厚度尺寸的精度。
3.2上传力杆
3.2.1上传力杆分布
上传力杆的分布,同样应以对称,均衡原则进行布置。
3.2.2上传力杆直径力求相同
3.2.3上传力杆的位置,尽可以地接近主凸模外廓,其距离为1~2。
3.2.4上支承杆设计同下传力杆要求一样。
4、平衡杆
在连续模冲裁过程中,一般情况下各工步向下移动的行程高度是不同的,各外传力杆下移高度也不同。
由此造成承压圈内的承压块受力不均,承压块产生倾斜。
另外第一次冲裁时,使齿圈板受力不均,造成小凸模断裂。
故至连续模中平衡杆的设立是不可缺少的。
4.1平衡杆设计
平衡杆应对称分布一般可采用2根,当工件步距较大或多工位连续模应采用4根平衡杆。
它的位置应在条料宽度以外,一般最小距离为2MM,有挤压工步的最小距离为5MM。
4.2平衡杆高度4H(见图3)
4H=(VU+S-F)
VU—顶件的凹模平面尺寸
S—条料最小厚度
F—系数(见简明精冲手册)
4.2下平衡杆结构
结构形式见图35、闭锁销
至连续模冲裁过程中,有较大的模向力,为防止上下偏移,保证凸,凹模间隙,闭锁销的设计,也是不可缺少的。
5.1闭锁销的设计
一般情况下采用对称均匀分布。
放置在条料两侧,但当闭锁销挡体工件或废料排出时,也可将它设计在条料一侧(即操作员侧)
5.2闭锁销有效长度L2(见图4)
L2=S+10+×+Y
S—条料厚度XY—闭锁销侧角尺寸6、平衡块(或齿圈保护)
连续模在条料的开头或末尾,为使齿圈板不致倾斜,必须设置平衡块。
在有齿圈时,它同时可以防止齿圈与凹模或上,下齿圈在合模时相撞,造成损坏。
(见图5)
6.1平衡块高度Amax
平衡块为一组四件,其形状可作成元柱形或方柱形。
设置成对称分布。
Amax=Smin-(0.002-0.005)
Smin—材料最小厚度
6.2平衡块高度AMAX的控制
由公式可知,Amax一定要比条料最小厚度小。
由于每批条料的厚度变化,平衡块高度(Amax)至试模时往往需要修磨,以达到上述要求。
为了拆装方便应将平衡块的紧固螺钉,设计在齿圈板下方,以便试模时,在机床上好装卸。
7、异正销
7.1异正销设计
异正销直径的大小与冲裁料厚有关,异正销的配合。
D2×5,Dmin=5mm
S—料厚
7.2异正销的凸模与凹模冲裁间隙
异正销的孔无需精冲,在冲其孔时其间隙值可取普通冲裁,双向间隙选取:
Z=2(0.01S)
7.3异正销配合孔外倒角
由于异正销孔的冲裁使用普通间隙,这时产生的毛刺很多,至连续冲裁中毛刺被压平,往往卡在异正销上,出现退料困难,的条料会被拉弯。
为了毛刺不被挤压,异正销配合孔端应倒角。
8、导料销
材料异料销的配合要求(见图7)
这里需要提示:
材料异料销与齿圈板配合精度不可忽视,间隙超过0.2mm以来,条料在送料时会产生很大的偏斜,搭边变化很大,造成工件局部断面质量恶化。
9、弹簧顶销
弹簧顶销是用来消除工件在顶件上的附作力,以便用压缩空气吹出工件。
因其作用在图纸上反映不明显,绘图时往往被遗漏,所以在绘制总图时,就在确定位置上首先注上标记,等待以后细化10、精冲间隙值
一般精冲技术文献都标明精冲间单边隙值SP均为0.5%S
笔者认为这个0.5与间隙值,是在精冲压力机、精冲模制造精度,精冲材料的质量,生产中的润滑条件,操作员技术水平都很理想的状态下提出的。
一般企业很少能达到以上要求进行生产,0.5%S的间隙值在实际使用中,反而容易产生凸模与凹模,局部快速磨损,不利提高模具使用寿命。
现将黑色金属精冲间隙值推荐为下:
S=1.35~1.5SP=0.7%S
S=1.5~3.8SP=0.8%~1.3%S
S=3.8~8SP=0.8%~1.4%S
总之,设计精冲模除以上叙述各元件的注意事项外,还应考虑以下几点:
1)模具零件加工工艺性
2)模具零件检测方法
3)模具装配,试模可行性
4)模具主要元件、凸模、凹模的可靠性
5)模具安装和维修
6)模具运输中安全
精冲零件
1.精冲零件的工艺性
精冲零件的工艺性,主要指保证零件的技术和使用要求,并在一定的批生产条件下,在制造上应最简单、最经济。
而影响它的主要因素有:
(1)零件结构的工艺性;
(2)零件尺寸公差和形位公差;
(3)材料性能和厚度;
(4)冲裁面质量;
(5)模具设计、制造质量及寿命;
(6)精冲机的选择等。
精冲零件结构的工艺性,是指构成零件几何形状的结构单元,它包括:
最小圆角半径、孔径、壁厚、环宽、槽宽、冲齿模数等的确定尤为重要。
图1所示,可供选择精冲零件结构参数的极限值。
它们都小于普冲零件。
这是由精冲原理决定的。
然而,合理的零件结构参数,有利于提高产品质量,降低生产成本。
2.精冲零件的难度等级
根据零件几何形状及其结构单元,在图1各图中划分为S1、S2和S3三级。
S1—简单的,适于精冲材料抗剪强度Ks=700N/mm2
S2—中等的,适于精冲材料抗剪强度Ks=530N/mm2
S3—复杂的,适于精冲材料抗剪强度Ks=430N/mm2
在S3以下的范围,不适宜精冲,或者要采用特别措施。
使用S3的范围时,其条件是冲裁元件要用高速钢制造,且精冲材料抗拉强度δb≤600N/mm2(抗剪强度Ks≤430N/mm2)。
例:
图1中开关凸轮,材料为Cr15(球化),Ks=420N/mm2,确定其难度等级。
·孔径d=4.1mmS1
·搭边b=3.5mmS3
·齿模数m=2.25mmS2
·圆角半径Ra=0.75mmS1/S2
此零件最大难度是搭边b,故总难度为S3,可以精冲。
3.精冲零件的技术要求
3.1尺寸公差
精冲零件的尺寸公差,取决于:
零件形状、模具制造质量、材料厚度及性能、润滑剂和压力机调整等因素。
可由表1中选取。
3.2平面度公差
精冲零件的平面度是指零件平面的挠度(见图2),其值为:
f=h-s
由于精冲材料是在压紧状态下进行的,故精冲件具有较好的平面度。
而这种平面度随零件尺寸、形状、材料厚度及机械性能等不同而有所差别。
一般来说,厚料比薄料零件平直;低强度材料比高强度材料平直;压边力大比压边力小的平直。
在凸模侧的材料表面总是中凹的,凹模侧总是中凸的。
但如果零件还需要压印、压痕、切口、弯形等工序或用连续模冲裁,由于在零件上产生局部的变形或冲裁方向不同,致使平面度有较大的波动范围。
但无论如何,精冲件总是要比普通冲压件的平面度好的多。
图3是在100mm距离上测定的一般直线度。
图1精冲零件几何单元及难度等级
A—孔径;B—槽宽、搭边;C—齿模数;D—圆角半径。
料厚S(mm)
抗拉强度600N/mm2
内形J
外形A
孔距X
ISO公差等级
0.5~1
6~7
7
7
1~2
7
7
7
2~3
7
7
7
3~4
7
8
7
4~5
7~8
8
8
5~6.3
8
9
8
6.3~8
8~9
9
8
8~10
9~10
10
8
10~12.5
9~10
10
9
12.5~16
10~11
10
9
3.3垂直度公差
精冲零件的冲裁面与基面成一定的角度公差(倒锥),谓之不垂直度。
它与料厚及其性能、冲裁刃口状态、模具刚度、压力机的调整等有关。
一般料厚为1mm时,不垂直度为0.0026mm,若料厚为10mm,则毛刺侧比塌角大0.052mm。
图4为料厚与不垂直度的关系。
图2零件平面图
图3平面度公差
图4料厚与X值的关系
3.4冲裁面质量
冲裁面是精冲零件质量高低的主要标志。
它与材料种类、性能、金相组织、模具质量和刃口状况、润滑剂及压力机调整等因素有关。
冲裁面的结构组成包括:
光洁面、撕裂面、塌角面和毛刺面。
冲裁面状况的表示方法和意义如图5所示,其质量特征表现为三个方面。
图5冲裁面的表示方法
图中:
S—材料厚度;h—断裂时,最小光洁面部分占材料厚度S的百分比(%);l—鱼鳞状断裂时,最小光洁面部分占材料厚度S的百分比(%);b—最大允许的鱼鳞状断裂宽度,b的总和不大于相关轮廓的10%;t—允许的断裂深度为1.5%S;e—毛刺高度(mm);c—塌角宽度为30%S(最大);d—塌角深度为20%S(最大)(齿形件时为30%S);E—撕裂带的最大宽度。
(1)冲裁面粗糙度
冲裁面的光洁程度,在冲裁方向和沿周边便于不同位置是有差别的。
即塌角侧优于毛刺侧。
冲裁面的粗糙度用算术平均值aR表示。
其值一般Ra=0.2~3.6,共分为六个等级(见表2),测量方向——垂直于冲裁方向;测量位置——在冲裁面的中部(见图6a)。
冲裁面的粗糙度与材料抗拉强度的关系如图6b所示。
表2冲裁面粗糙度
粗糙度等级
1
2
3
4
5
6
Ra(μm)
0.2
0.4
0.6(0.8)
2.4
3.4
3.8(3.6)
代号
N4
N5
N6
N7
N8
图6冲裁面粗糙度与抗拉强度的关系
(2)冲裁面完好率
精冲零件冲裁面完好率分为五个等级(见表3)。
冲裁面完好率
h
l
100%S
100%S
90%S
75%S
50%S
100%S
90%S
75%S
--
--
(3)冲裁面撕裂等级
精冲零件冲裁面撕裂等级分为四个级别(见表4)。
表4冲裁面撕裂等级
E(mm)
级别
0.3
0.6
1
2
1
2
3
4
(4)冲裁面质量的表示方法和意义
如图7所示为冲裁面质量特征的表示方法和意义。
示例:
图7冲裁面长度表示实例
例中,冲裁面粗糙度Ra=2.4μm;完好率h=90%S;l=75%S;撕裂级别为2。
图8求塌角值tE和bE
4.精冲零件的塌角
塌角系指精冲零件内、外廓平面与光洁面交界处的不规则外凸曲线的下陷塑性变形(见图8)。
塌角的大小与料厚、材质、零件形状、反压力及齿圈高度等有关。
塌角的计算方法可参看图8选取。
一般tE≈(5~10)S,bE≈(5~10)tE。
5.精冲零件的毛刺
毛刺系指精冲零件冲裁面端部上的不规则突起。
其大小与材料种类、间隙、模具刃口状况、凸模进入凹模深度及冲裁次数等有关。
精冲时产生的毛刺,不是切削毛刺而是挤压毛刺。
判断毛刺的大小,不仅是毛刺高度,而且还有毛刺根部的厚度。
根据VDI3345标准,当模具刃口锋利时,只产生薄毛刺,e=0.01~0.08mm;当模具刃口变钝时,产生厚毛刺,e=0.1~0.3mm(见图9)。
图9精冲毛刺高度
6.1尺寸公差
因为精冲是一个流动—剪切过程,在精冲时,冲裁凸模首先使金属组织的晶体发生强烈的变形,而后分离。
一定的精冲材料影响精冲零件的表面质量、尺寸精度和模具寿命。
对它的基本要求是:
(1)必须具有良好的可塑性和较大的变性能力
这主要是使剪切区材料的流动持续到剪切终结而无撕裂。
采用抗拉强度δb≤650N/mm2,含碳量到0.35%的钢,其精冲效果最好。
[1]材料的精冲性能
—抗拉强度
—屈服极限
—延伸率
—硬度
—渗碳体和碳化物(球化)变形程度
[2]材料的变形能力
—屈服极限低
—抗拉强度低
—断裂延伸率高
—端面收缩率高
精冲材料具有较高的断裂延伸率值和端面收缩率值就具有较高的变形性能。
低的屈服极限值说明材料在较低的压力作用下就开始流动。
精冲材料强度的适宜范围,见图10。
图中的含碳量是按当量含碳量计算,即
低碳钢含碳量及低合金钢当量含碳量(重量%)
图10合金含碳量与材料强度的关系
(2)必须具有良好的组织结构
精冲材料,对金相组织有较高的要求。
同样的材料,热处理不同,其金相组织和延伸率亦不同,对精冲件的质量也有显著的影响。
如对含碳量大于0.35%的碳钢、合金钢来说,渗碳体(Fe3C)的形状及其分布对剪切表面光洁度有决定性的影响,其中以球化后(经球化退火)碳化物以细粒状均匀分布最为理想,而有片装珠光体组织很难冲出光洁的剪切表面。
图11所示,系含碳量为0.45%的碳钢,由于金相组织的不同,而得到不同的剪切表面质量。
左边是未处理前铁素体-珠光体结构,右边是经球化后的球状渗碳体。
图11不同金相组织对剪切面的影响(C45)
(3)精冲时的冷作硬化
由于精冲是挤压-剪切过程的复合,因而材料在剪切区内晶体组织产生了强烈的冷作变形。
突出表现在冷作硬化区内材料的硬度比基体硬度有显著的增大。
为此,掌握精冲冷作硬化的变形规律,确定其冷作硬化的大小、形状和深度以及对精冲件的实际作用,是非常必要的。
图12所示,为普冲与精冲时材料的冷作硬化情况。
图12普冲与精冲时材料的冷作硬化
6.2精冲材料的选择
(1)选择原则
从技术上要满足精冲零件的功能要求,同时要考虑经济性,以降低成本。
它包括:
供应类型和状态、尺寸公差、表面质量和精冲难度。
(2)材料品种
黑色金属,包括:
软钢(C≤0.13%);非合金钢(0.12~1.0%C)
合金钢(0.15~0.20%C)不锈钢(C≤0.15%)
细晶粒钢(0.10~0.22%C)
有色金属,包括:
铜和铜合金;铝和铝合金。
(3)供应状态
对于钢材要求:
a.供应类型:
热轧带钢、冷轧带钢、扁钢,但状态各不一样,有退火、软化退火、球化退火等。
b.尺寸大小:
按设计模具确定。
c.厚度公差:
要与零件相符。
d.表面质量:
不同的轧制方法得到不同的表面质量,为酸洗的、喷砂的、酸洗平整的、冷轧的等。
e.金相组织:
根据产品零件要求,分为三级:
FSGⅠ:
具有最大的抗拉强度,对金相组织无要求;
FSGⅡ:
经退火处理,材料C>0.15%,约含80~90%球状渗碳体;
FSGⅢ:
经软化退火,材料C>0.15%,约含100%球状渗碳体。
对有色金属铜、铝及其合金均有化学成分及轧制状态要求。
6.3精冲材料的精冲性评价
精冲材料的精冲性评价及材料的选择,可参看表5。
表5钢材的精冲性
钢号
可冲厚度最大(mm)
精冲性评价
中国(YB)
美国(AISI)
德国(DIN)
日本JIS)
苏联(гOCT)
08
1008
15
1
10
1010
C10
S10C
10号钢
15
1
15
1015
C15
S15C
15号钢
12
1
20
1020
C22
S20C
20号钢
10
1
25
1025
S25C
25号钢
10
1
30
1030
S30C
30号钢
10
1
35
1035
C35
S35C
35号钢
8
2
40
1040
S40C
40号钢
7
2
45
1045
C45
S45C
45号钢
7
2
50
1050
CK53
S50C
50号钢
6
2
55
1055
Cf56
S55C
55号钢
6
2
60
1060
C60
SWRH4B
60号钢
5
2
1064
CK60
S58C
6
65
1065
CK67
SUP2
65号钢
3
70
1070
3
2
3
1074
C75
3
T8A
W1-0.8C
C85W2
SKU3
Y8A
3
T10A
3
3
15Mn/16Mn
8
3
15CrMn
16MnCr5
15XГ
5
2
14Ni6
8
2
14NiCr10
SNC21H
7
E3316
14NiCr14
SNC22H
7
14NiCr18