生产管理制度范本.docx
《生产管理制度范本.docx》由会员分享,可在线阅读,更多相关《生产管理制度范本.docx(71页珍藏版)》请在冰豆网上搜索。
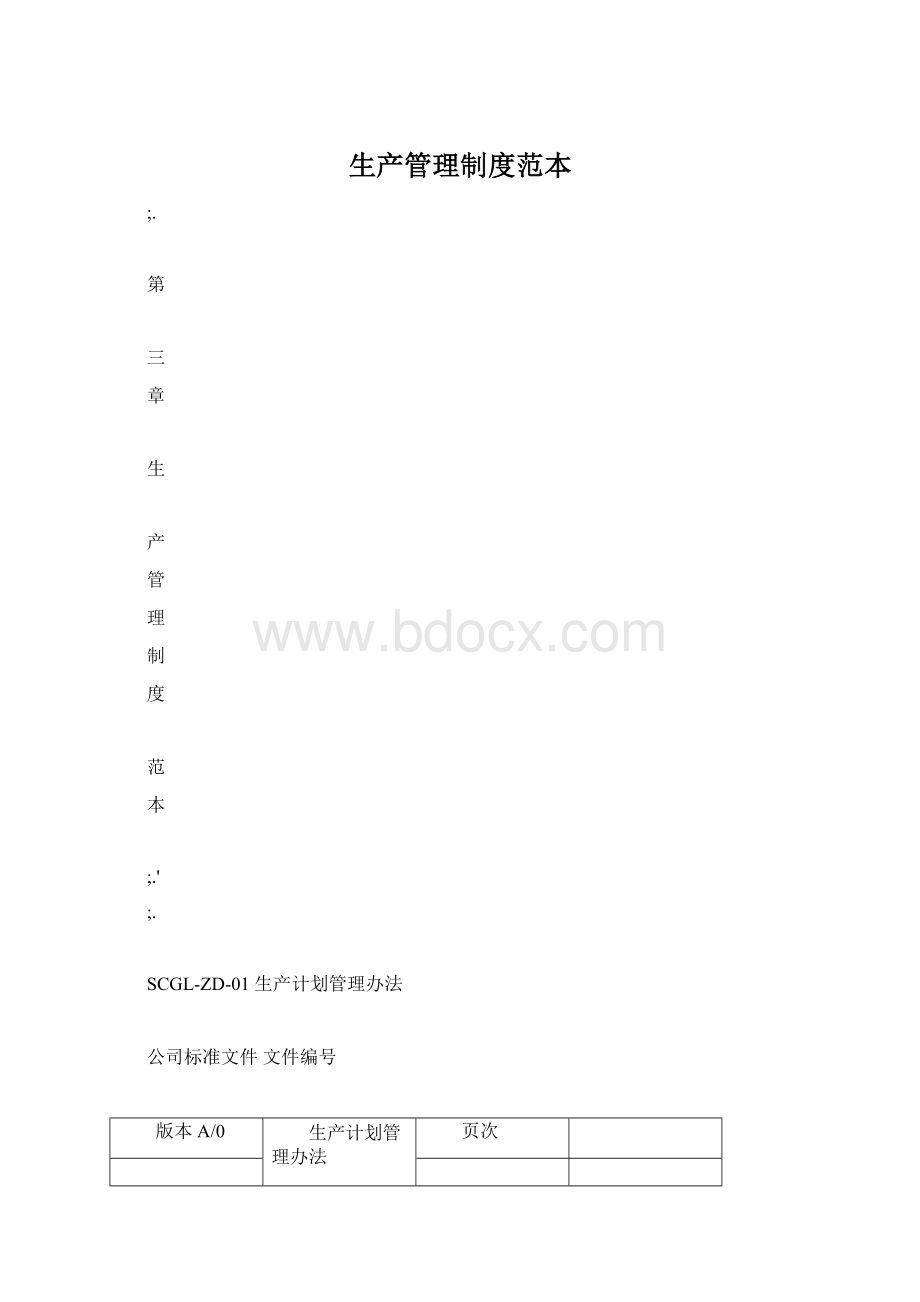
生产管理制度范本
;.
第
三
章
生
产
管
理
制
度
范
本
;.'
;.
SCGL-ZD-01生产计划管理办法
公司标准文件文件编号
版本A/0
生产计划管理办法
页次
1.目的
为使本公司的产能安排有所依据,满足客户对品质及交货期要求,以保证本公司有履行合
约的能力,降低库存、成本,提高生产效率,特制定本办法。
2.范围
适用于本公司所有生产产品的生产计划控制。
3.定义
3.1“生产计划表”、“制造通知单”:
指由PC部门签发作为通知生产的依据。
3.2“制程标示单”:
指由生产计划部门签发,规范批量和记录制作流程的单据。
4.职责
4.1销售部
4.1.1销售主管:
接受客户订单、组织评审及审核、协调重要订单等事宜。
4.1.2销售业务员:
接受客户订单、对订单进行评审、协调订单变更等事宜。
4.2PMC部
4.2.1生产计划主管:
负责生产计划安排、生产进度控制及督导生产计划管理作业的执行。
4.2.2生产计划员:
负责生产指示与生产计划管理及生产进度控制的执行,且负责出货作
业的执行。
4.3采购部:
负责生产物料的采购及交货期进度的控制。
4.4货仓部:
负责物料收发等作业。
4.5PIE部:
负责物料料号的编订和生产流程条件的确定。
4.6制造部:
负责领用材料、生产进度控制及品质控制。
5.作业流程
5.1接收订单
销售部业务人员按“订单评审程序”规定暂时接受客户订单,填写“顾客订货单”,经主
;.'
;.
管审核后交给PMC部门人员。
5.2生产负荷评估
5.2.1PMC部门人员应根据“顾客订货单”做生产计划账目。
生产计划主管根据“生产能
力负荷表”上所显示的生产能力,组织进行生产能力负荷评估。
5.2.2如评估确认生产能力无问题者,生产计划员、物控员与货仓人员确认物料是否可以
满足生产,如不能满足者,填写“物料请购计划表”通知采购人员。
5.2.3采购人员根据“物料请购计划表”询问有关厂商是否能满足交货期,得到较为肯定
的答复后,将结果回馈给物控人员,由物控员开出请购单,采购人员根据“采购控制程序”进
行采购作业。
5.2.4如评估的结果会影响订单交货期时,生产计划人员应通知销售部门人员与客户协
商,征得客户同意后,才可正式接受订单。
5.3安排生产计划
5.3.1生产计划员根据“顾客订货清单”的接单状况,依产能负荷预排4周内的“月生产
计划表”,以作为生产安排的初步依据。
5.3.2生产计划人员每周应更新“月生产计划表”的资料,作为生产进度控制的依据。
5.3.3生产计划人员依“月生产计划表”排出具体的“周生产计划表”,作为生产执行的
依据。
5.4生产指示
5.4.1生产计划员应将“周生产计划表”与“制造通知单”(五联),经生产计划主管核准
后,一联交制造部门准备领料,一联交货仓部门进行备料,一联交物料控员做账,一联交财务
部门,一联自留存档。
5.4.2生产计划员同时填写“制程标示单”,交PIE部门确认制程条件后分发至制造部门
安排生产。
5.5领发料:
制造部门物料人员接到“制造通知单”后,在规定的时间,与货仓人员沟通
协调后,由货仓人员送往制造车间指定地点,一齐清点物料。
5.6生产:
制造部门应按“周生产计划表”及“制程标示单”的交货期需求进行生产,并
进行进度控制,有关作业参照“制程控制程序”。
5.7品质、交货期、数量确认:
5.7.1生产计划员应按照“周生产计划表”的数量及交货期跟催生产进度。
;.'
;.
5.7.2如生产过程中发现进度落后或有品质异常情况,将影响订单交货期或数量时,PMC
部主管应协调各有关部门主管进行协商处理,当交货期最终不能符合订单要求时,应出具联络
单给销售部门,说明原因,销售人员按“订单评审程序”中的有关规定与客户重新协商变更交
货期。
5.8入库和出货:
5.8.1完成生产后,由品管部人员验收,包装入库。
5.8.2在无异常的情况下,报关人员和船务人员根据计划自行办理报关手续和船运联络事
宜。
5.8.3如须出货者,由生产计划员开出“出货通知单”及“出货排柜表”,通知货仓和品
管部门有关人员办理出货手续,有关作业参照“成品包装出货控制程序”。
6.相关文件
6.1生产能力负荷表。
6.2顾客订货清单。
6.3物料请购计划表。
6.4月生产计划表。
6.5周生产计划表。
6.6制造通知单。
6.7制程标示单。
6.8出货通知单。
6.9出货排柜表。
拟定审核审批
;.'
;.
.SCGL-2D-02客户要求评审程序
文件编号
公司标准文件
版本
A/O
客户要求评审程序
页次
1.目的
明确客户要求,通过评审和沟通,满足客户要求并争取超越客户期望。
2.适用范围
适用于客户与产品有关的要求的评审及与客户的沟通
3.职责
3.1业务及工程部各组或制造工程部负责客户要求的确定,组织有关部门对客户要求进
行评审。
3.2业务工程部各组或制造工程部负责依客户要求进行产品试作,并向其提供试作样板。
3.3生产及物料控制部负责对货单进行评审。
4.流程图
流程责任人
1.确定客户要求业务及工程部各组/制造工程部
2.产品试作业务及工程部各组/制造工程部
3.除产品之外的客户要求评审业务及工程部各组/制造工程部
4.订单的接受及认可客户服务部/业务及工程部国内组
5.做货单评审PMC
6.做货单、订单修改PMC/业务及工程部国内组
7.做货单、订单管理PMC/业务及工程部国内组
8.与客户沟通业务及工程部各组/制造工程部
5.程序说明
5.1确定客户要求。
5.1.1原则上,公司所生产的产品都是环保产品,业务及工程部各组在确认价格时,须
对产品进行RoHS评审,属非环保产品时,须通知担当工程师个案处理。
5.1.2订单及作货单的分类:
订单依产品是否已经客户认可,分为“已认可产品订单”
;.'
;.
和“未认可产品订单”。
做货单亦依此分为“已认可产品货单“和未认可产品货单”两类。
5.1.3业务及工程部各组或制造工程部确定客户明示的要求并识别客户潜在的要求,包
括习惯上隐含、无需明示的要求,不需履行的与产品有关的义务,相关质量法律法规、相关
国家和行业标准的要求等。
5.2产品试作
在确定客户要求的基础上,由业务及及工程部各组或制造工程部负责进行产品试作,并
向客户提供试作样板,具体流程见COP-10“新产品试作程序”。
5.3除产品之外的客户要求评审。
当客户提出产品之外的特别要求时,必要时业务及工程部各组或制造工程部负责人组织
相关部门以会议形式对除产品之外的客户要求,如交货地点、送货方式、海关手续等要求进
行评审,保存评审会议记录。
国内客户订单接收认可。
步骤
责任部门
(1)接收订单,对订单内容的合法性、完整
业务及工程部国内组
性、明确性及可接受性进行检查
(2)订单经检查合格后的认可
业务及工程部国内组经理
(3)订单经认可签名后,自认可日起两日内
打印“做货单”,发至生产及物料控制部主管
业务及工程部国内组
或主任
5.5做货单的评审。
5.5.1生产及物料控制部计划员按照“PMC
作业指引”,考虑生产物料的采购情况、出
货计划和生产进度情况,对“已认可产品做货单”
进行评审,将评审结果记录于做货单中相
应栏目。
5.5.2“未认可产品”不做评审,待其认可后再做评审。
5.6做货单及订单的修改。
5.6.1当生产安排(包括生产所需要物料申购情况、出货计划、实际生产)不能完全满
足做货单要求,需推迟送货日期或更改送货数量时,由计划员填写《出货修改申请》,直接
或通过业务及工程部国内组及客户服务部联络客户。
5.6.2客户接受《出货修改申请》的内容,但不变更订单时,计划员只需修改相应的出
货计划或《生产及物料发放单》。
5.6.3客户接受《出货修改申请》的内容并重新下单时,则由业务及工程部国内组或客
;.'
;.
户服务部变更相应的做货单。
5.6.4如客户不接受《出货修改申请》的内容,或PMC重新安排生产,务必满足做货
单要求;或与业务部及客户服务部协商解决。
5.6.5客户提出更改订单时,将此订单作为新订单进行评审,要求同
5.2和5.3。
5.7做货单、订单管理。
5.7.1生产及物料控制部负责保存国外客户的做货单。
5.7.2业务及工程部国内组负责保存国内客户的订单正本,并负责对其进行编目。
业务
及工程部国内组发放做货单时,要求接收者在背面签收。
业务及工程部国内组负责保存做货
单正本,生产及物料控制部负责保存做货单副本。
5.7.3生产及物料控制部负责定期统计做货单的达成情况,作成“做货单达标率统计图”。
统计方法如下:
达成送货批次/做货单(或要货计划)要求送货总批次×100%
(1)由产品认可、开始批量生产起,一种产品依次送货计为一个送货批次。
(2)依做货单(或要货计划)要求完成送货计划“达成”。
(3)客户要求提前交货的计为“达成”。
5.7.4
客户的要货计划视为订单的补充,由
PMC负责保存最终有效版本,保存期限:
半年。
5.8
与客户沟通。
5.8.1
业务及工程部各组或制造工程部负责对客户的电话、传真等方式的问询设专人回
复,暂时未能解答的,需与相关部门沟通后予以答复。
5.8.2生产及物料控制部负责根据需要将订单或做货单的进行情况反馈给客户,包括客
户要求方面的更改,要与公司内相关部门及客户协调一致。
5.8.3产品交付后,要多渠道搜集客户的反馈信息,由品管部负责即使妥善处理客户投
诉,及取得客户持续满意。
6.质量记录
6.1国内客户做货单
6.2出货修改申请
拟定审核审批
;.'
;.
SCGL-ZD-03订单审查作业规定
公司标准文件文件编号
版本
A/0
订单审查作业规定
页次
1.目的
为了达到生产顺畅,准时出货,客户满意之效果。
2.管理责任者
生管部主管。
3.工作程序
3.1订单确认:
3.1.1生管课接单员接到业务提供的正式订单后,审查订单客户要求、交期、港口、订购
单号和各机型BOM,包装方式是否明确等相关数据无误后,签名确认。
3.1.2如订单有新机型,则接单员须确认此款新机型有无料号、BOM、等书面及系统数据,
如数据不完整,接单员应及时知会业务及开发单位提供。
客供零件转厂内采购,接单员需列入接单审查并及时反馈给报价员更新成本。
3.1.3接单员第一次审单确认修改的内容,在订单上接单员签名确认即可;手写部份若有
再次修改需有签名确认。
3.1.4接单员确认交期过程中有异常须及时与业务协商,无法处理时应立即回报上级主管
协助处理。
3.1.5针对紧急订单,接单员应查询厂内物料状况,如无法满足交期应及时与业务协商至
双方可以接受的交期为止。
3.1.6接单员每天将确认无误的订单录入电脑。
3.1.7接单员接单后3天内需跟催业务提供包装材料设计单,7天内提供客户注意事项。
3.1.8.接单员每月底将下月交期的订单进行统计,按客户和机型进行分类统计出数量和箱
数,做出“受订明细表”。
3.2订单变更
3.2.1变更单(含样品单)的处理操作程序同正式订单。
交期在15天内的相关包装材料变更
;.'
;.
需发放书面的变更数据并签名确认。
3.2.2针对取消或数量变更的订单,接单员须追踪业务单位对库存提出处理意见。
3.3.备料单计划员须列表管制,并跟催备料完成状况,追踪业务部正式订单,备料单变更
同正式订单。
拟定审核审批
;.'
;.
SCGL-ZD-04产能负荷分析作业办法
公司标准文件文件编号
版本A/0页次
产能负荷分析作业办法
1.目的
为规范生产计划安排前对制造产能与生产负荷之间是否平衡的分析,使生产计划合理、可
靠,并可作为事前的设备、人力申请的依据,特制定本办法。
2.适用范围
生产管理部安排中日程生产计划(一般指月度生产计划)时适用,也可供制造部作为人力、
设备分析的参考。
3.定义
3.1工作中心区分
(1)为方便产能预估计算,由生产管理部将制造部门依功能别区分为若干个“工作中心”(一般以生产线别、课别为单位),作为产能与负荷的管制单位,并予编号区别。
(2)凡为必须连续作业的相连的不同设备,应将其整体视为一个工作中心。
(3)凡为工作性质相同,且规格类似或相同的各不同个别设备(如注塑机),其生产批作业可以互相替换者,应视为同一“工作中心”。
(4)凡为工作性质相同的班组(人员),应视为同一工作中心,不另依熟练度或更细工序再划分为不同的工作中心。
3.2产能与负荷分析管制表
生产管理部将各工作中心每一时段(一般为月度或周次)的产能与负荷分别换算成相同的可比单位,如时间或产量(一般用时间来衡量),填入同一张表单内,用以比较分析制造能力与
生产任务之间可否平衡。
此表称为“产能与负荷分析管制表”,一般应包括下列内容:
(1)工作中心的名称、编号。
(2)分析评估期间(一般为一个月或一周)。
(3)产能状况,含正常上班及加班,一般包括可稼动天数、可出勤人数、可稼动设备数、每日班次、产能系数及产能时间等项目。
;.'
;.
(4)负荷状况,含生产批号、生产产品、生产预定量、标准工时、负荷工时等项目。
(5)分析结论及对策。
4.实施规定
4.1产能预估分析
4.1.1月份产能预估分析
(1)每月24日前,生产管理部依各工作中心别分别填写产能状况。
(2)正常产能,指每月按公司规定正常上班的总时间内的产能状况,依次填入可稼动天数、可出勤人数、可稼动设备数、每日班次。
(3)产能系数以最近三个月该工作中心的平均生产效率为标准(如95%)。
(4)计算公式:
设备产能时间=每日正常上班时间×每日班次×可稼动天数×可稼动设备数
人力产能时间=每日正常上班时间×每日班次×可稼动天数×每班人数
4.1.2周次产能预估分析
(1)每周末,由生产管理部依各工作中心别分别填写下周产能状况。
(2)填写方法参照月份产能预估分析。
4.2负荷预估分析
4.2.1月份负荷预估分析
(1)每月24日前,生产管理部将业务部转发的订单状况,转换成生产订单,并编上生产批号,同时加上预估陆续补入的订单状况,依各工作中心别分别填写负荷状况。
(2)填入生产批号(预估订单可不填写批号)、生产产品、生产预定量、标准工时。
(3)计算公式:
负荷工时=生产预定量×标准工时
(4)合计的负荷工时为各批的负荷工时加总而成。
4.2.2周次负荷预估分析。
(1)每周末,由生产管理部依各工作中心分别填写下周负荷状况。
(2)填写方法参照月份负荷预估分析。
4.3分析结论及对策
4.3.1产能大于负荷。
预估次月(周)的产能大于负荷时,一般应对措施有:
;.'
;.
(1)要求业务部门追加订单。
(2)将下月(周)之订单提前。
(3)安排富余人力或设备支援其他工作中心。
(4)安排富余设备保养及人员教育培训。
(5)安排调休,减少加班。
(6)必要时评估设备变卖、转移,人员裁减、辞退。
4.3.2产能小于负荷状况。
当预估项目(周)的产能小于负荷时,一般应对措施有:
(1)向其他工作中心请求设备、人力支援。
(2)不足工作量由委外加工弥补。
(3)必要时增购设备,增加人力。
(4)延长加班时间,牺牲休息时间。
(5)必要时与业务部门协调将部分订单延迟或取消。
5.相关记录
产能负荷分析表。
拟定审核审批
;.'
;.
SCGL-ZD-05物料请购及委外计划拟定办法
公司标准文件文件编号
版本
A/0
物料请购及委外计划拟定办法
页次
1.目的
为及时进行物料请购或委外加工,保证物料按时按量到位,做到生产无欠料,并有效控制
原材料的存量水平,特制定本办法。
2.管理责任者
生管部主管。
3.工作程序
3.1请购及委外原则:
3.1.1计算净需求量:
净需求量=(库存量+在途采购单需求+在途“制造命令单”需求+计划请购单需求+计
划“制造命令单”需求)-(“制造命令单”需求+计划“制造命令单”需求)或净需求量=可用量-总需求量。
3.1.2对总需求量大于可用量的物料提出请购或委外加工。
3.1.3对有计划量的购买件与制造件物料,物控在ERP系统的MRP工作平台中维护交期,
数量,内部与外部请购件应以“请购单”书面形式向采购或加工厂商提出需求。
3.2周期短,耗用量大,低价值的物料请购:
3.2.1设定计划方式为min-max(最小—最大)。
3.2.2min量根据采购周期内用量进行考虑,设定合理的安全存量。
3.3请购计划维护好后,及时打印,经核决后生效。
3.4将请购单一联发采购,一联生管存档。
3.5对于大量采购,原物料应分批陆续到位,以免过分集中。
3.6物控员每周平衡物料一次,如需调整,则填写《供货商交期调整一览表》交采购。
3.7如有订单取消或交期变更等,物控员应在10小时内调整交期,并填写《供货商交期
调整一览表》,并交采购。
;.'
;.
3.8委外生产计划及作业。
3.8.1特殊颜色及委托机械加工产品,由生管提需求到采购,其依据车辆状况及厂商生产
能力进行委外。
3.8.2生管根据相关“制造命令单”制作出“请购单”交相关单位进行后续作业。
4.相关表单
4.1供货商交期调整一览表。
拟定审核审批
;.'
;.
SCGL-ZD-06生产计划变更管理办法
公司标准文件文件编号
版本A/0生产计划变更管理办法页次
1.目的
为规范生产计划变更流程,使计划更为顺畅得以执行,特制定本办法。
2.适用范围
因市场需求变化、生产条件变化或其他因素引起的生产计划变更。
3.定义
本办法所指的生产计划变更,是指已列入周生产计划内的生产订单,因市场需求变化、生产条件变化或其他因素需调整生产计划的变更。
4.具体内容
4.1变更时机
4.1.1客户要求追加或减少订单数量时。
4.1.2客户要求取消订单时。
4.1.3客户要求变更交货期时。
4.1.4客户有其他要求导致生产计划必须调整时。
4.1.5因生产进度延迟而可能影响交货期时。
4.1.6因物料短缺预计将导致较长时间停工时。
4.1.7因技术问题延误生产时。
4.1.8因品质问题尚未解决而需延迟生产时。
4.1.9因其他因素必须作生产计划调整时。
4.2变更流程规定
4.2.1生产管理部在遇到上款规定的各种状况,经确认必须变更生产计划时,应发出“生
产计划变更通知单”。
“生产计划变更通知单”一般应包含下列内容:
——生产计划变更原因。
——计划变更影响的生产部门及时间。
;.'
;.
——原生产计划排程状况。
——变更后生产计划排程状况。
——需各部门注意配合的事项。
4.2.2如生产计划变更范围较大,生产管理部应召集生控人员、物控人员、采购部、制造
部、业务部或其他相关部门进行检讨确认。
4.2.3如生产计划变更后,新计划与旧计划相比较有较大变化时,生产管理部门应在“生
产计划变更通知单”后附上新的周生产计划。
4.2.4“生产计划变更通知单”及其附件除生产管理部自存外,应比照生产计划的发放要求,
发放到下列部门:
业务部、开发部、生产技术部、品管部、制造部、采购部、资材部。
4.2.5各部门接获“生产计划变更通知单”后,应立即确认本部门工作安排之调整,以确
保计划的顺利执行。
4.3生产计划变更后的作业规定
4.3.1生产管理部
——修改周生产计划及每日生产进度安排。
——确认并追踪变更后的物料需求状况。
——协调各部门因此产生的工作调整、配合。
4.3.2业务部。
——修改出货计划或销售计划。
——确认变更后计划各订单交货期是否可以确保。
——处理因此而产生的需与客户沟通的事宜。
——处理出货安排的各项事务。
4.3.3开发部。
——确认产品设计、开发进度,确保生产。
——确认技术资料的完整性、及时性。
4.3.4生产技术部
——确认生产工艺、作业标准的及时性、完整性。
——确认设备状况。
——确认工装夹具状况。
——确认技术变更状况。
;.'
;.
4.3.5品管部
——确认检验规范、检验标准的完整性。
——确认检验、试验的设备、仪器状况。
——确认品质历史档案。
——安排品质重点、控制点。
4.3.6采购部
——确认物料供应状况。
——确认多订购物料数量及处理状况。
——处理与厂商的沟通事宜。
4.3.7资材部
——确认库存物料状况。
——负责现场多余物料的接受、保管、清退事宜。
——其他物料仓储事宜。
4.3.8制造部
——处理变更前后物料的盘点、清退、处理事宜。
——生产任务安排调整。
——人员、设备调度。
——确保新计划的顺利达成。
5.相关文件
生产计划变更通知单。
拟定审核审批
;.'
;.
.SCGL-ZD-07PMC
工作指引
公司标准文件
文件编号
版本
A/O
PMC工作指