铝及铝合金的焊接性分析.docx
《铝及铝合金的焊接性分析.docx》由会员分享,可在线阅读,更多相关《铝及铝合金的焊接性分析.docx(8页珍藏版)》请在冰豆网上搜索。
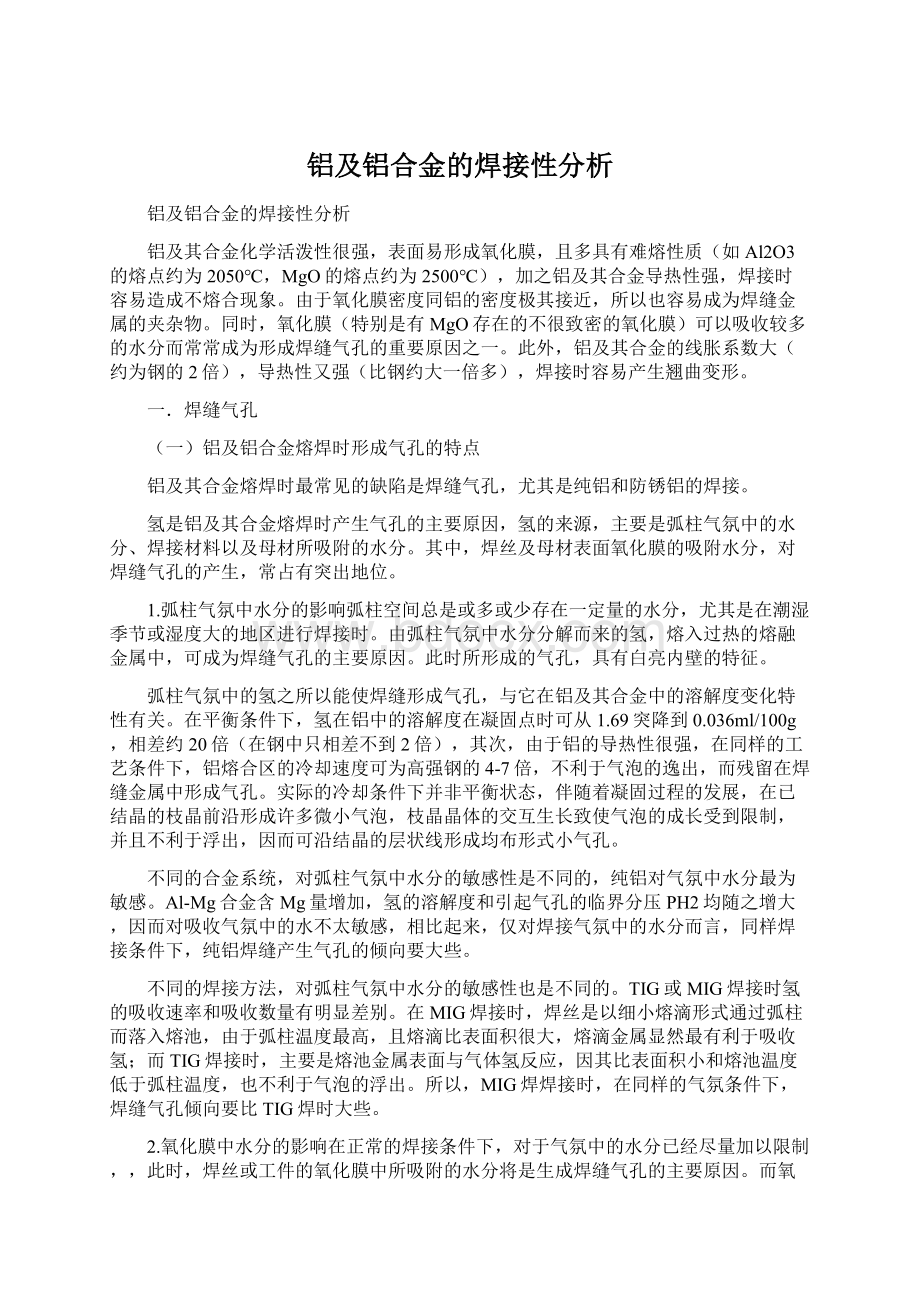
铝及铝合金的焊接性分析
铝及铝合金的焊接性分析
铝及其合金化学活泼性很强,表面易形成氧化膜,且多具有难熔性质(如Al2O3的熔点约为2050℃,MgO的熔点约为2500℃),加之铝及其合金导热性强,焊接时容易造成不熔合现象。
由于氧化膜密度同铝的密度极其接近,所以也容易成为焊缝金属的夹杂物。
同时,氧化膜(特别是有MgO存在的不很致密的氧化膜)可以吸收较多的水分而常常成为形成焊缝气孔的重要原因之一。
此外,铝及其合金的线胀系数大(约为钢的2倍),导热性又强(比钢约大一倍多),焊接时容易产生翘曲变形。
一.焊缝气孔
(一)铝及铝合金熔焊时形成气孔的特点
铝及其合金熔焊时最常见的缺陷是焊缝气孔,尤其是纯铝和防锈铝的焊接。
氢是铝及其合金熔焊时产生气孔的主要原因,氢的来源,主要是弧柱气氛中的水分、焊接材料以及母材所吸附的水分。
其中,焊丝及母材表面氧化膜的吸附水分,对焊缝气孔的产生,常占有突出地位。
1.弧柱气氛中水分的影响弧柱空间总是或多或少存在一定量的水分,尤其是在潮湿季节或湿度大的地区进行焊接时。
由弧柱气氛中水分分解而来的氢,熔入过热的熔融金属中,可成为焊缝气孔的主要原因。
此时所形成的气孔,具有白亮内壁的特征。
弧柱气氛中的氢之所以能使焊缝形成气孔,与它在铝及其合金中的溶解度变化特性有关。
在平衡条件下,氢在铝中的溶解度在凝固点时可从1.69突降到0.036ml/100g,相差约20倍(在钢中只相差不到2倍),其次,由于铝的导热性很强,在同样的工艺条件下,铝熔合区的冷却速度可为高强钢的4-7倍,不利于气泡的逸出,而残留在焊缝金属中形成气孔。
实际的冷却条件下并非平衡状态,伴随着凝固过程的发展,在已结晶的枝晶前沿形成许多微小气泡,枝晶晶体的交互生长致使气泡的成长受到限制,并且不利于浮出,因而可沿结晶的层状线形成均布形式小气孔。
不同的合金系统,对弧柱气氛中水分的敏感性是不同的,纯铝对气氛中水分最为敏感。
Al-Mg合金含Mg量增加,氢的溶解度和引起气孔的临界分压PH2均随之增大,因而对吸收气氛中的水不太敏感,相比起来,仅对焊接气氛中的水分而言,同样焊接条件下,纯铝焊缝产生气孔的倾向要大些。
不同的焊接方法,对弧柱气氛中水分的敏感性也是不同的。
TIG或MIG焊接时氢的吸收速率和吸收数量有明显差别。
在MIG焊接时,焊丝是以细小熔滴形式通过弧柱而落入熔池,由于弧柱温度最高,且熔滴比表面积很大,熔滴金属显然最有利于吸收氢;而TIG焊接时,主要是熔池金属表面与气体氢反应,因其比表面积小和熔池温度低于弧柱温度,也不利于气泡的浮出。
所以,MIG焊焊接时,在同样的气氛条件下,焊缝气孔倾向要比TIG焊时大些。
2.氧化膜中水分的影响在正常的焊接条件下,对于气氛中的水分已经尽量加以限制,,此时,焊丝或工件的氧化膜中所吸附的水分将是生成焊缝气孔的主要原因。
而氧化膜不致密、吸水性强的铝合金(主要是Al-Mg合金),要比氧化膜致密的纯铝具有更大的气孔倾向。
这是因为Al-Mg合金的氧化膜是由Al2O3和MgO所构成,而MgO越多,形成的氧化膜越不致密,因而更易吸收水分;纯铝的氧化膜只是由Al2O3构成,比较致密,相对吸水性要小。
在MIG焊接时,焊丝表面氧化膜的作用将具有重要意义。
MIG焊接时,由于熔深较大,工件坡口端部的氧化膜能迅速的熔化掉,有利于氧化膜中水分的排除,坡口氧化膜对焊缝气孔的影响就小得多。
焊丝表面氧化膜的清理情况对焊缝含氢量的影响是比较大的,若是用Al-Mg合金焊丝,这种影响必更显著。
实践证明,在严格限制弧柱气氛水分的MIG焊接条件下,用Al-Mg合金焊丝比用纯铝焊丝时具有较大的气孔倾向。
TIG焊接时,在熔透不足的情况下,母材坡口根部未除净的氧化膜中所吸附的水分,常常是产生焊缝气孔的主要原因。
这种氧化膜不仅提供了氢的来源,而且能使气泡聚集附着。
在刚刚形成熔池时,如果坡口附近的氧化膜未能完全熔化而残存下来,则氧化膜中水分因受热而分解出氢,并在氧化膜上萌生气泡;由于气泡是附着在残留氧化膜上的,不容易脱离浮出,而且还因气泡是在熔化的早期形成的,有条件长大,所以常常造成几种形式的大气孔。
这种气孔在焊缝根部有未熔合时就更严重。
坡口端部氧化膜引起的气孔,常常沿着熔合区原破口边缘分布,且内壁呈氧化色彩,使其重要特征。
由于Al-Mg合金比纯铝更易形成疏松而吸水性强的厚氧化膜,所以Al-Mg合金要比纯铝更容易产生这种集中形式的氧化膜气孔。
因此,焊接铝镁合金时,焊前必须他别仔细的清除坡口端部的氧化膜。
3.母材表面氧化膜也会在近缝区引起“气孔”,主要发现于Al-Mg合金气焊的条件下,实际上在用气焊火焰沿板表面加热一道后,也能看到这种现象。
这种“气孔”往往以表面密集的小颗粒状的“鼓泡”形式呈现出来,也可认为是“皮下气孔”。
(二)防止焊缝气孔的途径
为了防止焊缝气孔,可从两方面着手:
第一,限制氢溶入熔融金属,或者是减少氢的来源,或者减少氢同熔融金属作用的时间(如减少熔池吸氢时间);第二,尽量促使氢自熔池逸出,即在熔池凝固之前使氢以气泡形式及时排除,这就要改善冷却条件以增加氢的逸出时间(如增大熔池析氢时间)。
显然,熔池存在时间对氢的熔入和逸出的影响是有矛盾的。
在这种情况下,尽量限制氢的来源有着现实的意义。
1.减少氢的来源所有使用的焊接材料(包括保护气体、焊丝、焊条等)要严格限制含水量,使用前均需干燥处理。
一般认为,氩气中的含水量小于0.08%时不易形成气孔。
氩气的管路也要保持干燥。
焊前处理工作十分重要。
焊丝及母材表面氧化膜应彻底清除,采用化学方法或机械方法均可,两者并用,效果更佳。
在LF2手工TIG焊接时,仅经过化学清洗未能防止产生气孔。
化学清洗后,焊前应用细钢丝刷再全面刷一遍近缝区,并用刮刀刮削破口断面,装配时要防止再度弄脏;
化学清洗有两个步骤:
脱脂去油和除氧化膜。
清洗后应烘干。
需要注意的是,清洗后到焊前的时间间隔(即存放时间)对气孔的产生有影响。
存放时间延长,焊丝或母材吸附的水分即增多。
所以,化学清洗后最好及时施焊。
对于大型构件,清洗后做不到及时施焊时,临焊前应再用刮刀刮削坡口端面为宜。
将坡口下端(根部)刮去一个倒角(成为V形小坡口),对于防止根部氧化膜引起的气孔是比较有效的。
焊接时铲根极有利于减少焊缝气孔的倾向。
在MIG焊接时,采用粗直径焊丝,比用细直径焊丝时的气孔倾向小些,因为这使焊丝及熔滴比表面积降低了。
2.控制焊接工艺焊接工艺参数的影响主要可归结为对熔池在高温存在时间的影响,也就是对氢的溶入时间和氢的析出时间的影响。
熔池在高温存在时间增长,有利于氢的逸出,但也有利于氢的溶入;反之,熔池在高温存在时间减少,固然可以减少氢的溶入,但也不利于氢的逸出,焊接工艺参数调整不当时,如造成氢的溶入数量多而又不利于逸出时,气孔倾向势必增大。
在TIG焊接时,焊接工艺参数的选择,一方面要尽量采用小线能量以减少熔池存在时间,从而减少气氛中氢的溶入,因而须适当的提高焊接速度;但同时又要能充分保证根部的熔合,以利于根部氧化膜上气泡的逸出,因而又须适当的增大焊接电流。
实践证明,采用大的焊接电流配合较高的焊接速度是比较有利的。
因为,焊接电流不够大,焊接速度又比较高时,根部氧化膜不易熔掉,气体也不易排出。
气孔倾向必然增大。
而当焊接电流不够大时,放慢焊接速度,由于有利于熔池排出气体,气孔倾向也可有所减小,但却不利于根部的熔合,氧化膜中的水分的影响显著,气孔的倾向仍然比较大。
在MIG焊接条件下,焊丝氧化膜的影响更为主要,减少熔池存在时间,难以有效地防止焊丝氧化膜分解出来的氢向熔池侵入,因此一般希望增大熔池存在时间以利于气泡的逸出。
从此点出发,降低焊接速度和提高线能量,有利于减少焊缝中的气孔,实践中,薄板焊接时,焊接线能量的增大确实可以减少焊缝中的气体含量,但在中厚板焊接时,由于接头冷却速度已经比较大,线能量增的后的影响并不明显。
此外比较接头形式可以看出,由于T形接头的冷却速度约为对接接头的1.5倍,在同样的线能量条件下焊接薄板时,较对接接头的焊缝气孔含量高得多。
中厚板焊接时,由于实际上不可能采用相同的焊接工艺参数,不可能完全对比,但是仍可得出,T形接头饿焊缝是含有较多气孔的。
可见,在MIG焊接条件下,接头的冷却条件对焊缝的气体含量有比较明显的影响。
由此,必要时可采取预热的办法来降低接头冷却速度。
以利于气体逸出,对减少焊缝的气孔生成倾向有一定的好处。
二.焊接热裂纹
铝及其合金焊接时,常见到的热裂纹主要是焊缝金属凝固裂纹,有时也可在近缝区见到液化裂纹。
(一)铝合金焊接热裂纹的特点
铝合金属于典型的共晶合金。
最大裂纹倾向正好与合金的“最大凝固温度区间”相对应。
但这与实际却不甚相符,这是因为实际焊接时的加热和冷却过程都很迅速,使合金来不及建立平衡状态。
铝合金的线胀系数比钢约大2倍,在拘束条件下焊接时易产生较大的焊接应力,也是促使铝合金具有较大裂纹倾向的原因之一。
(二)防止焊接热裂纹的途径
母材的合金系统及其具体成分,对焊接热裂纹的产生有根本性的影响。
对于焊接金属的凝固裂纹的控制:
1.合金系统的影响
调整焊缝合金系统的着眼点,从抗裂角度考虑,在于控制适量的易熔共晶并缩小结晶温度区间。
由于现有铝合金均为共晶型合金,少量易熔共晶的存在总是增大凝固裂纹倾向,所以,一般都是在主要合金元素含量超过,以便能产生“愈合”作用。
在不同的防锈铝在TIG焊接时,填送不同的焊丝以获得不同Mg含量的焊缝,焊缝便具有不同的抗裂性能。
Al-Mg合金板焊接时,以采用含Mg量超过3.5%或有的超过5%的焊丝为好。
2.焊丝成分的影响
不同的母材配合不同的焊丝,具有不同的裂纹倾向。
如采用5083作为母材时,焊丝5356是适用的。
3.焊接工艺参数的影响
焊接工艺参数影响凝固过程的不平衡性和凝固的组织状态,也影响凝固过程中应变的增长速度,因而影响裂纹的产生。
热能集中的焊接方法,有利于快速进行焊接过程,可防止形成方向性强的粗大柱状晶。
因而可以改善抗裂性。
采用小的焊接电流,可减少熔池过热,也有利于改善抗裂性。
焊接速度的提高,促使增大焊接接头的应变速度,增大裂纹的倾向。
因此,增大焊接速度和焊接电流,都促使增大裂纹倾向。
由于大部分铝合金的裂纹倾向都比较大,所以,即使是采用合理的焊丝,但在熔合比大时,母材在焊缝中的比例大,从此点看,增大焊接电流也是不利的。
三.焊接接头的“等强性”
非时效强化的铝合金(如Al-Mg合金),在退火状态下焊接时,可以认为接头同母材是等强的;在冷作硬化状态下焊接时,接头强度低于母材。
表明在冷作状态下焊接时接头有软化现象。
时效强化铝合金,无论是在退火状态下还是时效状态下焊接,焊后不经过热处理,其接头强度均低于母材。
特别是在时效状态下焊接的硬铝,即使焊后经过人工时效处理,其接头强度系数(即接头的强度于母材强度之比的百分数)也未超过60%。
所有时效强化的铝合金,焊后不论是否经过时效处理,其接头塑性均未能达到母材的水平。
铝合金焊接时的这种不等强性的表现,说明焊接接头发生了某种程度的软化或存在某一性能上的消弱。
接头性能上的薄弱环节可以存在于焊缝,熔合区或热影响区三个区域中的一个区域之中。
就焊缝而言,由于是铸造组织,即使在退火状态以及焊缝成分同母材基本一样的条件下,强度可能差别不大,但焊缝塑性一般都不如母材。
若焊缝成分不同于母材,焊缝性能将主要决定于所选用的焊接材料。
为保证焊缝强度与塑性,固溶强化型合金系统要优于共晶型合金系统。
例如用LT1(Al-5%Si)焊丝焊接硬铝,接头强度及塑性在焊态下远远低于母材。
共晶数量越多,焊缝塑性越差。
另外,焊接工艺条件也有一定影响,如在多层焊时,后一层焊道可使前一层焊道重熔一部分,由于没有同素异构转变,不仅看不到象钢材多层焊时的层间晶粒微细化的现象,还可发生缺陷的积累,特别是在层间温度过高时,甚至可能使层间出现热裂纹,一般来说,焊接线能量越大,寒风性能下降的趋势也越大。
对于熔合区,非时效强化铝合金的主要问题是晶粒粗化而降低塑性,在时效强化铝合金焊接时,除了晶粒粗化,还可能因晶界液化而产生显微裂纹,所以熔合区的变化主要是恶化塑性。
热影响区(HAZ),无论是时效强化的合金还是非时效强化的合金,主要表现为强化效果的损失,即软化。
(一)非时效强化铝合金HAZ的软化
主要发生在焊前冷作硬化的合金上,经冷作硬化的铝合金,热影响区的峰值温度超过再结晶温度(200~300℃)时的区域就会产生明显的软化现象,接头的软化主要取决于加热的峰值温度,而冷却速度的影响不很明显。
由于软化后的硬度实际已低到退火状态的硬度水平,因此,焊前冷作硬化程度越高,焊后软化的程度就越显得大,板件越薄,这种影响越显著。
冷作硬化薄板铝合金的强化效果,焊后可能全部丧失,对于熔焊工艺来说,这是不可避免的结果。
(二)时效强化铝合金(HAZ)的软化
总的看来,主要是焊接热影响区“过时效”软化问题。
这是熔焊条件下不可避免的现象,其严重程度决定于合金第二相的性质,也与焊接热循环有一定的关系,最根本的就是第二相对时效反应的敏感性,第二相越容易于脱熔析出并易于聚集长大时,就越是容易发生“过时效”。
时效强化的铝合金中的超硬铝也和硬铝类似,热影响区有明显的软化现象,因此,对于时效强化合金,为防止热影响区软化,宜于采用小的焊接线能量。
一般,时效强化铝合金焊后不经完全的固溶和人工时效处理,性能总是不理想的。
四.焊接接头的耐蚀性
焊接接头的耐蚀性一般都低于母材,热处理强化铝合金(如硬铝)接头的耐蚀性能的降低尤其明显。
接头组织越不均匀,越易降低耐蚀性。
焊缝金属的纯度和致密性也是影响接头耐蚀的因素之一,杂质较多,晶粒粗大以及脆性相(如FeAl3)析出等,耐蚀性就会明显下降,不仅产生局部的表面腐蚀。
而且经常出现晶间腐蚀。
对于铝合金,焊接应力更是影响耐蚀性的敏感因素。
改善接头耐蚀性能的措施:
1.改善接头组织的成分的不均匀性主要是通过焊接材料使焊缝合金化,细化晶粒并防止缺陷;同时调整焊接工艺以减小热影响区,并防止过热。
焊后热处理有很好的效果。
2.消除焊接应力局部表面拉应力也可采用局部锤击办法来消除。
3.采取防护措施
铝及其合金的焊接工艺
一、焊接工艺一般特点
铝:
面心立方晶格,无同素异构转变,无低温脆性转变,强度低,塑性高。
表面易形成致密的Al2O3保护膜,耐蚀性好。
比强度高(抗拉强度/密度)铝及其合金的导热性强而热容量大,熔化潜热高,导电,导热以及在低温下能保持良好的力学性能。
同时,铝及其合金线胀系数大,熔点低(纯铝660℃)和高温强度小,给焊接工艺带来一定困难。
首先,必须采用能量集中的热源,以保证熔合良好;其次,要采用垫板和夹具,以保证装配质量和防止焊接变形。
另外,铝及其合金由固态转变为液态时并无颜色的变化,因此也不易确定接缝的坡口是否熔化,造成焊接操作上的困难。
同时,铝合金中的Mg、Zn、Mn均易蒸发,不仅影响焊接性能,也影响焊接操作。
铝与氧亲和力很大,铝及其合金表面极易形成难熔的氧化膜,不仅妨碍焊接并易形成夹杂物,而且还因吸附大量水分而促使焊缝产生气孔。
因此,焊前清理焊丝和母材的氧化膜,对焊接质量有极为重要的影响。
除了焊前采用化学和机械的方法清理之外,焊接过程中还必须加强保护,在氩弧焊时还特别利用“阴极清理”作用。
在气焊或其他熔焊方法时,都需要采用能除去氧化膜的焊剂。
这些焊剂都是由氯化物和氟化物所组成。
对铝及其合金有很强的腐蚀性,因此,焊后要彻底清除残渣,并且在使用此类焊剂时,应避免采用搭接形式的接头,以免残渣落入板的间隙中无法除去。
原则上同结构钢焊接时并无不同,波板焊接时一般不开坡口(手弧焊时在板厚3~4mm以内,自动焊时板厚在6mm以内)。
如果采用大功率焊接时,不开坡口而可焊透的厚度还可以增大。
厚度小于3mm时还可以采用卷边接头,主要问题是考虑能充分去除氧化膜。
二、焊接工艺的制定
各种熔焊方法以氩弧焊的应用最为广泛。
焊接薄板多应用TIG焊法,MIG焊法主要应用于板厚在3mm以上的焊接上。
铝合金氩弧焊时,氩气的纯度要控制在99.9%以上,其中限制杂质:
氧在0.005%以下,氢0.005以下,水分0.02mg/L以下,氮0.015%以下。
氧、氮增多,均恶化阴极清理作用。
氧超过0.3%则使钨极烧损加剧,超过0.1%氧则使焊缝表面无光泽或发黑。
氮超过0.05%。
熔池的流动性变坏,焊缝表面成型不良。
钨极一般采用含钍钨极,焊接电流应有所限制。
过大的电流会使钨极烧损,并可造成焊缝夹钨。
为了防止钨极烧,在直流反接(DCRP)焊时,电流要限制的很小,而采用直流正接时有无阴极清理作用。
所以,TIG焊接时一般都采用交流电源。
但由于大厚度铝合金焊接的需要,也在研究应用直流正接的TIG焊接方法。
主要是利用其熔深大的特点,同时焊缝截面成形好且气孔倾向相对较小,因此可降低对阴极清理的要求
MIG焊接时,一般采用DCRP,但所选用的焊接电流一般希望超过“临界电流”值,以便获得稳定的喷射过度的电弧过程。
MIG焊接时,为了获得喷射过渡,由于临界电流的限制,焊接板厚小于3mm时就必须采用很细的焊丝,这在送丝上造成很大的困难。
因此,板厚在3mm以下的构建一般不采用MIG焊焊接方法。
此时熔化极脉冲氩弧焊在薄板焊接上则有其优越性。
MIG焊用于厚板铝合金是有优越性的,但电流超过300~400A以上时焊缝表面容易产生“皱皮”或“起皱”
在TIG对接焊接时,在一定的钨极直径下电流增大,焊接速度也相应提高,在变动焊接速度时,气体流量也要与之相匹配,送丝速度也要相应的调整(填充汉斯送进速度可在0.16~2.0m/min之间变动)。
功率一定时,焊接速度海域焊件厚度有关,手工焊时可在0.065~0.25m/min间变动,自动焊时可在0.25~0.50m/min之间变动。
MIG焊接时,焊接速度可以在很大的范围内变化,一般为0.15~1.50m/min。
而焊丝送进速度可以在更大的范围内变动,一般为1.1~10.0m/min。
焊接电流必须适当,关键是确定临界电流,铝合金焊丝(直径ds)一般使用电流(I)及相应的送丝速度(vs),大体如表1所示,临界电流(Ic)与合金种类及焊丝直径(ds)有关。
表1铝合金焊丝的使用电流和送丝速度ds(mm)
ds(mm)
I(A)
vs(m/min)
0.8
40~170
4.5~20
1.2
100~200
4.2~12
1.6
150~290
3.5~10
2.4
220~350
2.5~5.5
在一定电流下送丝速度应等于熔化速度,若焊丝送进速度过大,焊丝未熔化就送入熔池可发生“粘丝”现象。
反之,送丝速度过小,电弧将拉长,可能导致喷嘴的“回烧”现象。
在送丝速度一定时,当电弧电压降低(电弧缩短)时,为了维持给定的送丝速度,焊接电流急剧减少;而在焊接电流一定的条件下。
为适应电弧缩短,在给定的送丝速度下,焊丝的熔化速度必然显著增大。
当电弧缩短到好像潜入熔池时,就成为所谓“下潜电弧”大电流焊接法。
层间温度的控制有重要作用,层间温度的增高,不仅接头强度下降,甚至降低塑性,还可促使产生微裂纹的倾向增大。
焊丝的选用
1.同质焊丝焊丝成分与母材成分相同,甚至可以把从母材上切下的板条作为填充金属使用。
2.异质焊丝主要是为适应抗裂性的要求而研制的焊丝,其成分与母材有较大的差异。
铝合金焊丝的选择常须考虑的几点是:
1>抗裂型;2>强度;3>耐蚀性;4>稀释性;5>颜色;
为了保证不产生裂纹,常不得不采用“超合金化”焊丝;但从耐蚀性考虑,往往须限定某些合金元素含量。
此外,选择焊丝时不能忽略焊丝对母材的稀释作用。
总结:
1.铝的导热系数比钢约大一倍多,而且比热容较大。
焊接同等厚度的铝及铝合金要比钢消耗更多的热量。
为了保证接头处融合良好,应采用能量集中、功率密度大的热源。
2.铝及其合金在高温下强度低、韧性差,以致不能支撑熔池中液态金属的重量,使焊缝底部形成塌陷或烧穿,在焊接薄板时应采用夹具和垫板。
3.铝及非热处理强化铝合金从固态到液态,无同素异构转变,在无其他细化晶粒措施的情况下,易形成较大的晶粒,在焊接热循环的作用下,热影响区性能的变化、焊材中元素的烧损及母材与焊缝成分的差异等,导致接头的耐蚀性低于母材,热处理强化铝合金尤为明显。
4.铝及其合金的线膨胀系数较大,约是钢的两倍,经过焊接加热、熔化、凝固易产生较大的内应力,结晶区间大的共晶型铝合金热裂纹倾向较大。
生产中常采用调整焊丝合金系统,增加易熔共晶的数量,产生“愈合”作用。
另外常采用加入变质剂Ti、Zr、V、B等产生包晶反应,形成难熔的化合物,细化晶粒;限制有害杂质的含量。
改变Fe、Si化合物的分布,正确选择焊接方法和工艺参数等来防止热裂纹。
5.在铝及铝合金焊缝中形成气孔的气体主要是氢,氢的主要来源于Al2O3膜的吸附水和弧柱中的水蒸气,防治措施如下:
①限制焊材含水量,采用干燥处理,氩气含水量要求小于0.08%,杂质含量小于0.05%;焊前清除母材及汉斯表面的氧化膜,清除后的母材和焊丝最好在2~3h内焊接,最多不超过24h,焊丝清除后最好放在150~200℃烘箱中,随取随用。
②加强正、背面保护,配合坡口刮削,清除根部氧化膜,可以有效的防止气孔。
③TIG焊选用大的焊接电流配合较高的焊接速度。
④MIG焊选用大的焊接电流,慢的焊接速度,以提到荣吃的存在时间。
⑤在氩气中加入少量的CO2和O2等氧化性气体,使氢发生氧化而降低氢的分压等。