电石生产工艺规程定稿.docx
《电石生产工艺规程定稿.docx》由会员分享,可在线阅读,更多相关《电石生产工艺规程定稿.docx(61页珍藏版)》请在冰豆网上搜索。
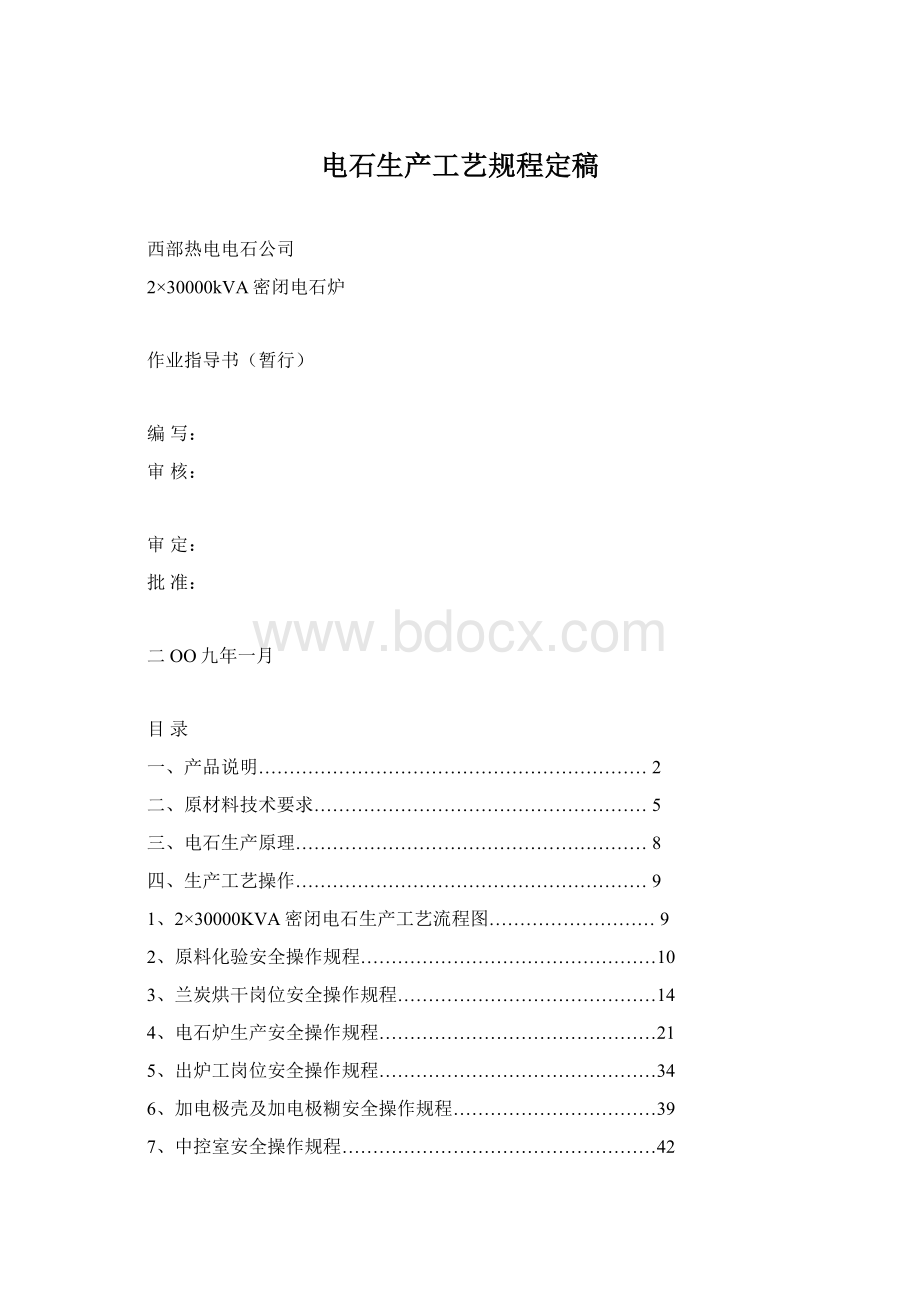
电石生产工艺规程定稿
西部热电电石公司
2×30000kVA密闭电石炉
作业指导书(暂行)
编写:
审核:
审定:
批准:
二OO九年一月
目录
一、产品说明………………………………………………………2
二、原材料技术要求………………………………………………5
三、电石生产原理…………………………………………………8
四、生产工艺操作…………………………………………………9
1、2×30000KVA密闭电石生产工艺流程图………………………9
2、原料化验安全操作规程…………………………………………10
3、兰炭烘干岗位安全操作规程……………………………………14
4、电石炉生产安全操作规程………………………………………21
5、出炉工岗位安全操作规程………………………………………34
6、加电极壳及加电极糊安全操作规程……………………………39
7、中控室安全操作规程……………………………………………42
8、电石冷却岗位安全操作规程……………………………………49
9、天车工岗位安全操作规程………………………………………51
10、循环水岗位安全操作规程……………………………………54
11、炉气净化系统安全操作规程…………………………………58
12、空压制氮岗位安全操作规程…………………………………66
一、产品说明
1、名称:
化学名称碳化钙,俗名电石。
其中含碳化钙约65-85%,其余为杂质。
2、分子式:
CaC2
3、分子量:
64.1C
4、结构式:
Ca
5、基本理化性质C
⑴、外观:
化学纯的碳化钙几乎为无色透明的晶体,极纯的碳化钙结晶为天蓝色大晶体,其色泽颇似淬火钢。
工业碳化钙为不规则块状体,其色泽与纯度有关,有灰色的、棕黄色的、黑色的,碳化钙含量较高时呈紫色,其新断面呈灰色,若暴露在潮湿的空气中则呈灰白色。
⑵、相对密度:
电石的相对密度决定于碳化钙的含量、电石的纯度越高,相对密度越小。
⑶、溶解度:
电石不溶于任何溶剂。
⑷、溶点:
电石的熔点随电石中CaC2含量而改变。
纯CaC2熔点为2300℃,电石中CaC2含量一般在80%左右,其熔点在2000℃左右,CaC2含量为69%时,熔点最低为1750℃,影响电石熔点的因素取决于杂质的量和性质。
如图1所示:
2600℃
2400℃
2200℃
2000℃
1800℃
1600℃
100806040200
CaC2含量(%)
图1电石熔点与其中CaC2含量的关系
⑸、导电性:
其导电性与电石纯度有关,CaC2含量越高,导电性能越好,当CaC2含量下降到70-65%之间时,其导电性能达到最低值,通常比电阻约120000欧姆/厘米3。
CaC2含量为94%时,通常比电阻为450欧姆/厘米3。
电石的导电性能与温度也有关系,温度越高,导电性则越好。
(6)化学性质:
电石的化学性质很活泼,能与多种气体、液体发生反应。
1)电石遇水分解成乙炔和氢氧化钙
CaC2+2H2O=C2H2+Ca(OH)2+126.96(kJ)
该反应是在水过剩的情况下进行的。
当CaC2过剩时,则除上述反应外还有如下反应:
CaC2+Ca(OH)2=2CaO+C2H2
CaC2是一种强脱水剂,用饱和水蒸气分解CaC2时,也和用水分解它时一样。
电石在空气中能吸收环境水份而逐渐分解,放出乙炔气。
2)粉状电石与氮气在加热条件下反应而生成氰氨化钙(石灰氮)CaC2+N2→CaCN2+C
3)氨、氯、氯化氢、硫等在赤热或高温情况下能与电石反应。
磷、砷、乙醇、浓硫酸等也都能与电石反应。
⑺、组成:
工业产品电石中碳化钙含量为65-85%,其余为杂质,杂质多半是制造时所使用的原材料带来的。
如:
CaC2含量80%的电石,其大致组成如下:
CaC2 80%
CaO15%
C1%
SiO2+MgO+Fe2O3+Al2O33.8%
S0.1%
P0.04%
6、用途
⑴、粉状电石与氮气在加热时,反应生成氰氨化钙即石灰氮,石灰氮是一种优良的碱性化学肥料。
石灰氮还可以继续深加工,是生产氰化物的原料。
⑵、电石遇水生成乙炔。
乙炔与氧气混合用于金属的切割焊接,乙炔高温裂解生成乙炔炭黑,可制造干电池。
乙炔为有机合成的重要原料,如:
乙醛、乙酸、乙烯、合成橡胶、合成树脂、合成纤维等均以乙炔为主要原料。
⑶、本身还直接用于钢铁工业的脱硫剂,生产优质钢。
近年来又找到了电石的许多新用途。
总之,电石的用途极为广泛。
7、产品质量标准或特性
⑴、电石
CaC2含量(%)78-82
发气量(l/kg)280以上(20℃)时
乙炔中PH3含量(%)≤0.06-0.03
乙炔中H2S含量(%)≤0.1
⑵、炉气
成份(体积):
预计大致组成:
(%)
CO85¬95
H22.5
CH41¬2
CO22-3
N21¬2
O20.2-0.6
热值(kJ/Nm3):
11302(2700kcal/Nm3)
粉尘含量(g/Nm3):
50-150
炉气体积(Nm3/h):
2300—2600
⑶、炉尘
成份(%)
C10-25
CaO30-50
MgO1-5
堆比重(g/cm3):
150-300
温度(℃):
250-350
粒度:
小于1μm者不超10%
8、包装
1.电石
电石遇水或潮湿空气生成C2H2易燃易爆,因此,电石用干燥的特种包装袋包装或桶包装,出口电石尚需充N2密封。
净重(kg):
50±0.2
二、原材料技术要求
1、石灰
成份(重量%)
CaO≥92
SiO2≤2
MgO≤1.8
R2O3(三氧化物)≤2
P≤0.01
S≤0.04
生、过烧总量(%)<5%
粒度(mm):
30-50
2、焦炭
成份(%)
固定碳≥84
灰份 ≤8
挥发份 ≤8
水份 ≤1(入炉)
粒度(mm)5-25
3、兰炭
成份(%):
固定碳≥84
灰份 ≤8
挥发份 ≤8
水份 ≤1(入炉)
粒度(mm)15-30>85%,10-15≤15%
4、电极糊
成份(%):
固定碳≥80
灰份 ≤5
挥发份 12.5—15.5
软化点(℃):
170℃
水分:
≤1
5、无烟煤:
成份(%):
固定碳≥84
灰份 <7.19(wt%)
挥发份 <7.79(wt%)
水份 ≤1
粒度(mm)(5-25)>85%
(<5)<5%
6、石灰石:
成份(重量%)
CaCO3≥96
SiO2≤1
MgO≤1
粒度(mm):
40-60(其中小于40或大于70不超过10%)
7、烧穿电极:
直径(mm):
φ100-150(暂用)
长度(mm):
1200
连接方式:
螺纹
8、电极壳:
规格:
φ1250×1250
材质:
08F或A3(冷轧钢板)
外壳尺寸(mm)
外壳外径×高度(mm):
φ1250×1250
外壳弓形板厚(mm):
2
长翅片数目(个):
12
长翅片长×宽(mm):
1500×273
短翅片数目(个):
12
短翅片长×宽(mm):
445×230
翅片板厚(mm):
3
翅片加强杆数目(个):
12
翅片加强杆直径(mm):
φ20
连接板数目(个):
12
连接板展开尺寸(mm):
320×30
连接板厚度(mm):
2
制作方式:
缝焊、电焊
连接方式:
电焊
焊条T422φ2-3.2
(全部焊接应可靠、焊缝表面应平滑、无瘤块、烧蚀、翅片处的焊缝无明显凸点)。
制作精度符合零件图要求,电极柱连接不直度≤1‰,不圆度≤1‰。
9、出炉圆钢直径(mm):
φ22
10、测电极用钢棒直径×长度(mm):
φ25×5000
三、电石生产原理
碳化钙生成反应:
工业碳化钙的生成是以生石灰和炭素材料(冶金焦、石油焦、无烟煤等)为原料,在电炉内混合均匀,炉料凭借电弧热和电阻热在1900℃-2200℃的高温下,成熔融状态而制得的。
CaC2的生成反应如下:
CaO+3C=CaC2+CO-465.9(kJ)
碳化钙以液态形成,并溶解过量的石灰和杂质,而CO通过炉料逸散。
这个反应是吸热的,也是可逆反应,根据平衡原理,提高温度和降低CO的压力,在这个反应过程中有利于从左向右进行,所以反应要在高温条件下进行,把反应生成的CO气体及时排出。
但当温度超过2200℃时,有严重的二次反应,碳化钙分解为金属钙和碳:
CaC2→Ca+2C+63.21(KJ)
当生成1吨发气量为300L/kg的电石,根据反应方程式,消耗于反应的电能为:
=1630KWh
1000×0.806×465.9×103/3600
64
式中:
0.806—发气量为300L/kg的电石中CaC2百分含量
3600—1KWh电能完全转化热能为3600KJ/KWh
64—CaC2分子量
四、生产工艺操作
石灰库
4.1、2×30000KVA密闭电石生产工艺流程图
电石炉
环形料仓
环形下料器
皮带运输机
电振给料机
电振给料机
皮带运输机
计量斗
计量斗
炭材粉料仓
白灰粉料仓
皮带运输机
振动筛
白灰贮仓
炭材贮仓
皮带运输机
兰碳振动筛
皮带机
提升机
石灰窑
振动筛
石灰窑排空燃烧
净气CO
炉气净化系统
粗气排空
4.2原料化验安全操作规程
4.2.1、岗位任务
根据原料验收标准验收原料,做好原料保管及场地的卫生清洁工作。
4.2.2、岗位职责
(1)严格按照岗位操作规程、遵守各项纪律和制度,维持正常生产。
(2)及时取样,及时入库。
(3)做好环境卫生工作。
(4)及时、准确填报和保管岗位原始记录。
(5)严格执行原料验收标准和折扣标准,不合格原料不得入厂。
(6)按质检员的化验单验收。
4.2.3、岗位范围
原料入厂至原料库房。
4.2.4、岗位流程简述
(1)初验由原料验料员负责,必须有两人同时在场验收。
(2)初验合格后通知化验员取样进行综合指标的分析。
(3)经化验合格的原料,过磅后由验料员押车开往指定地点,并监督卸车。
(4)验料员随车返回磅房回皮时,由验料员按原料净重及折扣标准计算折扣量,开入厂原料验收入库单,交地磅司磅员打印磅单。
(5)电石原料由验料员执行本流程。
(6)其它原料由使用部门验料员验收,并执行本流程。
4.2.5、原料表面粒度验收规定
(1)白灰:
合格供方供应的白灰,在入厂前必须由验料员对表面粒度进行每车检验,综合指标的化验分析实行抽检,每个合格供方每批次至少抽检一次;
(2)兰炭、焦炭:
合格供方供应的兰炭实行每批检验及化验;
4.2.6、不合格原料管理
不合格原料不得入厂.
4.2.7、原料表面粒度验收规定
(1)生产电石所用原料(白灰、精煤除外),在过磅前须由验料员亲自上车在车厢中心部位用铁锹深挖50~60cm,用目测的方法确定表面粒度合格率,若原料验收不合格供方有异议的,取样品100公斤,按粒度要求用相应筛网过筛,筛上物为合格,筛下物为不合格,然后用不合格总量除以总样品量计算表面粒度合格率,表面粒度兰碳、精煤、精焦合格率≥95%,不折扣,≤95%的,按检测实际百分率与95%的差乘以净重折扣,<85%的直接拒收。
(2)白灰、精煤表面粒度合格率≥95%,检验以卸料过程中的实际情况为准。
(3)原料表面粒度检验始终由2名验料员同时进行,符合标准同意进入综合指标化验分析的,由验料员填写《原料验收入库单》,签字确认后,通知化验员化验其他指标,指标合格的,通知磅房过磅。
每天16时以后的表面粒度验收和《交检单》填写由当班验料员和磅房值班人员同时签字。
(4)特殊时期另有规定的按规定执行。
4.2.8、原料质量验收标准
1、石灰
成份(重量%)
CaO≥92
SiO2≤2
MgO≤1.8
R2O3(三氧化物)≤2
P≤0.01
S≤0.04
生、过烧总量(%)<5%
粒度(mm):
30-50
2、焦炭
成份(%)
固定碳≥84
灰份 ≤8
挥发份 ≤8
水份 ≤1(入炉)
粒度(mm)5-25
3、兰炭
成份(%):
固定碳≥84
灰份 ≤8
挥发份 ≤8
水份 ≤1(入炉)
粒度(mm)15-30>85%,10-15≤15%
4、电极糊
成份(%):
固定碳≥80
灰份 ≤5
挥发份 12.5—15.5
软化点(℃):
170℃
水分:
≤1
5、无烟煤:
成份(%):
固定碳≥84
灰份 <7.19(wt%)
挥发份 <7.79(wt%)
水份 ≤1
粒度(mm)(5-25)>85%
(<5)<5%
6、石灰石:
成份(重量%)
CaCO3≥96
SiO2≤1
MgO≤1
粒度(mm):
40-60(其中小于40或大于70不超过10%)
4.2.9、安全注意事项
穿戴好劳保用品,上车取料时通知司机后与司机一起上车取料,在验料场地不得站在车的后方,注意交通事故。
4.2.10原料化验岗位操作流程
原料
初验
合格
填《交检单》
拒收
不合格
化验
合格
过磅
验料员押车到原料库
持《交检单》
监督卸车
验料员随车回磅房回皮、折算
开磅单
4.3、兰炭烘干岗位安全操作规程
4.3.1、岗位任务
负责把原料场兰炭烘干后送至上料点,控制烘干兰炭水份,保证电石炉用料,做好所用设备的维护保养工作和场地清洁卫生工作。
4.3.2、岗位职责
(1)严格按照岗位操作规程,遵守各项纪律和制度,维持正常生产,解决生产问题。
(2)完成岗位质量和上料任务。
(3)做好本岗位设备的维护保养工作和设备、环境卫生工作。
(4)及时、准确填报和保管岗位原始记录。
(5)按照中控室指令保证沸腾炉及烘干机的正常运行,确保烘干兰炭水份。
出现水分超标情况及时通知中控室。
4.3.3、岗位范围
从兰碳料场指定的兰炭,运至移动皮带输送机经兰炭中转仓通过运输设备运至烘干窑进行烘干。
4.3.4、岗位流程简述
(1)兰炭从料场经抓斗天车送至兰炭中转仓,经电磁振动给料机、皮带输送机运送至湿碳材仓,经电机振动给料机进入烘干机进行烘干。
(2)煤粉通过埋刮板及提升机进入缓冲仓,经圆盘给料机进入沸腾炉。
4.3.5沸腾炉安全操作规程
4.3.5.1沸腾炉点火准备工作
(1)沸腾炉能否正常运转。
(2)燃煤的粒度和水份符合要求。
(3)要求是:
含水<8%。
(4)粒度<10mm。
(5)对飞灰量有要求的工况则必须燃用粒度2~10mm粒煤。
(6)准备好司炉工具:
钩、耙、锹、推车、铁丝网筛(网孔尺寸10mm以下)等。
(7)准备好点火用材料(以供热1×106×4.18KJ/h的用量为例)木柴150斤左右:
直径<100mm,长度500mm左右(不含铁钉等)优质碎烟煤100~200Kg:
筛选1~6mm粒径为宜,木炭、废油或废棉纱适量,粗黄砂或炉渣(沸渣):
炉渣粒径<10mm,干黄砂粒径<3mm。
(8)检查风机、圆盘喂料机、斗式提升、烘干机、输送系统、除尘设备等是否正常。
(9)原煤含水量不超过8%。
(10)检查风帽是否堵塞,在主沸腾床上铺厚100mm干粗黄砂。
(11)开风机沸腾逐渐减少风量至黄砂呈鼓泡状运动。
(12)注意记录此时的风门开度和鼓风压力。
(13)然后停风机将不沸腾处风帽孔掏通直至整个炉床均匀沸腾为止。
(14)在主沸腾床上铺干粗黄砂至床料厚度约200mm,加入床料总量约8%的优质碎烟煤,开启风机使之混合均匀。
4.3.5.2沸腾炉开炉点火
(1)加入适量木柴,点火燃烧以预热炉膛和加热底料,底料上有足够火炭层(厚度约60mm)后,再把未烧透的大块木柴钩出,将赤红火炭层扒平。
(2)开动鼓风机,瞬间将风压升至3500Pa后突然关闭鼓风风门,使炭、砂、煤三者混合均匀,再徐徐开启鼓风风门,使炉料均匀蠕动,并不断搅拌均化,扒出焦块,待全部炉料燃烧成桔黄色后,加大鼓风风门开度,使之沸腾燃烧,注意此时不可加煤,只能压冷砂防止结焦,直至炉料含炭量降至正常值。
(3)当炉料中含煤量达正常值后,改用园盘喂料机自动加煤,调整主风阀门开度后即可正常燃烧,此时方可投料生产。
4.3.5.3正常运行
沸腾炉的炉温变化非常快,很短时间就可能造成熄火或结焦,因此司炉人员必须密切监视仪表指示炉膛燃烧情况,注意调整鼓风量、引风量和给煤量,保持在正常工作温度范围内沸腾燃烧,并利用增/减风、煤来控制炉膛温度及供热大小。
4.3.5.4送风量
(1)风门未动而风量自动减小,风室压力自行变大,说明煤粒过大或料层增厚,遇此应排渣,保持风量均衡。
(2)一般给煤量为定值时,可改变送风量维持正常运行,温度下降时,适当减小风量,反之适当增大风量。
也可调整煤量控温,但供热功率随给煤量变化,风量要及时匹配,以免结焦。
4.3.5.5料层温度
运行中应控制料层温度在正常工作温度范围内。
为了使燃料尽可能迅速和完全,一般烧无烟煤时,料层温度约为950~1050℃,烟煤较易燃烧,料层温度可控制在850~950℃。
运行料层温度波动引起主要原因有:
①由于风量或煤量变动引起的;
②由于风、煤配比失调;
③给煤不均匀,甚至因堵塞中断给煤;
④运行中变换了煤种,风、煤量调节不及时、不得当;
⑤烧混煤时,混合不均匀,给煤量调节不适;
因此,司炉人员必须密切注意温度的变化,及时调整和控制料层温度。
4.3.5.6压火备用
一班或两班作业需压火备用。
压火前,先停止给煤,待炉温下降到800℃(肉眼观察呈桔红色)左右,关闭风机,迅速用锹加入料层总量10%左右的煤粒(碎粉煤)后,开启风机运行3~4秒,使煤与炉料充分混合,在炉温尚未上升之前关闭鼓风机和引风机,密闭风门和炉门,进入压火状态。
重新开炉时,先开动鼓风机并徐徐打开鼓风风门,使炉温逐步升高,不断搅拌炉料,扒出焦块,增加引风,待整体炉料均匀地转为桔黄色后,开动系统设备,转入正常运行。
4.3.5.7结焦处理
(1)低温结焦
低温结焦通常在点火或压火时出现,布风不均是其产主的原因,炉温偏低、火口没有及时扒散也可形成低温结焦。
操作时要使炉床各处均匀燃烧,随炉温升高而逐渐看火调风,还应及时用耙子扒散较旺火口,控制在600~700℃以前的升温时间,引火煤要做到勤投、少加、投散。
低温结焦可在升温过程中用料耙扒出。
(2)高温结焦
当温度上升到1100℃左右,如不及时采取放底渣等降温措施,很容易产生高温结焦。
正常操作时底渣过厚,喂煤量变大,或煤发热量变高,或风、煤比控制不当,亦易产生高温结焦。
操作过程中,操作人员要坚守岗位,密切注意炉内变化情况,发现炉内温度升高,多处发现小孔喷火时,迅速采取减小喂煤量,用超量的送风猛吹沸腾层,同时采用放掉过多的底渣,向沸腾层加入适量冷湿炉渣等措施。
结焦不严重时,应尽快自炉门消除焦块。
如出现严重结焦应停炉清除之后再点火开炉。
4.3.6烘干机操作规程
4.3.6.1试运转
⑴、灌浆水泥干固后,进行空转试车
①连续运转8小时;
②试车前检查:
a地脚螺栓,轴承座螺栓及其它结合处是否紧固。
b检查齿轮传动,确认已无障碍。
③试车中检查下列各项:
a齿轮传动无剧烈震动及过高噪音。
b筒体无单向窜动或剧烈往复窜动。
c各部轴承温升不大于25℃,最高温度不大于60℃。
d电机电流无显著波动。
⑵、空转合格后,进行负荷试车,试车程序:
在筒体运转中通以热气流,逐步达到工作温度,并加入物料至达到负荷,在正常负荷下运转8小时,再检查第③条各项要求,确认无问题后,方可正式投产。
4.3.6.2操作、维护
(1)开车
①开车以前应作下列准备工作
a对热风炉(含系统配套设备)及烘干机各部件做一次全面的检查,确认无误后方能开车。
b检查空气导管,调节阀及鼓风机的传动。
c检查给料及卸料装置有无障碍。
②开车步骤
a点燃炉子
b开动烘干机的电动机,使系统温度达到露点以上。
c开动运输湿物料及干物料的设备。
(2)停车
①停车前30分钟停止向炉内进料并压火。
②出尽机内物料。
③关闭烘干机的电动机。
④停止运输干物料的设备。
⑤停车后,每隔10—15分钟点动一次筒体至冷却为止,以防筒体变形。
如因事故停车,除须马上压火外,亦按上法转动筒体直到冷却。
(3)在下列情况下禁止开动烘干机
①原、燃料储量不能保证烘干机或燃烧室在一定时间内连续使用。
②当筒体内扬料板缺少30%时。
③各部连接接件及地脚螺栓有松动现象,传动和支承装置的零部件如有不正常的振动噪音、冲击、发热、窜动等情况。
④当存在着没有排除的可能损坏设备正常运转的故障时。
(4)维护
①对传动支承挡轮装置必须经常检查,发现有噪音,振动和发热等不正常情况应及时处理。
②检查滚圈与托轮,挡轮的接触和磨损是否均匀,有无受力过大和出现麻面的情况。
③注意筒体上各焊缝是否良好,有无裂纹等。
④注意基础有无振动或下沉现象。
⑤检查筒体两端密封装置的密封情况是否正常。
⑥检查筒体内部扬料板的磨损、松动情况。
⑦检查出口废气温度及出料温度,以避免筒体过热,绝不允许筒体有局部烧红现象。
⑧仔细检查减速器声音有无异常。
4.3.7工艺控制指标:
烘干兰炭水份1%以下,在放料过程中取样化验。
4.3.8安全注意事项
(1)设备在运转中不能用手伸入减速机。
(2)在运行机件上不准用抹布擦机器外表。
(3)工作服应束紧,避免机件传动部分咬住衣袖造成人身事故。
(4)检修工具及零件不得放在运转机件上。
(5)操作人员在工作时要穿戴好完整的劳动保护用具。
(6)设备的转动部分,在运转时不能触动、加油、清扫和检修。
(7)突然停电时,禁止触动设备运转部分,以防突然送电造成伤亡,必须在电工检查处理后方可按规程继续开车。
(8)必须保证各运转设备有安全防护装置,否则禁止开车。
(9)检修和临时用照明灯必须采用36伏以下的安全电压。
(10)设备检修时所拆掉的安全装置,在检修后立即装好否则不准开车。
(11)当生石灰落入眼睛内的时候需用大量的水冲洗。
(12)向烘干窑内加料时必须连续均匀,以防止提升机堵塞造成设备损失事故。
(13)烘干人员在操作时必须注意正确的开机和关机程序。
(14)任何修理工作必须在停车后进行,先切断电源并在电动机控制开关处挂上“正在检修、禁止开启”的标志。
(1