年产10万吨合成氨装置精制工段13页word.docx
《年产10万吨合成氨装置精制工段13页word.docx》由会员分享,可在线阅读,更多相关《年产10万吨合成氨装置精制工段13页word.docx(9页珍藏版)》请在冰豆网上搜索。
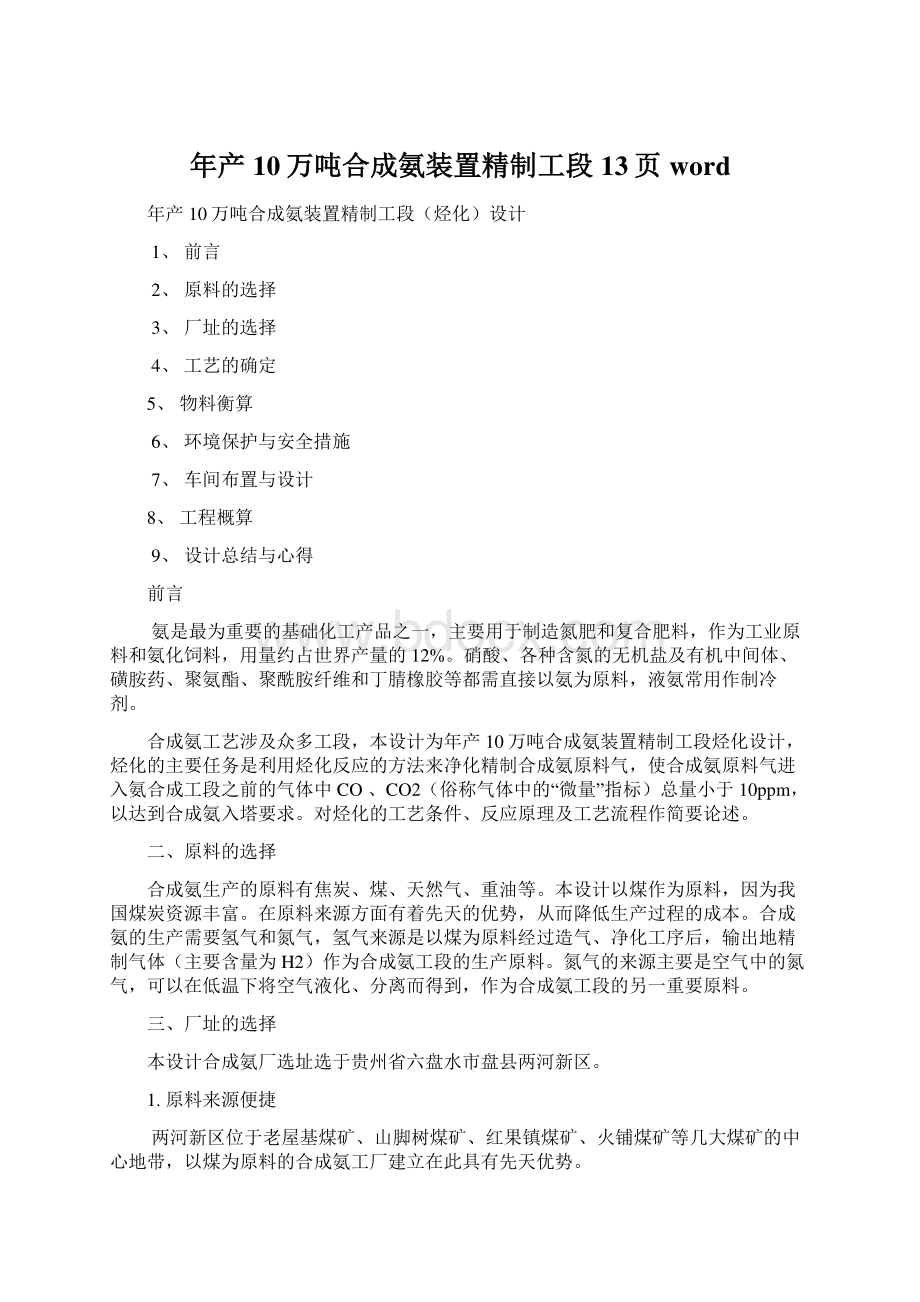
年产年产10万吨合成氨装置精制工段万吨合成氨装置精制工段13页页word年产10万吨合成氨装置精制工段(烃化)设计1、前言2、原料的选择3、厂址的选择4、工艺的确定5、物料衡算6、环境保护与安全措施7、车间布置与设计8、工程概算9、设计总结与心得前言氨是最为重要的基础化工产品之一,主要用于制造氮肥和复合肥料,作为工业原料和氨化饲料,用量约占世界产量的12%。
硝酸、各种含氮的无机盐及有机中间体、磺胺药、聚氨酯、聚酰胺纤维和丁腈橡胶等都需直接以氨为原料,液氨常用作制冷剂。
合成氨工艺涉及众多工段,本设计为年产10万吨合成氨装置精制工段烃化设计,烃化的主要任务是利用烃化反应的方法来净化精制合成氨原料气,使合成氨原料气进入氨合成工段之前的气体中CO、CO2(俗称气体中的“微量”指标)总量小于10ppm,以达到合成氨入塔要求。
对烃化的工艺条件、反应原理及工艺流程作简要论述。
二、原料的选择合成氨生产的原料有焦炭、煤、天然气、重油等。
本设计以煤作为原料,因为我国煤炭资源丰富。
在原料来源方面有着先天的优势,从而降低生产过程的成本。
合成氨的生产需要氢气和氮气,氢气来源是以煤为原料经过造气、净化工序后,输出地精制气体(主要含量为H2)作为合成氨工段的生产原料。
氮气的来源主要是空气中的氮气,可以在低温下将空气液化、分离而得到,作为合成氨工段的另一重要原料。
三、厂址的选择本设计合成氨厂选址选于贵州省六盘水市盘县两河新区。
1.原料来源便捷两河新区位于老屋基煤矿、山脚树煤矿、红果镇煤矿、火铺煤矿等几大煤矿的中心地带,以煤为原料的合成氨工厂建立在此具有先天优势。
2.交通便利新区内沪昆高速公路在沙坡和两河两地出入,即将通车的毕水兴高速公路水盘段与沪昆高速公路在区内海铺呈十字交汇,正在修建的长昆快速铁路冯家庄站紧挨海铺交汇点和沪昆两河出口,320国道贯穿全境。
3.水资源丰富新区邻近的托长江为珠江水系分支,为工业的发展带来甘霖。
4.电力资源丰富两河新区内有22万千伏安和11万千伏安的输变电站各一座,为配合搞好新区的建设,盘县供电局专门成立了两河新区电力服务领导小组,确保正常供电。
5.政策优势随着西部大开发战略的深入推进,国家实施重点支持西部大开发的政策优势,以及贵州省建立工业强省及全面改善投资环境的重大举措,为厂区的建设和未来的发展提供强有力的政策支持。
6.环境因素两河新区地段多为山地,厂区的建立占用的耕地少,且该地段的居民少,对周围居民的生活影响极小。
7.盘县人口多,劳动力资源丰富。
总之,两河园区处于盘北产业园区和盘南产业园区中间,紧靠红果城区,有着不可比拟的区位优势和交通优势、资源优势、技术优势和人才优势。
四、工艺的确定1、基本原理醇烃化工艺即在用甲醇化、烃化(或甲烷化)反应的方法来净化精制合成氨原料气,使合成氨原料气进入氨合成工段之前的气体中CO、CO2(俗称气体中的“微量”指标)总量小于10ppm,并联产甲醇。
它与铜洗工艺或甲烷化流程相比,流程短、精制度高,操作稳定可靠,节约能耗、物耗,经济效益显著。
2、技术特点把醇化和烃化串接起来,作为合成气的净化精制手段,减少了净化过程中有效氢的消耗,同时将传统铜洗工艺中放入大气并对大气造成污染的CO、CO2转化成有用的甲醇或醇醚混合物,变废为宝,改善了产品结构。
3、工艺流程造气出来的半水煤气经气柜后,进行粗脱硫,使硫化氢含量小于0.07,气体加压至0.8MPa,进入变换工段,变换工段出来的气体中二氧化碳含量控制在1.5%-5%,经脱碳后,使二氧化碳含量下降到0.2%,再进行精脱硫,使气体中硫含量降到0.1ppm,进入高压机压缩工段,压缩到5.9-13MPa,醇后气体进行换热,温度为200摄氏度,进入甲醇化反应,从甲醇化出来的气体与新鲜气体换热,再进过水冷器水冷到40摄氏度左右,进入醇化分离器,分离醇后气体中一氧化碳与二氧化碳的含量达到0.1%-0.3%,去高压机加压至与氨合成相等压力,进入醇烃化系统进反应,反应后气体一氧化碳与二氧化钛含量小于等于10ppm,经换热冷却分离水分离后,送入合格精制气。
五、物料衡算1、净化前半水煤气组成每生产一吨氨需半水煤气量为3560标准头(10C,101.3kpa,1kmoi气体的体积为22.4立方米)V1总=3560标准头n1总=VI/22.4=3560/22.4=158.9286kmolni=n1总ximi=niMiwi=Mini/m1总=mi/mi总表1净化前半水煤气组成(MH2O=18.06kg/kmol)组分xi体积分数(%)Mi(kg/kmol)ni(kmol)mi(kg)wi(%)H236.7442.01658.3967117.72773.7798CO33.02228.0052.48141469.479347.1801CO27.03244.0011.1759491.739615.7881N221.50028.0234.1696957.432230.7400CH40.35416.030.56269.01850.2896H2S0.20034.090.317910.83750.3479O21.14832.001.824558.38401.8475典型计算:
m总=mi=3114.6184kgn(H2)=36.744%158.92kmol核算:
wi=100%2、半水煤气脱硫脱硫过程:
半水煤气中只有硫化氢含量发生变化,且要求硫化氢含量小于0.1ppm,该过程视为全脱硫,则:
n2总=n1总-n1(H2S)=158.9286-0.3179=15862107kmol则xi=ni/n2总m2总=mi=m1总-m(H2S)=3103.7812kg典型计算:
以H2为例n2(H2)=n1(H2)=58.3967kmolx(H2)=n2(H2)/n2总=58.3967/158.6107=36.8176%w(H2)=m(H2)/m2总=117.7277/3103.7812=3.793%表2脱硫后混合气体组成组分H2COCO2N2CH4H2SO2xi(%)36.81833.0887.04631.5430.35801.15ni(kmol)58.39652.481411.175934.16960.562601.8245mi(kg)117.72771469.479481.7396957.43229.0185058.384wi(%)3.79347.34515.84330.8470.29101.881核算:
xi=100%wi=100%3、变换气组成转化率为8.2%,若O2全部消耗,则消耗的CO的量为:
nco=52.481488.2%=46.2886kmolCO+H2O=H2+CO2111146.288646.288646.288646.28862H2+O2=2H2O2123.64901.82453.6490nCO=n原COn消耗CO=52.481446.2886=6.1928nH2=n原H2n反应H2+n生成H2=58.39673.6490+46.2886=101.0363kmolnCO2=n原CO2+n生成CO2=11.1759+46.2886=57.4645kmolnN2=n原N2=34.1696kmolnCH4=0.5626kmolnH2S=0kmolnO2=0kmolnH2O=n原O2+n生成O2n反应H2O=174.3749+3.649046.2886=131.7353kmol表3变换气组成组成H2COCO2N2CH4H2SO2H2Oxi(%)30.51301.87017.35210.3180.17000039.7800ni(kmol)101.03636.192857.464534.16960.562600131.7353mi(kg)203.6892173.39842528.438957.43229.0185002373.343wi(%)3.26102.77640.48515.3300.14400038.0020N3总=101.0363+6.1928+57.4645+34.1696+0.5626+0+0+131.7353=331.1611kmolM3总=203.6892+173.3984+2528.438+957.4322+9.01850+0+2373.343=6245.3195kg典型计算:
以H2为例m(H2)=101.03632.016=203.6892kgx(H2)=nH2/n3总=101.0363/331.1611=30.510%w(H2)=m(H2)/m3总=203.6892/6245.3195=3.261%核算:
xi=100%wi=99.998%100%4、变换气脱碳脱碳后CO2含量达到0.2%,其他组分不变,则:
表4变换气脱碳后混合气组成组成H2COCO2N2CH4H2Oxi(%)36.2862.2570.20012.4540.20548.016ni(kmol)101.03636.19280.662334.16960.5626131.7353mi(kg)203.6892173.398429.1412957.432290.1852373.343wi(%)5.4374.6290.777925.5590.240763.356xi%=x3i/100-x3(CO2)-0.2=x3i/(100-17.352+0.2)=x3i/82.848(注:
上式中x3为表三中xi)典型计算:
以H2为例xH2=30.51./82.84836.826%17.352/57.4645=0.2/n(CO2)n(CO2)=57.46450.2/17.352=0.6623kmolm(CO2)=n(CO2)M(CO2)=0.662344=29.1412kgn4总=ni=274.3589kmolm4总=mi=3746.0217kgwi=mi/m4wH2=mH2/m2总=203.6892/3746.0217=5.437核算:
xi=99.46%100%wi=99.9996%100%5、甲醇化甲醇化前混合气体经冷却分离了水,故混合气组成为氢气、二氧化碳、一氧化碳、氮气、甲烷。
甲醇化过程中,有部分水生成,但经冷却分离后,完全去除。
甲醇化后,混合气体中的CO+CO2的含量在0.1%0.3%,以便直接进入醇烃化系统。
本设计取CO+CO2含量为0.3%计算。
甲醇化的主要反应方程式:
CO+2H2=CH3OHCO2+3H2=CH3OH+H2O由于反应中水的生成量较少(CO2含量少,且其转化率很低),故计算时忽略水的生成,若设反应消耗总碳为nmol,则:
2C总+5H22CH3OH25608511-n101.0363-2.5n(608511-n)/(n4总-n4(H2O)-n-2.5n)=0.3%即(608511-n)/(274.3589-131.7353-3.5n)=0.3%故n=6.4954kmol即反应消耗总碳为6.4954kmol所以剩余总碳含量为6.8551-6.4956=0.3597kmol剩余氢含量为101.0363-2.56.4954=84.7978kmol表5进入醇烃化系统的混合气组成组成H2CO+CO2N2CH4xi(%)70.7300.30028.5000.4693ni(kmol)84.79780.359734.16960.5626mi(kg)170.952412.9492957.43229.0185wi(%)14.8611.125783.2290.7840n5总=ni=84.7978+0.3597+34.1696+0.5626=119.8897kmolm5总=mi=170.9524+12.9492+957.4322+9.0185=1150.3523kgxi=mi/n5总wi=mi/m5总核算:
xi=99.999%100%mi=99.9997%100%6、醇烃化甲醇化后混合气中含CO+CO2为0.3%,已达到进入醇烃化系统的含碳量要求。
醇烃化系统是指将CO+CO2转化成醇烃物,使CO+CO2的最终含量小于等于10ppm,以达到净化精制原料气的目的。
醇烃化后的混合气将送往合成系统。
醇烃化的主要反应方程式:
(2n+1)H2+nCOC2H(2n+2)+nH2O2nH2O+nCOC2H2n+nH2O2nH2+nCOCnH(2n+2)O+(n-1)H2O(3n+1)H2+nCOCnH(2n+2)+2nH2O由于反应中的n值难以确定,故近似按氢碳比为2:
1计算,反应结束后,CO+CO2的含量小于等于10ppm,近似为全脱计算,即全部碳参与反应。
由表5可知,参与反应的碳为0.3597kmol由氢碳比可计算得消耗的氢气为0.4194kmol.所以反应后混合气中剩余氢气为84.7978-0.7194=84.0784kmol.又反应生成的水经冷却分离后全部被分离,故混合气中水的含量可忽略。
表6醇烃化后混合气的组成组成H2N2CH4xi(%)70.767028.76000.4735ni(kmol)84.078434.16960.5626mi(kg)169.5021957.43229.0185wi(%)14.922084.28500.7939六、环境保护与安全措施化学工业是我国国民经济的重要的支柱产业之一,化工的发展关系到企业和人民群众的生命财产,而化工生产中的安全和环保又历来在企业经营和政府领导者心中占据“第一要务”的位置。
随着化工企业发展节奏的不断加快、市场竞争的日益激烈以及安全管理体制的调整等因素的影响,化工行业的安全隐患和压力日益增大。
就本设计而言,相对于其他的精制工艺来说,醇烃化工艺更加的环保与安全:
对于甲醇化工艺来说,醇烃化反应中没有甲醇化反应中的剧毒物质产生,在甲烷化反应中,主要以镍为催化剂,在100150时,发生羰基反应:
Ni+4CO=Ni(CO)4(剧毒气体)。
在对系统进行检修及停车之前对甲烷化反应进行降温,需要进入的温度区,将生成羰基镍物质,该物质为神经类毒素蒸汽为人体有很强的毒害作用,故而对检修和开停车的要求都比较高,而醇烃化反应则没有镍元素存在,且催化剂中也没有其他的贵重金属,所以更加的环保且便宜;对于铜洗工艺来说,铜洗工艺的物料消耗大,运行费用高,净化度低及高污染弊病却无法根本改变。
且铜洗工序是合成氨厂的主要事故易发点和气液排放的主要污染源。
又铜洗工序再生气净氨和回收,铜液和稀氨水泄漏、排放始终是生产中的难题,而醇烃化工艺物料消耗少,净化度高,污染少;对于甲烷化工艺来说,甲烷化是一个强放热反应,入炉气相中(COCO2)组分要求十分苛刻,变换气中CO含量小于0.3%,(COCO2)0.7%,这就使变换和脱碳工序生产消耗增高。
甲烷化反应不消耗有效氢,而且生成无用的甲烷,使合成氨系统放空气量增加,生产效率降低。
而醇烃化反应对入炉气体的要求则没有那么高,且产率高。
但化工厂属易燃、易爆区域,常常伴有跑冒滴漏等现象,为火灾、爆炸等事故多发点。
就醇烃化厂区而言,甲醇易燃,且具有刺激性,况且其他醇烃物质都易燃易爆,故应注意以下几点:
1厂区严禁烟火;2定期检修防火防爆设施,确保其能正常使用,及时消除隐患;3建章立制,严肃纪律。
做到以法治厂,以制度管人,使员工在日常工作中有章可遁,有法可依。
4培训教育,持证上岗,做到培训教育经常化、制度化、多样化、专业化、系统化,提高员工的安技素质。
5尊重科学,按规操作。
制订套科学、系统、规范化的安全生产技术标准和操作规程及严格的安全防范措施,加强工艺管理、设备管理和现场管理,严肃工艺纪律和设备的安全操作。
七、车间布置与设计车间布置是本设计工作中很重要的一环,车间布置的好坏直接关系到车间建成后是否符合工艺要求,能否是良好的操作条件,使生产正常、安全的进行,设备的维护、检修的方便可行,以及对建设投资、经济效益等都有着极大的影响希望以上资料对你有所帮助,附励志名3条:
1、积金遗于子孙,子孙未必能守;积书于子孙,子孙未必能读。
不如积阴德于冥冥之中,此乃万世传家之宝训也。
2、积德为产业,强胜于美宅良田。
3、能付出爱心就是福,能消除烦恼就是慧。