铸件加工及检验.docx
《铸件加工及检验.docx》由会员分享,可在线阅读,更多相关《铸件加工及检验.docx(17页珍藏版)》请在冰豆网上搜索。
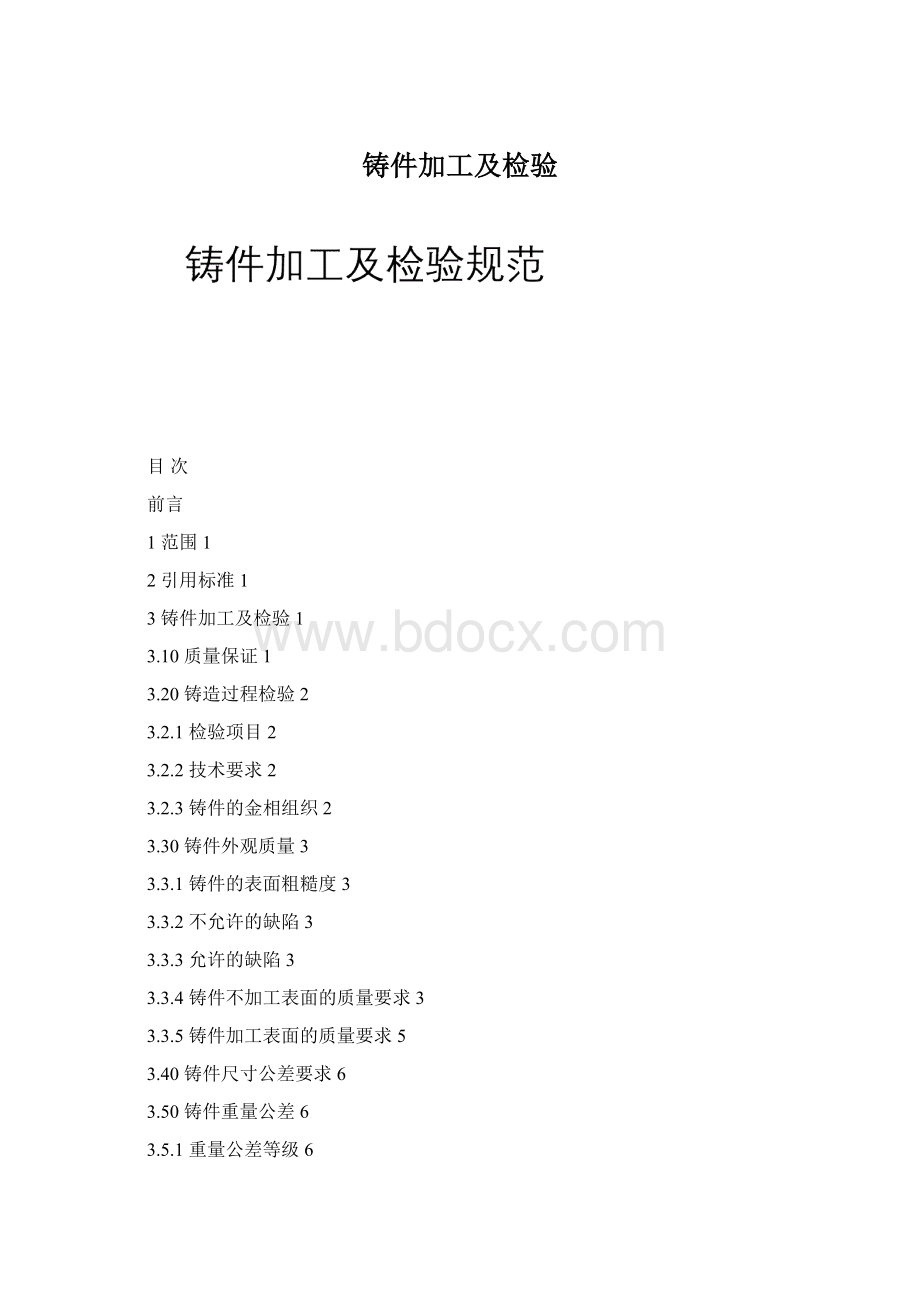
铸件加工及检验
目次
前言
1范围1
2引用标准1
3铸件加工及检验1
3.10质量保证1
3.20铸造过程检验2
3.2.1检验项目2
3.2.2技术要求2
3.2.3铸件的金相组织2
3.30铸件外观质量3
3.3.1铸件的表面粗糙度3
3.3.2不允许的缺陷3
3.3.3允许的缺陷3
3.3.4铸件不加工表面的质量要求3
3.3.5铸件加工表面的质量要求5
3.40铸件尺寸公差要求6
3.50铸件重量公差6
3.5.1重量公差等级6
3.5.2铸件重量评定7
3.60铸件内部质量验收7
3.6.1缺陷铸件处理原则7
3.70外表面质量验收7
3.80机械性能质量验收7
前言
为了提高金属结构件生产制造质量,加强对金属制品生产流程相关环节的监督检验和质量控制,保证结构件设计要求的完全贯彻和实施,特编写本系列标准。
《金属制品检验规范》为系列标准:
Q/ZX12.203.1-2001《金属制品检验规范-板金冷冲压加工及检验》
Q/ZX12.203.2-2001《金属制品检验规范-机械切削加工检验》
Q/ZX12.203.3-2001《金属制品检验规范-铸造加工及检验》
Q/ZX12.203.4-2001《金属制品检验规范-铝及铝型材加工及检验》
Q/ZX12.203.5-2001《金属制品检验规范-焊接加工及检验》
Q/ZX12.203.6-2001《金属制品检验规范-镀覆零件检验》
Q/ZX12.203.7-2001《金属制品检验规范-化学处理层的质量检验》
Q/ZX12.203.8-2001《金属制品检验规范-涂覆加工检验》
Q/ZX12.203.9-2001《金属制品检验规范-丝印加工检验》
Q/ZX12.203.10-2001《金属制品检验规范-紧固件加工检验》
Q/ZX12.203.11-2001《金属制品检验规范-机柜装配检验》
Q/ZX12.203.12-2001《金属制品检验规范-汇流排检验》
本标准是
本标准由有限公司质企中心工艺部提出,技术中心技术部归口。
本标准起草部门:
本标准起草人:
。
本标准于年月首次发布。
企业标准
(检验和试验方法技术标准)
铸件加工及检验
1范围
本标准规定了深圳市中兴通讯股份有限公司对有色金属压铸件加工过程的监督内容及成品检验的要求。
本标准适用于深圳市中兴通讯股份有限公司外协加工的各种有色金属压铸件。
2引用标准
GB228-1987金属拉伸实验方法
GB2828-1987逐批检查计数抽样程序及抽样表(适用于连续批的检查)
GB6414-1999铸件尺寸公差与机械加工余量
GB/T6987.1~6987.16-1986铝及铝合金化学分析方法
GB/T13818-1992压铸锌合金
GB/T13821-1992锌合金压铸件
GB/T13822-1992压铸有色合金试样
GB/T15056-1994铸造表面粗糙度评定方法
GB/T15114-1994铝合金压铸件
GB/T15115-1994压铸铝合金
GB/T15116-1994压铸铜合金
GB/T15117-1994铜合金压铸件
GB/T60601.1-1997表面粗糙度比较样块铸造表面
JB/T7528-1994铸件质量评定方法
JB/T7946.3-1999铸造铝合金金相铸造铝合金针孔
HB5343-1994铸造工艺质量控制
3铸件加工及检验
铸造的种类有很多,根据不同的材质、不同的铸造方法、特点和适用场合,所参照的工艺规程就有所不同。
目前我公司产品常用到的铸件主要是铝合金压铸件、锌合金压铸件,铜合金压铸件。
在生产过程中要遵照相关的国标或行标进行。
质量保证
当供需双方合同或协议中有规定时,供方应对合同中规定的所有试验或检验负责。
合同或协议中未规定,经我公司有关部门同意,供方可以用自己适宜的手段执行本标准的试验和检验要求,需方有责任对标准中的任何试验和检验项目进行检验。
铸造过程检验
铸造生产过程,变动因素很多,应根据HB5343—1994《铸造工艺质量控制》进行严格的质量控制,以保证铸件质量。
检测仪器、设备要定期进行检测。
检验人员须持有上岗证。
3.2.1检验项目
铸件的质量主要分为外部质量和内部质量。
外部质量包括表面粗糙度、尺寸公差、重量公差、表面缺陷及清理状态,内部质量包括力学性能、化学成分、金相组织、内部缺陷及耐压试验。
根据我公司产品特点,检验项目选择见表1。
表1
外部质量
选项说明
内部质量
选项说明
内、外部项目内容
表面粗糙度
重要面逐件检验,非重要面抽检
力学性能
按GB2828-1987抽检
尺寸公差
抽检
化学成分
按班次、每炉或每批为单位抽检,定期出分析报告。
表面缺陷
逐件检验
金相组织
按图纸要求决定
重量公差
当设计图纸上有要求时,按GB2828-1987抽检,一般不检。
内部缺陷
按班次、每炉或每批为单位抽检,定期出检验报告。
清理状态
逐件检验
耐压试验
视产品需求而定
3.2.2技术要求
3.2.2.1化学成分
压铸铝合金化学成分的检验应按GB6987.1-1987~GB6987.16-1987执行,化学成分应符合GB/T15115—1994中的规定。
压铸锌合金的化学成分的检验应符合GB/T13821—1994中的规定;压铸铜合金的化学成分的检验应符合GB/T15116—1994中的规定。
3.2.2.2铸件的力学性能
每批铸件应按其类别检验机械性能,呈铸态或热处理状态,压铸铝合金的力学性能检验应符合GB/T15115—1994中5.2.1表里的规定,拉力试验方法应符合GB228—1987的规定。
压铸锌合金的力学性能检验应符合GB/T13818—1992中5.2.5的规定,拉力试验方法应符合GB228—1987的规定。
铜合金压铸件的力学性能按GB/T15116—1994中5.2规定检验,拉力试验方法应符合GB228—1987的规定。
3.2.3铸件的金相组织
3.2.3.1断口检查
将铸件切断,用目视或5倍放大镜观察铸件断面有无缺陷,需要时可进行X射线透视。
3.2.3.2低倍检查
用不超过20倍的放大镜观察试样断面,主要检查内部针孔、疏松、夹渣、冷隔、裂纹、花纹等缺陷。
3.2.3.3高倍检查
用高倍显微镜检查铸件内部组织,我公司产品一般不用此项检验,除特殊需求外。
铸件外观质量
3.3.1铸件的表面粗糙度
铸造件的表面粗糙度等级参照GB/T6060.1—1997来评定,见表2。
被检铸件的铸造表面还可用视觉或触觉的方法进行比较。
非加工表面的粗糙度按图纸要求进行。
表2
粗糙度
Ra(µm)
铸型类型(金属型类)
合金种类
铜
铝
镁
锌
铸造方法(压力铸造)
0.2
○
○
0.4
○
○
○
0.8
○
●
●
1.6
○
●
●
●
3.2
○
●
●
●
6.3
●
●
●
●
12.5
●
●
●
●
25
●
●
●
●
50
●
●
●
●
注:
1○为采取特殊措施方能达到的粗糙度;
2●表示可以达到的粗糙度。
3.3.2不允许的缺陷
3.3.2.1不允许铸件上有砂眼、气孔、飞翅、欠铸、疏松、翘曲、裂纹和穿透等缺陷。
3.3.2.2表面不允许有粘附物痕迹、毛刺、气泡、顶杆痕迹。
3.3.3允许的缺陷
铸件的浇口、飞边、溢流口、隔皮、顶杆痕迹应清理干净,允许留有痕迹。
3.3.4铸件不加工表面的质量要求
3.3.4.1铸件在进行外观质量检验之前,应清理干净、平整。
3.3.4.2不允许有裂纹、欠铸和任何穿透性缺陷。
3.3.4.3铸件上的图案、文字、线条、符号必须清晰
3.3.4.4非加工面的浇冒口,应清理到与铸件表面平齐。
3.3.4.5表面花纹、麻点和有色斑点不允许超过下列表3中的规定。
根据产品使用情况,我公司装饰面选取1级,非装饰面选取2级。
表3
铸件表面质量级别
1级
2级
3级
缺陷面积不超过总面积的百分数%
5
20
40
3.3.4.6表面砂眼和气孔不允许超过下列规定,见表4、表5。
表4
缺陷类型
检验内容
检验状况
缺陷面积
缺陷个数
砂眼
无
无
合格(重要表面)
通过后序加工达到
0.2mm2
任意1平方厘米的范围内≤3个
合格(装饰面)
0.3~0.6mm2
整个被检面积≤10个(占总面积的1/6)
合格(非装饰面)
小于1mm2
任意1平方厘米的范围内≤3个
砂眼的密集性不超过所在面积的1/6
非直观面
注:
大于1mm以上的砂眼允许的数目;各产品在设计加工时,在总技术要求里具体写出。
也可与厂家协商后确定。
表5
缺陷类型
检验内容
表面质量
说明
检验状况
1级
2级
3级
气孔
平均直径
≤3mm
每100cm缺陷个数不超过
不允许
1
2
允许两种气泡同时存在,但大气泡不超过3个,总数不超过10个,且边距不小于10mm
装饰面1级,
非装饰面2级,
内表面3级。
对于第4项基带电路高频盒内底层表面1级。
合格
整个表面个数不超过
3
7
离铸件边缘距离
3
3
气泡凸起高度
0.2
0.3
平均直径
>3~6mm
每100cm缺陷个数不超过
不允许
1
1
同上
合格
整个表面个数不超过
1
3
离铸件边缘距离
5
5
气泡凸起高度
0.3
0.5
注:
1.对于1级或有特殊需求的表面,只有通过抛光或研磨去除缺陷。
2.检验时根据图纸要求或产品总技术条件来检验。
3.3.4.7各种缺陷允许范围见表6。
表6
序号
缺陷
类型
检验内容
表面质量
说明
检验状况
1级
2级
3级
1
流痕
深度不大于mm
0.05
0.07
0.15
装饰面不允许,非装饰面1~2级,内表面3级。
面积不大于总面积的%
5
15
30
2
冷隔
深度不大于mm
不允许
1/5壁厚
1/4壁厚
1.在同一部位对应处不允许同时存在。
2.长度是指缺陷流向的展开长度。
装饰面不允许,非装饰面1~2级,内表面3级。
长度不大于铸件最大轮廓尺寸的mm
1/10
1/5
所在面上不允许超过的数量
2处
2处
离铸件边缘不小于mm
4
4
两冷隔间距不小于mm
10
10
3
擦伤
深度不大于mm
0.05
0.1
0.25
浇口部位增加
一倍可接受
同上
面积不大于总面积的%
3
5
10
4
凹陷
凹陷深度不大于mm
0.1
0.3
0.5
装饰面不允许,非装饰面1~2级,内表面3级。
5
粘附物痕迹
整个铸件不允许超过
不允许
1处
2处
同上
占带缺陷的表面面积的%
5
10
6
边角残缺
深度mm
铸件边长≤100mm时
0.3
0.5
1.0
残缺长度不超过边长度的5%
装饰面不允许,非装饰面1级,内表面2级。
铸件边长>100mm时
0.5
0.8
1.2
同上
7
顶杆痕迹
凹入铸件深度不超过
1/8壁厚
装饰面不允许,非装饰面及内表面2级。
最大凹入量
≤0.4mm
凸起高度
≤0.2mm
8
网状毛刺
凸起或凹下
≤0.2mm
不利手
同上
9
各类缺陷总和
面积不超过总面积的
5
30
50
装饰面高于一级,其余介于1~2级间。
注:
根据产品总技术条件或要求进行检验
3.3.5铸件加工表面的质量要求
3.3.5.1铸件上作为基准的部位应平整,不允许有凸起的推杆痕迹。
3.3.5.2不允许有超过加工余量的表面缺陷和痕迹。
3.3.5.3加工后不允许有影响使用的局部铸志(未加工前表面不允许出现的铸件特征)表面存在。
3.3.5.4加工后不允许有超过下列表7中规定的孔穴存在。
装饰面出现一级状况时,需进行修补后,表面无孔穴或最大直径在0.12mm,占表面积的5%范围内,该表面检验合格。
非装饰面和内表面按一级验收。
表7
表面积
cm2
级别
1级
2级
3级
孔穴
最大直径
mm
最大深度
mm
最多个数
边缘间最小距离mm
最大直径
mm
最大深度
mm
最多个数
边缘间最小距离mm
最大直径
mm
最大深度
mm
最多
个数
边缘间最小距离mm
~25
0.8
0.5
3
4
1.5
1.0
3
4
2.0
1.5
3
3
>25~60
0.8
0.5
4
6
1.5
1.0
4
6
2.0
1.5
4
4
>25~150
1.0
0.5
4
6
2.0
1.5
4
6
2.5
1.5
5
4
>150~350
1.2
0.6
5
8
2.5
1.5
5
8
3.0
2.0
6
6
铸件尺寸公差要求
铸件尺寸应符合图样的要求。
铸件变形后的尺寸不得超过机加工余量或铸件本身的公差,没有标注公差的按GB/T6414—1999中的表1中第6级的精度等级规定(见表8)。
需要加工的铸件加工余量由工艺人员拟制铸件毛坯图时给出。
有特殊要求时,应在图样上注明。
表8mm
铸件尺寸公差等级CT
毛坯件基本尺寸(大于→至)
—10
10
16
16
25
25
40
40
63
63
100
100
160
160
250
250
400
400
630
630
1000
1000
1600
1600
2500
2500
4000
4000
6300
6300
10000
5
0.36
0.38
0.42
0.46
0.5
0.56
0.62
0.72
0.78
0.9
1
1.1
—
—
—
—
6
0.52
0.54
0.58
0.64
0.7
0.78
0.88
1
1.1
1.2
1.4
1.6
—
—
—
—
7
0.74
0.78
0.82
0.9
1
1.1
1.2
1.4
1.6
1.8
2
2.2
2.6
—
—
—
铸件重量公差
3.5.1重量公差等级
铸件重量也是衡量铸件是否合格的一项指标,重量公差应与尺寸公差对应选取。
例如:
尺寸公差按CT6级,重量公差按MT6级。
重量公差的下偏差也可比上偏差提高两级选用,标注方法可按GB/T11351—1989执行。
重量公差等级见表9。
表9铸件重量公差数值
公
公称重量,
Kg
重量公差数值MT
重量公差等级
1
2
3
4
5
6
7
8
9
10
11
12
13
14
15
16
>0.4
—
5
6
8
10
12
14
16
18
20
24
—
—
—
—
—
>0.4~1
—
4
5
6
8
10
12
14
16
18
20
24
—
—
—
—
>1~4
—
3
4
5
6
8
10
12
14
16
18
20
24
—
—
—
>4~10
—
2
3
4
5
6
8
10
12
14
16
18
20
24
—
—
>10~40
—
—
2
3
4
5
6
8
10
12
14
16
18
20
24
>40~100
—
—
—
2
3
4
5
6
8
10
12
14
16
18
20
24
>100~400
—
—
—
—
2
3
4
5
6
8
10
12
14
16
18
20
>400~1000
—
—
—
—
—
2
3
4
5
6
8
10
12
14
16
18
>1000~4000
—
—
—
—
—
—
2
3
4
5
6
8
10
12
14
16
>4000~10000
—
—
—
—
—
—
—
2
3
4
5
6
8
10
12
14
>10000~40000
—
—
—
—
—
—
—
—
2
3
4
5
6
8
10
12
注:
表中重量公差数值为上、下偏差之和,即一半为上偏差,一半为下偏差。
3.5.2铸件重量评定
3.5.2.1当有重量的公差作为验收要求时,应在图纸中或技术文件中写明。
3.5.2.2铸件有重量要求时,实际重量小于或等于公称重量与重量公差的上偏差或下偏差之和时(T实≤T公称+
),则铸件重量公差合格。
3.5.2.3铸件的公称重量与待检铸件的重量应选择同一精度等级的计量器具称量。
3.5.2.4公称重量在首批加工的供需双方认定的合格产品中任取3件,实称每一件重量然后将其相加平均,用该平均值作为公称重量。
铸件内部质量验收
对于内部质量,力学性能、化学成分、金相组织,在半年时间内随机抽检任意两个月的供方检验报告。
要符合国标的要求,内部缺陷每批次抽检3件,若都合格验收通过。
若抽检的3件中有1件不合格,需再增加3件检验,这3件都合格,方可通过。
如仍有1件不合格,该批次产品都拒收。
耐压试验根据产品设计要求来确定是否做检测。
3.6.1缺陷铸件处理原则
铸件若能满足使用要求,则铸件内部缺陷不作为报废的依据。
当征得我司设计人员同意,供方可以对铸件进行浸渗和修补处理。
经修补后的铸件还应作相应的质量检验。
合格品接收;不合格品拒收。
外表面质量验收
对于外部质量,要求每批产品逐件检。
检验项目见表1中所列。
机械性能质量验收
机械性能检测每批次产品抽样检验,提供三根试样做检测,若有1根性能不合格,再提供3根试样;若第二次仍有1根不合格,该批次产品拒收,予以报废。
并找出原因,采取预防措施。
机械性能的具体要求请参见3.2.2.2。
3.8.1.1拉力试样
试样件制作按GB/T13822—1992执行。
a)A型拉力试样
A型拉力试样的形状与尺寸应符合图1的规定,适用于测定抗拉强度和伸长率。
图1
b)B型拉力试样
B型拉力试样的形状与尺寸应符合图2的规定,适用于抗拉强度比较试验和硬度测定。
图2
3.8.1.2冲击韧性试样
冲击韧性试样的形状与尺寸应符合图3的规定,适用于冲击韧性试验,试验前截为两根。
试验时摆锤冲击在试样最窄面。
图3