硫化铅精矿的直接冶炼.docx
《硫化铅精矿的直接冶炼.docx》由会员分享,可在线阅读,更多相关《硫化铅精矿的直接冶炼.docx(22页珍藏版)》请在冰豆网上搜索。
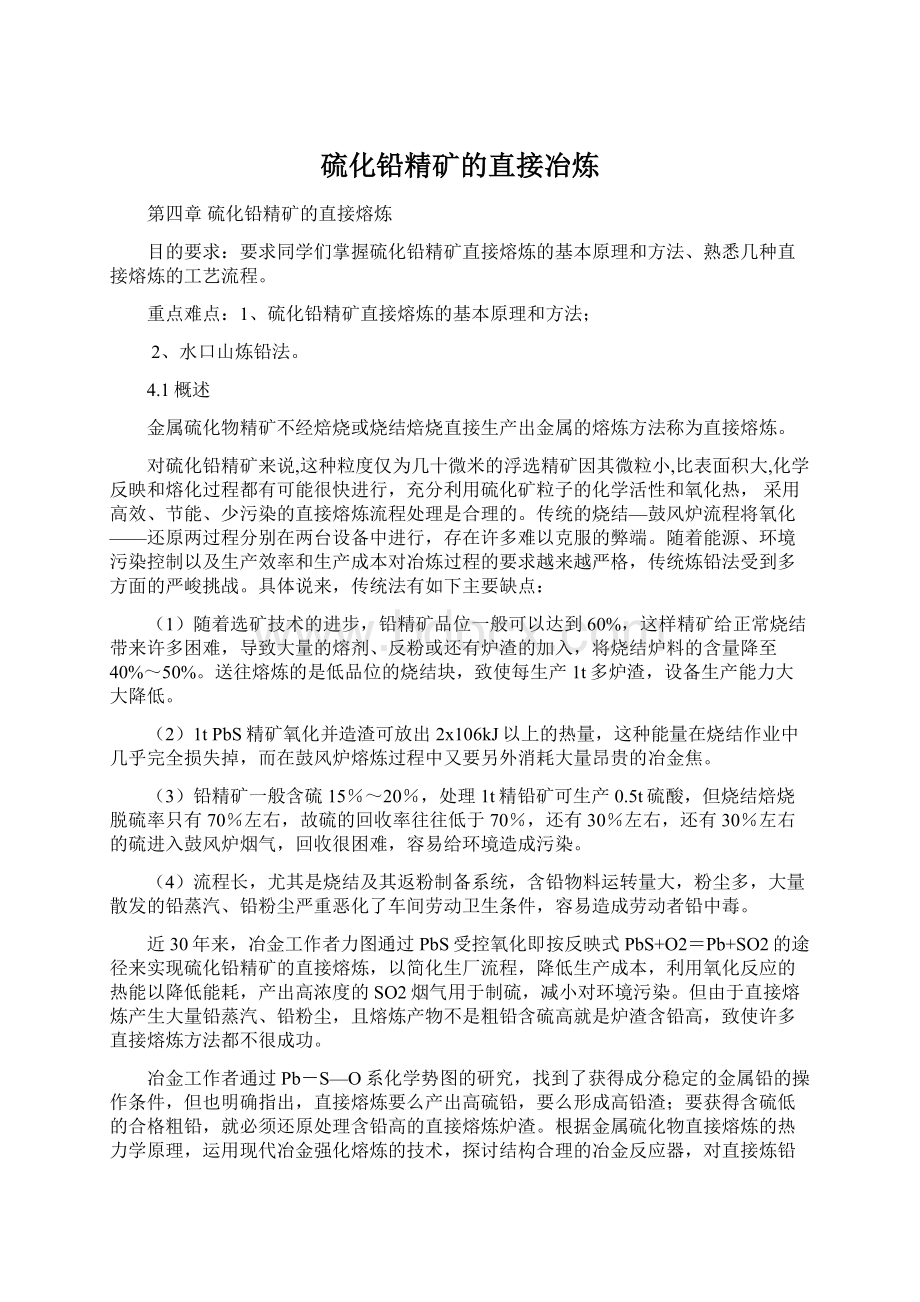
硫化铅精矿的直接冶炼
第四章硫化铅精矿的直接熔炼
目的要求:
要求同学们掌握硫化铅精矿直接熔炼的基本原理和方法、熟悉几种直接熔炼的工艺流程。
重点难点:
1、硫化铅精矿直接熔炼的基本原理和方法;
2、水口山炼铅法。
4.1概述
金属硫化物精矿不经焙烧或烧结焙烧直接生产出金属的熔炼方法称为直接熔炼。
对硫化铅精矿来说,这种粒度仅为几十微米的浮选精矿因其微粒小,比表面积大,化学反映和熔化过程都有可能很快进行,充分利用硫化矿粒子的化学活性和氧化热,采用高效、节能、少污染的直接熔炼流程处理是合理的。
传统的烧结—鼓风炉流程将氧化——还原两过程分别在两台设备中进行,存在许多难以克服的弊端。
随着能源、环境污染控制以及生产效率和生产成本对冶炼过程的要求越来越严格,传统炼铅法受到多方面的严峻挑战。
具体说来,传统法有如下主要缺点:
(1)随着选矿技术的进步,铅精矿品位一般可以达到60%,这样精矿给正常烧结带来许多困难,导致大量的熔剂、反粉或还有炉渣的加入,将烧结炉料的含量降至40%~50%。
送往熔炼的是低品位的烧结块,致使每生产1t多炉渣,设备生产能力大大降低。
(2)1tPbS精矿氧化并造渣可放出2x106kJ以上的热量,这种能量在烧结作业中几乎完全损失掉,而在鼓风炉熔炼过程中又要另外消耗大量昂贵的冶金焦。
(3)铅精矿一般含硫15%~20%,处理1t精铅矿可生产0.5t硫酸,但烧结焙烧脱硫率只有70%左右,故硫的回收率往往低于70%,还有30%左右,还有30%左右的硫进入鼓风炉烟气,回收很困难,容易给环境造成污染。
(4)流程长,尤其是烧结及其返粉制备系统,含铅物料运转量大,粉尘多,大量散发的铅蒸汽、铅粉尘严重恶化了车间劳动卫生条件,容易造成劳动者铅中毒。
近30年来,冶金工作者力图通过PbS受控氧化即按反映式PbS+O2=Pb+SO2的途径来实现硫化铅精矿的直接熔炼,以简化生厂流程,降低生产成本,利用氧化反应的热能以降低能耗,产出高浓度的SO2烟气用于制硫,减小对环境污染。
但由于直接熔炼产生大量铅蒸汽、铅粉尘,且熔炼产物不是粗铅含硫高就是炉渣含铅高,致使许多直接熔炼方法都不很成功。
冶金工作者通过Pb-S—O系化学势图的研究,找到了获得成分稳定的金属铅的操作条件,但也明确指出,直接熔炼要么产出高硫铅,要么形成高铅渣;要获得含硫低的合格粗铅,就必须还原处理含铅高的直接熔炼炉渣。
根据金属硫化物直接熔炼的热力学原理,运用现代冶金强化熔炼的技术,探讨结构合理的冶金反应器,对直接炼铅进行多种方法的研究,其中有些已经成功地用于大规模工业生产,显示了直接熔炼的强大生命力。
可以预言,直接熔炼将逐渐取代传统法生产金属铅。
4.2硫化铅精矿直接熔炼的基本原理和方法
4.2.1直接熔炼的基本原理
金属硫化物精矿直接熔炼的特点之一是利用工业氧气,二是采用强化冶炼过程的现代冶金设备,从而使金属硫化物受控氧化熔炼在工业上应用成为可能。
在铅精矿的直接熔炼中,根据原料主成分PbS的含量,按照PbS氧化发生的基本反应PbS+O2==Pb+SO2,控制氧的供给量与PbS的加入量的比例(简称为氧/料比),从而决定了金属硫化物受控氧化发生的程度。
实际上,PbS氧化生成金属铅有两种主要途径:
一是PbS直接氧化生成金属铅,较多发生在冶金反应器的炉膛空间内;二是PbS与PbO发生交互反应生成金属铅,较多发生在反应器熔池中。
为使氧化熔炼过程尽可能脱除硫(包括溶解在金属铅中的硫),有更多的PbO生成是不可避免的,在操作上合理控制氧/料比就成为直接熔炼的关键。
在理论上,可借助Pb-S-O系硫势—氧势化学势图(图4-1)进行讨论。
在图4-1中,横坐标和纵坐标分别代表Pb-S-O系中的硫势和氧势,并用多相体系中硫的平衡分压和氧的平衡分压表示,其对数值分别为lgPs2和lgPo2.图中间一条黑实线(折线)将该体系分成上下两个稳定区(又称优势区)。
上部PbO-PbSO4为熔盐,代表PbS氧化生成的烧结焙烧产物。
在该区域,随着硫势或SO2势增大,烧结产物中的硫酸盐增多;图下部为Pb-PbS共晶物的稳定区,由于Pb和PbS的互溶度很大,因此在高温下溶解在金属铅中的S含量可在很大范围内变化。
如图所示,在低氧势、高硫势条件下,金属铅相中的硫可达13%,甚至更高,这就形成了平衡于纵坐标的等硫量(S%)线。
随着硫势降低,意味着粗铅中更多的硫被氧化生成SO2进入气相。
在这里,用点实线(斜线)代表二氧化硫的等分压线(用PSO2表示)。
等PSO2线表示在多相体系中存在的平衡反应1/2S2+O2=SO2.
在一定PSO2下,体系中的氧势增大,则硫势降低。
反之亦然
4.2.2直接炼铅的方法
硫化铅精矿直接熔炼方法可分为两类:
一类是把精矿喷入灼热的炉膛空间,在悬浮状态下进行氧化熔炼,然后在沉淀池进行还原和澄清分离,如基夫赛特法.这种熔炼反应主要发生在炉膛空间的熔炼方式称为闪速熔炼.另一类是把精矿直接加入鼓风翻腾的熔体中进行熔炼,如QSL法、水口山法、奥斯麦特法和艾萨法等。
这种熔炼反应主要发生在熔池内的熔炼方式称为熔池熔炼。
按照闪速熔炼和熔池分类的硫化铅精矿直接熔炼的各种方法概括起来列于表4-1。
熔池熔炼法除了此表列出的底吹和顶吹法外,正在试验中的还有瓦纽柯夫法,它是一种侧吹的熔池熔炼方法。
无论是闪速熔炼,还是熔池熔炼,上述各种直接熔炼铅方法的共同优点是:
(1)硫化精矿的直接熔炼取代了氧化烧结焙烧与鼓风炉还原熔炼两过程,冶炼工序减少,流程缩短,免除了反粉破碎和烧结车间的铅粉、铅尘和SO2烟气污染,劳动卫生条件大大改善,设备投资减少。
(2)运用闪速熔炼或熔池的方法,采用富氧或氧气熔炼,强化了冶金过程。
由于细粒精矿直接进入氧化熔炼体系,充分利用了精矿表面巨大活性,反应速度快,加速了反应器中气-液-固物料之间的传热传质。
充分利用了硫化精矿氧化反应发热值,实现了自热或基本自热熔炼。
能耗低,生产率高,设备床能率大,余热利用好。
(3)氧气或富氧熔炼的烟气SO2浓度高,硫的利用率高。
(4)由于熔炼过程得到强化,可处理铅品位波动大、成分复杂的各种铅精矿以及其他含Pb、Zn的二次物料,伴生的各种有价元素综合回收好。
直接炼铅法具有下列优点:
熔炼强度高。
在双悬状态下,强劲的气流带动炉料相互碰撞;或在熔池内,气流使熔体剧烈翻腾。
热的利用率高。
烟气SO2浓度高;有利于综合回收。
直接炼铅既是高效、节能的提取治金方法,也是综合利用高、环境保护好的方法。
4.3基夫赛特法炼铅(Kivcet)
前苏联有色金属科学研究院从六十年代开始研究开发的直接炼铅工艺,八十年代用于大型工业生产,1986年初在哈萨克斯坦的乌斯季—卡缅诺尔斯克建成基夫赛特法炼铅厂。
1986年意大利萨明公司购买其专利建成处理炉料600t/d铅厂(KSS厂),目前在生产。
1996年底,加拿大科明科公司120000t/a粗铅的基夫赛特炼铅厂投产成功,目前在生产。
基夫赛特法炼铅属于闪速熔炼一电热还原法(Kivcet法),其反应过程主要在基夫赛特炉的反应塔空间进行。
其设备连接图如下图所示:
A.优点:
1.原料适应性强,能处理含铅锌渣料;
2.主要金属回收率高,综合回收较好;
3.渣含铅低,<2.0%;
4.烟尘率低,约5%,可直接返回炉内冶炼;
5.生产成本低,粗铅综合能耗0.35t标煤/t;
6.炉子寿命长,炉寿可达3年,维修费用省。
B.缺点:
1.原料需干燥至含水1%以下。
2.一次性投资较高。
基夫赛特炼铅技术属哈萨克斯坦东方有色金属矿冶研究院专利。
目前该技术仍处于专利保护期内,我国采用该技术必须购买专利许可证,实行技术引进。
需要引进内容:
1购买专利许可证;
2干燥、熔炼工序的基本设计及详细设计的技术参数;
3现场指导及试车投产时技术服务;
4基夫赛特炉专用物料喷嘴。
报价420万美元(前3项)。
C.主要技术经济指标
1、炉料含水<1%
2、干燥强度35kg/m3.h
3、干燥回收率99%
4、Kivcet炉料量1583.81t/d炉料
5、炉料含铅24.17%
6、铅回收率96.96%
7、银入粗铅率99.5%
8、金入粗铅率98.06%
9、铜入粗铅率80%
10、锌入氧化锌率50%
11、烟尘率5~7%
12、竖炉烟气SO2浓度18%
13、渣率49.5%
14、渣含铅2.10%
15、硫酸净化工序SO2回收率99.5%
16、硫酸总转化率99.75%
17、车间总硫回收率99.05%
18、尾气中SO2含量870.16mg/m3(标)
19、工作制度330d/a,24h/d
1)生产过程
含铅物料+熔剂+工业氧(~95%)喷入竖炉内,反应温度1573-1673K,硫化铅精矿在悬浮状态下完成氧化脱硫和熔化过程,生成粗铅、高铅炉渣和含SO2的烟气,并放出大量热。
由于氧气-精矿的喷射速度达100~120m/s,炉料的氧化、熔化和形成初步的粗铅、炉渣熔体仅在2~3s内完成。
当焦炭通过约4m高的反应塔空间时,被灼热的炉气加热,但由于精矿粒度细,着火温度低,先于焦炭燃烧。
焦炭在反应塔下落过程中仅有10%左右被燃烧。
焦炭密度小,落在反应塔下言的沉淀熔体上面形成赤热的焦炭层,这就像炼铅鼓风炉风口区的焦炭层一样,将含有一次粗铅和高铅炉渣的熔体进行过滤,使高铅渣中的PbO被还原出金属铅来,故称为焦炭过滤层。
在这里,约有80%~90%的氧化铅被还原。
基夫赛特法直接炼铅系统的设备组合如图4-2,炉料在反应塔和焦炭层发生的化学反应及其温度变化沿断面的分布如图4-3。
沉淀池加入焦炭块漂浮在熔体表面,氧化铅熔体在通过漂浮在熔池上赤热焦炭层(焦滤层)时被还原。
熔体中氧化锌也被还原进入烟尘。
产物:
粗铅、高铅炉渣、粗氧化锌、烟尘
2)基夫赛特熔炼的优点:
①劳动条件好;
②对原料适应性强,Pb20~70%,S13.5%~28%,Ag100~8000g/t的原料;
③连续作业,氧化和还原在一个炉内完成,生产环节少;
④烟气SO2浓度高,可直接制酸;烟气量少,带走的热少,余热利用好,从而烟气冷却和净化设备小,烟尘率约5%,烟尘可直接返回炉内冶炼;
⑤主金属回收率高(Pb回收率>98%),渣含铅低(<2%),贵金属回收率高,金、银入粗铅率达99%以上,还可回收原料中锌60%以上;
⑥能耗低,粗铅能耗为0.35t标煤/t;
⑦炉子寿命长,炉期可达3年,维修费用低。
3)基夫赛特熔炼的缺点:
①原料准备比较复杂:
对炉料和水分要求严格,粒度要控制在0.5mm以下,最大不能超过1mm,需要干燥至含水在1%以下;
②建设投资较高。
4.4氧气底吹炼铅法
4.4.1QSL法
德国鲁奇公司于七十年代研究开发的直接炼铅工艺。
德国施托尔贝格炼铅厂和韩国温山QSL厂,先后于1990年和1992年建成投产。
1989年加拿大科明科公司的QSL法炼铅厂投产,因工艺设备问题,仅试产3个月无法继续生产而被迫关闭,1993年用基夫赛特法改建;
我国西北冶炼厂20世纪80年代引进的QSL技术,于1992年建成投产,投产不久因故停产。
4.4.1.1QSL炉
QSL炉立体图
(1)设备
反应器:
卧式圆筒形转炉,内衬铬镁砖,外包钢板炉子中置隔墙(隔墙下部有连通孔,双烟道),分为氧化段和还原段。
加料口:
加入铅精矿或其他含铅二次物料
喷嘴:
氧化段喷入氧气;还原段喷入氧气、粉煤或天然气。
炉子向氧化段倾斜5%,可90度转动。
(2)工艺过程
熔池深度1500mm,炉底铅液深度250mm。
氧化段:
炉料加入后,在炉渣-金属-气体乳状熔体中发生反应,生产Pb和PbO,放出热量,实现自热熔炼,此时的氧势较高,约2.2左右。
初铅含S0.3-0.5%,初渣含铅40-45%。
氧化段温度1050~1100℃.
还原段:
粗渣从隔墙下流入到还原段。
粉煤(或天然气)和氧气喷入产生CO和H2,使高PbO炉渣在1250℃被还原。
还原区氧势较低,约为0.2左右。
温度实较高,为1150℃~1250℃。
炉渣在流向还原区端墙上的排渣口的过程中逐渐被还原,还原形成的金属铅(二次粗铅)沉降到炉低流向氧化区与一次粗铅(初铅)汇合。
粗铅与炉渣逆向流动,从虹吸口排出;炉渣从渣口连续或间断排出。
与氧化段硫化物氧化速度比较,还原速度较慢,还原段长度约为氧化段的2倍。
对含锌高的原料,QSL法的终渣需送烟化炉进一步挥发锌。
反应器熔池深度直接影响熔体和炉料的混合程度。
浅熔池操作不但两者混合不均匀,而且易被喷枪喷出的气流穿透,从而降低氧气或氧气-粉煤的利用率。
因此适当加深反应器熔池深度对反应器的操作是有利的。
由熔炼工艺特点所决定,QSL反应器内必须保持有足够的底铅层,以维持熔池反应体系中的化学势和温度的基本恒定。
在操作上,为使渣层与虹吸出铅口隔开,以保证液铅能顺利排出,也必须有足够的底铅层。
底铅层的厚度一般为200~400mm,而渣层宜薄,为100~150mm。
反应器氧化区的熔池深度大,一般为500~1000mm。
实践证明,还原段的起始处增设一个挡圈,使还原段始终保持200mm高的铅层,这有利于炉渣中被还原出来的铅珠能沉降下来,从而降低终渣含铅;此外,降低还原段的渣液面高度,使还原段的渣层较薄,渣层与铅层的界面交换传质强度加大,同时渣层的涡流强度也减弱了,利于铅沉降。
QSL法直接炼铅流程如图所示:
A.优点:
①氧化脱硫和还原在一座炉内连续完成;
②备料简单;
③返料量少,有利于提高设备生产能力和降低包括能源、劳动力等消耗费用;
④富氧使产生的烟尘量减少,烟中SO2浓度高,可直接制酸;
⑤以煤代焦,成本更低。
⑥主要金属回收率高。
B.缺点:
操作条件控制难度较高;烟尘率高(20~30%);喷枪使用寿命短;渣含铅高,需进一步处理。
4.4.2水口山法
水口山炼铅法是我国自行开发的一种氧气底吹直接炼铅法。
在20世纪80年代,水口山第三冶炼厂在规模为Φ2234mm×7980mm的氧化反应炉进行半工业试验成功后,扩大推广应用到河南豫光金铅公司和安徽池州两家铅厂生产,从而形成了氧气底吹熔炼-鼓风炉还原铅氧化渣的炼铅新工艺。
生产实践证明,对于我国目前生产上采用的烧结-鼓风炉炼铅老工艺改造,水口山法是一项污染少、投资省、见效快的可取方案。
氧气底吹熔炼一次成铅率与铅精矿品位有关,品位越高,一次粗铅产出率越高,为适应下一步鼓风炉还原要求,铅氧化渣含应在40%左右,略低于传统法炼铅原烧结块含铅率,相应地,一次粗铅产出率一般为35%~40%,粗铅含S<0.2%。
在氧气底吹熔炼过程中,为减少PbS的挥发,并产出含S、As低的粗铅,需要控制铅氧化渣的熔点不高于1000℃,CaO/SiO2比(0.7~0.8)有利于降低鼓风炉渣含铅。
考虑以两个因素,铅氧化渣中CaO/SiO2比控制在0.6~0.7之间为宜。
和烧结块相比,擗氧化渣孔隙率较低,同时,由于是熟料,其熔化速度较烧结块要快,熔渣在鼓风炉焦区的停留时间短,从而增加了鼓风炉还原工艺的难度。
但是,生产实践证明,采用鼓风炉处理铅氧化渣在工艺上是可行的,鼓风炉渣含Pb可控制在4%以内。
通过炉型的改进、渣型的调整、适应控制单位时间物料处理量等措施,渣含Pb可望进一步降低。
另外,尽管现有指标较烧结-鼓风炉工艺渣含Pb量1.5%~2%的指标稍高,但由于新工艺鼓风炉渣量仅为传统工艺鼓风炉渣量的50%~60%,因而,鼓风炉熔炼铅的损失基本不增加。
在技改过程中,利用原有的鼓风炉作适当改进即可,这样,可以节省基建投资。
该工艺的一个重要组成部分是氧气站,目前,国内工业纯氧的制备技术有两种,一种为传统的深冷法,一种为变压吸附法。
前者生产能力大,氧气纯度高,但成本高,氧气单位电耗一般为0.6~0.7kWh/Nm3;后者投资省,成本低,氧气单位电耗低于0.45kWh/Nm3。
国产1500m3/h的吸附制氧设备已研制成功,其氧气纯度达93%以上。
对于1×104t/a规模的炼铅厂,氧气需要量一般为700~800m3/h。
采用变压吸附法制氧完全能满足中型炼铅厂技改需要。
水口山法氧气底吹熔炼取代传统烧结工艺后,不仅解决了SO2烟气及铅烟尘的污染问题,还取得了如下效益:
(1)由于熔炼炉出炉烟气SO2浓度在12%以上,对制酸非常有利,硫的总回收率可达95%。
(2)熔炼炉出炉烟气温度高达1000~1100℃,可利用余热锅炉或汽化冷却器回收余热。
(3)采用氧气底吹熔炼,原料中Pb、S含量的上限不受限制,不需要添加返料,简化了流程,且取消了破碎设备,从而降低了工艺电耗。
(4)由于减少了工艺环节,提高了Pb及其他有价金属的回收率,氧气底吹熔炼车间Pb的机械损失<0.5%。
水口山炼铅法是我国自行开发的一种氧气底吹直接炼铅法。
在20世纪80年代,水口山第三冶炼厂在规模为Φ2234mm×7980mm的氧化反应炉进行半工业试验成功后,扩大推广应用到河南豫光金铅公司和安徽池州两家铅厂生产,从而形成了氧气底吹熔炼-鼓风炉还原铅氧化渣的炼铅新工艺。
生产实践证明,对于我国目前生产上采用的烧结-鼓风炉炼铅老工艺改造,水口山法是一项污染少、投资省、见效快的可取方案。
铅精矿的氧化熔炼是在一个水平回转式熔炼炉中进行,该底吹炉结构与QSL炉氧化段类似。
氧气底吹熔炼一次成铅率与铅精矿品位有关,品位越高,一次粗铅产出率越高,为适应下一步鼓风炉还原要求,铅氧化渣含应在40%左右,略低于传统法炼铅原烧结块含铅率,相应地,一次粗铅产出率一般为35%~40%,粗铅含S<0.2%。
在氧气底吹熔炼过程中,为减少PbS的挥发,并产出含S、As低的粗铅,需要控制铅氧化渣的熔点不高于1000℃,CaO/SiO2比(0.7~0.8)有利于降低鼓风炉渣含铅。
考虑以两个因素,铅氧化渣中CaO/SiO2比控制在0.6~0.7之间为宜。
和烧结块相比,铅氧化渣孔隙率较低,同时,由于是熟料,其熔化速度较烧结块要快,熔渣在鼓风炉焦区的停留时间短,从而增加了鼓风炉还原工艺的难度。
但是,生产实践证明,采用鼓风炉处理铅氧化渣在工艺上是可行的,鼓风炉渣含Pb可控制在4%以内。
通过炉型的改进、渣型的调整、适应控制单位时间物料处理量等措施,渣含Pb可望进一步降低。
另外,尽管现有指标较烧结-鼓风炉工艺渣含Pb量1.5%~2%的指标稍高,但由于新工艺鼓风炉渣量仅为传统工艺鼓风炉渣量的50%~60%,因而,鼓风炉熔炼铅的损失基本不增加。
在技改过程中,利用原有的鼓风炉作适当改进即可,这样,可以节省基建投资。
该工艺的一个重要组成部分是氧气站,目前,国内工业纯氧的制备技术有两种,一种为传统的深冷法,一种为变压吸附法。
前者生产能力大,氧气纯度高,但成本高,氧气单位电耗一般为0.6~0.7kWh/Nm3;后者投资省,成本低,氧气单位电耗低于0.45kWh/Nm3。
国产1500m3/h的吸附制氧设备已研制成功,其氧气纯度达93%以上。
对于1×104t/a规模的炼铅厂,氧气需要量一般为700~800m3/h。
采用变压吸附法制氧完全能满足中型炼铅厂技改需要。
水口山法氧气底吹熔炼取代传统烧结工艺后,不仅解决了SO2烟气及铅烟尘的污染问题,还取得了如下效益:
(1)由于熔炼炉出炉烟气SO2浓度在12%以上,对制酸非常有利,硫的总回收率可达95%。
(2)熔炼炉出炉烟气温度高达1000~1100℃,可利用余热锅炉或汽化冷却器回收余热。
(3)采用氧气底吹熔炼,原料中Pb、S含量的上限不受限制,不需要添加返料,简化了流程,且取消了破碎设备,从而降低了工艺电耗。
(4)由于减少了工艺环节,提高了Pb及其他有价金属的回收率,氧气底吹熔炼车间Pb的机械损失<0.5%。
4.4.2.1水口山法(SKS法)
水口山法是原水口山矿务局与国内有关科研、设计单位,于八十年代后期研究开发的氧气底吹直接炼铅工艺。
成功开发具有自主知识产权的氧气底吹熔炼——鼓风炉还原炼铅新工艺同时成功地将自主研发的“富氧渣鼓风炉熔炼技术”和“鼓风炉强化喷粉熔炼技术”有效整合,形成了世界上首次将艾萨炉应用于铅冶炼的先进技术。
已建成投产的有济源冶炼厂和池州冶炼厂
目前水口山矿务局也建成投产了一套80kt/a粗铅的铅厂,采用SKS炉+鼓风炉+烟化炉流程。
上世纪八十年代以前,世界上所有铅冶炼均采用烧结—鼓风炉熔炼工艺,低浓度SO2烟气及烧结破碎返粉铅尘污染十分严重,我国铅厂工人每年都要进行休假排铅,并且严重影响铅厂周围儿童智力发育。
各国都在开展铅冶炼新工艺的研究,以治理铅冶炼污染问题。
我国在1985年由国家计委、国家科委立项,把治理铅冶炼污染列为重点科研攻关项目。
确定在沈阳冶炼厂开展湿法炼铅扩大试验和在水口山矿务局开展氧气底吹氧化—电炉还原熔炼扩大试验研究。
湿法炼铅扩试工艺流程拉通,但因经济不合理而被否定。
在水口山经二年多试验,氧气底吹氧化工艺扩试取得阶段性成果。
电炉还原熔炼扩试因粉煤制备装置简陋及试验经费欠缺等原因未获成果。
SKS法创新点:
1.工艺流程创新
2.设备创新
1)原创底吹熔炼炉
2)余热锅炉创新
3)格盘式铸渣机
4)新型铅鼓风炉
5)喷枪设计创新
3.过程控制创新
4.开创铅尘封闭输送处理系统
1988年我国开始引进QSL炼铅工艺谈判,至1993年试投产,因各种原因,该工艺在我国未获成功,故难以推广。
1998年中国有色工程设计研究总院带头,组织池州冶炼厂、河南豫光金铅集团、温州冶炼厂和水口山矿务局五方集资,进行氧气底吹熔炼——鼓风炉还原工业试验,取得成功。
1999年国家计委、国家经贸委分别批准用该工艺在池州冶炼厂建设3万t/a的示范性工厂和在河南豫光金铅集团进行5万t/a铅冶炼厂的技术改造。
4.4.4.2SKS法设备创新
(1)原创底吹熔炼炉
底吹炉的长径比、底部氧枪布局及位置、加料口位置、熔池深度、排烟、放渣、放铅口位置,都是通过在科学院化冶所的冷态模拟试验后确定的,确保炉内传质、传热良好,排烟、放渣,放铅操作顺利。
(2)余热锅炉创新
为防止底吹炉SO2烟气在炉口处外逸,设计了一个香蕉型膜式壁密封烟罩,保证炉体在生产或转动时,炉口烟气不会外逸,保护了车间环境条件。
(3)格盘式铸渣机
为了使底吹炉产出的高铅渣,直接满足鼓风炉的块度要求,通过单模冷却试验,确定了铸模规格、铸锭机长度及运行速度。
设计了薄层速冷格盘式直线型铸渣机,完全满足了产能及鼓风炉熔炼的要求。
是满足该工艺要求的原创设备。
(4)新型铅鼓风炉
由于烧结块和高铅渣的理化性质差别较大,高铅渣极易熔化,原炼铅鼓风炉,不能满足处理高铅渣的要求,通过在水口山的试验,改变了鼓风炉炉腹角,采用双排风口,从而延伸了炙热焦炭高度,延长了铅渣中氧化铅的还原时间。
(5)喷枪设计创新
ISA喷枪寿命 1~2周
QSL喷枪寿命 2~4周
池州、豫光喷枪寿命 6~8周
主要创新点:
①强化了喷枪冷却效率;
②喷枪表面喷涂高温陶瓷,提高耐磨抗腐性能;
③提高了喷枪加工精度,确保氧及氮均布,保证了枪 头在炉内温度均一;
④喷枪材质进行了特殊预处理。
经济效益:
池州,较原烧结锅鼓风炉流程每吨铅成本下降200元,每产出一吨铅同时产出一吨酸,每吨酸视市场波动,利润可达100~200元。
豫光,较原烧结机鼓风炉流程每吨铅成本降低150元,每吨酸多盈利100~200元。
两厂合计每年新增效益:
3500~4800万
社会效益:
以推广应用80万t铅产量计,每年可减少50万吨SO2排放污染大气环境。