多晶硅制备说明书.docx
《多晶硅制备说明书.docx》由会员分享,可在线阅读,更多相关《多晶硅制备说明书.docx(25页珍藏版)》请在冰豆网上搜索。
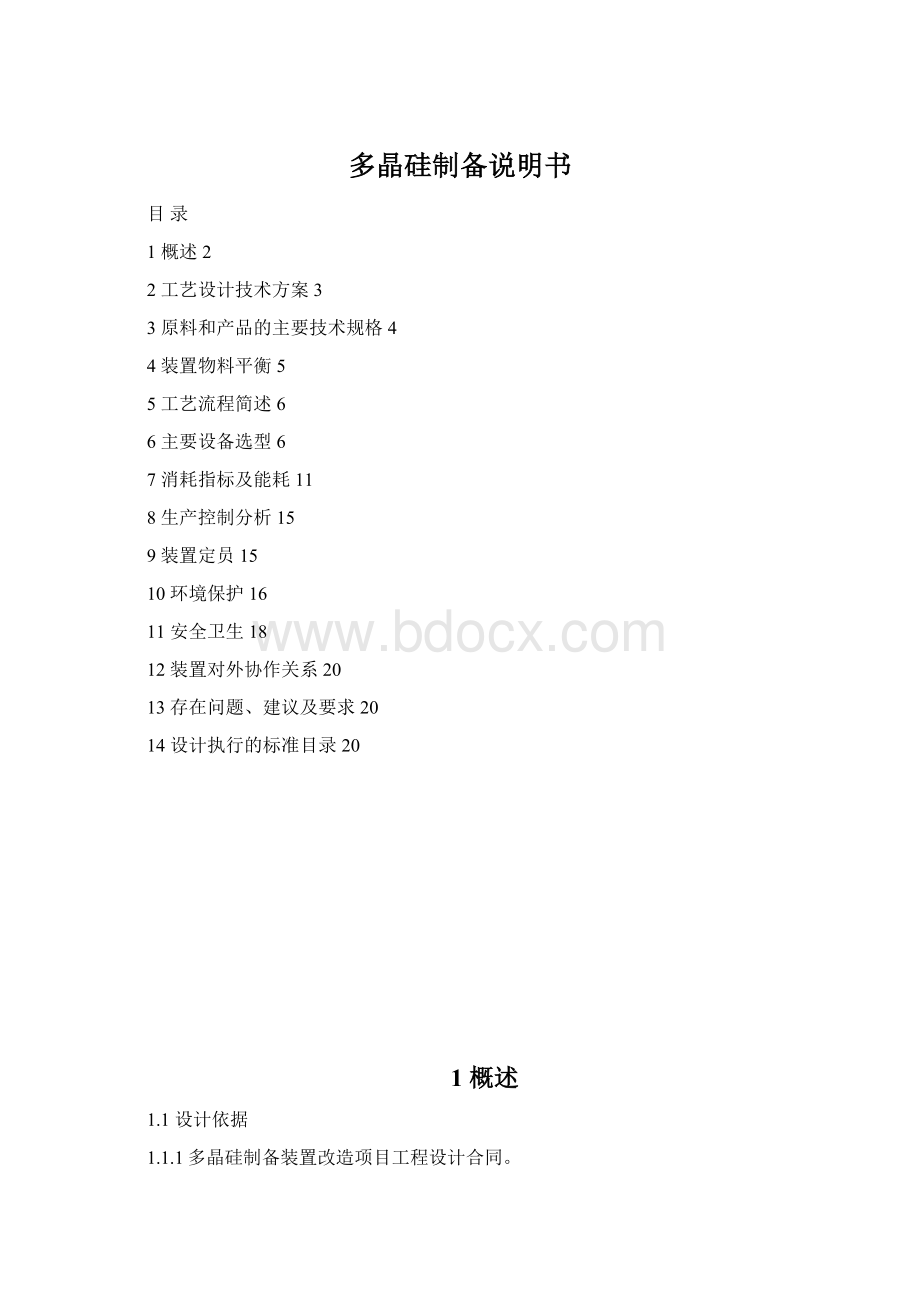
多晶硅制备说明书
目录
1概述2
2工艺设计技术方案3
3原料和产品的主要技术规格4
4装置物料平衡5
5工艺流程简述6
6主要设备选型6
7消耗指标及能耗11
8生产控制分析15
9装置定员15
10环境保护16
11安全卫生18
12装置对外协作关系20
13存在问题、建议及要求20
14设计执行的标准目录20
1概述
1.1设计依据
1.1.1多晶硅制备装置改造项目工程设计合同。
1.1.2关于多晶硅制备装置等问题的传真及相关文件。
1.2装置概况
1.2.1建设性质:
新建
1.2.2建设规模
装置设计规模:
制备太阳能多晶硅100t/a;年开工时间8000小时。
操作弹性为50~100%。
1.2.3装置组成及名称
该装置由原料精制部分、多晶硅还原部分、尾气处理部分以及产品后处理部分组成。
1.2.4设计原则
a)采用成熟可靠的先进技术,力求做到技术新、投资省,操作可靠。
b)尽量采用“清洁工艺”,确保污染物排放符合环保要求,减少环境污染。
c)严格遵循现行的有关安全法规,采取各种切实可靠、行之有效的事故防范及处理措施,确保装置安全生产。
d)贯彻“安全第一,预防为主”的方针,确保新建装置符合安全卫生要求。
1.2.5设计范围
该装置的设计范围为新建100t/a多晶硅制备界区内的工程,新建控制室及变配电室,公用工程系统新建。
1.2.6装置的主要产品
本装置的产品为:
太阳能级多晶硅。
1.2.7产品去向
太阳能级多晶硅工厂储存及汽车外运。
2工艺设计技术方案
2.1工艺技术路线
本项目改用的多晶硅制备工艺为目前国际上流行的改良西门子工艺,主要有三氯氢硅原料精制、三氯氢硅氢还原制备多晶硅、还原尾气回收利用以及相配套的辅助工艺和公用工程组成,确保获得纯度高、质量好的多晶硅产品,同时解决传统西门子法生产过程中产生的大量的氢气、氯化氢、四氯化硅等副产物造成的物料浪费,并由此带来的严重污染和多晶硅生产中大量的水耗、电耗等问题。
2.2.工艺技术特点
2.2.1多晶硅制备采用改良西门子工艺,实现了物料的闭路循环和能量的综合回收利用。
2.2.2改良的三氯氢硅提纯工艺,有效的分离三氯氢硅中的磷硼和金属杂质。
2.2.3三氯氢硅还原过程中产生的尾气通过冷冻吸收、活性炭吸附的特殊手段实现了各组分的回收和利用。
2.2.4三氯氢硅还原采用先进的还原炉,降低了多晶硅的电单耗。
2.2.5设置了开工油锅炉,为开车提供能量。
2.2.6采用导热油循环系统,实现了还原过程中产生热量的回收利用。
2.2.8仪表控制采用DCS控制系统。
2.2.9采用目前国内最成熟的还原供电装置。
2.2.10除关键设备及分析仪表引进外,其他均立足国内。
3原料和产品的主要技术规格
3.1原料性质
性能名称
SiCl4
SiHCl3
SiH4
分子量
169.2
135.4
32.092
密度(液体)g/cm3
1.49
1.318
0.68
沸点℃
57.6
31.5
-111.8
密度(蒸汽)g/cm3
0.0063
0.0055
熔点℃
-70
-128
-185
标准生成热千卡/摩尔
-1540
-105.7
-148
蒸发热千卡/摩尔
0.96
6.36
92.2
标准生成自由能千卡/摩尔
-136.9
-96.58
-9.4
发火点℃
28
空气中自然爆炸
化合物中硅的含量%
16.6
20.9
87.5
物理状态(常温)
无色透明液体
无色透明液体
爆发性无色气体
3.2产品性质
3.2.1多晶硅
性质
数量
性质
数量
原子量
28.08
本征载流子溶度
1.5×1010cm2/v·s
原子密度
5.0×1022原子/cm3
硅单晶本征电阻率
230000Ω·cm
密度
2.33克/cm3
界电常数
11.7±0.2
结构检查
金刚石型晶格
沸点
3145℃
晶格常数
5.42Å
熔点
1416±4℃
禁带宽度
1.115±0.008eV
临界温度
4920℃
电子迁移率
1350±100cm2/v·s
比热(18-100℃)
0.186卡/克·度
比热
0.219卡/克·度
表面张力
720达因/厘米
蒸发热
71千卡/摩尔
硬度
7.0莫氏硬度
升华热
(18+2)×103焦耳/克
折射率
3.420
熔解热
12.1千卡/摩尔
凝固时的膨胀
±10%
溶解潜热
425±64卡/克
线性热胀系数
(2.6±0.3)×10-6/℃
热传导率
0.3卡/秒·厘米·度
临界压力
1450大气压
空穴迁移率
480±15cm2/v·s
4装置物料平衡
装置物料平衡(正常工况)见表4-1。
表4-1物料平衡表
项目
Kg/h
t/a
入方
1、三氯氢硅
227.27
1800
2、氢气
2.7
21.4
出方
1、多晶硅
12.63
100
2、四氯化硅
164.14
1300
5工艺流程简述
5.1工艺流程简述
5.1.1三氯氢硅提纯工艺简述
5.1.1.1“改良西门子法”三氯氢硅提纯工艺特点
相对于传统西门子法三氯氢硅提纯工艺采用常压操作,改良西门子法三氯氢硅提纯工艺采用加压操作,经过B、P等分离效果的比较,分离BCl3用加压塔比常压塔有明显的优势,在加压条件下,BCl3等低沸点氯化物在每块塔板上富集系数及富集率比常压条件下高,BCl3在塔顶几乎全部除净。
分离PCl3则加压塔与常压塔的效率无明显差异。
因此,除精馏2#塔采用常压塔外,其余均采用加压塔。
5.1.1.2三氯氢硅提纯工艺原理
三氯氢硅提纯操作是利用原料中各组分挥发度的差异而使之分离的一种操作。
通过提纯塔把三氯氢硅、四氯化硅、及其它杂质氯化物的加热至沸腾,挥发度高的组分,即低沸点的组分(例如三氯氢硅),在气相中的浓度比液相中高,同理,将混合液的蒸汽冷凝,冷凝液中难挥发的组分,即高沸点组分(例如四氯化硅),在液相中的浓度比液相中高;经过多次部分汽化或部分冷凝,最终在气相中得到较纯的易挥发组分,即沸点低的组分(例如三氯氢硅),在液相中得到较纯的难挥发组分,即高沸点组分(例如四氯化硅)。
挥发度通常是用以表示某种纯态物质在某一温度下蒸汽压的大小。
当组分互溶时,各组分的挥发度用它们蒸汽压中的分压和在蒸汽中成平衡的液相中的摩尔分数之比来表示。
5.1.1.3三氯氢硅提纯工艺描述
1)合成粗馏:
三氯氢硅合成料、精馏高低沸物料经过合成粗馏1#塔、合成粗馏2#塔两塔连续提纯,控制一定的温度、压力、回流比,合成粗馏1#塔塔顶出低沸物,送往低沸物贮罐,塔釜出中间产品(三氯氢硅、四氯化硅、部分高沸点杂质)进入合成粗馏2#塔,合成粗馏2#塔塔顶出三氯氢硅粗馏产品,送往精馏进一步提纯,塔釜出高沸物,送往氢化工序。
2)合成精馏:
合成粗馏产品、氢化粗馏产品经过精馏1#塔、精馏2#塔两塔连续提纯,控制一定的温度、压力、回流比,精馏1#塔塔顶出低沸物,送往合成粗馏,塔釜出中间产品(三氯氢硅、四氯化硅等)进入精馏2#塔,精馏2#塔塔顶出精馏产品,送往还原工序,塔釜出高沸物,送往合成粗馏。
3)干法精馏:
干法料经过干法精馏1#塔、干法精馏2#塔两塔连续提纯,控制一定的温度、压力、回流比,干法精馏1#塔塔顶出低沸物,送往低沸物贮罐,塔釜出中间产品(三氯氢硅、四氯化硅等)进入干法精馏2#塔,干法精馏2#塔塔顶出干法精馏产品,送往还原工序,塔釜出高沸物,送往氢化工序。
5.1.2干法回收工艺简述
5.1.2.1采用干法回收工艺的意义
“传统西门子法”还原尾气回收是“湿法回收”,即还原尾气中没有反应的三氯氢硅、氢气和反应过程中生成的氯化氢、四氯化硅、二氯二氢硅等气体,经过-80℃冷却装置,三氯氢硅、四氯化硅冷凝为液体后回收利用,不凝的氢气、氯化氢及少量的氯硅烷再经过水洗喷淋,氯化氢和少量的氯硅烷被水溶解带走,氢气再经过纯化干燥后重新利用。
“改良西门子法”还原尾气回收过程中物料不接触水,相对于“传统西门子法”的“湿法回收”而言,称之为“干法回收”。
干法回收主要是利用还原尾气中氢气、氯化氢、三氯氢硅、四氯化硅、二氯二氢硅等各组分物理化学性质的差异,通过溶解吸收,吸收—脱吸,吸附—脱附等化工操作实现各组分的分离,并重新利用。
由于“湿法回收”中采用水洗来除去氢气中氯化氢、氯硅烷,在损失氯化氢、氯硅烷同时,增加了废水的处理量,并且水分及水中、空气中的杂质进入到氢气中,污染了氢气,必须另外采用氢气纯化干燥装置将其纯化干燥后才能重新返回系统利用。
湿法回收工艺消耗大、收率低,从而增加了整个多晶硅生产的成本。
采用干法回收工艺,还原尾气中的各组分几乎可以100%分离回收,由于整个系统是闭路循环,不引入新的污染源,故回收各组分品质稳定,可直接返回系统重新利用,从而提高了收率,减少了消耗。
5.1.2.2干法回收工艺原理
还原尾气干法回收主要包括:
鼓泡淋洗、加压冷凝、吸收脱吸、活性炭吸附四个主要工艺过程,每个过程的原理如下:
1)鼓泡淋洗:
利用四氯化硅在一定温度下对还原尾气中个组分溶解度的不同,通过鼓泡淋洗塔对还原尾气淋洗,溶解度大的三氯氢硅、四氯化硅绝大部分被溶解吸收,溶解度小的氢气、氯化氢二氯二氢硅便分离出来。
2)加压冷凝:
从鼓泡淋洗塔出来的不溶性气体,里面含有少量的三氯氢硅、四氯化硅,在常压下把其冷凝出来需要大量的冷量和很低的冷却温度,采取加压冷凝的办法,三氯氢硅、四氯化硅可在较高的温度下按照相平衡的规律几乎全部冷凝下来,同时大大减少冷媒的用量。
3)吸收脱吸:
吸收脱吸是分离气体混合物的一种重要方法,吸收过程实际上是气相组分在液相中溶解的过程,各种气体在液体中都有一定的溶解度,当气体和液体接触时,气体溶解到液体中的浓度逐渐增加至饱和为止;被溶解的气体叫溶质,溶解气体的溶液叫溶剂或吸收剂。
当溶质在气相中的分压大雨它在液相中饱和蒸汽压时,此压力差即为吸收过程的推动力,当压差等于零时,过程达到平衡,如果条件相反,溶质从液相转入气相,即为脱吸过程。
加压冷凝后的不凝气体主要是氢气、氯化氢、二氯二氢硅,采用四氯化硅作为吸收剂,其中大量的氯化氢、二氯二氢硅在加压低温条件下被四氯化硅溶解吸收,氢气分离出来。
被四氯化硅溶解吸收氯化氢、二氯二氢硅在脱吸塔中控制一定温度和压力下,二氯二氢硅以液态、氯化氢以气态分别从四氯化硅中分离出来。
4)活性炭吸附:
吸附作用是一种发生在相间的表面现象,有物理吸附和化学吸附,或两者兼而有之。
物理吸附又称范德华吸附,因为吸附剂是通过范德华力将吸附质吸引覆盖在表面上,而且可以形成多分子层,对不同的物质吸附能力不一样。
吸附速度快,容易达到平衡,吸附热较小,与气体的液化热相近,且吸收质与吸收剂不发生化学反应。
在一定条件下吸收质从吸附剂表面脱离返回气相或液相主体保持原来的分子结构,此为吸附的逆过程:
脱附。
活性炭吸附为物理吸附,从吸收-脱吸系统中分离出来的氢气中含有微量的氯化氢、氯硅烷等,通过活性炭吸附器吸附,氯化氢、氯硅烷等大分子物质首先被吸附下来,从而净化了氢气。
可以通过时间程序控制,吸附饱和后的活性炭进行脱附再生,控制一定的温度并通氢气吹赶,被活性炭吸附的氯化氢、氯硅烷等可以脱附出来,从而实现了活性炭吸附器重复利用。
5.1.2.3干法回收工艺描述
来自还原车间的(H2、SiHCl3、SiCl4、HCl、SiH2Cl2),经过鼓泡气-气换热器冷却后,进入鼓泡淋洗塔,用氯硅烷循环屏蔽泵输送的低温氯硅烷鼓泡淋洗,还原尾气中大部分三氯氢硅、四氯化硅绝大部分被溶解吸收后,返回氯硅烷贮罐供氯硅烷循环屏蔽泵循环使用,富余氯硅烷通过氯硅烷输送泵送往干法精馏工序。
鼓泡淋洗塔中不被吸收的气体,经过还原尾气压缩机压缩,压力由常压升至0.6MPa,经过压缩气-吸收气换热器、压缩气过冷气冷却后,冷凝下来的氯硅烷返回氯硅烷贮罐,不凝的低温气体进入吸收塔,其中绝大部分SiHCl3、SiCl4、HCl、吸收塔内低温四氯化硅(贫液)吸收下来,吸收了氯硅烷、HCl的四氯化硅称为富液,进入富液贮罐。
通过富液屏蔽泵输送,富液经过三级贫富液换热器、二级贫富液换热器、一级贫富液换热器与贫液换热升温后,进入脱吸塔,控制一定温度(塔釜144℃)和压力(塔顶0.8MPa),氯化氢以气态进入缓冲罐,返回三氯氢硅合成系统重新利用,SiH2Cl2以液态进入缓冲罐,然后进行处理和外卖。
脱吸以后的四氯化硅称之为贫液,温度144℃,经过贫液水冷器、一级贫富液换热器、二级贫富液换热器、三级贫富液换热器、贫液过冷器降温到-50℃,进入吸收塔重新使用。
吸收塔内不被吸收的气体主要是氢气,其中含有微量的氯硅烷、氯化氢,为进一步净化氢气,采用活性碳吸附器吸附氢气中的杂质;三个活性炭吸附器通过时间程序控制,分别进行吸附、再生、降温。
在吸附过程中,活性炭吸附下氢气中的量的氯硅烷、氯化氢杂质,通过带式过滤器过滤掉碳粉后,送到100方纯氢储罐,供还原等工序使用。
再生过程为对吸附饱和的活性炭吸附器加热、通氢气吹赶,氯硅烷、氯化氢随氢气经滤器过滤掉碳粉后重新返回鼓泡淋洗塔鼓泡淋洗。
降温过程是对再生后高温(190℃)活性炭吸附器通冷导热油降温。
5.1.2.4主要经济技术指标
1)氢气回收率:
~100%
2)氯硅烷回收率:
~100%
3)氯化氢回收率:
~100%
5.1.3多晶硅还原工艺简述
5.1.3.1多晶硅还原工艺原理
三氯氢硅在纯氢气的还原条件下,在1050℃的硅芯发热体表面沉积生长多晶硅,其主要的反应方程式为:
SiHCl3+H2=Si+3HCl↑
4SiHCl3=Si+3SiCl4+2H2↑
5.1.3.2生产工艺流程
电解氢气或干法回收的高纯氢气,经过氢气-油换热器加热后,温度约100℃,然后经过气体分布板后在三氯氢硅混合罐内均匀鼓泡,三氯氢硅挥发;控制三氯氢硅混合罐压力0.2MPa,温度-2℃,从而达到氢气与三氯氢硅气体的摩尔比为10:
1;温度为-2℃的混合气与温度为700℃的还原尾气在气-气换热器内进行热交换,温度升到400℃左右,进入还原炉内,在1050℃的硅芯发热体表面发生还原反应,沉积生长多晶硅,反应后尾气经过气-气换热器后进入干法回收系统。
按照程序控制混合气进料量,经过约10天的生长周期长成合乎要求的多晶硅棒。
每炉次的多晶硅棒经过取样检测后,按照不同用户的要求进行切割、滚磨、破碎、清洗、烘干等候加工处理,最后进行真空包装。
6主要设备选型
6.1反应器类
反应器为还原炉,是本项目的核心设备。
6.2塔类
提纯塔为筛板塔,吸收塔脱吸塔为填料塔。
6.3冷换设备
换热器多为列管式换热器和U形管换热器。
6.4容器类
主要为盛装氯硅烷的容器和气体缓冲罐。
表6-1主要工艺设备汇总
单位
数量
备注
反应器类
台
4
塔类
座
8
容器类
台
27
换热器类
台
30
炉子
台
2
导热油锅炉
烟囱
座
1
风机
台
20
泵
台
10
其它设备
台
14
7消耗指标及能耗
7.1辅助材料消耗
辅助材料消耗见表7-1
表7-1辅助材料消耗
序
号
名称
型号或规格
年用量
m3
一次装入量
m3
预期寿命
年
备注
A
B
C
D
E
F
G
1
混合酸
30
2
石灰粉
300
3
煤
600
7.2公用工程消耗
1)水用量(见表7-2)
2)电用量(见表7-3)
4)压缩空气用量(见表7-4)
5)氮气用量(见表7-5)
6)氢气用量(见表7-6)
6)装置消耗量汇总(见表7-7)
表7-2水用量
序号
使用地点
给水t/h
排水t/h
备
注
新
鲜
水
循
环
水
除
盐
水
中压除氧水
低压除氧水
循环热水
含油
污水
含硫
污水
含盐
污水
压力
自流
A
B
C
D
E
F
G
H
I
J
K
L
M
1
主工艺装置区
559
56
559
56
2
辅助工艺装置区
23
23
3
公用工程
30
65
65
30
表7-3电用量
序
号
使用地点
电压
V
设备数量台
设备容量
kW
轴功率kW
年工作时数
年用电量×104kWh
备注
操作
备用
操作
备用
A
B
C
D
E
F
G
H
I
J
K
1
还原炉供电装置
10000
4
0
4000
0
8000
3200
2
制冷机组
380
2
0
365
0
8000
292
3
制氮机组
380
1
0
160
0
8000
128
4
制氢装置
380
1
0
350
0
8000
280
5
循环水泵站
380
1
260
0
8000
208
6
其他
380
160
0
8000
128
合计
4236
注:
未计入照明和仪表用电
表7-4压缩空气用量
序号
使用地点及用途
用量m3(标)/min
备注
非净化
净化
正常
最大
正常
最大
A
B
C
D
E
F
G
1
装置吹扫
*间断
2
仪表用风
2
合计
2
表7-5氮气用量
序号
使用地点
用量m3(标)/min
纯度要求
备注
A
B
C
D
E
1
装置吹扫
2
99.99%(V)
*:
间断
2
合计
2
*:
间断
表7-6氢气用量
序号
使用地点
用量m3(标)/min
纯度要求
备注
A
B
C
D
E
1
装置
0.6
>99.99%(V)
合计
0.6
表7-7装置消耗量汇总
序号
名称
单位
消耗量
备注
A
B
C
D
E
1
循环冷水
t/h
624
2
电(380V)
Kw.h/h
5000
3
净化压缩空气
m3(标)/min
2
5
氮气
m3(标)/min
2*
*表示间断
10
除盐水
t/h
79
11
氢气
m3(标)/min
0.6
13
新鲜水
t/h
30*
*表示间断
7.3节能措施
鼓风机采用离心式风机,减少空气放空,减少风机的功率损失。
8生产控制分析
表8-1装置分析化验项目表
序
号
分析项目
样分
品析
名次
称数
三
氯
氢
硅
四
氯
化
硅
二
氯
二
氢
硅
氮
氧
碳
氯
化
氢
采样点
A
B
C
D
E
F
G
H
I
M
1
精馏产品
1/24
1/24
1/24
2
还原尾气
1/24
1/24
1/24
1/24
1/24
1/24
1/24
3
吸附后氢气
1/24
1/24
1/24
注
(1)表格中分数的分母表示分析一次间隔的小时数。
(2)√表示不定期分析
9装置定员
装置操作人员按内操、外操配置,采用四班三倒制。
装置定员详见表9-1。
表9-1装置定员表
序号
岗位
班次
人员/班
小计
备注
1
主工艺
4
6
24
2
公用工程
4
4
16
3
其他
1
12
12
小计
52
管理、技术人员及生产班长由工厂统一安排。
10环境保护
10.1说明
该装置是处理酸性气的环保设施。
本着“将废物无害化、减量化和资源化,或消灭在生产过程之中”的清洁生产思想,该装置的设计过程,无论是工艺方案的选择,还是流程的设置等诸多方面,都是在充分考虑了如何减少污染物的排放、排放的污染物危害性尽可能小,使得该装置对环境的污染程度最小化的基础上进行的,不仅如此,该装置对有用的硫资源进行了回收,作到变废为宝,综合利用,大大减轻了氯化氢对环境的污染。
同时,该装置本身不可避免排放的一部分污染物需要进行合理处置。
10.2“三废”排放情况
10.2.1废气污染源及污染物
该装置的主要废气污染源为氯化氢。
排放量及主要污染物见表10-1。
表10-1废气排放表(正常工况)
排放介质
污染源
排放方式
排放量
主要有害成分
系统尾气
连续
40m3(标)/h
氯化氢
其中尾气中主要污染物氯化氢的排放量为0.16kg/h,浓度为4g/m3(标)。
10.2.2废水污染源及污染物
该装置产生的废水主要是淋洗塔连续排放的酸性水。
装置排放废水基本情况见表10-2。
表10-2装置排放废水基本情况
排放介质
污染源
排放方式
排放量(kg/h)
主要有害成分
酸性水
连续
26
氯化氢
10.2.3固体废物
主要固体废物排放见表10-3。
表10-3主要固体废物排放
序号
固体废物类别
有毒有害成分组成
一次