材料耐磨性的研究.docx
《材料耐磨性的研究.docx》由会员分享,可在线阅读,更多相关《材料耐磨性的研究.docx(13页珍藏版)》请在冰豆网上搜索。
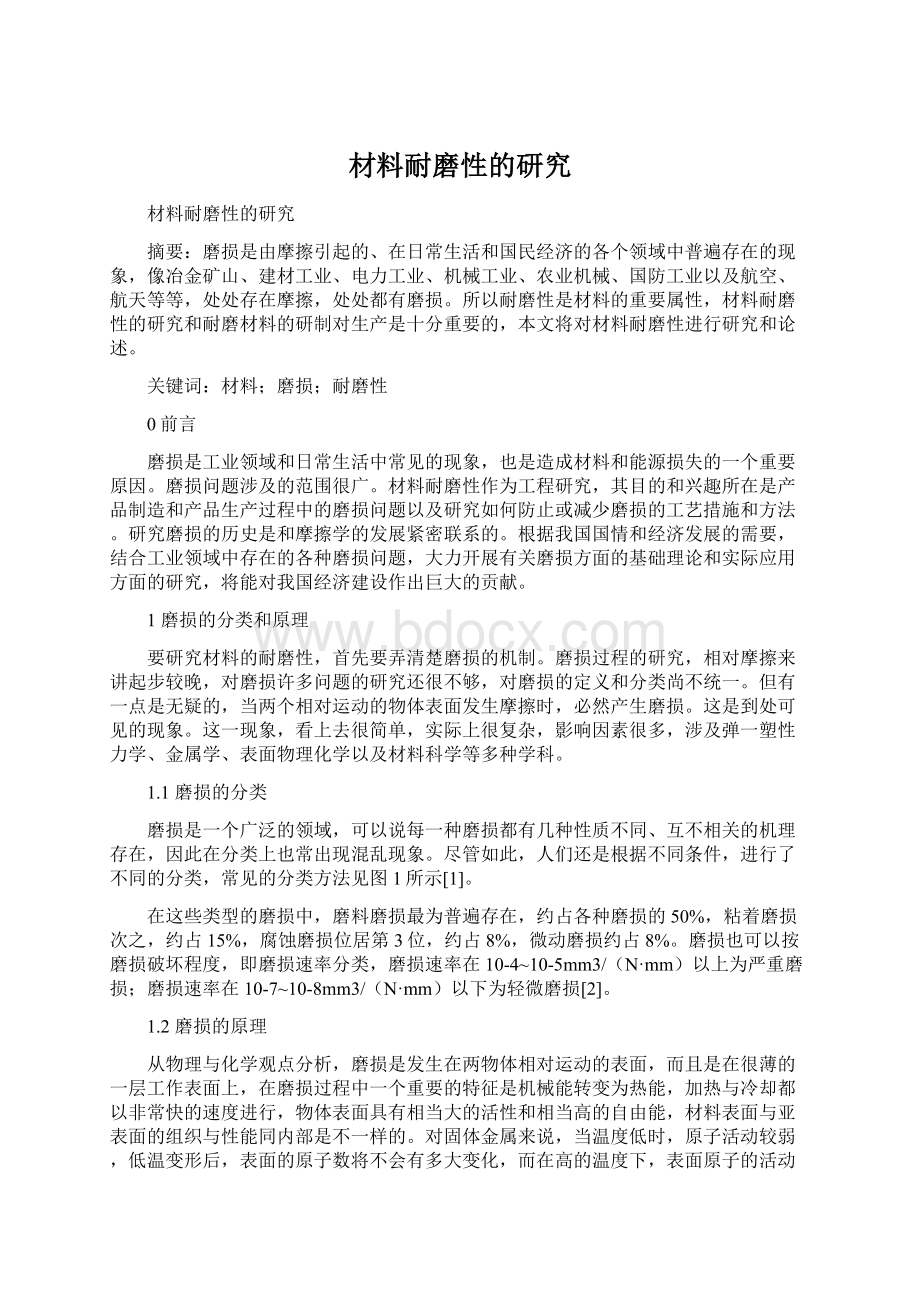
材料耐磨性的研究
材料耐磨性的研究
摘要:
磨损是由摩擦引起的、在日常生活和国民经济的各个领域中普遍存在的现象,像冶金矿山、建材工业、电力工业、机械工业、农业机械、国防工业以及航空、航天等等,处处存在摩擦,处处都有磨损。
所以耐磨性是材料的重要属性,材料耐磨性的研究和耐磨材料的研制对生产是十分重要的,本文将对材料耐磨性进行研究和论述。
关键词:
材料;磨损;耐磨性
0前言
磨损是工业领域和日常生活中常见的现象,也是造成材料和能源损失的一个重要原因。
磨损问题涉及的范围很广。
材料耐磨性作为工程研究,其目的和兴趣所在是产品制造和产品生产过程中的磨损问题以及研究如何防止或减少磨损的工艺措施和方法。
研究磨损的历史是和摩擦学的发展紧密联系的。
根据我国国情和经济发展的需要,结合工业领域中存在的各种磨损问题,大力开展有关磨损方面的基础理论和实际应用方面的研究,将能对我国经济建设作出巨大的贡献。
1磨损的分类和原理
要研究材料的耐磨性,首先要弄清楚磨损的机制。
磨损过程的研究,相对摩擦来讲起步较晚,对磨损许多问题的研究还很不够,对磨损的定义和分类尚不统一。
但有一点是无疑的,当两个相对运动的物体表面发生摩擦时,必然产生磨损。
这是到处可见的现象。
这一现象,看上去很简单,实际上很复杂,影响因素很多,涉及弹一塑性力学、金属学、表面物理化学以及材料科学等多种学科。
1.1磨损的分类
磨损是一个广泛的领域,可以说每一种磨损都有几种性质不同、互不相关的机理存在,因此在分类上也常出现混乱现象。
尽管如此,人们还是根据不同条件,进行了不同的分类,常见的分类方法见图1所示[1]。
在这些类型的磨损中,磨料磨损最为普遍存在,约占各种磨损的50%,粘着磨损次之,约占15%,腐蚀磨损位居第3位,约占8%,微动磨损约占8%。
磨损也可以按磨损破坏程度,即磨损速率分类,磨损速率在10-4~10-5mm3/(N·mm)以上为严重磨损;磨损速率在10-7~10-8mm3/(N·mm)以下为轻微磨损[2]。
1.2磨损的原理
从物理与化学观点分析,磨损是发生在两物体相对运动的表面,而且是在很薄的一层工作表面上,在磨损过程中一个重要的特征是机械能转变为热能,加热与冷却都以非常快的速度进行,物体表面具有相当大的活性和相当高的自由能,材料表面与亚表面的组织与性能同内部是不一样的。
对固体金属来说,当温度低时,原子活动较弱,低温变形后,表面的原子数将不会有多大变化,而在高的温度下,表面原子的活动能力增强,因此,材料的结构可能会出现某种程度的重新调整与改变,结果使金属性质和能量发生变化。
材料表面原子会与环境(介质)发生相互作用,产生物理吸附、化学吸附或化学反应,使材料表面可能产生加工硬化层或者形成表面织构,将会影响材料的磨损过程。
可以说磨损是一个动态过程。
图1磨损的分类
从原子与作用力分析,由于相互接触的两物体表面,其中一物体表面的原子可能与另一物体表面的原子极靠近,甚至进入斥力场,在相对运动时,两表面分子就会产生能量损耗。
在相对运动中将有些原子进入斥力场,而有另一些原子将离开斥力场,其变化大小,决定于接触程度,而其定量数决定于统计学的相率。
当两物体充分接近时,原子将被排斥而其自然的趋向是回到它原来的位置上去,然而这是个似乎不可能的假说,即原子可能被撞击出,并运动得足够远,以至进入相对表面上另一个原子场内,在这里得到新的平衡位置。
也就是说原子可以从一个物体表面上被对面的另一个物体表面俘获去。
按汤姆林逊的著作,这就是磨损的实质[3]。
磨损过程的研究,相对摩擦来讲起步较晚,对磨损许多问题的研究还很不够,对磨损的定义和分类尚不统一。
但有一点是无疑的,当两个相对运动的物体表面发生摩擦时,必然产生磨损。
这是到处可见的现象。
这一现象,看上去很简单,实际上很复杂,影响因素很多,涉及弹一塑性力学、金属学、表面物理化学以及材料科学等多种学科,虽然经过了较长时间的大量研究,但迄今为止对磨损机理的研究还很不够,也还没有一个可靠的简明的定量公式。
磨损是摩擦学研究的摩擦、磨损与润滑三大课题之一,三者之间摩擦是根源,磨损是结果,润滑是减少磨损有效的手段。
磨损又是机械零件三种主要破坏形式之一,即磨损、腐蚀和断裂,由此可见,磨损比摩擦更重要,但到目前为止,人们对磨损的研究,居多还限于孤立地或针对特定的机制进行。
主要是对运动物体表面润滑介质和环境的研究,而对磨损过程物理机制、磨损动力学、磨粒的形成等研究很少。
人们对磨损的理解也比对摩擦的理解相差很远。
对大多数不同性质的材料来说,在空倍,例如气中的摩擦系数相差大约不超过20倍。
磨损似乎比摩擦更复杂更敏感,比如软固体比硬固体容易磨损,而且磨损随着载荷和滑动距离的增加而增加,但是,也有例外,聚乙烯比钢软磨损反而小。
磨损影响因素甚多又十分复杂,其中环境因素有温度、湿度及周围介质;润滑条件和工作条件,像载荷、速度及运动方式;还有材料的成分、组织及工作表面的物理化学性质等诸多因素中,哪一个有变化都会引起磨损量的改变,同时也有可能引起机理发生变化。
系统的研究磨损机理以求得磨损变量与磨损系数以及材料结构性质之间的定量关系。
磨损按不同机理和条件,主要分为四大基本类型如图2所示[4]。
图2主要磨损类型示意图
(a)属粘着磨损,主要特征是磨损表面有细的划痕,严重时有材料转移现象,磨损产物多为片状或小颗粒,一般发生在蜗轮与蜗杆、凸轮挺杆以及缸套与活塞环之间的磨损。
(b)为磨料磨损,主要特征是磨损表面有明显的划痕或犁沟,磨损物为条状或切屑状,常见于农用犁铧、斗齿、球磨机用磨球与衬板等。
(c)是接触疲劳磨损,主要特征为磨损表面有裂纹、小坑等,磨损产物为块状或饼状,通常在滚动轴承、齿轮的表面发生较普遍。
(d)为腐蚀磨损,它的主要特征是磨损表面有化学反应膜或小麻点,但麻点比较光滑。
磨损物为薄的碎片或粉末,典型工件如汽缸与活塞、船舶外壳、水力发电的水轮机叶片等。
1.2.1粘着磨损
粘着磨损也称咬合(胶合)磨损或摩擦磨损。
粘着磨损是在法向加载下,两物体接触表面相对滑动时产生的磨损。
磨损产物通常呈小颗粒状,从一物体表面粘附到另一个物体表面上,然后在继续的摩擦过程中,表面层发生断裂,有时还发生反粘附,即被粘附到另一个表面上的材料又回到原来的表面上,这种粘附反粘附往往使材料以自由磨屑状脱落下来。
粘着磨损产物可以在任意的循环中形成,粘着以后的断裂分离,并不一定在最初的接触表面产生。
粘着磨损过程一般分为三个阶段(Ⅰ)跑合阶段亦称磨合阶段;(Ⅱ)稳定磨损阶段;(Ⅲ)急剧磨损阶段亦称破坏点以后,由于磨损阶段,如图3所示[5]。
图3典型的粘着磨损过程
1.2.2磨料磨损
磨料磨损是指硬的磨(颗)粒或硬的凸出物在与摩擦表面相互接触运动过程中,使表面材料发生损耗的一种现象或过程。
硬颗粒或凸出物一般为非金属材料,如石英砂、矿石等,也可能是金属,像落入齿轮间的金属屑等。
磨料磨损几乎没有一种是单一的磨损机理而引起的,经常是多种磨损机制综合作用的结果,而且随着磨损条件的变化,可能从一种机制转化为另一种机制。
对磨料磨损也称为磨粒磨损。
其实磨料与磨粒是两个概念。
磨料是指参加磨损的行为的所有介质,如空气、水、油、酸、碱、盐和各种磨粒,即硬颗粒或硬凸出物等。
而磨粒则指参加磨损行为的是具有一定几何形状的硬质颗粒或硬的凸出物,如非金属的砂石和金属的微屑和金属化合物以及非金属化合物颗粒。
从而可以看出,磨料磨损应计入磨料的物理化学作用及机械作用的综合结果,而磨粒磨损只计入颗粒机械作用。
所以磨料磨损是包括磨粒在内的与外界介质有关的磨损,磨粒只是磨料的一组元。
磨粒磨损是磨粒本身性质而与外界无关的机械作用结果。
磨料磨损时,作用在质点上的力分为垂直分力和水平分力,前者使硬质点压入材料表面,而后者使硬质点与表面之间产生相对位移,硬质点与材料相互作用的结果,使被磨损表面产生犁皱或切屑,形成磨损或在表面留下沟槽[6]。
1.2.3腐蚀磨损
腐蚀磨损是一种极为复杂又是常见的磨损形式,它是材料受腐蚀和磨损综合作用的磨损过程。
对环境、温度、介质、滑动速度、载荷大小及润滑条件等极为敏感。
稍有变化就可能使腐蚀磨损发生很大变化,当腐蚀成为主要原因时,通常都有几种磨损机理存在,各种机理之间还存在着复杂的相互作用,像金属与金属之间的磨损,开始可能是粘着磨损和腐蚀磨损,但因磨损产物又都具有磨粒的特性,因此会出现磨料磨损或者还有其他磨损机理。
因此在腐蚀磨损过程中,既不能忽视腐蚀的作用,也不能忽视磨损的作用,甚至还要考虑到其它磨损存在的综合作用,可能相互作用的结果,会使磨损量产生较大的变化。
腐蚀磨损可分为化学腐蚀磨损和电化学腐蚀磨损。
化学腐蚀磨损又可分为氧化磨损和特殊介质腐蚀磨损。
腐蚀磨损的产生过程是两物体表面产生摩擦时,工作环境中的介质如液体或气体或者在润滑剂等作用下,将与材料表面起化学反应或电化学反应,在表面上形成腐蚀产物,这些产物往往粘附不牢,在摩擦过程中剥落下上形成腐蚀产物,这些产物往往来,其后新的表面又继续与介质发生反应。
这种腐蚀和磨损的反复过程称为腐蚀磨损。
这种磨损通常是轻微的磨损,但在高温和潮湿的环境中,它可以变为严重磨损。
在腐蚀磨损中工作条件不同,作用程度亦不同,化学反应与机械作用可以是交替进行的并且互相起促进作用[7]。
1.2.4疲劳磨损
疲劳磨损是一种最普遍的磨损形式,主要发生在承受周期性的接触载荷或交变应力的机器零件表面上,如滚动轴承、车轴、齿轮、钢轨、轧辊等,这种形式的磨损也被称为接触疲劳磨损。
因为都是在循环载荷作用下产生表面失效的形式,其过程同样包括裂纹的萌生,扩展以致最后裂断。
典型特征是点蚀与剥落。
疲劳磨损定义为:
当两个接触体相对滚动或滑动时,在接触区形成的循环应力超过材料的疲劳强度的情况下,在表面层将引发裂纹并逐步扩展,最后使裂纹以上的材料断裂剥落下来的磨损过程。
研究表明滚动疲劳磨损的过程有两个阶段,即裂纹的萌生阶段和裂纹扩展至剥落阶段。
对纯滚动接触裂纹发生在亚表层(次表层)最大剪应力处,裂纹发展慢,经历时间比裂纹萌生长,裂纹断口颜色比较光亮。
对滚动加滑动的疲劳磨损,因存在剪应力和压应力,易在表面上产生微裂纹,它的萌生阶段往往大于扩展阶段,断口较暗。
对于经过表面强化处理的机器零件,裂纹起源于表面硬化层和芯部的交界处,裂纹的发展一般先平行于表面,待扩展一段后再垂直或倾斜向外发展。
损伤痕迹先为小点蚀,后是大块剥落[8]。
2材料耐磨性
材料的耐磨性并不是材料的固有特性,而是与磨损工程中的工作条件(如载荷、速度、温度、环境因素等)和材料本身性能及相互作用等因素有光的系统特性。
2.1材料耐磨性的定义
材料耐磨性是指某种材料在一定的摩擦条件下抵抗磨损的能力。
通常,它以磨损率的倒数来表示。
即
=
式中
——材料的耐磨性;
W——材料在单位时间或单位运动距离内产生的磨损量,即磨损率。
如前所述,材料的耐磨性必然也是工作条件的函数,脱离材料的工作条件来评定材料耐磨性的好坏是没有实际意义的。
同样,在工程实际中也找不到一种在所有的工作条件下都能适用的、万能的耐磨材料。
所以,在研究和使用过程中,人们往往采用材料的相对耐磨性这一概念。
也就是说,在评定各种材料耐磨性时.采用一种“标准”材料为参考试样,用其与参考试样在相同磨损条件下进行试验的结果来进行评定。
因此,材料的相对耐磨性即定义为试验材料与“标准”材料在同一工况条件下耐磨性之比。
即
式中
和
分别为“标准”试样及实验试样的磨损率。
为相对耐磨性。
它是一个无量纲参数。
采用相对耐磨性的方法来评定材料的耐磨性,在一定程度上可以避免在磨损过程中由于参量变化及测量误差造成的系统误差,可以更科学而精确地评定材料的磨损性能。
因此,这种评定方法己得到广泛的应用[9]。
2.2材料耐磨性的评定方法和测试技术
精确而可靠地测定磨损试验的结果是获得材料耐磨性准确信息的保证,也是评定耐磨性的依据。
首先,必须根据实际零件的使用情况和工作条件来选择便于模拟的磨损试验装置。
然后,再来确定适当的测定磨损量的仪器、工具和评定方法。
材料的磨损,有时可在使用条件下进行实物试验,能取得有用的数据。
但是实物试验周期很长,而且成本高,所以实物试验很难推广。
另一方面,在实验室里对材料进行磨损试验,周期一般都很短.还可能尽量地模拟工况条件而常采用较为合适的试验机,这对于选择金属耐磨材料和研究磨损都是有利的。
实验室磨损试验除可以得到磨损的定量数据外,还可以研究磨损过程中的一些动态现象,以及在磨损试验后观察金属材料被磨表面的形貌及通过收集磨屑来进行形貌观察和成分分析。
目前.对磨损量的测定方法主要有:
失重法、尺寸变化法、形貌测定法、刻痕测定法以及放射性同位素测定法等[10]。
2.2.1失重法
这种方法比较简单,它较广泛地适用于各种高、低精度磨损量的测定。
但要注意称量前试样的清洗干燥以及合适的称量天秤的选择。
一般,对于中等硬度的材料可以选用万分之—克的天平。
对于某些产生不均匀磨损或局部严重磨损的零件以及在磨损过程中发生粘着转移时,失重法就不够准确。
对比重相差较大的材料比较磨损量时,一般可采用将磨损失重换算成体积变化量来评定磨损结果。
2.2.2尺寸变化测定法
采用普通的测微卡尺或螺旋测微仪,可以很方便而精确地测出零件某个部位磨损尺寸(长度、厚度或直径)的变化量。
例如,内燃讥缸套主要是测定其内径的磨损量;拖拉机履带板主要是测定其销孔、跑道和节销部位的尺寸变化。
这里的关键在于前后多次测量位置的一致性。
所以.一般需要标明或确定测定位置或预先选定不产生磨损的基准面。
由于实际零件形状比较复杂,有的表面比较组糙或根本找不到理想的基准位置,这时可能需要制造专门的夹具以达到精确测量的目的。
对某些可拆卸的零件如齿轮等,还可以通过投影仅等专门仪器来稿确测量其形状和尺寸的变化量。
2.2.3表面形貌测定法
利用触针式表面形貌测量仪可以测出磨损前后表面粗糙度的变化。
这种方法可以全面地评价磨损表面的特征,但它不易定量地估计出零件或试祥的磨损值。
这种方法主要适用于磨损量非常小的超硬材料(如陶瓷、硬涂层)磨损或轻微磨损的情况。
2.2.4刻痕法
这种方法主要是指预制刻痕尺寸在磨损后的变化。
一般采用专门的金刚石在经受磨损的零件或试样表面上预先刻上压痕,最后测量磨损前后刻痕尺寸的变化,以确定其磨损量。
这种方法的优点是零件经短期使用就可确定其磨损量,精确度较高。
同时,它还能测定不同部位磨损的分布,且不受零件变形的影响。
这种方法可方便地使用于测定气缸套相机床导轨的磨损。
另外,还可采用干涉显微镜,利用磨损表面产生的干涉条纹测出磨痕的高度差.以确定磨损量。
2.2.5同位素测定法
这种测量方法相通常的磨损试验方法不问,它所测量的是磨损产物在单位时间内原子的衰变数,只要有足够的放射件。
极微量的磨削中也可显示可观的原子衰变数而被探测仪器测定出来。
这种方法的优点是:
(1)灵敏度和精确度高;
(2)可对磨损过程连续测定而无需拆卸被测试样;
(3)如果在摩擦副中分别引入不同的同位素,可以同时测出两个摩擦表面各自的磨损量及其变化,这是其它方法所不能实现的。
随着科技发展很多新设备新技术得到发展和广泛使用。
图4是利用扫描电子显微镜观察磨损的示意图。
金属材料在磨损试验后,对被磨表面及次表面进行形貌观察,以及收集磨屑进行观察和分析,是研究磨损及其机制的—种重要方法,获得广轻采用。
应注意被潜表面不被污染,直接在扫描电子显微镜中观察,从而分析材料磨损的一些特征和现象。
观察被磨表面的次表面(即紧接被磨表面的表面层)时,可先给被磨表面镀上薄层金属(如镍或铬)保护被磨表面不受破坏。
次表面应与被磨表面成一定角度,切取样品后制备金相试样,在扫描电子显微镜中对次表面的形貌照结构进行观察并作出分析[11]。
图4在扫描电子显微镜中进行“现场”单颗粒磨损试验装置示意图
金属材料通过磨损试验机的试验能够得到定量的磨损数据。
这些磨损数据可以用失重、体积磨损、磨损比、磨损率、耐磨性等形式表示。
固定磨料磨损试验机大多数是销盘式和销带式。
根据试验条件需要,可以选用不同磨料和不同磨科粒度的砂纸或砂布。
这类试验机属于高应力磨料磨损。
美国克利麦克斯(Climax)公司研究室和密执安大学合作试制的高应力磨科磨损试验现是销带式,图5所示。
图5磨料磨损试验机
1—放料盘;2—行程平台;3—限制开关;4—计时器;5—换挡马达控制器;6—马达;
7—控制器;8—料盘转动马达;9—变速马达控制器;10—变速马达;11—主轴;12—试样;13—紧固连接装置;14—电脉冲计数器;15—套管;16—垫圈;17—机架;18—负荷传感器;19—弹簧;20—套管外壳;21—平台;22—环形轴承;23—单通道记录器;
24—磨料砂布滚筒;25、26—重锤
3提高材料耐磨性的途径
磨损、腐蚀和断裂是机件失效的三种主要形式。
因此,提高机件的耐磨性一直是人们较为关心的问题。
从磨损机理及磨损过程来看,影响磨损的因素较为复杂。
由于材料的磨损主要是表面的变形和断裂过程。
因此,提高材料的表面强度和韧性,可提高材料的耐磨性[12]。
3.1表面热处理
表面热处理可有效地减轻材料的粘着磨损。
否是外部粘首磨损,可采用渗硫、磷化、软氮化等表面处理,以降低配对材料原子间的结合力。
这种处理实际上是使材料表面形成与基体材料不同的化合物层或非金属层,避免摩擦副直接接触,降低原子间的结合力,同时降低摩擦系数。
若摩擦面发生内部粘着磨损,则采用渗碳、氮化、氰化及碳氮硼三元共渗等热处理工艺,此时不但能降低配对材料的结合力,而且能提高机件本身的表层硬度[13]。
3.2改善材料组织和性能
材料组织和力学性能对耐磨性有重要影响。
当材料受低应力磨粒磨损时,应尽量提高材料硬度。
选用含碳量较高且基体组织为马氏体的钢,可有效提高抗磨粒磨损性能。
钢经淬火回火处理后,在磨粒磨损时材料硬度与相对耐磨性的关系是随着硬度增加,耐磨性增加;含碳量越高,材料抗磨粒磨损性能也就越好。
因此,实际中经常采用较高含碳量的钢并经热处理后获得马氏体组织,以提高其耐磨性。
当材料在高应力下工作时,基体织织最好是下贝氏体。
因为下贝氏体组织既有较高的硬度,又打良好的韧性。
对于合众金来说,控制和改善碳化物的数量、分布、形态,能极大地提高材料的耐磨性。
3.3机械加工强化
机械加工强化处理方法不改变表面化学成分,而是通过加工过程改变材料表面的组织结构、力学性能或几何形貌来达到强化的目的。
常用的机械加工强化方法有喷丸、滚压和挤压等。
如喷丸法是将高速的弹丸流喷射到工件表面,在弹丸的冲击下,表层晶粒的形状、尺寸和方位发生变化,造成晶格畸形,产生塑性变形和亚晶细化,形成微细的镶嵌组织,并在表层形成硬化层[14]。
3.4表面涂层处理
表面涂覆处理是直接在材料表面进行镀、涂,或利用物理、化学方法在材料表面上形成一层强化层。
按涂层的软硬程度,涂层可分为软涂层(如Au、MoS2、Teflon等)、硬涂层(如TiN、BN、Si3N4等)和复合涂层(如MoS2—TiN、Teflon—Si3N4等)。
常用的表面涂覆方法,有电镀(包括复合电镀、电刷镀)、化学镀、气相沉淀(化学气相沉淀和物理气相沉淀)、热喷涂(火焰喷涂、电弧喷涂、和等离子喷涂)、堆焊(电弧堆焊、埋弧堆焊、等离子堆焊等)、激光熔敷、浆液涂层和胶黏涂层等[15]。
处理之外还有扩散处理、激光表面处理[16]、深冷处理[17]和离子注入技术[18]等提高耐磨性的方法。
4耐磨材料
常用的耐磨材料有金属耐磨材料、陶瓷材料、聚合物及复合材料等[19]。
研究磨损的目的在于正确地选择材料、节约材料和降低能耗,这是一项复杂而十分重要的工作。
这时就要综合考虑耐磨材料的特性,零件工作特点、经济因素、资源条件等多方面因素进行最佳的选择。
由于作者专业所限和论文篇幅等原因这里重点介绍金属耐磨材料。
4.1耐磨钢
耐磨钢目前并没有形成一个独立的钢类。
若干抗磨料的专用钢种,主要用于制造农机具、矿山机械、工程机械、钻探机械等耐磨零件。
另外,还有一部分结构钢、工具钢、轴承钢、低合金高强度钢等也常用于制造各种耐磨零件。
根据工作条件.磨损类型以及材料破坏机理的不同,钢种的选用也不同[20]。
低碳低合金钢:
低碳合金钢的强度与耐磨性比低碳钢高,并可通过热处理,直接淬成低碳马氏体,进一步提高强度、硬度和耐磨性。
中碳钢和中碳低合金钢:
用于材料要求有足够强度及耐磨性的零件,并需采用调质及表面淬火等工艺。
高碳低合金钢:
用于耐磨性要求高的零件。
低碳铬钢和不锈钢:
主要用于液体介质中工作的耐磨零件。
高碳高合金钢:
用于耐磨性要求很高的零件。
铸造石墨钢:
兼有铸钢和铸铁的综合性能,有较高的机械性能及较好的铸造性能。
高锰钢:
有很高的耐冲击性和加工硬化能力,广泛应用于制造矿山、建材、冶金、电力、铁路等机械中的耐磨件。
4.2耐磨铸铁
耐磨铸铁具有优良的耐磨性,作为耐磨材料得到广泛应用。
铸铁的耐磨性取决于其组织,在摩擦磨损条件下,灰铁或球铁中的石墨是良好的润滑剂,能起到储油与润滑的作用。
在磨料磨损条件下,白口铁中的碳化物硬度高,具有很强的抗磨料粒子擦划的能力,如与强韧的基体配合可表现很高的耐磨性。
4.3有色合金耐磨材料
在有色台金耐磨材料中,较为重要的有两类:
一类是钴基耐磨合金,另一类是青铜。
钴基耐磨台金是由高温合金发展而来的。
它不但具有优异的耐磨性,而且还具有良好的耐机械冲击和热冲击性能,良好的耐热性、杭高温氧化性,耐蚀性以及高温硬度等等。
因而常被用于在苛刻环境中工作的磨件。
青铜合金除作为减摩材料用来制作轴承等零件外,也可作为耐磨材料使用,铝青铜是无锡青铜中应用最广泛的—种。
4.3硬质合金
硬质台金是由难熔金属的碳化物.如碳化钨、碳比钛、碳化铌等以铁族金属钴或镍等作粘结剂,用粉末冶金的方法制成的合金材料。
由于硬质合金具有高硬度、耐磨损、耐腐蚀及耐高温等一系列优点。
在现代工业生产中已经成为金属加工、矿山开采、石油钻探、国防、军工等不可缺少的重要工具材料[21]。
4结论
各种机械零件的磨损造成的材料和能源消耗是谅人的。
据不完全统计,我国每年磨损造成的损失达400亿元。
能源消耗仅大庆油田的粗略估计,每年总能耗的1/3—1/2是无功耗损。
美国每年由于摩擦磨损和腐蚀造成的损失约960亿美元,占国民经济总收入的4%。
在我国估计每年消耗金属耐磨材料300万吨以上。
应用摩擦磨损理论防止和减轻摩擦磨损,每年可节省150亿美元[22]。
近年来,针对各种设备部件磨损的具体工况和资源情况,研制出许多新型耐磨材料。
但仍有许多行业,如冶金矿山等,还大量沿用己过时的耐磨材料,所以对材料耐磨性的研究有重大了现实意义。
参考文献:
[1]王振廷,赵国刚,陈洪玉.磨料磨损与耐磨材料[M].黑龙江:
哈尔滨地图出版社,2004:
2-15.
[2]刘家浚.材料磨损原理及其耐磨性[M].北京:
清华大学出版社,1993:
92-220.
[3]孙建林.材料成形摩擦磨损与润滑[M].北京:
国防工业大学出版社,2007:
1-4.
[4]何奖爱,王玉玮.材料磨损与耐磨材料[M].辽宁:
东北大学出版社,2002:
1-14.
[5]续海峰.粘着磨损机理及其分析[J].机械管理开发,2007,1:
95-96.
[6]材料耐磨抗蚀及其表面技术丛书编委会.材料的磨料磨损[M].北京:
机械工业出版社,1990:
1-20.
[7]姜晓霞,等.金属的腐蚀磨损[M].北京:
化学工业出版社,2003.
[8]黄平.摩擦学教程[M].北京:
高等教育出版社,2008:
108-115.
[9]陈华辉.耐磨材料应用手册[M].北京:
机械工业出版社,2006:
30~70.
[10]刘正林.摩擦学原理[M].北京:
高等教育出版社,2009:
20~65.
[11]周叔良.材料耐磨性试验和评估[J].国外黄金参考,1998,11(12):
8-13.
[12]刘春廷,马继.材料力学性