基于PLC水塔水位控制系统的设计.docx
《基于PLC水塔水位控制系统的设计.docx》由会员分享,可在线阅读,更多相关《基于PLC水塔水位控制系统的设计.docx(15页珍藏版)》请在冰豆网上搜索。
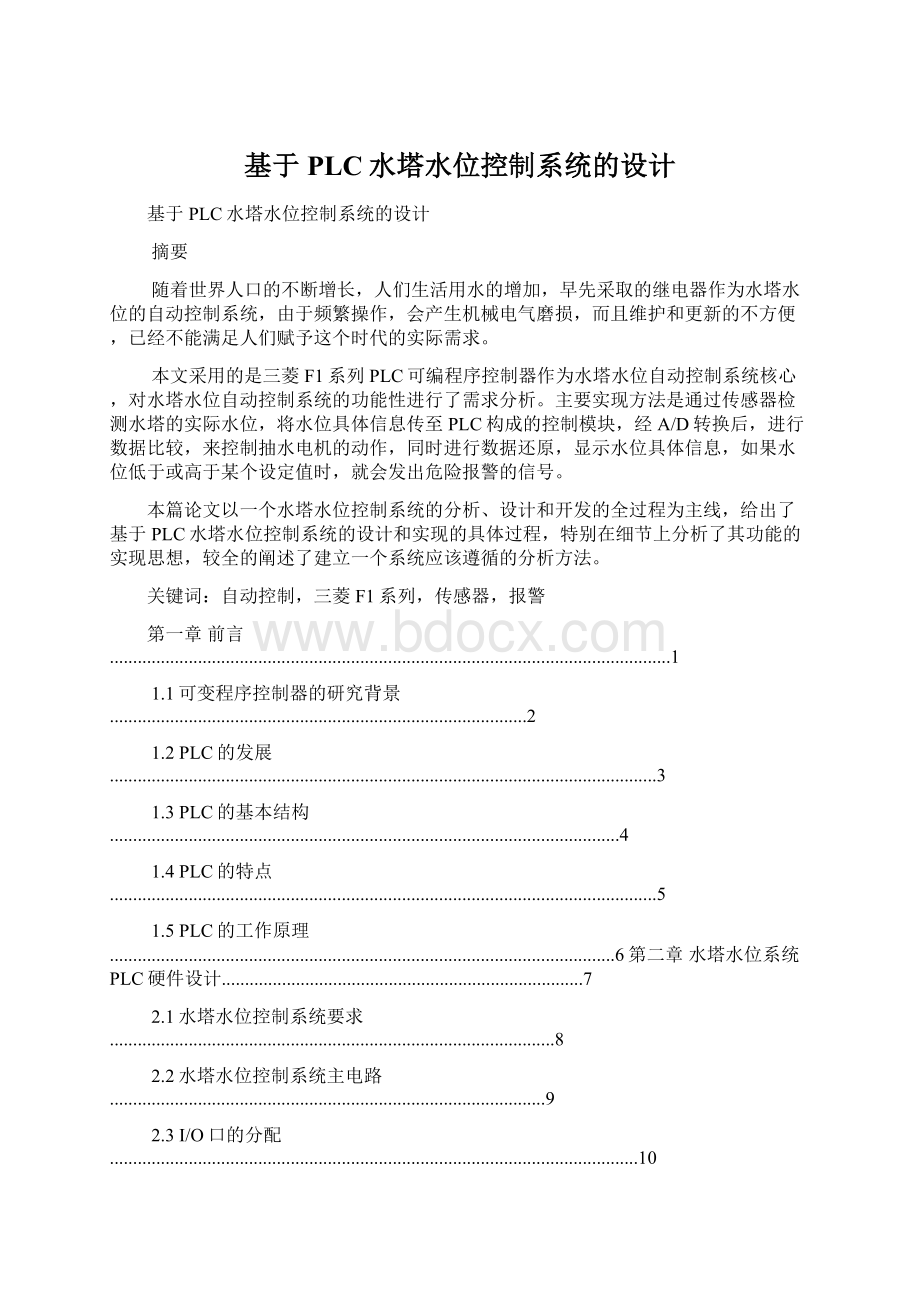
基于PLC水塔水位控制系统的设计
基于PLC水塔水位控制系统的设计
摘要
随着世界人口的不断增长,人们生活用水的增加,早先采取的继电器作为水塔水位的自动控制系统,由于频繁操作,会产生机械电气磨损,而且维护和更新的不方便,已经不能满足人们赋予这个时代的实际需求。
本文采用的是三菱F1系列PLC可编程序控制器作为水塔水位自动控制系统核心,对水塔水位自动控制系统的功能性进行了需求分析。
主要实现方法是通过传感器检测水塔的实际水位,将水位具体信息传至PLC构成的控制模块,经A/D转换后,进行数据比较,来控制抽水电机的动作,同时进行数据还原,显示水位具体信息,如果水位低于或高于某个设定值时,就会发出危险报警的信号。
本篇论文以一个水塔水位控制系统的分析、设计和开发的全过程为主线,给出了基于PLC水塔水位控制系统的设计和实现的具体过程,特别在细节上分析了其功能的实现思想,较全的阐述了建立一个系统应该遵循的分析方法。
关键词:
自动控制,三菱F1系列,传感器,报警
第一章前言.........................................................................................................................1
1.1可变程序控制器的研究背景..........................................................................................2
1.2PLC的发展......................................................................................................................3
1.3PLC的基本结构..............................................................................................................4
1.4PLC的特点......................................................................................................................5
1.5PLC的工作原理.............................................................................................................6第二章水塔水位系统PLC硬件设计..............................................................................7
2.1水塔水位控制系统要求................................................................................................8
2.2水塔水位控制系统主电路..............................................................................................9
2.3I/O口的分配..................................................................................................................10
2.4水塔水位系统的输入/输出设备...................................................................................11第三章水塔水位系统的PLC软件设计.........................................................................12
3.1水位控制系统的工作过程...........................................................................................13
3.2程序流程图....................................................................................................................14
3.3梯形图...........................................................................................................................15
3.4指令表...........................................................................................................................16
第四章总结....................................................................................................................18参考文献.......................................................................................................................................19
致谢.................................................................................................................................................20
第一章前言
1.1可变程序控制器的产生背景
可编程控制器是二十世纪七十年代发展起来的控制设备,是集微处理器、储存器、输入/输出接口与中断于一体的器件,已经被广泛应用于机械制造、冶金、化工、能源、交通等各个行业。
计算机在操作系统、应用软件、通行能力上的飞速发展,大大加强了可编程控制器通信能力,丰富了可编程控制器编程软件和编程技巧,增强了PLC过程控制能力。
因此,无论是单机还是多机控制、是流水线控制还是过程控制,都可以采用可编程控制器,推广和普及可编程控制器的使用技术,对提高我国工业自动化生产及生产效率都有十分重要的意义。
可编程控制器(ProgrammableController)也可称逻辑控制器(ProgrammableLogicController),是一微处理器为核心的工业自动控制通用装置,是计算机家族的一名成员,简称PC。
为了与个人电脑(也简称PC)相混淆通常将可编程控制器称为PLC。
可编程控制器的产生和继电器—接触器控制系统有很大的关系。
继电器—接触器控制已经有百年的历史,它是一种弱电信号控制强电信号的电磁开关,具有结构简单、电路直观、价格低廉、容易操作、易于维修的有优点。
对于工作模式固定、要求比较简单的场合非常使用,至今仍有广泛的用途。
但是当工作模式改变时,就必须改变系统的硬件接线,控制柜中的物件以及接线都要作相应的变动,改造工期长、费用高,用户宁愿扔掉旧控制柜,另做一个新控制柜使用,阻碍了产品更新换代。
随着工业生产的迅速发展,市场竞争的激烈,产品更新换代的周期日益缩短,工业生产从大批量、少品种,向小批量、多品种转换,继电器—接触器控制难以满足市场要求,此问题首先被美国通用汽车公司(GM公司)提了出来。
通用汽车公司为适合汽车型号的不断翻新,满足用户对产品多样性的需求,公开对外招标,要求制造一种新的工业控制装置,取代传统的继电器—接触器控制。
其对新装置性能提出的要求就是著名的GM10条,即:
1.编程方便,现场可修改程序;
2.维修方便,采用模块化结构;
3.可靠性高于继电器控制装置;
4.体积小于继电器控制装置;
5.数据可直接送入管理计算机;
6.成本可与继电器控制装置竞争;
7.输入可以是交流115V;
8.输出为交流115V,2A以上,能直接驱动电磁阀,接触器等;
9.在扩展时,原系统只要很小变更;
10.用户程序存储器容量至少能扩展到4K。
这十项指标就是现代PLC的最基本功能,值得注意的是PLC并不等同于普通计算机,它与有关的外部设备,按照“易于与工业控制系统连成一体”和“便于扩充功能”的原则来设计。
用可编程控制器代替了继电器—接触器的控制,实现了逻辑控制功能,并且具有计算机功能灵活、通用性等特点,用程序代替硬接线,并且具有计算机功能灵活、通用性能强等优点,用程序代替硬接线,减少了重新设计,重新接线的工作,此种控制器借鉴计算机的高级语言,利用面向控制过程,面向问题的“自然语言”编程,其标志性语言是极易为IT电器人员掌握的梯形图语言,使得熟悉计算机的人也能方便地使用。
这样,工作人员不必在变更上花费大量地精力,只需集中精力去考虑如何操作并发挥更改装置地功能即可,输入、输出电平与市电接口,使控制系统可方便地在需要的地方运行。
所以,可编程控制器广泛地应用于各个工业领域。
1.2PLC的发展
虽然PLC问世时间不长,但是随着微处理器的出现,大规模,超大规模集成电路技术的迅速发展和数据通讯技术的不断进步,PLC也迅速发展,其发展过程大致可分为三各阶段:
早期的PLC一般称为可编程逻辑控制器。
这时的PLC也就是继电器控制装置的替代物的含义,其主要功能只是执行原先由继电器完成的顺序控制、定时等。
它在硬件上以计算机的形式出现,在I/O接口电路上作了改进以适应工业控制现场的要求。
装置中的器件主要采用分离元件和中小规模集成电路,存储器采用磁芯存储器。
另外还采取了一些措施,以提高其抗干扰的能力。
在软件编程上采用广大电器工程技术人员所熟悉的继电器控制线路的方式—梯形图。
因此,早期的PLC的性能要优于继电器控制装置,其优点包括简单易懂,便于安装,体积小,能耗低,有故障指示,能重复使用等。
其中PLC特有的编程语言—梯形图一直沿用至今。
在七十年代,微处理器的出现使PLC发生了巨大的变化。
美国,日本,德国等一些厂家先后开始采用微处理器作为PLC的中央处理单元(CPU)。
这样,使PLC的功能大大增强。
在软件方面,除了保持其原有的逻辑运算、计时、计数等功能以外,还增加了算术运算、数据处理和传送、通讯、自诊断等功能。
在硬件方面,除了保持其原有的开关模块以外,还增加了模拟量快、远程I/O模块、各种特殊功能模块。
并扩大了存储器的容量,使各种逻辑线圈的数量增加,还提供了一定数量的数据寄存器,使PLC的应用范围得以扩大。
进入八十年代中、后期,由于大规模集成电路技术的迅速发展,微处理器的市场价格大幅度下跌,使得各种类型的PLC所采用的微处理器的档次普遍提高。
而且,为了进一步提高PLC的处理速度,各制造厂商纷纷开发研制了专用逻辑处理芯片。
这样使得PLC软、硬功能发生了巨大变化。
1.3PLC的基本结构
PLC实质是一种专用于工业控制计算机,其硬件结构基本上与微型计算机相同,中央处理单元(CPU),如下图所示。
图1-1
、中央处理单元(CPU)
中央处理单元(CPU)是PLC的控制中枢。
它按照PLC系统程序赋予的功能接收并存储从编程器键入的用户程序和数据;检查电源、存储器、I/O以及警戒定时器的状态,并能诊断用户程序中的语法错误。
当PLC投入运行时,首先它以扫描的方式接收现场各输入装置的状态和数据,并分别存入I/O映象区,然后从用户程序存储器中逐条读取用户程序,命令解释后按指令规定执行逻辑或算数运算结果送入I/O映象区或数据寄存器内。
等所有用户程序执行完毕之后,最后将I/O映象区各输出状态或输出寄存器内数据传送到相应输出装置,如此循环运行,直到停止运行。
进一步提高PLC可靠性,近年来对大型PLC还采用双CPU构成冗余系统,或采用三CPU表决式系统。
这样,某个CPU出现故障,整个系统仍能正常运行。
、存储器
存放系统软件的存储器称为系统程序存储器。
存放应用软件的存储器称为用户程序存储器。
PLC常用的存储器类型
(1)RAM(RandomAssessMemory) 这是一种读/写存储器(随机存储器),其存取速度最快,由锂电池支持。
(2)EPROM(ErasableProgrammableReadOnlyMemory)这是一种可擦除的只读存储器。
在断电情况下,存储器内的所有内容保持不变。
(在紫外线连续照射下可擦除存储器内容)。
(3)EEPROM(ElectricalErasableProgrammableReadOnlyMemory)这是一种可擦除的只读存储器。
使用编程器就能很容易地对其所存储的内容进行修改。
、输入/输出模块
输入/输出模块是可编程控制器与工业生产设备或工业生产过程连接的接口。
现场的输入信号,如按钮开关,行程开关、限位开关以及传感器输出的开关量或模拟量(压力、流量、温度、电压、电流)等,都要通过输入模块送到PLC。
、扩展模块
当一个PLC中心单元的1/0点数不够用时,就要对系统进行扩展,扩展接口就是用于连接中心基本单元与扩展单元的。
模块随着可编程控制器在工业控制中的广泛应用和发展,各可编程控制器制造厂家已经开发出一系列的智能接口模块,使可编程控制器的功能更加强大和完善。
智能1/0接口模块种类很多,例如高速技术模块、PLCA控制模块、数字位基于PLC的变频恒压供水系统的设计置译码模块、阀门控制模块、中断控制模块、智能存贮模块以及智能1/0模块等。
、编程器
它的作用是供用户进行程序的编制、编辑、调试和监视。
有的编程器还可与打印机或磁带机相连,以将用户程序和有关信息打印出来或存放在磁带上,磁带上的信息可以重新装入PLC。
目前编程器主要有以下三种类型:
便携式编程器(也叫简易编程器);图形编程器;用于IBM一PC及其兼容机的编程器。
、电源
PLC中的电源一般有三类:
1、+5V、±15V直流电源:
供PLC中TTL芯片和集成运放使用;
2、供输出接口使用的高压大电流的功率电源;
3、锂电池及其充电电源。
考虑到系统的可靠性以及光电隔离器的使用,不同类型的电源其地线也不同。
1.4PLC的特点
(一)高可靠性
1.所有的I/O接口电路均采用光电隔离使工业现场的外电路与PLC内部电路之间在电气上隔离
2.各输入端均采用R-C滤波器其滤波时间常数一般为10~20ms
3.各模块均采用屏蔽措施以防止辐射干扰
4.采用性能优良的开关电源
5.对采用的器件进行严格的筛选
6.良好的自诊断功能一旦电源或其他软硬件发生异常情况,CPU立即采用有效措施以防止故障扩大
7.大型PLC还可以采用由双CPU构成冗余系统或有三CPU构成表决系统,使可靠性更进一步提高
(二)丰富的I/O接口模块
1.PLC针对不同的工业现场信号如:
交流或直流;开关量或模拟量;电压或电流;脉冲或电位;强电或弱电等。
2.有相应的I/O模块与工业现场的器件或设备如:
按钮;行程开关;接近开关;传感器及变送器;电磁线圈;控制阀。
3.直接连接,另外为了提高操作性能它还有多种人-机对话的接口模块;为了组成工业局部网络,它还有多种通讯联网的接口模块等等。
(三)采用模块化结构
为了适应各种工业控制需要除了单元式的小型PLC以外,绝大多数PLC均采用模块化结构,PLC的各个部件包括CPU电源I/O等均采用模块化设计,由机架及电缆将各模块连接起来,系统的规模和功能可根据用户的需要自行组合。
(四)编程简单易学
PLC的编程大多采用类似于继电器控制线路的梯形图形式,对使用者来说不需要具备计算机的专门知识,因此很容易被一般工程技术人员所理解和掌握。
(五)安装简单维修方便
PLC不需要专门的机房,可以在各种工业环境下直接运行,使用时只需将现场的各种设备与PLC相应的I/O端相连接即可投入运行,各种模块上均有运行和故障指示装置,便于用户了解运行情况和查找故障,由于采用模块化结构,因此一旦某模块发生故障,用户可以通过更换模块的方法使系统迅速恢复运行。
1.5PLC的工作原理
最初研制生产的PLC主要用于代替传统的由继电器接触器构成的控制装置,但这两者的运行方式是不相同的:
(1)继电器控制装置采用硬逻辑并行运行的方式,即如果这个继电器的线圈通电或断电,该继电器所有的触点(包括其常开或常闭触点)在继电器控制线路的哪个位置上都会立即同时动作。
(2)PLC的CPU则采用顺序逻辑扫描用户程序的运行方式,即如果一个输出线圈或逻辑线圈被接通或断开,该线圈的所有触点(包括其常开或常闭触点)不会立即动作,必须等扫描到该触点时才会动作。
为了消除二者之间由于运行方式不同而造成的差异,考虑到继电器控制装置各类触点的动作时间一般在100ms以上,而PLC扫描用户程序的时间一般均小于100ms,因此,PLC采用了一种不同于一般微型计算机的运行方式---扫描技术。
这样在对于I/O响应要求不高的场合,PLC与继电器控制装置的处理结果上就没有什么区别了。
1、扫描技术当PLC投入运行后,其工作过程一般分为三个阶段,即输入采样、用户程序执行和输出刷新三个阶段。
完成上述三个阶段称作一个扫描周期。
在整个运行期间,PLC的CPU以一定的扫描速度重复执行上述三个阶段。
如下图:
图1-2PLC扫描周期
(1)输入采样阶段
在输入采样阶段,PLC以扫描方式依次地读入所有输入状态和数据,并将它们存入I/O映象区中的相应得单元内。
输入采样结束后,转入用户程序执行和输出刷新阶段。
在这两个阶段中,即使输入状态和数据发生变化,I/O映象区中的相应单元的状态和数据也不会改变。
因此,如果输入是脉冲信号,则该脉冲信号的宽度必须大于一个扫描周期,才能保证在任何情况下,该输入均能被读入。
(2)用户程序执行阶段
在用户程序执行阶段,PLC总是按由上而下的顺序依次地扫描用户程序(梯形图)。
在扫描每一条梯形图时,又总是先扫描梯形图左边的由各触点构成的控制线路,并按先左后右、先上后下的顺序对由触点构成的控制线路进行逻辑运算,然后根据逻辑运算的结果,刷新该逻辑线圈在系统RAM存储区中对应位的状态;或者刷新该输出线圈在I/O映象区中对应位的状态;或者确定是否要执行该梯形图所规定的特殊功能指令。
即在用户程序执行过程中,只有输入点在I/O映象区内的状态和数据不会发生变化,而其他输出点和软设备在I/O映象区或系统RAM存储区内的状态和数据都有可能发生变化,而且排在上面的梯形图,其程序执行结果会对排在下面的凡是用到这些线圈或数据的梯形图起作用;相反,排在下面的梯形图,其被刷新的逻辑线圈的状态或数据只能到下一个扫描周期才能对排在其上面的程序起作用。
(3)输出刷新阶段
当扫描用户程序结束后,PLC就进入输出刷新阶段。
在此期间,CPU按照I/O映象区内对应的状态和数据刷新所有的输出锁存电路,再经输出电路驱动相应的外设。
这时,才是PLC的真正输出。
2、PLC的I/O响应时间
为了增强PLC的抗干扰能力,提高其可靠性,PLC的每个开关量输入端都采用光电隔离等技术。
为了能实现继电器控制线路的硬逻辑并行控制,PLC采用了不同于一般微型计算机的运行方式(扫描技术)。
以上两个主要原因,使得PLC得I/O响应比一般微型计算机构成的工业控制系统满的多,其响应时间至少等于一个扫描周期,一般均大于一个扫描周期甚至更长。
所谓I/O响应时间指从PLC的某一输入信号变化开始到系统有关输出端信号的改变所需的时间。
如下图:
图1-3PLC扫描周期示意图
第二章水塔水位系统PLC硬件设计
图2-1水塔水位控制装置图
2.1水塔水位控制系统要求
1)保持水池的水位在S1——S2之间,当水池水位低于下限液位开关S1,此时S1为ON,电磁阀打开,开始往水池里注水,当4S以后,若水池水位没有超过水池下限液位开关S1时,则系统发出警报;若系统正常运行,此时水池下限液位开关S1为OFF,表示水位高于下限水位。
当页面高于上限水位S2时,则S2为ON,电磁阀关闭。
2)保持水塔的水位在S3——S4之间,当水塔水位低于水塔下限水位开关S3时,则水塔下限液位开关S3为ON,则驱动电机M开始工作,向水塔供水。
当S3为OFF时,表示水塔水位高于水塔下限水位。
当水塔液面高于水塔上限水位开关S4时,则S4为ON,电机M停止抽水。
3)当水塔水位低于下限水位时,同时水池水位也低于下限水位时,电机M不能启动。
2.2水塔水位控制系统主电路
图2-2水塔水位系统控制主电路图
2.3I/O口的分配
表2-1水塔水位系统PLC的输入/输出接口分配表
输入
继电器
输入变量名
输出
继电器
输出变量名
X0
控制开关
Y0
电磁阀
X1
水塔上限液位开关
Y1
电机M
X2
水塔下限液位开关
Y2
水池下限指示灯a1
X3
水池下限液位开关
Y3
水池上限指示灯a2
X4
水池上限液位开关
Y4
水塔下限指示灯a3
Y5
水塔上限指示灯a4
Y6
报警指示灯a5
2.4水塔水位系统的输入/输出设备
这是一个单体控制小系统,没有特殊的控制要求,它有5个开关量,开关量输出触点共有8个,输入、输出触点数共有13个,只需选用一般中小型控制器即可。
据此,可以对输入、输出点作出地址分配,水塔水位控制系统的I/O接线图如下:
图2-3
第三章水塔水位控制系统PLC软件设计
3.1水位控制系统的工作过程
设水塔、水池初始状态都为空着的,4个液位指示灯全亮。
当执行程序是,扫描到水池为液位低于水池下限位时,电磁阀打开,开始往水池里进水,如果进水超过4S,而水池液位没有超过水池下限位,说明系统出现故障,系统就会自动报警。
若4S只有水池液位按预定的超过水池下限位,说明系统在正常的工作,水池下限位的指示灯a1灭。
此时,水池的液位已经超过了下限位了,系统检测到此信号时,由于水塔液位低于水塔水位下限,电机M开始工作,向水塔供水,当水池的液位超过水池上限液位时,水池上限指示灯a2,电磁阀就关闭,但是水塔现在还没有装满,可此时水塔液位已经超过水塔下限水位,则水塔下限指示灯a3灭,电机M继续工作,从水池向水塔抽水,水塔抽满是,水塔也未超过水塔上限,水塔上限指示灯a4灭,但刚刚给水塔供水的时候,电机M已经把水池的水抽走了,此时水塔液位已经低于水池上限,水池上限指示灯a2亮。
此次给水塔供水完成。
3.2程序流程图
水塔水位控制系统的PLC控制流程图,根据设计要求控制流程图如下:
图3-1
3.3梯形图
图3-2水塔水位控制系统的梯形图
3.4指令表
图3-3水塔水位控制系统指令表
第四章总结
毕业