电液伺服折弯机数控系统操作手册资料.docx
《电液伺服折弯机数控系统操作手册资料.docx》由会员分享,可在线阅读,更多相关《电液伺服折弯机数控系统操作手册资料.docx(29页珍藏版)》请在冰豆网上搜索。
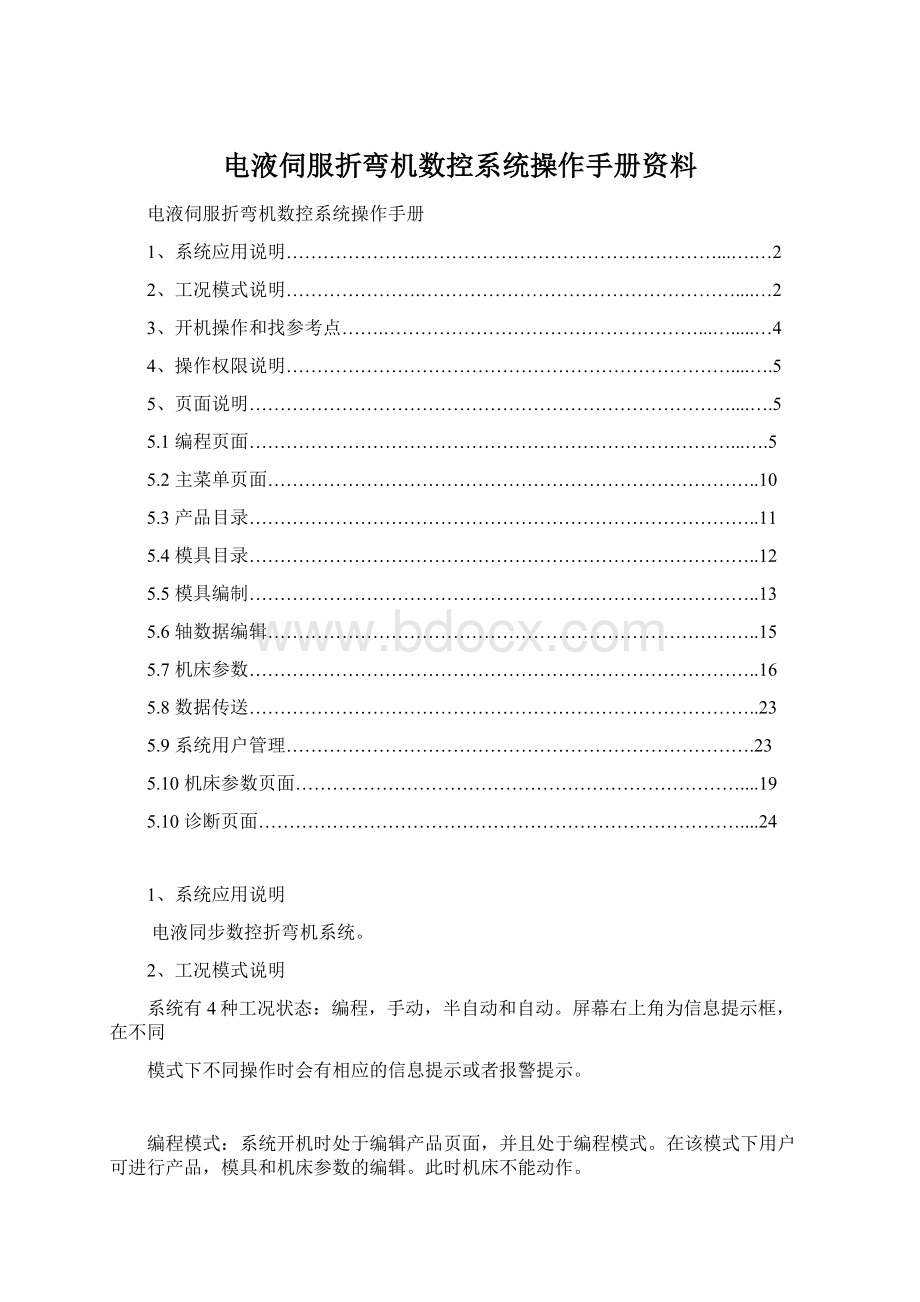
电液伺服折弯机数控系统操作手册资料
电液伺服折弯机数控系统操作手册
1、系统应用说明………………….…………………………………………...….…2
2、工况模式说明………………….……………………………………………....…2
3、开机操作和找参考点…….……………………………………………...….....…4
4、操作权限说明………………………………………………………………....….5
5、页面说明……………………………………………………………………....….5
5.1编程页面……………………………………………………………………...….5
5.2主菜单页面……………………………………………………………………..10
5.3产品目录………………………………………………………………………..11
5.4模具目录………………………………………………………………………..12
5.5模具编制………………………………………………………………………..13
5.6轴数据编辑……………………………………………………………………..15
5.7机床参数………………………………………………………………………..16
5.8数据传送………………………………………………………………………..23
5.9系统用户管理………………………………………………………………….23
5.10机床参数页面………………………………………………………………....19
5.10诊断页面……………………………………………………………………....24
1、系统应用说明
电液同步数控折弯机系统。
2、工况模式说明
系统有4种工况状态:
编程,手动,半自动和自动。
屏幕右上角为信息提示框,在不同
模式下不同操作时会有相应的信息提示或者报警提示。
编程模式:
系统开机时处于编辑产品页面,并且处于编程模式。
在该模式下用户可进行产品,模具和机床参数的编辑。
此时机床不能动作。
手动模式:
机床调试时常用模式,用户可操作某个轴单独运行,以下以手动移动X轴为例,
按“手动”键,进入手动页面
点击“X”,选择X轴
按“+”或“++”,X轴将往加计数方向(后)运行,按“—”或“——”将往减计数
方向(前)运行,“++”和“——”为快速,“+”和“—”为慢速。
速度大小由轴参数决定。
当轴当前值超过最小极限值时,轴将不能朝减计数方向移动,但可以朝加计数方向移动。
当轴当前值超过最大极限值时,轴将不能朝加计数方向移动,但可以朝减计数方向移动。
伺服轴X轴和R轴手动只能单轴操作,不能同时移动两个或两个以上的伺服轴。
滑块手动操作使用外部的脚踏开关。
踩“脚踏下”时,滑块慢下,踩“脚踏上”时,滑块返程。
滑块下行为减计数方向,上行为加计数方向。
自动模式:
机床正常工作时状态。
当编好产品后,系统从编程模式切换到自动模式时,页面出现安全对话信息:
确认油泵、模具等外部信息无误后,点击“确认”键,系统进入“自动”模式页面:
按“启动”键,各伺服轴(包括机械补偿轴)将自动定位到目标值,所以轴到位后踩下“脚踏下”开关,滑块开始下行(大致分快下,慢下和返程阶段),第一个折弯结束后,工步自动转换,页面自动切换到第二个弯头,等待第二次的脚踏开关信号。
如此直到最后一个弯头折完,页面又切换到第一个弯头页面,一个产品才算折弯结束。
半自动模式:
操作同自动模式,只是系统一直运行在当前弯头页面,折弯结束后,工步不转换。
3、开机操作和找参考点
机床开机后正常使用前滑块(Y1/Y2)需要找参考点(手动模式除外),伺服轴X轴,R轴则由系统参数决定。
机床必须在所有需要找参考点的轴找到参考点后才能正常运行。
否则,只能运行在编程模式或者手动模式
找参考点操作:
机床开机后,外部信号齐全(如油泵启动,伺服OK信号)且产品程序编辑正确后,进入“半自动”或者“自动”模式,按“启动”键,各个轴便开始寻找参考点。
屏幕右上角信息提示框将出现“正在找参考点”提示,一般情况滑块会上行寻找参考点,伺服轴会根据系统参数往加计数或者减计数找参考点。
等所有轴找到参考点后,机床便可正常折弯了。
如果哪个轴没有找到参考点,将有对应的信息提示。
操作者可根据提示来调整故障轴,重新寻找。
4、操作权限说明
为保证设备正常的使用及维护,对操作设置了权限密码。
系统最高级别为3。
开机时初
始级别为0。
要更换级别时,点击页面的
键,出现用户级别登录页面:
“用户级别”可选择1、2和3,分别代表级别1、2和3,,密码分别是“111111”、
“222222”和“333333”。
选择所需级别,输入正确密码后,原
键会显示你登录
的用户级别
、
和
。
最后点击“关闭”,退出登录页面。
如果密码输错,将有错误提示,重新输入密码即可。
用户级别越高权限越大。
用户0:
仅翻页及查看一些页面数据。
开机为初始用户
用户1:
包含0,还可编辑产品(保存,删除,调用产品),使用机床。
密码111111
用户2:
包含0,1,还可编辑模具(保存,删除,调用模具)及轴数据编辑。
密码222222
用户3:
包含0,1,2,还可编辑机床参数,系统测试等。
密码333333
注销:
退出到用户0状态。
5、页面说明
5.1编程页面
产品编号:
一个产品的编号,可数字或字母,产品保存、调用或删除时使用。
步序分子:
显示当前第几个折弯,单个产品最多?
个折弯。
步序分母:
显示当前产品的总折弯数,单个产品最多?
个折弯。
上模:
产品的上模编号,可数字或字母。
下模:
产品的下模编号,可数字或字母。
材料:
板材材料,铁、铝和不锈钢,默认对应的抗拉强度分别为42、25和72Kg/mm²。
抗拉强度:
材料的抗拉强度,单位Kg/mm²。
可根据材料选择时自动显示,也可根据实际人
工输入或者修改。
板厚:
板材厚度,数值范围0~99.99,单位毫米。
板长:
折弯板长的长度,数值范围0~9999.99,单位毫米。
角度编程值:
工件折弯角度。
角度校正值:
工件实际折弯角度。
Y1/Y2编程值:
滑块高度的编程值,系统根据上模、下模、板厚和材料等数据自动计算。
Y1/Y2当前值:
通过光栅尺实时反馈滑块高度的当前位置值。
Y1/Y2校正值:
滑块高度的校正值,系统可根据角度校正值自动计算,也可根据实际情况人为输入修改。
X编程值:
后挡料X轴编程值,数值范围0~9999.99,单位毫米。
可选择绝对值编程或相对值编程。
绝对值是以上下合模时的中心线为零位置。
X当前值:
通过伺服编码器实时反馈X轴的当前位置。
X校正值:
X轴的校正尺寸,用于X轴实际位置与当前值不符时调整。
R编程值:
后挡料R轴编程值,数值范围0~9999.99,单位毫米。
可选择绝对值编程或相对值编程。
绝对值是以下工作台面为零位置。
R当前值:
通过伺服编码器实时反馈显示R轴的当前位置。
R校正值:
R轴的校正尺寸,用于R轴实际位置与当前值不符时调整。
压力:
折弯压力,单位吨。
该值由系统自动计算,也可人为输入。
补偿:
工作台补偿量,该值由系统自动计算,也可人为输入。
单步循环:
当前折弯重复的次数,数值范围1~99。
在自动模式下起作用。
开启高度:
也称上死点,指滑块返程时停止的位置值,该值系统自动计算也可人为输入修改。
转速点:
滑块由快下转慢下时的位置值,该值系统自动计算也可人为输入修改。
夹紧点:
滑块进入慢下后,刚触碰到板料时的位置,该值系统自动计算也可人为输入修改。
退让方式/距离:
滑块到达夹紧点时,可选择后挡料是否退让。
退让方式分为“同时”或者“到达”,“同时”指X轴退让和滑块下行同时进行,“到位”指X轴退让时,滑块停止不动,退让到位后,滑块再继续下行。
保压时间:
滑块在下死点保持压力的时间,单位秒。
该数值由系统自动计算也可人工输入。
计件分子:
当前折弯产品数量。
计件分母:
产品目标数量。
轴启动:
指滑块折弯结束时工步转换后,各伺服轴的定位时机。
有3种方式,
上死点,滑块返程到上死点后定位;
下死点,折弯结束后开始返程时就定位;
外部启动,滑块返程到上死点后,踩“脚踏下”开关时再定位。
CR:
大圆弧折弯次数,折弯大圆弧时使用,数值范围1~99。
RI:
大圆弧折弯半径,折弯大圆弧时使用,数值范围0~9999.99,单位毫米。
编新产品:
编辑新产品,将当前页面的有关数据清空,准备开始编辑新产品数据。
加一弯头:
增加一个折弯,同时将当前弯头的数据复制到新的弯头,总弯头个数增加一。
减一弯头:
减少一个折弯,总弯头数减一。
前一弯头:
翻页至前一个弯头数据。
后一弯头:
翻页至后一个弯头数据。
保存:
产品数据编辑正确完整后,设定一个产品编号保存。
用户0:
操作权限,详见上述4、用户权限及操作说明
?
:
进入帮助说明页面。
主要用于给新用户提供编程页面的相关解释说明。
点击任何一项,将出现该项说明信息。
比如点击“板厚1.20”,显示以下窗口:
编辑一个新产品
编辑一个完整的产品至少需要输入:
上模、下模、材料、板厚、板长、抗拉强度、角度、X轴编程值、R轴编程值、压力和补偿。
其中抗拉强度、R轴编程值、压力和补偿由系统自动计算也可根据实际情况人为输入或修改。
另外的单步循环、开启高度、转速点、夹紧点、退让方式及距离、保压时间、计件和轴启动也由系统自动计算并可人为输入修改。
以下举例编一个3个弯头的产品。
在编程页面,点击“编新产品”,清空当前页面数值
输入相关数值:
上模、下模、材料、板厚、板长、抗拉强度、角度、X轴编程值、R轴编程值、压力和补偿。
点击“加一弯头”,弯头数增加为2,“当前弯头”显示第2弯头,开始编辑第二个弯头,输入相关数据,此处输入角度100°,X轴编程值300.00,第二个弯头编辑完成。
再点击“加一弯头”,弯头数增加为3,“当前弯头”显示第3弯头,开始编辑第三个弯头,输入相关数据,此处输入角度120°,X轴编程值400.00,第三个弯头编辑完成。
此时切换到“半自动”或者“自动”状态,便可以正常生产了,也可以输入一个产品号,点击“保存”,来保存产品。
编程方式:
产品编辑时有两种编程方式,数据编程和图形编程,上述编程为数据编程,以下为图形编
程页面:
图形编程主要根据成品外形输入长度(外形包边长度),角度及其它信息,同时生成相应的图形信息,在半自动或自动模式下运行时,根据折弯顺序同步显示。
如自动模式下:
5.2主菜单页面
按“菜单”键,进入系统主菜单,显示系统各个单元。
5.3产品目录
显示已经保存的产品,在该页面可对产品进行调取编辑或者删除操作。
以调取产品编号3为例,点击3号产品:
点击“调取”键,即打开3号产品。
5.4模具目录
‘
显示已经保存的模具,在该页面可对模具进行调取、编辑或者删除操作。
以删除16号下模为例,点击16号下模:
点击“删除”键,出现确认对话框:
点击“确认”键,操作完成。
5.5模具编制
编辑产品前需要先编辑模具(上模和下模数据)并保存。
编辑上模时输入:
上模编号:
数字范围1~99,编号不能为0,也不能重复。
在保存,删除和调用时使用。
角度:
上模模尖的角度,数值范围0~179.99°,单位度。
高度H1:
上模模尖到上滑块底面的距离,数值范围0~9999.99,单位毫米。
倒角:
上模模尖的倒角圆弧半径,数值范围0~99.99,单位毫米。
线性力:
上模单位距离可承受的压力,数值范围0~999,单位吨/米。
操作键选择“上模”,再点击“保存”键,完成保存。
上模编号不能重复,如已存有同编号
上模,出现对话框:
选择“确认”,将覆盖同编号上模,选择“取消”,关闭对话框。
编辑下模时输入
下模编号:
数字范围1~99,编号不能为0,也不能重复。
在保存,删除和调用时使用;
槽宽V:
下模开口的距离,数值范围0~9999.99,单位毫米。
角度:
下模开口的角度,数值范围0~179.99°,单位度。
高度H2:
下模上平面到下工作台平面的距离,数值范围0~9999.99,单位毫米。
倒角:
下模槽口的倒角圆弧半径,数值范围0~99.99,单位毫米。
线性力:
下模单位距离可承受的压力,数值范围0~999,单位吨/米。
操作键选择“下模”,再点击“保存”键,完成保存。
下模编号不能重复,如已存有同编号
下模,出现对话框:
选择“确认”,将覆盖同编号下模,选择“取消”,关闭对话框。
安全距离Xs:
后挡指到上下合模中心线的距离,数值范围0~9999.99,单位毫米。
设置该安全参数,为防止后挡指撞到模具。
5.6轴数据编辑
轴数据编辑主要是对各个轴的当前值进行修改编辑,一般在调试机床时使用。
如上图X轴当前值显示为405.00MM,如果实际位置为408.00MM,可在其前面直接输入408.00,便可修改完成。
5.7机床参数
机床参数用于控制机床动作运行,为调试机床时使用,为重要的数据。
包括:
“机床配置”、“滑块参数”、“压力补偿参数”、“轴参数”、“”I/O配置“”和“辅助参数”。
机床配置
机床配置是根据机床实际配置情况对各轴端口进行定义配置,如上图“轴1”到“轴4”分别配置了“Y1”、“Y2”、“X”、和“R”。
“小数位”是定义该轴在工作页面数值显示的小数位数,有0.01、0.1和0位可供选择。
轴1:
Y1轴指机床滑块左侧(面对机床),由比例阀驱动运行,光栅尺反馈位置。
当滑块接触至下工作台表面时为0位置,数值越大,位置越高。
激活了该轴,每次开机机床必须要先找参考点。
轴2:
Y2轴指机床滑块右侧(面对机床),由比例阀驱动运行,光栅尺反馈位置。
当滑块接触至下工作台表面时为0位置,数值越大,位置越高。
激活了该轴,每次开机机床必须要先找参考点。
轴3:
X轴指控制后挡指前后方向运行的轴,上下合模时,以下模槽口中心为0位置,数值越大,越靠后。
激活了该轴,该轴开机找参考点功能由该轴轴参数决定。
轴4:
R轴指控制后挡指上下方向运行的轴,以下工作台面为0位置,数值越大,位置越高。
激活了该轴,该轴开机找参考点功能由该轴轴参数决定。
如果在这个页面关闭了某个轴,那么该轴的功能也将关闭,同时相关的页面将不再显示该轴信息,相关页面有:
编程页面,手动页面,半自动页面,自动页面和轴位置编辑页面。
滑块参数
滑块参数主要是控制机床滑块的运行曲线。
在手动模式下,滑块下行时全程慢速。
在自动或者半自动模式下,滑块运行大致分为快下,慢下,折弯,保压,泄压和返程。
具体过程:
最初滑块停在上死点,踩下“脚踏下”开关后,滑块快速下行至转速点,进入慢下阶段,接触到板材,开始折弯,直到下死点,并且保压一定时间,开始卸荷,然后滑块自动返程至上死点停止。
具体参数作用详见滑块参数说明。
压力补偿参数
机床的主压力通过系统其中一路模拟量输出端口输出0~10V的电压量再通过外置的放大器转换为电流量来控制比例压力阀,从而实现压力控制的。
机床吨位:
指机床的最大吨位。
压力比例曲线:
指机床不同压力下对应的电压输出。
100%对应的电压输出对应机床最大吨位。
压力曲线的数值可通过以下操作来获得:
机床接入压力表,油泵启动后,进入该页,选择“压力”
选择其中一项百分比电压数值,按“——”,“—”,“+”或“++”键,来控制电压输出,数值同时呈递增或递减(“+”,“++”分别递增0.01V,0.1V,“—”,“——”分别递减0.01V,0.1V)变化,当压力表示数达到百分比压力值时,此时的电压值就是该点的数值。
其它百分比电压数值也按同样方法获得。
补偿方式:
机床可以配置补偿也可以不配置补偿,当配置补偿时,补偿有两种方式:
一为液
压补偿,原理类似压力控制,输出0~10V的电压量通过外置的放大器转换为电流量,来控制
比例阀。
另外一种是机械补偿,通过两路数字量输出“机械补偿正转”和“机械补偿反转”(
在系统机床参数的I/O配置-输出里面配置)来控制机械补偿电机的正反向运转,从而达到
补偿效果,同时一路模拟量输入接口外接电位计,实时反馈补偿位置。
“补偿方式”选择“液
压”液压时,页面如下:
最大补偿量:
指液压补偿的最大变形量,单位0.01MM
液压补偿曲线:
指机床不同补偿下对应的电压输出。
100%对应的电压输出对应最大补偿量。
补偿曲线的数值获得方式同压力。
“补偿方式”选择“机械补偿”时,页面如下:
最大补偿量:
指机械补偿的最大变形量,单位0.01MM
补偿允差:
补偿电机定位允差。
机械补偿曲线:
指机床不同补偿下对应的DA值输出。
100%对应的DA值输出对应最大补偿量。
补偿曲线的数值获得方式同上。
电位计端口:
即反馈电位计的输入接口,可选择模拟量1和模拟量2,
当前值:
即电位计的反馈的当前位置DA值。
轴参数
轴参数是伺服轴控制运行参数,
编码器分辨率:
电机编码器的分辨率。
计数方向\电机转向:
电机编码器的计数方向,和实际电机转向。
加速时间:
电机从零加速至正常速度时的所需时间。
减速时间:
电机从正常速度减速至停止所需的时间。
定位允差:
电机定位与目标值的允许差值。
定位速度:
电机正常运行时的速度。
手动慢速:
手动控制时的慢速。
手动快速:
手动控制时的快速。
寻参方式:
开机寻找参考点方向可加计数或减计数方向,也可关闭,不找参考点。
寻参速度:
寻找参考点时的速度。
找参考点速度:
机床找参考点时的速度。
参考点位置:
参考点的设置位置,由所安装的开关位置决定。
最小极限:
轴能运行的最小位置。
最大极限:
轴能运行的最大位置。
I/O配置
系统的16路数字量输入为通用通道,可任意分配定义,但不能重复定义。
例如“01”脚可定义为“油泵启动”,也可定义为“自动”,但不能同时定义两个“油泵启动”信号。
同时每个脚位的“状态”能显示该脚位的外接信号是否已接通或关闭。
常用的输入信号说明:
油泵启动完毕:
机床油泵启动完毕后输出给系统的信号。
一旦配置该信号,必须要一直保持,
否则机床无法运行,并提示报警。
脚踏下:
脚踏开关下行信号。
脚踏上:
脚踏开关上行信号。
返回最大上死点:
指给滑块返程到最大极限的信号。
上死点:
指给滑块返程到上死点的信号。
系统的16路数字量输出为通用通道,可任意分配定义,但不能重复定义。
脚位的“状态”显示了该脚位是否有正常输出。
常用的输出信号说明:
滑块快下:
滑块快下时输出的信号,在慢下时依然保持。
滑块慢下:
滑块慢下时输出的信号。
滑块返程:
滑块返程时输出的信号。
上死点:
滑块到达上死点时输出的信号。
转速点:
滑块到达转速点时输出的信号。
夹紧点:
滑块到达夹紧点时输出的信号。
下死点:
滑块到达下死点时输出的信号。
折弯结束:
滑块折弯结束(保压结束)时输出的信号。
机械补偿正向:
机械补偿正向运行时输出的信号。
机械补偿反向:
机械补偿反向运行时输出的信号。
辅助参数
该页面主要是系统辅助功能的参数。
产品计数方式:
对折弯产品计数,可加计数或者减计数,在“自动”模式有效。
计数到达停止:
折弯数量到达时,可选择是否要停止并提示。
安全距离:
后挡料X轴R轴运行到此区域内,按安全轨迹运行。
折弯系数:
滑块目标值的影响因素之一。
5.8数据传送
数据传送页面主要用于数据备份维护。
当机床调试完成后,维修人员可以把机床参数,模具数据和产品数据下载到外部设备,也可以将备份好的数据上传到系统。
数据“传送方式”的媒介可以选择系统内部、U盘、SD卡、CF卡或者移动硬盘。
例如要把系统的机床参数备份到外部的U盘,“项目”选择“机床参数”:
“传送方式”选择“系统内部”—>“U盘”,点击“传送”便可完成。
如果要将系统数据全部清空,可点击“系统初始”,便可恢复到系统的出厂设置。
5.9系统用户管理
上述所说的3级操作权限各有各的密码,当需要修改以上密码时,可在该页面操作,进入该页面后,输入系统管理员密码:
140626,点击“确认”,打开权限级别密码修改页面:
q
输入要修改的级别新密码,点击修改框内的“确认”键,再点击“关闭”退出即可完成!
5.10诊断页面
“系统诊断”页面主要针对系统本身的软硬件进行诊断测试。
分为键盘检测,数字量检测和模拟量检测。
键盘检测:
键盘检测主要对系统硬件部分的键盘进行检测,按下任一个系统按键,屏幕上对应的按键应该有相应的显示才算正常,否则视为故障。
数字量检测
数字量检测分为“数字量输入监控”和“数量输出开关”两部分。
“数字量输入监控”是对系统的16路数字量输入脚位进行检测。
当脚位为低电平时,该脚位“状态”显示为“0”,当有高电平输入时,该脚位“状态”显示为“1”,该脚位即为正常,否则视为故障。
“数字量输出开关”是对系统的16路数字量输出脚位进行检测。
当脚位没有输出时,该脚位“状态”显示为“0”,当“置位”为“ON”时,即有输出,“状态”显示为“1”(如上图输出08脚)。
即为正常,否则视为故障。
模拟量检测
模拟量检测分为“模拟量输入监控”,“模拟量输出开关”和“编码器计数监控”。
“模拟量输入监控”是对系统2路模拟量输入进行检测。
脚位定义:
模拟量输入一,01、02和03,其中01和03脚位为电源,02脚位接电位计采样信号;模拟量输入二,04、05和06,其中04和06脚位为电源,05脚位接电位计采样信号。
当接入电位计时,对应采样信号脚位02或者04的“状态”显示数值会随电位变化而变化。
数值变化范围0~255。
“模拟量输出开关”是对系统6路模拟量输出(Y1、Y2、X、R、压力和补偿)进行检测。
打开对应的通道脚号,如图打开模拟量R轴,点击“+”键或者“++”键,“状态”显示电压数值将变大。
单次点击“+”或“—”,数值量变化为0.01V,“++”或“——”为0.1V。
变化范围0~9.99V。
“编码器计数监控”是对系统编码器接口(Y1、Y2光栅尺接口,X、R伺服轴编码器接口)
进行检测。
当光栅尺或电机运行时对应轴“状态”显示的数值有相应正常的变化,当到达参考点时,“参考点”数值将跳变至事先设定的数值。