基于PLC实现的板材切割机的设计.docx
《基于PLC实现的板材切割机的设计.docx》由会员分享,可在线阅读,更多相关《基于PLC实现的板材切割机的设计.docx(26页珍藏版)》请在冰豆网上搜索。
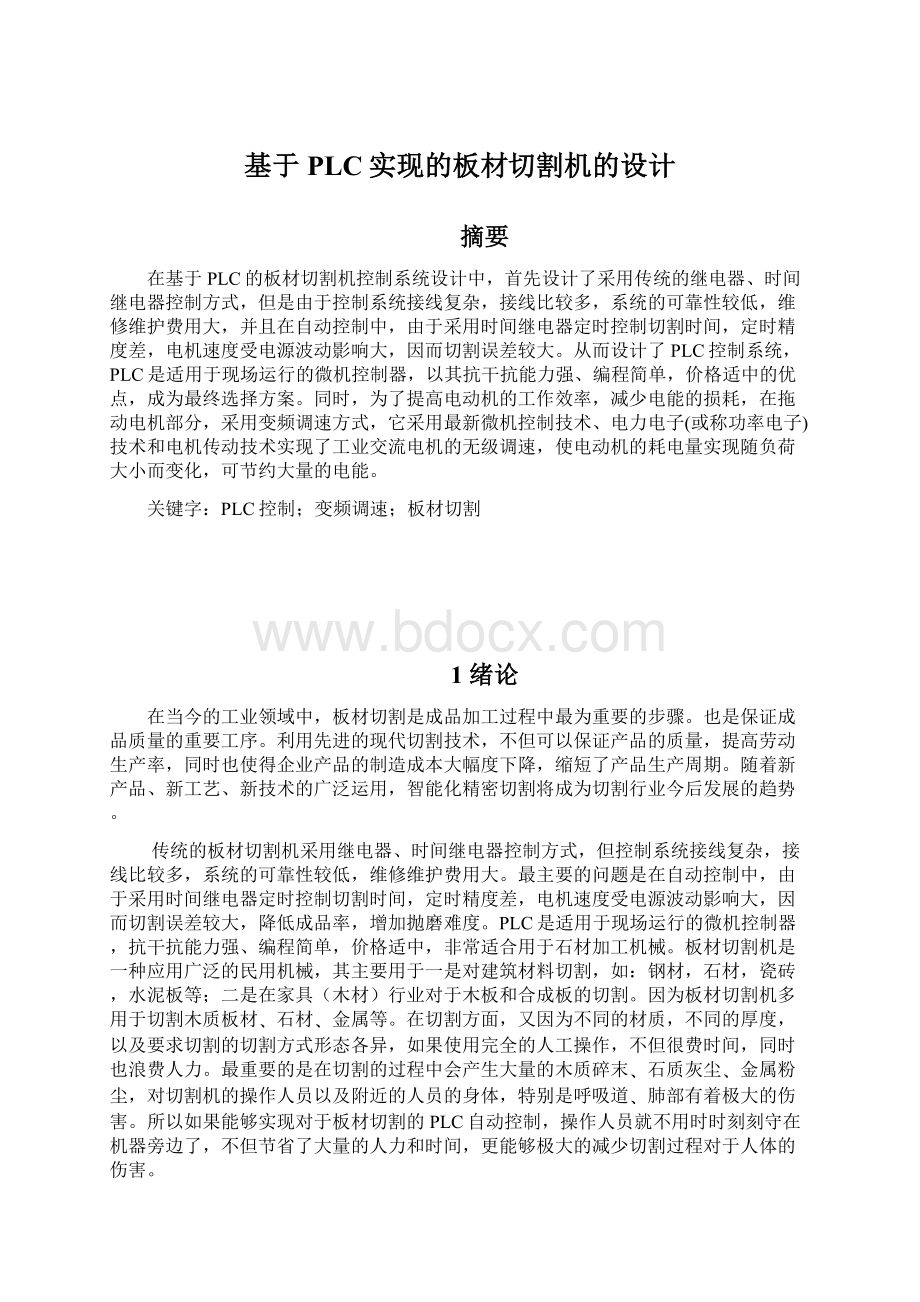
基于PLC实现的板材切割机的设计
摘要
在基于PLC的板材切割机控制系统设计中,首先设计了采用传统的继电器、时间继电器控制方式,但是由于控制系统接线复杂,接线比较多,系统的可靠性较低,维修维护费用大,并且在自动控制中,由于采用时间继电器定时控制切割时间,定时精度差,电机速度受电源波动影响大,因而切割误差较大。
从而设计了PLC控制系统,PLC是适用于现场运行的微机控制器,以其抗干抗能力强、编程简单,价格适中的优点,成为最终选择方案。
同时,为了提高电动机的工作效率,减少电能的损耗,在拖动电机部分,采用变频调速方式,它采用最新微机控制技术、电力电子(或称功率电子)技术和电机传动技术实现了工业交流电机的无级调速,使电动机的耗电量实现随负荷大小而变化,可节约大量的电能。
关键字:
PLC控制;变频调速;板材切割
1绪论
在当今的工业领域中,板材切割是成品加工过程中最为重要的步骤。
也是保证成品质量的重要工序。
利用先进的现代切割技术,不但可以保证产品的质量,提高劳动生产率,同时也使得企业产品的制造成本大幅度下降,缩短了产品生产周期。
随着新产品、新工艺、新技术的广泛运用,智能化精密切割将成为切割行业今后发展的趋势。
传统的板材切割机采用继电器、时间继电器控制方式,但控制系统接线复杂,接线比较多,系统的可靠性较低,维修维护费用大。
最主要的问题是在自动控制中,由于采用时间继电器定时控制切割时间,定时精度差,电机速度受电源波动影响大,因而切割误差较大,降低成品率,增加抛磨难度。
PLC是适用于现场运行的微机控制器,抗干抗能力强、编程简单,价格适中,非常适合用于石材加工机械。
板材切割机是一种应用广泛的民用机械,其主要用于一是对建筑材料切割,如:
钢材,石材,瓷砖,水泥板等;二是在家具(木材)行业对于木板和合成板的切割。
因为板材切割机多用于切割木质板材﹑石材﹑金属等。
在切割方面,又因为不同的材质,不同的厚度,以及要求切割的切割方式形态各异,如果使用完全的人工操作,不但很费时间,同时也浪费人力。
最重要的是在切割的过程中会产生大量的木质碎末﹑石质灰尘﹑金属粉尘,对切割机的操作人员以及附近的人员的身体,特别是呼吸道﹑肺部有着极大的伤害。
所以如果能够实现对于板材切割的PLC自动控制,操作人员就不用时时刻刻守在机器旁边了,不但节省了大量的人力和时间,更能够极大的减少切割过程对于人体的伤害。
当今社会,电动机的应用极为广泛,其消耗的电能约占工业电耗的65%,故合理有效地使用电动机,提高电动机的工作效率使其节能运行十分重要。
目前我国交流电动机传动大多为非调速型,耗能惊人,如改成调速运行,使电动机的耗电量实现随负荷大小而变化,则可节约大量的能源。
调速运行的方式很多,其中变频调速优于以往任何一种交流调速方式(调压调速、变极调速、串级调速、滑差电机调速等),是当今国际上一项效益最高、性能最好、应用最广的高新技术。
它采用最新微机控制技术、电力电子(或称功率电子)技术和电机传动技术实现了工业交流电机的无级调速。
在国外尤其是在日、美、德、英等工业发达国家获得了广泛应用,是自动化电力拖动的发展方向。
所以选择本题的目的就是:
一方面是为了加深学习变频器调速的应用和PLC控制的应用;另一方面就是为了研究如何让民用机械更好的实现自动控制和实现碳的减排工作。
意义就在于对板材切割机实现基于PLC控制的自动控制,增强生产能力,最重要的就是减少生产过程对人体的伤害和实现能源的节约。
2板材切割机功能实现
2.1通用板材切割机基本结构
自20世纪70年代以来,板材切割机凭借其结构紧凑、工作平稳、操纵轻便灵活、安装维修方便等特点,在钢材,石材,瓷砖,木板等加工中得到了广泛应用。
主要用于小型板材加工厂、板材市场、板材经销商、现场加工及建筑单位现场施工,目的是把前道工序加工好的板材切割成所需规格的成品板材。
特别是近几年来,随着国内广场道路建设以及买房装修的飞速发展,板材切割机被更广泛地用于各种广场石、地板石、墙壁石、家具装潢的成品加工,由于其现场操作性强,加工质量好,效率高而得到板材加工企业、施工企业的青睐。
通过对常用板材切割机功能进行分析,本设计得出通用板材切割机基本构成如下:
1)板材切割机的基本功能是切割,多采用电动机拖动锯盘或者砂轮,对板材进行切割,此部分即为板材切割机的切割机构。
2)在对板材切割时,切割机构需要行进与后退完成对与板材的切割工作,这里的切割机构的移动就需要拖动电机与牵引部分的参与,此部分即为板材切割机的牵引机构。
3)在对板材进行切割前,需要对板材进行固定,使板材在切割过程中不至于移动,所以板材切割机就需要一个压紧机制,所以就有了压紧机构。
根据以上板材切割机的基本构成,本设计在此基础上加以实现与改进,实现以下过程:
放上板材——板材压紧——启动主轴切割机构——牵引机构拖动切割机构进行行进完成对板材的切割——切割机构返回——切割机构停止运转——松开切割好的板材。
根据以上过程,板材切割机结构简图如图2.1、图2.2。
图2.1通用板材切割机结构简图1
图2.2通用板材切割机结构简图2
2.2板材切割机的控制要求
根据图2.1和图2.2,为了实现对于此板材切割机的工作过程,设计了继电器逻辑控制和基于PLC控制,控制要求如下:
2.2.1继电器控制逻辑控制要求
切割机构主轴电动机采用直接启动方式,在启动前,要求用于压料的压缩空气的压力足够,否则不允许主轴启动。
只有当主轴启动完成后,并且物料被可靠压紧后,才可以启动锯料行进。
每次锯料前采用手动物料压紧操作,然后再开锯料行进,当电磁阀得电时,气缸柱塞下压,完成物料固定;电磁阀失电时,气缸柱塞升起,将物料松开。
每次锯料要求只启动锯料行进,然后到达终点或者锯片离开物料后能自动返回。
返回控制应考虑终端返回、锯割短料时的短程返回和初次起动时手动返回。
短程返回要求进行物料检测,当锯片离开物料后自动返回。
无论哪种返回操作,到达起始位置后均自动停止。
2.2.2PLC逻辑控制要求
1)首次起动后的自动回返起始位的控制动作,要求系统能在首次主轴起动完成后,有自动回返起始位置的控制动作。
2)主轴起动后,在开锯料行进前不必再进行手动压料操作,应直接开料行进,在锯料行进前自动压紧物料,压紧后锯料行进自动进行。
每次返回前必须先停止锯料行进,延时1-2S然后返回,以减少电动机的反向起动电流。
3)实现无物料返回,在物料没有放好时错按下锯料起动按钮,经过延时,未检测到物料后自动返回。
物料检测还是使用了行程开关,起始位、终点位、物料压紧等检测元件均采用接近开关。
3板材切割机继电器逻辑设计
3.1控制原理图
图3.1继电器逻辑设计方案控制原理图
表3.1继电器控制逻辑部件对应功能
名称
功能
名称
功能
名称
功能
KM1
主轴
SQ1
短距锯料检测
SB1
主轴起动
KA1
短程返回标志
SQ2
锯料起始端
SB2
主轴停止
KA2
锯料前进
SQ3
锯料末端
SB3
锯料行进
KA3
锯料返回
SQ4
物料压紧完成
SB4
锯料返回
KA4
压紧进气阀
SQ5
物料压紧完成
SB5
长锯/短锯
KT
短程返回定时
SB7
压料气缸压
SB6
压料气缸松
3.2继电器控制原理
3.2.1长锯控制
起始位置,SQ2处于动作状态。
SB5锁定长锯,SB5断开。
放上待锯物料,按下SB7——KM4得电(压紧进气阀打开进气)——SQ4、SQ5动作(压紧到位)。
按下SB1——KM1得电(自锁,KM1常开闭合)——主轴启动(切割机构工作)。
按下SB3——KA2得电(KA2自锁互锁完成)——拖动电机正向转(锯料行进)。
锯料行进过程中:
切割机构离开起始位置,SQ2复原。
接着,SQ1物料检测动作,KA1得电。
锯料到达终点,SQ3动作——KA2失电(切割机构停止前进接触互锁)——KA3得电(自锁互锁完成)——切割机构返回。
切割机构返回到起始位置,SQ2动作——KA3失电(拖动机构停止运行)。
按下SB2——切割机构停止运行。
按下SB6——电磁阀打开,压紧气缸松开。
可取下板材。
为保证切割质量以及保护锯盘,拖动电机采用变频器驱动,实现调速。
3.2.2短距控制
起始位置,SQ2处于动作状态。
SB5锁定短锯,SB5闭合。
放上待锯物料,按下SB7——KM4得电(压紧进气阀打开进气)——SQ4、SQ5动作(压紧到位)。
按下SB1——KM1得电(自锁,KM1常开闭合)——主轴启动(切割机构工作)。
按下SB3——KA2得电(自锁互锁完成)——拖动电机正转(锯料行进)。
切割机构离开起始位置,SQ1物料检测动作——SQ2复原——KA1得电。
切割到板材末端,SQ1检测不到物料(复原)——KT动作(断电延时闭合触点瞬时断开)——KA2失电(切割机构停止前进)——KT通电延时闭合触点延时闭合——KA3得电(拖动电机反转,切割机构返回)。
SQ1重新检测到物料,发生动作——KT失电。
切割机构返回到起始位置,SQ2动作——KA3、KA1失电(拖动机构停止运行)。
按下SB2——切割机构停止运行。
按下SB6——电磁阀打开,压紧气缸松开。
可取下板材。
为保证切割质量以及保护锯盘,拖动电机采用变频器驱动,实现调速。
4PLC逻辑控制设计
4.1PLC控制与继电器控制比较
1)控制逻辑:
继电器控制逻辑采用硬接线逻辑,利用继电器机械触点的串联或并联及延时继电器的滞后动作等组合成控制逻辑,其连线多而复杂,体积大,功耗大,一旦系统构成后,想再改变或增加功能都很困难。
另外继电器触点数目有限,每只一般只有4~8对触点,因此灵活性和扩展性都很差。
而PLC采用存储逻辑,其控制逻辑以程序方式存储在内存中,要改变控制逻辑,只需改变程序,故称为“软接线”,其连线少,体积小,加之PLC中每只软继电器的触点数理论上无限制,因此灵活性和扩展性都很好。
PLC由中大规模集成电路组成,功耗小。
2)工作方式:
当电流接通时,继电控制线路中各继电器都处于受约状态,即该吸合的都应吸合,不该吸合的都因受某种条件限制不能吸合。
而PLC的控制逻辑中,各继电器都处于周期性循环扫描接通之中,从宏观上看,每个继电器受制约接通的时间是短暂的。
3)控制速度:
继电控制逻辑依靠触点的机械动作实现控制,工作频率低。
触点的开闭动作一般在几十毫秒数量级。
另外机械触点还会出现抖动问题。
而PLC是由程序指令控制半导体电路来实现控制的,速度极快,一般一条用户指令的执行时间在微秒数量级。
PLC内部还有严格的同步,不会出现抖动问题。
4)限时控制:
继电控制逻辑利用时间继电器的滞后动作进行限时控制。
时间继电器一般分为空气阻尼式、电磁式、半导体式等,其定时精度不高,定时时间易受环境湿度和温度变化的影响,调整时间困难。
有些特殊的时间继电器结构复杂,不便维护。
PLC使用半导体集成电路作定时器,时基脉冲由晶体振荡器产生,精度相当高,定时范围一般从0.1s到若干分钟甚至更长,用户可根据需要在程序中设定定时值,然后由软件和硬件计数器来控制定时时间,定时精度小于10ms且定时时间不受环境的影响。
5)计数控制:
PLC能实现计数功能,而继电控制逻辑一般不具备计数控制功能。
6)设计与施工:
使用继电控制逻辑完成一项控制工程,其设计、施工、调试必须依次进行,周期长,而且修改困难。
工程越大,这一点就越突出。
而用PLC完成一项控制工程,在系统设计完成以后,现场施工和控制逻辑的设计(包括梯形图和程序设计)可以同时进行,周期短,且调试和修改都很方便。
7)可靠性和可维护性:
继电控制逻辑使用了大量的机械触点,连线也多。
触点开闭时会受到电弧的损坏,并有机械磨损,寿命短,因此可靠性和可