驾驶室油漆质量问题原因分析.docx
《驾驶室油漆质量问题原因分析.docx》由会员分享,可在线阅读,更多相关《驾驶室油漆质量问题原因分析.docx(15页珍藏版)》请在冰豆网上搜索。
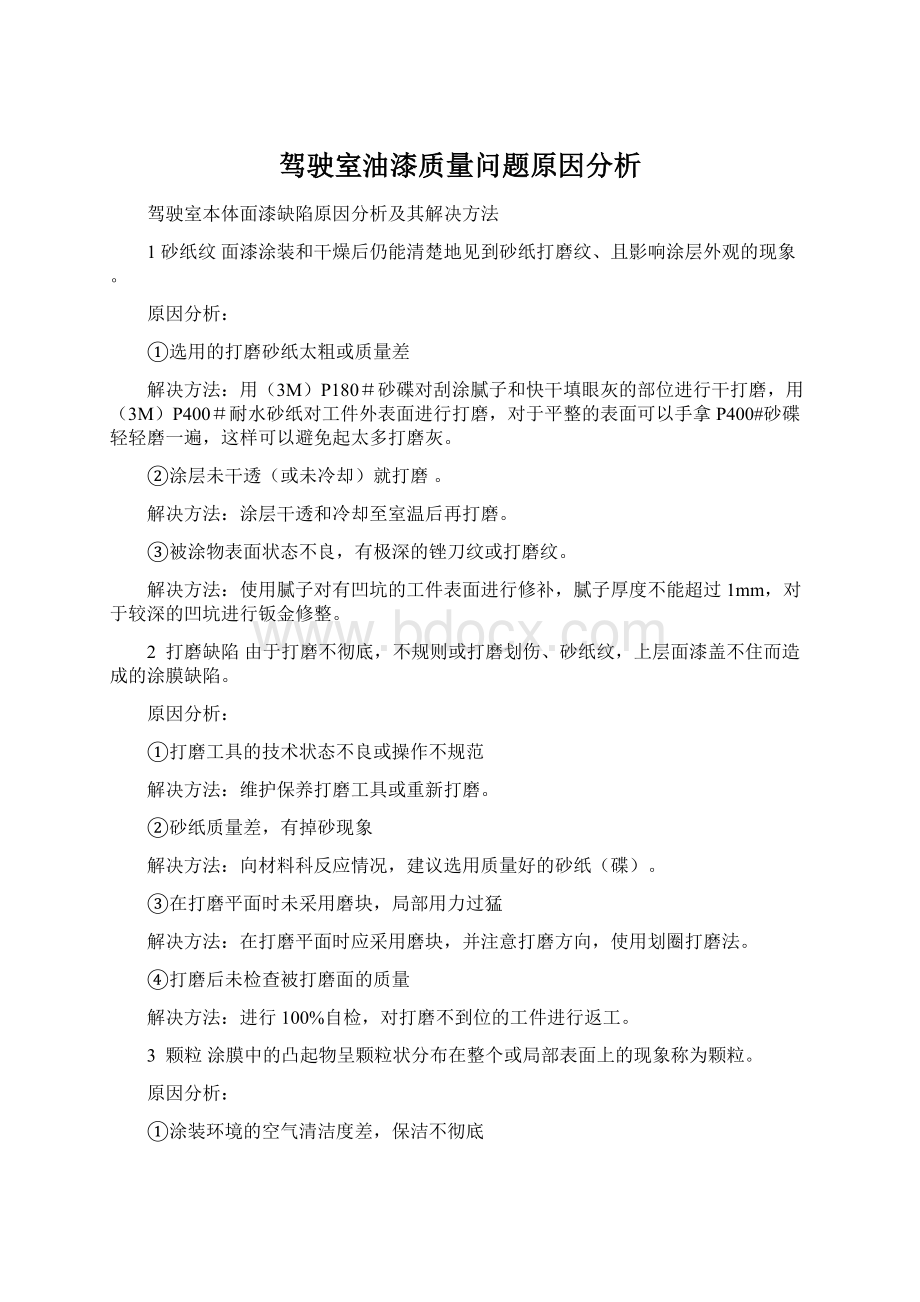
驾驶室油漆质量问题原因分析
驾驶室本体面漆缺陷原因分析及其解决方法
1砂纸纹面漆涂装和干燥后仍能清楚地见到砂纸打磨纹、且影响涂层外观的现象。
原因分析:
①选用的打磨砂纸太粗或质量差
解决方法:
用(3M)P180#砂碟对刮涂腻子和快干填眼灰的部位进行干打磨,用(3M)P400#耐水砂纸对工件外表面进行打磨,对于平整的表面可以手拿P400#砂碟轻轻磨一遍,这样可以避免起太多打磨灰。
②涂层未干透(或未冷却)就打磨。
解决方法:
涂层干透和冷却至室温后再打磨。
③被涂物表面状态不良,有极深的锉刀纹或打磨纹。
解决方法:
使用腻子对有凹坑的工件表面进行修补,腻子厚度不能超过1mm,对于较深的凹坑进行钣金修整。
2打磨缺陷由于打磨不彻底,不规则或打磨划伤、砂纸纹,上层面漆盖不住而造成的涂膜缺陷。
原因分析:
①打磨工具的技术状态不良或操作不规范
解决方法:
维护保养打磨工具或重新打磨。
②砂纸质量差,有掉砂现象
解决方法:
向材料科反应情况,建议选用质量好的砂纸(碟)。
③在打磨平面时未采用磨块,局部用力过猛
解决方法:
在打磨平面时应采用磨块,并注意打磨方向,使用划圈打磨法。
④打磨后未检查被打磨面的质量
解决方法:
进行100%自检,对打磨不到位的工件进行返工。
3颗粒涂膜中的凸起物呈颗粒状分布在整个或局部表面上的现象称为颗粒。
原因分析:
①涂装环境的空气清洁度差,保洁不彻底
解决方法:
调输漆室、喷涂室、晾干室和烘干室的送给空气除尘要充分,确保涂装环境洁净,要求保洁公司定期做深度保洁,并且测试喷漆室等关键设备内的表面洁净度,出具洁净度报告。
测试步骤及等级评定遵循ISO14644-9的内容。
②被涂物表面不洁净
解决方法:
被涂物表面应清洁,如用粘性纱布擦净被涂面上的尘埃或纤维。
③施工操作人员的工作服、手套及涂装前擦净用材料掉纤维,或喷漆室静压层的过滤棉不合格,容易掉纤维
解决方法:
应选用带不掉纤维的防静电布料做工作服、专用手套及过滤棉,完善保洁公司的工作服清洁管理制度,要求保洁公司在每洗完一批工作服之后做工作服洁净度检测,并出具纤维数量检测,如果数量超标进行整改。
④易沉淀的涂料未充分搅拌或过滤,或涂料变质
解决方法:
供漆管路上应装有过滤器,调漆时必须按照操作规程对油漆进行严格的过滤,并及时清洗过滤袋,以便循环利用。
⑤擦净使用的粘性纱布不合格,粘尘效果不好。
解决方法:
更换粘性纱布,使用粘尘效果好、擦净效率高的长丝粘尘布,且该种粘尘布可以反复使用300次,减少浪费降低废物排放。
刮腻子常见缺陷、原因分析及解决方法:
4腻子开裂:
腻子层从中间裂开的现象。
原因分析:
①一次性刮涂过厚
解决方法:
每次刮涂不能超过允许的厚度。
②腻子层未刮涂严实
解决方法:
仔细刮涂,不让腻子层留有孔隙。
③腻子层收缩性大,且不平整
解决方法:
选用收缩比小的腻子,刮涂平整。
5腻子脱落:
腻子层部分或者全部从被修补的部位脱离工件表面的现象。
原因:
①腻子与底漆不配套或被涂物表面事先未涂底漆
解决方法:
选用相配套的腻子和底漆,刮涂腻子前,被涂物表面必须先涂过底漆。
②被涂物表面有油污
解决方法:
被涂物表面的油污应去除干净。
③腻子的体质颜料组分过多
解决方法:
选用合适的腻子,在腻子中不能任意增加体质颜料。
④腻子太稠,润湿性能差
解决方法:
适当添加稀释剂并调匀。
6腻子起泡:
在刮涂过程中,腻子表面呈泡状突起,或有产生气泡的现象。
原因:
①腻子层刮涂不严实,残留有气泡
解决方法:
重新刮涂严实,不得残留空气。
②腻子中含有水分
解决方法:
调配腻子时,严格避免水分混入腻子。
③腻子层未干透
解决方法:
上道腻子层干透后,方可刮涂下道腻子或涂底漆。
7腻子边翻卷:
腻子层边缘沿工件表面卷起的现象。
原因:
①一道腻子刮涂次数太多
解决方法:
每挖取一次腻子,应该按操作步骤,不停顿地、尽快刮涂好,不要多次来回涂刮。
②腻子的润湿性能差
解决方法:
适当添加稀释剂。
③被涂物表面不干净
解决方法:
刮涂前被涂物表面应清理干净。
8腻子不平整有刮痕:
腻子层表面不光滑,有刮刀或刮板的痕迹或细小凹槽的现象。
原因:
①腻子太稠,且一次刮涂太厚。
解决方法:
适当添加稀释剂,一道腻子层不要超过允许的厚度0.5mm。
②打磨不规范或打磨器材选用不当。
解决方法:
选用适合的打磨器材,手工打磨要用垫板。
③腻子打磨性能差,腻子层太厚。
解决方法:
采用机械打磨与手工打磨相结合的方法。
9流挂指在涂覆和固化期涂膜出现的下边缘较厚或流痕的现象。
①所使用溶剂挥发过慢或与涂料不配套
解决方法:
正确选用配套溶剂。
②一次涂的过厚,喷涂操作不规范,喷枪压力过大。
解决方法:
提高喷涂操作的熟练程度,喷涂均匀,一次不宜喷涂太厚,一般控制在20µm左右为宜,如需一次喷得30-40µm厚得涂膜,则要采用“湿碰湿”工艺。
③涂料粘度偏低
解决方法:
严格控制涂料的施工粘度和温度在工艺要求的范围内。
④环境温度过低或周围空气的溶剂蒸汽含量过高
解决方法:
增加换气量,施工场所的环境温度保持在15℃-25℃。
⑤在光滑的涂膜上涂布新涂料时,发生垂流
解决方法:
在旧涂膜上涂新涂料时要预先打磨旧涂层。
⑥涂料本身的抗流挂性能不良
解决方法:
要求涂料供应商对涂料进行改善,提高其抗流挂性能。
⑦喷涂扇面较大,在机器人喷涂和手工喷涂部位产生重叠,造成过喷涂。
解决方案:
在和机器人配合喷涂时,手工修补部位采用小扇面喷涂,减少喷涂重叠。
⒑露底、盖底不良由于漏涂而使被涂面未涂上涂料的现象称为露底(俗称缺漆),因涂的薄或涂料遮盖力差未盖住底色的现象称为盖底不良。
原因:
①所用涂料的遮盖力差或在使用前未搅拌均匀。
解决方法:
选用遮盖力强的涂料,增加涂层厚度或增加喷涂道数,涂料在使用前和涂装过程中应充分搅拌。
②涂料的施工粘度偏低,涂的过薄。
解决方法:
适当提高涂料的施工粘度或选用施工固体分高的涂料,每道涂装应达到规定的喷涂厚度:
一般每道喷涂厚度为20µm左右为宜。
③发生漏涂。
解决方法:
提高喷涂操作的熟练程度,增加自检。
④底、面漆的色差过大,如在深色漆面上涂亮度高的浅色涂料。
解决方法:
底涂层的颜色尽可能与面漆的颜色相近,或将原涂层去除。
⒒咬起涂面漆后底涂层被咬起脱离,产生皱纹、胀起、起泡等现象称为咬起。
原因:
①涂层未干透就涂下一道涂料。
解决方法:
底涂层干透后再涂面漆。
②底、面涂料不配套。
解决方法:
选用底、面配套涂料。
③涂层涂的过厚。
解决方法:
在易产生咬起的配套场合,应先在底涂层上薄薄涂一层面漆,等稍干后再喷涂。
⒓缩孔、抽缩受被涂物表面存在的(或混入涂料中)异物(如油、水等)的影响,涂料不能均匀附着,产生抽缩而露出被涂面的现象。
这种缺陷有时产生在刚涂装完的湿涂膜上,有时在烘干后的干涂膜才发现。
原因:
①喷漆工具及设备不洁净,使有害物混入涂料中。
解决方法:
在涂装车间,无论是设备、工具还是生产用辅助材料等,绝对不能带有对涂料有害的物质,尤其是硅酮。
②被涂物面不净,有水、油、灰尘、肥皂、硅酮等异物附着。
解决方法:
清理干净被涂物表面的附着物。
③涂装环境空气不清洁。
解决方法:
净化环境空气,更换工作区域空调过滤层或过滤袋。
④涂装工具、工作服、手套不干净
解决方法:
及时清洗工作服、手套,给涂装工具做好保洁。
⒔针孔在涂膜上产生针状小孔或象皮革的毛孔那样的孔的现象称为针孔。
原因:
①涂料的流动性不良,流平性差,释放气泡性差
解决方法:
选用合适的涂料。
②涂料储运时变质。
解决方法:
选用合适的涂料,对易产生针孔的涂料应加强进厂检验,避免不合格材料投入生产。
③涂料中混入不纯物。
解决方法:
注意存涂料的容器与涂装工具的清洁和溶剂的存储,防止不纯物混入涂料中。
④涂装后晾干不充分,烘干时升温过急,表面干燥过快。
解决方法:
涂装后应按工艺要求进行挥发,保证挥发的工艺时间。
⑤被涂物的温度过高和被涂物表面有污物和小孔。
解决方法:
注意被涂物的温度和清洁度,消除被涂物面的小孔。
⑥环境空气湿度过高。
解决方法:
关闭加湿器或提高环境温度,使喷涂环境的湿度降下来。
⒕气泡在涂装过程中,涂膜表面呈泡状鼓起,或在涂膜中有产生气泡的现象。
烘干型涂料易产生这一缺陷。
搅拌引起的气泡或由溶剂蒸发产生的气泡,在涂装成膜过程中未消失而残留在涂膜中,统称为气泡。
原因:
①溶剂挥发快,涂料的粘度偏高。
解决方法:
使用指定溶剂,粘度应按涂装方法选择,不宜偏高。
②涂层烘干时加热过急,晾干时间过短。
解决方法:
涂层烘干时有个缓冲区域不宜升温过急。
③底材、底涂层或被涂面含有(或残留有)溶剂、水份或气体。
解决方法:
喷涂前擦净底材、底涂层或被涂面,使其干燥清洁,不含水分和溶剂。
④搅拌混入涂料中的气体未释放尽就涂装。
解决方法:
添加醇类溶剂或消泡剂。
⒖桔皮在喷涂时不能形成平滑的涂膜面,而出现类似桔皮状的皱纹表层。
原因:
1涂料的施工粘度高,流平性差。
解决方法:
选用合适的溶剂,添加流平剂或挥发较慢的高沸点有机溶剂,降低施工粘度,以改善涂料的流平性。
②压缩空气的压力低,出漆量过大和喷具不佳,导致雾化不良。
解决方法:
调整压缩空气压力,选择出漆量和雾化性能良好的喷涂工具,使涂料达到良好的雾化。
③被涂物和空气的温度偏高,喷涂室内风速过大,导致溶剂挥发过快。
解决方法:
被涂物应冷却到50℃以下,喷漆室内空气温度应在20℃左右。
④涂层晾干时间短,喷涂厚度不足。
解决方法:
一次喷涂到规定厚度(宜控制到不流挂的限度),适当延长涂层晾干时间,不宜过早进入高温炉烘干。
⑤喷涂距离不适当。
如太远。
解决方法:
调整喷涂距离在200mm—300mm。
⒗烘干不良、未干透涂膜干燥(自干或烘干)后未达到完全干透,手摸涂膜有发湿之感,涂膜发软,未达到规定硬度或存在表干、里不干等现象。
原因:
①烘干或烘干的温度和时间未达到工艺规范。
解决方法:
严格执行干燥工艺规范。
②自干场所换气不良,湿度高,温度偏低;烘干室的技术状态不良,温度偏低或烘干时间不足。
解决方法:
调整设备或场所的湿度和温度,使自干场所和烘干室的技术状态达到工艺要求。
③涂料一次涂的太厚。
解决方法:
氧化固化型涂料一次不宜涂得太厚,如厚度超过20μm,则应分几次涂装。
④自干型涂料所含固化剂失效,或未添加固化剂。
解决方法:
添加合适的固化剂,并且按照规定的用量来添加。
⑤烘干室内的被烘干物过多,热容量不同的工件同时在一个烘干室内烘干。
解决方法:
不同热容量的工件应有不同的烘干规范(或都按工件达到烘干温度后计烘干时间),烘干室的装载量应控制在一定的范围内。
⒘过烘干涂层在烘干过程中因烘干温度过高或时间过长,产生失光、变色、变脆、开裂和剥落等现象。
原因:
①烘干设备失控,造成烘干温度过高。
解决方法:
调整烘干设备的技术状态良好,防止烘干温度失控。
2烘干时间过长。
解决方法:
烘干时间应符合工艺规定,如被涂物因故在烘干室中停留时间过长,应设法紧急降温,在高温烘干场合,被涂物不宜长时间放在烘干室内,应进行排空,即把驾驶室从烘干室中排出。
3涂层配套和烘干规范选择不当。
解决方法:
涂层配套应合适,面漆涂层的烘干温度应符合涂层工艺要求的烘干温度,如现执行的底漆烘干温度为180±5℃,面漆烘干温度为145±5℃,烘干室温度一经设定好之后,不能随意变动。
⒙起泡涂膜的一部分从被涂面或底涂层上浮起,其内部还充满这液体或气体,且大小直径由(1~5)mm或大块浮起的现象。
原因:
①被涂面有油汗液、指纹、盐碱、打磨灰等亲水物质残存。
解决方法:
清理被涂表面残存的亲水物质。
②清洗被涂面的最后一道纯水的洁净度差,杂质离子含量高。
解决方法:
更换电泳前的最后一道纯水洗,使其电导率符合工艺要求。
③涂层干燥固化的不充分。
解决方法:
涂膜应充分干透。
④所用涂料的涂膜耐水性或耐潮湿性差。
解决方法:
根据被涂物使用环境,选用耐水性优良的涂料。
⑤涂环境高温高湿,如在梅雨季节涂膜易起泡。
解决方法:
及时调整喷漆室温度和湿度,使其保持在工艺要求的范围之内:
温度26±4℃,湿度60%-70%。
⒚涂膜剥落由于附着力不良,受外力作用产生漆膜脱落的现象。
原因:
①涂装前表面预处理不佳,或表面预处理后至涂装的间隔时间过长。
解决方法:
涂装前被涂面应处理清洁,并应立即进行涂装。
②被涂面太光滑。
解决方法:
被涂面太光滑时应打磨或经过特殊化学或物理方法处理;旧漆层应打磨,提高涂层的附着力。
③底漆层过烘干或在旧漆层上涂装,而面漆层附着性不佳。
解决方法:
严格执行工艺,严防过烘干。
④涂料配套不适当。
解决方法:
选用合适的涂料。
⒛裂纹、开裂涂膜出现部分断裂的现象。
原因:
主要原因是涂层经受不住冷热、干湿或侵蚀液体的交替变化。
①涂层配套不适当,如底层涂膜比面层涂膜软。
解决方法:
通过实验解决涂层的配套性,使底、面漆硬度、伸缩性接近。
②底漆涂层未干透就涂面漆。
解决方法:
底漆涂层按规定时间干透后方能涂面漆。
③所用面漆的耐候性差。
解决方法:
选用耐候性、耐温变性优良的面漆。
④涂层老化。
解决方法:
重新喷涂。
21.色不匀(色发花)涂膜的颜色局部不均匀,出现斑印、条纹和色相杂乱的现象。
一般是由涂料的涂装不当,以及涂料组分变质等引起的。
原因:
①涂料中的颜料分散不良或两种以上的色漆相互混合时混合得不充分
解决方法:
应选用分散性和互溶性良好的颜料。
②所用溶剂的溶剂力不足或施工粘度不适当
解决方法:
应选择适当的溶剂,采用符合工艺要求的涂装粘度,调配复色漆时应使用同一类型的涂料,最好用同一厂家生产的同一类型的涂料。
③涂得太厚,使涂膜中的颜料产生里表“对流”
解决方法:
应采用符合工艺要求的膜厚,施工过程中喷涂要均匀。
④在涂装场所附近有能与涂膜产生作用的气体(如氨气、二氧化硫等)的发生源
解决方法:
应同那些气体的发生源隔离开,避免影响。
22.金属闪光色不匀(银粉不匀)在喷涂金属闪光面漆时,因喷涂的厚度不匀,流挂和所用溶剂与涂料不配套而引起铝粉分布不匀、定向不匀,导致涂膜外观颜色不匀的现象。
原因:
①喷涂粘度选择不当(过低或过高)
解决方法:
调整到合适的喷涂施工粘度。
②涂层过厚或膜厚不均匀,雾化差、喷涂操作不熟练
解决方法:
应提高喷涂操作的熟练程度,采用专用喷涂工具或涂装机器人。
③涂底色与罩光清漆采用“湿碰湿”工艺时,中间晾干时间过短
解决方法:
选择“湿碰湿”工艺的合适晾干时间。
或增加吹(60-80)℃热风的工序。
④环境温度过低
解决方法:
应将喷涂时的环境温度调节到合适的范围内。
23.光泽不良(发糊)有光泽涂层干燥后没有达到应有的光泽或涂装后不久涂层出现光泽下降、雾状朦胧现象。
原因:
①被涂面对涂料的吸收量大,且不均匀
解决方法:
涂相应的封底涂料,以消除被涂面对面漆的吸收或不均匀的吸收。
②被涂面粗糙,且不均匀
解决方法:
打磨到位,注意打磨的方向和砂纸牌号的选择,以消除被涂面的粗糙度。
③涂层过烘干或烘干时换气不充分
解决方法:
严格遵守规定的涂层烘干条件,烘干室换气要适当。
④喷涂虚雾附着或由补漆造成
解决方法:
按喷涂顺序,确保厚度均匀,减少喷涂虚雾的附着。
⑤抛光的涂层未干透就抛光
解决方法:
抛光工序要在涂层完全干透后再进行。
⑥在高温、高湿或极低温的环境下涂装
解决方法:
控制涂装环境,应在温度湿度合适的环境下进行涂装。
24.丰满度不良涂膜虽然涂得很厚,但从外表看仍然很薄而显得干瘪的现象。
原因:
①使用高聚合度的漆基制的涂料,其本身丰满度差
解决方法:
选用丰满度高的涂料。
②颜料含量少和涂料过稀
解决方法:
选用固体分含量高的涂料,一般溶剂型色漆和清漆的固体份含量应达到45%以上。
4涂面不平滑且吸收涂料
解决方法:
打磨以消除被涂面的粗糙度,使粗糙度≤0.4,涂封底涂料以消除底材对面层涂料的吸收。
25.落上漆雾喷涂过程中漆雾飞溅或落在被涂面或涂膜上(成虚雾状),影响涂膜的光泽和外观装饰性的现象。
如落上异色漆雾则称为漆雾污染。
原因:
1喷涂操作不正确,如喷枪与被涂面的距离太远、喷流与被涂面不垂直等
解决方法:
按规范喷涂操作。
2被涂件之间距离太近
解决方法:
被涂件之间应保留足够距离,以防飞溅。
以汽车车身为例,间距不应小于1.5m。
3喷漆室气流混乱,风速太低(小于0.3m/s)
解决方法:
调整空调送风,保持各喷涂室间的风量平衡,喷涂室的气流应有一定方向,风速在静电喷涂场合不小于0.3m/s,在手工喷涂场合应在(0.4-0.5)m/s。
4需涂装的表面未遮盖
解决方法:
遮盖不需涂装的表面,尤其在喷涂异色漆和进行修补喷涂时。
26.腻子残痕涂层表面刮过腻子的部位产生段痕印或失光等现象。
原因:
①刮腻子部位打磨不足
解决方法:
对腻子部位充分打磨。
②刮腻子部位未涂封底漆,腻子层的吸漆量大,或颜色与底涂层不同
解决方法:
在刮腻子部位涂封底漆。
③所用腻子的收缩性大,固化后变形
解决方法:
选用收缩性小的腻子,硝基腻子收缩性大,只适宜于填平砂眼之类缺陷。
27.鲜映性不良涂层的鲜映性(平滑性、光泽)不良的现象,也就是涂层的装饰性差。
原因:
①被涂物表面的平整度差
解决方法:
提高加工精度,防止储运过程中磕碰伤,保证被涂件表面质量达到技术要求。
②所选用涂料的展平性差,光泽差和细度不达标
解决方法:
选用展平性好,细度和光泽优良的涂料。
③涂装环境差,涂层表面产生颗粒
解决方法:
改善涂装环境,高装饰性涂料的涂装宜在有空调除尘的喷漆室中进行,涂层干燥场所(或烘干室)的空气应无尘。
④喷涂工具不好,施工粘度及溶剂选用不当,喷涂时涂料雾化不良,涂面的桔皮严重
解决方法:
选用雾化性能好的喷涂工具和方法及合适的施工粘度,使涂料达到最佳的雾化效果。
⑤涂层厚度不足,丰满度差
解决方法:
高装饰性涂层一般多采用多层涂装体系,增加涂层厚度,以提高涂层的丰满度和平滑性。
28.修补斑印修补部位与原涂面的光泽、色相有差别的现象。
原因:
①修补涂料与原涂料的光泽和颜色不同,或修补涂料较原涂料的耐老化性(如耐侯性)差
解决方法:
应使修补涂料的颜色、光泽和耐老化性应与原涂料尽可能地接近,最好仍采用原工艺和原涂料。
②被修补部位打磨不良而产生光泽不均
解决方法:
按工艺要求打磨被修补部位。
5局部修补而造成
解决方法:
应将修补面扩大到明显的几何分界线处。
29.渗色因面漆层内的溶剂溶解了底层漆,使两层漆之间部分互溶,从而使面层漆呈现不均匀的杂色现象。
原因:
1底层漆被面层漆溶剂溶解,底层漆色浮泛在面层漆上;或涂料中含有易渗色的颜料和有机染料。
解决方法:
由涂料供应厂家来调整涂料各组分之间的配方。
2底层漆未完全干透,就喷面漆,使底漆、面漆产生互溶
解决方法:
底层漆必须彻底干燥后再喷面漆。
3底层漆表面留有彩色粉笔留下痕迹或龙丹紫等难以清洗的染色
解决方法:
彩色粉笔、龙丹紫等污染了涂膜,必须彻底洗净并磨光后再喷面漆。
4喷枪、刷漆等涂装工具上残留有可溶解的颜料、染料未被洗干净
解决方法:
喷枪、刷漆使用前要彻底洗净污染物后才能使用。
30、斜纹漆点:
油漆没有完全雾化就直接喷涂在工件表面形成的斜条纹状油漆聚集的缺陷。
原因:
由于旋杯被污染或旋杯磨损,造成喷涂形状不均匀。
解决方法:
清洗静旋杯并检查旋杯状态,保持旋杯干净,旋杯工作状态正常。
31.局部漆点:
油漆没有完全雾化就直接喷涂在工件表面形成的圆形油漆聚集的缺陷。
原因:
由于供应油漆压力过高或齿轮泵先于喷枪打开,造成在开枪时油漆不能充分雾化。
解决方法:
控制油漆供应压力在(6-8)bar之间,并控制齿轮泵晚于喷枪打开时间在100ms。
32、带状色差:
由于颜料在喷涂时分布不均匀而造成的带状云雾,同其他正常区域形成了颜色差异。
原因:
喷涂扇幅偏小或喷涂成形空气增大或不均匀。
解决方法:
控制喷涂扇幅,检查成形空气管路并清洗成形空气罩,保证成形空气的均匀稳定性。
33、漆膜单薄:
由于油漆吸附率低下造成的漆膜过薄现象。
原因:
喷涂时无高压或高压不足,或工件电阻较大,降低油漆吸附率。
解决方法:
①检查高压发生器的连接电缆,保证连接良好。
②清洗滑橇和格栅,保证工件的接地电阻在控制范围内。
34.钣金凹凸:
钢板结构件(如车身外观件)由于冲压钣金加工不良及储运、焊装过程中产生凹凸不平,影响涂层外观的装饰性的现象。
由点焊产生的坑称为点焊坑;冲压时产生的小的凹凸,在涂装后残留在涂面上且更显眼,称为星状不平。
原因:
①模具的精度不够或手工成形,钢板表面不平,有划痕线等。
解决方法:
提高模具精度,用模具成形代替手工钣金成形,检查钢板表面的平整度和清洁度。
②钢板表面有尘埃,冲压工场环境较差,如在冲压时,模具或钢板上附着有小砂粒,产生凹凸不平的形状;
解决方法:
控制冲压工场的环境,防止砂粒等污物附着在模具上或钢板上。
③储运和组装过程中保护不好,产生碰伤,造成凹凸不平
解决方法:
①加强管理,防止碰伤;
②用烫锡、锉平等修整工序来消除钣金件表面的凹凸不平和点焊坑,或以胶代替焊减少和消除点焊坑;
③或者使用刮腻子填平(此属消极方法)。
35.遮盖痕迹:
遮盖用的胶带痕迹照原样残留在涂面上,或分色线呈锯齿形状,超过工艺标准规定的现象。
原因:
①胶带的质量差;
解决方法:
选用涂装专用胶带,在烘干场合胶带应耐热。
②遮盖工序执行不认真;
解决方法:
按工艺要求认真遮盖,为确保分色线无锯齿,应选用边端整齐的胶带。
③涂膜未干就撕下胶带或其他遮盖物;
解决方法:
涂膜干(至少表干)后才撕下胶带或其他遮盖物。
36.接触伤痕、划碰伤、笔划痕:
涂层受外界作用产生伤痕,失去完整性的现象,在涂层未干前因胶管、手等接触留下的伤痕成为接触伤痕;被涂物在储运和装配过程中因划碰造成的干涂膜的损伤成为划痕伤;用笔作标记在涂面上留下的痕迹成为笔痕迹。
原因:
①湿涂膜受外界作用,完整状态被改变。
解决方法:
涂层未干前严禁外物接触;
②干涂膜受机械划碰。
解决方法:
加强被涂物在储运、装配过程中的保护,严禁磕碰,凡挂具(或工位器具)与被涂物接触部位,应有软化保护,在装配过程中涂层面要加保护罩保护。
③作标记的笔不符合要求。
解决方法:
用笔(如粉笔)在涂装前的被涂物上作的标记,在预清理时一定要除净。
涂层上严禁用普通的笔或粉笔作标记。
37.色差:
刚涂装完的涂膜的色相、明度、彩度与标准色板有差异,或在补涂装时与原漆色有差异。
原因:
1所用涂料各批之间有较大的色差。
解决方法:
加强涂料进厂检验。
2在更换颜色时,输漆管路未洗干净。
解决方法:
更换颜色时,必须将输漆管路洗干净。
3干燥规范不一致,尤其是在烘干场合。
解决方法:
烘干规范(烘干时间、温度)应严格控制在工艺规定的要求内。
4补漆造成的斑痕。
解决方法:
力争少补漆,如需补漆则将整个部件(或有明确分界线的表面)进行补漆。