喷油泵齿轮轮毂专用钻削头说明书.docx
《喷油泵齿轮轮毂专用钻削头说明书.docx》由会员分享,可在线阅读,更多相关《喷油泵齿轮轮毂专用钻削头说明书.docx(19页珍藏版)》请在冰豆网上搜索。
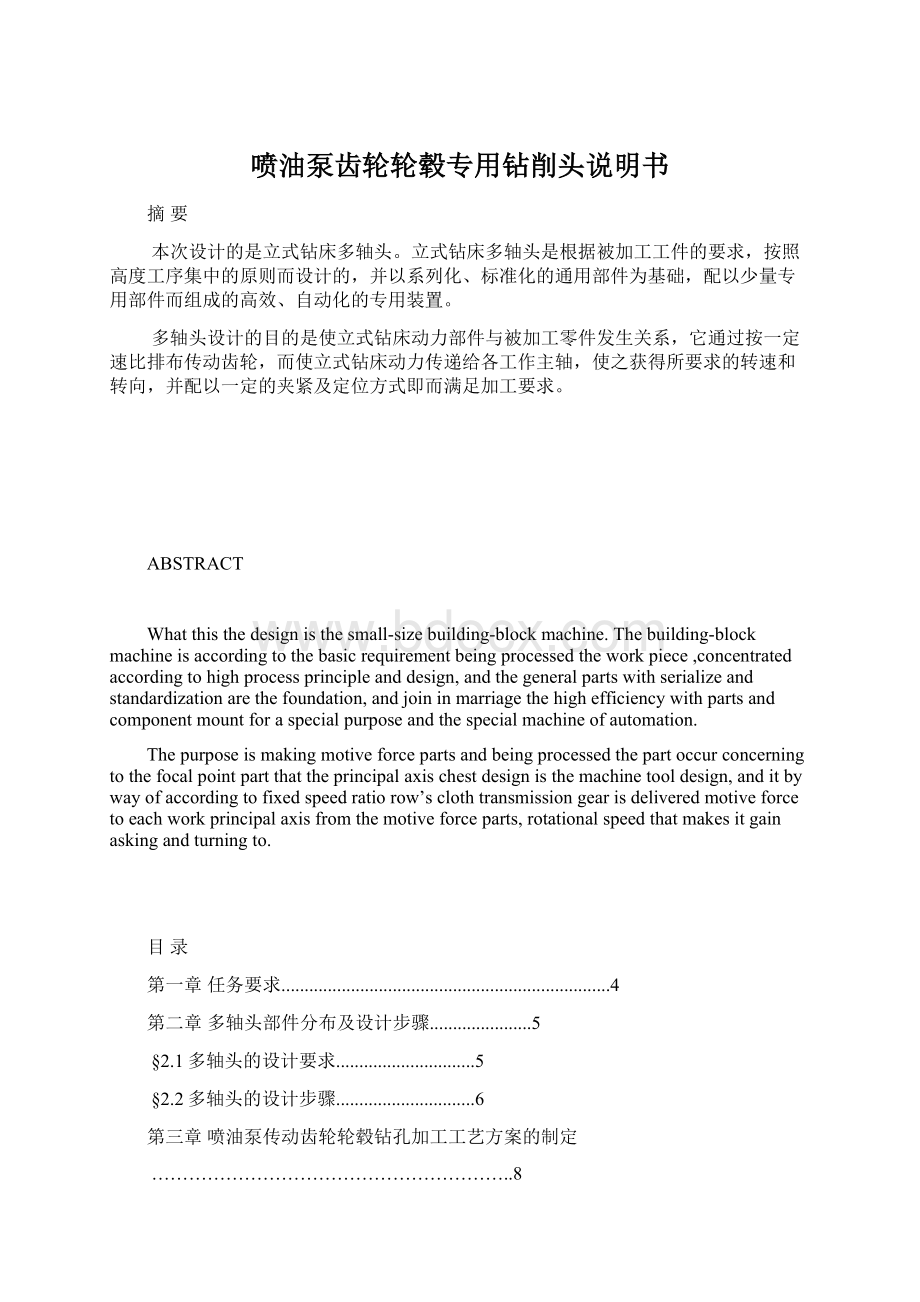
喷油泵齿轮轮毂专用钻削头说明书
摘要
本次设计的是立式钻床多轴头。
立式钻床多轴头是根据被加工工件的要求,按照高度工序集中的原则而设计的,并以系列化、标准化的通用部件为基础,配以少量专用部件而组成的高效、自动化的专用装置。
多轴头设计的目的是使立式钻床动力部件与被加工零件发生关系,它通过按一定速比排布传动齿轮,而使立式钻床动力传递给各工作主轴,使之获得所要求的转速和转向,并配以一定的夹紧及定位方式即而满足加工要求。
ABSTRACT
Whatthisthedesignisthesmall-sizebuilding-blockmachine.Thebuilding-blockmachineisaccordingtothebasicrequirementbeingprocessedtheworkpiece,concentratedaccordingtohighprocessprincipleanddesign,andthegeneralpartswithserializeandstandardizationarethefoundation,andjoininmarriagethehighefficiencywithpartsandcomponentmountforaspecialpurposeandthespecialmachineofautomation.
Thepurposeismakingmotiveforcepartsandbeingprocessedthepartoccurconcerningtothefocalpointpartthattheprincipalaxischestdesignisthemachinetooldesign,anditbywayofaccordingtofixedspeedratiorow’sclothtransmissiongearisdeliveredmotiveforcetoeachworkprincipalaxisfromthemotiveforceparts,rotationalspeedthatmakesitgainaskingandturningto.
目录
第一章任务要求.......................................................................4
第二章多轴头部件分布及设计步骤......................5
§2.1多轴头的设计要求..............................5
§2.2多轴头的设计步骤..............................6
第三章喷油泵传动齿轮轮毂钻孔加工工艺方案的制定
…………………………………………………..8
§3.1加工的工序和加工精度的要求………………………….8
§3.2被加工零件的特点………………………………………..8
§3.3工件的生产方式…………………………………………..9
§3.4使用厂的技术的后方能力………………………………..9
第四章工艺基面的选择…………………………………………..10
§4.1工艺基面的选择原则……………………………………..10
§4.2确定夹压位置应该注意的问题…………………………..10
第五章加工工艺的分析…………………………………………...12
第六章刀具结构的选择………………………………………......13
第七章钻孔切削用量的选择……………………………………..15
第八章导向装置的选择…………………………………………...16
第九章主要参数的计算…………………………………………...17
§9.1计算切削用量………………………………………………17
§9.2轴向力,扭矩,功率计算…………………………………17
§9.3传动齿轮的设计…………………………………………...18
§9.4计算实际的刀具主轴转速n’刀和进给量s’刀……………..18
§9.5选择工作轴直径…………………………………………...19
第一十章润滑,冷却………………………………………………….20
第一十一章零部件的选择……………………………………………...21
小结…………………………………………………………………….22
参考文献……………………………………………………………….23
致谢…………………………………………………………………….24
外文资料……………………………………………………………….25
第一章任务要求
该任务要求在制造喷油泵传动齿轮轮毂上钻四个孔。
在保证尺寸和精度要求的情况下,提高生产效率降低成本,年产量在1万件以上。
具体尺寸及要求如零件图所示。
设计所需机床资料如下:
型号Z5140
其技术参数如下:
最大钻孔直径40mm
主轴中心线至导轨面距离335mm
主轴端面至工作台距离750mm
主轴行程250mm
主轴箱行程200mm
主轴转速范围31.5~1400r/min
主轴转速级数12
进给量范围0.056~1.8mm/r
进给量级数9
主轴孔莫氏维度量4
主轴最大进给抗力16000N
主轴最大扭矩350N.m
主电动机功率3kw
总功率3.1kw
工作台行程300mm
工作台尺寸560x480
机床外形尺寸(长x宽x高)1090x905x2530
生产厂大河机床厂等
T型槽数3
T150
A18
B30
C14
H30
第二章多轴头部件分布及设计步骤
§2.1多轴头的设计要求
一.工艺可能性
多轴头的工艺可能性是指多轴头是适应不同的生产要求的能力。
大致包括以下内容:
(1)在多轴头上可以完成的工序种类;
(2)加工零件的类型、材料、和尺寸范围;(3)毛坯的种类等。
工艺可能性主要根据生产批量,也就是根据工艺要分散的还是要集中而定。
在大批量的生产中,为了提高生产率,供需往往是分散的,一个多轴头只能担负某一道工序的加工。
因此,用于大批量的生产的专门化多轴头,必须适当的扩大其工艺的可能性,以提高效率,简化结构和降低成本。
在小批量生产中,工序适当的集中,使一个多轴头尽可能多的完成多种工序。
因此,用于小批量的多轴头,要适应不同工业部门的要求和完成各种各样的工作,工艺可能性应当宽一些。
综上所述本设计在制造喷油泵传动齿轮轮毂上钻四个孔,其工艺性完全满足要求。
二.加工精度和表面粗糙度
多轴头的加工精度是指被加工零件在尺寸、形状和相互位置等方面所达到的准确程度。
影响多轴头的加工精度的因素很多,例如多轴头的几何精度、传动精度、运动精度和刚度等。
几何精度取决于多轴头主要部件的几何形状和相互位置。
传动精度取决于传动系统的制造精度和装配精度以及传动系统设计的合理性。
运动精度是多轴头的零部件在外在载荷的条件下以工作速度运转的精度。
刚度是指多轴头抵抗弹性形变的能力。
多轴头所加工零件的表面粗糙度是多轴头的主要性能之一。
它与工件的和刀具的材料、进给量、刀具的几何形状以及切削时的震动有关。
综上所述本设计的多轴头在加工精度和表面粗糙度都能满足加工设计要求。
三.生产率
多轴头的生产率通常是指在单位时间内多轴头加工的工件数量。
要提高多轴头的生产率,必须缩短加工一个零件的平均总时间,其中包括缩短切削加工时间、辅助时间和分摊到每个工件上的准备时间和结束时间。
提高多轴头的切削速度,采用大的进给量等都可以缩短加工时间以提高生产率。
本设计采用四个钻头在传动齿轮轮毂上同时加工四个Φ6.7孔,进而提高了生产率。
四.结构、制造与维修
在满足使用要求的前提下,多轴头的结构应尽量的简单,容易制造和装配,维修方便等。
多轴头零部件的通用化和标准化,对多轴头的结构、制造与维修有直接的影响。
多轴头的系列化可以用最少的品种满足各种不同的需要,尤其是同类的多轴头结构典型化,以减少的设计的劳动量。
部件的通用化和零件的标准化既可以缩短多轴头的设计周期和制造周期又可以扩大生产批量,有利于实现生产的专业化。
本设计的多轴头大部分采用标准零件,其结构如多轴头总装图所示,在制造与维修方面也都非常方便。
五.其他
设计的还应注意使用多轴头体积小、重量轻、占地面积小、外形美观以及注意防止污染环境,例如减轻噪音、防止漏油、消雾等。
§2.2多轴头的设计步骤
多轴头设计工作大体可分为四个步骤:
1.调查研究
调查研究的内容一般包括有:
(1)学习有关多轴头设计的方针、政策,明确设计要求;
(2)到使用单位调查,了解所设计的新多轴头将要承担的生产任务和加工工艺,了解使用单位对多轴头的要求;(3)到制造单位调查,了解制造厂的设备条件、技术能力和生产经验;(4)收集国内外同类多轴头的技术文献和图纸资料,并注意调查他的结构性能、使用和制造情况等,尤其注意了解新技术在同类型多轴头上应用的情况。
根据本设计的特点和要求,在老师的指导下我到中国第一拖拉机制造厂和中信重型机械厂等进行了实际的调查研究。
2.方案拟定
在调查和科学实验的基础上,通常可以订出几个方案进行分析比较。
每个方案所包括的内容有:
工艺分析、主要技术参数、总布局、传动系统、主要部件的结构草图、试验结果及技术经济效果分析等。
本设计方案拟定的具体内容将在后面做具体论述。
3.工作图设计
首先,绘制多轴头总图和各部件装配图。
为使各部件能够同时且协调的进行设计,一般应划出多轴头的总体尺寸联系图,在图中确定各部分的轮廓尺寸和各部分建有联系的相关用途和零件图尺寸。
进行必要的计算。
其次,绘制多轴头的全部零件图。
最后,整理多轴头有关部件和主要零件的设计计算说明书,编制明细表。
第三章喷油泵传动齿轮轮毂钻孔加工工艺方案的制定
制定加工零件工艺方案是设计组合机床最重要的步骤之一。
本设计多轴头的工艺方案制定的正确与否,将决定多轴头能否达到“重量轻,体积小,结构简单,使用方便,效率高,质量好”的要求。
为了使工艺方案制定的合理。
先进,必须开展以人工为主体的“三结合”设计,密切联系实际,总结生产实践经验,全面了解被加工零件的加工情况和影响机床方案制定的因素。
影响机床工艺方案制定的主要因素有:
§3.1加工的工序和加工精度的要求
被加工零件在多轴头上完成的工序及加工精度,是制定多轴头工艺方案的主要依据。
制定工艺方案时,首先需要全面分析工件的加工精度及技术要求,了解现场加工工艺及保证精度的有效措施。
例如,加工1~2级精度的孔,不仅工步数要多,而且不同的孔径也应采用不同的工艺方法。
当孔间的位置精度要求很高时,工艺安排上应使所有孔的精加工在同一个工位上进行。
如果同一轴线上的几个孔同心度要求较高,则应尽可能考虑从一面进行加工。
根据本设计任务及零件加工精度的要求,用四个钻头同时加工四个通孔,这样能完全满足其零件图上加工的工序和加工精度的要求。
§3.2被加工零件的特点
如工件材料及硬度,加工部位的结构形式,工件的刚性,工艺基面等。
对于机床工艺方案的制定都有重要的影响。
加工同样精度的孔,加工钢件比加工铸铁件的工步数就多一些。
加工薄壁易振的工件(如薄壁铜合金件),安排工序时要防止共振,否则,将严重影响加工精度。
当工件内壁孔径大于外壁孔径时,只能采用单刀镗的加工方法,加工时工件(或镗头)让刀,使镗刀头定向后送进工件,方能加工。
工件的刚性不足,加工时工序就不能太集中。
有时为了减少机床台数,必须采取高度集中工序时,必安排上,也必须把一些工序从时间上错开加工,以免同时加工时因工件受力变形,发热变形以及振动而影响加工精度。
必须重视工件在机床加工前已完成的工序以及毛坯孔的质量。
当毛坯孔余量很大或铸造质量较差,有大毛刺时,有时则安排拉荒工序,对几个同心常采用粗扩的加工方法。
工件有无适当的工艺基面也是影响工艺方案制订的重要因素。
本设计中要加工零件材料为45#钢,材料硬度为HRC27~32,故采用圆锥面和键槽定位,具体如零件加工工序图所示。
§3.3工件的生产方式
被加工零件的生产批量的大小,对机床工艺方案的制定也有影响。
对大批大量生产的箱体零件,工序安排上,一般趋于分散。
以汽缸体为例,缸孔的三轴孔加工多由两套机床来完成。
其粗加工,半精加工及精加工也分别在不同机床上进行。
这样,机床虽然多一些,但由于生产批量很大,从提高生产率,稳定地保证加工精度的角度来讲仍然是合理的。
在中小批生产情况下,完成同样工艺内容,则要力求减少机床台数。
此时应当将工序尽量集中在一台或少数几台机床上进行加工,以提高机床的利用率。
本设计属于大批量生产,故工序安排上趋于分散。
§3.4使用厂的技术的后方能力
另外根据实际厂方的生产能力和所具备的生产资料。
通过调查对被加工零件的加工内容及与其相关的问题有了规律性的了解。
综合上述四点内容故采用多轴头设计的工艺方案。
第四章工艺基面的选择
§4.1工艺基面的选择原则:
一、应当尽量选用设计基面作为在机床上加工用的定位基面。
这样能建设累计误差,有利于保证加工精度。
二、选择的定位基面应力保工件稳定定位。
定位的支撑而应该大一些,力求采用已加工面作为定位基面,在加工精度要求高时,尤其必要。
只有在不得已时才采用毛面定位。
并且必须选取那些与加工面有一定关系的毛面作为定位基面,同时应对定位面处进行仔细清理平整,切记不能选择在铸件或锻件的分型面上,也不要选在有铸孔的地方。
因为铸孔口上往往有毛刺,会破坏定位精度。
三、选择基面时要保证在一次安装下,能对尽可能多的面进行加工。
这样便于有效地集中加工工序,提高机床生产率,保证加工部位相互间的精度要求。
四、统一基面的原则。
即在各台机床上采取共同的定位基面来加工工件不同面上的孔,对同一个面上的孔完成不同的工序。
这一原则对加工工序长的箱体件尤有必要。
五、选择定位基面应考虑夹紧方便,夹具结构简单
六、当被加工零件不具备理想工序基面时,可在机床夹具上增加辅助支撑机构。
综上所述,喷油泵传动齿轮轮毂钻孔加工的工艺基面的选择如加工工序图所示,采用圆锥面和键槽进行定位,以圆环面为支承,具体如零件加工工序图所示。
§4.2确定夹压位置应该注意的问题
在选择工艺基面的同时要相应地决定夹压位置。
因为它对定位的可靠,工件的稳定以及保证加工精度都有直接的影响。
确定夹压位置时应该注意如下的问题:
一、保证工件夹压后定位稳定。
组合机床是按集中工序组成的。
常常是多轴,多面同时加工,切削负荷重。
特别是多轴钻孔时,往往产生很大的切削力,为了使工件在加工过程中不产生位移和振动,必须将工件牢固的夹位,并且有足够的夹压刚度。
例如夹压点的布置应使夹压合力落在定位平面之内,力求接近定位平面的中心。
对一些比较高的或刚性较差的箱体件宜将夹压点放在箱体上面,而不放在下方。
二、夹压点应避免放在工件加工部位的上方。
力求使其靠近箱体的筋或壁,以减少夹压变形影响加工精度。
三、对刚性差的工件,力求使夹压点对着定位支撑点,避免形成力矩,造成工件变形而影响精度。
有时候对刚性差,精度要求高的工件可以采用多点夹压,是夹压力均匀分布。
综合上述可知,采用工件上的圆锥孔和键槽定位,配以弹簧用活动钻模压板进行夹紧。
第五章加工工艺的分析
分析被加工零件和工艺,亦是制定工艺方案的极其重要的问题。
钻孔有一般钻孔(钻孔深度不大)和钻深孔两种情况。
从钻深角度来看,钻孔深度为3~4倍直径的占绝大多数。
钻深孔时,为了防止切屑堵塞而引起钻头折断,要采取分级进给的方法,即在加工过程中钻头定期退出以排除切屑。
当钻削直径较小,而孔的深度很大,尤其是在钢件上钻孔时,通常存在下列主要问题:
1、切屑排除困难。
由于切屑阻塞使扭矩增大,造成钻头经常折断。
这在加工钢件小直径深孔时尤为严重。
2、刀具冷却困难。
加工小直径深孔,冷却液不易进入空间,钻头发热严重,降低了钻头的使用寿命。
3、钻孔轴线容易歪斜。
由于钻头细长,强度与刚度很弱,特别当钻头刃磨得不对称时,钻孔很易偏斜。
为了使深孔加工过程能够顺利进行,还需要根据具体情况灵活地采取不同的措施。
(a)为了排屑方便。
小直径深孔加工应当采取卧式方案加工深孔甚至可以不用分级进给。
(b)刀具的结构形式对排屑有重要的影响。
若加大钻头的螺旋槽角度,就能使钻头排屑方便。
关于“钻削”部分当加工直径较大的深孔时,可采用“中空”的钻头,加工时冷却液通过钻头进入加工空间,使切屑排出,并且可提高冷却效果。
(c)为了提高冷却效果,可将工件浸入冷却液中加工。
目前在加工曲轴、高压泵体等工件的深孔时,就是采用“水盆”式夹具,将工件浸在冷却液中进行的。
(d)减少钻深孔的轴线歪斜。
影响钻深孔轴线直线性的主要因素,是钻头切屑刃的对称性及钻头的导向条件。
因此提高钻头切屑刃的对称性,并采用较长的导向,缩小导向距工件的距离(以妨碍排屑为原则)是提高钻深孔轴线直线性的主要措施。
被加工零件表面的不平和倾斜,对钻深孔轴线的直线性也有影响。
因为刚钻进时一偏,则钻深愈大,偏斜愈大。
为此可采取大直径的中心钻在精密导向中预先钻出一个准确的中心导向孔。
另外,使工件旋转加工,在一定程度上也能提高深孔的直线性。
综上所述,本加工工序是加工通孔,孔径为Φ6.7的孔。
故钻削直径较小,且为通孔加工钻削深度也不大。
所以在钻模板上配以固定式钻模套即可满足加工零件的技术要求。
第六章刀具结构的选择
众所周知,为了使一个加工过程能顺利的进行,正确地设计,制造刀具是极其重要的环节,根据工艺要求与加工精度的不同,经常采用的刀具有:
一般刀具,复合刀具以及特种刀具等。
对刀具结构选择应注意的问题:
(a)在制定工艺方案时,只要条件允许,应首先选取标准刀具。
(b)为了提高工序集中程度,或达到更高的精度,可以采用复合刀具。
但在确定复合刀具结构时,应尽可能采用组装式的复合刀具。
选择刀具结构时,必须认真考虑被加工零件材料的特点,比如加工铸铁时,由于其硬度较高,宜采用多刃铰刀或镗刀头加工,以提高刀具的使用寿命。
对于钢件也宜采用多刃镗刀头或铰刀加工。
这样可以避免切屑缠绕镗杆。
综合本设计加工要求的特点,在喷油泵传动齿轮轮毂钻孔,故选择标准钻头即可,无需考虑采用复合刀具。
第七章钻孔切屑用量的选择
当采用高速钢钻头加工钢件时,切削速度一般为12-16米/分,钻孔切屑用量的选择与钻孔深度也联系。
当加工铸铁件孔深为钻孔直径的6-8倍时,在组合机床上通常都是和其他浅孔一样采取一次走刀的办法加工出来,不过加工这种较深孔的切削用量要适当降低一点。
根据具体情况适当选择。
降低进给量的目的是为了减少轴向切削力,以避免钻头折断。
因为钻削深度较大的孔时。
由于冷却排屑条件不好。
在一定程度上使刀具寿命有所降低。
所以降低切削速度,主要是为了提高刀具寿命,并使加工较深孔的钻头寿命与其它加工浅孔的钻头寿命比较接近。
选择切削量用量还需要注意。
不能一律按孔深增加而递减,在某些情况下反而应适当地提高切削用量。
故根据设计任务可知该钻孔为小孔,且为通孔。
选用高速钢钻头加工故取S转=0.6mm/r。
第八章导向装置的选择
导向装置:
在组合机床上完成的孔加工工序中,除采用“刚性主轴”加工方法外,在大多数情况下,切削刀具都在导向装置中工作。
因此,具有精密的导向便成为机床刀具工作的显著特点之一。
机床夹具上的导向装置是作为引导刀具对工件进行切削加工的重要装置。
导向装置的作用在于:
保证刀具对于工件的正确位置;保证各刀具相互间的正确位置和提高刀具系统的支撑刚性。
因此,它对于保证加工精度和机床的可靠工作有着重要的影响。
装置在一般情况下都是固定地设置在机床夹具上的,并且成为组合机床夹具的一个重要组成部分。
但是,在某些特定的情况下,为了适当机床特殊的工作要求,还常常需要采用可移动的导向装置即活动钻模板。
但即使是在这样的情况下,也必须使活动钻模板与机床夹具间保持精确的定位关系。
以利于保证加工精度,因此活动钻模板实质上就是一种特殊形式的刀具导向装置。
具导向装置,具有多种不同的结构形式,但根据其运动形式的不同,可将导向装置大致分为两类:
第一类导向装置:
这类导向装置的导套安装在机床夹具的鏜模架上,并且是固定不动的。
刀具或刀杆本身在导套内既有相对转动又有相对移动。
这类导向装置可以有两种不同的使用方式:
一种是刀具本身在导套内工作;另一种是以刀杆部分作为导向。
第二类导向装置:
这类导向装置带有可旋转的部分。
旋转部分可以作在刀杆上,也可以设在夹具的鏜模架上,此时刀杆本身在导套内只有相对移动而无相对转动。
综合上述,该零件在加工精度上不是太高,并依据结构的经济性选择第一类导向装置。
具体结构如多轴头总装图所示。
第九章主要参数的计算
§9.1计算切削用量
钻Φ6.7的孔。
查《组合机床讲义》表3-6选。
切削用量So=0.06mm/r.V=14m/min.
因为多轴头同时加工的特点,选用的切削用量要比单刀加工时的低。
其原因是考虑大量刀具在使用中迅速磨损。
刀具消耗增加,换刀时间增加,影响机床的市场效率和经济效益。
故选So=0.05mm/r.由于切削速度对刀具磨损较大影响。
多轴钻削时,比一般单刀加工时约降低30-50%左右。
故选V=8m/min.
则:
n1=1000v/πd
=1000x8/3.14x6.7=380.3r/min.
§9.2轴向力,扭矩,功率计算
轴向力:
P=3.3DS00.7σb0.75
=3.3x6.7x0.060.7x620.75
=68.4kg=670.32N
ΣP=Px4=670.32Nx4
=2681.28N<9000N
扭矩:
Mkp=1.65D2So0.8σb0.7
=1.65x6.72x0.060.8x620.7
=146.5kg.mm=1.44N.m
ΣMkp=1.44x4=5.76N.m<<160N.m
功率:
N=Mkp.V/716.2π.Dx1.36
=146.5x8/716.2x3.14x6.7x1.36
=0.06kw.
ΣN=0.06x4=0.24kw.
若考虑传动效率N机≥ΣN/η机=0.24/0.8=0.31kw<2.2kw.
以上公式详见《组合机床讲义》P220.
各结果均乘以4是四轴头所需的轴向力、扭矩、功率。
§9.3传动齿轮的设计
多轴箱的传动设计,是根据动力箱驱动轴位置亦转速。
各主轴位置及其转速要求设计传动链,把驱动轴与各主轴连接起来。
使各主轴获得预定的转速和转向。
多轴箱传动系统的一般要求:
1.力求使传动轴和齿轮的规格数量最少,应尽量用一根传动轴带动多根主轴,并将齿轮布置在同一平面上。
2.尽量不用主轴带动主轴的方案,以免增加主轴负荷影响加工质量。
3.为使结构紧凑,多轴箱内齿轮副的传动比一般大于0.5(最佳传动比为0.66~1)
4.用于粗加工上的齿轮,应尽可能设置在第Ⅰ排,以减少扭转变形;精加工主轴上的齿轮,应设置在第Ⅲ排以减少主轴端的弯曲变形。
5.主轴旋转方向一致,且与驱动轴转向一致。
根据上述几点要求,驱动轴做成齿轮圈轴受齿轮副传动的限制和钻孔切削速度的限制,及Z5140已有转速的限制,取传动齿轮圈转速为n2=127r/min.
故传动比
i12=n1/n2=380.3r/min/127r/min=3
决定主动齿轮的m和z。
根据在45号钢上钻孔时的许