氢脆现象对螺纹紧固件强度的影响.docx
《氢脆现象对螺纹紧固件强度的影响.docx》由会员分享,可在线阅读,更多相关《氢脆现象对螺纹紧固件强度的影响.docx(6页珍藏版)》请在冰豆网上搜索。
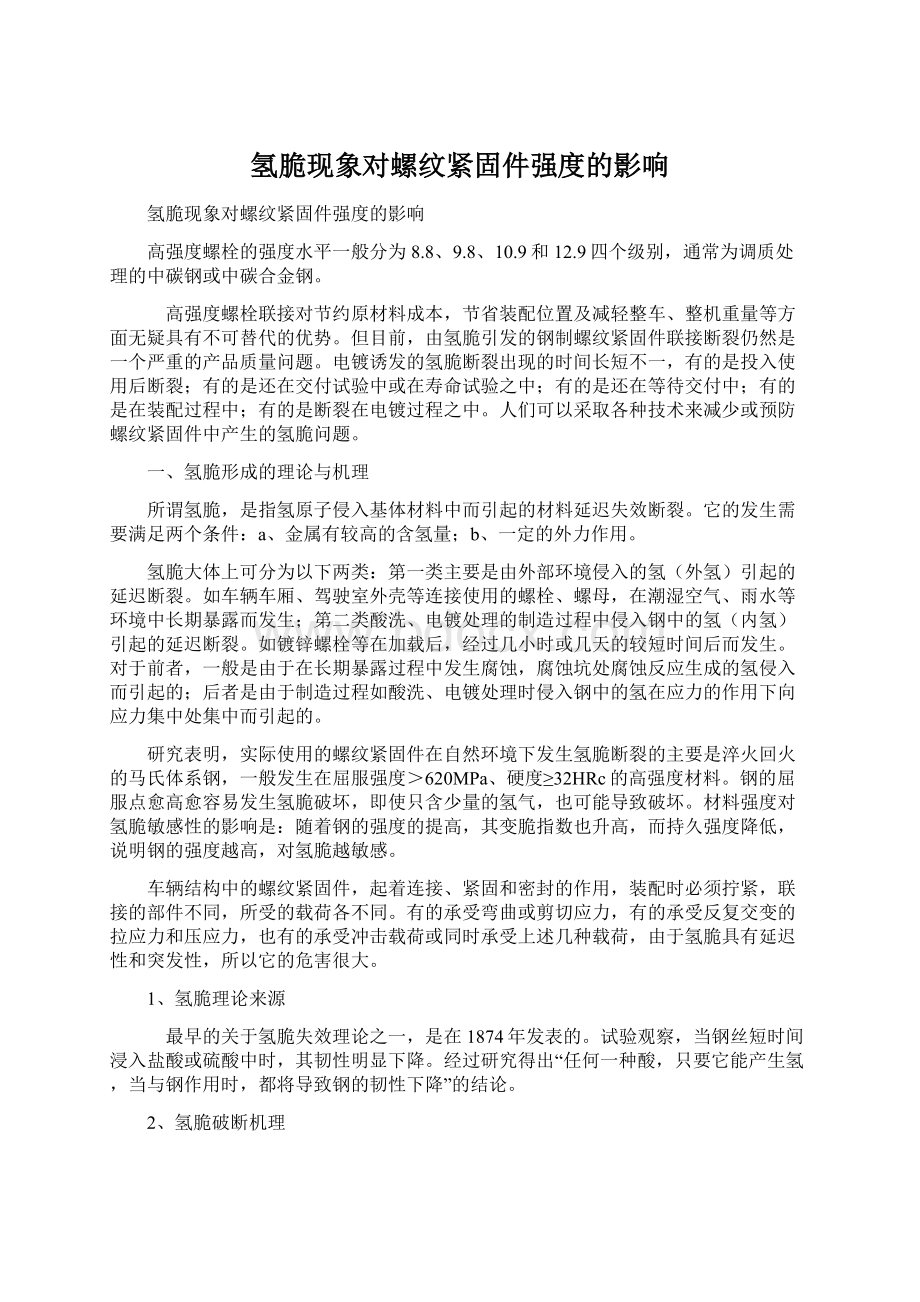
氢脆现象对螺纹紧固件强度的影响
氢脆现象对螺纹紧固件强度的影响
高强度螺栓的强度水平一般分为8.8、9.8、10.9和12.9四个级别,通常为调质处理的中碳钢或中碳合金钢。
高强度螺栓联接对节约原材料成本,节省装配位置及减轻整车、整机重量等方面无疑具有不可替代的优势。
但目前,由氢脆引发的钢制螺纹紧固件联接断裂仍然是一个严重的产品质量问题。
电镀诱发的氢脆断裂出现的时间长短不一,有的是投入使用后断裂;有的是还在交付试验中或在寿命试验之中;有的是还在等待交付中;有的是在装配过程中;有的是断裂在电镀过程之中。
人们可以采取各种技术来减少或预防螺纹紧固件中产生的氢脆问题。
一、氢脆形成的理论与机理
所谓氢脆,是指氢原子侵入基体材料中而引起的材料延迟失效断裂。
它的发生需要满足两个条件:
a、金属有较高的含氢量;b、一定的外力作用。
氢脆大体上可分为以下两类:
第一类主要是由外部环境侵入的氢(外氢)引起的延迟断裂。
如车辆车厢、驾驶室外壳等连接使用的螺栓、螺母,在潮湿空气、雨水等环境中长期暴露而发生;第二类酸洗、电镀处理的制造过程中侵入钢中的氢(内氢)引起的延迟断裂。
如镀锌螺栓等在加载后,经过几小时或几天的较短时间后而发生。
对于前者,一般是由于在长期暴露过程中发生腐蚀,腐蚀坑处腐蚀反应生成的氢侵入而引起的;后者是由于制造过程如酸洗、电镀处理时侵入钢中的氢在应力的作用下向应力集中处集中而引起的。
研究表明,实际使用的螺纹紧固件在自然环境下发生氢脆断裂的主要是淬火回火的马氏体系钢,一般发生在屈服强度>620MPa、硬度≥32HRc的高强度材料。
钢的屈服点愈高愈容易发生氢脆破坏,即使只含少量的氢气,也可能导致破坏。
材料强度对氢脆敏感性的影响是:
随着钢的强度的提高,其变脆指数也升高,而持久强度降低,说明钢的强度越高,对氢脆越敏感。
车辆结构中的螺纹紧固件,起着连接、紧固和密封的作用,装配时必须拧紧,联接的部件不同,所受的载荷各不同。
有的承受弯曲或剪切应力,有的承受反复交变的拉应力和压应力,也有的承受冲击载荷或同时承受上述几种载荷,由于氢脆具有延迟性和突发性,所以它的危害很大。
1、氢脆理论来源
最早的关于氢脆失效理论之一,是在1874年发表的。
试验观察,当钢丝短时间浸入盐酸或硫酸中时,其韧性明显下降。
经过研究得出“任何一种酸,只要它能产生氢,当与钢作用时,都将导致钢的韧性下降”的结论。
2、氢脆破断机理
氢脆破断机理目前分别有氢气压力假说、位错假说、氢吸附假说和晶格脆化假说。
氢原子具有最小的原子半径(RH=0.53A°),所以易于进入金属内部.当在一定的应力(包括外加的、残余的以及原子之间的相互作用力)作用下,在局部的应力集中处产生滑移和塑性变形,进而产生微裂纹核。
在已有裂纹前沿的三向应力区域内,由于位错的塞积而产生微裂纹核,这些微裂纹核如果没有氢的进一步作用,当裂纹继续向内深入扩展所需的活化能超过这种深入扩展所能引起的应变能的降低时,这种裂纹一般是不会扩展的。
但当钢中溶有一定氢的情况下,氢原子继续在微裂纹中扩散、聚集,由两个氢原子变成一个氢分子,H++e→H、2H→H2↑,同时体积增大,即一个氢分子的体积比两个氢原子的和大。
此时在氢聚集的部位会产生巨大的体积膨胀效应,导致许多微裂纹相互合并,并与原有裂纹连接,微裂纹继续向前扩展,这样不断循环,直到剩余的有效截面小到不能支持外载荷时,即发生瞬时断裂失效。
裂纹扩展的方向将决定于内应力或外加应力的方向,但使钢件氢脆失效所需的力则主要来自氢。
由于氢在金属中扩散需要一定时间,裂纹扩展也有一定的速率,因此氢脆破断存在着潜伏期。
应力愈大微裂纹的生核率愈大,裂纹的扩展速率也愈大,则氢脆破断的潜伏期也愈短。
当应力小于氢脆破断的下限应力时,不能造成必要的应力集中,并推动位错的运动和造成大量的位错塞积,因而也不能产生微小的裂纹核,即使能生成个别的裂纹核也不能相互合并或连接,当金属的屈服强度极限很高时,裂纹尖端的应力集中系数就大,微裂纹的生核率就高,裂纹扩展速度就快,就容易产生氢脆。
二、氢脆发生的环节
影响氢脆现象的因素有多种,即氢脆的发生环节。
如:
基体材料的机械和物理性能、扩散比、温度、氢的聚集、零件表面状况、应力水平、应力状态、活动裂纹前端的动力学特性等等。
螺纹紧固件,尤其是高强度紧固件经材料改制→冷镦成型→滚搓螺纹→调质热处理→磨削或机加工后,再进行表面处理,极易受氢脆的破坏。
表色工序中的酸洗、电镀是产生氢脆关键的因素之一。
1、热处理
对于高强度螺纹紧固件,尤其是10.9级和12.9级螺栓,不但使用中碳合金结构钢,而且还要进行调质热处理。
对于自攻螺钉、自攻锁紧螺钉等,都要求进行浅层渗碳(碳氮共渗)。
为了避免加热中螺纹氧化、脱碳,且得到光亮和光洁的表面,采用保护气氛或渗碳气氛,气氛常采用高纯度甲醇经高温催化裂解:
CH3OH→CO+2H2,炉内气氛成分H2(64%)、CO(32%)、CO2(﹤1%)、CH4(0.2%)、CH3OH(余量)。
在淬火加热和渗碳(碳氮共渗)时,较高的加热温度下,氢很容易渗入工件应力集中的区域(如螺栓头杆结合处)。
渗入钢中的氢一般以原子状态存在,但为降低能量,总是与杂质原子、位错、空位、晶粒边界及滑移带等相互作用,并力图结合成氢分子。
氢的这一行为对钢的氢脆破坏有重要影响。
2、酸洗
紧固件用户市场对紧固件表面的要求越来越高(即要求紧固件表面具有特殊的处理、防蚀性、均一的摩擦系数和起动扭矩等)。
表面处理除发黑外,通常是电镀、有机和无机物涂覆或磷化,所有这些工艺都有一个共同的前提,必须除去紧固件表面黑色氧化层,使金属具有光亮。
为此,就必须对紧固件进行酸洗。
酸洗是把紧固件放在稀盐酸中搅动1--10min。
酸洗是紧固件电镀过程中产生渗氢作用的主要环节,紧固件在酸洗时存在反应:
Fe+2HCl=FeCl2+H2↑。
在酸洗中钢所吸收的氢是随时间的平方根而成线性增长达到饱和值,在PH值较低的溶液中其饱和值较高,而PH值较高则饱和值较低。
3、除油
在电镀除油过程中渗氢的环节主要存在于电镀除油中,由于阴极除油的速度较快,多数企业采取阴极和阴阳交替联合除油。
但阴极除油过程会产生大量的氢原子,附着在紧固件表面,从而产生渗氢。
4、电镀
镀锌过程中,阴极上除了锌的沉积外还有氢的析出。
因此,镀锌时同时会产生渗氢现象。
但由于锌有阻止氢渗透作用,当紧固件表面沉积一薄层锌后,该镀层将阻碍氢原子向紧固件内部扩散。
同理,若紧固件在镀锌前已有渗氢,镀锌后其内部的氢亦不易逸出。
三、氢脆的消除
为了减小氢脆倾向,应从材料和工艺的角度考虑。
1、材料与热处理
首先尽量选择氢脆倾向小的钢材,应尽量选用含Mo的合金结构钢。
Mo具有抑止氢扩散的能力,从而可以抑止氢脆破断的产生,减少氢脆的危害。
如可用SCM435(35CrMo)、SCM440(42CrMo)或ML20MnTiB钢制造10.9级、12.9级高强度紧固件。
在进行紧固件调质热处理时,加热炉内应保证有足够的保护气氛,碳势在0.35%--0.45%的前提下,尽量减少载气富化气的供给量,使炉内氢的浓度降低,也就使紧固件中氢的渗入量减少。
适当降低淬火加热温度,由于氢在金属中的溶解度与温度有关,所以降低温度,可减少紧固件的吸氢量,对SCM435(35CrMo)、SCM440(42CrMo)钢淬火或复碳工艺,加热温度一律控制在850℃(淬火)--870℃(复碳)。
对自攻螺钉、自攻锁紧螺钉渗碳(碳氮共渗)时,碳势控制在0.90%--1.10%。
在保证螺纹紧固件达到各项力学性能指标的基础上(尤其把强度和保证应力控制在合格范围内),如对汽车高强度螺栓的硬度控制在中间差范围内,可取得实际的效果,见表1。
表1 高强度螺栓技术要求控制范围
螺栓级别
螺栓规格/mm
硬度控制范围/HRC
抗拉强度控制范围/Mpa
8.8级
≤M8
26~29
830~880
>M10且≤M16
27~31
850~900
>M16
29~33
870~920
10.9级
≤M8
34~36
1050~1100
≥M10且≤M16
35~37
1080~1120
>M16
36~39
1100~1150
12.9级
≤M12
39~41
1220~1280
≥M14且<M24
40~42
1250~1300
≥M24
39~40
1250~1330
2、酸洗与电镀
在满足螺纹紧固件技术条件的情况下,可采用不会造成渗氢的涂层,如机械镀锌、无铬锌铝涂层和电泳涂层,不会发生氢脆,耐蚀性高、附着力强,且比电解镀锌环保。
而在一般以防蚀、防腐及装饰为主要目的,而进行电解镀锌,对硬度≥32HRC的螺纹紧固件,镀层厚度应控制在≤8μm。
高强度紧固件的清洗、去除氧化皮等最好应用喷丸、喷砂清理,或者是三氯乙烯清洗、阳极清洗等方法,必须尽量避免使用导致氢脆性的酸洗(阴极清洗)方法。
a.高强度紧固件(如波形弹垫、锥形弹垫)一般不进行强酸洗。
b.对于抗拉强度≥1200MPa的紧固件不允许用强酸洗,抗拉强度在1000MPa以上的螺纹紧固件,酸洗时间尽量减少,控制在1--3min。
c.酸洗所用酸的浓度不宜太高,在3%--5%之间为佳。
四、镀后驱氢与氢脆检查
氢损伤或氢脆的表现形式有两种,一般可以分为不可逆氢脆和可逆氢脆,前者指氢造成永久性损伤,其缺陷是氢致鼓泡,或材料中出现白点、发纹等;可逆氢脆是指排除氢后力学性能可以恢复的氢脆现象。
高强度紧固件的金相组织显示一般都属于可逆氢脆,可通过镀后驱氢消除氢脆。
用美国LECO测氢仪测量GB5782M10×70外六角螺栓不经镀锌处理,螺栓的氢含量不足1×10-6,酸洗之后测得的氢含量只有轻微增加。
35、ML35和SCM435钢的氢含量不足1×10-6,而在镀锌之后,测得氢含量分别超过了5.5×10-6、6.5×10-6和1.0×10-6。
把氢含量为5.5×10-6的35钢和氢含量1.0×10-6的SCM435钢镀锌螺栓,去除镀层后测得氢含量仅为0.2×10-6和0.96×10-6,这说明电镀处理产生的氢大部分都驻留在镀层中,而不是在基体材料中。
氢含量的试验表明,酸洗将少量的氢渗入到材料中,而电镀处理试样中的氢含量要比酸洗试样中的氢含量多得多,且氢主要驻留在镀层中
驱氢处理使导致氢损伤减小的机理还在探讨,但从以上3种材料驱氢试验后断裂应力的恢复表明,驱氢处理是减小氢脆损伤的有力对策。
尽管在驱氢处理中只除去了很小一部份氢,驱氢处理可使钢中的氢重新分布,并使之不易于聚集到较为危险的陷阱位置,也就是说驱氢处理可以防止螺纹紧固件中的氢聚集到应力集中的部位
由于温度可提高氢在钢中的扩散系数,因此,150--200℃保温可以排除氢脆,但温度过高,例如,400℃以上,氢在钢中溶解度也增加,氢不再自动从钢中逸出,达不到驱氢的目的。
1、镀后驱氢
驱氢处理是一种能够使氢的聚集减少到氢脆临界水平以下的处理方法。
为防止产生氢脆,高强度紧固件必须在镀后规范驱氢工艺,其要求为:
a.驱氢越早开始越好,在紧固件镀锌后,未钝化之前进行。
b.电镀至驱氢的间隔时间,抗拉强度≥1200MPa的紧固件,不得大于1h;抗拉强度在800-1180MPa的工件不得大于2h。
驱氢时间从达到规定的温度时开始计算。
c.对带洛氏硬度在≥45HRC的弹性垫圈的组合件,不论性能等级,电镀在190--210℃;磷化在140-160℃驱氢处理,驱氢时间8--12h,而其它紧固件可根据性能等级,驱氢工艺见表2。
表2 驱氢工艺一览表
紧固件性能等级
表面处理状态
驱氢温度/℃
最短驱氢时间/h
9.8/10.9级螺钉螺栓
镀锌
190~210
4
10.9级自攻锁紧螺栓
6
10.9级螺栓
磷化
140~160
6
9.8/10.9级自攻锁紧螺钉
自攻螺钉
4
2、氢脆检查
a.平行支承面法
通常将紧固件放在试验夹具上,紧固件承受的应力应在屈服点以内,或者处在破坏扭矩的范围内,至少保持48h,每隔24h应将紧固件再次施加该扭矩,然后再保持24h。
松开后同样检查紧固件是否因氢脆已发生破坏。
若将紧固件拧入带有楔角(4°或6°)的平板,可以大大提高这种试验的可靠性。
b.气泡法
目前有一种非常简便的方法测定驱氢效果,具体方法如下:
将家用小电炉接通电源,上面放一石棉瓦,把盛有适量凡士林的烧杯置于石棉瓦上,均匀加热至凡士林完全融化,(凡士林量应以融化后能完全浸没紧固件为准),并保持在100—110℃,约5min,以完全去除其中的水分。
然后将紧固件上的油迹和水清除干净,放入凡士林液中,若在10s内凡士林中有气泡产生,就证明该紧固件含有一定量的氢。
五、后语
螺纹紧固件的氢脆问题已是国内外相关行业重要研究课题之一。
在紧固件国内外标准、设计中已有了一些规定,尽管这还不够完善。
但在国内,特别是紧固件企业对此的了解和重视尚显不足,需要人们继续探讨和研究。
氢脆现象是妨碍螺纹紧固件高强度化的一个重要因素,防止电镀诱发的氢脆断裂事故最重要的措施,是严格执行科学的驱氢工艺,只有从材料、热处理、电镀、研发和测试等诸方面持续改进、完善,才能满足市场对紧固件不断增长的需求。