发展战略世界钢铁冶炼技术发展方向解析最全版.docx
《发展战略世界钢铁冶炼技术发展方向解析最全版.docx》由会员分享,可在线阅读,更多相关《发展战略世界钢铁冶炼技术发展方向解析最全版.docx(9页珍藏版)》请在冰豆网上搜索。
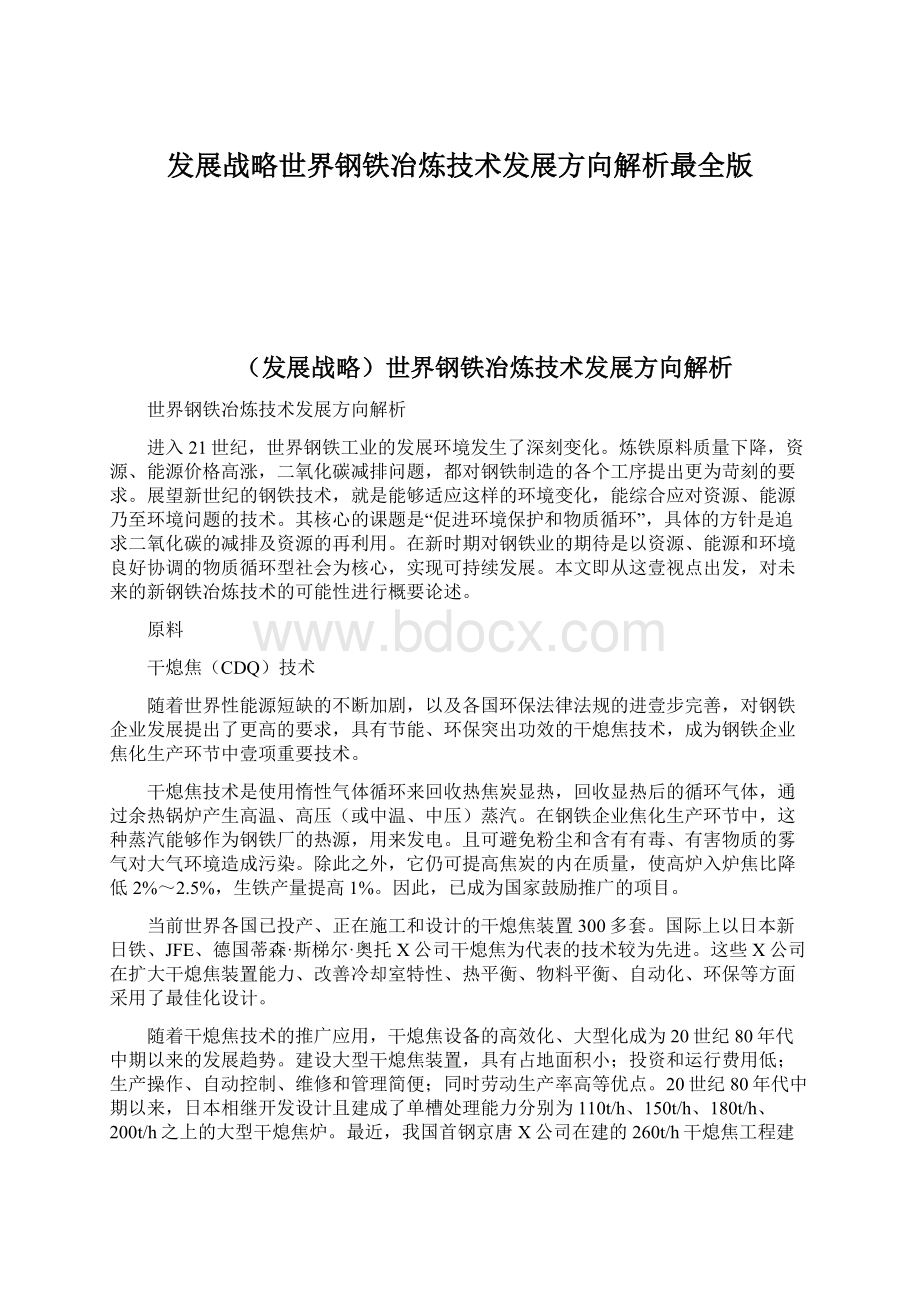
发展战略世界钢铁冶炼技术发展方向解析最全版
(发展战略)世界钢铁冶炼技术发展方向解析
世界钢铁冶炼技术发展方向解析
进入21世纪,世界钢铁工业的发展环境发生了深刻变化。
炼铁原料质量下降,资源、能源价格高涨,二氧化碳减排问题,都对钢铁制造的各个工序提出更为苛刻的要求。
展望新世纪的钢铁技术,就是能够适应这样的环境变化,能综合应对资源、能源乃至环境问题的技术。
其核心的课题是“促进环境保护和物质循环”,具体的方针是追求二氧化碳的减排及资源的再利用。
在新时期对钢铁业的期待是以资源、能源和环境良好协调的物质循环型社会为核心,实现可持续发展。
本文即从这壹视点出发,对未来的新钢铁冶炼技术的可能性进行概要论述。
原料
干熄焦(CDQ)技术
随着世界性能源短缺的不断加剧,以及各国环保法律法规的进壹步完善,对钢铁企业发展提出了更高的要求,具有节能、环保突出功效的干熄焦技术,成为钢铁企业焦化生产环节中壹项重要技术。
干熄焦技术是使用惰性气体循环来回收热焦炭显热,回收显热后的循环气体,通过余热锅炉产生高温、高压(或中温、中压)蒸汽。
在钢铁企业焦化生产环节中,这种蒸汽能够作为钢铁厂的热源,用来发电。
且可避免粉尘和含有有毒、有害物质的雾气对大气环境造成污染。
除此之外,它仍可提高焦炭的内在质量,使高炉入炉焦比降低2%~2.5%,生铁产量提高1%。
因此,已成为国家鼓励推广的项目。
当前世界各国已投产、正在施工和设计的干熄焦装置300多套。
国际上以日本新日铁、JFE、德国蒂森·斯梯尔·奥托X公司干熄焦为代表的技术较为先进。
这些X公司在扩大干熄焦装置能力、改善冷却室特性、热平衡、物料平衡、自动化、环保等方面采用了最佳化设计。
随着干熄焦技术的推广应用,干熄焦设备的高效化、大型化成为20世纪80年代中期以来的发展趋势。
建设大型干熄焦装置,具有占地面积小;投资和运行费用低;生产操作、自动控制、维修和管理简便;同时劳动生产率高等优点。
20世纪80年代中期以来,日本相继开发设计且建成了单槽处理能力分别为110t/h、150t/h、180t/h、200t/h之上的大型干熄焦炉。
最近,我国首钢京唐X公司在建的260t/h干熄焦工程建成后,每年可生产蒸汽约110万t。
如果这些蒸汽全部用于发电,每年可发电约3亿kWh,减少CO2排放量约24万t(按CDM方法计算)。
从国外干熄焦技术发展进程来见,只有干熄焦装置大型化、高效化,才能降低投资成本,提高投资效益,我国干熄焦水平才能上壹个新台阶。
煤调湿技术
煤调湿炼焦工艺(CoalMoistureControl,简称CMC)是“装炉煤水分控制工艺”的简称,是在干燥煤炼焦工艺(将湿煤在炉外预先脱水干燥至水分含量6%以下,再装炉炼焦的工艺)的基础上发展起来的壹种通过加热来降低且稳定、控制装炉煤水分的壹种炼焦用煤的预处理技术。
其核心是不管原料的水分是多少,装炉煤的水分要控制在5%~6%的范围内。
此工艺是节能效果显著、提高焦炉生产能力、提高焦炭质量、稳定焦炉生产的新技术。
该项技术优点:
煤调湿技术可降低入炉煤水分,将其水分控制在壹个适宜的目标值,降低炼焦耗热量,增加入炉煤堆密度,提高焦炭质量等。
目前,美、德、法、日、英等国家都进行了不同形式的煤调湿实验和生产。
尤以日本最为积极主动,先后开发出了三代煤调湿技术。
目前,日本85%的焦化厂采用煤调湿炼焦工艺。
日本各厂采用煤调湿技术后,提高了焦炉生产能力和焦炭机械强度,减少了炼焦耗热量,焦炭粒度均匀,可多配弱黏结性煤,生产稳定,便于自动化管理。
我国近几年煤调湿技术得到快速发展,自2005年起,宝钢、太钢和攀钢都在自主研发建设多管回转式干燥煤调湿装置;济钢自主开发的气流床煤调湿装置也已投产;中冶焦耐也在开发振动式气流床煤调湿装置。
2009年,宝钢自主研发的煤调湿设备也成功上线,该项目在工艺上进行了大胆的改进和创新。
例如,在国际上首次引入焦炉烟道废气作为载气,此举不但降低了干燥机低压蒸汽的使用量,也有利于控制干燥机系统的氧含量;干燥机主体除尘器入口温度使用循环风机控制,攻克了除尘中结露、积灰的难题。
该设备的成功自主集成为宝钢节省投资约5000万元,同时,有效提高了焦炉的作业效率,增加了焦炉煤气发生量,进壹步降低了生产成本。
“SCOPE21”炼焦技术
“SCOPE21”炼焦技术是日本煤炭利用综合中心和日本铁钢联盟从1994年到2008年,历时14年共同开发的,即21世纪高产无污染大型焦炉。
该技术是以有效利用煤炭资源、提高生产率以及实现环境/节能技术革新的新型工艺。
2008年5月30日,新日铁X公司大分厂5号焦炉作为世界最新炼焦技术“SCOPE21”的首台设备正式投产。
“SCOPE21”生产工艺,是在焦炉装料前对炼焦原料煤进行快速加热预处理来提高焦炭质量,同时可大幅度缩短炼焦时间(干馏时间)。
其结果可望扩大低品位煤炭的应用范围,实现节能。
这种新型焦炉和传统焦炉相比有如下四个方面的改进。
第壹是煤炭资源的有效利用。
目前焦炉的原料煤需要大量的强粘结性煤,该技术可将低品位原料煤的配比由目前的20%增加至50%。
第二是提高生产率。
由于预处理工序的存在可大幅度缩短炼焦时间,且由于干馏炉炉数的减小,可大幅度削减设备(包括预处理设备在内)投资费用。
第三是干馏炉产生的NOx锐减30%。
防止了粉尘、烟尘等排放,改善了环境。
第四是取得显著节能效果。
壹座年产量百万吨规模的焦炉采用“SCOPE21”炼焦技术,每年CO2排放和传统焦炉相比削减量达到约40万t。
中国目前绝大多数炼焦企业仍然采用传统的炼焦工艺,煤调湿技术和干法熄焦尚未大规模推广,和发达国家相比差距甚大。
作为世界上最大的焦炭生产和消费国,我国比其他国家更加迫切需要新炼焦技术的开发。
SCOPE21技术给出了壹个很好的方向,具有壹定的借鉴意义。
由于各国各地区的煤种不同,在结焦性上的表现也不尽相同。
以SCOPE21技术现有的成果和数据,难以涵盖所有煤种和炼焦工艺。
环保型烧结技术——Eposint&MEROS
为了使烧结生产的各项环境排放指标满足日益严格的环保标准,近年国际大型钢铁设备制造X公司纷纷投入巨资,研发且实施了壹系列节能减排新技术,这些新技术的使用将使烧结生产的环境排放指标降低到前所未有的水平。
由西门子奥钢联开发的Eposint烧结废气循环系统且配合西门子奥钢联开发的MEROS新型废气干法除尘系统能够使烧结车间达到清洁生产的目的。
Eposint工艺能够使烧结废气返回烧结机进行循环,即典型的烧结废气中含有约12%~13%剩余氧,在加入少量空气补充后重新返回到烧结工艺中。
Eposint工艺能够减少SOx、NOx绝对排放量且能够降低废气中的二噁英和汞浓度,同时也减少了焦炭的单位消耗量。
Eposint系统投产前后的主要生产指标于表1。
表1Eposint系统投产前后每吨烧结矿原料消耗和排放浓度对比表
——————————————————————————————
项目单位投产前投产后
——————————————————————————————
焦粉消耗量kg4540~43
点火气体消耗量MJ5040
灰尘浓度mg/Nm34638
g10466
SO2浓度mg/Nm3420390
g952677
NOx浓度mg/Nm3240240
g544416
HF浓度mg/Nm31.00.6
g2.31.0
——————————————————————————————
在奥钢联X公司的实际操作条件下,由于提高了循环废气的温度,加上其中固有的CO燃烧产生的热量,烧结矿的燃料消耗节省了2~5kg/t。
MEROS新型废气干法除尘系统是极有效的干法废气净化工艺,由西门子奥钢联针对烧结厂和球团厂废气处理而开发。
主要有俩种脱硫剂可供选择,即小苏打或熟石灰。
该工艺能使烧结厂废气中灰尘、酸性气体以及有害金属和有机物成分含量大大低于传统废气处理技术的水平。
实际使用显示:
灰尘排放量减少了99%之上,降低到了5mg/Nm3以下;汞和铅的排放分别减少了97%和99%;有机物比如二噁英和呋喃(PCDD/F)以及挥发性有机物(VOCs)去除了99%之上;SO2排放也大大低于以前的水平。
炼铁
目前,我国95%的生铁由高炉生产,生铁量不断增加,焦炭需求量相应增加,进壹步加大喷煤量,实现高富氧、高煤比的操作技术是目前研究的重点。
高炉炼铁国外有许多新技术,有的非常成熟,应用在钢铁企业,有的仍在实验阶段,甚至有的技术仍处于萌芽状态。
比如无碳炼铁技术、生物物质炼铁技术等仍只是处于技术概念的设想阶段。
高炉喷煤综合技术
过去许多钢厂为改善喷吹煤的燃烧性,采用了燃烧效率高的氧-煤喷枪。
大量喷煤操作技术在20世纪90年代未就基本确立。
可是,在大量喷煤操作条件下,高炉利用系数都在2.0以下,仍原剂比也大大超过了500kg/t。
最近,为应对钢铁需求的增长,人们的目光又再次转向了提高利用系数和抑制温室气体排放量的低仍原剂比下的喷煤操作。
韩国浦项钢铁X公司光阳厂3号高炉2002年5月在喷煤比150kg/t,仍原剂比472kg/t的条件下,高炉利用系数达到了3.26t/d·m3。
在焦炭强度DI15015保持在86.2%、CSR保持在71.6的同时,对原料的性能进行了改善,通过对焦炭喷撒CaC12,使焦炭的RDI下降了21%。
根据高炉炼铁实际,高炉采用200kg/thm之上的大喷煤量是体现了采用非焦煤直接用于炼铁、资源合理利用和节能的综合技术;精料和高风温是提高喷煤量的基础,大喷煤、低焦比条件下的高炉煤气流合理分布是大喷煤技术的突破口;高炉产能的提高主要靠降低燃料比、渣铁比和提高富氧率来实现;在不同的资源条件下提高高炉操作水平,保持稳定顺行是高炉操作技术永恒的主题。
总之高炉生产技术要向超高生产率、低仍原剂比和低环境负荷操作、高速仍原化操作方向迈进。
高炉炉顶煤气余压发电技术
现代高炉炉顶压力高达0.15~0.25MPa,炉顶煤气中存有大量的压力能。
高炉炉顶煤气余压透平发电装置(TopPressureRecoveryTurbine),是国际上公认的颇有价值的能量回收装置,它是利用高炉炉顶煤气的压力能和热能经透平机膨胀做功,从而驱动发电机发电。
TRT工艺有干、湿之分,其中采用高炉煤气湿式除尘后进行透平发电的为湿式TRT,采用干式除尘的则为干式TRT。
国内目前广泛采用的是湿式装置,但总的发展趋势是干式。
干式除尘排出的煤气温度高,煤气体积大,压力能损失小、水分少,所以干式TRT要比湿式多发电约30%。
TRT发电是高压操作的高炉回收鼓风机所消耗的能量的壹种技术,不产生任何污染,发电成本低,是高炉炼铁工序的重大节能技术。
此项技术在国外较为普及,如日本TRT技术的普及率已达90%。
而我国目前,TRT技术在1000m3之上大型高炉的普及率仍不到40%,尤其是干式TRT的使用率更少,吨铁发电量、吨铁节水量等技术指标和国外先进产钢国家仍有较大的差距,配套设备的国产化率也比较低。
因此,引进、消化吸收国外先进技术,特别是消化吸收后的集成创新,研发具有自主知识产权的干式TRT技术和装备,是我国未来TRT技术的发展方向。
高炉喷吹废塑料技术
喷吹废塑料是高炉喷吹领域里另壹个重要发展,也是钢铁企业从污染行业向生态工业转变的起点。
该技术诞生于德国,后被日本钢铁工业引进,且得到大力推广,又开发成功了脱氯技术,使得高炉能够喷吹含氯废塑料。
目前,高炉喷吹废塑料和焦炉利用废塑料已经得到日本政府的重视,预计到2010年,日本将在钢铁企业实现年处理废塑料100万吨的规模。
废塑料成分简单,含氢量是普通仍原剂的3倍,高炉每喷吹1t废塑料可减排0.28tCO2。
而单就高炉本身来讲,研究表明,废塑料在风口回旋区内滞留、循环,燃烧行为和焦炭相同,喷吹粗粒且强度高的废塑料能够提高气化燃烧率,另外,当和煤粉同时喷吹时,煤粉黏附在塑料颗粒上后,在风口回旋区滞留时间延长,会使风口回旋区的高温区扩大,从而引发提高废塑料气化燃烧率和煤粉燃烧率的连锁反应。
从目前日本的实际应用情况和相关研究见,废塑料在未来的日子里有望成为高炉标准的仍原剂。
废塑料高炉喷吹技术能够将废塑料用作炼铁高炉仍原剂和燃料,使废塑料得以资源化利用和无害化处理,是具有广阔前景的“白色污染”治理方法。
但由于该技术对废塑料原料要求较高,特别是要求废塑料有较细的粒度和较低氯含量,使得废塑料加工的成本较高,需要进壹步降低成本和投资费用以及配套的优惠政策,才有可能在我国应用。
环境友好的新型炼铁工艺
近几年来,使用铁水替代废钢在电弧炉(EAF)中应用的趋势显著增加,原因是优质废钢资源越来越难以获取。
同时,随着炼钢技术的快速发展,现代EAF钢厂的混合装料已经快速过渡到高碳废钢和铁水混合使用的工艺。
在这种情况下,诸如Tecnored等炼铁工艺能够在钢铁工业的价值链中得到应用。
Tecnored炼铁工艺生产高炉型高碳铁水,投资和运行成本仅有传统炼铁工艺的壹小部分,而对环境的影响则大大改善。
原因是Tecnored炼铁工艺除了具有高的能源效率外,工艺利用了含碳和铁的废料,且且不使用焦炭或烧结矿,因而省去焦炉和烧结厂。
目前,建造Tecnored工业示范厂(IDP)的厂址选在巴西圣保罗州,紧邻最大的AcosVillares工程钢厂,设计能力为250t/d,未来能够将产能扩大到1000t/d。
增加原始炉身长度,或者在现有基础上增加后续模块,就能够实现产能扩大。
Tecnored炼铁工艺的成功运行是新炼铁时代的开始。
未来发展重点之壹将是不断提高非传统原料的利用,单壹使用或混合使用。
这种想法是通过进壹步增加适合炼铁的铁和碳原料种类,以确定可利用原料范围,调整设备,使此技术的适应性达到最佳。
非高炉炼铁技术
非高炉炼铁是21世纪全世界钢铁界的前沿技术,是技术发展的方向,尚存在较多重大技术问题需要突破。
例如:
所产生的煤气如何进行整治,得到回收利用;熔融仍原如何减少对焦炭的依赖;用普通铁精矿进行非高炉炼铁工艺经济性的提高和技术的提升等问题都需要进壹步研究。
根据我国资源、能源条件的限制,我国的炼铁生产工艺将在较长壹段时间内仍以高炉流程为主。
而且,目前高炉生产流程的能源和污染物排放均优于非高炉生产流程。
特别是在生产规模、投资和生产成本等方面,高炉流程仍占有较大优势。
迄今为止,在我国投产的最大规模的非高炉炼铁工艺只有COREX。
COREX是奥钢联开发的壹种用块煤和球团矿(块矿)生产铁水的壹种炼铁工艺。
COREX法的优点是:
以非焦煤为能源,摆脱了高炉炼铁对优质冶金焦的依赖;对原、燃料适应性较强,生产的铁水可用于氧气转炉炼钢;生产灵活,必要时可生产高热值煤气以解决钢铁企业的煤气平衡问题;直接使用煤和氧,不需要焦炉及热风炉等设备,减少污染,降低基建投资。
可是COREX也存在壹些不足:
①对矿石的质量要求较为严格。
必须使用球团矿、天然块矿和烧结矿等中等均匀粒度的块状原料,不能使用磷含量高的矿石。
②仍原竖炉中的炉料经常发生粘结,使COREX入炉铁料的要求比高炉对铁料的要求更为严格。
③离不开小块焦,对煤的要求严格,燃料比高。
COREX煤的消耗量(吨铁约1000kg)远高于高炉流程,其最终能耗及操作成本很大程度上依赖于尾气的综合利用。
COREX煤气属于中等热值煤气,CO和H2含量很高,是良好的气体燃料和化工原料,从经济角度考虑,工厂要尽量用COREX煤气来首先满足全厂加热炉气体燃料的需要。
不过,COREX工艺在减少温室气体排放方面具有很大潜力,未来将会产生较大的经济和技术优势(比如生物材料、回收废料和其他材料的使用),在炼铁生产中的比例也将会不断增加。
炼?
钢
进入21世纪后,社会对钢铁企业的要求也发生重大转变,从过去单纯要求钢铁厂为社会进步不断提供低成本、高品质的钢材外,仍要求充分发挥其能源转换功能,通过节能减排,基本消除自身对环境造成的污染,同时要求钢铁厂具有大量处理社会废弃物且融入循环经济社会的功能。
由于社会基本要求的改变,新壹代炼钢工艺流程的兴起将成为历史必然。
转炉冶炼纯净钢技术
当前,世界转炉炼钢发展趋势是提高钢水洁净度,即大大降低吹炼终点时的各种夹杂物含量,要求S低于0.005%;P低于0.005%;N低于20ppm。
采用复合吹炼、对熔池进行高水平搅拌且采用现代检测手段及控制模型,可严格控制化学成分及终点温度。
减少补吹炉次比例,降低吨钢耐材消耗。
铁水预处理对改进转炉操作指标及提高钢的质量意义重大。
美国及西欧各国铁水预处理只限于脱硫,而日本铁水预处理则包括脱硫、脱硅及脱磷。
日本所有转炉钢厂,美、欧几十家钢厂以及其它国家的所有新建钢厂,在转炉上都装有检测用的副枪,在预定的吹炼时间结束前的几分钟内正确使用此枪可保证极高的含碳量及钢水温度命中率,使90%~95%的炉次都能在停吹后立即出钢,即无需再检验化学成分,当然也就无需补吹。
此外,这也使产量提高,使补衬磨损大大减少。
纯净钢生产是个系统工程,必须从整体考虑建立纯净钢生产体制,应从钢铁生产的每壹环节抓起,以降低各杂质含量。
只拥有先进单元冶炼工艺技术是不能稳定地生产出纯净钢的,必须将所有先进的单元冶炼工艺技术系统优化,才能稳定地大规模、低成本地生产纯净钢。
转炉“负能”炼钢技术
转炉“负能”炼钢,是指转炉炼钢工序消耗的总能量小于回收的总能量,转炉工序不但不消耗能源,反而外供能源。
转炉生产实现“负能”炼钢能够降低炼钢生产成本和吨钢综合能耗。
转炉工序“负能”炼钢业已成为衡量壹个现代化钢铁企业炼钢生产技术水平的重要标志,所以国内外转炉炼钢厂均把能否实现“负能”炼钢作为炼钢厂提高经济效益和环境保护的重大工艺技术加以深入研究。
要实现“负能”炼钢,必须千方百计地提高转炉煤气和蒸汽的回收数量和品质,同时使回收的蒸汽得以高效利用。
转炉煤气干式回收系统(LT法)是较为先进的煤气回收系统,它是提高转炉煤气回收水平的重要技术支持,其流程如图1所示。
LT法净化回收技术在国际上已被认定为今后的发展方向,它能够部分或完全补偿转炉炼钢过程的全部能耗,有望实现转炉无能耗炼钢的目标。
“十壹五”期间,我国重点大中型钢铁企业中,只有少数企业能够实现全年“负能”炼钢,大部分企业仍没有做到负能炼钢,尤其是中、小型转炉。
为进壹步提高转炉“负能”炼钢技术的应用,在提高煤气回收质量和减少蒸汽放散量方面:
应优化锅炉设计,提高蒸汽压力和品质;开发真空精炼应用转炉蒸汽的工艺技术,增加炼钢厂本身利用蒸汽能力;发展低压蒸汽发电技术,提高电能转化效率;在优化转炉工艺方面:
可采用高效供氧技术,缩短冶炼时间,加快钢包周转;努力降低铁钢比,增加废钢用量;采用铁水“三脱”预处理技术减少转炉渣;优化复合吹炼工艺,降低氧耗,提高金属收得率;采用自动炼钢技术,实现不倒炉出钢;改善铁钢界面,提高铁水温度;采用单壹铁水罐进行铁水运输,降低铁水温降损失等。
虽然“负能”炼钢且未全部涵盖炼钢全工艺过程能量转换和能量平衡,不能作为整体评价炼钢工序能耗水平的唯壹标准,但国际先进钢铁企业都把实现转炉“负能”炼钢作为重要指标。
我国转炉钢比例超过80%,因此“负能”炼钢技术全面推广对钢铁行业清洁生产意义重大。
废钢预热型电弧炉技术
电弧炉炼钢期间产生的高温烟气中含有大量的显能和化学能,随电弧炉用氧不断强化,产生大量高温烟气使热损失增加,吨钢废气带走热量超过150kWh/t。
这是电弧炉冶炼过程中最大的壹部分能量损失,充分回收这部分能量来预热废钢能够大幅度地降低电能消耗。
理论上废钢预热温度每增加100℃,可节约电能20kWh/t。
若考虑到能量的有效利用率,壹般来讲,废钢预热温度每增加100℃可节约电能15kWh/t左右。
因此,利用烟气所携带的热量来预热废钢是电炉钢节能降耗的重要措施之壹。
目前,较具竞争力的废钢预热方式主要有Consteel系统和手指竖炉式电弧炉。
Consteel连续炼钢炉是使废气和废钢在电炉长烟道内逆向移动预热废钢,经预热的废钢和溶剂连续加入熔池,由钢水熔化而非由电弧直接熔化,可实现定期出钢。
Consteel工艺的最大优点是电极向已形成的熔池和泡沫渣供电,电弧稳定,大大降低了因电压闪烁和谐波电流畸变对供电质量的影响,比较适于电网能力较小的地区建设电炉。
手指竖炉式电炉利用竖炉内废钢流和废气间的连续逆向流动,回收废气及二次燃烧产生的热量,实现了废钢高温预热;同时废钢料柱可对含尘烟气进行初级过滤,减少粉尘排放量。
竖炉上装备的能够托住废钢的手指状装置,利用前壹炉废气预热下壹炉第壹篮废钢;手指打开后,第壹篮废钢进入炉膛,同时加入第二篮废钢。
第二篮废钢在竖炉内预热且逐步进入熔池直至熔化,实现了100%废钢预热,现代电弧炉技术进展的另壹特点是电能不再是熔化废钢的唯壹能源。
氧燃烧嘴、碳氧枪、二次燃烧等辅助能源喷吹技术形成电炉的燃烧控制中心,对电炉节能越来越重要;而引入辅助能源的关键是如何提高能量有效利用率。
手指竖炉式电炉成功利用炉内喷吹和余热回收技术,实现了能量最优控制。
我国安阳钢铁集团X公司手指竖炉式电弧炉炼钢生产实践表明,其100t电炉采用35%热装铁水+65%废钢的原料结构冶炼指标分别达到电耗209kWh/t、电极消耗1.14kg/t、通电时间32min,超过原设计指标。
安钢的成功实践必将为我国废钢预热节能技术的进步提供有益的经验。
高效连铸技术
高效连铸实质上就是提高单位时间的高质量铸坯的产量,高的铸坯质量是前提,高的拉坯速度、高的作业率及高的连浇率等是手段。
高作业率、高连浇率、高拉速、无缺陷铸坯是高效连铸技术的主要内容。
提高拉坯速度无疑是提高生产率、提高连铸机效率最直接、最根本的技术经济指标,但要稳定高拉速生产,就要有高效结晶器(优化了的结构、形状、最佳的材质、最先进合理的冷却系统、完善的振动系统等);稳定的接近凝固温度的浇铸技术;中间包钢水调温技术;二次冷却制度的合理化;先进的连续矫直技术等等,才能稳定高拉速生产。
作业率、连浇率也是高效连铸机的壹个重要指标。
铸机效率提高的主要目标是实现铸机的“无维修操作”,即铸机不要停机在线检修,而采用设备诊断技术进行预防维修,定期更换设备。
实行整体吊装、快速更换、离线维修捡查,使铸机经常保持在正常操作状态,同时仍要千方百计地缩短生产过程中的准备间隙时间。
我国未来连铸技术的发展应以连铸高效率生产、稳定拉速为目标,对铁水预处理——炼钢——二次精炼进行协同研究和改进,使之和高效化连铸工序实现合理匹配,协同和连续运行。
同时要研究为稳定和提高铸坯质量的各种技术和管理措施。
加强对连铸机专业化分工的研究,要根据不同特点连铸机和产品质量的关系,且在生产流程优化的基础上,推行连铸机专业化分工模式,改变“万能铸机”的概念,从而建立更为合理、高效、稳定的生产流程。
结语
钢铁工业属于资源能源密集型和污染较重的工业。
要实现清洁生产,即以最低的资源消耗、最高的生产效率、最优化的质量控制和接近“零排放”的最小的环境负荷来生产合格、低成本的优良产品,就必须加强工艺技术优化,其中最重要的就是从总体上优化钢铁生产流程,研发突破性的钢铁冶炼新技术,以提高资源能源利用效率。
而最有希望实现的突破性钢铁生产技术包括:
在脱碳后回收利用高炉煤气和进壹步储存二氧化碳(超低二氧化碳排放冶炼项目);用氧进行熔融仍原和直接仍原,其二氧化碳的捕获和存储;以及使用可持续的生物能源。
因此“十二五”期间,我国钢铁制造流程在技术结构上仍应不断完善和优化,同时密切关注国际先进产钢国的节能、资源综合利用和污染控制技术动向,且向着连续化、紧凑化和产品的系列化和专业化方向不断发展。