阳光弯管资料.docx
《阳光弯管资料.docx》由会员分享,可在线阅读,更多相关《阳光弯管资料.docx(12页珍藏版)》请在冰豆网上搜索。
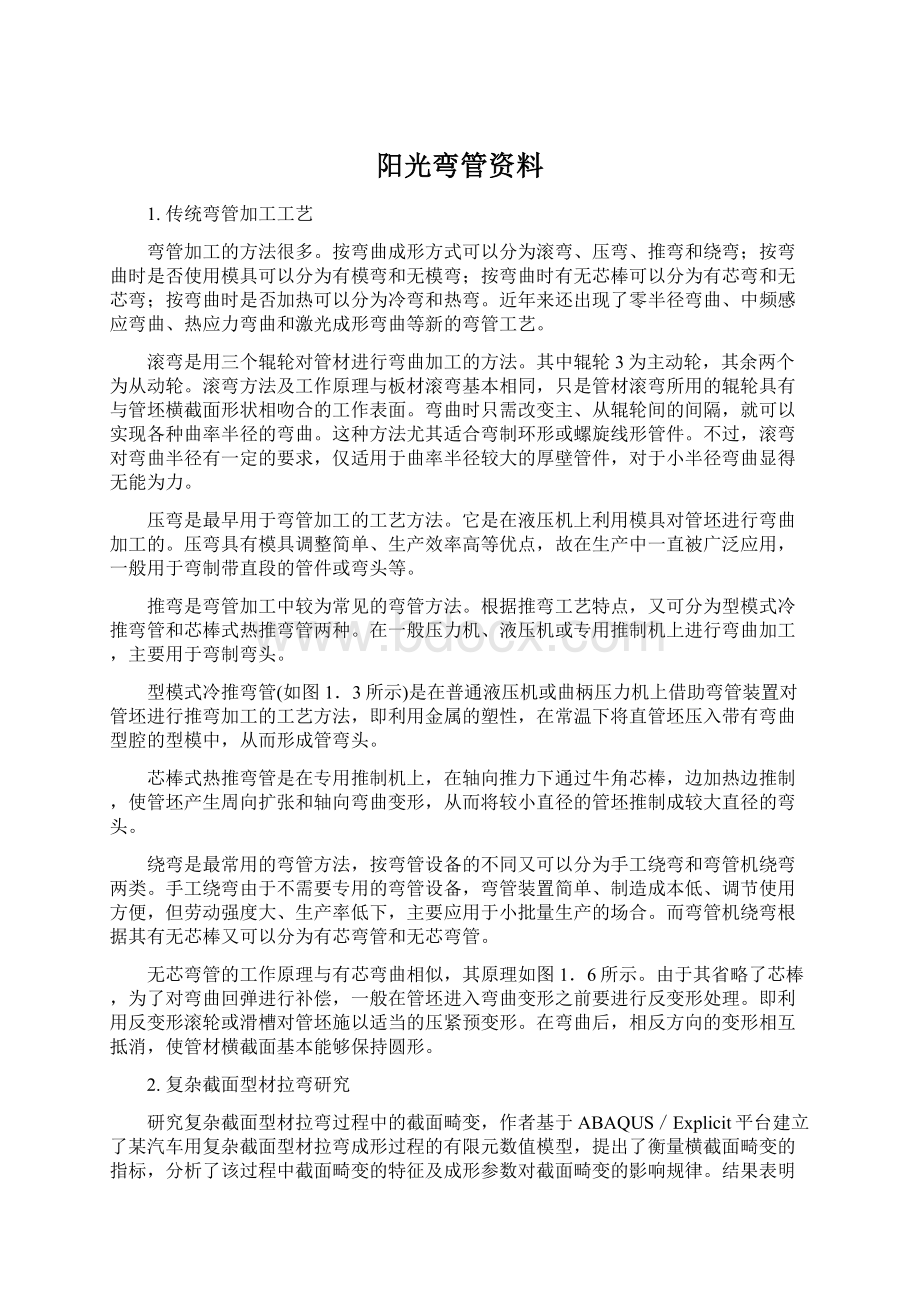
阳光弯管资料
1.传统弯管加工工艺
弯管加工的方法很多。
按弯曲成形方式可以分为滚弯、压弯、推弯和绕弯;按弯曲时是否使用模具可以分为有模弯和无模弯;按弯曲时有无芯棒可以分为有芯弯和无芯弯;按弯曲时是否加热可以分为冷弯和热弯。
近年来还出现了零半径弯曲、中频感应弯曲、热应力弯曲和激光成形弯曲等新的弯管工艺。
滚弯是用三个辊轮对管材进行弯曲加工的方法。
其中辊轮3为主动轮,其余两个为从动轮。
滚弯方法及工作原理与板材滚弯基本相同,只是管材滚弯所用的辊轮具有与管坯横截面形状相吻合的工作表面。
弯曲时只需改变主、从辊轮间的间隔,就可以实现各种曲率半径的弯曲。
这种方法尤其适合弯制环形或螺旋线形管件。
不过,滚弯对弯曲半径有一定的要求,仅适用于曲率半径较大的厚壁管件,对于小半径弯曲显得无能为力。
压弯是最早用于弯管加工的工艺方法。
它是在液压机上利用模具对管坯进行弯曲加工的。
压弯具有模具调整简单、生产效率高等优点,故在生产中一直被广泛应用,一般用于弯制带直段的管件或弯头等。
推弯是弯管加工中较为常见的弯管方法。
根据推弯工艺特点,又可分为型模式冷推弯管和芯棒式热推弯管两种。
在一般压力机、液压机或专用推制机上进行弯曲加工,主要用于弯制弯头。
型模式冷推弯管(如图1.3所示)是在普通液压机或曲柄压力机上借助弯管装置对管坯进行推弯加工的工艺方法,即利用金属的塑性,在常温下将直管坯压入带有弯曲型腔的型模中,从而形成管弯头。
芯棒式热推弯管是在专用推制机上,在轴向推力下通过牛角芯棒,边加热边推制,使管坯产生周向扩张和轴向弯曲变形,从而将较小直径的管坯推制成较大直径的弯头。
绕弯是最常用的弯管方法,按弯管设备的不同又可以分为手工绕弯和弯管机绕弯两类。
手工绕弯由于不需要专用的弯管设备,弯管装置简单、制造成本低、调节使用方便,但劳动强度大、生产率低下,主要应用于小批量生产的场合。
而弯管机绕弯根据其有无芯棒又可以分为有芯弯管和无芯弯管。
无芯弯管的工作原理与有芯弯曲相似,其原理如图1.6所示。
由于其省略了芯棒,为了对弯曲回弹进行补偿,一般在管坯进入弯曲变形之前要进行反变形处理。
即利用反变形滚轮或滑槽对管坯施以适当的压紧预变形。
在弯曲后,相反方向的变形相互抵消,使管材横截面基本能够保持圆形。
2.复杂截面型材拉弯研究
研究复杂截面型材拉弯过程中的截面畸变,作者基于ABAQUS/Explicit平台建立了某汽车用复杂截面型材拉弯成形过程的有限元数值模型,提出了衡量横截面畸变的指标,分析了该过程中截面畸变的特征及成形参数对截面畸变的影响规律。
结果表明:
补拉对型材梯形直边塌陷量有着明显的改善,有利于减小顶边和中边外侧塌陷量和减缓梯形截面间距的变小;拉弯模速度越小,越有利于改善零件截面畸变,尤其是对梯形直边塌陷量;在拉弯成形后期,摩擦系数越小,梯形截面间距和高度、梯形直边塌陷量和塌陷量越小,但折叠张开量越大。
这些研究结果对航空、航天和汽车领域广泛应用的复杂截面型材拉弯成形过程中零件截面畸变的预测和控制,加工效率的提高具有十分重要的意义。
3.拉弯数字化设计
拉弯工艺是型材弯曲成形的重要方法,它可以有效减少回弹,达到提高成形精度的目的。
因此,在飞机、汽车弯曲件成形中得到了广泛的应用。
拉弯卸载后的回弹控制是影响成形精度的主要因素。
拉弯成形过程中,材料受力状态复杂,同时受材料物性参数、摩擦条件等因素的影响,拉弯成形回弹预测很困难。
在实际生产中,拉弯模修正量及工艺参数的确定主要以实际经验或通过试错法来解决,但此方法不能够一次拉弯精确成形型材,且周期长,成本高。
金春凤的学位论文《型材拉弯成形及回弹分析》以型材为研究对象,首先介绍了型材拉弯的基本概念,在此基础上讨论了型材拉弯工艺相对于其他弯曲工艺的优点、用途以及迫切需要解决的两个关键技术问题。
总结了拉弯工艺过程中容易产生的五种成形缺陷,从型材力学性能、截面形状、工艺参数三个方面阐述目前国内外在试验和数值模拟这两方面的研究状况。
介绍了弹塑性力学的初始屈服条件、基本法则,其中包括流动法则和强化法则。
在此基础上以各向同性硬化法则的材料为例推导了应力应变增量关系,为后续的力学分析提供了理论基础。
在介绍的理论基础上,根据拉弯成形力学分析的基本假设,建立了预拉阶段、拉弯弯曲阶段和拉弯补拉阶段三个阶段拉弯成形过程的力学模型。
在拉弯弯曲阶段详细描述了模具与型材间的摩擦力计算方法;型材拉伸弯曲后应力应变分析和弯距的计算方法。
介绍了拉弯成形回弹分析方法,推导了板材回弹半径与回弹角的计算公式;进一步在型材拉弯与板料压弯过程中应力分布差异的基础上推导了型材的回弹半径与回弹角的计算公式。
在拉弯回弹理论分析基础上,形成了结合拉弯零件数字化模型来修正拉弯模模具轮廓的方法;给出了用圆弧样条表示的模具轮廓上点的计算方法;修正后的模具轮廓曲线沿整个轮廓曲线都是一阶连续的,曲率为分段常数。
该方法可通过拉弯件轮廓曲线上布点的密度来控制模具轮廓曲线上曲率分段的多少和误差大小。
本文还通过有限元分析方法计算了拉弯型材的回弹量,用于评估拉弯模轮廓面的回弹修正量,以及拉弯件的校形余量的减少情况。
本文的工作为提高汽车和飞机拉弯件的质量和促进工装的数字化设计提供了一合理有效的方法。
值得大家学习
4.拉弯加工需减少回弹
型材因其良好的机械性能在航空及汽车工业上应用广泛。
型材拉弯是指在型材预拉伸至材料屈服极限时,加载弯曲并同时保持一定的轴向拉力,使之进入模具型槽内而成形的弯曲过程。
在弯曲的同时施加轴向拉力以克服内侧的起皱及改善截面内的应力分布,减少回弹,提高其外形精度。
型材拉弯回弹量的控制是型材拉弯要解决的主要问题之一。
在拉弯零件生产过程中,拉弯模外形是依据拉弯零件的形状设计得到的。
即使在技术规范所允许的残余应变规定下尽量增大轴向拉力,但由于型材零件的相对弯曲半径较大,仍存在一定的回弹量。
拉弯成形后的曲率仍偏小,因而拉弯后仍需要进行校形。
5.拉弯过程中的起皱现象
型材拉弯过程中,中性层以下部分受到纵向压应力作用,径向和宽度方向也受到压应力作用,在三向压应力作用下,容易产生纵向收缩、径向增厚的变形,严重时会造成起皱。
目前,许多学者就型材拉弯起皱问题进行了研究。
Li和ReidE研究了矩形截面型材和矩形板材起皱之间的联系。
Corona和Vaze详细分析了矩形面型材拉弯起皱行为,并进行了实验研究。
Paulsen和Weld采用实验和理论分析相结合的方法研究了纯弯曲下的起皱行为,比较了不同材料、不同截面形状的型材起皱行为的差异。
Paulsen等人基于塑性变形理论,采用能量方法,提出了纯弯曲变形起皱和截面畸变的理论分析模型,并对该模型进行了试验验证。
研究发现,矩形截面型材宽度与厚度的比值(b/t)和型材宽度是影响起皱发生的主要因素;材料性能对起皱的影响也比较明显。
贾俐俐和高锦张指出,型材内侧腹板起皱失稳与薄壁壳体两端受压失稳相似,不仅与压应力大小有关,而且与型材厚度与宽度的比值大小有关,比值越小,越容易发生起皱失稳;增加型材内侧腹板的厚度,可以提高其抗皱能力。
笔者认为,在截面形状一定的情况下,拉弯成形中增大预拉力可以有效地防止起皱的发生。
6.拉弯加工方案探讨
拉弯机主要用于制造尺寸大、外形精度要求较高、相对弯曲半径较大的变曲率挤压和扳弯型材弯曲件,尤其是飞机上的框肋线条、汽车和火车车窗的密封胶条等型材零件生产的必须设备。
拉弯机一般分为转台式和转臂式两类。
型材拉弯主要是指型材在预拉伸至材料屈服极限前加载弯曲并保持一定的轴向拉力,使之压入模具的空槽内而成形的弯曲过程。
拉弯机对型材零件拉弯卸载后,拉弯零件会出现曲率半径回弹及角度回弹现象,为了有效地防止材料的回弹变形,拉弯成形是在精确控制工件的应力、应变以及应变速率下成形的。
拉弯工艺要求精确控制拉弯机的拉伸力、拉伸速度、拉伸位移等工作参数拉伸弯曲是一种复杂的塑性变形过程,成形时毛料受到弯曲力矩和轴向拉伸力的共同作用。
不同的加载顺序对毛料的变形特点和应力分布影响不同。
理论上“先弯后拉”的工艺方案中只需少量的补充拉伸便可获得明显的效果,使零件的回跳量最小。
但实际上,当毛料受到弯曲与模具贴合后,由于摩擦力作用,补拉力很难均匀传递到毛料的所有剖面,毛料的外层纤维易破裂,效果欠佳。
“先拉后弯”工艺方案,毛料虽然在弯曲前获得均匀的塑性拉伸,但仍不能有效地防止弯曲后出现的异号应力分布,卸载后回弹较大,通过弯曲后的补拉可以解决这一问题。
所以,现场生产中大多采用“先拉后弯最后补拉”的复合方案。
弯曲后补拉,理论上所有纤维将均匀伸长,使应力沿断面高度重新分布。
由于消除了异号应力状态的影响,内力矩减小,工件可更好地保持要求的弯曲形状。
7.计算压弯(拉弯)构件的强度计算准则*
对于弯矩沿纵轴变化而最大弯矩发生在构件端部的压弯构件,以及在构件的某些部位存在截面削弱时,非常有可能在这些部位出现塑性铰而导致强度破坏。
计算压弯(拉弯)构件的强度时.根据不同情况,可以采用三种不同的强度计算准则:
1.边缘纤维屈服准则:
采用这个准则时,当构件受力最大截面边缘处的最大应力达到屈服时,即认为构件达到了强度极限。
按此准则,构件始终在弹性阶段工作。
GB50017规范对需要计算疲劳的构件和部分格构式构件的强度计算采用这一准则,GB50018规范也采用这一准则。
2.全截面屈服准则:
这一准则以构件最大受力截面形成塑性铰为强度极限。
3.部分发展塑性准则:
这一准则以构件最大受力截面的部分受压区和受拉区进入塑性为强度极限,截面塑性发展深度将根据具体情况给予规定。
为了避免构件形成塑性铰时过大的非弹性变形,GB50017规范规定,一般构件以这一准则作为强度极限。
为了计算简便并偏于安全,强度计算可用直线式相关关系,并和受弯构件的强度计算一样,用γyWny和γxWnx分别代替截面对两个主轴的塑性抵抗矩。
单向压弯(拉弯)构件的强度计算公式为:
表3-4中有几种单轴对称截面,绕非对称轴弯曲时,与截面边缘1和2对应的地方有γx1和γx2两个不同的数值。
对于格构式构件,当绕截面的虚轴弯曲时,将截面边缘纤维开始屈服看做是构件发生强度破坏的标志,所以γ值取1.0。
8.拉弯、压弯构件的应用
根据受力情况不同,构件分为有偏心拉力作用的构件和有横向荷载作用的拉杆都是拉弯构件。
钢屋架的下弦杆一般属于轴心拉杆,但如果下弦杆的节点之间存在横向荷载就属于拉弯构件。
对于拉弯构件,如果所承受的弯矩不大,而主要承受轴拉力时,它的截面形式和一般轴心拉杆一样。
当拉弯构件要承受较大的弯矩时,应该采用在弯矩作用平面内有较大抗弯刚度的截面。
在拉力和弯矩的共同作用下,截面出现塑性铰是拉弯构件承载能力的极限。
但是对于格构式拉弯构件或者冷弯壁簿型钢拉弯构件,截面边缘的纤维开始屈服就基本上达到了承载能力的极限。
对于轴线拉力很小而弯矩却很大的拉弯构件,也可能和受弯构件一样出现弯扭失稳的破坏。
拉弯构件受压部分的板件也存在局部屈曲的可能性,不过通常这两种可能性都不大。
承受偏心压力作用的构件,有横向荷载作用的压杆以及在构件的端部作用有弯矩的压杆,都属于压弯构件。
厂房的框架柱,多、高层建筑的框架柱和海洋平台的立柱等都属于压弯构件。
对于承受弯矩很小而轴压力很大的压弯构件、其截面形式和一般轴心受压构件相同。
当构件承受的弯矩相对很大时,除了采用截面高度较大的双轴对称截面外,有时还采用如图3-40所示的单独对称截面,以便获得较好的经济效果。
图3-40中的单轴对称截面有实腹式和格构式两种,都是在受压较大一侧分布更多的材料。
为了更有效地利用材料,构件截面沿杆轴线可以变化,如工业厂房中的阶形柱、楔形柱等。
9.压弯构件整体破坏的形式
压弯构件整体破坏的形式有三种:
1.强度破坏:
因为杆端弯矩构件可能发生强度破坏,杆截面局部有较大削弱时也可能产生强度破坏。
2.弯曲失稳破坏:
对于在一个对称轴的平面内作用有弯矩的压弯构件,如果在非弯矩作用的方向有足够支承能阻止构件发生侧向位移和扭转,就只会在弯矩作用的平面内发生,构件的变形形式没有改变,仍为弯矩作用平面内的弯曲变形。
3.弯扭失稳破坏:
如果压弯构件的侧向缺乏足够支承,也有可能发生弯扭失稳破坏。
此时,除在弯矩作用平面存在弯曲变形外,垂直于弯短作用的方向会突然产生弯曲变形。
同时截面绕杆轴发生扭转。
双向弯曲的压弯构件总是空间弯扭失稳破坏。
由于组成压弯构件的板件有一部分受压,和轴心受压构件一样,压弯构件也存在局部屈曲问题。
和轴心受力构件一样,对于正常使用极限状态,拉弯、压弯构件也是通过限制其长细比来满足刚度要求。
10.拉弯加工的未来发展趋势及展望
1.在拉弯与弯管加工中,对于异型型材拉弯成形的研究还有待进一步研究。
主要是由于异型型材由于截面形状复杂,截面畸变严重,对其建立力学模型,不仅涉及回弹计算问题,而且还涉及截面畸变等成形缺陷的预测问题。
2.铝合金型材力学性能的屈服准则。
目前已提出的屈服准则还没有一个能完整描述铝合金的各向异性,因此要想准确的对拉弯成形过程进行数值模拟研究,必须提出适合铝合金型材力学性能的屈服准则,这方面还有待进一步研究。
3.型材拉弯的成形极限。
型材拉弯由于截面变量及变化的影响,加之截面尺寸通常不大,难以沿用板材的典型试验方法获取成形性指标或建立成形极限图来衡量成形极限。
因此针对型材截面形状和变形特点,建立适用于型材拉弯的成形极限判据是目前急需解决的问题之一。
4.型材拉弯成形模具轮廓的确定。
由于成形中存在截面畸变和起皱,并且沿型材长度方向不同位置的截面形状不同,变形后截面形状描述困难,卸载时的弯曲力矩M和截面惯性矩I很难求得,因此对于回弹量计算、型材拉弯成形模具轮廓的确定,目前还没有理想的解决方法,尚有待进一步的深化研究。
5.拉弯精确成形智能控制的方法。
目前工艺参数的确定主要是依赖实际经验或通过试错法来解决,这样所制定的工艺参数的优劣依赖操作者的经验,不能适应材料特性和工况条件的变化所引起的成形质量的波动。
因此还有待进一步研究拉弯精确成形智能控制的方法,对成形回弹量进行在线预测控制,实现一次拉弯精确成形。
11.拉弯加工工艺参数及研究现状*
型材拉弯工艺参数主要包括五点:
预拉伸量、弯曲半径、弯曲角度、补拉伸量、摩擦及润滑等。
型材工艺参数的研究现状初步总结如下:
型材工艺参数的研究现状主要研究者研究内容研究结论
孙惠学对异型断面型材拉弯成形进行了数值模拟,得出了沿型材长度方向的回弹值分布曲线和最大回弹值随补拉力变化的曲线。
这对拉弯模具的设计和工艺参数的确定有重要作用。
J.E.Miller开发了一种可对管材内腔施加气压的拉弯试验装置,对拉弯工艺参数进行优化研究;建立了矩形截面铝型材拉弯过程力学模型,分析了摩擦、轴向应力和内压力对截面畸变、回弹和伸长的影响,得出了减小预拉力,可防止截面畸变,采用补拉力来减少回弹。
AridH.Clausen采用试验和数值模拟方法对加载方式进行研究,得出结论:
1.相同预拉力下,预拉同时进行弯曲比预拉完毕后再弯曲回弹量减少;没有补拉力的情况下,加大预拉力,回弹明显减少;增加补拉,回弹量减少。
2.若力控制法中预拉力达到材料屈服极限,则位移控制法中的回弹量介于力控制法中有补拉和没补拉之间。
3.在力控制法中,相同预拉力且不加补拉力情况下,预拉完毕后再弯曲比预拉同时进行弯曲的截面畸变小。
4.加大预拉力或加补拉力,截面畸变明显增加。
5.而位移控制法中因型材两端夹持不动,随着模具上移型材弯曲变形程度加大,拉力逐渐增大,导致截面畸变比力控制法的大。
刁可山、周贤宾、金朝海、李晓星(北京航空航天大学)通过对复杂截面挤压型材的直进台面式拉弯成形,研究型材截面畸变和回弹随补拉力增大的变形规律和摩擦系数对成形精度的影响规律。
于成龙对角型材拉弯成形过程的研究,预拉力、补拉力和侧压力对拉弯工件的应力应变分布和回弹的影响规律。
AridH.Clausen,OddS.Hopperstadd对矩形铝型材等曲率拉弯成形的工艺参数进行分析与试验工件的回弹是受预拉力及材料的应变硬化指数控制。
截面畸变受截面的几何形状,磨具半径和预拉力控制,增加预拉力和减少应变硬化指数都可以减少回弹。
王永军采用BP神经网络及数据库方法对拉弯成形过程智能控制进行了较深入的研究,建立了拉弯成形过程智能控制系统,实现了拉弯成形过程工艺参数预测控制。
综上所述,工艺参数对型材拉弯成形性有着重要而复杂的影响,而拉弯工艺参数的研究主要采用试验和数值模拟这两种方法进行,由于拉弯机对型材零件拉弯卸载后拉弯件会出现曲率半径回弹现象,为了克服材料的回弹变形,在拉弯成形过程中必须精确的控制工件所受的应力、应变以及应变速度,并且在成形过程中施加一定的侧压力,为此,拉弯工艺参数的精确制定是目前的难点之一。
12.拉弯加工中容易产生的缺陷
拉弯件容易产生以下成形缺陷:
1.型材弯曲变形区外侧壁厚变薄;2.型材弯曲变形区内侧壁厚增大、起皱;3.横截面形状畸变;4.回弹。
在拉弯工艺中,回弹是模具设计中要考虑的重要因素,拉弯件的最终成形很大程度上受到成形后回弹量的影响。
回弹主要表现为整体卸载回弹、切边回弹。
当回弹量超过允许值后就是成形缺陷,影响拉弯件的几何精度。
为了控制相对弯曲半径较大的零件在成形后所产生的回弹量,可以采用拉弯成形工艺,这样可以使成形后的零件具有合理的校形余量,减少工人进行手工校形的工作量,如果零件的回弹量太大就会造成手工校形无法进行修正,从而导致零件报废。
因此,回弹是影响和制约拉弯模具和拉弯件成形的重要因素。
13.拉弯加工中的拉弯方式及适合的拉弯加工范围*
拉弯方式一般包括转台式和张臂式两种。
转台式的基本原理是台面连同模具旋转,从而完成型材的拉伸和弯曲,而拉伸作动筒固定在床身上。
适用于成形精度高,半径小的型材拉弯件,也适用于在中空型材内加芯轴和填充材料的拉弯成形。
张臂式的基本原理是拉弯机的台面固定不动,由两侧支臂旋转实现型材的拉弯成形。
根据轴向拉力与弯矩的组合方式、变形温度以及变形速度的不同,到目前比较成熟的拉弯方法有以下四种:
1.先拉伸后弯曲再拉伸:
首先对型材截面的形心施加轴向预拉力,使横截面上的应力达到屈服极限;而后在预拉力不变的条件下施加弯矩使型材贴模;最后补加轴向拉力,总拉力的数值以使型材最小半径截面上的内层材料达到拉伸屈服极限为宜。
预拉力的作用在于消除供应状态的初始扭曲变形以及防止弯曲过程中型材腹板的边缘失稳起皱。
足够的总拉力保证了回弹量显著减小并减少或消除残余应力。
优点:
回弹量较小,能消除初始扭曲;防止腹板失稳起皱;残余应力小或不存在。
缺点:
有外摩擦的影响。
适用范围:
除弯角特别大以外的一切型材。
2.先拉伸后弯曲:
首先对型材截面的形心施加轴向拉力,而后在拉力不变的条件下施加弯矩使之贴模。
轴向拉力的数值以弯曲后型材内部截面上最小的应力达到拉伸屈服极限为宜。
优点:
无摩擦的影响,能消除初始扭曲,防止腹板失稳起皱。
缺点:
回弹量较大,有残余应力存在。
适用范围:
弯角很大的型材(弯角θ≥90°~180°)。
3.先弯曲后拉伸:
首先对型材施加弯矩使之贴模;而后施加轴向拉力。
轴向拉力的数值以使型材内部截面上最小的应力达到拉伸屈服极限为宜。
优点:
回弹量较小,残余应力小或不存在。
缺点:
有外摩擦的影响,不能消除初始扭曲,腹板可能失稳起皱。
4.二次拉弯:
第一次拉弯仍采用上述的先拉伸后弯曲再拉伸的方法,由于第一次拉弯后型材已基本成形,但仍有一定的回弹量,所以第二次拉弯时弯曲变形很小,剖面上最外层与最内层材料的应力差很小,卸载后回弹量显著减少。
优点:
不考虑回弹量的情况下零件能较好的贴膜。
缺点:
增加一次拉弯工序。
通过前四种方法的主要优缺点(如回弹量的大小、外摩擦的影响、失稳起皱的可能性、消除型材初始扭曲变形的可能性以及残余应力的大小)的比较,显然第一种方法比第二、三种方法具有较显著的优越性,在生产中已获得广泛使用。
由于第一方法的弯角大小受外摩擦影响的限制,因此在特殊情况下(对于弯角很大的型材)才采用第二种方法。
第三种方法在理论上是研究第一种方法的基础,所以在理论上有研究价值,然后在实际应用方面已为第一种方法所包含。
二次拉弯法由于它可以在拉弯模不考虑回弹量的情况下零件较好的贴膜,已被生产实践愈来愈广泛地采用。
边拉伸边弯曲的方法所存在的问题是一方面回弹量的减少次于上述第一、三种方法;另一方面实际操作按遵循简单加载条件,有一定的困难。
14.拉弯及弯管工艺介绍及拉弯加工中有待解决的问题
型材拉弯是指在型材预拉伸至材料屈服极限时加载弯曲并同时保持一定的轴向拉力,使之压入模具型槽内而成形的弯曲过程。
在弯曲的同时施加轴向拉力用以克服内侧的起皱、改善截面内的应力分布、减少回弹、提高外形精度。
拉弯和其他弯曲工艺相比有如下特点:
1.能成形空间结构复杂的型材零件;2.能成形屈强比大的型材弯曲零件;3.具有不同工艺方法相结合的综合成形特点;4.弯曲精度高,回弹小。
型材拉弯在飞机、汽车型材弯曲件的生产中得到了非常广泛的应用。
在飞机生产中,飞机框肋上的缘条、机身前后段、发动机短仓的长桁等尺寸大的型材弯曲件是组成飞机骨架的关键零件,并直接影响到飞机的气动力外形,形状精度要求很高。
因此在汽车生产中,拉弯主要用于加工车身结构和保险杠的中空铝型材弯曲件,在保持与钢铁制件同样的抗冲击强度条件下,能减轻车体重量,降低使用成本。
拉弯工艺可实现铝型材的高精度弯曲,但由于拉弯成形中可能会出现壁厚减薄破裂、起皱、截面畸变等成形缺陷,而这些成形缺陷与型材的材料性能、截面形状及工艺参数这些因素密切相关,非常复杂。
目前拉弯成形性的研究迫切需要解决以下两个关键技术问题:
1.合理确定拉弯成形过程中的工艺参数;2.准确预测拉弯零件的回弹量。
实际生产中拉弯模修正量及工艺参数的确定主要以实际经验或通过试错法来解决,即根据经验反复调整修模量,改变主拉力、补拉力等工艺参数。
有时还需要多次预拉弯及热处理,最终成形后还要进行人工校形。
这种方法成本高,时间长,形状精度难以保证。
随着产品加工精度要求的日益提高,近/净成形的要求逐步增加,数字化设计制造也对拉弯成形工艺提出了新的要求,传统的拉弯成形工艺已不能满足现代生产的需要。
随着科技的进步,技术的不断的革新,特别是CAD/CAE技术的不断发展,大型的CAD通用软件为拉弯模具的设计提供了强大的技术支持。
在CAD软件环境下,可以得到零件的一些有效的几何信息,例如通过几何分析功能,可以得到整条曲线的曲率分布及其大小,可以检查曲面的质量。
同时其提供的二次开发工具为用户开发自己专用的CAD系统提供了技术支持。
CAE在型材拉弯成形工艺中的应用,使得技术人员可以更直观的观察到型材的动态成形过程,以及每个瞬时材料的应力、应变、位移分布,通过这些基本数据,可以得出型材的成形性能,并结合其力能参数来调整模具的参数和成形工艺,修改模具的型面,调整回弹量。
CAE技术已经成为型材拉弯成型中十分重要的工具,然而它在实际中的应用却受到诸多因素的限制。
要准确地对拉弯过程进行数值模拟,就必须精确描述工件材料的力学性能,合理确定边界条件,同时能准确地处理拉弯中的各种非线性问题;此外,还要求使用者具有一定的理论基础、掌握相关的软件知识并对生产工艺有相当的了解。
其中的任何一个环节出现失误都将导致分析的结果和实际情况的偏差。
因此,有必要对拉弯机理进行深入的研究,结合CAE技术,确定拉弯工艺参数对工件成形质量的影响规律,使成形后的零件具有合理的校形余量,从而提高汽车和飞机拉弯件的质量和加速汽车和飞机拉弯件的国产化进程有着十分重要的意义。
15.弯管美观工艺方法
1.将钢管的一端用木楔子堵结实,朝下立起(注意:
要留外头儿,以方便拨出来),把用火炒过的砂子(颗粒度不能太大,也不能太不,筛好的建筑用砂最合适)趁热用漏斗慢慢灌进去,一边灌,一边用手锤敲打管壁,使干砂子充分填实后,紧紧地打入另一个同样的木楔子,直到干燥的砂子在管中没有任何松动的可能为止。
2.在工作平台上,画出弯管大样:
外园半径为50+外径/2,内径为50-外径/2,并在开始弯曲处与停止处点焊上掣子,防止煨过头或