高炉气体运动.docx
《高炉气体运动.docx》由会员分享,可在线阅读,更多相关《高炉气体运动.docx(22页珍藏版)》请在冰豆网上搜索。
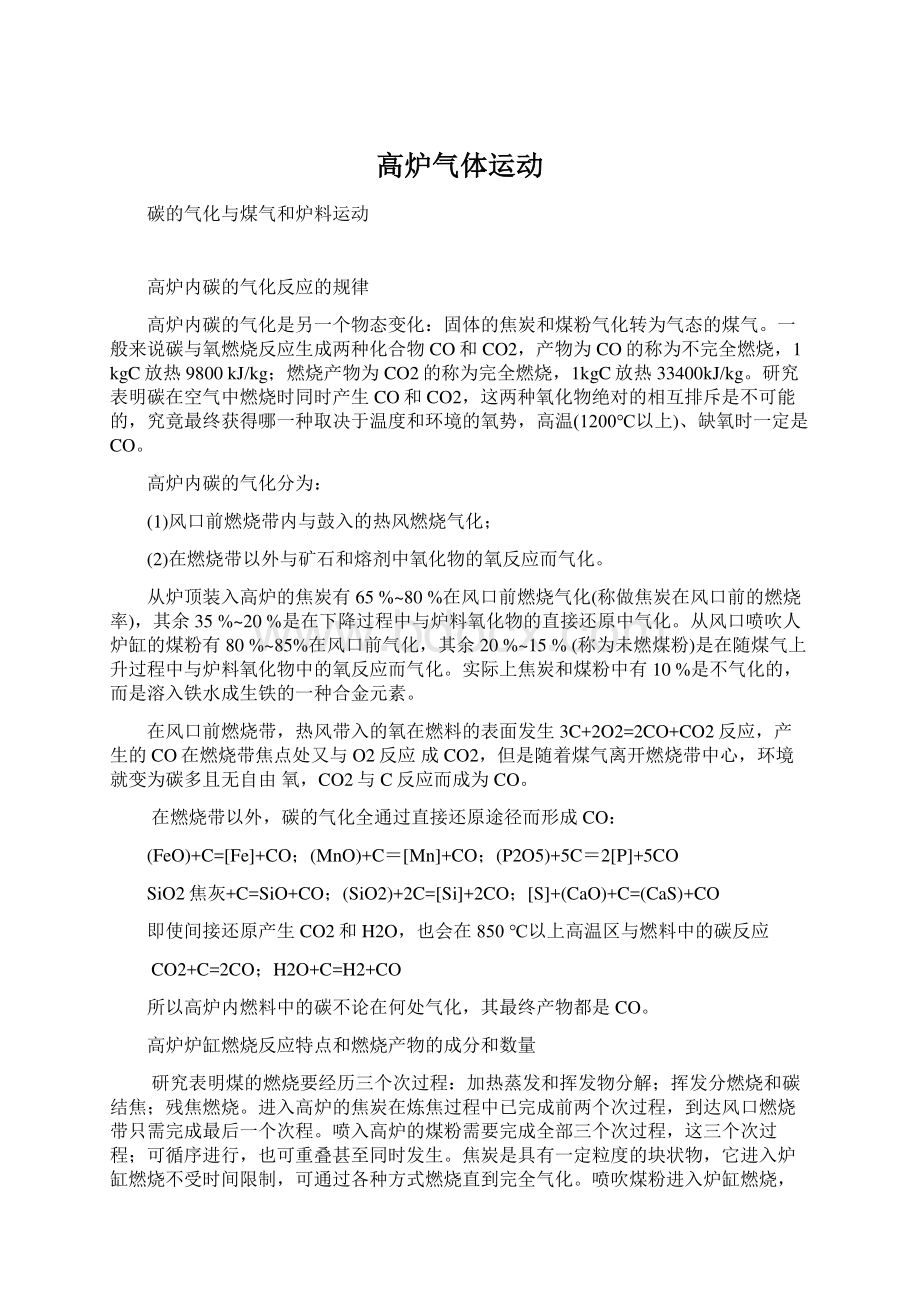
高炉气体运动高炉气体运动碳的气化与煤气和炉料运动高炉内碳的气化反应的规律高炉内碳的气化是另一个物态变化:
固体的焦炭和煤粉气化转为气态的煤气。
一般来说碳与氧燃烧反应生成两种化合物CO和CO2,产物为CO的称为不完全燃烧,1kgC放热9800kJ/kg;燃烧产物为CO2的称为完全燃烧,1kgC放热33400kJ/kg。
研究表明碳在空气中燃烧时同时产生CO和CO2,这两种氧化物绝对的相互排斥是不可能的,究竟最终获得哪一种取决于温度和环境的氧势,高温(1200以上)、缺氧时一定是CO。
高炉内碳的气化分为:
(1)风口前燃烧带内与鼓入的热风燃烧气化;
(2)在燃烧带以外与矿石和熔剂中氧化物的氧反应而气化。
从炉顶装入高炉的焦炭有65%80%在风口前燃烧气化(称做焦炭在风口前的燃烧率),其余35%20%是在下降过程中与炉料氧化物的直接还原中气化。
从风口喷吹人炉缸的煤粉有80%85%在风口前气化,其余20%15%(称为未燃煤粉)是在随煤气上升过程中与炉料氧化物中的氧反应而气化。
实际上焦炭和煤粉中有10%是不气化的,而是溶入铁水成生铁的一种合金元素。
在风口前燃烧带,热风带入的氧在燃料的表面发生3C+2O2=2CO+CO2反应,产生的CO在燃烧带焦点处又与O2反应成CO2,但是随着煤气离开燃烧带中心,环境就变为碳多且无自由氧,CO2与C反应而成为CO。
在燃烧带以外,碳的气化全通过直接还原途径而形成CO:
(FeO)+C=Fe+CO;(MnO)+CMn+CO;(P2O5)+5C2P+5COSiO2焦灰+C=SiO+CO;(SiO2)+2C=Si+2CO;S+(CaO)+C=(CaS)+CO即使间接还原产生CO2和H2O,也会在850以上高温区与燃料中的碳反应CO2+C=2CO;H2O+C=H2+CO所以高炉内燃料中的碳不论在何处气化,其最终产物都是CO。
高炉炉缸燃烧反应特点和燃烧产物的成分和数量研究表明煤的燃烧要经历三个次过程:
加热蒸发和挥发物分解;挥发分燃烧和碳结焦;残焦燃烧。
进入高炉的焦炭在炼焦过程中已完成前两个次过程,到达风口燃烧带只需完成最后一个次程。
喷入高炉的煤粉需要完成全部三个次过程,这三个次过程;可循序进行,也可重叠甚至同时发生。
焦炭是具有一定粒度的块状物,它进入炉缸燃烧不受时间限制,可通过各种方式燃烧直到完全气化。
喷吹煤粉进入炉缸燃烧,不仅比焦炭燃烧多了两个次过程,而且它是粉状,能随气流流动,它应在炉缸燃烧带内停留的有限时间(0.010.04s)和有限空间(燃烧带长度1.21.4m)内完成,否则将随煤气上升而成为未燃煤粉,过量的未燃煤粉会给高炉生产带来很多麻烦。
所以要采取技术措施加快煤粉的燃烧过程,:
保证煤粉在燃烧带内的燃烧率达到80%85%。
在现代高炉上,炉缸燃烧反应是在燃料作剧烈旋转运动中与氧反应而气化的,完全替代了20世纪50年代前高炉没有强化时的层状燃烧。
在炉缸燃料中碳的燃烧反应的产物是CO,属不完全燃烧,燃烧产物由CO、H2和N2组成。
在已知鼓风中氧含量,湿度后,可用燃烧1kg碳;1m3鼓风或生产1t生铁为基准计算出燃烧带煤气的成分和数量。
只要原始数据正确无误,三种计算所得煤气成分是相同的。
影响炉缸煤气成分的因素有鼓风湿度、鼓风含氧量和喷吹物等。
当鼓风湿度增加时,由于水分在风口前分解成H2和O2,炉缸煤气中的含H2量和CO量增加,N2含量相对下降。
喷吹含H2量较高的喷吹物时,炉缸煤气中含H2量增加,CO和N2相对下降。
当鼓风中的氧浓度增加时(如富氧鼓风),炉缸煤气中的CO浓度增加,N2浓度下降,由于N2浓度下降的幅度较大,煤气中的H2浓度相对增加。
前两种情况下炉缸煤气量增加,后一种情况下煤气量下降。
炉缸燃烧反应在高炉冶炼过程中的作用炉缸燃烧反应在高炉冶炼过程中的作用如下:
(1)焦炭在风口前燃烧放出的热量,是高炉冶炼过程中的主要热量来源。
高炉冶炼所需要的热量,包括炉料的预热、水分蒸发和分解、碳酸盐的分解、直接还原吸热、渣铁的熔化和过热、炉体散热和煤气带走的热量等,绝大部分由风口前燃烧焦炭供给。
(2)炉缸燃烧反应的结果产生了还原性气体CO,为炉身中上部固体炉料的间接还原提供了还原剂,并在上升过程中将热量带到上部起传热介质的作用。
(3)由于炉缸燃烧反应过程中固体焦炭不断变为气体离开高炉,为炉料的下降提供了40%左右的自由空间,保证炉料的不断下降。
(4)风口前焦炭的燃烧状态影响煤气流的初始分布,从而影响整个炉内的煤气流分布和高炉顺行。
(5)炉缸燃烧反应决定炉缸温度水平和分布,从而影响造渣、脱硫和生铁的最终形成过程及炉缸工作的均匀性,也就是说炉缸燃烧反应影响生铁的质量。
由此可见,炉缸燃烧反应在高炉冶炼过程中起着极为重要的作用,正确掌握炉缸燃烧反应的规律,保持良好的炉缸工作状态,是操作高炉和达到高产优质的基本条件。
风口燃烧带和风口回旋区炉缸内燃料燃烧的区域称为燃烧带。
它包括氧化区和还原区。
风口前自由氧存在的区域称为氧化区,自由氧消失到CO2消失的区域称为还原区。
由于燃烧带是高炉内睢一属于氧化气氛的区域,因此亦称氧化带。
在燃烧带中,当O2过剩时,C首先与O2反应生成CO2,只有当O2开始下降时,CO2才与C反应,使CO急剧增加,CO2逐渐消失。
因此,燃烧带的尺寸可按CO2消失的位置确定,实践中常以CO2降到1%2%的位置定为燃烧带的界限。
在喷吹含H2燃料时,由于H2O较CO2有更强的扩散能力,燃烧带向中心相应延伸,这种情况下的燃烧带的边界定在H2O的浓度降到1%2%处。
在现代高炉中热风以l00m/s以上的速度通过风口射向炉缸中心,遇到由上方滑落下来的焦炭发生燃烧反应,与此同时焦炭在高速鼓风冲击下做回旋运动,其速度因粒度大小、互相碰撞和进入回旋区时的初速度而在430m/s的大范围内波动。
做高速回旋运动的固、气多相流产生的离心力与作用在此区域外部的料柱有效重力相平衡,从而在每个风口前形成一个疏散而近似梨形的空间,通常称它为风口回旋区。
如图1所示。
图1风口前燃烧带与回旋区示意图从回旋区上方滴流下来的液体(约2040g/s的熔渣和铁液)被高速气流抛向炉子中心与焦粒回旋运动中产生的而又未气化的碎焦形成较致密的回旋区外壳。
回旋区的尺寸略小于燃烧带,回旋区的前端约为燃烧带氧化区的边缘,而燃烧带的还原区则在回旋区外壳之外的焦炭层内。
燃烧带和回旋区的大小及它们在炉缸截面上的分布对高炉内煤气流和温度场的分布有极重要的影响。
因此布置好风口位置以尽量缩小相邻两燃烧带之间的死区、控制好与炉缸直径相适应的燃烧带和回旋区的大小成为高炉操作的重要内容。
影响燃烧带和回旋区大选的因素有:
(1)鼓风参数。
如风量、风温、风压、湿度等。
一般来说能增大鼓风通过风口时的风速,从而增加鼓风动能的,都可使燃烧带和回旋区增大,如加大风量、提高风温;而增加风压却相反,它使同样质量鼓风的体积缩小,降低鼓风动能。
(2)燃料燃烧速度。
碳的气化反应速率高,则气化性物质消耗快,燃烧带缩小。
富氧鼓风,燃料的反应性好,介质温度高等都将缩小燃烧带。
(3)上部炉料和煤气分布情况。
如果燃烧带上方的分布为边缘矿石少、焦炭多的边缘发展型,则燃烧带缩小;若实行的是中心加焦技术,边缘矿石多、而中心焦炭多的中心发展型,则燃烧带向中心延伸。
如果上部炉料负荷重;堆密度大,作用于回旋区上的有效重力大,回旋区会缩小;而焦炭粒度大,落入回旋区的液态物数量多,它们受鼓风冲击而运动时消耗鼓风动能多,鼓风动能衰减快,回旋区和燃烧带都会缩小。
(4)喷吹煤粉。
喷吹煤粉的影响是多方面的:
1)喷吹煤粉在直吹管内部分分解和燃烧,增加了通过风口时的混合气体(鼓风加部分煤粉分解燃烧产生的煤气),动能增加;2)燃烧带形成的煤气中含H2量增加;3)喷吹煤粉后煤粉置换部分焦炭,炉料中负荷增大,堆密度增加;4)低喷煤量时中心气流发展,大喷煤量时未燃煤粉造成中心打不开等。
因此喷吹煤粉对燃烧带和回旋区大小的影响要视具体情况分析确定。
风速、鼓风动能和计算方法高炉炼铁中鼓风通过风口时所达到的速度,它有标准风速和实际风速两种表示方法,单位时间内每个风口鼓入高炉内鼓风所具有的机械能称为鼓风动能。
风速和鼓风动能与冶炼条件有关,它们在一定程度上决定着燃烧带和回旋区的大小,也就决定着初始煤气的分布。
风速是用单位时间内通过一个风口的风量Q(m3/s)除以风口截面积(m2)求得。
用标准状态下的风量Q0算得的风速称标准风速:
m/s而用冶炼实际风温(t风)和热风压力条件下算得的为实际风速:
m/s鼓风动能按下式计算:
kgm/s或kNm/s式中:
Q0鼓风量,m3/s;n风口个数;d风口直径,m;每个风口的截面积,d2/4,m2;t风热风温度,;p热风压力,MPa;P0标准状态时鼓风密度,kg/m3;g重力加速度,9.81m/s2。
风口前理论燃烧温度和炉缸温度风口前焦炭燃烧所能达到的最高温度,即假定风口前焦炭燃烧放出的热量全部用来加热燃烧产物时所能达到的最高温度叫做风口前理论燃烧温度,也叫高炉火焰温度或绝热火焰温度。
用下式汁算:
式中:
t理风口前理论燃烧温度,;Q碳风口前碳燃烧成CO所放出的吨铁热量,kJ/t;Q风鼓风带人的吨铁物理热,kJ/t;Q燃燃料带入的吨铁物理热,kJ/t;Q水鼓风和喷吹物中的吨铁水分分解热,kJ/t;Q喷喷吹物吨铁分解热,kJ/t;cCO,N2CO和N2的热容,kJ/(m3);cH2H2的热容,kJ/(m3);VCO、VN2、VH2炉缸吨铁煤气中CO、N2、H2的量,m3/t。
理论燃烧温度是指燃烧带在理论上能达到的最高温度,生产中一般指燃烧带燃烧焦点的温度。
而炉缸温度一般是指炉缸渣铁的温度,两者有本质上的区别。
理论燃烧温度可达18002400,而炉缸温度一般在1500左右。
影响理论燃烧温度的因素影响理论燃烧温度的因素如下:
(1)鼓风温度。
鼓风温度升高,则鼓风带入的物理热增加,理论燃烧温度升高。
鼓风湿度为1.5%且无富氧无喷吹时,鼓风温度和理论燃烧温度的数值对应如下:
风温/800900100011001200理论燃烧温度/19942013215422372319
(2)鼓风富氧度。
鼓风含氧量提高以后,N2含量减少,此时虽因风量减少而使Q风有所降低。
但由于VN2降低的幅度大,理论燃烧温度显著升高。
风温为1100,鼓风湿度为1.5%,无喷吹时有下列关系:
鼓风含氧量/%2122232425理论燃烧温度/22372267231423602404(3)喷吹燃料。
由于喷吹物分解吸热和VH2比增加,理论燃烧温度降低。
由于各种喷吹燃料的分解热不同:
含H22%24%的天然气分解热为3350kJ/m3,含H211%13%的重油分解热为1675kJ/kg,含H22%4%的无烟煤分解热为1047kg/kg,所以,喷吹天然气降低理论燃烧温度最剧烈,重油次之,无烟煤降低最少。
(4)鼓风湿度。
鼓风湿度的影响与喷吹物相同,由于水分分解吸热,理论燃烧温度降低。
煤气上升过程中量、成分和温度的变化燃烧带内形成的煤气进入炉缸、炉腹及其在上升过程中,由于在高温区内各种形成CO的碳气化反应的发生,使煤气的量和成分都有变化。
主要表现为CO数量和百分比都增大。
由高温区进人中温间接还原区时的煤气,常被称为炉腹煤气,其数量和成分可按以下各式计算:
VCO=VCO燃+2CO2+22.4(1/12WCd+1/44WCO2熔+1/28WCO焦挥)VH2=VH2燃+11.2(WH2有机+WH2挥发)VN2=VN2燃+22.4/28(WN2有机+WN2挥发)炉腹煤气量V腹=VCO+VH2+VN2式中:
VCO燃、VH2燃、VN2燃燃烧带生成的CO、H2、N2量,m3/t;WCd直接还原耗碳,包括Fe、少量元素及脱硫等耗碳,kg/t;CO2熔剂在高温区分解的分数,即熔剂分解出CO2再与C反应的分数,一般在0.5-0.75之间;WCO2熔吨铁消耗熔剂中CO2总量,kg/t;WH2有机、WN2有机吨铁消耗焦炭中有机H2和有机N2的量,kg/t;WCO焦挥、WH2挥发、WN2挥发吨铁消耗焦炭挥发分中CO、H2和N2的量,kg/t。
在间接还原区内,煤气中部分CO和H2参与间接还原而转化为CO2、H2O,易分解熔剂分解出少量CO2、也进入煤气。
由于生产中炉顶煤气无法分析出H2O还,所以无论是取样分析或计算都是干煤气成分,H2还原生成的H2O还不算在炉顶煤气成分中,而单独算出。
另外过去长时间认为炉顶煤气中有CH4,理论上讲高炉内没有生成CH4的条件,相反焦炭和喷吹燃料(特别是天然气90%以上是CH4)带入的CH4在高炉内要分解,现代的气相色谱仪分析炉顶煤气表明炉顶煤气中没有CH4,用奥氏分析仪吸收法分析煤气出现CH4,纯属分析误差所造成。
炉顶煤气的量可按以下各式计算:
VCO2顶=VCO2间+22.4/44(1CO2)WCO2熔+WCO2焦挥VCO顶=VCO+VCO2间VH2顶=VH2+VH2间VN2顶=VN2V顶总=VCO2顶+VCO顶+VH2顶+VN2顶式中VCO2间、VH2间间接还原生成的CO2量、消耗的H2量,m3/t;WCO2焦挥吨铁消耗焦炭挥发分中CO2的量,kg/t。
其余同炉腹煤气计算式。
高炉内煤气量、成分以及煤气温度沿高炉高度的变化示于图2。
图2煤气上升过程中量、成分以及煤气温度沿高炉高度的变化1炉顶煤气量V顶;2风量V风:
3炉缸燃烧带煤气量V燃;4风口中心线;5一煤气温度由于炉缸燃烧带内形成的煤气中CO量是鼓风中氧量(包括热风中的自由氧和湿分中的氧)的1倍,所以在不富氧时V燃/V风1.25,富氧鼓风后此比值增大,增大数值与富氧率相对应。
炉顶煤气量因直接还原、熔剂分解、焦炭挥发分的析出等又比V燃增大,V顶/V风1.4。
煤气温度由于热交换,将热量传给炉料及消耗于各种反应而降低。
影响炉顶煤气成分的因素因冶炼条件的变化而引起炉顶煤气成分(体积分数)的变化,主要指煤气中(CO和CO2数量的变化,其他成分的变化不十分明显。
炉顶煤气中的(CO+CO2)量基本稳定在40%42%之间,下列因素影响其值的波动:
(1)当焦比升高时,单位生铁的炉缸煤气量增加,煤气利用率降低,煤气中的CO升高,CO2降低。
同时,由于入炉风量增加,带入的N2在煤气中的比例增加,(CO+CO2)含量下降;
(2)当炉内铁的直接还原度rd提高时,煤气中的CO增加,CO2下降,同时,由于风口前燃烧的碳量减少,入炉风量降低,带入的N2量下降,(CO+CO2)含量升高;(3)熔剂用量增加时,由于分解产生CO2,煤气中CO2和(CO+CO2)含量增加,N2下降。
(4)矿石氧化度提高时,即矿石中的Fe2O3增加时,间接还原消耗的CO增加,产生同体积的CO2,因此,煤气中的CO2增加,CO下降,(CO+CO2)含量没有变化;(5)鼓风含氧量增加时,由于煤气中的N2的比例下降,CO和CO2升高,(CO+CO2)含量可增大到45。
(6)喷吹燃料时,由于煤气中H2所占的比例增加,N2和(CO+CO2)含量下降。
炉料与煤气的水当量水当量是为了研究高炉热交换过程而引出的概念。
单位时间内通过高炉某一截面的炉料或煤气升高(或降低)1所吸收(或放出)的热量,称为炉料或煤气的水当量。
用炉料流股或煤气流股的质量(或体积)与其平均热容的乘积表示:
=G料c料=G气c气式中:
、炉料和煤气的水当量,kJ/(h);G料、G气炉料和煤气流股的质量或体积流量,kg/h或m3/h;c料、c气炉料和煤气的平均表观热容,既包括物理加热吸收的热量,还包括吸热反应吸收的热量,kJ/(kg)或kJ/(m3)。
高炉冶炼中还用每吨生铁的炉料或煤气升高(或降低)1所吸收(或放出)的热量来表示水当量。
在现代高炉上,水当量沿高炉高度上的变化规律是:
煤气水当量上、下部基本相同(约20002500kJ/(t),这是因为G气上部大,下部小,而ct相反,上部小,下部大,两者乘积基本相同;炉料水当量上部小,下部大(上部18002200kJ/(t),下部50006000kJ/(t),这是由于上部不仅吸热反应少,而且CO间接还原还放热,所以表观c气小,下部则有大量的吸热反应,还需炉渣和生铁熔化耗热,所以表观c气很大。
煤气上升过程中的热交换的规律煤气上升过程中经过三个不同的热交换区(图3),即炉料水当量大于煤气水当量()的下部热交换区、炉料水当量与煤气水当量相同()的中部热交换空区、炉料水当量小于煤气水当量()的上部热交换区。
下部热交换区的特点是,由于此区内发生Fe、Mn、Si、P等元素的直接还原、部分碳酸盐的分解、炉料的熔化和渣铁的过热等大量的吸热反应,煤气降温快和炉料升温慢,炉料与煤气之间的热交换非常激烈。
煤气从离开燃烧带时的温度18002000下降到中部空区950,而炉料从中部空区的950上升到渣铁出炉温度1500,煤气和炉料之间的温度差达到300500。
中部空区,炉料和煤气温度接近,只有2050左右的温差,而且此区内炉料和煤气水当量相等,因此热交换非常缓慢或者基本上不发生热交换过程,属于热交换呆滞区。
空区和下部热交换区的界线是碳酸盐开始大量分解和碳的气化反应(CO2+C=2CO)明显发展的温度线,即9501100的区域。
上部热交换区的特点是,由于此区内发生高级氧化物的间接还原是放热反应,炉料吸热量少,炉料水当量小于煤气水当量:
因此炉料升温快而煤气降温慢,同时,上升煤气遇到刚入炉的冷料,煤气与炉料间有较大温差,所以热交换激烈,炉料由2030常温升高到中部空区950,而煤气温度则从950下降到200300炉顶温度。
炉内煤气和炉料的温度分布如图3所示。
图3高炉内热交换过程示意图a高炉内热交换分区;b大、小高炉内炉料和煤气温度沿炉子高度的变化高炉料柱的散料特性料柱的散料特性如下:
(1)空隙度。
单位体积的炉料内空隙体积所占份额称为炉料的空隙度,可以通过体积测量或炉料的实际密度和堆密度测量得出:
与炉料筛分组成、形状和堆放方式等有关,高炉炉料(焦炭,矿石等)的空隙度在0.350.5之间,它是决定料柱透气性的重要因素之一。
(2)形状参数。
有两个参数说明形状的不同,一个是形状系数(球形度),一个是水力学直径d当,对粒度组成不均匀的料常用比表面积平均直径de作为参数:
式中:
d实、d0分别为实际颗粒和实际颗粒体积相等的球的直径,m;V料层内炉料之间空隙的体积,m3;S料层内炉料的全部表面积,m2;d当水力学直径(也叫当量直径),m;de比表面平均直径,m;料层的空隙度;wi第i级颗粒的质量分数,%;di第i级颗粒的直径,m。
(3)堆角(安息角)。
炉料在自然堆放形成料堆,料堆斜面与水平面形成的角称为自然堆角,在高炉内炉料从装料设备(大料钟、无钟溜槽)上落入炉喉料面,不同于自然堆料,它受到上升煤气流的浮力、炉墙及中心料等影响,堆角比自然堆角要小。
堆角的变化是进行高炉操作上部调节的重要依据。
高炉炉料上述散料特性的实测结果之一列于表1表1高炉炉料的散料特性炉料种类堆角孔隙度比表面平均直径de/mm形状系数透气性指数K/mm自然炉内焦炭364428330.50390.724.0球团矿28320.3612.70.920.48烧结矿323629330.487100.650.59块矿364024330.4130.50.871.57高炉煤气是从炉缸向上运动到达炉顶的过程高炉煤气在风口前燃烧带内形成后,在炉缸与炉顶压力差的推动之下向上运动。
燃烧带的大小决定着煤气流初始分布状况,煤气流穿过料柱向上运动的特点之一就是尽量沿阻力小的途径流动,因此上升过程中,哪部分阻力小,煤气量就多,相反阻力大的地方,煤气量就少。
炉缸煤气是沿着软熔带与滴落带之间的下落焦炭的疏松区向炉子中心区上升。
也有部分穿过软熔带根部与炉墙间的焦炭层向边缘流动。
这初始分布取决于燃烧带的大小以及燃烧带上方两侧炉料的透气性。
燃烧带小、边缘焦炭多、矿石少时,初始煤气向边缘流得多;而中心加焦,边缘矿石多,燃烧带向中心伸展时,初始煤气向中心流得多。
煤气上升穿过滴落带,其中既有透气良好的焦炭,还有向下滴落的液体炉渣和铁,它们的流动互相影响。
向下流动的渣铁占据了部分焦炭的空隙,特别是有部分炉渣滞留在其中(其值约为0.04),使滴落带的下降,影响了煤气流运动,严重时还会出现“液泛”现象。
当煤气流到软熔带的下边界处时,由于软熔带内矿石层的软熔,其空隙极少,煤气主要通过焦炭层(焦窗)而流动,煤气流在这里产生了横向运动,由于软熔带的形状、位置和厚薄的不同,穿过的煤气在方向和数量都有差别,所以软熔带成为高炉煤气的二次分配器。
从煤气流分布来说,倒形比W形的好,因为在倒形时煤气由内圆向外圆流动比较顺畅;而在W形时,既有内圆向外圆的流动,又有外圆向内圆的流动,会产生煤气流的冲突,不利于煤气的分布。
由于高炉块状带料柱是由分层的矿石和焦炭组成,它们的透气阻力差别很大,而且高炉的截面积从下往上逐渐缩小,料面又是按炉料堆角向中心倾斜,煤气在这类不等截面、不等高度和透气阻差别很大的料层间向上运动,不断地改变着方向,实际上在块状带内形成了偏向中心的之字形流动。
到达炉顶煤气流的分布常用炉喉料面以下水平截面上的分布来表示。
常用的是通过煤气中CO2曲线、十字测温的炉喉温度曲线以及红外线热图像仪测定给出料面等温线,分色的温度区带等来判断。
煤气在块状带内运动的阻力损失(p)和对其影响的因素高炉内煤气穿过块状带的运动常被假定为气体沿着彼此平行、有着不规则形状和不稳定截面、互不相通的管束的运动。
这样应用流体力学中气体通过管道的阻力损失一般公式和类似高炉炉料的散料上研究测得的修正阻力系数,得到高炉块状带内阻力损失变化规律的半经验表达式,最常用的有扎沃隆科夫公式:
和厄根公式:
式中:
p块状带内煤气流阻力损失(压差、压强降);H料层高度,m;、煤气的密度,kg/m3;煤气的空炉速度,m/s;煤气的运动黏度,m2/s;炉料的空隙度;g重力加速度,m/s2;d当炉料空隙的当量直径,m;d炉料颗粒的比表面平均直径,m;炉料形状系数。
扎氏认为高炉内块状带的煤气流运动处于不稳定紊流区,即处于层流转变为紊流过渡区;而厄根认为它处于紊流区,这样造成两者表达式有差别。
现在高炉工作者普遍认为现代高炉上块状带内的煤气运动属紊流状态,所以常用厄根公式来表达煤气在块状带内阻力损失变化的规律。
从厄根公式可以看出影响p的因素有煤气的性能(分子上)和炉料的特性(分母上)。
煤气性能主要是它的密度和速度;炉料的特性是其形状系数,炉料颗粒的平均直径和炉料的空隙度。
降低p的措施是增加煤气含H2量(喷吹含H2燃料)以降低煤气的密度和黏度,高压操作缩小炉内煤气体积以降低煤气速度;在不影响还原速度的情况下适当增大炉料的粒度,最重要的是提高炉料的空隙度,这就要限制炉料粒度的上限和筛除粒度小于5mm的粉末。
高炉料柱的透气性高炉料柱的透气性指煤气通过料柱时的阻力大小。
煤气通过料柱时的阻力主要取决于炉料的空隙度s(散料体总体积中空隙所占的比例叫做空隙度),空隙度大,则阻力小,炉料透气性好;空隙度小,则阻力大,炉料透气性坏。
空隙度是反映炉料透气性的主要参数。
气体力学分析表明,空隙度、风量Q与压差p之间有如下关系(可从厄根公式推出):
式中:
Q风量;p料柱全压差;K比例系数;炉料空隙度。
由此可见,炉内Q2/p反映了/(1-)的变化,因Q2/p与3成正比,的任何一点变化都将敏感地反映在Q2/p上,所以,生产中用Q2/p作为高炉透气性指标,称为透气性指数。
料柱透气性在高炉冶炼过程的