2电站锅炉制造工艺.docx
《2电站锅炉制造工艺.docx》由会员分享,可在线阅读,更多相关《2电站锅炉制造工艺.docx(17页珍藏版)》请在冰豆网上搜索。
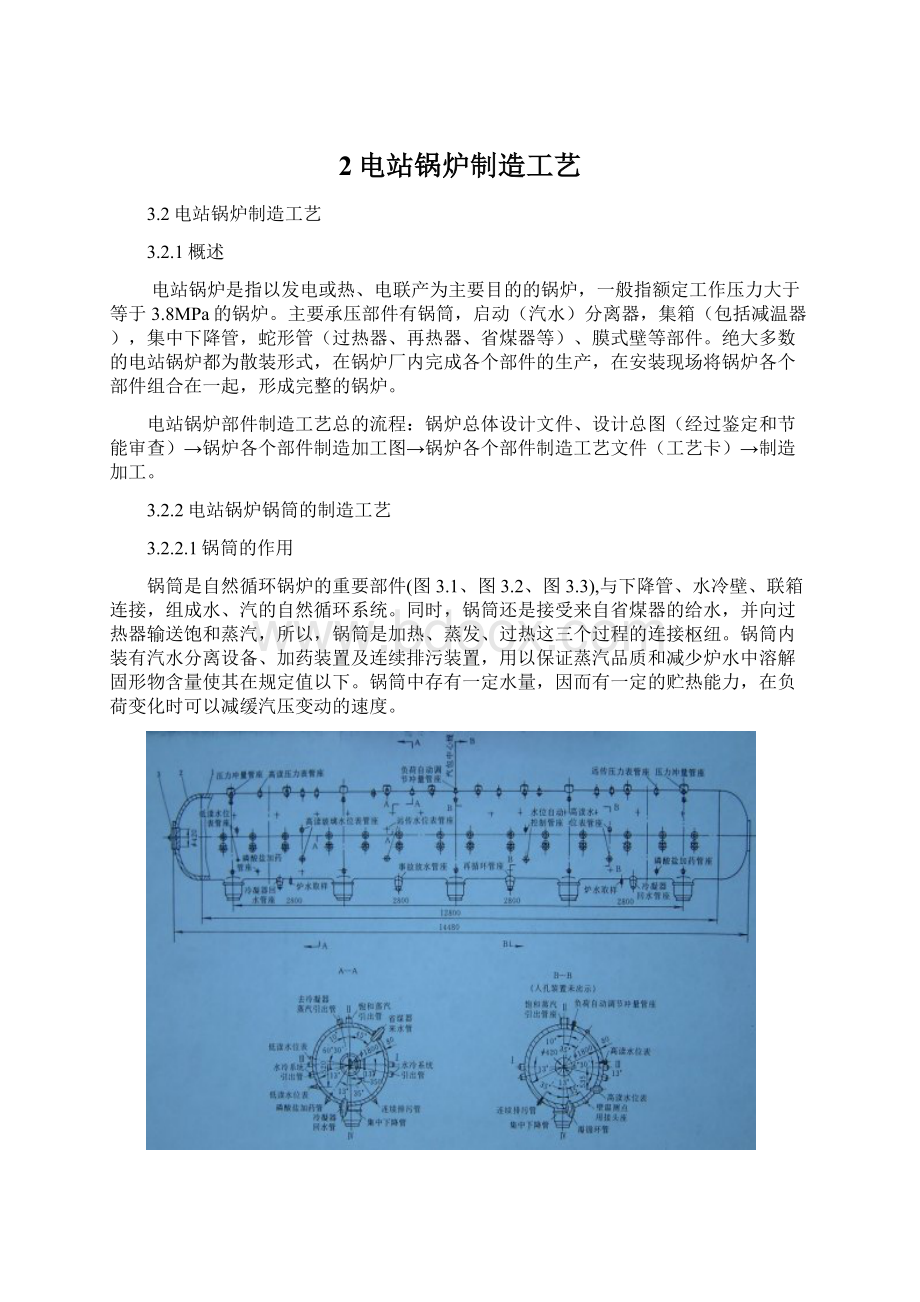
2电站锅炉制造工艺
3.2电站锅炉制造工艺
3.2.1概述
电站锅炉是指以发电或热、电联产为主要目的的锅炉,一般指额定工作压力大于等于3.8MPa的锅炉。
主要承压部件有锅筒,启动(汽水)分离器,集箱(包括减温器),集中下降管,蛇形管(过热器、再热器、省煤器等)、膜式壁等部件。
绝大多数的电站锅炉都为散装形式,在锅炉厂内完成各个部件的生产,在安装现场将锅炉各个部件组合在一起,形成完整的锅炉。
电站锅炉部件制造工艺总的流程:
锅炉总体设计文件、设计总图(经过鉴定和节能审查)→锅炉各个部件制造加工图→锅炉各个部件制造工艺文件(工艺卡)→制造加工。
3.2.2电站锅炉锅筒的制造工艺
3.2.2.1锅筒的作用
锅筒是自然循环锅炉的重要部件(图3.1、图3.2、图3.3),与下降管、水冷壁、联箱连接,组成水、汽的自然循环系统。
同时,锅筒还是接受来自省煤器的给水,并向过热器输送饱和蒸汽,所以,锅筒是加热、蒸发、过热这三个过程的连接枢纽。
锅筒内装有汽水分离设备、加药装置及连续排污装置,用以保证蒸汽品质和减少炉水中溶解固形物含量使其在规定值以下。
锅筒中存有一定水量,因而有一定的贮热能力,在负荷变化时可以减缓汽压变动的速度。
图3.1电站锅炉锅筒的图样
图3.2大型电站锅炉的锅筒吊装
图3.3大型电站锅炉的锅筒连接及悬吊结构
3.2.2.2锅筒制造工艺
锅筒由筒体(也称筒节)、封头、下降管、大小管接头,还有锅筒内部装置等零部件组装焊接而成。
它的一般制造工艺:
选材→下料(光谱检查、材料标记移植、材料切割)→封头压制、筒节卷圆→坡口加工→组对→焊接→受压元部件成形→无损检测→开孔→焊接管座、管接头→角焊缝无损检测(有需要时)→热处理(有需要时)→耐压试验→内部清理、内部装置安装→封头封堵→油漆包装→出厂。
锅筒的制造难度较高,一般是卷焊结构,如图3.4由钢板卷制焊接成的圆筒体,两端焊上冲压成型的凸形封头。
锅筒外部连接各种受热面管子,内部则装设有各种内件(主要是汽水分离装置、蒸汽清洗装置、排污装置、加药装置、取样装置等)。
锅炉的主要安全附件(安全阀、压力表、水位表等)也都装设在锅筒外部。
锅筒焊接前的装配工作的好坏将直接影响锅筒焊接质量,所以装配工作是一项很重要的工作。
如果卷筒质量不高,则常常出现间隙过大、错边或纵缝相对边缘错扭等偏差,如图3.5,将给装配带来一定困难。
卷制筒节钢板长度为筒节圆周周长,筒节纵缝的坡口采用刨边机或铣边机加工或采用气割+打磨方法加工纵缝坡口,筒节一般采用等厚度钢板,每个筒节焊接一条纵缝,纵缝焊完后还要进行校圆。
为了使装配工作易于进行。
现场常使用焊上角铁、压环、压板,楔子或位紧螺栓等,以便对齐边缘或减小间隙,而后进行点固焊接。
生产批量较大时,可采用各种专用的装配胎夹具以及各式液压装配台,如图3.6。
图3.4锅筒结构简图
3.5锅筒常见的偏差
锅筒的筒节纵缝多采用埋弧自动焊,大型锅筒筒节和筒体的制造过程中,纵、环缝对接焊接也常常采用‘窄间隙埋弧焊’工艺方法,比常规坡口埋弧自动焊不仅可节约焊材和提高生产效率,由于热输入量小焊接接头的性能更有保证。
在锅筒的组装工艺上,应充分考虑总装工作场地、装焊工作劳动条件、工序的衔接等因素。
为了保证焊接接头的质量,焊前预热、焊后及时消氢及焊后热处理十分关键。
锅筒的制造质量在很大程度上取决于焊接质量的优劣。
在内压力作用下,锅筒纵缝受力是环缝受力的二倍,因此筒节纵缝焊接是锅炉制造的关键工艺之一。
由于制造的误差,卷筒、纵缝焊接、筒节与封头都有一定的椭圆度,每个筒节和封头的圆周长度都不尽相同,所以锅筒环向焊缝的装配比纵缝困难得多。
图3.6大型电站锅炉的筒节卷制
锅筒的热处理应优先选用闭式加热炉中整体热处理的工艺方法(图3.7)。
当锅筒长度大于加热炉的有效长度时,可采用分段热处理最终环焊缝,即将其一部分露出在加热炉以外。
《锅炉安全技术监察规程》4.4.4要求“如果采用分段热处理则加热的各段至少有1500mm的重叠部分,并且伸出炉外部分有绝热措施。
”“补焊和环缝局部热处理时,焊缝和焊缝两侧的加热宽度应当各不小于焊接接头两侧钢板厚度(取较大值)的3倍或者不小于200mm”。
在装焊大直径、厚壁的下降管管接头时,必须采用成熟焊接工艺,防止在焊缝及热影响区开裂等焊缝缺陷。
锅筒的制造,还包括锅筒内部装置的加工制造及预埋件的焊接。
图3.7大型热处理炉
3.2.3电站锅炉集箱的制造工艺
3.2.3.1集箱的作用
集箱又称为联箱(包括减温器),是起到将锅炉的汽、水介质进行中间汇集、分配、调温等作用的重要部件。
锅炉上的集箱数量很多,例如,一台350MW的锅炉,集箱多达150个左右(如图3.8)。
在受压件中,过热器和再热器,还有屏过的出口集箱运行温度最高,壁厚最厚。
集箱的结构主要随管接头的结构而不同,包括集箱上的开孔和孔排结构,集箱上往往焊有大量的管接头(如图3.9)。
集箱制造时无论孔加工、焊接、热处理及无损检验,工作量都相当大,加上材料类别多,因此制造质量问题突出。
减温器主要用于蒸汽温度的调节,并起到中间联箱的作用,大多数采用文丘里管式喷水减温器(如图3.10),布置在蒸汽集箱内,减温水从喷嘴喷出,雾化成较细的颗粒,与蒸汽达到充分接触,从而有效地进行热交换,降低蒸汽温度。
图3.8水冷壁、过热器集箱
图3.9集箱的大量长管接头
图3.10文丘里管式喷水减温器示意图
3.2.3.2集箱的制造工艺
集箱元件多采用厚壁碳素钢及铬钼钢制成,一般由筒体、集箱端盖或封头和长、短管接头等受压件组焊而成。
其筒体材料一般采用热轧或锻轧大口径钢管,大尺寸筒体也可以考虑用钢板制造。
它的一般制造工艺:
选材→下料(光谱检查、材料标记移植、材料切割)→封头压制、坡口加工→组对→焊接→受压元部件成形→无损检测→开孔→焊接管座、管接头→无损检测→最终热处理(有需要时)→耐压试验→内部清理→封头封堵→油漆包装→出厂。
集箱筒体上的拼接焊缝为环焊缝(如图3.11、图3.12)。
集箱上小直径管接头数量多、管壁薄,手工电弧焊时容易产生咬边、气孔、弧坑裂纹等焊接缺陷。
集箱管接头的焊接方法有:
手工焊(SMAW),手工氩弧焊加手工焊(GTAW+SMAW),内孔氩弧焊加手工焊(GTAW+SMAW)等。
集箱组对焊接后的内部清理工作十分重要,不允有残留物存在于集箱内部(图3.13)。
图3.11环焊缝自动焊
图3.12环焊缝手工氩弧焊打底
图3.13集箱清理和接管封堵
3.2.4电站锅炉的膜式壁水冷壁的制造工艺
3.2.4.1膜式壁水冷壁的作用
电站锅炉上的膜式壁管组包括炉膛水冷壁、顶棚过热器和包墙过热器,它是由普通光管或内螺纹管加膜片扁钢组焊而成。
一般炉膛水冷壁上管子的节距较小,因此,所需与管子的膜片扁钢较窄;而构成顶棚过热器和包墙过热器用的膜式壁节距较大,所用扁钢较宽。
锅炉采用膜式水冷壁属于辐射受热面,节省金属消耗量;降低高温对炉墙的破坏,起到保护炉墙的作用;能有效的防止炉壁结渣;悬吊炉墙;作为锅炉蒸发受热面,吸收炉内辐射热量,使水冷壁管内的热水汽化,产生锅炉的全部饱和蒸汽。
同时具有保护和减轻炉墙的功能。
在结构上,它采用管子加膜片扁钢焊接而成,通常称为“膜式水冷壁”(见图3.14)。
其主要优点有:
(1)膜式水冷壁能保证炉膛良好的严密性,对负压锅炉来说,能大大降低炉膛漏风,改善炉膛燃烧工况。
(2)膜式水冷壁对炉墙保护最为彻底,因为其炉墙只需保温材料,这样炉墙重量可以减轻,也降低了钢架的荷重,因此降低了金属耗用量,同时施工工时也大量降低。
(3)当炉膛爆燃时,膜式水冷壁可以承受冲击压力所引起的弯曲应力。
(4)由于炉墙只有保温材料,炉墙的蓄热量减少了很多,使启停时间可以缩短。
图3.14现场膜式水冷壁
3.2.4.1膜式壁水冷壁的制造工艺
膜式壁水冷壁的一般制造工艺:
选材→下料(光谱检查)→管子除锈、扁钢精整→组对→焊接→成排弯校→通球→无损检测→耐压试验→油漆包装→出厂。
膜式水冷壁包括带与不带折弯的水冷壁、以及螺旋上升的水冷壁,带与不带燃烧器、吹灰器开孔的水冷壁以及需与集箱组合的水冷壁,还有需焊接大量圆销钉作卫燃带用的水冷壁的制造。
根据沿炉膛高度或长度上的分段的需要,以及对运输条件的考虑,膜式壁管组的宽度可达约3.4m,最大长度可达16~18m左右。
普通光管或内螺纹管与膜片扁钢的组焊(见图3.15、图3.16、图3.17、图3.18),可采用膜式壁拼焊生产线来完成。
从传热和连接强度两方面考虑,膜片扁钢与管子沿管长方向的两条焊缝必须具有足够的熔深(见图3.19)。
膜式壁管组的折弯称为‘成排弯’,制造工艺上分为直立折弯和‘平放’折弯两种方法(见图3.20)。
平放折弯适合宽度大的膜式壁和倾斜或螺旋管圈膜式壁管组的成排弯。
图3.15扁钢精整、加工
图3.16钢管抛光除锈
图3.17膜式水冷壁制作
图3.18膜式水冷壁焊枪
图3.19膜式水冷壁制作、焊接过程
图3.20膜式壁折弯机
3.2.5电站锅炉的蛇形管制造工艺
3.2.5.1蛇形管的作用
电站锅炉的蛇形管一般包括过热器、再热器、省煤器等,过热器和再热器都是用于提高蒸汽温度的部件,省煤器是用于提高锅炉给水温度的部件。
过热器布置在炉膛出口及之后的烟道内,其作用是将锅筒来的饱和蒸汽加热成为过热蒸汽,并要求在锅炉出力或其它工况条件发生变动时,能保证过热蒸汽温度的波动处在允许的范围内,如图3.21所示。
再热器是将汽机高压缸排汽加热到与过热蒸汽温度相近的再热蒸汽温度,然后送到中压缸膨胀作功的蛇形管屏,结构与过热器相似。
电站锅炉上的省煤器普遍大多采用φ42~φ51mm的钢管,如图3.22所示。
在大型电站锅炉中,省煤器大大提高了进入锅筒中的给水温度,因此其作用主要是为了减少蒸发受热面,可降低制造成本。
省煤器还可降低进水温度与锅筒中工质饱和温度之间的温度差。
1.蛇形管φ42×52;2.蛇形管φ42×5;3.蛇形管φ42×5;4.蛇形管φ42×5;5.定位板;6.吊箍
图3.21所示为过热器的结构示意图
图3.22省煤器的结构示意图
过热器和再热器按其传热方式不同,可分为对流式、辐射式和半辐射式三种型式。
对流过热器中,按蒸汽和烟气的相对流向可分为顺流、逆流和混合流等三种形式。
大型电站锅炉通常采用上述型式的多级布置的过热器或再热器系统(见图3.23)。
在水平烟道和尾部竖井烟道的内壁,像水冷壁那样布置过热器管,称为包墙管过热器。
图3.23大型电站锅炉多级布置的过热器或再热器系统
3.2.5.2蛇形管的制造工艺
大型电站锅炉的省煤器、过热器、再热器的管排通常均为蛇形管排,有s形和U形两种套式管圈;管径大多数小于等于76mm;壁厚范围3.5~13mm,过热器管的壁厚较厚,再热器的壁厚较薄;多数管排的弯管半径r=1~5倍的管子外径;管子材料包括碳钢、铁素体耐热合金钢和奥氏体不锈钢。
大型锅炉上的蛇形管圈,即使是单根管圈也往往由多种材质、多种管径及壁厚组合,甚至需通过‘管端缩径’来变化管段管径;为了使得管排紧凑,减少管排占用空间的高度,处于同一管圈平面内圈的管排需要采用弯管半径r<1.5Dw的小R180°弯头。
蛇形管的制造方式较多,由于其所需数量很大,工艺难度较高,因此应优先采用自动生产线上的生产工艺,采用直管子首先按图样要求下料,完成对接焊口及无损探伤,即‘先接后弯’的制造程序。
为了最大限度地提高生产效率,保证焊口质量及弯管质量,这种生产线需要在生产线上配备‘多层选料架’、‘送管装置及滚道’、‘管子对接自动焊机’、‘探伤设备’、‘成对数控弯管机’、‘管排翻转装置’等装备。
图3.24所示为蛇形管自动生产线,其接管最大长度可达70~80m长,每加工完成一个蛇形管排所需时间平均大约为25min。
生产线上一般采用自动TIG焊(钨极惰性气体保护焊,也称钨极氩弧焊,代号GTAW),管子转动,焊头位于管子上方。
焊接质量好,生产效率高。
图3.24蛇形管自动生产线
蛇形管制造一般制造工艺过程如图3.25。
图3.25蛇形管制造的典型工艺过程