强化烧结的手段.docx
《强化烧结的手段.docx》由会员分享,可在线阅读,更多相关《强化烧结的手段.docx(11页珍藏版)》请在冰豆网上搜索。
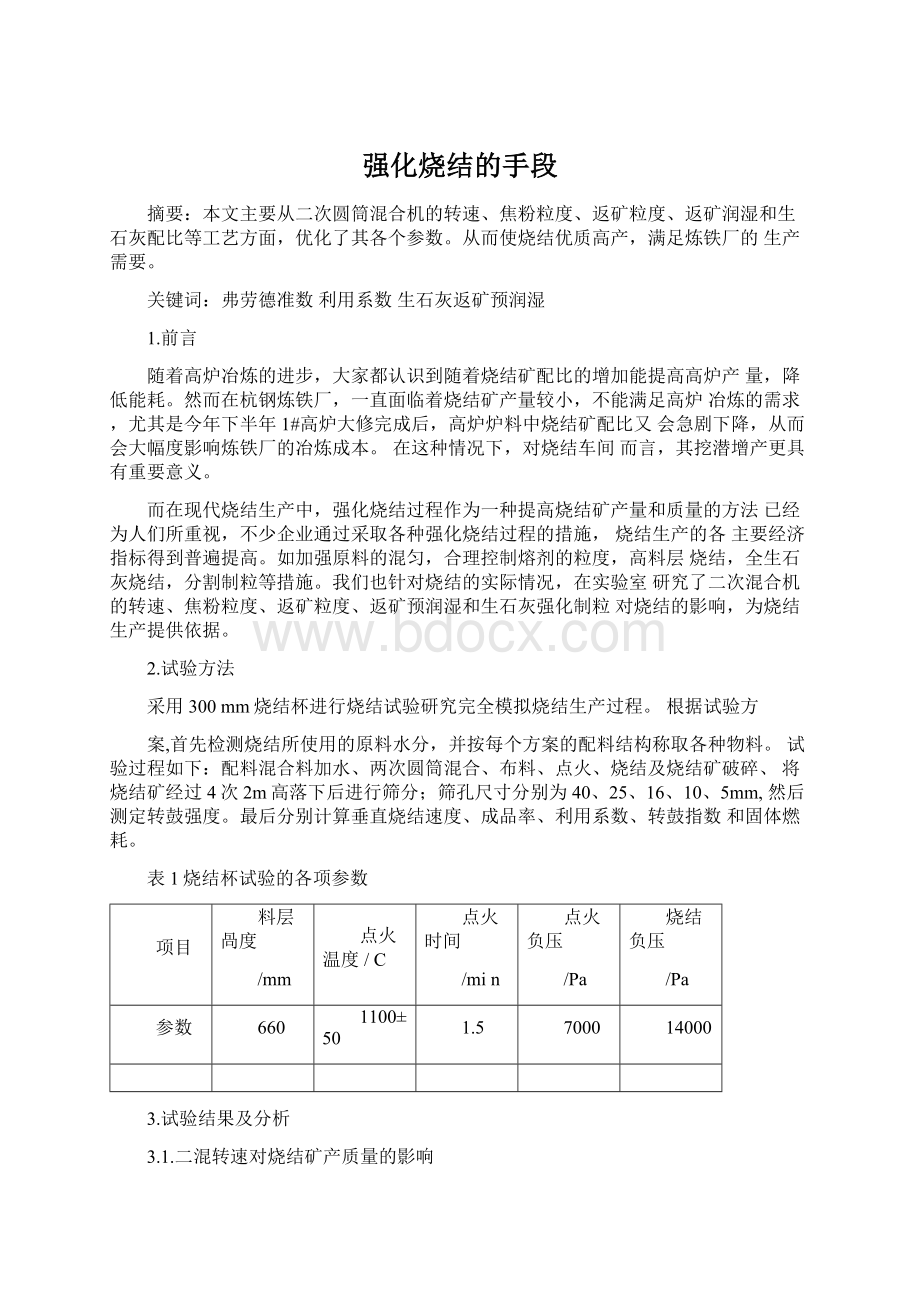
强化烧结的手段
摘要:
本文主要从二次圆筒混合机的转速、焦粉粒度、返矿粒度、返矿润湿和生石灰配比等工艺方面,优化了其各个参数。
从而使烧结优质高产,满足炼铁厂的生产需要。
关键词:
弗劳德准数利用系数生石灰返矿预润湿
1.前言
随着高炉冶炼的进步,大家都认识到随着烧结矿配比的增加能提高高炉产量,降低能耗。
然而在杭钢炼铁厂,一直面临着烧结矿产量较小,不能满足高炉冶炼的需求,尤其是今年下半年1#高炉大修完成后,高炉炉料中烧结矿配比又会急剧下降,从而会大幅度影响炼铁厂的冶炼成本。
在这种情况下,对烧结车间而言,其挖潜增产更具有重要意义。
而在现代烧结生产中,强化烧结过程作为一种提高烧结矿产量和质量的方法已经为人们所重视,不少企业通过采取各种强化烧结过程的措施,烧结生产的各主要经济指标得到普遍提高。
如加强原料的混匀,合理控制熔剂的粒度,高料层烧结,全生石灰烧结,分割制粒等措施。
我们也针对烧结的实际情况,在实验室研究了二次混合机的转速、焦粉粒度、返矿粒度、返矿预润湿和生石灰强化制粒对烧结的影响,为烧结生产提供依据。
2.试验方法
采用300mm烧结杯进行烧结试验研究完全模拟烧结生产过程。
根据试验方
案,首先检测烧结所使用的原料水分,并按每个方案的配料结构称取各种物料。
试验过程如下:
配料混合料加水、两次圆筒混合、布料、点火、烧结及烧结矿破碎、将烧结矿经过4次2m高落下后进行筛分;筛孔尺寸分别为40、25、16、10、5mm,然后测定转鼓强度。
最后分别计算垂直烧结速度、成品率、利用系数、转鼓指数和固体燃耗。
表1烧结杯试验的各项参数
项目
料层咼度
/mm
点火温度/C
点火时间
/min
点火负压
/Pa
烧结负压
/Pa
参数
660
1100±50
1.5
7000
14000
3.试验结果及分析
3.1.二混转速对烧结矿产质量的影响
为了优化新烧二次混合机的转速,从而提高制粒效果,在实验室内根据弗劳德准数模拟烧结现场的转速。
弗劳德准数为:
Fr=D(N/60)79.8
其中Fr为弗劳德准数;
D为二次混合机直径;
N为二次混合机转速;
已知,烧结车间二次混合机的参数为①3000X12000mm实验室内二次混合机为700mM1200mm以此为依据,可知当新烧二次混合机转速为6r/min时,
实验室内混合机转速应为12.42r/min,新烧二次混合机转速为6.5r/min时,实验室内混合机转速应为13.46r/min,以此类推,当新烧二次混合机转速为
7r/min,7.5r/min和8r/min,实验室内烧结机转速则依次为
14.49r/min,15.53r/min和16.50r/min.
表7是混合机转速对烧结矿产质量的影响。
化学成分为R2.20,MgO3.20
SiO25.10,焦粉4.0%,水分6.7%。
表2二混转速对烧结的影响
二次混合机转速
r/min
烧结混合矿的水分
/%
烧结速度
/mm/min
成品率/%
利用系数/t•m
-2•h-1
转鼓强度
+6.3mm/%
固体燃耗
/kg/t
12.42
6.6
19.75
78.39
1.18
73.53
44.876
13.46
6.7
22.43
80.16
1.41
75.33
44.214
14.49
6.6
21.27
80.01
1.38
75.07
44.210
15.53
6.7
20.15
80.16
1.31
74.80
44.345
16.50
6.7
20.33
78.98
1.30
73.73
45.011
由表2可知,随着二次混合机转速的从12.42r/min增加到16.50r/min,烧结的利用系数和转鼓强度都是先从1.18t•后•h-1增加到1.41t•m2•h-1,后
降低到1.30t•nf•h-1。
在二次混合机转速为13.46r/min时,利用系数达到最大1.41t•m2•h-1。
这是因为如果增大二次混合机转速后,烧结混合料的滚动路径增加,增加了成核粒子和粘附粒子之间的接触机会,造球效果增加;但继续
增加混合机转速到15.53r/min和16.50r/min,则烧结混合料在二次圆筒混合机内则会出现部分泄落情况,从而破坏了混合机的制粒效果。
因此二次混合机的转速最好控制在13.46r/min〜14.49r/min之间,相应的烧结车间的二次混合机转速适宜的转速为6.5r/min和7r/min之间。
3.2焦粉粒度对烧结的影响
表3是焦粉粒度对烧结矿产质量的影响。
焦粉是用3.2mm的圆孔筛手动的方
法分出的。
其中,R2.00,MgO3.2QSQ25.43,焦粉配比4.0%。
表3焦粉粒度对烧结矿产质量的影响
焦粉
-3.2mm/
%
烧结混合矿的水分
/%
烧结速度
/mm/min
成品率/%
利用系数/t•m
-2•h-1
转鼓强度
+6.3mm
/%
固体燃耗
/kg/t
76
6.6
20.00
80.08
1.34
73.60
44.25
80
6.5
21.36
78.49
1.41
72.00
44.82
84
6.5
18.91
78.38
1.24
72.67
43.53
88
6.6
20.55
78.19
1.27
71.73
45.13
图1焦粉粒度对烧结矿产质量的影响
由表3和图1可以看出,随着焦粉—3.2mm粒度的增加,转鼓强度先降低再增加再降低。
当焦粉粒度为-3.2mm占88%时,转鼓强度均最低;当焦粉-3.2mm粒度占76%时,转鼓强度最高。
利用系数是先降低再增加又降低,利用系数在焦粉-3.2mm占80%时最高,其次是焦粉粒度为76%时。
这是因为,当焦粉粒度过细时,被抽到料层下部,从而导致下部过熔,透气性变差,影响烧结利用系数,而杭钢烧结机的负压与其它烧结厂的烧结负压相比又更大,所以要控制焦粉粒度-0.5mm部分也要少。
因此,综合考虑适宜的焦粉粒度为80%,此时利用系数最
高,强度也能保证。
3.3返矿粒度对烧结的影响
表4是不同时段取得到的不同的返矿的粒度。
表5是除了返矿粒度不同,其它各项条件都相同时的烧结杯试验结果,烧结工艺参数为其中,R2.00,MgO3.20SQ25.00,焦粉配比4.0%。
表4是不同时段取的两种不同返矿的粒度/%
项目
>3mm
3〜1mm
1〜0.5mm
-0.5mm
返矿A
76.28
18.90
2.22
2.60
返矿B
29.34
33.54
17.48
19.64
表5是返矿粒度对烧结矿质量的影响
试验编号
烧结混合矿的水分
/%
烧结速度
/mm/min
成品
率/%
利用系数
/t•m
-2•h-1
转鼓强度
+6.3mm
/%
固体燃耗
/kg/t
返矿A
6.6
20.80
73.43
1.28
70.80
49.09
返矿B
6.5
14.66
75.00
0.89
72.53
48.05
由表4可知,返矿B和返矿A相比,-1mm粒级大幅度增加
由表5可知,用返矿A与用返矿B相比,致使烧结矿的利用系数下降了
30.47%,严重影响了生产指标。
这是因为返矿A和返矿B相比,-1mm粒级增加了32.24%,返矿中难于制粒的中间粒子和粘附粒子大幅度增加,但返矿本身亲水性差,-0.2mm粒级的返矿难于粘附在成核粒子上面,致使烧结混合料的透气性变差,因此对于烧结而言,应控制返矿粒度大部分在1mm以上,从而较好的起到成核粒子的作用。
3.4返矿预润湿对烧结过程的影响
烧结混合料中,返矿的配比是较高的,它具有粒度粗、多孔、形状不规则等结构特征,在混合料的制粒过程中,其表面容易粘附其它微细颗粒,起到成核粒子的作用,可强化混合料的制粒效果。
而返矿预润湿则是增加返矿表面粘附性的有效途径之一。
返矿预润湿是在烧结返矿中预先加入一定量的水,使其达到良好的润湿状态
后,再与其它原料一起混合制粒。
返矿润湿主要做了两部分,1.是低润湿返矿水分,2.是高润湿返矿水分。
3.4.1返矿低水分预润湿
表6是返矿低水分预润湿时对烧结矿产质量的影响,其工艺参数R为2.20,
MgO3.2QSQ25.15。
表6返矿低水分预润湿对烧结矿产质量的影响
试验编号
烧结混合矿的水分
/%
烧结速度
mm/min
成品率
/%
利用系数
/t•m-
-2•h-1
转鼓强度
+6.3mm/%
固体燃
耗/kg/t
返矿不润湿
6.8
25.93
79.55
1.54
73.40
44.506
返矿水分3%
6.8
23.91
79.93
1.44
75.20
43.610
返矿水分5%
6.8
25.98
79.98
1.52
74.13
43.734
返矿水分7%
6.7
26.29
78.64
1.56
73.47
44.159
由表6可知,在返矿润湿水分从0增加到7%过程中,烧结矿的转鼓强度是增加的,在返矿水分增加到3%时,转鼓强度增加了1.8%,但利用系数是先降低后略有增加的。
可见在返矿预润湿低水分条件下,对利用系数的影响是效果不是很明显,但转鼓强度有较大幅度的增加。
原因可能在于,在低水分润湿情况下,与进入一混后又进行了混匀至烧结混合料的水分6.8%左右,而一混的主要作用是混匀,因此在低润湿返矿时,其预先润湿的效果没有体现出来。
3.4.2返矿预润湿高水分(注:
中南大学钢铁系为涟钢烧结厂做的烧结杯试验)
表7是返矿高水分预润湿时对烧结矿产质量的影响,。
表7返矿高水分预润湿对烧结矿产质量的影响
试验条件
烧结指标
水分/%
返矿其它原料
7.07.0
转鼓强度
/%
62.74
成品率/%
82.64
烧结速度
/mm-min-1
19.56
利用系数
/t.m-2-h-1
1.674
8.0
7.0
63.19
82.84
20.66
1.832
8.5
7.0
62.73
82.13
22.99
1.926
9.0
7.0
62.73
84.08
22.36
1.912
注:
表中返矿水分为7.0%时,表示返矿未采取预润湿措施
表7所示结果表明,与返矿不润湿相比,当返矿预润湿水分为8.0%时,在
利用系数基本一致的情况下,烧结矿转鼓强度提高了近1%。
进一步提高返矿预
润湿水分至8.5%、9鸠后,垂直烧结速度明显加快,达到了22mmmin-1以上,利用系数也超过了1.9t-m2-h-1,生产效率大大提高,而与此同时烧结矿的质量并未恶化,转鼓强度并没有降低。
试验表明,返矿润湿水分在8.0%左右较为适宜。
当然各个厂家的用料千差万别,但对于我们烧结车间而言,也至少应将返矿润湿水分略高于烧结混合料的水分,效果才能体现出来。
3.5生石灰配比
表8是生石灰配比对烧结产质量的影响。
其工艺参数为:
R2.00,MgO3.20
SiO25.10,焦粉配比4.0%。
表8对烧结矿产质量的影
生石灰用量
/%
烧结混合矿的水分
/%
烧结速度
/mm/min
成品率
/%
利用系数
/t•m
-2•h-1
转鼓强度
+6.3mm
/%
固体燃
耗/kg/t
0
7.0
20.31
80.28
1.308
72.23
44.15
3.0
7.0
20.01
81.01
1.310
73.07
43.82
5.0
7.0
22.07
79.89
1.422
71.99
44.53
6.0
7.0
21.55
80.90
1.421
72.70
43.95
由表8可知,当生石灰部分取代石灰石时烧结矿转鼓强度先增大后降低,但
继续增加生石灰用量至5%6%寸,烧结矿的转鼓强度相反略有降低,但垂直烧结速度和利用系数一直是增加的,在生石灰用量为5%时达到最大。
这是因为生石灰消化后生成消石灰放热,提高料温,降低过湿层厚度,改善料层透气性。
而消石灰具有胶体的特征,比表面积大,可充当粘结剂,起到强化混合料制粒的作用,能提高小球的成球率和强度,从而增加垂直烧结速度,提高烧结机利用系数。
由此可见,在碱度允许的条件下,可以生石灰配比可以提高到5%。
4.结论
1.对于烧结车间二次混合机适宜转速为6.5r/min~7r/min;
2.焦粉粒度在—3.2mm为76%时,转鼓强度最高,但当焦粉粒度-3.2mm为80%时,利用系数最高,但也要控制-0.5mm粒级焦粉的含量能太高。
3.返矿粒度大部分在1mml以上,较好的起到成核粒子的作用,利于烧结混合料制粒,增加烧结料层的透气性;
4.返矿润湿水分高于烧结混合料的水分;
5.生石灰可以提高烧结机的利用系数,在碱度允许的情况下,可以增加生石灰的配比到5%
强化烧结助燃剂
该产品不仅解决了铁精矿烧结工艺的传统强化措施(低温烧结、小球烧结、燃料分加等)存在的弊端,同时也攻克了传统添加剂应用方面生产综合负值的问题。
该产品主要由燃气化剂、增氧剂阻凝剂和超细粉末稳定剂组成,
根据配方按比例配料后,经机械混合、研磨烘干、分装而成,生产过程中不产生任何污染。
在烧结混合料中添加快烧结过程燃烧速度,提高烧结机的利用系数,增加烧结矿产量和强度,同时可降低烧结尾气中二氧化硫的含量,为大学科研成果奖,并颁发证书。
一强化烧结助燃剂的主要功能可对固体燃料的气化燃烧起催化助燃作用,特别是对固体燃料中非碳物质的催化作用更强,
增加固体燃料的反应活性,使烧结过程烧结带温度提高,有利于矿化反应的进行,能产生极多的液相。
可改善烧结过程气液相间的传热质条件,使烧结速度加快,烧结时间短,提高生产效率。
可使混合料的熔融温度降低,点火条件得以改善,降低返矿量,提高成品率。
强化烧结助燃剂中的卤化物的稀土元素,可使烧结矿的自然粉化现象得以抑制,有利于烧结矿强度的提高。
由于反应的放热节能作用,在烧结生产中降低了固体燃料的加入,减少烧结废气中的二氧化硫含量,降低环境污染。
在助燃剂的强化、催化作用下,大部分液相反应可在低于1300以下完成,至使燃耗可降低13以上,生产过程的其他固定费用亦同步下降。
强化烧结助燃剂可提高烧结机利用系数5%以上,提高烧结矿转鼓指数6%以上,
降低亚铁含量2%左右,提高成品率,降低返矿率,经济和社会效益显著。
低温烧结
一种铁矿石烧结工艺。
它以较低的烧结温度,产生一种强度高、还原性好的较理想的黏结相矿物——针状铁酸钙,并以此去粘结那些部分起反应或未起反应的残余矿石。
工艺原理工艺矿物学的研究表明:
烧结矿质量的优劣与其中黏结相矿物有密切关系。
在众多的黏结相矿物中以针状铁酸钙矿物的还原性及机械强咬最好。
因之,提高烧结矿质量的重要途径是发展以针状铁酸钙为主的烧结矿牯结相矿物。
针状铁酸钙是一种钙、铝、硅复合铁酸盐,简写为SFCA。
工艺特点低温烧结与高温熔融型烧结工艺相比,有以下特点:
(1)烧结温度低,高温保持时问长。
低温烧结工艺的最佳烧结温度为1230〜
1270E,最高不超过1300C。
1100C以上的高温保持时间在3〜5min以上,比高温熔融型烧结工艺要长1〜3min,见图1。
(2)烧结矿的胶结相以针状铁酸钙为主,其数量超过30%〜40%,而高温熔融型
烧结矿,由于烧结温度超过1300E,针状铁酸钙变为柱状或分解,其数量将急剧减少
(3)烧结矿的显微结构为交织熔蚀结构。
理想的烧结矿结构,是由两种矿相组成的非均质结构。
一种属于多元体系的针状胶结相,另一种是被上述胶结相所胶结的残留矿石颗粒。
图2示出低温型烧结矿的交织熔蚀结构。
其中未熔矿石约占30%〜40%。
以赤铁矿为主的烧结料,其残余结构矿石为赤铁矿;以磁铁矿为主的烧结料,其残余结构矿石为磁铁矿。
工艺条件生产中要实现低温烧结工艺应具有以下条件:
(1)良好的原料准备。
对原料、燃料、熔剂和返矿等烧结原料应进行严格整粒,充分混匀。
并应有一定比例的粒度粗、强度高、还原性好,多孔的矿石作为成球核心。
以化学反应好,易于形成铁酸钙的细矿粉作为外面的粘附颗粒,借以获得理想的准颗粒结构。
严格控制制粒的水分,加强混合料的制粒,最大限度的提高料层透气性。
(2)生产高碱度烧结矿。
一般铁矿粉或铁精矿绝大多数都是酸性矿,为获得针状
铁酸钙,必须添加较多的石灰石或生石灰。
据研究,烧结矿碱度(CaO/SiO2)1.5
以上时,即有一定量铁酸钙出现,但以碱度1.7〜1.8为最好。
(3)烧结矿中要有适宜的铝硅比AI2O3/SiO2。
以0.1〜0.2为宜,只有这样才可在较低的烧结温度下(1230〜1270C)促成针状铁酸盐的生成。
⑷合理的烧结制度。
由Fe2O3和CaO组成的熔体大约在1200C产生。
当温度超过1300E时,铁酸钙熔解或熔化变为次生赤铁矿或磁铁矿及渣相。
另外,为使针状铁酸钙和“粒状赤铁矿”稳定形成,温度又要严格控制在高于1250C,而
且1100C以上的高温保持时间应长一些,以保证有足够的反应时间。
因此,低温烧结的工艺操作.要求低碳、高料层、高氧位,并按原料的特性,采用合理的点火、烧结制度,尽量符合图3所示的理想加热曲线。
低温烧结矿由于强度好、亚铁低、还原度高,因此在烧结节能、高炉增产节焦等方面都十分显著。
小球烧结
将烧结料制成一定粒度的小球,进行烧结的铁矿石烧结工艺。
矿粉经过成球处理可以大幅度地提高混合料中小料球(一般指大于3mm)的数量,从而改善烧结料的透气性和强化烧结过程,特别是对细矿粉烧结效果更好。
工艺流程部分小球烧结与全部小球烧结的工艺流程示于图中。
在全部小球烧结工艺流程中,全部原料(含返矿)经配料(只配入一小部分燃料)、混合后,由造球机将混合料制成一定粒度的小球(3〜8mm),然后在圆筒混合机内将细粒燃料黏附于小球表面。
为了减少小球的破碎,用梭式布料机及宽皮带布料机将小球均匀地布在台车上,进行点火抽风烧结。
如球粒较大,则需先进行干燥而后点火,防止爆裂。
烧结后的产品处理与普通烧结相同。
效果小球烧结技术可以获得以下效果:
(1)改善烧结料层透气性,提高烧结速度与产量;
(2)有利于增加料层高度和降低固体燃料消耗量以实现低温烧结;(3)由于小球自身依靠固相扩散固结,而小球间为液相粘结,故可提高烧结矿强度增加成品率;(4)可以降低烧结矿的FeO含量,改善其还原性;(5)可以用低负压抽风烧结,节省电耗。
燃料分加对混合料造小球团及烧结过程的影响
燃料分加对混合料造小球团的影响
在首钢矿业公司烧结厂原料条件下,燃烧分加后混合料的原始透气性略低于燃料分加前。
燃料分加量越大,分加时间越晚,对透气性的影响越大。
燃料分加前混合料在较高水分下造球,有利于混合料成球长大。
但因煤粉粒度较大,亲水性较弱,成球性差,燃料分加后煤粉粘在小球团的表面会阻止球团内部的水向外渗,无法湿润小球团的表面,妨碍球团进一步长大。
为提高燃料利用率,燃料最好分加得晚些、多些。
但燃料分加得太晚、太多,煤粉在球团表面粘结不牢,粘结量少,煤粉都集中在小颗粒混合料中。
综合考虑,燃料分加量取75%,分加后再混合2min较合适。
3.2燃料分加对混合料中固定碳含量的影响:
混合料粒度越小,碳含量越高;燃料分加时间越晚、分加量越大,碳越易向
小粒度混合料中偏析。
在烧结机内,混合料通过泥辊、布料器向烧结机台车上布料时,混合料中部分小粒度混合料向上偏析。
如燃料分加后,燃料过多地向混合料小粒度偏析,小粒度混合料又过多地向料层上部偏析,势必造成料层上部热量过剩,下部热量不足,使烧结过程合理的热制度被破坏。
3.3燃料分加对混合料布料的影响
燃料分加造球后偏析布料烧结,使垂直烧结速度加快、烧结杯利用系数增加、烧结矿强度降低。
在总造球时间为6min条件下,燃料分加后造球时间的长短对烧结杯利用系数影响不大。
在造球4min+燃料分加+造球2min的条件下,燃料分加比例从0%增加到100%时,随着燃料分加量的增加,垂直烧结速度及燃料消耗量都呈现出增加的趋势,返矿量增加,烧结矿中小于10mm粒级的烧结矿增加,烧结矿强度呈现出下降的趋势。
由于烧结矿成品率低,虽然随着燃料分加比例的增加,其垂直烧结速度加快,但烧结杯利用系数并没有提高。
燃料分加后100%烧结杯偏析布料时,料层粒度偏析过大,造成料层上部燃料过于集中,下部燃料不足,因而破坏了烧结过程合理的热制度。
在燃料分加小球团烧结条件下,通过适当的偏析布料,可以使烧结料层的上部温度与下部温度基本一致,烧结饼上部与下部烧结矿质量基本一致。
燃料分加后烧结速度加快,如不提高料层厚度,烧结强度会降低。
燃料分加后,混合料的燃烧条件得到改善,垂直烧结速度加快,为提高料层厚度提供了条件。
本实验中50号实验的料层厚度为700mn,其烧结杯利用系数达到1.53t/(m2.h)、烧结矿转鼓指数达到71.05%、烧结矿固体燃料消耗量降至64.65kg/t、烧结矿中小于10mm粒级的烧结矿占21.34%,远低于其它实验条件。
4结论
(1)在首钢矿业公司烧结厂的原料条件下,采用燃料分加工艺后混合
料的原始透气性略低于燃料分加前,但烧结杯垂直烧结速度加快。
(2)采用燃料分加工艺必须注意燃料分加量、分加时间和混合料在烧结杯中的布料偏析情况,否则混合料粒度的过度偏析会破坏烧结过程热制度,从而降低烧结杯的利用系数和烧结矿质量。
(3)采用合适的燃料分加量、分加时间及混合料在烧结杯中的布料方式,并
适当提高料层厚度时,烧结杯利用系数、烧结矿固体燃料消耗量、ISO转鼓指数
及小于10mm粒级的烧结矿含量均优于普通小球团烧结工艺。
(4)采用燃料分加小球团烧结工艺时,烧结矿粘结相中既有高碱度烧结矿(由磁铁矿和少量赤铁矿与铁酸钙形成)的熔蚀交织结构,又有碱性球团矿(赤铁矿连晶和磁铁矿、赤铁矿与铁酸钙形成)的熔蚀结构。
各钢铁长使用烧结机情况
首钢京唐钢铁厂烧结工序,采用500平方米大型烧结机和厚料、低SiO2、低FeO烧结工艺,有助于提高烧结矿强度、质量和利用率,使烧结矿品位达到58%以上,转鼓指数达到78%以上,高炉返矿率由传统的12%降低到8%,为高炉生产提高精料水平、降低原料消耗创造了良好的条件。
在对于废气处理上,此烧结工艺将利用废气余热作为原料干燥的热能和用于点火助燃空气。
此项烧结工艺的应用,将使燃料用量由传统工艺的50千克/吨降低到43千克/吨,以达到节能减排、降低能耗,在实现烧结矿质量的同时,实现对能源的节约。
新疆八一钢铁厂2号265就烧结机
上海宝钢