40CrNiMoA拔叉齿轮热处理工艺设计.docx
《40CrNiMoA拔叉齿轮热处理工艺设计.docx》由会员分享,可在线阅读,更多相关《40CrNiMoA拔叉齿轮热处理工艺设计.docx(17页珍藏版)》请在冰豆网上搜索。
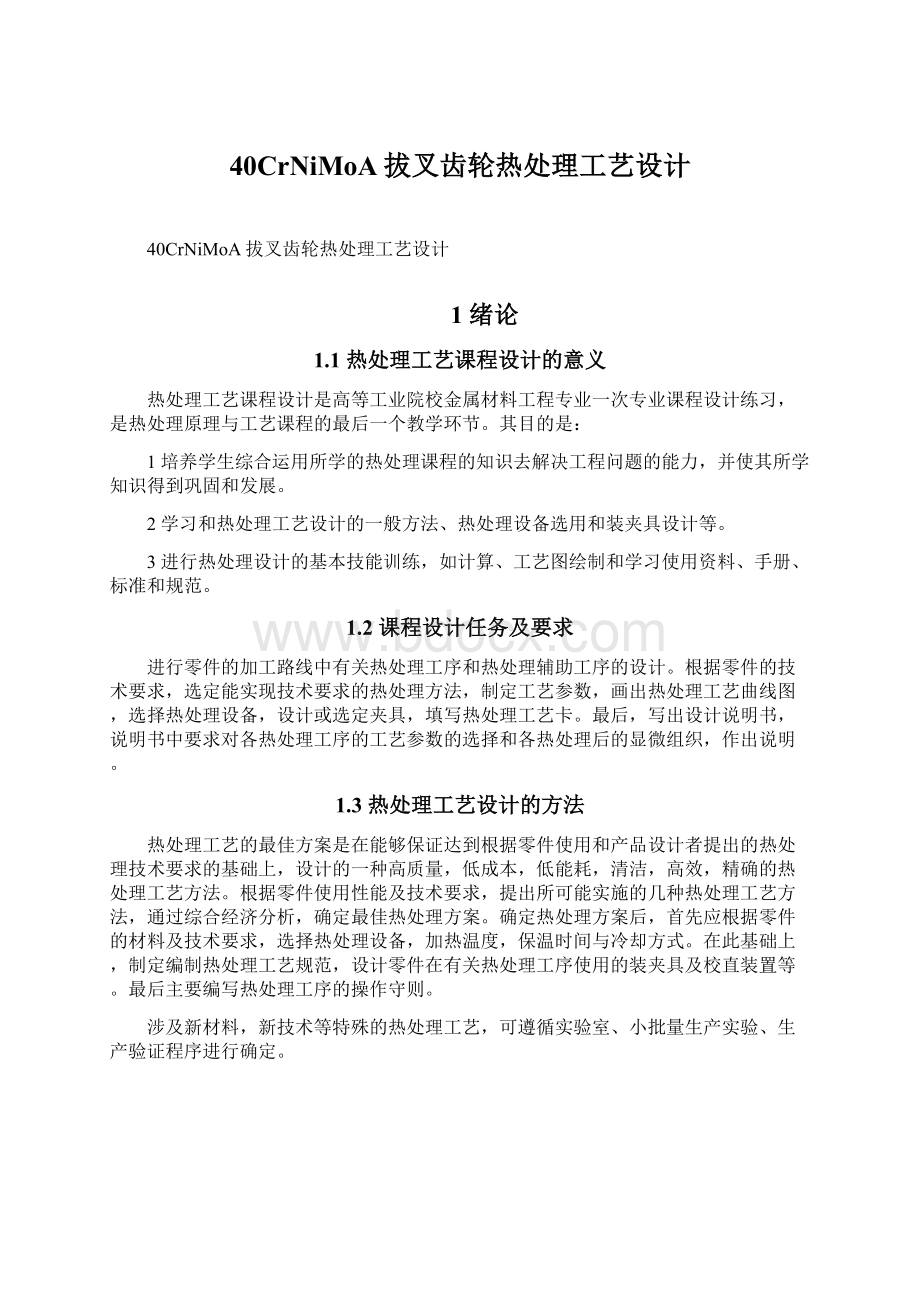
40CrNiMoA拔叉齿轮热处理工艺设计
40CrNiMoA拔叉齿轮热处理工艺设计
1绪论
1.1热处理工艺课程设计的意义
热处理工艺课程设计是高等工业院校金属材料工程专业一次专业课程设计练习,是热处理原理与工艺课程的最后一个教学环节。
其目的是:
1培养学生综合运用所学的热处理课程的知识去解决工程问题的能力,并使其所学知识得到巩固和发展。
2学习和热处理工艺设计的一般方法、热处理设备选用和装夹具设计等。
3进行热处理设计的基本技能训练,如计算、工艺图绘制和学习使用资料、手册、标准和规范。
1.2课程设计任务及要求
进行零件的加工路线中有关热处理工序和热处理辅助工序的设计。
根据零件的技术要求,选定能实现技术要求的热处理方法,制定工艺参数,画出热处理工艺曲线图,选择热处理设备,设计或选定夹具,填写热处理工艺卡。
最后,写出设计说明书,说明书中要求对各热处理工序的工艺参数的选择和各热处理后的显微组织,作出说明。
1.3热处理工艺设计的方法
热处理工艺的最佳方案是在能够保证达到根据零件使用和产品设计者提出的热处理技术要求的基础上,设计的一种高质量,低成本,低能耗,清洁,高效,精确的热处理工艺方法。
根据零件使用性能及技术要求,提出所可能实施的几种热处理工艺方法,通过综合经济分析,确定最佳热处理方案。
确定热处理方案后,首先应根据零件的材料及技术要求,选择热处理设备,加热温度,保温时间与冷却方式。
在此基础上,制定编制热处理工艺规范,设计零件在有关热处理工序使用的装夹具及校直装置等。
最后主要编写热处理工序的操作守则。
涉及新材料,新技术等特殊的热处理工艺,可遵循实验室、小批量生产实验、生产验证程序进行确定。
2材料的选择和要求
2.1课题工件简图
课题工件简图如图2.1所示
图2.1拔叉齿轮的示意图【1】
2.2技术要求
齿轮齿部及30H11槽部渗氮
调质:
250-280HBS
渗氮层深度:
0.35-0.55mm
表面硬度:
850-950HV
生产批量为:
5件
2.3钢材的介绍
合金结构钢简称合结钢,40CrNiMoA是合结钢的其中一种,也称合金钢,它是在优质碳素结构钢的基础上,适当地加入一种或数种合金元素(总含量不超过5%)而制成的钢种。
40CrNiMoA化学成分见表2.1。
表2.140CrNiMoA钢的化学成分[3](%)
C
Mn
Si
Cr
Ni
Mo
0.37~0.44
0.50~0.80
0.20~0.40
0.60~0.90
1.25~1.75
0.15~0.25
合金元素的作用如下:
主要加入的元素是Cr、Mo、Ni,加Cr的主要目的是为了提高淬透性,并有二次硬化作用增加高碳钢的耐磨性,还可以提高钢的耐回火性和抗氧化性,提高钢的热强性。
Mo的主要作用是提高钢的淬透性,提高热强性和蠕变温度。
并热硬性,原因是在淬火后的回火过程中,析出了这些元素的碳化物,使钢产生二次硬化。
加Mn主要是降低钢的下临界点,增加奥氏体冷却时的过冷度,细化珠光体组织以及改善其力学性能。
而Si是常用的脱氧剂,有固溶强化作用,提高钢的淬透性,抗回火性,对改善综合力学性能有利。
2.440CrNiMoA钢热处理临界温度
40CrNiMoA钢热处理临界温度及硬度范围见表2.2
表2.240CrNiMoA完全退火与正火加热温度及硬度范围[1]
相变临界点/℃
退火
正火
Ac1
Ac3
Ar1
加热温度/℃
硬度HB
加热温度/℃
硬度HB
760
810
-
840~880
≤269
890~920
220~270
3拔叉齿轮热处理工艺设计
3.1拔叉齿轮加工工艺路线
锻造毛坯—预备热处理—粗机械加工—去应力退火—精机械加工—调质处理(淬火-高温回火)—气体渗氮处理—检查
3.2预备热处理—等温退火
3.2.1等温退火目的及工艺
等温退火的加热温度与完全退火时大体相同,冷却时则在
一下的某一温度等温,使之发生珠光体转变,然后出炉空冷到室温。
由IT图可知,等温退火可以缩短退火时间,所得珠光体组织,也更加均匀。
具体工艺参数见表3.1
表3.140CrNiMoA等温退火工艺参数
奥氏体化温度/℃
冷却方式
随炉冷却(℃·
)
控制冷却
等温退火
由℃到℃
冷速/℃·
温度/℃
时间/t
830
28
704-666
8
649
8
3.2.2
T
温度
等温退火工艺曲线
图3.1等温退火加工工艺曲线
3.2.3装具的选择
相数为三,每次装炉三件,每件之间有一定距离,使工件充分加热,提高效率,装具如图3.2
装料口
图3.2装具
3.2.4热处理炉的选择
根据工件的尺寸和重量,选择高温井式电阻炉,设备的技术参数见表3.2
表3.2RJ2-40-9型中温井式电阻炉参数[2]
型号
RJ2-80-12
额定功率/KW
80
额定电压/V
380
额定温度/℃
1200
相数
3
工作空间尺寸(直径×深)/mm×mm
Φ800×1000
空路升温时间/h
≦3
空路损耗功率/KW
≦17
最大装载量/kg
800
3.2.5检验:
检验金相组织和硬度,方法见表3.3
表3.3检验方法[4]
项目
技术要求
检验方法
金相
组织
均匀珠光体
用金相显微镜检查,亚共析钢等温退火后的组织是铁素体+珠光体,共析钢是珠光体,过共析钢是珠光体+渗碳体
硬度
硬度≤223HBS
在模具试样零件侧面选取某点用布式硬度机测量其硬度值是否达标
脱碳
检验
零件单面脱碳层深不大于加工余量度的1/3
检验方法见GB/T224-1987《钢的脱碳层深度测定法》规定进行
变形
检验
变形量应不影响其后的机械加工和使用性能
工艺规定对拔叉进行测量
3.3淬火工艺
3.3.1淬火的目的以及工艺参数
是使过冷奥氏体进行马氏体或贝氏体转变,得到马氏体或贝氏体组织,然后配合以不同温度的回火,以大幅提高钢的强度、硬度、耐磨性、疲劳强度以及韧性等,从而满足各种机械零件和工具的不同使用要求。
淬火温度:
850±10℃
依据:
Ac3+(30~50)℃。
加热方法:
采用当炉温加热到850℃时,将工件装进热处理炉进行加热。
原因是加热速度快,节约时间,便于批量生产。
保温时间:
4.5h
选定依据:
加热时间可按下列公式进行计算:
t=
×K×D[4]
t为加热时间(min或h)。
为加热系数[3],合金钢空气电阻炉取1.3~1.6min/mm,这里取1.5min/mm。
D为零件有效厚度:
其中D为160mm。
K为装炉条件修正系数[3],通常取1~1.5,这里取1。
由公式可知,t=
×K×D=1.5×1.0×160=240min,取4h。
3.3.2冷却方法
由于工件淬火温度较高,淬火介质选用油质淬火剂,不会由于工件与油的接触导热提高油温而降低冷却能力。
使工件能淬成马氏体,又不致引起太大的淬火应力。
将加热保温后的工件,直接淬火机油中,80℃热油对900~1000℃(碳化物析出最敏感区)工件具有较快的冷却速度。
淬火后得到细小晶粒的马氏体组织。
冷却介质为20号机械油。
选择依据:
油的闪点是指油表面的蒸汽与空气自然混合时,与火接触而出现火苗的温度,它的温度的高低,对淬火零件的安全性有一定的影响。
油的序号越高,则黏度越大,闪点越高。
一般在150-300℃。
常见矿物油的闪点见表3.4
表3.4常见矿物油的闪点
油号
闪点/℃
10
165
20
170
30
180
40
190
3.3.3热处理炉的选择
根据工件的尺寸和重量,选择高温井式电阻炉,设备的技术参数见表3.5
表3.5RJ2-80-12型高温井式电阻炉参数[2]
型号
RJ2-80-12
额定功率/KW
80
额定电压/V
380
额定温度/℃
1200
相数
3
工作空间尺寸(直径×深)/mm×mm
Φ800×1000
空路升温时间/h
≦3
空路损耗功率/KW
≦17
最大装载量/kg
800
3.3.4
850±10℃
淬火工艺曲线
通过高温回火获得具有一定的强度、硬度和良好的韧性、塑性相配合的综合机械性能。
高温回火,即调制处理,得到回火索氏体。
具有较低的硬度、强度和较高的塑性和韧性。
回火温度:
600±10℃,取600℃。
保温时间:
4-5h
依据:
在空气炉中回火,见表3.6
表3.6回火时间参考表[4](单位:
min)
零件的有效厚度/mm
﹤25
25~50
50~75
75~100
100~125
125~150
高温回火
450~650℃
盐炉
10~30
30~45
45~75
75~90
90~120
120~150
空气炉
40~70
70~100
100~140
140~180
180~210
210~240
注:
合金钢的保温时间按上述表所列时间增加20-30%
3.3.5冷却方式
具有第二类回火脆性的合金钢,经450-650℃回火后在油或水中进行快冷,以免出现回火脆性。
3.3.6热处理炉的选择
根据工件的尺寸和重量,选择低温井式电阻炉,设备的技术参数见表3.7
表3.7RJ2-55-6型低温井式电阻炉参数[2]
型号
RJ2-55-6
额定功率/KW
55
额定电压/V
380
额定温度/℃
650
相数
3
工作空间尺寸(直径×深)/mm×mm
Φ700×900
空路升温时间/h
≦1.2
空路损耗功率/KW
≦7.0
最大装载量/kg
750
3.3.7高温回火工艺曲线
3.3.8得到的组织
得到回火索氏体,具有较低的硬度、强度和较高的塑性和韧性。
3.3.9检验
需要检验金相组织、表面和心部硬度、工件的抗压强度,见表3.8
表3.8检验方法[4]
项目
技术要求
检验方法
金相组织
细小、均匀的回火索氏体组织
用金相显微镜检查
硬度检验
250~280HBS
通过加载将钢球压头压入被检测的金属零件表面,根据单位压痕面积上所受的负荷大小来确定硬度值。
HB=P/F=P/DtπF:
凹陷压痕的面积t:
压痕凹陷的深度检测面应是光滑平面。
抗压强度检验
有一定的抗压强度,σbc≥150MPa
试验在普通万能材料试验机进行,当对工件施加到150Mpa压力时,仍未开裂的话,说明它达到技术要求
3.4渗氮
3.4.1渗氮的特点
140CrNiMoA系中碳合金钢渗碳后,表面硬度很高,1000-1100HV,相当于65-72(HRC),具有良好的耐磨性,这种性能可保持在600℃左右不下降。
特别是铝元素的加入,渗氮后表面硬度很高,耐磨性很好;
2具有高的疲劳强度和抗腐蚀性
3氮化处理温度较低(450-600℃),零件的变形极小,氮化后渗层直接获得高硬度,避免了淬火引起的变形。
3.4.2选择渗氮的目的
提高工件齿部高的耐磨性及一定得强度,同时心部要有一定的塑韧性。
此件采用两段渗氮工艺,就是为了缩短渗氮周期,加快渗氮速度,降低渗层脆性。
3.4.3渗氮前的热处理
渗氮本质上是一种时效强化,是在氮化过程中完成的,所以渗氮后不需要再进行热处理,而氮化零件的心部性能是由氮化前的热处理决定的。
氮化前的热处理一般都是调质处理。
在确定调质工艺时的淬火温度由钢的Ac3决定,淬火介质由钢的淬透性决定,回火温度的选择不仅要根据心部硬度要求,而且还必须考虑其对氮化结果的影响。
一般来说,回火温度低,不仅心部硬度高且氮化层硬度也较高,因而有效深层深度也会有所提高(具体见以上淬火、回火工艺)。
3.4.4渗氮工艺参数
渗氮温度:
第一段520±10℃,第二段545±10℃。
选择依据:
480-570℃。
常用510-560℃,渗氮温度越高,扩散速度越快,渗层越深。
当需要去应力处理时,最高去应力处理温度应低于调质回火温度20-30℃,最高渗氮温度应低于去应力处理温度20-30℃
渗氮时间:
第一段15-20h,取18h。
第二段10-15h,取15h。
选择依据:
见下表3.10气体渗氮工艺的确定原则。
表3.9渗氮时间
阶段
温度/℃
时间/h
氨分解率(%)
深层深度/mm
1
520±10
20
25-35
0.40-0.70
2
545±10
10-15
35-50
氨分解率:
第一段25-30%,第二段40-50%。
选择依据:
渗氮温度一定时,氨流量增大,分解率减小;氨流量减小,分解率增大。
不同温度下氨分解率的合理范围见下表3.9
表3.10气体渗氮工艺的确定原则
渗氮温度/℃
500
520
540
550
560
氨分解率%
25-30
30-35
35-40
40-45
45-50
3.4.5渗氮炉中的气氛
合水<0.2%的液氨,用氨直接渗氮,使用方便。
选用RN-75-6井式气体渗氮炉,井式气体渗氮炉结构见图3.4,设备的技术参数见表3.11
表3.11RN-75-6井式气体渗氮炉参数[2]
型号
RN-75-6
额定功率/KW
75
额定电压/V
380
额定温度/℃
650
相数
3
工作空间尺寸(直径×深)/mm×mm
Φ800×1300
空路升温时间/h
≦2
3.4.6渗氮工艺曲线
3.4.7渗氮后的组织
表层为氮化索氏体+细小网状氮化物,心部为索氏体。
渗氮层表面是氮化物,在100×金相显微镜下观察到亮白色的就是通常所说的白亮层,为化合物层,为ε相;次层是基体上弥散分布的γ`相,扩散层,黑色;与中心索氏体有明显交界的是α+γ`组织。
3.4.8检验
检验,如表3.11所示。
表3.11渗氮后的检验方法[4]
检验项目
检验内容与方法
渗氮层深度的测定
金相法:
在垂直表面的方向上做一金相磨面,腐蚀后,既可在放大镜下,也可在显微镜下做渗层的测定,测定为0.35-0.55mm,符合要求
渗氮层硬度的测定
用维式硬度计或表面化洛氏硬度计测定,为850-950HV
渗氮层脆性的测定
根据维式硬度压痕的形状来确定渗氮层的脆性,一般定义一边或一角有碎裂为2级,测定为2级,合格
原始组织
渗氮前原始组织为回火索氏体
3.5
总的热处理工艺曲线
4热处理工序中材料的组织、性能分析
4.1淬火工艺中的组织转变
1正常加热冷却:
工件加热到940℃后珠光体转变成奥氏体,保温时组织不变,晶粒细化,出炉油冷至室温时,得到马氏体+残余奥氏体+碳化物(少量),具有很高的耐磨性和硬度。
2加热温度不足时,即不能完全奥氏体化,会显著降低工件的硬度。
3加热温度过高时,表面粗大马氏体+过多的残余奥氏体,心部粗大马氏体+铁素体+索氏体,残余奥氏体过多,零件尺寸不确定,硬度及耐磨性降低,磨削时易于开裂。
4冷却速度过大时,大量的过冷残余奥氏体冷却到室温易发生分解,工件易开裂。
5冷却速度过小时,可能出现贝氏体转变,表面硬度会降低,韧性增大。
4.2回火工艺中的组织转变
1正常加热冷却:
工件加热到650℃后组织为马氏体+碳化物,保温时组织发生分解,析出碳化物。
室温时组织为回火索氏体。
硬度高,塑性有所提高,但依然较低。
2加热温度不足时,回火马氏体+大量的残余奥氏体+碳化物,表现出明显的脆性。
加热温度过高时,回火索氏体或回火屈氏体,强度、硬度降低,韧性显著提高,可能出现二次回火脆性。
3冷却速度过大的,大量的残余奥氏体来不及分解,强度、硬度降低;冷却速度过小时,残余奥氏体的含量减少,回火马氏体的量增加,工件易开裂。
4.3渗氮工艺中的组织转变
正常加热冷却:
表层Fe4N相高度弥散分布在回火索氏体心部,调质回火索氏体组织。
化合物层是由铁和氮的金属化合物组成的薄层。
主要有γ′、γ′+ε、ε、ε+γ′+Fe3C、ε+Fe3C和ε+γ′+Fe3O4等几种形式。
γ′相是面心立方晶格的金属间化合物Fe4N,具有足够的耐磨性和良好的韧性。
ε相是六方晶格的金属间化合物Fe2-3N,具有良好的耐磨性、抗蚀性和一定的韧性。
一般认为,单相的化合物层不但具有高硬度,而且具有较好的韧性,其中γ′相的韧性又胜过ε相,但若出现混合相γ′+ε的化合物层则是脆性的。
在化合物层以内,随着氮的扩散而形成扩散层。
扩散层基本由氮αN+γ′+Fe3C组成。
5热处理缺陷及措施
5.1淬火缺陷及其产生的原因及预防措施
1硬度不足
产生原因:
亚共析钢加热不足,有未溶铁素体;冷却速度不够;在淬火介质中停留时间不够;氧化和脱碳导致淬火后的硬度降低。
预防措施:
正确选择并严格控制加热温度,保留时间和炉温的均匀性;合理选择淬火介质;控制淬火介质的温度不超过最高使用温度;定期检查或更换淬火介质。
正确控制在淬火介质中的停留时间。
采取防氧化脱碳措施;采用下线加热温度;在600℃左右预热,然后再加热到淬火温度,缩短高温加热时间。
2软点
产生原因:
原材料中存在带状组织或大块铁素体组织;冷却不均。
预防措施:
合理选材,对有缺陷的钢材进行预备热处理,以消除缺陷;加热工件与介质的相对运动或对介质进行搅拌;保持淬火介质的清洁;合理选择淬火介质。
3畸变和开裂
产生原因:
淬火过程中某一瞬间热应力和组织应力的综合作用大于钢的屈服强度时,就会产生畸变;当两种应力的综合作用超过钢的抗拉强度时,则引起开裂。
预防措施:
合理选择钢材与正确设计结构;正确锻造和进行预备热处理;采用去应力退火;合理的热处理规范。
5.2回火缺陷及其产生的原因及预防措施
1回火硬度偏高或偏低
产生原因:
回火温度或低或高;保温时间短;淬火组织中有非马氏体组织(偏低)。
预防措施:
提高或降低回火温度;按规定时间保温;改进淬火工艺,重新淬火。
2硬度不均匀
产生原因:
回火温度不均匀;装炉量大。
预防措施:
采用有气流循环的设备回火;适当减小装炉量。
3回火畸变
产生原因:
由回火内应力而引起。
预防措施:
采用回火校正法校正。
4回火脆性
产生原因:
回火间脆性回火;高温回火引起第二类回火脆。
预防措施:
避开第一类回火脆性区回火;高温回火后快速冷却。
5回火开裂
产生原因:
淬火后未及时回火行程显微裂纹,在回火过程中开裂。
预防措施:
减小淬火应力,淬火后及时回火。
5.3退火缺陷及其产生的原因及预防措施
1过烧
产生原因:
加热温度过高,使晶界局部熔化。
预防措施:
报废。
2过热
产生原因:
加热温度过高,使奥氏体晶粒长大,冷却后形成魏氏组织或粗晶组织。
预防措施:
完全退火。
3出现粗大块状铁素体
产生原因:
冷却速度太慢。
预防措施:
冷却速度控制在30℃以上。
4奥氏体析出二次渗碳体
产生原因:
退火温度高,在缓慢冷却过程中二次渗碳体会沿奥氏体晶界析出,并网状分布。
预防措施:
过共析钢退火温度不可高于Accm。
5.4气体渗氮的缺陷及其产生原因及预防措施
1渗氮层硬度低
产生原因:
渗氮温度高;分段渗氮时,第一阶段氨分解率偏高;使用新渗氮罐时未经预渗氮;渗氮罐久用未退氮。
预防措施:
校正测温仪表,严格控制渗氮工艺参数;严格控制氨分解率;加大氨气流量;渗氮罐每渗氮10炉后,应在800-860℃空载保温2-4h,进行一次退氮处理。
2渗氮层厚度不均匀
产生原因:
炉温不均匀;炉气循环不畅;装炉量太大;工件表面有油污。
预防措施:
注意均匀装炉;保持间隙,保证炉气循环畅通;合理装炉;认真清洗工件表面。
3渗氮层深度浅
产生原因:
渗氮温度低;时间不足;渗氮第二阶段氨分解率低;渗氮罐久用未退氮;装炉量太大,炉气循环不良。
预防措施:
提高渗氮温度;保证渗氮时间;提高氨分解率,按第二段工艺规范重新处理;渗氮罐每渗氮10炉后,应在800-860℃空载保温2-4h,进行一次退氮处理;均匀装炉,工件间隙不小于5㎜,保证炉气循环畅通。
4渗氮层脆性太大或易剥落
产生原因:
氨分解率低;炉气氮势高;退氮工艺不当;工件表面有脱碳层;工件有尖角、锐边。
预防措施:
严格控制氨分解率;按工艺规范操作;将氨分解率提高到70%以上,重新进行退氮处理,以降低脆性;增大加工余量;尽可能将尖角、锐角倒圆。
5畸变
产生原因:
消除机械加工应力不充分;装炉方式不合理;加热或冷却速度太快,热应力大。
预防措施:
渗氮前充分消除应力;合理装炉,注意工件自重的影响;严格控制淬火温度。
6参考文献
[1]《典型零件热处理技术》.王忠诚、齐宝森、李扬.化学工业出版社,2010年6月第二版
[2]《热处理工程师手册》.樊东黎、徐跃明、佟晓辉.机械工业出版社,2010年6月第二版
[3]《工程材料学》.王晓敏.哈尔滨工业大学出版社,2005年3月第三版《实用热处理技术手册》.杨满.机械工业出版社,2010年6月第一版
[4]《实用热处理技术手册》.杨满.机械工业出版社,2010年6月第一版
[5]《实用热处理手册》.上海市热处理协会编.上海科技出版社,2009年1月第二版
[6]《热处理工实用技术手册》.樊新民.江苏科学技术出版社,2010年1月第二版
[7]《钢的热处理(修订版)》.胡光立、谢希文.西北工业大学出版社,1996年3月第一版
[8]《钢铁热处理实用技术》.胡光立.化学工业出版社.2008年4月第三版
[9]《金属学与热处理》.刘宗昌.化学工业出版社.2008年8月第一版
7心得体会
通过这次热处理工艺设计,我了解了具体工艺编写过程及操作的具体步骤。
工艺的每一步都要有标准依据又要考虑到实际情况。
这一段课程设计中,有老师的指导、自己的努力,我学的了不少东西,工艺设计程序,实际中的应用,同时使自己感到学无止境,自己懂得东西太很少,还需要加倍学习。
这次的课程设计,为下学期的毕业设计进行了一部分知识上的储备,学到了很多关于热处理方面的知识,还有有关计算机软件的一些知识丰富了自己。
感谢各位老师的辛勤付出,也感谢老师给了我们这么好的一次锻炼自己的机会!