电厂脱硫改造方案.docx
《电厂脱硫改造方案.docx》由会员分享,可在线阅读,更多相关《电厂脱硫改造方案.docx(126页珍藏版)》请在冰豆网上搜索。
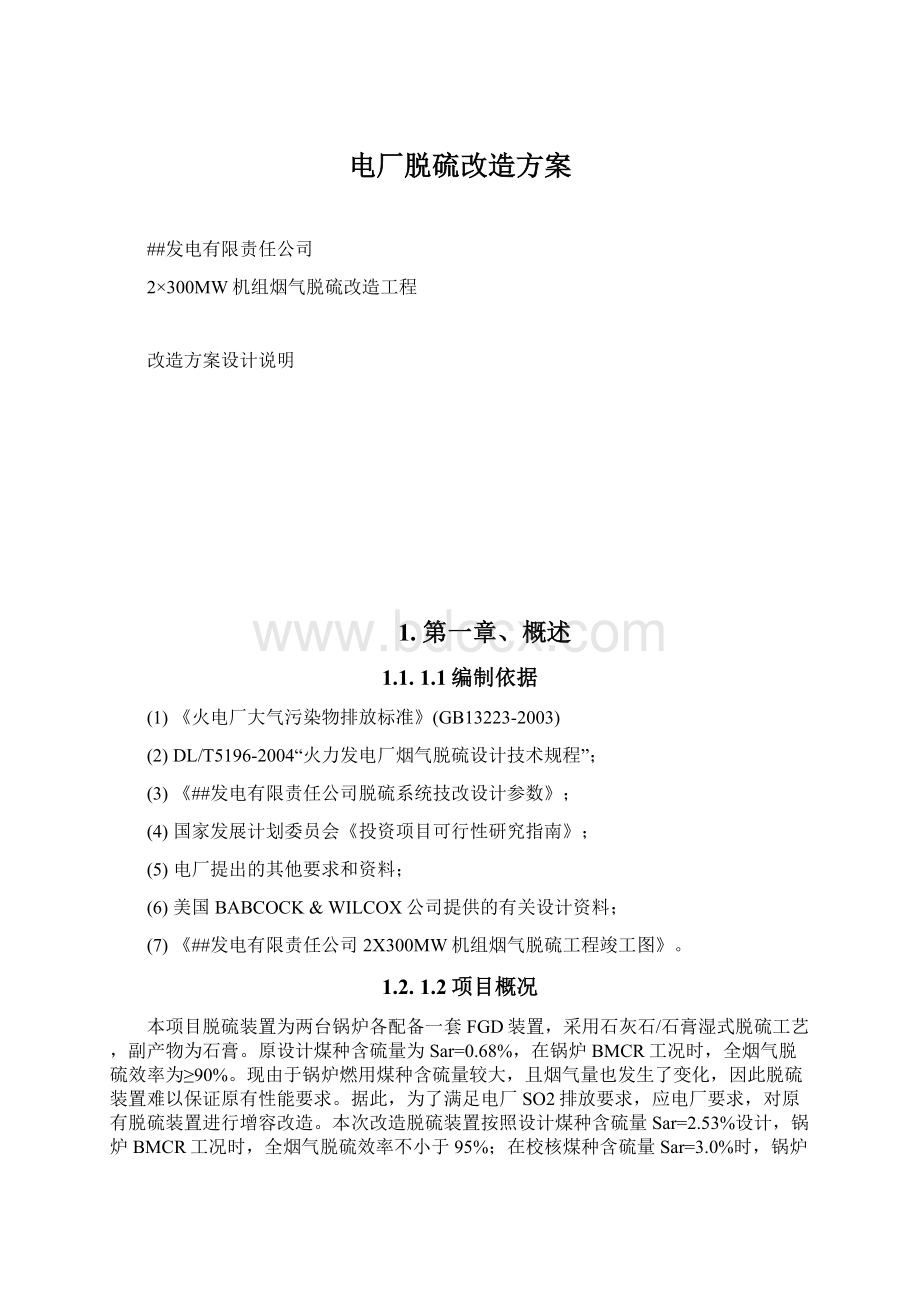
电厂脱硫改造方案
##发电有限责任公司
2×300MW机组烟气脱硫改造工程
改造方案设计说明
1.第一章、概述
1.1.1.1编制依据
(1)《火电厂大气污染物排放标准》(GB13223-2003)
(2)DL/T5196-2004“火力发电厂烟气脱硫设计技术规程”;
(3)《##发电有限责任公司脱硫系统技改设计参数》;
(4)国家发展计划委员会《投资项目可行性研究指南》;
(5)电厂提出的其他要求和资料;
(6)美国BABCOCK&WILCOX公司提供的有关设计资料;
(7)《##发电有限责任公司2X300MW机组烟气脱硫工程竣工图》。
1.2.1.2项目概况
本项目脱硫装置为两台锅炉各配备一套FGD装置,采用石灰石/石膏湿式脱硫工艺,副产物为石膏。
原设计煤种含硫量为Sar=0.68%,在锅炉BMCR工况时,全烟气脱硫效率为≥90%。
现由于锅炉燃用煤种含硫量较大,且烟气量也发生了变化,因此脱硫装置难以保证原有性能要求。
据此,为了满足电厂SO2排放要求,应电厂要求,对原有脱硫装置进行增容改造。
本次改造脱硫装置按照设计煤种含硫量Sar=2.53%设计,锅炉BMCR工况时,全烟气脱硫效率不小于95%;在校核煤种含硫量Sar=3.0%时,锅炉BMCR工况时,FGD出口净烟气SO2浓度满足《火电厂大气污染物排放标准》第三时段排放要求400mg/Nm3。
1.3.1.3研究范围
(8)1)脱硫工艺改造技术方案选择;
(9)2)原有脱硫装置各系统的核算;
(10)3)脱硫剂供应及脱硫剂制备系统;
(11)4)脱硫副产品处置;
(12)5)公用工程和辅助设施;
(13)6)投资估算和技术经济评价
1.4.1.4主要技术原则
(14)1)遵照我国电力建设的规定,贯彻安全、可靠、经济、适用、符合国情的原则。
(15)2)本脱硫工程为原有机组脱硫系统的增容改造项目,存在场地小,系统布置困难,施工难度大,利旧等状况,在工艺选择和设备布置中要充分考虑原有条件,需充分考虑利用原有场地,对原有建、构筑物、设备尽量少拆除,尽可能使用原有的设备、管道、阀门以及仪器仪表等。
(16)3)推荐的脱硫工艺应该是技术成熟、先进、有应用业绩的。
其主要技术指标满足国家和地方环保法规,技术经济合理。
(17)4)尽量采用国产设备和材料;以尽量降低造价。
国内没有生产或技术指标达不到要求的设备、材料可选用进口。
(18)5)脱硫工艺应尽可能节约能源和用水。
(19)6)每套脱硫装置按处理锅炉100%BMCR工况下烟气量考虑。
(20)7)脱硫装置相对于锅炉年运行时间可用率不低于95%,运行负荷范围35-100%BMCR工况。
(21)8)设计煤种含硫量按照Sar=2.53%,校核煤种Sar=3.0%。
(22)9)脱硫率≥95%。
(23)10)脱硫剂为外购成品石灰石粉厂内制浆。
(24)11)脱硫副产品石膏浆液经一、二级脱水后,可得到含水率不大于10%的石膏。
石膏储存利用原有石膏库中,本期不再对原有石膏库房改造。
成品石膏由卡车运至石膏堆场堆放,或直接外卖综合利用。
(25)12)根据电厂要求,本次改造按照有GGH和无GGH两种方案设计。
(26)13)本次改造增加废水处理系统,脱硫废水达标后排放。
(27)14)脱硫装置入口烟气参数,按照电厂提供煤质报告和燃煤量计算所得。
2.第二章、电厂概况
2.1.2.1工程概况
2.1.1.2.1.1工程概述
2.1.2.2.1.2厂址
铁路运输:
铁路##北站至电厂铁路专用线。
公路运输:
107国道或京珠高速至##市经大白线到进厂公路
FGD装置布置在炉后,石膏脱水综合车间布置在二期扩建端的位置上。
2.1.3.2.1.3气象资料
(28)多年平均气温:
14.2℃
(29)极端最高气温:
42.3℃
(30)极端最低气温:
-15.5℃
(31)多年平均相对湿度:
59%
(32)多年最大风速:
24m/s
(33)30年一遇10分钟平均风速:
26m/s
(34)多年平均气压:
99.57kPa
(35)海拔:
182.5m(黄海高程基准)
(36)地震烈度:
8度
2.1.4.2.1.4区域地质、工程地质和地震
厂址区在区域地质构造单元上位于新华夏系第三隆起带太行隆折带的东部,东临第二沉绛带的汤阴地堑。
厂区内未发原有较大断裂的迹象,厂区外围也只有一些次一级小型构造,且规模小、活动性也不明显,不具备发生破坏性地震的条件。
厂区地层由新到老为:
①素填土:
分布于主厂房区、冷却塔区、汽车受煤站区及辅助生产区地段。
出露标高一般为173.0~187.0m,层厚最大达14.5m。
②第四系全新统冲积洪积粉质粘土,分布于冷却塔地段的冲沟底部,出露标高一般为166.6~179.9m,层厚一般为0.6~1.9m。
③第四系上更新统冲积黄土状粉质粘土,分布于冷却塔区、煤场区及辅助生产区地段,该层黄土状粉质粘土具有湿陷性。
④第四系中更新统冲积洪积状粉质粘土,分布于整个厂区,出露标高一般为173.8~182.4m,层厚一般为1.7~12.2m。
⑤第四系坡残积层,分布于主厂房区、冷却塔区及辅助生产区,出露标高一般为166.1~185.4m,层厚一般为0.4~3.3m。
⑥第三系上新统湖积泥岩夹砂岩,分布于整个厂区。
厂址区①层填土质量极差;⑥层钙质泥岩具较轻微至中等胀缩性;③层黄土状粉质粘土具有湿陷性。
厂区在勘探深度范围内地层基本不含水,地下水埋深一般在16以下,因而不存在地下水对各类混凝土的侵蚀性问题。
2.2.2.2燃煤和烟气数据
2.2.1.2.2.1燃煤品质
项目名称
符号
单位
设计煤种
校核煤种
全水分
Mt
%
7.1
空气干燥基水分
Mad
%
1.01
收到基灰分
Aar
%
33.15
干燥无灰基挥发分
Vad
%
18.25
收到基碳
Car
%
53.25
收到基氢
Har
%
2.82
收到基氮分
Nar
%
0.91
收到基氧
Oar
%
0.24
全硫
Sar
%
2.53
3.0
空气干燥基高位发热量
Qgr,ad
MJ/kg
21.24
收到基低位发热量
Qnet,ar
MJ/kg
19.19
煤耗量
t/h
148.4
灰渣成份分析
二氧化硅
SiO2
%
53.56
三氧化二铝
Al2O3
%
25.24
三氧化二铁
Fe2O3
%
8.61
氧化钙
CaO
%
4.5
氧化镁
MgO
%
0.34
氧化钠
Na2O
%
0.60
氧化钾
K2O
%
1.48
二氧化钛
TiO2
%
1.00
三氧化硫
SO3
%
3.60
五氧化二磷
%
0.1
2.2.2.2.2.2烟气参数
(37)FGD入口烟气参数
锅炉BMCR工况烟气参数
单位
设计煤
备注
FGD入口烟气量(BMCR,每炉)
Nm3/h
1126883
标态,干基,6.15%O2
Nm3/h
1197781
标态,湿基,5.78%O2
m3/h
1667326
干基,6.15%O2
m3/h
1772224
湿基,5.78%O2
FGD入口烟气温度
℃
124
最低停运温度160℃
FGD入口烟气压力
Pa
0
BMCR工况
(38)锅炉BMCR工况烟气中污染物成分(技改煤质,标准状态,干基,6.15%O2)
项目
单位
设计煤
SO2
mg/Nm3
5891
SO3
mg/Nm3
125
Cl(HCl)
mg/Nm3
54
F(HF)
mg/Nm3
28
烟尘(引风机出口)
mg/Nm3
103
2.3.2.3主要设备及参数
设备名称
参数名称
单位
数据
锅炉
型式
最大连续蒸发量
t/h
1065
台数
台
2
引风机
型式
静叶可调轴流式
数量(每台炉)
个
2
烟囱
高度
m
210
出口内径
m
内部防腐材料
2.4.2.4水质
电厂补给水主要水源为##,##地下水作备用水源,水质如下:
表3-1
项目
单位
##地下水
取样日期
2001.11.5
2001.1.12
外状
透明
透明
pH值
8.15
7.61
导电度25℃
μs/cm
温度
℃
25
16.6
全固形物
mg/L
299
316.8
溶解固形物
mg/L
289.9
315.8
悬浮物
mg/L
9.10
1.0
灼烧碱量
mg/L
111.10
136
二氧化硅
mg/L
13.10
12
铁铝氧化物
mg/L
8.20
2.0
耗氧量
mg/L
1.224
0.166
全碱度
mmol/L
4.20
4.50
全硬度
mmol/L
4.60
5.40
钙
mg/L
89.80
105.20
镁
mg/L
1.43
1.823
钾
mg/L
1.34
0.606
钠
mg/L
5.50
2.50
铜
mg/L
0.0053
0.0052
铁
mg/L
0.036
0.0233
重碳酸根
mg/L
256.30
274.95
硫酸根
mg/L
17.53
31.11
氯离子
mg/L
9.50
11.00
硅酸根
mg/L
8.235
11.15
阳离子总和
mmol/L
4.875
5.525
阴离子总和
mmol/L
5.057
5.755
2.5.2.5石灰石品质
·来源
鹤煤集团建材厂
·距电厂距离
Km
·运输方式
-
罐车到厂
·来源容量
t/a
29000
矿物组份分析
CaCO3
wt-%
93.66
H2O
wt-%
0.05
MgO
wt-%
0.71
SiO2
wt-%
2.02
Al2O3
wt-%
0.20
CaO
wt-%
53.8
S03
wt-%
0.32
烧失量
wt-%
42.56
-粒径
μm
44
2.6.2.6电厂大气污染物排放情况
原有脱硫装置按照设计煤种(S=0.68%)设计,脱硫效率不低于90%。
现在实际燃用煤种硫含量在2%-3%之间,远远超过原设计,不仅脱硫效率下降,更为严重的是脱硫系统无法连续全烟气运行,否则将危害设备及系统安全,也就是说,因为脱硫系统无法连续全烟气运行,因此电厂二氧化硫排放量不能满足目前环保排放要求400mg/Nm3,据此,必须对原有的脱硫装置进行增容改造,以满足环保要求。
3.第三章、脱硫系统改造
3.1.3.1总图部分
脱硫岛总平面布置改造方案:
本期脱硫装置改造,基本与原有脱硫岛总平面布置保持一致。
仅在需要改造的设备进行局部修改和增加。
总平面布置主要修改有:
一、无GGH方案:
1、吸收塔直径加大同时增加高度,两台吸收塔基础均向GGH方向偏移,同时靠近吸收塔的
(1)列柱向GGH方向移动2m;
2、由于吸收塔高度增加,造成吸收塔出口烟道相应提高,原有GGH烟道框架增高;
3、1号浆液循环泵房右侧增加一跨,零米放置新增浆液循环泵,二楼放置更换后的真空皮带脱水机设备;
4、2号浆液循环泵泵房左侧放置新增浆液循环泵,并增加循环泵检修起吊框架;
二、有GGH方案
1、吸收塔直径与位置保持不变,增加吸收塔高度;
2、原有GGH烟道框架增高,满足增高后的吸收塔出口烟道布置要求;
3、1号吸收塔新增浆液循环泵放置于吸收塔左侧石膏库房上方,2号吸收塔新增浆液循环泵放置于吸收塔右上方。
两台新增浆液循环泵考虑采用汽车吊检修吊装,不再另设检修起吊装置;
4、原有真空皮带脱水机厂房向1号增压风机方向增加6m宽一跨,满足更换后真空皮带脱水机布置要求。
以上两种方案,更换后氧化风机均在原有风机处增大设备基础,布置更换后氧化风机。
新增一座石灰石粉仓及石灰石浆液制备系统、废水处理系统统一布置在1号机引风机区域左侧与电厂管架之间空地区域。
新增石灰石粉仓与原有脱水楼之间预留9m宽道路,1号机增压风机检修通车要求。
其它脱硫岛布置基本保持原有状况,尽可能减少拆迁和修改工作量。
3.2.3.2工艺部分
本次改造,参照原有系统,根据石灰石-石膏湿法脱硫工艺特点,并遵循系统简单、安全可靠、维护方便、尽可能减少改造工作量的原则进行。
工艺系统由下述各分系统组成:
石灰石浆液制备系统、烟气系统、SO2吸收系统、排空系统、石膏脱水系统、工艺水系统、新增废水处理系统等。
3.2.1.3.2.1石灰石浆液制备系统
(39)3.2.1.1原有石灰石浆液制备系统简述
石灰石浆液制备系统为两炉公用,采用外购石灰石粉(粒径90%小于44μm)。
加水搅拌,制成浓度为30%(wt)石灰石浆液,供给吸收塔系统。
系统包括石灰石粉仓,旋转给料机,石灰石浆液池、搅拌器、石灰石浆液给料泵及输送管道等。
两台机组共用一个石灰石粉仓,有效容积按两台炉设计煤种BMCR工况下石灰石3天(24小时)耗量设计。
(40)3.2.1.2石灰石耗量
每台机组每小时耗石灰石量(t/h)
两台机组每小时耗石灰石量(t/h)
两台炉日耗石灰石量(t/d)
改造前
2.96
5.92
142.1
改造后
11.6
23.2
556.8
注:
1、石灰石CaCO3含量按90%考虑;
2、石灰石耗量按设计煤种耗量考虑;
(41)3.2.1.3石灰石浆液制备系统改造方案
原有石灰石粉仓450m3,按照两台炉石灰石3天耗量设计,三台石灰石浆液输送泵(两运一备)分别向两台吸收塔供应成品石灰石浆液,每台出力Q=19m3/hH=55m。
本次改造保留原有该浆液制备系统,原有系统仅用于给2号吸收塔提供石灰石浆液制备。
石灰石粉仓满足单台吸收塔2天耗量,三台石灰石浆液输送泵仅用于2号吸收塔供浆,采用两运一备,修改相应管道系统。
1号吸收塔系统新增一座石灰石粉仓640m3,满足单台吸收塔3天石灰石耗量,同时增加一座石灰石浆液箱200m3,新增两台石灰石浆液输送泵用于1号吸收塔浆液供浆,每台出力Q=60m3/hH=45m。
(42)3.2.1.4石灰石浆液制备系统,改造方案设备变化参见工艺设备清册。
3.2.2.3.2.2烟气系统及SO2吸收系统
3.2.2.1.3.2.2.1原有烟气系统及SO2吸收系统简述
从锅炉引风机后的烟道上引出的烟气,经增压风机升压,通过烟气换热器(GGH)将热原烟气中的热量蓄积并加热吸收塔出来净化后的冷烟气。
原烟气温度由116℃降至76.8℃经过吸收塔的入口向上流动穿过托盘及喷淋层,在此,烟气被冷却、饱和,烟气中的SO2被吸收。
经过喷淋洗涤的冷烟气经除雾器除去水雾后,进入烟气换热器(GGH)的冷端,离开GGH后被加热至80℃,加热后的冷烟气通过旁路烟道进入烟囱。
在电厂旁路烟道上设置旁路烟气挡板门,当锅炉启动和FGD装置故障停运时,烟气由旁路烟气挡板经烟囱排放。
整个烟气系统采用将增压风机布置在吸收塔上游烟气侧运行的方案,以保证整个FGD系统均为正压操作,并同时避免增压风机可能受到的低温烟气的腐蚀,从而保证了增压风机及整个FGD系统安全、长寿命运行。
烟气系统为单元制,每炉烟气系统包括1台增压风机、1个旁路烟气挡板、1个入口原烟气挡板、1个出口净烟气挡板及相应的烟道,膨胀节等。
SO2吸收系统设置主要用于脱除烟气中SO2、SO3、HCl、HF等污染物及烟气中的飞灰等物质。
FGD的二氧化硫吸收系统包括一台吸收塔(含两级除雾器、两层喷淋层及喷嘴、托盘、氧化空气矛式喷管)、四台侧进搅拌器、两台浆液循环泵、一台氧化风机(两台吸收塔公用两运一备)及相应的管道阀门等。
该系统包括以下几个子系统:
吸收塔系统、浆液再循环系统、氧化空气系统。
3.2.2.2.3.2.2.2改造前后参数对比
3.2.2.2.1.3.2.2.2.1增压风机
原设计参数
改造后参数(无GGH)
改造后参数(有GGH)
BMCR工况进口烟气量
1604194m3/h
1772224
1772224
TB工况进口烟气量
1810329m3/h
增压风机BMCR工况设计压升
3417Pa
3400
4900
增压风机TB工况设计压升
4100Pa
4100
5880
风机进口温度
113℃
124
124
3.2.2.2.2.3.2.2.2.2烟气换热器
原设计参数
改造后参数(无GGH)
改造后参数(有GGH)
原烟气侧进口烟气量
1574537m3/h
1722339m3/h
原烟气侧出口烟气量
1408095m3/h
1558863m3/h
净烟气侧进口烟气量
1325045m3/h
1476463m3/h
净烟气侧出口烟气量
1507458m3/h
1659007m3/h
原烟气侧进口温度
116℃
128℃
原烟气侧出口温度
76.8℃
92.5℃
净烟气侧进口温度
42℃
45.9℃
净烟气侧出口温度
80℃
80℃
3.2.2.2.3.3.2.2.2.3吸收塔系统
原设计参数
改造后参数(无GGH)
改造后参数(有GGH)
吸收塔进口烟气量
1408095m3/h
1739851
1558863m3/h
吸收塔出口烟气量
1325045m3/h
1544382
1476463m3/h
喷淋层数量
2层
3层
3层
喷淋层运行方式
全部运行
全部运行
全部运行
托盘开孔率
36%
30.5%
32%
入口SO2浓度
1611mg/DNm3
5892mg/DNm3
5892mg/DNm3
出口SO2浓度
117mg/DNm3
291mg/DNm3
291mg/DNm3
脱硫效率
90%
95%
95%
氧化风机设计流量
3500m3/h
14330Nm3/h
9597m3/h
氧化风机设计压升
83kPa
98kPa
150kPa
石膏浆液排出量
24m3/h
94m3/h
94m3/h
3.2.2.3.3.2.2.3烟气系统及SO2吸收系统改造方案
改造方案的原则是按照原有的场地布置和设备配置情况做最小最经济的改动,尽可能多的保留原有的设备。
按照无GGH和有GGH两种方案设计。
无GGH方案,由于设计煤种含硫量增大较多,吸收塔直径加大,同时增加一层喷淋层,吸收塔基础向GGH方向增大偏移。
有GGH方案,由于场地条件有限,该方案仅考虑吸收塔直径、位置不变,增高吸收塔浆池高度,同时增加一层喷淋层,原有GGH布置不变。
3.2.2.3.1.3.2.2.3.1浆液循环系统
由于实际的燃煤含硫量远远高于设计煤种,因此吸收塔的喷淋层需要增加一层,浆池容量也要增加。
(43)一、无GGH方案
吸收塔浆池部分直径改为14m,上部直径12m,增加一层喷淋层。
浆液循环泵设计出力为由Q=5289m3/h修改为Q=5500m3/h,扬程由18.3m/20m修改为19.1m/20.8m均可在原有设备基础上相应改造。
同时每台吸收塔增加一台浆液循环泵Q=5500,扬程22.5m。
除雾器(部分利用)、喷淋层、托盘、吸收塔搅拌器(增加)均根据该设计方案进行更换改造。
(44)二、有GGH方案
原有吸收塔直径不变,浆池部分增加8.26m,喷淋层增加1.9m。
浆液循环泵采用原有设备不变,同时每台吸收塔增加一台Q=5289m3/h,H=21.9m的浆液循环泵。
托盘、吸收塔搅拌器(增加)均根据该设计方案进行更换改造。
每塔增加一层喷淋层。
3.2.2.3.2.3.2.2.3.2氧化空气系统
改造前氧化空气流量为3500Nm3/h,改造后流量为14330Nm3/h,由于场地所限,增加氧化风机不可行,改造方案为更换所有氧化风机。
为了减少改造后氧化风机的电耗,提高氧化效果,氧化方式由原有的矛射式改为管网式。
原有塔内外氧化空气管道全部更换。
无GGH方案,氧化风机压升98kpa;有GGH方案,氧化风机压升为150kpa。
3.2.2.3.3.3.2.2.3.3石膏排出系统
原有系统的吸收塔浆液排出量为24m3/h,吸收塔排出泵出力为38m3/h。
改造后吸收塔浆液排出量为94m3/h,原有排出泵不能满足需要,而且现有布置场地有限,本次改造考虑重新更换所以吸收塔排出泵,设计出力为Q=115m3/h,H=45m,共4台。
3.2.2.3.4.3.2.2.3.4烟气系统
3.2.2.3.4.1.一、无GGH方案
根据新的物料平衡计算,取消GGH后,增压风机无须改造,原有增压风机能够满足改造后要求。
由于吸收塔修改,吸收塔进出口烟道需相应修改。
由于无GGH时,吸收塔出口净烟气直接进入电厂烟囱,此时烟气温度约为49℃,电厂烟囱应考虑湿烟气对烟囱的腐蚀,对现有烟囱进行防腐处理。
烟囱防腐施工安装,由业主组织实行,未包含在本报价范围内。
3.2.2.3.4.2.二、有GGH方案
根据核算,如保留GGH,系统阻力增大较多。
原有增压风机不能满足改造后要求,需更换设备型号,原有扩压器及筒芯可现场实施修割后使用。
由于脱硫装置入口烟气温度较原来提高,原有GGH基本可以满足换热要求。
由于吸收塔高度增加,吸收塔进出口烟道需相应修改。
3.2.2.3.5.3.2.2.3.5吸收塔本体
(45)一、无GGH方案
吸收塔直径加大、高度增加,原有吸收塔需推倒重来,修改后吸收塔本体较原来变化较大,需重新制作。
(46)二、有GGH方案
吸收塔直径不变、高度增加,吸收塔浆池16mm厚区域增加8.26m,喷淋层区域增加1.9m高。
由于施工影响原有防腐,两种方案吸收塔防腐均考虑重新施工。
(47)3.2.2.3.6烟气系统及SO2吸收系统,改造方案设备变化参见工艺设备清册。
3.2.3.3.2.3排空系统
3.2.3.1.3.2.3.1原有的排空系统简述
原有FGD岛内设置一个两台炉公用的事故浆液池,用来储存吸收塔在停运检修和/或修理期间吸收塔下部浆池中的部分浆液,满足吸收塔重新启动时石膏浆液晶种需要。
事故浆液池配1台顶进式搅拌器。
事故浆液池设浆液返回泵1台。
浆液返回泵将事故浆液池中的浆液送回吸收塔。
FGD装置的浆液管道和浆液泵等,在停运时需要进行冲洗,其冲洗水就近收集在FGD装置区内设置的排水坑内。
每个吸收塔区各设有一带搅拌器的排水坑,汇集系统冲洗、排放和溢流的液体,每个排水坑设置一台排水坑泵将排水坑中的浆液送到吸收塔。
3.2.3.2排空系统改造方案
无GGH方案,由于吸收塔基础增大,原有吸收塔排水坑移动至吸收塔远离烟囱侧,两台机组对称布置。
有GGH方案,吸收塔排水坑保持不变。
两种方案,事故浆液池保持原有不变,满足吸收塔重新启动石膏晶种需