煤气的终冷及除萘.docx
《煤气的终冷及除萘.docx》由会员分享,可在线阅读,更多相关《煤气的终冷及除萘.docx(16页珍藏版)》请在冰豆网上搜索。
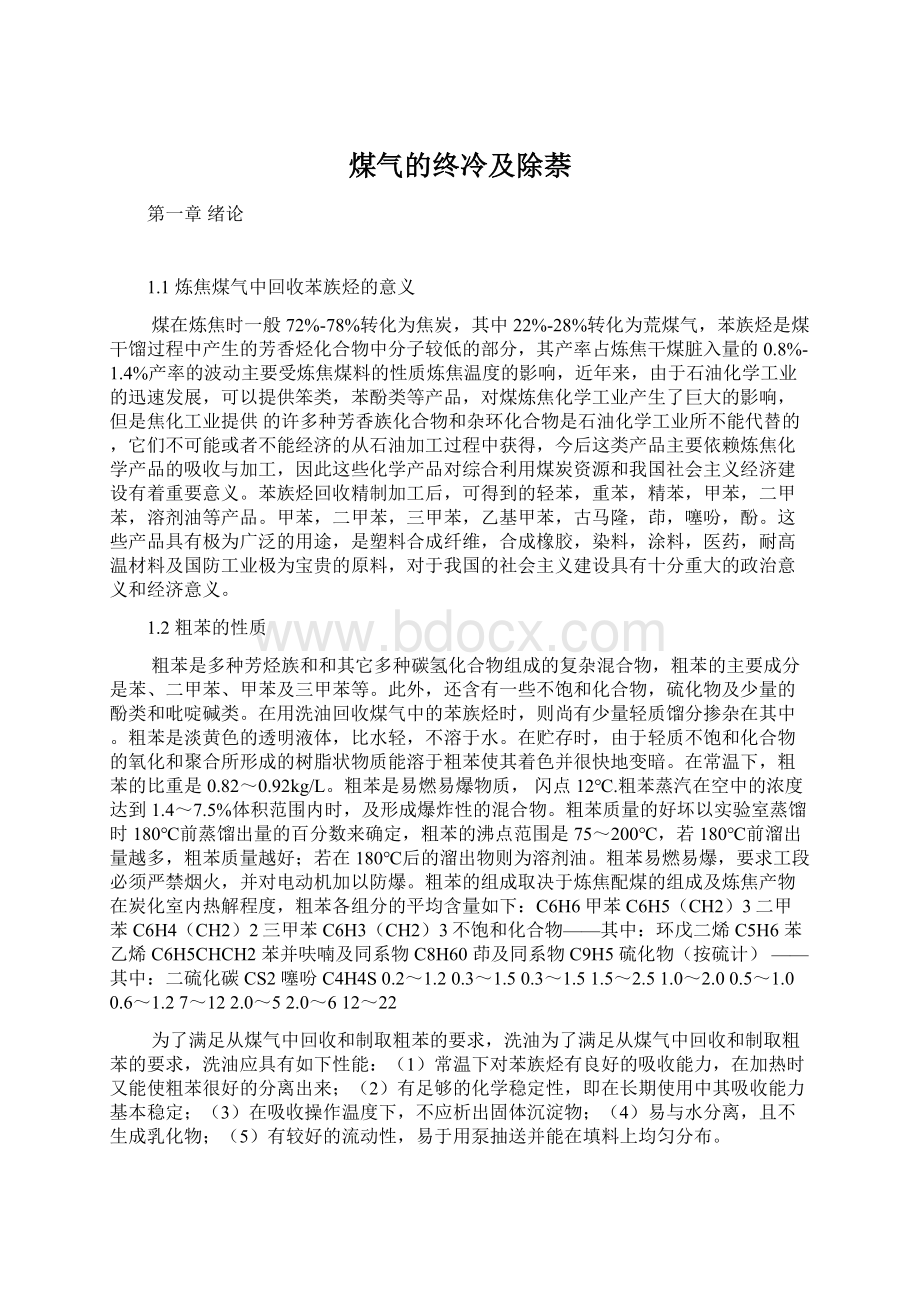
煤气的终冷及除萘
第一章绪论
1.1炼焦煤气中回收苯族烃的意义
煤在炼焦时一般72%-78%转化为焦炭,其中22%-28%转化为荒煤气,苯族烃是煤干馏过程中产生的芳香烃化合物中分子较低的部分,其产率占炼焦干煤脏入量的0.8%-1.4%产率的波动主要受炼焦煤料的性质炼焦温度的影响,近年来,由于石油化学工业的迅速发展,可以提供笨类,苯酚类等产品,对煤炼焦化学工业产生了巨大的影响,但是焦化工业提供的许多种芳香族化合物和杂环化合物是石油化学工业所不能代替的,它们不可能或者不能经济的从石油加工过程中获得,今后这类产品主要依赖炼焦化学产品的吸收与加工,因此这些化学产品对综合利用煤炭资源和我国社会主义经济建设有着重要意义。
苯族烃回收精制加工后,可得到的轻苯,重苯,精苯,甲苯,二甲苯,溶剂油等产品。
甲苯,二甲苯,三甲苯,乙基甲苯,古马隆,茚,噻吩,酚。
这些产品具有极为广泛的用途,是塑料合成纤维,合成橡胶,染料,涂料,医药,耐高温材料及国防工业极为宝贵的原料,对于我国的社会主义建设具有十分重大的政治意义和经济意义。
1.2粗苯的性质
粗苯是多种芳烃族和和其它多种碳氢化合物组成的复杂混合物,粗苯的主要成分是苯、二甲苯、甲苯及三甲苯等。
此外,还含有一些不饱和化合物,硫化物及少量的酚类和吡啶碱类。
在用洗油回收煤气中的苯族烃时,则尚有少量轻质馏分掺杂在其中。
粗苯是淡黄色的透明液体,比水轻,不溶于水。
在贮存时,由于轻质不饱和化合物的氧化和聚合所形成的树脂状物质能溶于粗苯使其着色并很快地变暗。
在常温下,粗苯的比重是0.82~0.92kg/L。
粗苯是易燃易爆物质,闪点12℃.粗苯蒸汽在空中的浓度达到1.4~7.5%体积范围内时,及形成爆炸性的混合物。
粗苯质量的好坏以实验室蒸馏时180℃前蒸馏出量的百分数来确定,粗苯的沸点范围是75~200℃,若180℃前溜出量越多,粗苯质量越好;若在180℃后的溜出物则为溶剂油。
粗苯易燃易爆,要求工段必须严禁烟火,并对电动机加以防爆。
粗苯的组成取决于炼焦配煤的组成及炼焦产物在炭化室内热解程度,粗苯各组分的平均含量如下:
C6H6甲苯C6H5(CH2)3二甲苯C6H4(CH2)2三甲苯C6H3(CH2)3不饱和化合物——其中:
环戊二烯C5H6苯乙烯C6H5CHCH2苯并呋喃及同系物C8H60茚及同系物C9H5硫化物(按硫计)——其中:
二硫化碳CS2噻吩C4H4S0.2~1.20.3~1.50.3~1.51.5~2.51.0~2.00.5~1.00.6~1.27~122.0~52.0~612~22
为了满足从煤气中回收和制取粗苯的要求,洗油为了满足从煤气中回收和制取粗苯的要求,洗油应具有如下性能:
(1)常温下对苯族烃有良好的吸收能力,在加热时又能使粗苯很好的分离出来;
(2)有足够的化学稳定性,即在长期使用中其吸收能力基本稳定;(3)在吸收操作温度下,不应析出固体沉淀物;(4)易与水分离,且不生成乳化物;(5)有较好的流动性,易于用泵抽送并能在填料上均匀分布。
第2章工艺论证及确定
2.1煤气的终冷及除萘的方法及工艺选择
回收煤气中的苯族烃的适量温度为21-27℃左右,在饱和器后温度通常是在50-56℃,被有喷淋下来的富油洗萘。
富油进塔温度比煤气温度高5-7℃,50-56℃的煤气进入终冷塔,煤气含萘可由2000-2500mg/Nm3降到500-800mg/Nm3。
除萘后的煤气进入终冷塔,该塔为隔板式,分两段。
下段用从凉水架来的循环水冷却至20-23℃的循环水喷淋,将煤气再冷却25℃左右,额外水从终冷塔底部经水封管流入热水池;然后用泵送至凉水架,经冷却后自流入冷水池。
再用泵送至终冷冷塔的上下两端,送往上端的水须于间冷器用低温水冷却,由于终冷器只是为了冷却煤气,所以终冷循环水量可减至2.5-3吨/1000标米3煤气左右,因此,在回收苯族烃之前,煤气必须进行最终冷却.由于在煤气冷却和部分水蒸气冷凝的同时,也有萘从煤气中析出,所以,煤气的最终冷却同时也兼有除萘的作用.我国焦化厂目前所采用的煤气终冷及除萘的工艺流程主要有四种,即:
煤气终冷和机械除萘工艺;煤气终冷和焦油洗油工艺;洗油萘和煤气最终冷却工艺;横管终冷喷洒轻焦油洗萘工艺.
2.1.1煤气终冷和机械化除萘工艺来自硫铵工段煤气在终冷塔内自下而上流动,在流动过程中与经由隔板孔眼喷淋而下的冷却水流密切接触,从55-60℃冷却至21-27℃,部分水汽被冷凝下来,同时还有相当数量的萘也从煤气中析出,并被水冲洗下来,煤气含量可从2000-3000mg/Nm3,降到800-1200mg/Nm3。
冷却后的煤气去洗苯塔脱苯。
含萘冷却水由塔底经水封管自流入机械化刮萘槽,水和萘在槽中分离后,水自流入凉水架冷却到30-32℃,再由泵抽送经冷却器冷却到21℃左右后,回终冷塔循环使用。
在刮萘槽中积聚的萘,定期用水蒸气间接加热熔化后流入萘的扬液槽,再用水蒸汽压送往焦油槽或焦油氨水澄清槽。
亦可用冷凝工段的初冷冷凝液来熔化萘,熔萘后的冷凝液自流返冷凝鼓风段,这样既简化了操作又改善了劳动条件。
该流程的优点是操作稳定,便于管理,缺点是该工艺流程的除萘率受冷却水温的影响,故塔后的煤气含萘量较高。
水和萘不能充分分离,部分萘被水带到凉水架,增加了凉水架清扫工作,因其排污水量大,刮萘槽结构复杂且笨重,基建费高。
该洗萘法仅用于硫铵生产工序之后。
2.1.2煤气终冷和焦油洗萘工艺含萘冷却水从终冷塔底部流出,经液封管导入焦油洗萘器底部并向上流动。
热焦油经伸入器的分布管均匀喷洒在筛板上,通过筛板孔眼向下流动,在与水对流接触过程中将水中含萘降到800mg/Nm3以下。
洗萘后的焦油从洗萘器下部排出,经液位调节器流入焦油槽。
焦油在循环使用24小时后,经加热静止脱水用泵送往焦油车间加工处理,送空的焦油槽再接受冷鼓工段的新鲜焦油以备循环洗萘使用。
从洗萘器上部流出的水进入水澄清槽,分离出残余焦油后,自流到凉水架。
分离出的焦油及浮在水面上的油类、萘等混合物自流到焦油槽。
焦油洗萘比机械化除萘效率高,但操作复杂。
该流程的优点是不仅可以把冷却水中的萘几乎全部清除,而且对水中的酚有一定萃取作用结果,减少凉水架的清扫次数,有利于冷却水的进一步处理。
缺点是操作复杂,出口煤气含萘量高,用水量大,后期仍需进行污水处理。
2.1.3油洗萘和煤气终冷工艺饱和器来的50-55℃的煤气进入木格填料洗萘塔底部,塔顶喷洒温度为55-57℃的洗苯富油进行洗萘。
富油进塔温度比煤气温度高5-7℃,使煤气含萘可由2000-2500mg/Nm3降到500-800mg/Nm3。
除萘后的煤气进入终冷塔,该塔为隔板式,分两段。
上段用从凉水架来的循环水冷却至20-23℃的循环水喷淋,将煤气再冷却25℃左右,额外水从终冷塔底部经水封管流入热水池;然后用泵送至凉水架,经冷却后自流入冷水池。
再用泵送至终冷冷塔的上下两端,送往上端的水须于间冷器用低温水冷却,由于终冷器只是为了冷却煤气,所以终冷循环水量可减至2.5-3吨/1000标米3煤气
该流程的优点是塔后煤气含萘量要前两种工艺流程,用水量为水洗萘的一半,因而可减少含酚污水的排放量。
缺点是该流程油洗萘在较为高的温度下进行,塔后煤气含萘量仍较高,煤气温度波动;操作复杂,洗油耗量大,脱苯困难,仍需进行污水处理。
2.1.4横管终冷喷洒轻质焦油洗萘工艺从硫铵工段来的煤气由塔顶进入,与连续喷洒的轻质焦油并流差速接触速冷,至横管段继续冷却至21-25℃,同时脱萘至450毫克/标米3以下,然后从塔底排出,进入旋风捕雾器除掉夹带的焦油,萘和凝结水雾,然后去洗苯塔。
轻质焦油由其补充至塔底循环油槽,循环油由槽底泵出至槽中部,顶部喷洒,与横管束和煤气接触换热,同时溶解煤气中析出的萘,然后经液封回循环槽。
(此过程中,循环油槽内,入塔处,出塔处油温基本相同)。
焦油循环至一定程度,用泵送至焦油上段。
18℃的冷冻水由塔下部横管冷却器进入,向上经串联着的各横管器与塔内循环油,煤气间接换热绳温,然后从塔的外部排出。
由于该工程主要依靠降低煤气的温度使煤气中萘析出,并由轻质焦油将萘溶解,因此煤气温度需降至21℃左右。
如此低温,就决定了必须要有低温水的焦化厂才易采用该工艺。
该流程的优点是:
1、此工艺不仅对煤气中的萘的脱除率高,而且冷却效果非常好。
出口煤气约21℃左右,煤气含萘量大约在350-450mg/Nm3。
2、无须洗油,只须自产轻质焦油,节约洗油耗量;煤气中的萘直接转入焦油,降低了萘的损失。
3、该系统阻力小,风机电耗低;操作维护简便;无污染;占地面积小,基建费用少。
4、由于煤气冷却不直接与水接触,所以无含酚污水的处理。
综合上述的四种工艺,通过比较,第四种优点突出,徐州地区有低温的水源。
因此本设计采用第四种方法即:
横管终冷喷洒轻质焦油洗萘工艺。
2.2洗苯工艺
2.2.1焦油洗油吸收法目前,国内焦化厂主要采用洗油吸收法回收煤气中的苯族烃,经过终冷的煤气温度降至25~27℃,然后进入洗苯塔回收苯族烃,回收方法大致分为下列三种:
1.洗油吸收法用洗油在洗涤塔中回收煤气中毒苯族烃,再将吸收了苯族烃的洗油(富油)送入脱笨蒸馏装置中,以提取粗苯,脱笨后的洗油(贫油)经过冷却后,重新送至洗涤塔循环使用,洗油吸收法又分为常压吸收法和加压吸收法,加压吸收法可以强化生产过程,适用于煤气远距离输送或用作合成氨厂原料的情况下采用。
吸附法:
2.吸附法使煤气通过具有微孔组织比表面很大的活性炭或硅胶等固体吸附剂,苯族烃即被吸附在其表面上,直至达到接近饱和状态,然后用水蒸气直接进行解析,即得粗苯。
用活性炭做吸附剂,可将煤气的苯族烃完全吸附下来但此法要求煤气净化的程度较高,加之吸附剂价格昂贵,因此在工业上应用受到一定的限制,而多用于煤气苯族烃的定量分析。
凝结法:
3.凝结法在低温加压的情况下,使苯族烃从煤气中冷凝出来,此法比吸收法所得到的粗苯质量好,但煤气的压缩及冷冻过程复杂,阻力消耗大,设备材质要求高。
目前国内焦化厂主要采用洗油吸收法回收煤气中的苯族烃,油吸收法可分为焦油洗油吸收法和石油吸收法。
煤气经最终冷却到25-27℃后进入洗苯塔。
塔前的煤气含粗苯32-40克/标m3,塔后的煤气中含粗苯低于2克/标m3。
从脱苯工序来的贫油,含苯0.2-0.4%,进入贫油槽,用贫油泵进入洗苯塔顶部,从塔顶喷淋而下,含苯量增至2.5%左右。
用富油泵将富油从塔底抽出,送往脱苯工序。
脱苯后的贫油送回贫油槽循环使用。
本设计所选用的就是这种工艺流程,但洗苯塔有多种形式,选择合适的塔型是值得研究的。
用洗油回收煤气中的粗苯的方法,所用的洗苯塔有多种形式,但工艺流程基本一样。
洗苯塔底部为洗油接受槽,用钢板与煤气部分隔开,从塔顶下来的洗油经U型管流入该槽,U型管内有一定的液位,足以封位煤气,阻止它进入油槽从放散管溢出。
洗苯塔喷头上方设置捕雾器,以捕集的油滴,减少洗油损失,塔顶还有一个喷口,以清洗捕雾层。
2.2.2石油洗油回收粗苯用石油洗油回收粗苯的工艺流程与用焦油洗油回收的一样,只是在设计贫油槽时,须考虑经常排油渣和生成腐蚀物。
目前国内使用的是有洗油为轻柴油,与焦油洗油比较耗量低,油水分离容易,具有较高的稳定性,长期使用后其物理化学性质几乎不变,此外,石油洗油吸萘的能力强,一般塔后煤气含萘量可低于150mg/Nm3.石油洗油的缺点是洗苯能力较低,富油含苯量为1.2~0.3%,故循环洗油量每吨(180℃前粗苯为65m3)和脱笨的耗气量较多,此外,在洗苯过程生成难溶的油渣,容易堵塞换热设备,含油渣的洗油和水容易形成乳蚀液,影响正常操作,所以洗油含渣量不宜大于20mg/ρ.另外焦化厂使用石油洗油需外购,因此多数焦化厂采用焦油洗油。
为了满足从煤气中回收和制取粗苯的要求,洗油具有如下性能:
1)常温下对苯族烃有良好的吸收能力,在加热时又能使粗苯很好的分离出来。
2)有足够的化学稳定性,即在长期使用中吸收能力基本稳定。
3)在吸收操作温度下不应析出固体沉淀物。
4)易于水分离,且不能生成乳蚀物。
5)有较好的流动性,易于用泵抽送并能在调料上均匀分布。
由于石油洗苯工艺流程缺点较多,特别选型上存在难题,故一般不采用它,而多采用第一种工艺流程。
本设计就采用焦油洗油回收粗苯工艺。
第三章粗苯脱苯方法及工艺选择
由洗苯工序过来的含苯富油需进行脱笨。
脱苯工艺与很多种,我国焦化厂均采用水蒸气蒸馏法脱苯。
安装粗苯产品可以分为生产一种苯工艺和生产两种苯工艺,按照富油的加热方式可以分为蒸汽加热法和管式炉加热法。
下面就蒸汽加热生产一种苯工艺和管式炉加热法生产一种苯工艺分别进行介绍。
3.1蒸汽加热法生产一种苯工艺
本设计采用生产一种苯工艺,用直接蒸汽蒸馏的方法脱苯,现将各种工艺流程及选用的设备介绍如下:
由洗涤(洗苯)工序来的富油,在分离器下面的三个中,被脱苯塔来的蒸汽加热至70~80℃,然后进入贫富油换热器,被来自脱苯塔底的温度为130~140℃的热贫油加热至90~100℃,最后在富油预热器中用大于8kgf/cm的间接蒸汽加热到135~145℃,在从脱苯塔的第十二层塔板进入塔内。
富油在塔内逐板向下溢流,在由塔底进入的直接蒸汽的蒸吹作用下,富油中绝大部分粗苯,洗油部分轻质馏分及萘,从洗油中蒸出来并同一定量的水蒸气从塔顶逸出.温度比富油的预热温度约1~2℃的油气和水汽混合物,进入分缩器顶上一格用冷水冷却,从而使大部分洗油气和水汽冷凝下来,从分缩器顶部逸出的即为粗苯蒸汽。
为得到合格粗苯产品,可用冷却水量控制分缩器顶部蒸汽温度,使其在86~89℃的范围内。
由分缩器顶部逸出的粗苯蒸汽进入蒸汽冷凝冷却器,在此用冷水冷凝冷却到25~30℃,再经粗苯分离器将水分出后即进入粗苯贮槽,并定期用产品泵送往精制车间或出售。
进入分缩器的油气和水汽混合物,在分缩器底部两个所形成的冷凝液实施油气中的重馏分,即重分缩油。
轻重分缩油分别进分缩器,在与分水分离后兑入富油中并一起送往脱苯塔。
在三个油水分离器,排出的分离水均进入控制分离器进一步分离,以减少洗油的损失。
从脱苯塔底排出的贫油温度比富油的预热温度约低3~5℃(130~140℃)热贫油子流入贫富有换热器,与富油换热并被冷却至110~120℃后,在回到脱苯塔底的热贫油槽中,在此用用热贫油泵送到喷淋式贫油冷却器,冷却至25~30℃后,在送往洗苯塔循环喷洒。
由于洗油在循环使用的过程中质量会变坏,为保持循环洗油的质量,将循环油量的1~1.5%有富油入塔前的管路或脱苯塔加料板以下的一块塔板处引入洗油再生器,洗油被10~12kgf/cm的间接蒸汽加热至160~180℃,并用过热直接蒸汽直接蒸吹,从再生器顶部蒸吹出来的温度,留在再生器底部的高沸点聚合物及油渣称为残渣。
可以靠设备内地蒸汽压力间歇地或连续地排至残渣油槽。
从再生器排出的残渣油,300℃前的馏出量要求低于40%,若馏出量过高会大大增加洗油耗量。
洗油再生器操作之好坏,还对洗油耗量有较大的影响,在洗苯塔后煤气中所夹带的洗油较少分离良好的情况下,如洗油再生器操作正常,则生产每吨180℃前的粗苯的焦油洗油约为50kg,石油洗油的耗量较高,约为50~100kg.(故此设计采用焦油洗油)
3.2管式炉加热富油脱苯
该工艺与蒸汽法脱笨工艺相同,唯一的区别在于富油经贫富油换热器后,不是用蒸汽加热而是用管式炉加热至180~200℃后,在进入脱苯塔。
管式炉加热的富油脱苯工艺,因富油的加热温度高,同蒸汽法脱苯比较具有以下优点:
1.富油在管式炉内加热至180℃左右,脱苯程度高,贫油中粗苯含量可降至0.1%左右,从而使粗苯的塔后损失减小,粗苯的回收率可高达95~97%2.蒸汽耗量低,每生产一顿180℃前的粗苯好蒸汽约1~1.05吨且不受蒸汽压力波动的影响,操作稳定。
3.酚水含量少,蒸汽法脱苯,每吨180℃前粗苯要产生3~4吨工业酚水,而管式炉法只产生1.05吨以下的酚水。
4.设备费用低,蒸汽耗量显著降低,大大缩小罗冷凝冷却和蒸馏设备的尺寸,从而使设备费用大为降低。
因此,本设计选用管式炉加热法生产一种苯工艺。
第4章粗苯回收原理
4.1洗油吸收苯族烃的基本原理
用洗油吸收煤气中的粗苯烃是物理吸收过程,服从亨利定律和道尔顿定律,当煤气中苯族烃的分压大于洗油液面上苯族烃的平衡蒸汽压时,煤气中苯族烃即被洗油吸收,二者差值越大,则洗收过程进行的越容易,吸收速率也越快。
目前,吸收过程的机理仍建立在被吸收组分经稳定的界面薄膜扩散传递的概念上,即液相与气相之间有相界面,假定在相界面的两侧,分别存着不呈湍流的薄膜,在气相侧的称为气膜,在液相侧的成为液膜,扩散过程的阻力及等于气膜和液膜的阻力之和。
吸收系数大小取决于所采用的吸收剂的形式,填料內型与规格及吸收段过程进行条件(温度,气相和液相流速等)显然,这些因素吸收速率均匀影响。
4.1.1影响苯族烃吸收的因素煤气中毒苯族烃在洗苯塔内被吸收的程度称为吸收率,吸收率的大小取决于以下因素,煤气和洗油中的苯族烃的含量;煤气流速及压力;洗油循环量及其分子量,吸收温度,洗苯塔结构,对填料塔则为填料表面积及特性等。
分述如下:
1、吸收温度:
吸收温度是指洗苯塔内气液两相接触面积的平均温度,它取决于煤气和洗油的温度,也受大气温度的影响。
吸收温度是通过吸收系数和吸收推动力的变化而影响吸收率的,提高的吸收温度,可使吸收系数与一定增加,但不显著,而吸收推动力却显著减小。
对于洗油吸收煤气中毒苯族烃来说,洗油分子量及煤气总压的破洞很小,可视为常数,而粗苯的蒸汽压是随温度的变化而变化,温度升高,粗苯的蒸汽压力也升高,当煤气中的苯族烃的含量一定时,温度愈低,洗油中与其呈平衡的粗苯含量愈高;而当提高温度时,洗油中与其呈平衡的粗苯含量则有较大的降低。
当入塔贫油含量一定时,洗油液面上苯族烃的蒸汽压随吸收温度升高而增大,吸收推动力则随之减小,致使洗苯后煤气中的苯族烃含量(塔后损失)增粗苯的回收率降低。
因此,吸收温度不宜过高,但也并非越低越好,在低于15℃时洗苯油粘度将显著增加,使洗油输送及其他内均匀分布和自由流动均发生困难,当洗油温度低于10℃时,还可能从油中析出固体沉淀物。
因此适宜的吸收温度约25℃,实际操作波动于25~30℃之间。
另外,操作中洗油温度应略高于煤气温度,以防止煤气中毒水汽冷凝进入洗油中,一般规定,洗油温度在夏季比煤气温度高2℃左右,冬季高4℃左右。
为了保证吸收温度,煤气进洗苯塔前,应在终冷期内冷却至20~28℃,循环油冷却至小于30℃.2、洗油的分子量及循环量的影响当其他条件一定时,洗油的分子量变小,将使洗油中粗苯含量变大,及吸收得愈好,同类油剂的吸收能力与其分子量成反比。
吸收剂与溶质的分子量愈接近,则吸收得愈完全。
在回收等量粗苯的情况下,如洗油循环量也可以相应地减少。
但洗油的分子量不宜过小,否则洗油中吸收过程中损失较大,并且脱苯蒸馏时不易与粗苯分离。
增加循环油量可降低洗油中粗苯的含量,增加气液间的吸收推动力,从而可以提高粗苯的回收推动力。
提高回收率,但循环洗油量不宜过大,以免过多增大电、蒸汽的耗量和冷却水用量。
在塔后煤气含苯量一定的情况下,随着吸收温度的升高,则需要的循环洗油量随之增加。
3、贫油含苯量的影响:
贫油含苯量是决定塔后煤气汗苯族烃量的主要因素之一,当其它条件一定时,入塔贫油中的含苯量越高,则塔后损失愈大,按现行3规定,塔后煤气中粗苯含量不大于2g/Nm.为是塔后损失不大于2g/Nm3,设贫油中的粗苯含量为2.2%,为了维持一定的吸收推动力,2.2%应除以平衡偏移系数n,一般n=1.1~1.2.若取n=1.15,则允许贫油含苯量为c1=(2.2/1.5)%=1.92%<2%.实际上,由于贫油中粗苯的组成中苯和甲苯的含量少,绝大部分分为二甲苯和溶剂油,其蒸汽压仅相当于统一温度下煤气中汗苯族烃蒸汽压的20~30%,故实际贫油含苯量可达到0.4~0.6%,此时仍能保证塔后煤气含粗苯量子32g/Nm3以下。
如何一步降低贫油中的粗苯含量,虽然有助于降低塔后损失,但将增加脱苯蒸馏时代蒸汽耗量,使粗苯产品的180℃前馏出率减少,并且是洗油含量增加。
3近年来,国外一些焦化厂,塔后煤气含粗苯量控制在4g/Nm3左右,甚至更好,这一指标对大型焦化厂的粗苯回收是经济合理的。
另外,从一般粗苯粗苯和回炉煤气中分离出来的苯族烃的性质可以看出,由回炉煤气中得到的苯族烃,硫含量比粗苯高3.5倍,不饱和化合物的含量高1.1倍,由于这些物质很容易聚合,故会增加粗苯的回收和精致难度,因此,塔后煤气含苯量控制高一些也合理。
4、吸收表面积的影响为使洗油充分吸收煤气中毒苯族烃,必须使气液两相之间有足够的接粗面积(即吸收面积)填料塔的吸收面积即为塔内填料表面积。
调料表面积愈大,则煤气与洗油接触时间愈长,回收过程进行的愈完全。
适当的吸收面积即能保证一定的粗苯回收率,又使设备费和操作费经济合理。
5、煤气压力与流速的影响:
当增大煤气诶压力时,扩散系数Dg将随之减少,因而是吸收系数与所降低。
但随着压力的增加,煤气中的苯族烃分压将成比例地增加,使吸收推动力显著增加,因而,吸收速率也将增加。
煤气速度的增大也可提高吸收系数,并且可以提高气液相接触的涡流程度和提高洗苯塔的生产能力,所以,加大煤气速度可以强化吸收过程,但煤气速度太大时,容易使洗苯塔阻力和雾沫夹带量急剧增加。
4.2脱苯原理
脱苯原理实际上是精馏原理,由挥发度不同的组分的混合液中精馏塔内多次地进行部分气化和部分冷凝,使其分离几乎纯态的组分的过程,在精馏过程中,当加热互不相容的液体混合物时,如果塔内的总压力等于个混合组分的饱和蒸汽分压之和时,液体开始沸腾,但从富油中蒸出粗苯,达到过苯蒸出粗苯,达到脱苯原理时,必将富油加热到250~300℃,这实际上是不可行的。
为了降低蒸馏温度采用水蒸气法蒸馏。
这样,在脱苯过程中通入大量的直接水蒸气,当塔内总压力的为一定值时,若气相中水蒸气所占的分压愈高,则粗苯和洗油的蒸汽分压就愈低,这样就可以在较低的温度下(远低于250~300℃),将粗苯完全地从洗油中蒸馏出来。
由此可见,脱苯操作时直接蒸汽用量,对蒸馏过程有着重要影响。
下面就脱苯蒸馏中的蒸汽耗量进行几点讨论:
1)放贫油含苯量一定时,直接蒸汽的耗量是随着洗油预热,温度的升高而减少,一般在富油预热温度从140℃提高到180℃时,直接蒸汽耗量可降低一半以上。
2)提高直接蒸汽的过热温度,可降低其耗用量。
3)当富油中粗苯含量较高时,在一定的预热温度下,由于粗苯的蒸汽分压较高,对于蒸出每吨180℃之前的粗苯,可以减少直接蒸汽耗用量。
4)在其他田间一定时,蒸汽的耗用量是随塔内总压倒提高而增加的,否则若要达到所需求的脱苯程度时,塔内温度必然要搞。
4.2.1影响脱苯的因素脱苯塔内地脱出率取决于一下因素:
1、在塔底油温下各组分的蒸汽压:
若富油的如热温度高,塔底贫油温度相应也高,贫油中各组分的蒸汽压变大,故馏出率也增加。
但因本的挥发度较大,在较低温度下几乎全部蒸出,所以富油预热温度对苯的馏出率影响很小,而对其它组分的影响则很大。
如甲苯的回收率随着预热温度的提高而相应提高。
2、塔内操作压力:
提高塔内的操作压力时,各组分的馏出率会相应减小,但同样对苯的影响小。
3、加料板一下的塔盘:
显然,当增加加料板一下的塔盘层数时,各族分到馏出率相应增加,尤其是对甲苯和二甲苯等影响较大。
4、直接蒸汽量:
蒸汽耗量增加,增大了蒸汽分压,相应增加各组分的馏出率,但蒸汽耗量过分增加:
一是给油水分离带来负担,二是冷却水量增加,三是蒸汽耗量大了不经济。
因此,直接蒸汽的多少应以及能保证脱苯顺利进行,又保证经济合理为标准。
第5章粗苯工段工艺的详述
5.1工艺流程详述
5.1.1横管终冷洗萘工艺进入煤气粗苯回收工段的煤气,温度为55℃左右,从终冷塔顶进入,在被横管内冷却水冷却到25℃左右的同时,煤气中的萘也被从轻质焦油循环槽来的连续喷洒的轻焦油溶解吸收。
脱萘至0.45g/Nm3以下,然后从塔底排出,经旋风捕雾器除去大部分