铸造工艺考试复习重点.docx
《铸造工艺考试复习重点.docx》由会员分享,可在线阅读,更多相关《铸造工艺考试复习重点.docx(10页珍藏版)》请在冰豆网上搜索。
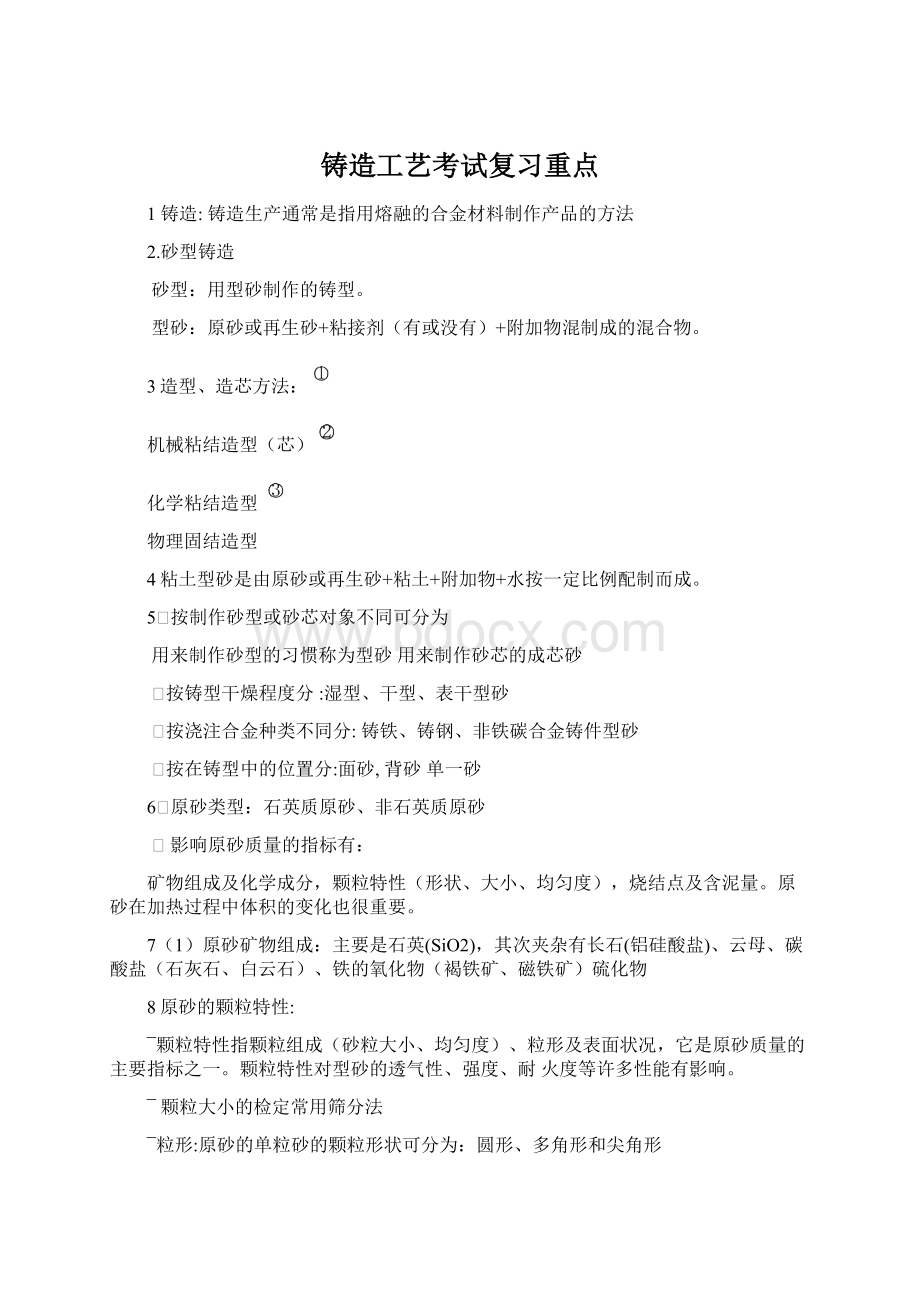
铸造工艺考试复习重点
1铸造:
铸造生产通常是指用熔融的合金材料制作产品的方法
2.砂型铸造
砂型:
用型砂制作的铸型。
型砂:
原砂或再生砂+粘接剂(有或没有)+附加物混制成的混合物。
3造型、造芯方法:
机械粘结造型(芯)
化学粘结造型
物理固结造型
4粘土型砂是由原砂或再生砂+粘土+附加物+水按一定比例配制而成。
5v按制作砂型或砂芯对象不同可分为
用来制作砂型的习惯称为型砂用来制作砂芯的成芯砂
v按铸型干燥程度分:
湿型、干型、表干型砂
v按浇注合金种类不同分:
铸铁、铸钢、非铁碳合金铸件型砂
v按在铸型中的位置分:
面砂,背砂单一砂
6v原砂类型:
石英质原砂、非石英质原砂
v影响原砂质量的指标有:
矿物组成及化学成分,颗粒特性(形状、大小、均匀度),烧结点及含泥量。
原砂在加热过程中体积的变化也很重要。
7
(1)原砂矿物组成:
主要是石英(SiO2),其次夹杂有长石(铝硅酸盐)、云母、碳酸盐(石灰石、白云石)、铁的氧化物(褐铁矿、磁铁矿)硫化物
8原砂的颗粒特性:
¯颗粒特性指颗粒组成(砂粒大小、均匀度)、粒形及表面状况,它是原砂质量的主要指标之一。
颗粒特性对型砂的透气性、强度、耐火度等许多性能有影响。
¯颗粒大小的检定常用筛分法
¯粒形:
原砂的单粒砂的颗粒形状可分为:
圆形、多角形和尖角形
¯原砂粒形对型砂性能的影响
对湿型而言,其它条件相同时,原砂的颗粒形状越圆,型砂就越紧实、标准砂型试样质量就愈大、透气性愈低,砂粒更靠近,粘结桥越多,且完善,因而强度越高
9含泥量:
指原砂或型砂中直径小于0.02mm的细小颗粒的含量(质量百分数),
10烧结点:
烧结点是原砂颗粒表面或砂粒间混合物开始熔化的温度。
¯原砂烧结点的高低主要决定于矿物组成化学成分和颗粒特性
11¯加热时石英晶体颗粒体积发生膨胀,膨胀有两方面的原因:
一是因温度升高产生的热膨胀;
二是温度升高时因石英相变而发生相变膨胀。
12¯根据粘土矿物种类的不同分为普通粘土和膨润土
普通粘土:
俗称白泥,主要由高岭石或伊利石类粘土矿物组成。
膨润土:
又称为酸性陶土,主要由蒙脱石类粘土矿物组成
13¯可交换性阳离子
所谓离子交换是指粘土中已吸附的阳离子能与溶液中的离子之间进行当量交换作用,把粘土中已吸附的并能与其它阳离子发生交换反应的阳离子称为可交换性阳离子。
¯蒙脱石阳离子交换性质具有:
同号离子相互交换,等电荷量相互交换、阳离子的交换和吸附是可逆的三个特点。
14活化处理:
根据粘土的阳离子交换特性,对钙膨润土加
入钠盐进行适当处理,使其转化为钠膨润土,其实质
是使吸附的钙离子被钠离子所置换,对这种离子交换
过程的处理技术,通常称膨润土的活化处理
15¯粘土选用
粘结力耐火度抗夹砂能力复用性
16附加物
v煤粉:
铸铁用湿型砂中加入煤粉,可以防止铸件表面产生粘砂缺陷,并能改善铸件表面光洁程度
v淀粉:
淀粉加入湿型砂中,可减少夹砂结疤缺陷、冲蚀缺陷,增加型砂变形量,提高型砂韧性、可塑性、降低起模时模样与砂型间的磨擦阻力、减少因砂型表面风干和强度下降而引起的砂孔缺陷
v渣油:
渣油液能提高型砂的紧实流动性,使砂型表面密实,减少砂粒间孔隙,使透气性明显降低
17粘土砂的性能
常温性能:
湿强度、干强度、透气性、流动性、韧性等。
高温性能:
高温强度、热湿拉强度、退让性、发气性、体积膨胀性等。
18铸铁件用型砂
湿型砂:
用湿型砂浇注铸件时,应着眼于提高铸件的尺寸精度和表面光洁度,预防砂眼、粘砂、夹砂和气孔缺陷的产生。
干型砂:
对于中、大型铸件和质量要求较高的重要铸件,以及多数砂芯,一般采用干型砂
表面干型:
表面干型铸造是将型腔表面层烘干;应具有特高的透气性、湿强度和低的发气性,较好的抗夹砂能力。
19湿型中的夹砂结疤、鼠尾缺陷
20水玻璃的模数:
水玻璃中SiO2和Na2O的摩尔数比值称为模数
☞模数的大小直接影响到水玻璃性质。
在一定浓度范围内,水玻璃的模数越高,说明SiO2的相对含量越高,此水玻璃的粘结性就高,硬化速度也快。
但是模数太高,硬化速度太快,溶胶凝聚的网状结构紊乱不齐,反而使砂型的硬化强度不高
☞模数的大小仅表示水玻璃中SiO2与Na2O的相对含量,并不表示水玻璃中硅酸钠的浓度
21水玻璃在一定条件下逐渐变硬的过程称为水玻璃的硬化反应
硬化过程:
硅酸钠的水解平衡硅酸溶胶的形成硅酸凝胶的形成
22促使钠水玻璃硬化的措施
v失水由液态到固态的转变:
加热烘干吹热空气、吹干燥的压缩空气真空脱水微波照射加入产生放热反应的化合物
v化学反应形成新的产物:
吹CO2硬化的CO2-钠水玻璃砂
23CO2硬化砂
v向水玻璃砂制成的型(芯)中吹入CO2气,在很短的时间内就可以使型(芯)硬化,这就称为CO2硬化法
v硬化原理
☞CO2是一种脱水能力相当强的气体,从沙粒周围流过,CO2与粘接剂接触面积大,使钠水玻璃部分失水,同时CO2与钠水玻璃中的水作用形成碳酸从而使表面钠水玻璃的PH值不断降低,并达到迅速硬化。
☞CO2硬化既有钠水玻璃的物理脱水作用,又有化学反应,两种机理难以截然分开,通常其粘接是两种作用的结果。
24水玻璃砂使用中存在的问题
v表面粉化(白霜
☞解决方法是控制钠水玻璃砂水分不要偏高,CO2吹气时间不宜过长,型、芯不要久放。
另据有的工厂经验,在钠水玻璃中加入占砂重1%左右、密度为1.3g/cm3的糖浆,可以有效地防止表面粉化。
v粘砂
①原因:
☞用钠水玻璃砂制造的型、芯浇注铸铁件时,常产生严
重粘砂,这限制了它在铸铁件上的应用。
☞用于一般中小型铸钢件时,只要选用粒度较细、SiO2
含量高的石英砂,舂的紧实,通常可获得表面光洁的
铸件。
用于厚大铸钢件或高合金钢铸件,粘砂也较严
重。
☞钠水玻璃砂的粘砂往往是机械粘砂和化学粘砂并存
②防粘砂措施:
☞一般铸铁件可刷涂料而且最好醇基涂料,也可在钠水玻璃砂中加入适量的煤粉(如3~5%)(质量分数);也有加2%(质量分数)有填料效能(fillereffect)的高龄土式粘土,从而得到了表面光洁的铸件。
☞大、厚铸钢件:
刷涂料,在水玻璃砂中加入易熔的硅酸盐材料,或加少量FeO,MnO等物质,以促使铸钢件表面形成易熔的玻璃体物质。
(三)出砂性和旧砂回用
(1)出砂性
☞钠水玻璃砂的主要缺点是溃散性差,使出砂困难,从而限制了它在铸造上更广泛的应用。
残留强度是评定钠水玻璃砂的溃散性常用方法之一。
☞钠水玻璃砂残留强度随温度的改变呈双峰特性。
这两个峰值的高低决定了钠水玻璃砂溃散性的好坏,铸件出砂的难易。
¯改善钠水玻璃砂的出砂性所遵循的主要途径和采取的主要措施:
加入有机或无机附加物。
②减少钠水玻璃用量。
③降低易熔物质的含量
④采用石灰石作原砂的钠水玻璃CO2硬化砂。
25壳芯(型
¯铸造生产中,砂芯(型)直接承受液态金属作用的只是表面一层厚度仅数毫米的砂壳,其余的砂只是起到支承这层砂壳的作用,这就促使铸造工作者寻求用壳型、壳芯来制造铸件
用热法制造壳型,称为“C”法或“壳法”
26覆膜砂生产方法
¯壳芯法树脂砂常用树脂是酚醛树脂。
由于酚醛树脂是固态粘结剂
¯生产复膜砂的方法有三种:
冷法、温法和热法。
27制壳(型)芯方法
有翻斗法和吹砂法:
翻斗法常用于制造壳型,吹砂法用于制造壳芯
28吹砂法有顶吹法和底吹法:
顶吹法用于制造大型复杂的砂芯
底吹法一般用于小型砂芯的生产
29热芯盒法制芯是将用液态热固性树脂和催化剂配成的芯砂,填入预热到180~250℃的芯盒中,贴近芯盒表面的砂芯受热,其粘结剂在很短时间即可缩聚而硬化。
¯热芯盒法树脂砂所采用的粘结剂:
呋喃树脂和酚醛树脂
30热芯盒法硬化用催化剂
热芯盒法使用的催化剂为潜伏型催化剂,目前使用的为在常温下呈中性或弱酸性(有利于混合好的树脂砂的存放,即达到可使用时间长),而在加热时激活成强酸,促使树脂迅速硬化。
生产中常用的是氯化氨、硝酸氨、磷酸氨水溶液,也有采用对甲苯黄酸铜盐、甚至对甲苯黄酸铵盐的。
31温芯盒用粘结剂通常采用糠醇型呋喃树脂
32自硬冷芯盒法是将原砂、液态树脂及液态催化剂混合均匀后,填充到芯盒(或砂箱)中,稍加紧实即于室温下在芯盒(或砂芯)内硬化成形,叫自硬冷芯盒
法。
¯自硬冷芯盒法可分为:
酸催化树脂自硬法;尿烷系树脂砂自硬法;酚醛-酯自硬法。
33¯酸催化树脂自硬砂用树脂:
常用粘结剂为呋喃树脂和热固性酚醛树脂
¯酸催化树脂自硬砂用催化剂
常用催化剂:
采用活性催化剂,本身就是强酸或中强酸,一般采用芳基磺酸、无机酸、及他们的复合物。
常用的无机酸为:
磷酸、硫酸单脂、硫酸乙酯、
常用的芳基磺酸:
对甲苯磺酸、苯磺酸、二甲苯磺酸、苯酚磺酸、萘磺酸、对氯苯磺酸等。
34气化模铸造的实质:
用泡沫聚苯乙烯塑料模样代替普通模样,造好型后不取出模样就浇入金属液,在灼热的液态金属的作用下,泡沫塑料模气化,燃烧而消失,金属液取代了原来塑料模所占据的空间位置,冷却凝固后即可获得所需要的铸件
35气化模的材料特点及对它的要求
(1)密度小、气化速度快、发气量和残留物少
(2)气化温度低,气化时所需热量小
(3)材料强度及表面刚性较好,模样在制造、搬运、保管和造型过程中不易损伤或变形,能保持原来的尺寸及形状。
(4)泡沫塑料的组织尽量细密、均匀,加工性能好,制造出来的模样表面光洁、平整。
(5)泡沫塑料模样表面易于涂挂涂料,烘干后涂料层能牢固地粘附在模样表面上
(6)来源丰富,价格便宜
36¯气化模铸造涂料与砂型铸造涂料的区别:
将涂料刷在气化模表面上,而不是涂刷在铸型的型腔表面上。
37¯熔模铸造就是在蜡模表面涂覆多层耐火材料,待硬化干燥后,加热将蜡模熔去,而获得具有与蜡模形状相应空腔的型壳,再经焙烧之后进行浇注而获得铸件的一种方法,故又称为失蜡铸造。
38型壳的制备:
¯熔模铸造的铸型可分为实体型和多层型壳两种,目前普遍采用的是多层型壳
¯将模组浸涂耐火涂料后,撒上粒状耐火材料,再经干燥硬化,如此反复多次,直至耐火涂料层达到所需要求的厚度为止。
¯对型壳性能的要求:
(1)具有高的常温强度,适宜的高温强度和较低的残留强度。
(2)好的透气性(特别是高温透气性)和导热性。
(3)线胀系数小(热膨胀量低)和膨胀均匀。
(4)优良的热震稳定性(即抗急冷急热性)和热化学稳定性
¯制壳的主要工序包括模组的脱脂,上涂料和撒砂,干燥和硬化,脱模和焙烧等。
¯模组的脱脂的目的:
为了改善涂料对模组的润湿性
¯撤砂的目的:
使砂粒成为型壳的骨架而得到增厚加固;
减少应力集中,防止涂料层微裂纹扩大:
使下一层涂料能与前一层很好地粘合在一起。
¯撒砂方法:
雨淋式(重力)撒砂及流态化(沸腾床)撒砂两种
¯焙烧的目的:
去除型壳中的水分、残留模料、NH4Cl及盐分等,避免浇注时产生气体,导致出现气孔、浇不到或恶化铸件表面等缺陷。
39浇注位置的选择原则:
1重要加工面应朝下或呈直立状态
2铸件的大平面应朝下
3应有利于铸件的补缩
4应保证铸件有良好的液态金属导入位置,保证铸件能充满
5应尽量减少砂芯数目
40选择分型面时,应注意以下原则:
⑴为保证铸件尺寸精度,将铸件的全部或大部分置于同一半型中成型
⑵应尽量减少分型面的数目
⑶平直分型面和曲折分型面的选择
⑷选择的分型面要有利于下芯、验型和合型
6定分型面时不要使某一砂箱过高
41型芯的设计:
¯作用:
是形成铸件内腔、孔洞和形状复杂阻碍取模部分的外形以及铸型中有特殊要求的部分
¯分类:
砂芯;金属芯;可溶性型芯;
42芯头的设计的作用:
是砂芯的定位、支撑和排气结构
43浇注系统:
¯铸型中液态金属进入型腔的通道的总称
¯浇注系统的组元:
浇口杯、直浇道、直浇道窝、横浇道、内浇道
44浇注系统的种类:
<一>按浇注系统各基本组元截面积的比例分类
(1)封闭式浇注系统:
☞指从浇口杯底孔到内浇道的截面积逐渐缩小,阻流基元为内浇道的浇注系统。
☞这种浇注系统充满得快、挡渣能力好,金属液在浇道中不容易带入空气和氧化,金属消耗少、清理方便。
☞缺点:
金属液进入型腔的线速度高,易冲坏铸型,易使金属液产生喷溅,氧化和卷入气体。
☞主要适用于不易氧化的各种铸铁件,不适用于易氧化的非铁合金铸件和用柱塞包浇注的铸钢件。
(2)开放式浇注系统
☞从浇口杯底孔到内浇道的截面积逐渐增大,阻流截面位于浇口杯底孔或直浇道上口。
☞优点:
进入型腔时金属液流速度小,充型平稳、冲刷力小,金属氧化少。
☞缺点:
挡渣效果不好,内浇道大,消耗的金属液多。
☞适用于易氧化的非铁合金铸件,球墨铸铁件和用柱塞包浇注的中、大型铸钢件。
(3)半封闭式
☞横浇道截面最大,作阻流元的是内浇道。
☞直流道上大下小,可很快充满,横浇道最后充满,可有效降低液流速度,在浇注开始时充型平稳,对铸型冲刷比封闭式小得多,挡渣作用比开放式好。
☞半封闭式浇注系统在各类铸铁件,尤其在球墨铸铁件及表面干型中广泛应用。
(4)封闭—开放式:
☞阻流截面位于直浇道下端或横浇道中。
☞挡渣效果好、充型平稳,兼有封闭式和开放式两者的优点,一般用于小型铸铁件及铝合金件。
☞但浇注系统复杂,多用于模板造型。
<二>按浇注系统在铸件浇注时的位置分类
(1)顶注式浇注系统。
☞金属液从铸件顶部注入型腔的浇注系统。
☞优点:
易于充满型腔,型腔中金属温度由下至上递增、有利于实现顺序凝固,补缩作用好。
冒口尺寸较小、节约金属。
☞缺点:
冲击力大、充型不平稳、易产生飞溅、氧化和卷入空气,铸件中容易出现砂眼、气孔、夹渣等缺陷。
☞适合于重量小、高度低、形状简单的铸件。
(2)底注式浇注系统
金属液从铸件底部注入型腔。
⏹优点:
充型平稳、排气方便,不易冲坏型腔和引起飞溅,对易于氧化的合金可以避免或减少金属液在充型过程中形成的再生渣。
⏹缺点:
金属液自下部流入,铸型温度分布不利于自下而上的顺序凝固和冒口的补缩,充型速度慢,对复杂薄壁铸件不易充满,易形成浇不到,冷隔等缺陷。
⏹多用于大、中型厚壁铸钢、铸铁件及有色合金铸件。
(3)中间注入式浇注系统
☞优点:
减低了液流落下的高度,温度分布较为适宜,内浇道开设在分型面上,便于选择部位,应用较广
☞适用于高度不太大的中等壁厚铸件。
(4)阶梯式浇注系统
☞优点:
既减轻了金属液对型腔的冲击,又使型腔上部获得高温金属液,改善补缩条件,消除铸型局部过热,有利于渣、气的上浮。
☞缺点:
造型复杂,需要合理地设计和计算,否则易出现“乱浇”现象。
☞多用于比较高大和复杂的铸件以及重型铸件。
(5)缝隙式浇注系统:
☞优点:
充型平稳、有利于阻渣,有利铸件自下而上顺序凝固和上部冒口补缩。
☞缺点:
金属消耗多,浇道切割麻烦。
☞广泛用于轻合金铸造中,尤其适合缩松倾向大的镁合金铸件,由于切割困难,铸钢、铸铁中很少使用
(6)复合式浇注系统:
对于重、大型铸件
45冒口的作用、分类:
☞冒口—铸型内靠近铸件最后凝固的部位所开设的具有一定补缩能力的合金液容器称作冒口。
☞冒口的作用:
主要作用是补缩铸件,此外还有集渣、排气和合箱操作观察的作用。
46通用冒口补缩原理
①冒口凝固时间大于或等于(被补缩部分)的凝固时间。
②有足够的金属液补充铸件的液态收缩和凝固收缩及浇注后型腔扩大的体积。
③在凝固期间,冒口被补缩部位之间存在补缩通道,扩张角始终向着冒口。
47¯确定冒口位置的一般原则
1冒口应放在铸件最后被补缩部位的上部或热节附近。
②冒口应尽量放在铸件最高最厚的地方,以便利用金属液的自重进行补缩。
对低处的热节,增设补贴或使用冷铁,实现顺序凝固
③冒口不应设在铸件重要的、受力大的部位,以防组织粗大,减低铸件强度。
④对铸件不同高度处的热节进行补缩时,可分别安放冒口
⑤冒口应尽可能不阻碍铸件的收缩,不安放在铸件的应力集中处,以免引起裂纹。
⑥冒口的设置应便于清除和随后的机械加工。
48冷铁—为增加铸件局部冷却速度,在型腔内部及工作表面安放的激冷物称作冷铁
49冷铁的分类:
☞内冷铁——放置在型腔中需要激冷的部位,使合金激冷并同铸件熔为一体的金属激冷物称为内冷铁
☞外冷铁:
又分为直接外冷铁和间接外冷铁两类
50设计冷铁的主要内容是确定冷铁放置的位置,冷铁的形状和尺寸。