高速拉伸第1部分钢铁标准网.docx
《高速拉伸第1部分钢铁标准网.docx》由会员分享,可在线阅读,更多相关《高速拉伸第1部分钢铁标准网.docx(41页珍藏版)》请在冰豆网上搜索。
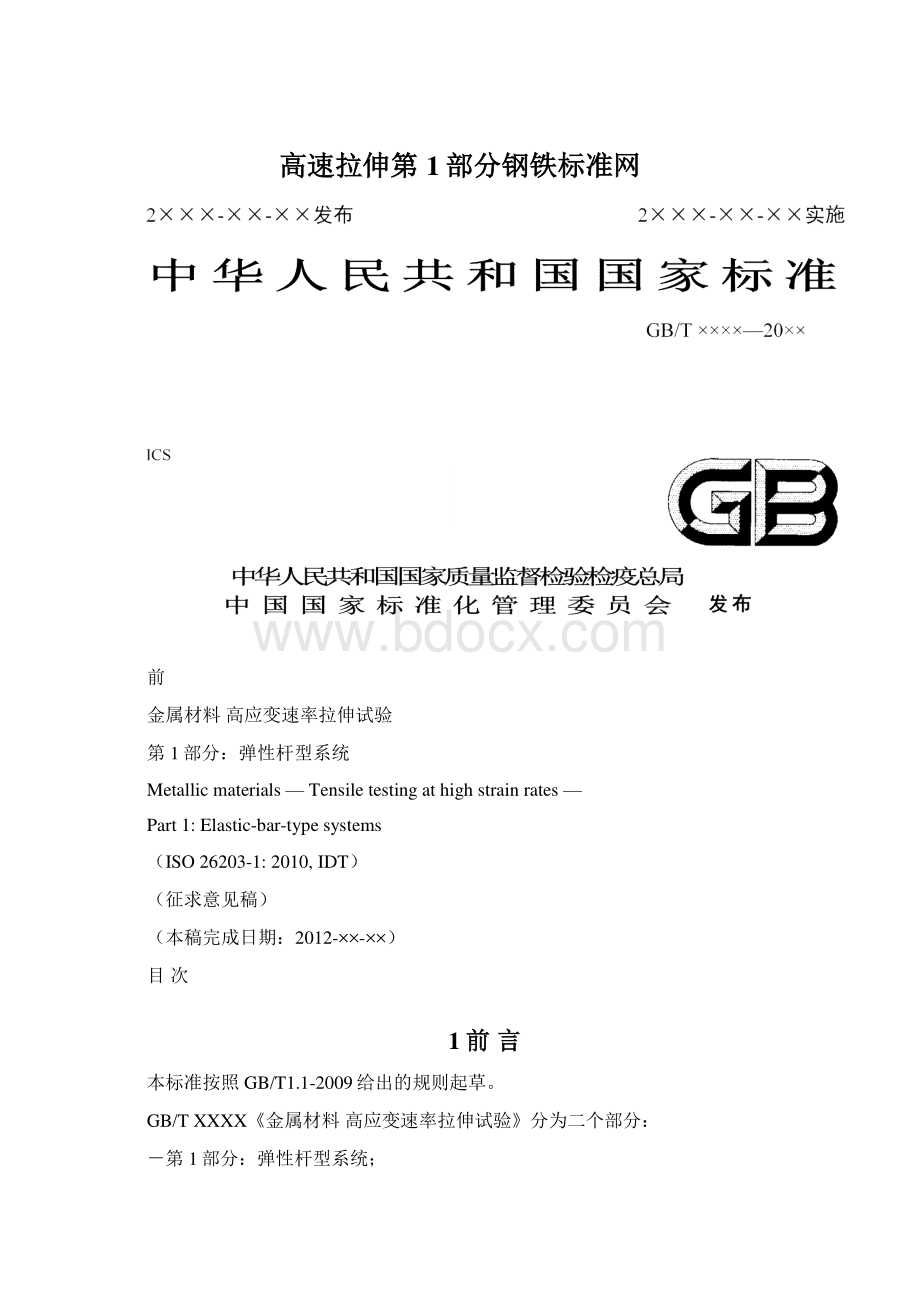
高速拉伸第高速拉伸第1部分钢铁标准网部分钢铁标准网前金属材料高应变速率拉伸试验第1部分:
弹性杆型系统MetallicmaterialsTensiletestingathighstrainratesPart1:
Elastic-bar-typesystems(ISO26203-1:
2010,IDT)(征求意见稿)(本稿完成日期:
2012-)目次1前前言言本标准按照GB/T1.1-2009给出的规则起草。
GB/TXXXX金属材料高应变速率拉伸试验分为二个部分:
第1部分:
弹性杆型系统;第2部分:
液压伺服与其他试验系统。
本部分为GB/T的第1部分。
本部分等同采用国际标准ISO26203-1:
2010金属材料高应变速率拉伸试验第1部分:
弹性杆型系统。
本部分的整体结构、层次划分、编写方法和技术内容与ISO26203-1:
2010相同。
为了便于使用,本部分做了下列编辑性修改:
a)“本国际标准”一词改为“本标准”;b)在规范性引用文件中,本标准直接引用与国际标准相对应的我国国家标准;c)增加了规范性引用文件GB/T16825.1静力单轴试验机的检验第1部分拉力和(或)压力试验机测力系统的检验与校准与国际标准参考文献17对应;d)增加了资料性附录NA“仪器化冲击拉伸法(IIT)示例”;e)用小数点.代替作为小数点的逗号,;f)删除了国际标准的前言;g)在试验报告部分增加了“本标准编号”一项;h)删除了国际标准的参考文献17。
本部分的附录A、附录B、附录C、附录NA均为资料性附录。
本部分由中国钢铁工业协会提出。
本部分由全国钢标准化技术委员会归口。
本部分起草单位:
宝山钢铁股份有限公司、武汉钢铁(集团)公司研究院、上海电气电站设备有限公司、本部分主要起草人:
方健、周冶东、李荣锋、朱月梅、1引引言言金属板材高应变速率拉伸试验对于车辆碰撞可靠性分析而言非常重要。
在碰撞发生时,最大的应变速率经常可达到103s-1,在此情形下材料的强度将显著高于准静态加载时的性能指标。
因此表征材料应变速率敏感性的输入参数是否准确将直接影响到碰撞模拟的可靠程度。
尽管已有多种高应变速率试验方法,对于以下三个问题依然需要有效的解决方法。
第一个问题有关力测定信号的噪声:
试验力通常由测力装置上的测量点探测,而测量装置与试样往往间隔一定的距离。
此外,已通过测量点的弹性波到达测力装置端部时会反射折回。
如果试验时间与应力波通过测量装置的传播时间相当的话,应力应变曲线将因直达波与间接波的叠加而发生严重的振荡。
与此不同的是,在准静态试验中试验时间足够长已至数倍于弹性波往返的时间,因而在测力装置任何部位的力信号已达到饱和与平衡态。
针对上述问题有以下两个截然不同的解决方法:
第一种方法是使用较短的测力装置以利于较快的达到饱和态。
液压伺服型系统经常采用这一方法。
第二种方法是使用较长的测力装置,当力反射波到达测量点时试验已经完成。
弹性杆型系统即基于这种方法。
第二个问题是针对位移或试样伸长需要快速准确的测定方法:
常规引伸计因存在加大的惯性效应而不适用。
非接触式测量方法如光学及激光装置可应用于高应变速率拉伸。
在设计得当的设备中利用弹性波传播理论测量位移也是可行的方法,如在本标准中讨论的一些例子。
杆端位移可利用相同的测力数据经简单计算获得,比如在杆的特定位置记录应变随时间的变化过程。
因此,在弹性杆型系统中不需要评估设备的刚度。
最后一个问题是沿试样力分布的不均匀性:
在准静态试验中,推荐使用具有较长平行部位与较大过渡弧的试样以利于标距部位达到均匀的单轴应力状态。
在动态试验中因满足有效试验所需的力平衡条件,试样设计有别于典型的准静态试样。
与准静态试验相比,动态试样通常在其平行于加载轴线方向上的尺寸设计得较小。
弹性杆型系统为解决上述试验问题提供了有效的解决方法,广泛应用于103s-1应变速率区间并能获得准确的应力应变曲线。
国际钢铁协会基于各类实验室间的比对试验发布了“钢板动态拉伸试验推荐方法”。
比对试验结果表明应用弹性杆型系统可获得高质量的数据结果。
本部分总结了弹性杆型系统的发展历程,本标准第2部分将包括采用液压伺服与其他类型试验系统开展高应变速率拉伸试验。
金属材料高应变速率拉伸试验第1部分:
弹性杆型系统11范围范围本部分规定了高应变速率条件下测定金属板材应力应变特征的试验方法。
本部分标准包括弹性杆型系统的使用。
基于实验及数值计算,如碰撞有限元模拟(FEA)表明,处于10-3到103s-1范围内的应变速率与车辆碰撞事故密切相关。
为准确评价车辆耐碰撞性能,在高于10-3s-1应变速率条件下得到金属材料可靠的应力应变特征尤为关键。
本试验方法包括高于102s-1应变速率范围。
1注1:
当应变速率低于10-1s-1时,可应用GB/T16825.1规定的准静态拉伸试验机与GB/T228拉伸试验方法。
2注2:
除本方法考虑的平板类试样外,本部分同样可应用于其他几何尺寸的拉伸试样。
12规范性引用文件规范性引用文件以下引用的文件对本文件的应用是必不可少的。
凡是注日期的引用文件,仅注明日期的版本适用于本文件。
凡是不注日期的引用文件,其最新版本(包括所有修订单)适用于本文件。
GB/T228.1金属材料拉伸试验第1部分:
室温试验方法(GB/T228.1-2010,ISO6892-1:
2009,MOD)GB/T16825.1静力单轴试验机的检验第1部分:
拉力和(或)压力试验机测力系统的检验与校准(GB/T16825.1-2008,ISO7500-1:
2004,IDT)GB/T10623金属材料力学性能试验术语(GB/T10623-2008,ISO23718:
2007,MOD)13试验原理试验原理本部分用来评价金属材料在高应变速率条件下的应力应变特征。
当应变速率高于10s-1时,准静态试验使用的力传感器由于波的多次反射将对力值信号造成严重干扰。
因此需采用特殊的力值测定技术,可通过以下两类不同的方法加以实现:
1一种是在加载方向上加长力测定装置,以实现当弹性波从另一端折返时力值测定已经结束(弹性杆型系统)。
2另一种方法是缩短力值测定装置,即减少力测定装置达到动态平衡所需要的时间以及实现较高的本征频率(液压伺服型系统)。
低应变速率(低于10-1s-1)试验可利用准静态拉伸试验机开展。
然而,当利用此类试验机实施较常规应变速率高的试验时须特别加以关注。
本部分须使用高应变速率试验方法规定的试样。
附录A提供了此类试验的详细程序。
14术语和定义术语和定义GB/T10623规定的以及下列术语和定义适用于本部分。
14.1弹性杆型系统弹性杆型系统在轴线方向上安装有加长的力测定装置的试验系统,可避免由设备端部折回的反射波影响力值的测定。
1注:
“弹性杆型系统”名称源于此类系统通常采用较长的弹性杆作为力测定装置。
15符号及说明符号及说明符号及说明见表1。
表1符号及说明符号单位说明试样a0mm板状试样的原始厚度b0mm板状试样平行长度的原始宽度bgmm试样夹持部分的宽度L0mm标距原始长度(见7.1e)LCmm平行长度Ltotalmm包括平行长度与肩部的试样总长度Lumm断后标距长度rmm肩部半径S0mm2平行长度原始横截面积Sbmm2弹性杆横截面积时间ts时间时间伸长A%断后伸长率断后伸长率注:
对于非比例试样,可对符号A加下标注明初始标距的长度(单位:
mm),例如A20mm表示原始标距长度L0=20mm试样的断后伸长率。
Au%某平均应变速率时的指定伸长率上限位移umm弹性波的位移u1mm原始标距长度一端的位移原始标距长度一端的位移u2mm原始标距长度另一端的位移uB(t)mmt时刻弹性杆一端的位移应变e工程应变es达到平衡前期望的工程应变弹性应变弹性应变B弹性杆端的弹性应变(见附录A)gC部分的弹性应变(见附录B)表1(续上页)符号单位说明应变速率s-1工程应变速率s-1平均工程应变速率力FN力FmN最大力应力RMPa工程应力RmMPa抗拉强度RtMPa规定总延伸强度弹性模量EMPa弹性模量EbMPa杆的弹性模量波速c0mms-1弹性杆中波的传播速度cmms-1试样中弹性波的传播速度速度vA(t)mms-1冲击块的速度(见附录B)vmms-1杆中任一位置的质点速度(见附录C)vimms-1输入质点速度(见附录C)vrmms-1反射质点速度(见附录C)vtmms-1透射质点速度(见附录C)16试验设备试验设备16.1弹性杆弹性杆应用弹性长杆时,试验需在弹性波由试样另一边的杆端位置处折返前完成。
因此,力值的测定可不受反射波的干扰。
单杆(One-Bar)试验机与分离式霍布金森杆(SHB)试验机通常被用来实施此类方法(见附录B与附录C)。
16.2输入装置输入装置开环型加载通常被用做载荷输入的方法。
加载输入的上限约为20ms-1。
对于SHB试验机,可采用撞管或撞杆作为加载输入。
而对于单杆试验机,通常采用锤击的方式。
16.3夹持方式夹持方式恰当的夹持方式(试样与弹性杆的连接方法)直接影响数据的质量(见附录B与附录C)。
SHB与单杆试验机的夹持装置直接装配在弹性杆上。
夹持装置应采用与弹性杆相同的材料与直径以保证应力波在加载传导过程中的阻抗最低。
若采用的材料或尺寸不同时,后续处理应力与应变结果时需采用恰当的方法。
16.4力值测量装置力值测量装置采用适宜的短标距应变片测量力值,如2mm标距,应变片粘贴在与试样直接相连的弹性杆上。
应变片粘贴的位置需避免顶端效应的影响。
为确保测量到一维弹性波,应变片粘贴处距离杆的末端需至少5倍于杆的直径(见附录B与附录C)。
2注:
本方法测量的应变速率通常高于102s-1。
由于需采用数十米长的撞杆来实现低于102s-1的应变速率,因而不具备实际可操作性。
为确保应力应变曲线的有效性,弹性杆的平直性非常重要。
为实现这一目标,对弹性杆采用恰当的支撑与导向非常关键。
16.5位移测量装置位移测量装置拉伸试验中的应变通常采用标距部分两点相对位移的比值来表示,如试样的初始与结束时的标距长度。
在准静态试验中,一般采用在试样标距部分加装引伸计的方法可获得准确的应变结果。
然而在高应变速率试验中,由于引伸计的惯性效应影响而无法采用这种方法,此时,应采用非接触型装置或弹性杆上的应变片来测量位移或试样伸长。
6.5.1至6.5.3说明了在弹性杆型系统中可用于测量位移的装置。
使用这些装置时,建议应变速率条件达到103s-1左右,且位移测量需在试验过程中全程记录。
这些装置可组合使用,例如,当组合使用6.5.1与6.5.3装置时,初始标距长度(L0)一端的位移可使用非接触型位移计(6.5.1)测量,而另一端可使用粘贴在杆表面上的应变片测量(6.5.3)。
非接触型位移计非接触型位移计使用激光、光学或类似的装置测量初始标距长度(L0)一端的位移。
使用两个6.5.1类型装置或一个6.5.1与一个6.5.3类型装置时,可测量图1中Ltotal(第7章A型试样)随时间的变化及计算相应的伸长。
非接触式引伸计非接触式引伸计使用高速摄像机,多普勒或激光引伸计以及其他非接触系统可测量图2中LC(第7章B型试样)的变化。
应变片应变片应使用式
(1)并基于粘贴在弹性杆上的应变片所测量的应变过程记录计算得到弹性杆末端随时间的位移变化。
(1)式中,uB(t)弹性杆末端在某时刻t的位移;B弹性杆末端的弹性应变(见附录B);c0弹性杆中波的传播速度。
16.6数据记录仪数据记录仪使用放大器与数据记录仪,如示波器等,从原始信号中评测应力-应变曲线。
这类仪器应具有足够高的频响性能。
电子测量系统中所有元部件的频响选择需保证仪器记录的数据不应受单独元件的频响性能影响。
典型的频响性能至少要求达到500kHz。
对于数字式数据记录仪来说,测量数据的最小分辨率应优于10位。
17试样试样17.1试样形状、尺寸与制备试样形状、尺寸与制备试样的几何尺寸应满足以下要求。
a)根据最大应变速率的需要确定平行长度。
试样平行长度越短对应的应变速率越高。
为使试样达到力平衡态,在设定的应变速率范围内应使平行长度足够短。
b)为确保能够在103s-1应变速率上实现力平衡,建议试样平行长度小余20mm。
为满足试样平行长度的均匀变形,应使得试样两端的受力同时达到平衡。
由于力以弹性波形式传播,为实现平衡态应至少满足以下不等式:
(2)式中,LC试样的平行长度;c弹性波在试样中的传播速度;eS达到平衡态前期望的工程应变试验时应变速率。
c)试样的宽度应能满足在试验中获得单轴应力,并满足以下条件:
(3)(4)式中:
a0板状试样的初始厚度;b0板状试样平行长度的初始宽度;L0初始标距长度。
d)通常情况下,若试验机能力允许且无其他特殊要求,试样的厚度应保留材料的原始厚度。
e)A型试样(见图1)肩部过渡弧半径应足够小,此时Ltotal可认作初始标距长度(L0)。
B型试样(见图2)肩部过渡弧半径应足够大,此时LC可认作初始标距长度(L0)。
对于A型与B型试样而言,由于计算应变需使用参考标距长度,而在初始标距长度内的轴向应变存在不均匀性,因此根据根据杆位移计算得到的单轴拉伸数据存在不确定性。
为评估应变不均匀性的潜在影响,建议利用两套准静态加载时的真应力-真应变数据评估相符性。
1)对于选定类型的高应变速率拉伸试样,根据杆的位移(即试样上与杆端相连的位置点位移)与Ltotal或LC的比值获得一套应变数据;2)在GB/T228标准规定的常规拉伸试样平行长度中央区域装夹引伸计,得到另一套应变数据。
在试验报告中宜包含针对上述结果的比较,以供潜在用户评估使用本技术规定获得的高应变速率拉伸试验结果。
若两者偏差超出预期,应在试样标距长度内通过局域应变测量技术获得应变结果(如应变片,非接触式引伸计等)。
f)为确保夹持区域的变形可被忽略且无塑性变形,夹持部分的横截面须大于平行长度部分。
通常试样夹持部分与标距长度的厚度相同,因此夹持部分与标距长度部分的宽度比需满足以下关系:
(5)式中,b0板状试样平行长度的初始宽度;bg试样夹持部分的宽度;Rm抗拉强度;Rt规定总延伸强度。
g)试样表面应避免加工冷作、裂纹与其他表面缺陷造成的应力集中。
图例:
b0平行长度的初始宽度bg夹持部分的宽度LC平行长度Ltotal包括平行长度与肩部的总长r肩部过渡弧半径图1A型试样图例:
b0平行长度的初始宽度bg夹持部分的宽度LC平行长度r肩部过渡弧半径图2B型试样17.2典型试样典型试样试样的推荐尺寸见图3与图4所示,其中试样夹持部分与标距部分的宽度比值通常大于2。
根据试验方法或其他试验目的,也可以使用其他类型的试样。
图3与图4中的典型试样可用于实测应变速率高至103s-1的试验,也可用于不同应变速率试验数据的比较。
由于在拉伸试验均匀伸长阶段,试样的尺寸效应对性能影响较小,然而均匀变形结束后,试验测得的拉伸性能结果受试样的尺寸影响,因此建议不同应变速率的试验,包括低应变速率,均使用同一几何形状与尺寸的试样,便于得到一整套试验结果。
单位:
mmb0最大5Ltotal101.5图3A型试样的典型尺寸单位:
mmb0最大5LC10r5.0图4B型试样的典型尺寸18装置的标定装置的标定18.1总则总则应通过对粘贴有应变片的弹性杆施加已知的静态力来标定应变片的输出信号,图B.3给出了一台单杆试验机的标定示例。
当使用SHB试验机时,可根据密度、弹性模量以及弹性杆中的纵波传播速率应用理论公式计算应力与应变数据。
此时,应当在准确测出各物性参数并确保其一致性后方能实施试验。
(详见附录C)18.2位移测量装置位移测量装置采用合适的方法在静态条件下校准位移测量装置。
19试验程序试验程序19.1总则总则采用加载输入装置(6.2),在试样上沿轴向施加高速应变,力测量装置(6.4)可测出在试样上施加的力。
同时,试样上Ltotal、LC或L0的变化可由位移测量装置记录(6.5)。
根据试验应变速率范围确定试样形状、加载输入装置(6.2)、测力装置(6.4)与位移测量装置(6.5)。
除非另有规定,试验一般在室温1035范围内进行,根据需要记录试验时的温度。
对温度要求严格的试验,试验温度应为235。
19.2试样安装试样安装使用夹具时,需保证试样与夹头间良好的连接状态以施加单轴力,当使用弹性杆时也应当确保试样与弹性杆间良好的连接。
选用A型试样时,安装试样应满足两夹头端部的间距为Ltotal且试样标距部分居中(见图C.3)。
19.3施加力施加力根据6.2章的方法施加力。
为获得试验所需的目标应变速率,应在试验前预先确定撞管、撞杆或撞锤的速度。
3注:
有关单杆法撞锤速度与分离式霍布金森杆法撞杆速度的参考指南见B.2与C.2章。
19.4测量与记录测量与记录试验中,6.4规定的力测量装置可测量弹性应变的变化,6.5规定的位移测量装置可测量弹杆与试样连接点间的位移变化,或标距L0端点间位移变化,应记录上述实测数据。
a)工程应变与工程应变速率(e,)采用6.5介绍的位移测量技术并通过下列公式计算得到工程应变(e)与工程应变速率()结果。
(6)(7)式中,u1,u2初始标距长度端点的位移;en+1n+1步长时刻的工程应变;enn步长时刻的工程应变;n与n+1步长时刻间的时间增量。
b)工程应力(R)根据6.4测量力值,并通过以下公式计算工程应力。
(8)式中,R工程应力;F力;S0平行长度的初始横截面积。
c)断后伸长率(A)选用以下合适的公式计算试样断后伸长率。
对于A型试样,(9)式中,A断后伸长率;Lu断后标距的长度;LtotalA型试样初始标距长度。
对于B型试样,(10)式中,Ltotal断后伸长率;Lu断后标距的长度;LCB型试样初始标距长度。
d)平均应变速率()通过1%(0.01)与10%(0.1)应变时刻的均值得到平均应变速率。
(11)式中,平均应变速率(s-1);t11%应变时的时间;t1010%应变时的时间。
若试样断裂应变小于10%,则根据1%应变与测得的断裂应变计算平均应变速率。
通过协商,计算平均应变速率的应变区间上限可由10%更改为其他约定的应变点,如峰值力时刻的应变。
当采用其他约定的伸长率作为应变区间上限时,平均应变速率的符号应如下标记,式中,Au表示计算平均应变速率采用的应变区间上限所对应的试样伸长率。
110试验结果的评价试验结果的评价以下情况将可能对材料性能评价带来影响,此时需重新试验或对试验结果给出恰当的解释说明。
a)断裂位置距离试样中心处未处于标距长度1/4的范围内;b)应力信号发生较大的振荡(见图5);c)试验时平均应变速率与目标应变速率发生显著的偏差,且应变速率初始上升沿未处于约定的应变区间内(例如,约定5%应变区间);d)处于约定应变区间内的,但应变速率超过平均应变速率的30%;e)动态条件下的应力-应变曲线弹性段斜率与期望斜率存在显著差异(不规则斜率,见图5)。
图例1无测量问题的数据2不规则斜率3不规则斜率振荡R工程应力(MPa)e工程应变图5高应变速率试验中常见测量问题示例加载振荡与应力-应变曲线弹性段的不规则斜率是影响高应变速率拉伸试验质量的两大主要问题。
第一个问题与力测量系统有关,即当试验机或加载链上元部件未恰当连接时(如对中性差或弹性杆间的不重合)较易发生载荷振荡现象,此时可通过仔细调节试验机装配、弹性杆系统的支撑与导向部件加以消除。
第二个问题有关应力-应变曲线弹性段的不规则斜率,这是由于试样标距外加载链上的元部件发生变形造成的附加结果。
这在杆型试验系统中不常出现,因为可通过弹性波传播理论计算得到杆末端的实际位移。
然而当夹头与试样间的装配力或夹持力不充分(见图B.2与B.3),或试样边缘(即Ltotal的边缘)与杆端存在显著位置偏离时,则会发生不规则斜率现象。
针对上述情况,需相应调节试验装置。
111试验报告试验报告试验各方可协商在报告中包含以下内容:
a)本国家标准编号;b)材料名称,牌号(如已知);c)试验方法(力测量方法,位移测量方法以及测力传感器型号等);d)试样标识;e)试样形状与尺寸;f)试样的取样位置与方向;g)测得的材料性能与结果,如应力-应变曲线、应变速率、平均应变速率、抗拉强度、最大力伸长率、断后伸长率等。
附录A(资料性附录)准静态拉伸试验方法A.1范围范围附录给出了通过应变控制在10-3s-1至10-1s-1应变速率范围内评价金属材料拉伸性能的试验方法。
A.2加载输入方法与试验机类型加载输入方法与试验机类型用于加载的试验机需符合GB/T16825.1标准的要求,试验双方协商确定试验机级别,通常使用电子式或液压伺服型试验机。
A.3夹持方法夹持方法试验机应当配备与试样匹配的夹具,在整个试验过程中夹具夹持试样时应保证其对中性,除拉伸试验力外夹具不应对试样产生其他轴向力。
A.4力测量方法力测量方法通常使用一个在弹性体上粘贴电阻式应变片所构成的力传感器来测量试验过程中的力值。
A.5位移测量位移测量根据试样形状,测量LO、LC或Ltotal。
通过测量横梁位移,或优先采用在试样上夹装引伸计来测量位移的变化。
当采用测量横梁位移的方法,由于未考虑试验机的柔度性能,试样上测出的应变速率可能低于从横梁位移测得的应变速率,GB/T228-2011附录F给出了相关说明。
4注:
可使用差动转换器类、光学视频类、与应变片等各类型引伸计。
A.6试样试样推荐在高应变速率试验与准静态试验中使用相同构造的试样,经试验双方协商,也可使用其他尺寸的试样。
5注:
在评价汽车碰撞性能时需提供不同应变速率时的材料性能数据,为满足不同应变速率相同应变范围内数据的一致性,优先采用相同的试样。
A.7试验程序试验程序试样安装试样安装选用与试样形状相符的夹具,并确保在整个试验过程中轴向力仅作用于试样上。
拉紧试样拉紧试样基于引伸计的反馈控制,试样以设定的应变速率拉紧变形。
当采用横梁位移法时,应控制横梁位移速度以确保试样平行长度的应变速率符合试验所需的应变速率条件。
如有需要,可设置试验预拉段以确保在达到所需的应变速率时方能拉紧试样。
测量与记录测量与记录试验中记录力与试样位移随时间的变化,并通过下列公式计算应变速率、工程应力与平均应变速率。
a)应变速率()(A.1)式中,en+1n+1步长时的工程应变;enn步长时的工程应变;n与n+1步长间的时间增量。
b)工程应力(R)根据6.4测量力值,并通过以下公式计算工程应力。
(A.2)式中,F力;S0平行长度的初始横截面积。
c)平均工程应变速率()根据9.4d)得到平均工程应变速率。
附录B(资料性附录)单杆法示例B.1单杆法原理单杆法原理单杆法利用一根弹性长杆作为输出杆测量力值,并在弹性波自输出杆末端反射折回前完成力值测量。
利用撞锤直接击打挡块实施动态加载,载荷传递至试样致使其变形破断。
原则上,此类构造的试验装置对于试验持续时间没有特别限制。
原则上,使用单杆法时对于可供实施的应变速率而言并无固定的上限。
然而由于试样本身具有一定的长度,因此单杆法常用的应变速率上限为2103s-13103s-1。
加载后由于受应力波从杆另一端折回至应变片处的影响,单杆法的应变速率下限通常在102s-1,并