螺杆的工艺与工装设计.docx
《螺杆的工艺与工装设计.docx》由会员分享,可在线阅读,更多相关《螺杆的工艺与工装设计.docx(16页珍藏版)》请在冰豆网上搜索。
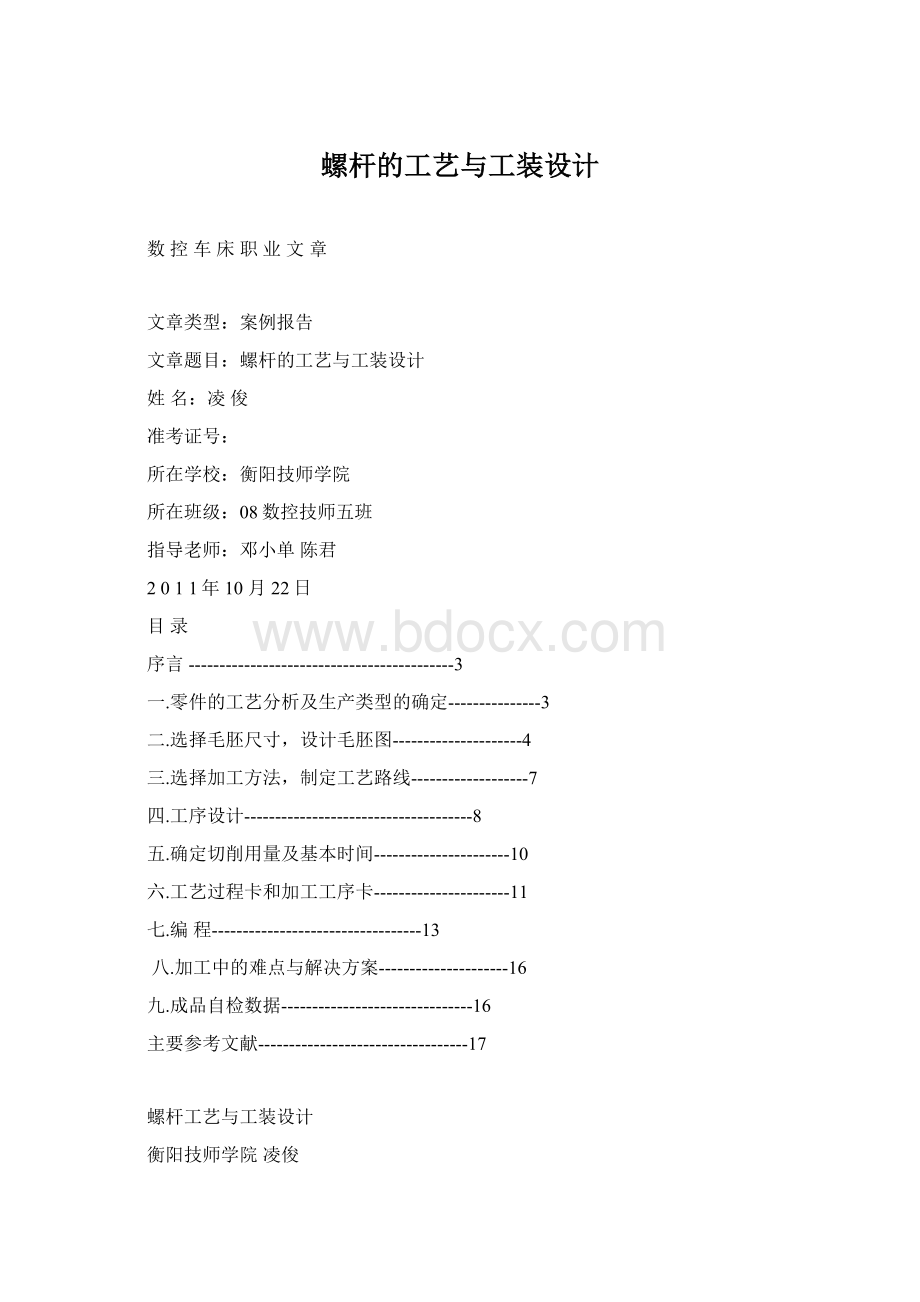
螺杆的工艺与工装设计
数控车床职业文章
文章类型:
案例报告
文章题目:
螺杆的工艺与工装设计
姓名:
凌俊
准考证号:
所在学校:
衡阳技师学院
所在班级:
08数控技师五班
指导老师:
邓小单陈君
2011年10月22日
目录
序言-------------------------------------------3
一.零件的工艺分析及生产类型的确定---------------3
二.选择毛胚尺寸,设计毛胚图---------------------4
三.选择加工方法,制定工艺路线-------------------7
四.工序设计-------------------------------------8
五.确定切削用量及基本时间----------------------10
六.工艺过程卡和加工工序卡----------------------11
七.编程----------------------------------13
八.加工中的难点与解决方案---------------------16
九.成品自检数据-------------------------------16
主要参考文献----------------------------------17
螺杆工艺与工装设计
衡阳技师学院凌俊
摘要:
本设计对螺杆的各个加工难点,生产类型进行分析,
针对零件的结构特点进行毛坯设计,对其工艺过程进行了设计。
为提高生产效率,设计了各个加工工序的方法,对高硬度,高耐磨材料分析,选用最合理的加工刀具以及对形状精度和表面精度的保证方法。
对其他轴类零件的加工有一定的借鉴意义
序言
机械制造技术基础课程设计是在学完了机械制造技术基础和大部分专业课程,并进行了实习的基础上进行的又一个实践性教学环节。
这次设计使我们能综合运用数控加工加工技术基础中的基本理论,并结合生产实习中学到的实践知识,独立地分析和解决了零件机械制造工艺问题,提高了结构设计能力,为今后的毕业设计及未来从事的工作打下了良好的基础。
一.件的工艺分析及生产类型的确定
1.零件的作用
螺杆(见实体图1-1)是机用台虎钳里的螺杆,是一根低速回转的高精度螺杆,它主要的作用是用来传递运动和动力的。
右端的14×14的方形截面与扳手相连;φ18-0.016-0.034与φ12-0.016-0.034两段轴段与固定钳身配合;Tr18×2梯形螺纹与螺母联接。
φ6的销孔与销相配合,限制螺杆的轴向移动。
2.零件的工艺分析
通过对该零件图的重新绘制,知道了得原图的视图正确、完整,尺寸、公差及技术要求齐全。
该零件属于轴类零件,结构简单,整体对尺寸要求较高。
但对圆度,同轴度,平行度的要求较低。
根据这一特点,它的机械加工工艺过程必须分粗、精加工两步进行。
与螺母、固定钳身配合的表面Tr18×2、φ18-0.016-0.034、φ12-0.016-0.034粗糙度要求较高,需用车床精车才可保证。
右端的14×14的方形截面与扳手相连,可用铣削的方法获得。
用两顶尖装夹零件可以以轴中心线为径向基准,使设计基准与工艺基准相重合,实现基准统一。
3.零件的生产类型
依设计题目知:
Q=200台/年,n=1件/台;结合生产实际,备品率和废品率分别取为2%和5%。
代入《机械制造技术基础课程设计指南》的公式(2-1)得该零件的生产纲领
N=200×5000×(1+2%)×(1+5%)=1071000件/年
零件是机用台虎钳里的螺杆,质量为0.34kg,查表2-1可知其属轻型零件,生产类型为大批生产。
二.选择毛坯,确定毛坯尺寸,设计毛坯图
1.选择毛坯
该零件的材料为45#号钢,主要用于与活动钳身里的螺母旋合,随着螺杆的转动,带动活动钳身在钳座上左右移动,所以它主要的作用是用来传递运动动力的。
在工作过程中经常承受载荷,要有良好的力学性能,因此选用锻件,以使金属纤维尽量不被切断,保证零件工作可靠。
由于零件的年产量为214件,属小批生产,故可采用自由锻,虽然毛坯精度低,加工余量大,生产率不高,但不需要专用模具,成本较低。
2.确定机械加工余量,毛坯尺寸及公差。
参见《机械制造技术基础课程设计指南》第五章第一节,钢质模锻件的公差及加工余量按GB/T12362-2003确定。
要确定毛坯的尺寸公差及机械加工余量,应先确定如下各项因素。
(1)锻件公差等级
由该零件的功用和技术要求,确定其锻件公差等级为普通级。
(2)锻件质量
根据零件成品质量0.34kg,估算为mf=0.53kg
(3)锻件形状复杂系数S
S=mf/mn
该铸件为圆形,假设其最大长度为250mm,最大高度为30mm,则由公式
由于0.60介于0.63和0.32之间,故该零件的形状复杂系数S属S2级。
(4)铸件的材质系数M由于该零件的材料45钢,是碳的分子质量小于0.65%的材料,故该铸件的材质系数为M1级。
(5)零件的表面粗糙度由零件图知,3个轴的表面粗糙度为1.6um,其他部分为6.3um,属于大于1.6um的范围。
3.确定机械加工余量
根据铸件质量,零件表面粗糙度、形状复杂系数查表5-9,由此查得单边余量在厚度方向为1.5~2.0mm,水平方向亦为1.5~2.0mm,即铸件各外径的单面余量为1.5~2.0mm,各轴向的单面尺寸余量亦为1.5~2.0mm。
4.确定毛坯尺寸
上面查得的加工余量适用于机械加工表面粗糙度大于等于1.6.小于1.6的表面,余量要适当增大。
分析本零件,除前面3个轴之外其余部分的毛坯尺寸只需加上所查尺寸即可(由于有的表面只需粗加工,这时可取所查数据中的小值(当表面需经粗加工和半精加工时,可取其较大值)。
由于是自由锻,适当加0.5,综上所述,确定毛坯尺寸见表1.
表1螺杆毛坯(锻件)尺寸
零件尺寸
单面加工余量
铸件尺寸
零件尺寸
单面加工余量
铸件尺寸
Φ12
2.0
Φ16
40
2.0
42
T18*2
2.0
Φ22
100
2.0
102
Φ14
2.0
Φ18
7
2.0
7
Φ18
2.0
Φ22
30
2.0
30
Φ22
2.0
Φ26
210
2.0
214
Φ14
2.0
Φ18
5.确定毛坯尺寸公差
毛坯尺寸公差根据铸件质量、材质系数、形状复杂系数从表5-6、表5-7中查得。
本零件的毛坯尺寸允许偏差见表2.
表2螺杆毛坯(铸件)尺寸允许偏差
锻件尺寸
偏差
根据
锻件尺寸
偏差
根据
Φ17
+0.8-0.3
表5-6
40
+1.0-0.4
表5-7
Φ23
+0.9-0.3
137
+1.2-0.6
Φ23
+0.9-0.3
8
±0.6
Φ27
+0.9-0.3
30
+0.8-0.4
Φ19
+0.9-0.3
215
±1.0
设计毛坯图
确定圆角半径
锻件的外圆角半径按表5-12确定。
本锻件大部分的t/H为>1,故均按表中第二行。
为简化起见,本锻件的外圆角均取相同数值,,以台阶高H≤10进行确定,结果为R=2,这样就能保证各表面的加工
7.确定毛坯的热处理方式:
毛坯锻造完成后正火处理。
以消除残余的锻造内应力,并使不均匀的金相组织通过重新结晶而得到细化、均匀的组织,从而改善加工性。
图3螺杆毛坯图
三.选择加工方法,制定工艺路线
1.定位基准的选择
本零件总体是通轴。
以轴的中心线为其设计基准(也是装配基准和测量基准),为避免由于基准不重合而产生的误差,应以轴为定位基准,即遵循“基准重合”的原则。
具体而言,用两顶尖定位粗基准和精基准。
2.零件表面加工方法的选择
本零件的加工面有外圆、槽、削孔、罗纹等,材料为38CrMoAIA。
以公差等级和表面粗糙度要求,参考有关指南资料,其加工方法选择如下。
外圆的加工方法
①.两个端面的尺寸精度要求不高,表面粗糙度只有Ra6.3um,经过粗车即可达到要求(《指南》表5-16)。
②.T18×2的螺纹表面粗糙度需通过粗加工、半精加工、精加工来获得。
③.其余外圆面公差等级为IT6,表面粗糙度为Ra1.6um,需进行粗车、半精车及精磨(《指南》表5-14)。
3.制定工艺路线
本零件按照先加工基准面和先粗后精的加工原则,该零件加工可以按下述工艺路线进行。
工序1:
下料:
铸造Φ22mm×214mm,按铸件毛坯图锻造成形。
工序2:
正火。
消除残余的锻造内应力
工序3:
用车床。
去毛刺。
可以确保装夹稳固和基准的重合。
工序4:
用车床。
平端面保证总长。
打两个B型中心孔。
工序5:
用车床。
粗车右端Φ18的外圆和。
工序6:
用车床。
粗车、半精车Φ12、Φ18、Φ22的外圆和Φ14×7的槽。
工序7:
调质处理
工序8:
用车床。
精车Φ12、Φ18、Φ22的外圆,粗、半精、精车T18×2的螺纹。
工序9:
用铣床铣14×14的正方形柱。
工序10;钳工。
钻Φ6的孔,然后精绞Φ6的孔。
工序11:
去毛刺。
工序12:
检验。
工序13:
入库。
四.工序设计
1.选择加工设备与工艺设备
(1)选择机床根据不同的工序选择机床。
精度要求较好,故选用CK6140型数控卧式车床。
(表5-60)
铣方形柱用立式铣床X51。
(表5-71)
(2)选择夹具由于该零件形状并不复杂,通用夹具可以可靠的夹持并进行加工,所以不需设计专用夹具,用三爪自定心卡盘和一夹一顶装夹就可以啦。
(3)刀具的选择
1)直槽A型中心钻。
(表-91)
2)刀片材质的选择主要依据被加工工件的材料、被加工表面的精度、表面质量要求、切削载荷的大小以及切削过程有无冲击和振动,故加工此零件选择硬质合金刀片。
根据零件的外形结构,加工需要如下刀具:
45°硬质合金端面车刀、90°外圆车刀、外切槽刀、T型外螺纹刀、30°外圆尖刀。
3)铣刀直柄立铣刀。
(表5-99)
2、确定工序尺寸
1)确定圆柱面的工序尺寸
圆柱表面多次加工的工序尺寸只与加工余量有关。
前面已确定各圆柱面的总加工余量(毛坯余量),应将毛坯余量分为各工序加工余量,然后由后往前计算工序尺寸。
中间工序尺寸的公差按加工方法的经济精度确定。
本零件各圆柱表面的工序加工余量、工序尺寸及公差、表面粗糙度见表3。
表3圆柱表面的工序加工余量、工序尺寸及公差、表面粗糙度
加工表面
工序双边余量
工序尺寸
表面粗糙度
粗
半精
精
粗
半精
精
粗
半精
精
右端Φ18外圆
4
—
—
Φ18
—
—
6.3
Φ22台阶
4
—
—
Φ22
—
—
6.3
左端Φ18
2
1.5
0.5
Φ20
Φ18.5
Φ18
6.3
3.2
1.6
左端Φ12
2
1.5
0.5
Φ14
Φ12.5
Φ12
6.3
3.2
1.6
槽Φ14
2
1.5
0.5
Φ16
Φ14.5
Φ14
2)确定轴向工序尺寸
总长在平端面、钻中心孔时就应保证。
粗车第一段台阶(φ12、Φ18外圆长度)时留1mm余量,半精车和精车不留余量。
五.确定切削用量及基本时间
切削用量包括背吃刀量
、进给量
和切削速度
。
粗加工应遵守先背吃刀量(切削深度),再进给量,最后切削速度。
精加工应遵守先切削速度,再进给量,最后背吃刀量(切削深度)的原则,正确选择各个切削用量。
以工序6粗车、半精车Φ12、Φ18外圆面为例确定切削用量及基本时间:
根据《数控车削用量推荐表》,选择合适的切削用量。
(1)车端面时选择主轴转速为500r/min;
(2)粗车外圆时,选取Vc=120m/min,f=0.2mm/r,ap=2mm,粗加工时直径为26mm。
则:
主轴转速:
n=1000Vc/πd
=[(1000×120)/(3.14×26)]r/min=1469r/min
进给速度:
F=f×n=(0.2×1496)mm/min=229.2mm/min
考虑刀具强度、机床刚度等实际情况,选择n=600r/min,F=150mm/min,ap=2mm。
(3)精车外圆时,选取Vc=150m/min,f=0.1mm/r,ap=0.2mm,精加工时取直径为22mm。
则:
主轴转速:
n=1000Vc/πd
=[(1000×150)/(3.14×22)]r/min=2171r/min
进给速度:
F=f×n=0.1×2171mm/min=217.1mm/min
考虑刀具强度、机床刚度等实际情况,选取n=1200r/min,F=100r/min,ap=0.5mm。
(4) 车槽时,选择Vc=70m/min,f=0.1mm/r,车槽时直径为18mm。
则:
主轴转速:
n=1000Vc/πd
=[(1000×70)/(3.14×18)]r/min=1238r/min
进给速度:
F=f×n=(0.1×1238)mm/min=123.8mm/min
考虑刀具强度、机床刚度等实际情况,选取n=400r/min,F=30r/min。
(5)车螺纹时,主轴转速n≤(1200/P)-k,k为安全系数,一般取80。
则:
n≤[(1200/2)-80]/r/min=520r/min
考虑刀具强度、机床刚度等实际加工情况,选取n=400r/min.
(6)计算基本时间
被加工轴的长度l=210mm
粗车=
半精=
(7)确定辅助时间
查《指导》一书相关资料有,变换刀架的时间为3s,变速或变换进给量的时间为1.2s,启动和调节切削液的时间为3s,启动机床的时间为1.2s,取量具并测量的时间为30s,共计
=38.4s。
(8).确定工序的基本时间Tj=
总+
总=205.2s
六.工艺过程卡和加工工序卡
机械加工工艺过程卡
零件名称
产品名称
零件图号
螺杆
螺杆
A3
材料名称及牌号
45#钢
毛坯种类或材料规格
模锻件φ48×405
总工时
49min
工序号
工序名称
工序简要内容
夹具
1.量具
设备型号
工时
1
下料
铸造Φ22mm×214mm,按铸件毛坯图锻造而成
0~250mm游标卡尺
2
热处理
正火消除残余的锻造内应力
3
粗车
去毛刺。
可以确保装夹稳固和基准的重合。
专用夹具
CK6140
4
平端面、钻中心孔
平端面保证总长。
打两个B型中心孔
专用夹具
0~250mm游标卡尺
CK6140
5
粗车
粗车右端Φ18的外圆
专用夹具
0~150mm游标卡尺
CK6140
6
粗车、半精车
粗车、半精车Φ12、Φ18、Φ22的外圆和Φ14×7的槽
专用夹具
25~50mm千分尺
CK6140
7
热处理
调质处理
8
粗车、半精车、精车
精车Φ12、Φ18、Φ22的外圆,粗、半精、精车T18×2的螺纹
专用夹具
25~50mm千分尺
CK6140
9
粗铣、半精铣
铣14×14的正方形柱
通用夹具
0~150mm游标卡尺
X51
10
钳工
钻Φ6的孔,然后精绞Φ6的孔
11
去毛刺
去除全部毛刺
12
检验
按零件图纸要求全面检查
13
入库
车端面
T05
45°端面车刀
0.8
500
30
0
自动
粗车外圆
T01
90°菱形外圆车刀
0.8
600
2
150
0.5
自动
精车 外圆
T02
30°菱形外圆车刀
0.8
1200
0.5
100
0
自动
切槽
T03
外切槽刀
5
400
30
0
自动
车螺纹
T04
90°外螺纹刀
0.8
400
0
自动
七、加工程序和编程
(一)加工以下部分程序
00001;程序头
G97G99M03S750;程序开始
T0101;选择1号刀
G00X28.Z2.;定位
G90X24.Z-30.F0.2;车第一刀外圆
X22.Z-30.;车第刀外圆
X20.Z-30.;车第三刀外圆
X18.Z-30.;车第四刀外圆
G00X100.Z100.;快速退刀
M05;主轴停止
M00;暂停
掉头车端面,保证总长,用一夹一顶装夹。
M03S600;主轴以600r/min的速度正转
T0101;选择1号90°外圆车刀
G00X28.Z2.;将刀具定位在工件外表面
G71U1.R0.5;外轮廓粗车循环
G71P10Q20U0.5W0F0.2;外轮廓粗车循环并指定精车路线N10~N20
N10G00X8.;刀具快速移动
G01Z0.;刀具移动
X12.Z-2.;倒45度2mm倒角
Z-40.;车直径40mm外圆
X18.;车直径18mm圆柱
Z-177.;车直径177mm外圆
X22.;车直径22mm圆柱
N20Z-180.;车直径22mm外圆
G00X100.Z100.;快速退刀
M05;主轴停止
M00;暂停
M03S1000;主轴正转,转速1000r/min
T0202;换2号30°精车外圆刀
G00X28.Z2.;定位
G70P10Q20F0.1;精车循环
G00X100.Z100.;快速退刀
M05;主轴停止
M00;暂停
M03S600;主轴正转,速度600r/min
T0303;换3号槽刀
G00X35.Z-147.;快速定位
G01X18.F0.2;定位
G01X14.F0.06;切槽
G00X30.;快速退刀
X100.Z100.;快速退刀
M05;主轴停止
M00;暂停
MO3S600;程序开始
T0404;4号螺纹刀
G00X19.Z-38.;定位
G92X16.4Z-143.F2.;车螺纹第一刀
X15.2;第二刀
X14.6;第三刀
X14.2;第四刀
X14.;第五刀
X14.;修光第六刀
G00X100.Z100.;快速退刀
M05;主轴停止
M30;程序停止并返回
钻φ6的孔,绞φ6的孔,使其达到要求。
用铣床14×14的方形柱。
八、加工中的难点与解决方案
(1)螺纹切削说明:
螺纹切削应注意在两端设置足够的升速进刀段和降速退刀段,以剔除两端因变速而出现的非标准螺距的螺纹段;
①在螺纹切削过程中,进给速度修调功能和进给暂停功能无效;
②在螺纹加工过程中,不应该使用恒线速控制功能;
③从粗加工到精加工,主轴转速必须保持一致,否则螺距将发生变化。
(2)螺纹加工,当牙型较深,螺距较大时,可分数次进给,常用螺纹切削的进给次数与背吃刀量参考《数控加工与编程》表2-2
(3)外圆车刀刀尖为圆弧,可以提高加工表面粗糙度。
加工时采用这样的车刀车内、外圆和端面时,刀尖圆弧不影响加工尺寸和形状,但转角处的刀尖无法车出,并且在切削锥面或圆弧面时,会造成过切或少切,因此,在加工时要采用刀尖半径补偿来消除误差。
九、成品自检数据
零件的加工质量包括加工精度和表面质量。
加工精度是指实际零件的形状、尺寸和理想零件的形状、尺寸相符合的程度。
其中加工精度有尺寸精度、形状精度和位置精度,尺寸精度是指实际零件的尺寸和理想零件的尺寸相符合的程度,常用游标卡尺、百分尺等来检验。
零件的形状精度是指同一表面的实际形状与理想形状相符合的程度,形状精度通常用直尺、百分表、轮廓测量仪等来检验。
位置精度是指零件点、线、面的实际位置与理想位置相符合的程度,位置精度常用游标卡尺、百分表、直角尺等来检验。
表面质量的指标有表面粗糙度、表面加工硬化的程度、残余应力的性质和大小,表面质量的主要指标是表面粗糙度。
表面粗糙度用表面粗糙度样板测量。
参考文献
1、 詹华西编.《数控加工与编程》.西安电子科技大学出版社,2004年
2、 余英良编.《数控加工编程及操作》.高等教育出版社,2005年
3、 李华编.《机械制造技术》.高等教育出版社,2006年
4、 朱淑萍编.《机械加工工艺及装备》.机械工业出版社,2002年
5、 陈子银,徐鲲鹏编.《数控加工技术》.北京理工大学出版社,2006年
6、 武汉华中数控股份有限公司.《数控车床编程与操作基础》
2011年10月22日
........忽略此处.......