设计技术部冲压常用材料培训 3.docx
《设计技术部冲压常用材料培训 3.docx》由会员分享,可在线阅读,更多相关《设计技术部冲压常用材料培训 3.docx(19页珍藏版)》请在冰豆网上搜索。
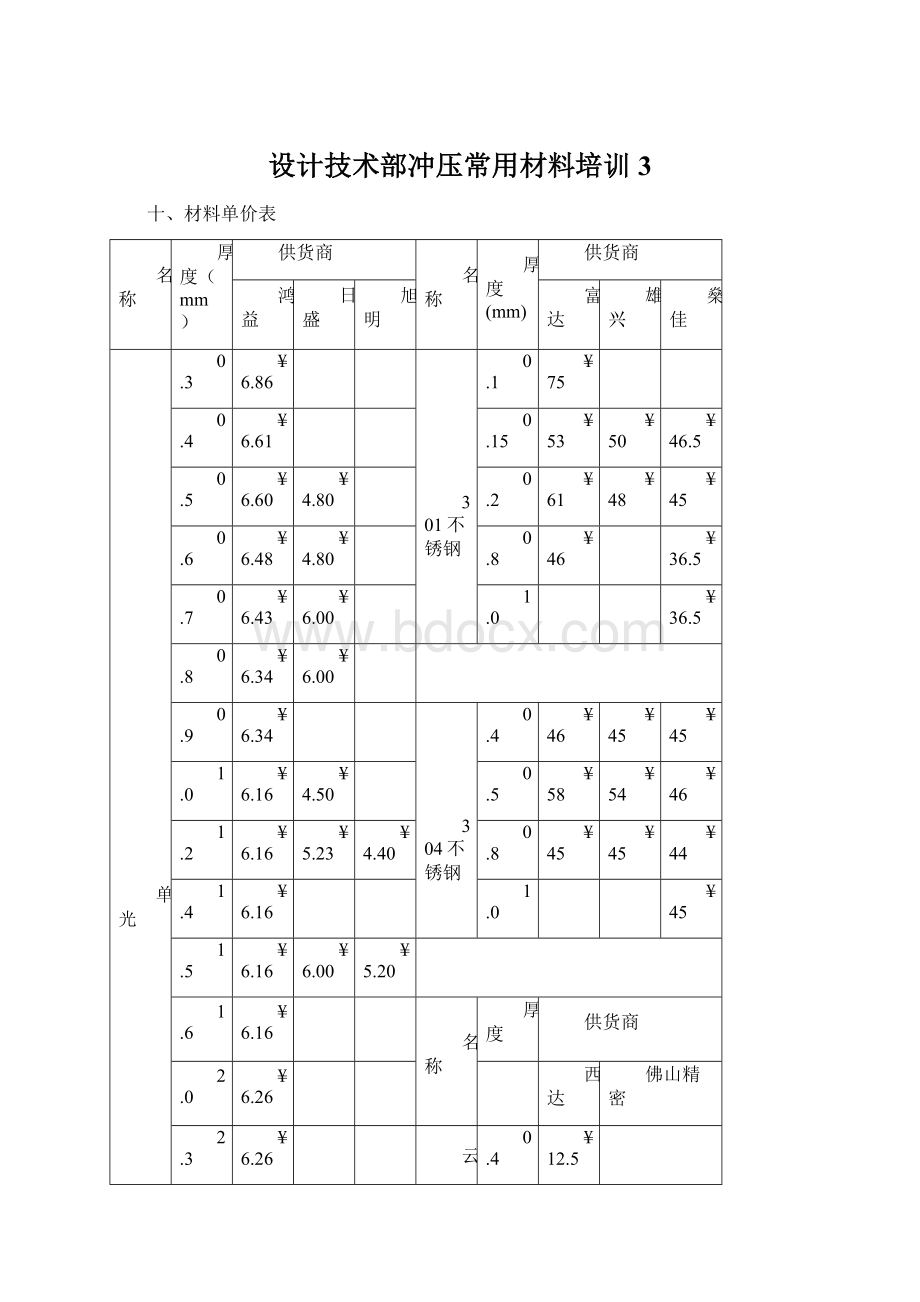
设计技术部冲压常用材料培训3
十、材料单价表
名称
厚度(mm)
供货商
名称
厚度(mm)
供货商
鸿益
日盛
旭明
富达
雄兴
燊佳
单光
0.3
¥6.86
301不锈钢
0.1
¥75
0.4
¥6.61
0.15
¥53
¥50
¥46.5
0.5
¥6.60
¥4.80
0.2
¥61
¥48
¥45
0.6
¥6.48
¥4.80
0.8
¥46
¥36.5
0.7
¥6.43
¥6.00
1.0
¥36.5
0.8
¥6.34
¥6.00
0.9
¥6.34
304不锈钢
0.4
¥46
¥45
¥45
1.0
¥6.16
¥4.50
0.5
¥58
¥54
¥46
1.2
¥6.16
¥5.23
¥4.40
0.8
¥45
¥45
¥44
1.4
¥6.16
1.0
¥45
1.5
¥6.16
¥6.00
¥5.20
1.6
¥6.16
名称
厚度
供货商
2.0
¥6.26
西达
佛山精密
2.3
¥6.26
云母片
0.4
¥12.5
2.5
¥6.31
0.5
¥14.5
3.0
¥6.31
双金属
0.8
¥295
FPA206-9
名称
厚度(mm)
供货商
名称
厚度(mm)
供货商
基霖
景发
盛兴昌
试谊
景发
盛兴昌
磷铜
0.15
¥75
¥87
青铜
0.2
¥60.2
0.25
¥72.5
¥83.1
0.3
¥59.5
0.4
¥69
¥82.5
0.4
¥59.5
0.5
¥46
¥82.5
0.5
¥70
¥55
¥59.5
0.6
¥82.5
0.8
¥59.5
SPCC:
冷轧钢板(steelplatecoldcommercial)
SPCD:
冷轧深拉钢板(steelplatecolddeepdrawn)
SPCE:
冷轧深深拉钢板(steelplaetcolddeepdrawnextra)
SECC:
冷轧电镀板(steelelectrolyticcoldcommercial)
SECD:
冷轧深深拉电镀钢板(steelelectrolyticcolddeepdrawn)
SECE:
冷间压延深深拉电镀钢板(steelelectrolyticcolddeepdrawnextra)
SECC-K2:
其中SECC指冷轧电镀钢板,K2为神户制钢所表面耐指纹电镀锌钢板的行业的表示代号,其表面涂层为有机涂层;
SECC-KS:
其中SECC指冷轧电镀钢板,KS为神户制钢所对表面耐指纹电镀锌钢板的行业的表示代号,其表面涂层为有机涂层;
SEGC-CS:
其中EGC(EGC为electrolyticgalvanizedcold)为新日本制铁行业标准代号,与日本工业标准(JIS标准)代号CC等同对应,CS为新日本制铁行业标准代的UF处理钢板(耐指纹)的一种;
UF处理钢板分以下三种:
EGC-CZ有机被膜 0.5μm;
EGC-CF有机被膜 1.0μm;
EGC-CS有机被膜 0.7μm;
SEHC:
热轧镀锌钢板及钢带;
SEHD:
热轧镀锌深拉钢板及钢带;
SEHE:
热轧镀锌深深拉钢板及钢带;
SGCC:
冷轧涂镀锌钢板及钢带;
SGCH:
冷轧涂镀锌冷硬钢板及钢带;
SGCD:
冷轧涂镀锌深拉钢板及钢带;
SGHC:
热轧涂镀锌钢板及钢带;
CGCC:
冷轧涂彩锌钢板及钢带;
CGCH:
冷轧涂彩锌冷硬钢板及钢带
CGCD:
冷轧涂彩锌深拉钢板及钢带
SUS301CSP-SEH:
冷轧弹性不锈钢带
SUS304CSP-1/2H:
冷轧弹性不锈钢带
SUS304CSP-3/4H:
冷轧弹性不锈钢带
SUS304CSP-H:
冷轧弹性不锈钢带
后注:
新推出的新型材料(环保材料)与旧材料有以下区别:
环保材料又称无铬电镀钢板,只对表面有做处理的材料而言,而冷轧钢板作为所有钢材后处理的原板无需进行表面处理,目前推出的环保材料暂时只有电镀锌钢板一种类型如下:
新日本制铁材料:
EGC-QS:
一般环保电镀锌钢板
EGC-QZ:
是特别为理光公司商定的环保镀锌钢板
环保电镀锌钢板与目前的电镀锌钢板的主要区别如下:
环保电镀锌钢板包括有机被膜、镀锌层、铁基板而普通镀锌钢板包括有机被膜、铬酸盐涂层、镀锌层、铁基板,即环保电镀锌钢板不包括铬酸盐涂层。
模具钢淬火十种裂纹分析与措施
摘要:
1、纵向裂纹 裂纹呈轴向,形状细而长。
当模具完全淬透即无心淬火时,心部转变为比容最大的淬火马氏体,产生切向拉应力,模具钢的含碳量愈高,产生的切向拉应力愈大,当拉应力大于该钢强度极限时导致纵向裂纹形成。
以下因素又加剧了纵向裂纹的产生:
(1)钢中含有较
1、纵向裂纹
裂纹呈轴向,形状细而长。
当模具完全淬透即无心淬火时,心部转变为比容最大的淬火马氏体,产生切向拉应力,模具钢的含碳量愈高,产生的切向拉应力愈大,当拉应力大于该钢强度极限时导致纵向裂纹形成。
以下因素又加剧了纵向裂纹的产生:
(1)钢中含有较多S、P、***、Bi、Pb、Sn、As等低熔点有害杂质,钢锭轧制时沿轧制方向呈纵向严重偏析分布,易产生应力集中形成纵向淬火裂纹,或原材料轧制后快冷形成的纵向裂纹未加工掉保留在产品中导致最终淬火裂纹扩大形成纵向裂纹;
(2)模具尺寸在钢的淬裂敏感尺寸范围内(碳工具钢淬裂危险尺寸为8-15mm,中低合金钢危险尺寸为25-40mm)或选择的淬火冷却介质大大超过该钢的临界淬火冷却速度时均易形成纵向裂纹。
预防措施:
(1)严格原材料入库检查,对有害杂质含量超标钢材不投产;
(2)尽量选用真空冶炼,炉外精炼或电渣重熔模具钢材;(3)改进热处理工艺,采用真空加热、保护气氛加热和充分脱氧盐浴炉加热及分级淬火、等温淬火;(4)变无心淬火为有心淬火即不完全淬透,获得强韧性高的下贝氏体组织等措施,大幅度降低拉应力,能有效避免模具纵向开裂和淬火畸变。
2、横向裂纹
裂纹特征是垂直于轴向。
未淬透模具,在淬硬区与未淬硬区过渡部分存在大的拉应力峰值,大型模具快速冷却时易形成大的拉应力峰值,因形成的轴向应力大于切向应力,导致产生横向裂纹。
锻造模块中S、P.***,Bi,Pb,Sn,As等低熔点有害杂质的横向偏析或模块存在横向显微裂纹,淬火后经扩展形成横向裂纹。
预防措施:
(1)模块应合理锻造,原材料长度与直径之比即锻造比最好选在2—3之间,锻造采用双十字形变向锻造,经五镦五拔多火锻造,使钢中碳化物和杂质呈细、小,匀分布于钢基体,锻造纤维组织围绕型腔无定向分布,大幅度提高模块横向力学性能,减少和消除应力源;
(2)选择理想的冷却速度和冷却介质:
在钢的Ms点以上快冷,大于该钢临界淬火冷却速度,钢中过冷奥氏体产生的应力为热应力,表层为压应力,内层为张应力,相互抵消,有效防止热应力裂纹形成,在钢的Ms—Mf之间缓冷,大幅度降低形成淬火马氏体时的组织应力。
当钢中热应力与相应应力总和为正(张应力)时,则易淬裂,为负时,则不易淬裂。
充分利用热应力,降低相变应力,控制应力总和为负,能有效避免横向淬火裂纹发生。
CL-1有机淬火介质是较理想淬火剂,同时可减少和避免淬火模具畸变,还可控制硬化层合理分布。
调正CL-1淬火剂不同浓度配比,可得到不同冷却速度,获得所需硬化层分布,满足不同模具钢需求。
3、弧状裂纹
常发生在模具棱角角、缺口、孔穴、凹模接线飞边等形状突变处。
这是因为,淬火时棱角处产生的应力是平滑表面平均应力的10倍。
另外,
(1)钢中含碳(C)量和合金元素含量愈高,钢Ms点愈低,Ms点降低2℃,则淬裂倾向增加1.2倍,Ms点降低8℃,淬裂倾向则增加8倍;
(2)钢中不同组织转变和相同组织转变不同时性,由于不同组织比容差,造成巨大组织应力,导致组织交界处形成弧状裂纹;(3)淬火后未及时回火,或回火不充分,钢中残余奥氏体未充分转变,保留在使用状态中,促进应力重新分布,或模具服役时残余奥氏体发生马氏体相变产生新的内应力,当综合应力大于该钢强度极限时便形成弧状裂纹;(4)具有第二类回火脆性钢,淬火后高温回火缓冷,导致钢中P,s等有害杂质化合物沿晶界析出,大大降低晶界结合力和强韧性,增加脆性,服役时在外力作用下形成弧状裂纹。
预防措施:
(1)改进设计,尽量使形状对称,减少形状突变,增加工艺孔与加强筋,或采用组合装配;
(2)圆角代直角及尖角锐边,贯穿孔代盲孔,提高加工精度和表面光洁度,减少应力集中源,对于无法避免直角、尖角锐边、盲孔等处一般硬度要求不高,可用铁丝、石棉绳、耐火泥等进行包扎或填塞,人为造成冷却屏障,使之缓慢冷却淬火,避免应力集中,防止淬火时弧状裂纹形成;(3)淬火钢应及时回火,消除部分淬火内应力,防止淬火应力扩展;(4)较长时间回火,提高模具抗断裂韧性值;(5)充分回火,得到稳定组织性能;多次回火使残余奥氏体转变充分和消除新的应力;(7)合理回火,提高钢件疲劳抗力和综合机械力学性能;对于有第二类回火脆性模具钢高温回火后应快冷(水冷或油冷),可消除二类回火脆性,防止和避免淬火时弧状裂纹形成。
1.1 冲裁间隙配置原则:
冲孔跟公落料跟模,
即冲孔的大小,是和冲头大小一样的(细微差别忽略),而冲出之物体(或为产品,或为凸米,或为打舌位等)的形状大小则是和模腔一样大小(细微差别忽略)。
1.2 材料冲裁上下模间隙配置标准:
材料
硬冷轧钢片,半硬或全硬不锈钢片取8%
硬冷轧钢片
SUS301
特硬
SUS301
全硬
SUS304-H
SUS301-H3/4
SUS304-H3/4
SUS301-H1/2
SUS304-H1/2
硬度HV
>500
490最小
430最小
370最小
310最小
250最小
间隙
(单边)
9-10%
8.5%
8%
8%
7%
7%
对于漏屎锥度,通常取0.5°单边锥度,但对于软材料(如软铝),必须遵循“小间隙大锥度”的原则,锥度必须保证在1°~1.5°.
1.3 其它板件孔与零件线割间隙设定
单边间隙
导柱孔
小导套孔(硬压)
小导套孔(粘胶水)
冲头固定孔
销钉孔
冲头活动孔
冲头过孔
镶件固定孔
漏屎孔
t≤0.5
+0.005
+0.005
+0.1
+0.005
+0.005
+0.01
+0.5
+0.005
+0.5
t>0.5
+0.008
+0.008
+0.1
+0.01
+0.008
+0.02
+0.5
+0.01
+1.0
1.4 紧固件过孔的间隙设定:
1螺丝杯头与过孔:
螺丝
M4
M5
M6
M8
M10
M12
M14
M16
M20
过孔
Φ4.4
Φ5.5
Φ6.5
Φ8.5
Φ11
Φ13
Φ15
Φ17
Φ21
杯头孔
Φ8
Φ10
Φ11
Φ15
Φ17
Φ20
Φ24
Φ27
Φ35
2真三打螺丝杯头与过孔:
三打螺丝
M5
M6
M8
M10
过孔
Φ6.5
Φ8.5
Φ11
Φ13
杯头孔
Φ11
Φ15
Φ17
Φ20
工模设计指引
一.工模设计指引总则
1.规范五金工模设计,进一步完善设计标准.
2.适应工厂发展要求.
3.提高公司机械化﹑自动化程度.
4.不断创新,不断完善,使工模设计水平进一步提高.
二.工模设计准则
1.展开前,必须仔细检查产品图,特别注意技术要求﹑毛刺方向,图纸是否清晰,是否缺少尺寸,与展开尺寸是否冲突,必要时与上级嗟商,寻求解决办法.
2.展开系数的确认:
V责形,U责形,L责形,责直角且内R=0时,展开补偿值见下表:
料厚T展开补偿值
1.0以下0.4T
1.0~1.50.45T
1.5以上0.5T
一次责多个直角不适用此表.
3.展开图必须标注重要的外形尺寸,方便检查,尺寸标注必须精确到小数点两位,标明产品展开图之毛刺方向.
4.模具设计图必须套标准图框
5.设计前必须清楚图纸的披锋要求,日本图纸披锋表示的方法与中文对照如下:
A.表示“披锋面”:
力(侧,八面,力工侧,力面
B.表示“披锋方向”:
力工方向,sheardroopside
C.表示“光面”:
侧,面,拔方向(draftdirection),才乇面,
6.展开及设计时尺寸处理:
A.冲圆孔及方孔等有公差要求之孔,必须考虑其公差,设计时冲孔公务必偏上公差
例:
冲ø5±0.1孔,冲孔公设计尺寸为ø5.08,如果未标公差则按±0.1设计,特殊情况,
如冲同一种规格孔数量多,例:
产品要引导冲ø4孔20个,为了减少磨床的工作量,直接按ø4设计引导冲,其预冲孔ø4.04.
B.产品图有位置公差要求之尺寸,展开时取上下极限之中间值,产品外形尺寸根据不同公差要求及材料厚度视实际情况取偏中下公差.
C.攻牙底孔确定:
电解,单光材料,M5(含M5)以下牙底孔全部按挤压攻牙(硬料/细牙/无屑)方式设计铝,铜软料,M5以上底孔全部按切削攻牙(软料/粗牙/有屑)方式设计.
牙底孔设计值如下表:
切削攻牙挤压攻牙切削攻牙挤压攻牙
M2.5x0.45ø2.1ø2.28M5x0.8ø4.25ø4.6
M3x0.5ø2.53ø2.752-56UNCø1.8ø2.0
M4x0.7ø3.35ø3.656-32UNCø2.8ø3.15
C.包胶之产品,包胶部位冲孔,设计时考虑包胶厚度之影响,设计冲孔值比产品图标注值大0.5mm,例:
冲孔ø5,设计底孔值为ø5.5.
D.喷油,喷粉之产品,冲孔及外形尺寸设计时,应考虑喷油,喷粉厚度之影响,喷油厚度按0.05mm设计,喷粉厚度按0.07mm设计.
喷油厚度见下表:
喷油厚度
刮地灰后(喷油记号含B):
40~100um
不用刮地灰喷油(喷油记号含C):
20~80um
喷叻咖(光油):
15~80um
7.模具图面具体要求:
A.范本图框必须注明料厚,步距,料宽及材质.
工模设计时,务必注意,料宽要采用整数,不允许有小数字之料宽出现,如用产品展开尺寸做料宽,不用飞边的另作别论.
B.工模设计图面要求标识清晰,线割,计算机锣等加工注解明确,用计算机锣加工部份可不用标注尺寸.
C.计算机锣,线割加工之范本左下角标识,加工基准符号
D.对每块模板进行统一的编号如下:
模板名称模板代号铣床层颜色线割层颜色文字尺寸层颜色其它图层及说明
上盖板OVERTEXT/DIM3A3图框层
上垫脚UTEXT/DIM4center中心线层
上模座UPUPO222UPM/DIM222HI虚线层
上垫板UBUBO22UBM/DIM22LA排样层
上夹板PHPHO5PHW1PHM/DIM5mater料带层
中垫板PPSPPSO11PPSW53PPSM/DIM11part产品图
外打屎PSPSO114PSW30PSM/DIM114PS2内打屎
下范本DIEDIEO50DIEW6DIEM/DIM50DIE2上范本
下垫板LBLBO140LBW40LBM/DIM140PH2下夹板
下模座LPLPO60LPWLPM/DIM60side料带侧面图
下垫脚BTEXT/DIM5punch冲头侧面图
下托板LOWERTEXT/DIM6SP线孔层
E.对各相应模板的零件进行统一的编号,各模板对应孔编号尽量一致,以便模具加工和装配容易识别.
A,表示圆冲;B,B1表示引导预冲和引导针;C,表示异形冲孔;
D,表示管位;E,表示公补强在打屎的铣位;F,表示浮块;
G,表示两用梢;H,表示责形;J,表示背面避位;K,表示导柱;L,表示边钉;M,表示螺丝;N表示顶料梢;O,表示凸包;
P,表示责形(披锋);Q表示气梢;R表示朱咀,翻孔;S表示山形;T,T1分别表示内外打屎的等高螺丝;U,表示线孔;V,表示铆钉孔;W,表示扣位;X表示弹簧孔;Y,表示压线;Z,表示Z责
F.如范本大于300x500,要线割的模,脱料,工夹等要增加2个ø6修模用碰数孔.
三.模具结构
1.飞屎模基本结构(见工作底稿)
A.高精度折飞屎模安装检知器,以防止跳屎.
说明:
(1)适用于下模是一整件之飞屎模
(2)下范本对角安装检知器
(3)检知器上表面低于下模面1~1.5mm
B.不锈钢,磷铜等薄片之飞屎模,所有剪口用ASP-23做镶件且下垫板攻牙,小于ø3冲孔针从指定公司订购.厚料易拉料,N折后再飞边.
C.设计飞屎模务必考虑出件方便,小五金件尽量用风出件或产品从模底出,不允许模面残留废料,下模尾部铣斜,上脱背面磨料槽.
D.为防止冲朱咀跳屎,设计飞屎模时,必须先预冲孔再冲朱咀,若最后两步无引导可用预冲孔引导,最后冲朱咀.注意引导孔在不影响模具强度时下垫座作落屎孔.
E.产品有位置公差要求且公差小,尽可能按排在同一步冲孔.
F.飞屎模用浮升两用销,至少ø8或ø8以上,第一步单边至少两个或两个以上.
G.上脱.上垫板材质用2510,下模用SKD11,其它范本用王牌,当上脱有入子时,限位板用DF-2或2510,下模有入子时,下垫板用DF-2或2510,王牌不淬火可做一整件,2510淬火易变形,长500以上要分板,下垫用那码.
H.小模具用标准铸铁模座,不攻牙不设计出图(除止付螺丝)
I.切边及折弯冲作后振位,责形的对向面加骨位入子和顶梢.
J.山打螺丝在模座沉头,方便调整开模行程;合梢在上垫锣D+0.5孔,模座配钻不画.
2.复合模基本结构(见工作底稿)
A.自制复合模采用王牌钢模座,多攻M27/33止付牙,模座设弹簧孔,下设中框板(25厚)及打板
B.标准铸铁模座复合模,弹簧及打板装在模座内,上加20厚盖板,模座不设计出图
C.大型复合模结构因足够位置放弹簧孔,不要中框板及打板
以上结构下模板用SKD11,其它用王牌;若有向上打凸抽牙,脱板用2510根据闭模高度决定下垫脚高度
D.设计防呆导柱
3.冲孔模基本结构(见工作底稿)
A.在产品不对称的废料孔内设计防反针
B.下范本用SKD11,其它用王牌;若有向上打凸抽牙,脱板用2510
C.若用标准铸铁模座,不设计出图;根据闭模高度决定下垫脚高度
D.胶片冲裁间隙0.01t,铜铝冲裁间隙0.025t
以上3种模具内导柱长度保证开模能导向,背.垫板设避位孔
4.U责形模基本结构
折弯宽度不够放弹簧,下垫打杆与弹簧(ø22)间用ø22*8厚的顶块,下座攻M27
5.V责形模基本结构
成型块用DF-2,其它用王牌
上公中心线按产品折弯内线外偏半个折弯系数,下模V沟在组立图上按料厚偏
上公只攻盲牙,上夹锣固定槽,下模定位规则产品磨料槽,不规则产品锁案内
下模V沟深3~5mm,若折弯附近有冲大孔,为防拉料此面应不少于45度或做对称
V沟天面磨R角
以上注意加工说明代号.数量.内容与模板一致
6.锁模槽分布
80T以上(含)模座必须设计锁模吊孔或U形槽
锁模槽方向间距个数参照冲床上下工作台尺寸参数表
开槽尺寸:
25宽*45深
四.机械加工及图档转换
1.锣刀规格与加工深度见下表
锣刀规格加工深度锣刀规格加工深度
ø45ø1027
ø510ø1230
ø615ø16/ø2035
ø820ø2540
2.磨床加工镶件时,注意手摇磨床最长磨削长度350mm,最高磨削高度270mm.
3.穿线孔大小规定:
穿线尽量钻大,一般穿线孔尺寸ø6、ø3、ø2,如果穿线孔
小于ø2用中心钻选点,再用打孔机加工,同一范本,穿线孔大小尽量统一.
4.转移线割、计算机锣图文件规定:
A.全部转换为DXF檔,转档后打开MILL7确认完全读取方可.
B.线割、计算机锣图文件只保留各自须加工的像素.
5.加工间隙处理:
A.工模设计间隙处理方式:
间隙值直接加到像素上,标注文字说明.
B.复合模公模共享:
工模设计时,外形剪口像素不放间隙,以文字注解说明,线割模时按DXF图档实际
尺寸处理,公按DXF图档实际尺寸再单边缩小冲裁间隙值,具体见下模冲裁间隙对照
表;内外脱料共享,工模设计外形剪口不放间隙,以文字注解说明,线割必须保证内外
脱料与公模的配合良好.
C.下模板冲裁间隙对照表:
(T为产品材料厚度)
单边间隙
单光,铝材2~3%T不锈钢,不锈铁5~6%T
铜片3~4%T电解5~6%T
双光4%T
D.螺栓过孔及沉头孔加工尺寸表:
螺栓尺寸DdH
过孔及沉头孔尺寸D+1d+1H+2~4
山打螺钉沉头孔深度请根据实际需要决定.
6.螺丝底孔加工尺寸
(普通螺丝底孔加工表:
螺丝尺寸底孔尺寸螺丝尺寸底孔尺寸
M4ø3.4M8ø6.8
M5ø4.3M10ø8.6
M6ø5.1
基米螺丝底孔加工表:
螺丝尺寸底孔尺寸螺丝尺寸底孔尺寸螺丝尺寸底孔尺寸
M5ø4.2M10x1.5ø8.5M20x1.5ø18.5
M6ø5.0M12x1.5ø10.5M22x1.5ø20.5
M8ø6.8M16x1.5ø14.5M27x1.5ø25.5
M18x1.5ø16.5M33x1.5ø31.5
7.镶件加工要求:
A.为避免因镶件无扣位造成模具裂开之情况出现,工模设计时所有镶件必须加扣位
镶件扣位高5mm
B.为减少磨床工作量,充分利用生钢原材料,备料时务必考虑加工余量0.5~1mm.
要研磨R角的冲头入子应标注在外观交点.
C.为减少用针大小尺寸与磨削尺寸严重失调情况,对生钢针加工明确规定:
D-V<=0~2mm
公制螺丝孔攻牙前后孔径标准
公称直径螺距(粗牙)平面切削牙朱咀挤压牙攻牙后内孔
M1.00.250.75±0.020.88±0.020.78
M1.10.250.85±0.020.98±0.020.88
M1.20.250.95±0.021.08±0.020.98
M1.40.31.1±0