基于PLC的自动化零件装配线系统本科毕业设计 精品.docx
《基于PLC的自动化零件装配线系统本科毕业设计 精品.docx》由会员分享,可在线阅读,更多相关《基于PLC的自动化零件装配线系统本科毕业设计 精品.docx(41页珍藏版)》请在冰豆网上搜索。
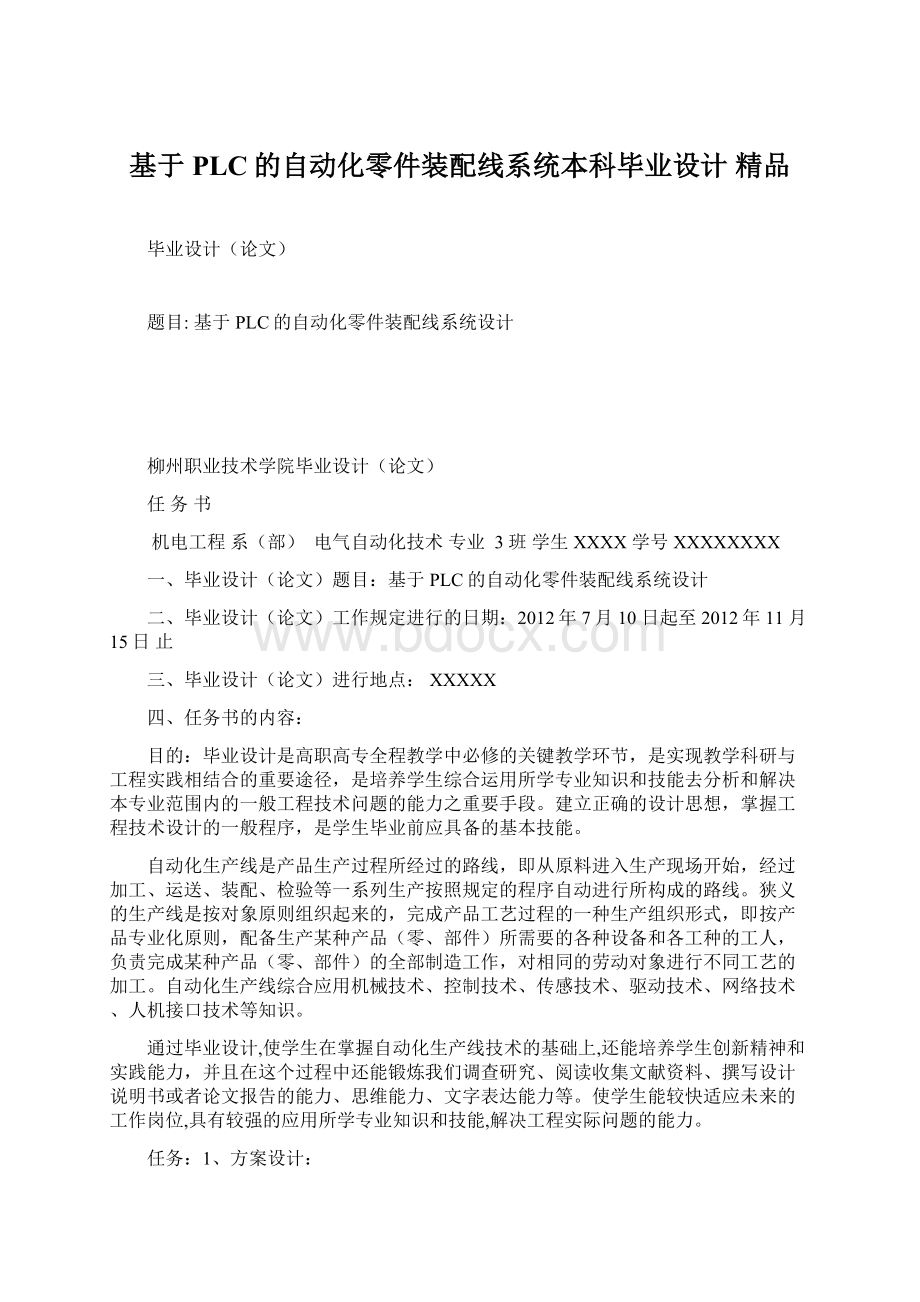
基于PLC的自动化零件装配线系统本科毕业设计精品
毕业设计(论文)
题目:
基于PLC的自动化零件装配线系统设计
柳州职业技术学院毕业设计(论文)
任务书
机电工程系(部)电气自动化技术专业3班学生XXXX学号XXXXXXXX
一、毕业设计(论文)题目:
基于PLC的自动化零件装配线系统设计
二、毕业设计(论文)工作规定进行的日期:
2012年7月10日起至2012年11月15日止
三、毕业设计(论文)进行地点:
XXXXX
四、任务书的内容:
目的:
毕业设计是高职高专全程教学中必修的关键教学环节,是实现教学科研与工程实践相结合的重要途径,是培养学生综合运用所学专业知识和技能去分析和解决本专业范围内的一般工程技术问题的能力之重要手段。
建立正确的设计思想,掌握工程技术设计的一般程序,是学生毕业前应具备的基本技能。
自动化生产线是产品生产过程所经过的路线,即从原料进入生产现场开始,经过加工、运送、装配、检验等一系列生产按照规定的程序自动进行所构成的路线。
狭义的生产线是按对象原则组织起来的,完成产品工艺过程的一种生产组织形式,即按产品专业化原则,配备生产某种产品(零、部件)所需要的各种设备和各工种的工人,负责完成某种产品(零、部件)的全部制造工作,对相同的劳动对象进行不同工艺的加工。
自动化生产线综合应用机械技术、控制技术、传感技术、驱动技术、网络技术、人机接口技术等知识。
通过毕业设计,使学生在掌握自动化生产线技术的基础上,还能培养学生创新精神和实践能力,并且在这个过程中还能锻炼我们调查研究、阅读收集文献资料、撰写设计说明书或者论文报告的能力、思维能力、文字表达能力等。
使学生能较快适应未来的工作岗位,具有较强的应用所学专业知识和技能,解决工程实际问题的能力。
任务:
1、方案设计:
完成一个工件的拆卸、分拣工作,模拟一个生产流水线的生产过程。
首先由供料站提供原料,运输站将其送至加工站加工,然后送至装配站进行安装,最后由分拣站进行分拣。
设计以送料、加工、装配、输送、分拣等工作单元作为自动生产线的整体设计,构成一个典型的自动生产线的机械平台
2、技术设计:
以PLC编程控制技术、变频器控制技术、气动机械控制技术、传感器技术和伺服电机控制技术等,设计出包括供料单元、分拣单元、输送单元、加工单元及装配单元在内的五个单元的程序,各单元为一个工作站,每个工作站均设置一台PLC承担其控制任务,各PLC之间通过RS-485串行通信线实现互连,构成分布式的控制系统。
3、图纸设计:
按照设计要求,绘制出基于PLC-200自动化装配线的梯形图
工作日程安排:
第1周(2012.7.10——2012.7.17):
下达毕业设计任务书,分组明确设计课题,收集参考资料。
第2周(2012.7.18——2012.7.25):
编制设计方案。
第2~3周(2012.7.25——2012.8.2):
方案设计。
第4~5周(2012.8.3——2012.8.17):
实施设计任务。
第6~7周(2012.8.18——2012.9.1):
整理并撰写毕业设计说明书,完成初稿工作。
第8周(2012.9.2——2012.9.9):
修改设计说明书,完成定稿工作。
第8周(2012.9.10——2012.9.17):
交毕业设计,经过审查后准备答辩。
第10周(2012.9.18——2012.9.25):
毕业设计(论文)审阅评分并进行答辩。
第12周(2012.9.26——2012.11.15):
将毕业设计归档、清点、装订、装袋后上交归档。
设计(论文)要求:
1、根据所选的课题,要求学生独立完成设计工作,训练学生运用所学专业知识解决工程实际问题的能力。
2、要求学生在通读教材、理解和掌握所学基础知识和基本方法的基础上,查阅相关参考书,吃透每一个知识点,结合内容进行实例分析。
3、要求学生对基本概念要做到深刻理解,对基本原理要弄清弄懂,对基本方法要熟练掌握,通过工程知识和工程技能的综合训练,以达到提高分析问题、解决问题的能力。
4、通过毕业设计,提高学生科研和实际技能水平,提高识图、制图、查阅技术手册,正确运算、文字表达能力和组织管理的能力。
5、培养学生独立工作的能力,进一步巩固和扩展专业知识,提高自学能力和工作适应能力。
6、培养学生严谨求实,理论联系实际的工作作风和严肃认真的科学态度。
学生开始执行任务书日期:
2012年7月10日指导教师签名:
年月日
学生送交毕业设计(论文)日期:
2012年11月15日教研室主任签名:
年月日
学生签名:
年月日
摘要及关键词
摘要:
本系统完成一个工件的加工、组装、分拣工作,模拟一个生产流水线的生产过程。
设计以供料、加工、装配、输送、分拣等工作单元作为自动生产线的整体设计,构成一个典型的自动生产线的机械平台,系统各机构的采用了气动驱动、变频器驱动和伺服电机位置控制等技术。
系统的控制方式采用每一工作单元由一台PLC承担其控制任务,各PLC之间通过RS485串行通讯实现互连的分布式控制方式。
所以,本设计综合应用了多种技术知识,如气动控制技术、机械技术(机械传动、机械连接等)、传感器应用技术、PLC控制和组网、伺服电机位置控制和变频器技术等。
关键词:
网络,组态,自动化,PLC,装配线,伺服
引言
现代化的自动化生产设备(自动生产线)的最大特点是它的综合性和系统性,在这里,机械技术、微电子技术、电工电子技术、传感测试技术、接口技术、信息变换技术、网络通信技术等多种技术有机地结合,并综合应用到生产设备中;而系统性指的是,生产线的传感检测、传输与处理、控制、执行与驱动等机构在微处理单元的控制下协调有序地工作,有机地融合在一起。
可编程控制器(PLC)以其高抗干扰能力、高可靠性、高性能价格比且编程简单而广泛地应用在现代化的自动生产设备中,担负着生产线的大脑--微处理单元的角色。
本系统模拟一个生产流水线的生产过程,完成一个工件的加工、组装、分拣工作。
首先由供料站提供原料,运输站将其送至加工站加工,然后送至装配站进行安装,最后由分拣站进行分拣。
整个过程要充分考虑生产过程中所出现的情况,对各种生产要求进行处理,系统分成五个操作站:
供料站、加工站、装配站、运输站、分拣站。
整个系统基于RS485串行通信的N:
N网络,使PLC、变频器、伺服电机等组成一个自动化控制系统,是各种电气控制的综合应用。
第一章自动化装配零件线系统思路和概述
一、系统设计思路
本系统的设计主要是依靠PLC作为核心的控制元件,通过PLC发送脉控制伺服电机也就是机械手的精确移动,通过PLC的输出控制电磁阀工作。
根据生产线的实际需要以及系统的灵活性,本系统设又分为五个单元,分别是供料单元,加工单元,装配单元,分拣单元,输送单元。
由于自动化装配生产线的基本特性,是将工件分别输送到各个单元,进行加工,组装和分拣。
因此采用西门子S7-200系列PLC,并以PPI协议的通信方式,连接到每个工作站,组成一个工业控制网络。
如图1-1所示。
图1-1自动化装配生产线PPI网络
以输送站为主站,把供料站提供的工件分别输送到加工站、装配站、分拣站。
输送站通过PPI网络,读出每一个站的工作完成信号,然后取出工件输送到下一个工作站。
二、系统各个单元功能概述
各工作单元在实训台上的分布如图1-2的俯视图所示。
图1-2各工作单元在实训台上的俯视图
1.供料单元的基本功能:
供料单元是自动化装配生产线系统的起始单元,在整个系统中,起着向系统中的其他单元提供原料的作用。
具体的功能是:
按照需要将放置在料仓中待加工工件(原料)自动地推出到物料台上,以便输送单元的机械手将其抓取,输送到其他单元上。
2.加工单元的基本功能:
把该单元物料台上的工件(工件由输送单元的抓取机械手装置送来)送到冲压机构下面,完成一次冲压加工动作,然后再送回到物料台上,待输送单元的抓取机械手装置取出。
3.装配单元的基本功能:
完成将该单元料仓内的黑色或白色小圆柱工件嵌入到已加工的工件中的装配过程。
4.分拣单元的基本功能:
完成将上一单元送来的已加工、装配的工件进行分拣,使不同颜色的工件从不同的料槽分流的功能。
5.输送单元的基本功能:
该单元通过直线运动传动机构驱动抓取机械手装置到指定单元的物料台上精确定位,并在该物料台上抓取工件,把抓取到的工件输送到指定地点然后放下,实现传送工件的功能。
第二章供料单元的设计
一、供料单元的基本功能
供料单元是自动化装配生产线系统的起始单元,在整个系统中,起着向系统中的其他单元提供原料的作用。
具体的功能是:
按照需要将放置在料仓中待加工工件(原料)自动地推出到物料台上,以便输送单元的机械手将其抓取,输送到其他单元上。
如图2-1所示为供料单元实物的全貌。
图2-1供料单元实物的全貌
二、供料单元结构及工作原理
供料单元的主要结构组成为:
工件装料管,工件推出装置,支撑架,阀组,端子排组件,PLC,急停按钮和启动/停止按钮,走线槽、底板等。
如图2-1所示。
其中,管形料仓和工件推出装置用于储存工件原料,在需要时将料仓中最下层的工件推出到出料台上。
它主要由管形料仓、推料气缸、顶料气缸、磁感应接近开关、漫射式光电传感器组成。
该部分的工作原理是:
工件垂直叠放在料仓中,推料缸处于料仓的底层并且其活塞杆可从料仓的底部通过。
当活塞杆在退回位置时,它与最下层工件处于同一水平位置,而夹紧气缸则与次下层工件处于同一水平位置。
在需要将工件推出到物料台上时,首先使夹紧气缸的活塞杆推出,压住次下层工件;然后使推料气缸活塞杆推出,从而把最下层工件推到物料台上。
在推料气缸返回并从料仓底部抽出后,再使夹紧气缸返回,松开次下层工件。
这样,料仓中的工件在重力的作用下,就自动向下移动一个工件,为下一次推出工件做好准备。
在底座和管形料仓第4层工件位置,分别安装一个漫射式光电开关。
它们的功能是检测料仓中有无储料或储料是否足够。
若该部分机构内没有工件,则处于底层和第4层位置的两个漫射式光电接近开关均处于常态;若仅在底层起有3个工件,则底层处光电接近开关动作而第4层处光电接近开关常态,表明工件已经快用完了。
这样,料仓中有无储料或储料是否足够,就可用这两个光电接近开关的信号状态反映出来。
推料缸把工件推出到出料台上。
出料台面开有小孔,出料台下面设有一个园柱形漫射式光电接近开关,工作时向上发出光线,从而透过小孔检测是否有工件存在,以便向系统提供本单元出料台有无工件的信号。
在输送单元的控制程序中,就可以利用该信号状态来判断是否需要驱动机械手装置来抓取此工件。
三、供料单元气动控制回路
气动控制回路是本工作单元的执行机构,该执行机构的控制逻辑控制功能是由PLC实现的。
气动控制回路的工作原理如图2-2所示。
图中1A和2A分别为推料气缸和顶料气缸。
1B1和1B2为安装在推料缸的两个极限工作位置的磁感应接近开关,2B1和2B2为安装在推料缸的两个极限工作位置的磁感应接近开关。
1Y1和2Y1分别为控制推料缸和顶料缸的电磁阀的电磁控制端。
通常,这两个气缸的初始位置均设定在缩回状态。
图2-2供料单元气动控制回路工作原理图
四、供料单元的PLC控制系统
1.本地控制
各工作单元作为独立设备运行,但在供料单元中,主令信号输入点被限制为1个,如果需要有启动和停止2种主令信号,只能由软件编程实现。
图2-3是软件实现用一个按钮产生启动/停止信号的一个方法。
图2-3用一个按钮产生启动/停止信号程序
2.网络控制
采用RS485串行通信实现的网络控制方案,系统的主令信号均从连接到输送站PLC(主站)的按钮/指示灯模块发出,经输送站PLC程序处理后,把控制要求存储到其发送缓冲区,通过调用NET_EXE子程序,向各从站发送控制要求,以实现各站的复位、启动、停止等等操作。
供料、加工、装配、分拣各从站单元在运行过程中的状态信号,应存储到该单元PLC规划好的数据缓冲区,等待主站单元的读取而回馈到系统,以实现整个系统的协调运行。
程序应包括两部分,一是如何响应系统的启动、停止指令和状态信息的返回,二是送料过程的控制。
可以编写实现这二个功能的子程序,在主程序中调用。
供料控制子程序的步进顺序流程则如下图2-4所示。
图中,初始步S0.0在主程序中,当系统准备就绪且接收到启动脉冲时被置位。
图2-4 供料控制子程序流程图
(1)主程序如图2-5所示:
图2-5主程序梯形图
(2)启动/停止子程序如图2-6所示:
图2-6启动/停止子程序梯形图
(3)送料子程序如图2-7所示
图2-7送料子程序梯形图
4.根据工作单元装置的工作要求,供料单元PLC选用S7-224AC/DC/RLY主单元,共14点输入和10点继电器输出。
PLC的I/O信号分配及接线原理图则见图2-8。
图2-8供料单元PLC的I/O接线
第三章加工单元的设计
一、加工单元的基本功能
加工单元的功能是完成把待加工工件从物料台移送到加工区域冲压气缸的正下方;完成对工件的冲压加工,然后把加工好的工件重新送回物料台的过程。
如图3-1所示为加工单元实物的全貌。
图3-1加工单元实物的全貌
二、加工单元气动控制回路
气动控制回路的工作原理如图3-2所示。
1B1和1B2为安装在冲压气缸的两个极限工作位置的磁感应接近开关,2B1和2B2为安装在加工台伸缩气缸的两个极限工作位置的磁感应接近开关,3B1为安装在手爪气缸工作位置的磁感应接近开关。
1Y1、2Y1和3Y1分别为控制冲压气缸、加工台伸缩气缸和手爪气缸的电磁阀的电磁控制端。
图3-2加工单元气动控制回路工作原理图
三、加工单元的PLC控制系统
1、在加工单元中,提供一个启动/停止按钮和一个急停按钮。
与供料单元同样,如果需要有启动和停止2种主令信号,只能由软件编程实现。
本单元的急停按钮是当本单元出现紧急情况下提供的局部急停信号,一旦发生,本单元所有机构应立即停止运行,直到急停解除为止;同时,急停状态信号应回馈到系统,以便协调处理。
2、加工过程也是一个顺序控制,其步进流程图如图3-3所示。
图3-3加工过程的流程图
从流程图可以看到,当一个加工周期结束,只有加工好的工件被取走后,程序才能返回S0.0步,这就避免了重复加工的可能。
主程序如图3-4所示,它只是在每一扫描周期(SM0.0ON)调用2个子程序,一个是启动/停止子程序,其功能是在读取主站发送来的控制命令以及把本站状态信号写到通信数据存储区。
另一个子程序则是完成加工工艺控制功能。
图3-4加工站主程序梯形图
启动/停止子程序如图3-5所示
加工子程序梯形图3-6所示
图3-6加工子程序梯形图
3、加工单元选用S7-224AC/DC/RLY主单元,共14点输入和10点继电器输出。
PLC的信号接线原理图如图3-7所示。
图3-7 加工单元PLC的I/O接线图
第四章装配单元的设计
一、装配单元的基本功能
装配单元是将该生产线中分散的两个物料进行装配的过程。
主要是通过对自身物料仓库的物料按生产需要进行分配,并使用机械手将其插入来自加工单元的物料中心孔的过程。
装配单元总装实物图如4-1。
图4-1装配单元总装实物
装配单元的功能是完成将该单元料仓内的黑色或白色小圆柱工件嵌入到放置在装配料斗的待装配工件中的装配过程。
二、装配单元气动控制回路
装配单元的阀组6个二位五通单电控电磁换向阀组成,这些阀分别对供料,位置变换和装配动作气路进行控制,以改变各自的动作状态。
气动控制回路图如图4-2所示。
图4-2装配单元气动控制回路
三、装配单元的PLC控制系统
装配单元较为复杂,可细分为以下几个部分进行设计:
(一)落料机构的设计
落料机构的工作原理可设计成,和供料单元相似,根据其结构如图4-3所示,设计的工作流程为:
检测到料仓有物料,且出料回转台无物料(延时1.5S)→顶料气缸动作顶料(延时1S)→顶料到位→挡料气缸缩回→缩回到位(延时0.3S)→挡料气缸伸出(延时0.3S)→顶料气缸缩回→缩回到位→检测物料回转台有无物料。
图4-3落料机构工作流程图
(二)回转物料台的设计
在程序上,设计回转物料台的光电传感器1、电传感器2,分别为落料机构和机械手的物料台上有/无物料的检测。
如图4-4所示。
回转物料台的工作过程是:
当光电传感器1检测到料盘中有物料,光电传感器2检测到料盘中无物料(延时1S)→摆动气缸旋转180°。
图4-4廻转物料台的结构
(三)装配机械手的设计
装配机械手是整个装配单元的核心。
当装配机械手正下方的廻转物料台料盘上有小园柱零件,且装配台侧面的光纤传感器检测到装配台上有待装配工件的情况下,机械手从初始状态开始执行装配操作过程。
装配机械手整体外形如图4-5所示。
整体的控制流程为:
检测到装配台有物料→手爪下降抓料→手爪夹紧→手爪上升→手爪上升到位→手爪伸出→手爪伸出到位→手爪下降→手爪下降到位→手爪松开→手爪上升→手爪上升到位→手爪缩回初始位置
图4-5装配机械手的控制流程图
6.在运行中发生“零件不足”报警时,指示灯HL3以1Hz的频率闪烁,HL1和HL2灯常亮;在运行中发生“零件没有”报警时,指示灯HL3以亮1秒,灭0.5秒的方式闪烁,HL2熄灭,HL1常亮。
上述4部分的控制,可分别编写相应的子程序,在主程序中调用。
图4-6是主程序梯形图。
图4-6装配单元主程序梯形图
启动/停止子程序梯形图见图4-7:
图4-7启动/停止子程序梯形
下料控制子程序清单见图4-8
图4-8下料控制子程序
抓料控制子程序清单见图4-9:
图4-9抓料控制子程序
警示灯控制子程序清单见图4-10:
图4-10警示灯控制子程序
装配单元由于使用的I/O点数较多,所以选用的PLC为S7-200-226CN,根据程序中是用到的I/O分配情况,画出如下PLC接线原理图。
如图4-11、4-12:
图4-11装配单元PLC输入口接线原理图
图4-12装配单元PLC输出口接线原理图
第五章分拣单元的设计
一、分拣单元的基本功能
分拣单元是YL-335A中的最末单元,完成对上一单元送来的已加工、装配的工件进行分拣,使不同颜色的工件从不同的料槽分流的功能。
当输送站送来工件放到传送带上并为入料口光电传感器检测到时,即启动变频器,工件开始送入分拣区进行分拣。
如图5-1所示分拣单元实物的全貌。
图5-1分拣单元实物的全貌
二、分拣单元气动控制回路
本单元气动控制回路的工作原理如图5-2所示。
通过传感器的检测,判别工件的种类,在PLC程序中分别实现对1Y1、2Y1和3Y1的控制,从而分别控制3个分拣气缸。
图中1A、2A和3A分别为分拣一气缸、分拣二气缸和分拣三气缸。
1B1、2B1和3B1分别为安装在各分拣气缸的前极限工作位置的磁感应接近开关。
图5-2 分拣单元气动控制回路工作原理图
三、分拣单元变频器的设置
在分拣单元的设计上,首先有设计好传动机构,因此首先要先设置好变频器的参数。
变频器采用的是西门子MM420。
变频器按照表5.1的内容设置好之后,当DIN1=1,DIN2=0,变频器输出25Hz(中速);当DIN1=0,DIN2=1,变频器输出15Hz(低速);当DIN3=1,电动机反转。
表5.1 2段固定频率控制参数表
步骤号
参数号
出厂值
设置值
说明
1
P0003
1
1
设用户访问级为标准级
2
P0004
0
7
命令组为命令和数字I/O
3
P0700
2
2
命令源选择“由端子排输入”
4
P0003
1
2
设用户访问级为扩展级
5
P0701
1
16
DIN1功能设定为固定频率设定值(直接选择+ON)
6
P0702
12
16
DIN2功能设定为固定频率设定值(直接选择+ON)
7
P0703
9
12
DIN3功能设定为接通时反转
8
P0004
0
10
命令组为设定值通道和斜坡函数发生器
9
P1000
2
3
频率给定输入方式设定为固定频率设定值
10
P1001
0
25
固定频率1
11
P1002
5
15
固定频率2
四、分拣单元的程序结构
分拣控制程序采用步进顺控程序:
1.当检测到待分拣工件下料到进料口后,清零HC0当前值,以固定频率启动变频器驱动电机运转。
梯形图如图5-3所示。
图5-3分拣控制子程序初始步梯形图
2.当工件经过安装传感器支架上的光纤探头和电感式传感器时,根据2个传感器动作与否,判别工件的属性,决定程序的流向。
HC0当前值与传感器位置值的比较可采用触点比较指令实现。
完成上述功能的梯形图见图5-4。
3.根据工件属性和分拣任务要求,在相应的推料气缸位置把工件推出。
推料气缸返回后,步进顺控子程序返回初始步。
图5-4在传感器位置判别工件属性的梯形图
根据程序中I/O端口的分配使用情况,画出PLC的I/O接线原理图5-5如下:
图5-5I/O接线原理图
第六章输送单元的设计
一、输送单元的基本功能
输送单元的基本功能:
通过直线运动传动机构驱动抓取机械手装置到指定单元的物料台上精确定位,并在该物料台上抓取工件,把抓取到的工件输送到指定地点然后放下,实现传送工件的功能。
如图6-1输送单元总装实物:
图6-1输送单元总装实物
二、输送单元的结构与工作过程
输送单元工艺功能是:
驱动其抓取机械手装置精确定位到指定单元的物料台,在物料台上抓取工件,把抓取到的工件输送到指定地点然后放下的功能。
输送单元在网络系统中担任着主站角色,它接收来自触摸屏的系统主令信号,读取网络上各从站的状态信息,加以综合后,向各从站发送控制要求,协调整个系统的工作。
抓取机械手装置是一个能实现四自由度运动(即升降、伸缩、气动手指夹紧/松开和沿垂直轴旋转的四维运动)的工作单元,该装置整体安装在直线运动传动组件的滑动溜板上,在传动组件带动下整体作直线往复运动,定位到其他各工作单元的物料台,然后完成抓取和放下工件的功能。
三、输送单元气动控制回路
输送单元的抓取机械手装置上的所有气缸连接的气管沿拖链敷设,插接到电磁阀组上,其气动控制回路如图6-2所示。
图6-2输送单元气动控制回路原理图
四、伺服电机驱动器的使用
(1)设置伺服电机驱动器参数
表2.3伺服电机驱动器参数设置表
序号
参数
设置数值
功能和含义
参数编号
参数名称
1
Pr01
LED初始状态
1
显示电机转速
2
Pr02
控制模式
0
位置控制(相关代码P)
3
Pr04
行程限位禁止输入无效设置
2
当左或右限位动作,则会发生Err38行程限位禁止输入信号出错报警。
设置此参数值必须在控制电源断电重启之后才能修改、写入成功
4
Pr20
惯量比
1678
该值自动调整得到,具体请参AC
5
Pr21
实时自动增益设置
1
实时自动调整为常规模式,运行时负载惯量的变化情况很小
6
Pr22
实时自动增益设置的机械刚性选择
1
次参数值设得越大,响应越快,但过大可能不稳定
7
Pr41
指令脉冲旋转方向设置
1
指令脉冲+指令方向,设置次参数值必须在控制电源断电重启之后才能修改、写入成功
指令脉冲
+
指令方向
8
Pr42
指令脉冲输入方式
3
9
Pr48
指令脉冲分倍频第1分子
1